1. Introduction
Cellulose is by far the most abundant organic compound mainly derived from biomass. The main source of cellulose is the existing lignocellulosic material in forests, wood being considered the most important source. Other material containing cellulose may tentatively include agricultural waste, water plants and grasses. However, from the point of view of industrial marketing, cellulose, the most common biopolymer, has been used for centuries as a raw material of trees and other plants in various applications. World production of this biopolymer is estimated between 1010-1011 tonnes each year [1] and only about 6 x 109 tonnes is processed for paper, textile, and chemical materials [2].
Sugarcane Bagasse (SCB) is a residue generated in prominent proportions in sugar and brown sugar industries, which contains a high percentage of cellulose, can be separated from other substances, which are mainly lignin and hemicellulose [3]. Natural fibers have attracted much attention from researchers because they are inexpensive, abundant, biodegradable, renewable, strong and light weight. Cellulose fibers are valuable in a wide range of fields such as filtration and biomedical applications [4], [5].
With the Arrival of nanotechnology, cellulose began to work on this scale. Areas such as biotechnology, food, pharmaceutical, chemical, textile materials with superior properties, are an example of it [6]. Furthermore, electrospinning, a manufacturing technique of electrostatic fiber, has shown great interest because of potential applications in several fields such as tissue engineering, biosensors, filtration, wound dressing, and drug delivery and enzyme immobilization [7]. Electrospinning, is a technique in which polymeric solutions are made with substances with high dielectric constants, with which can be obtained nanoscale fibers with various compounds such as chitosan, starch, cellulose acetate, polylactic acid (PLA), among others.
Cellulose acetates are obtained treating cellulose with a mixture of acid and acetic anhydride, in the presence of catalysts such as sulfuric acid, hydrochloric acid, phosphoric acid, zinc chloride, etc. or electrolytes that promote the formation of compounds of adding cellulose. However, the reactions require a very long time [8-10] and the energy consumption is high. The synthesis by microwave represents an alternative technique to provide thermal energy to the reaction with interesting advantages such as time savings and energy, generating fewer BY-products, the optimization of yields, obtaining products in a smaller number of steps, without counting that is an alternative that supports the development of new lines of research through the optimization of conditions [11].
In this study, cellulose acetate fibers were generated by electrospinning, using equipment developed at the Pedagogical and Technological University of Colombia in the DANUM group, this allowed different types of nanoscale fibers to be obtained, with different substances such as chitosan, starch acetate, cellulose, polylactic acid (PLA), among others; It also allowed finding the optimal processing parameters (concentration, tension, flow out and away from the needle to the collector) that affect the final product quality[21-22] .
2. Materials and Methods
Sodium hydroxide, NaOH (Emsure, 99%) was used for purification of cellulose, Nitric Acid, HNO3 (Merck, 65%), Ethanol, EtOH (Sigma-Aldrich, 99.8%) was also used this was done in an oven (MLW WSO 100 S1086); for the synthesis of Cellulose Acetate (AC) Resublimed Iodine (Carlo Erba, 99.9%), Acetic Anhydride, AA (Merck, 98.5%) and Microwave equipment (SINEO MDS-8G, No. was used Ref 08G086M).; for electrospinning an equipment of high voltage source (HV350R), Injector Pump Systems Inc NE-1000, a copper collector, covered with aluminum, plastic needles 10 ml mark Plasticak a capillary diameter as used 0.8mm. Electrospinning equipment was developed and built in the Pedagogical and Technological University of Colombia (UPTC) in a group: Development and Application of New Materials (DANUM). To prepare the electrospinning polymer solution, N-dimethyl formamide, DMF (Panreac, 99.8%) and acetone, Ac (Panreac, 93.5%) were used as solvents .The bagasse from sugar cane was obtained in the town of Moniquirá (Boyacá, Colombia). All chemicals were of analytical grade, purchased from Representante de Productos Químicos (Bogotá, Colombia).The commercial cellulose acetate was obtained from Alldrich Chemical Company, and used without further purification.
Purification: Purification of the sugarcane bagasse (SCB) was obtained in a laboratory following the methodology proposed by Rodrigues Filho et al. [9]. A mixture of 754 mL NaOH (0.25 M) and 4 g of dry, ground bagasse was kept at room temperature for 184 h. Then, this mixture was filtered and washed with distilled water. Next, the bagasse was refluxed with a HNO3/ethanol solution (20% v/v) for 34 h, with the alcoholic solution being changed at 14 h intervals. After the reflux, the bagasse was washed with distilled water and oven dried at 1054 C for 64 h.
Acetylation: Acetylation of SCB cellulose was obtained in a laboratory using the methodology proposed by Rodrigues Filho et al. [10], with some modifications.
Electrospinning: Two types of fibers were made, one with the SCB cellulose acetate and another with Aldrich cellulose acetate, using the electrospinning equipment of the Pedagogical and Technological University of Colombia, adapting Khatri's methodology [14] at a concentration of 17% w/v with the following modifications:
Infrared Spectroscopy (FTIR): IR spectra of cellulose and cellulose acetate (CA) were obtained with IS50 NICOLET FT-IR, using the ATR method.
SEM Scanning Electron Microscopy: The morphology of the fibers was examined on a SEM-JSM-7600F JEOL, at the Institute for Materials Research of the National Autonomous University of Mexico (UNAM); the data was processed using the "Imagej" program.
Differential Scanning Calorimetry (DSC): DSC analysis was carried out on a DSC Q2000 V24.10 Build 122, DSC Module Standard Cell RC, located at the Institute for Materials Research at UNAM. Treatment of the results was performed using Universal Analysis 2000 software by TA Instruments.
Table 1 Electrospinning Parameters.
Cellulose acetate from SCB Parameters | Cellulose acetate from Aldrich Parameters | |
Distance from Injec- tor to Collector | 15 cm | 15 cm |
Potential | 15 KV | 15 KV |
Solution Injection Speed | 0,3 μL/h | 90 μL/h |
Capillary Diameter | 0,4 mm | 0,4 mm |
Solvent 2:1 | Acetone/DMFA | Acetone/DMFA |
TGA Thermogravimetric Analysis: Fibre analysis was carried out on a TGA Q5000 V3.15 Build 263 Module TGA. The data results were processed using Universal Analysis 2000 software by TA Instruments.
3 Results and Discussion
Infrared Spectroscopy (FTIR):Figure 1, showing the spectra of purified cellulose bagasse sugarcane, it can be seen that the purification was carried out successfully because of the comparison with the infrared spectrum of Contreras et al. [15] as well as acetylated cellulose (cellulose acetate); the presence of a band was observed at 1734.94 cm-1, attributed to the stretching vibration of the carbonyl group; this band is not present in the spectrum of the cellulose since it is characteristic of an acetylated material; reduction is also observed in the intensity of the band at 3322.5 cm-1 (OH stretch), concluding that the reaction occurred [8].
Scanning Electron Microscopy-SEM: In figure 2, SEM micrographs seen at 1000x and 10000x; we see that the nanofibers from the SCB cellulose acetate are of a uniform, cylindrical structure; while drops in the fibers (clusters) can be seen in the Aldrich cellulose nanofibers: this is mainly due to the lower flow rate of the injector pumping the polymer with the BCA cellulose acetate when compared with Aldrich's; This could lead to the conclusion that a lower flow rate results in thinner fibers, and this is comparable with what is observed in the literature [16-20]. As for the fiber size, average sizes are: cellulose ac- etate BCA 258 nm with SD = 0.123 nm; Aldrich cellulose acetate 448 nm with SD = 0.410 nm (See Figure 3).
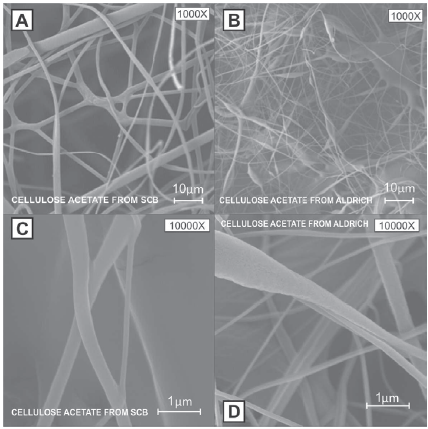
Figure 2 A) and C) SCB Cellulose acetate micrographs; B) and D) Aldrich cellulose acetate micrographs.
Differential Scanning Calorimetry - DSC:Table 2 summarizes DSC performance of Aldrich cellulose acetate compared to DSC of cellulose acetate from sugar cane bagasse. Enthalpy relaxation corresponding to sol- vent evaporation can be observed, the exothermic curve corresponding to a crystallization temperature and a further enthalpy relaxation corresponding to the material melting.
As can be seen, the crystallization temperature in the SCB cellulose acetate is lower, probably due to the smaller diameter of the nanofibers making it much easier to reach the crystallization point; The same happens with the melting point, which in the case of the SCB is also higher, given that melting resistance is higher the smaller the diameter of the fibers.
Thermogravimetric Analysis (TGA): With the TGA we can observe the mass loss versus temperature in the case of cellulose acetate SCB, with a loss of mass of12.16%, corresponding to the retained solvents and adsorbed moisture; in the case of Aldrich cellulose ac etate, the percentage of loss of these solvents is lower, at 6.911%; this may be because the cellulose acetate fiber of the SCB, being thinner, adsorbs more moisture and this may be due to the greater porosity of the material. This test is complementary to the DSC, as when the mass is completely decreasing it is due to the material being degraded; said degradation starts after melting, as seen in Table 2.
4 Conclusions
FTIR analysis confirmed the production of cellulose acetate synthesis from the cellulose of natural sugar bagasse. Cellulose acetate nanofibers were successfully obtained by electrospinning technique, with an average diameter of 258 nm from the bagasse of sugar cane. By minimizing the injection rate, we obtained finer fibers without clusters and with better properties. Cellulose acetate from sugarcane bagasse is comparable with that from the Aldrich brand, according to the DSC and TGA.TGA presents loss between 325°C-390°C this is due to a phenomenon of fusion of cellulose derivative. On the basis of the characterization we should use this nanofibers as a material for biofilters.