Introducción
Las organizaciones han implementado en sus procesos metodologías de mejoramiento continuo para garantizar su sostenimiento en mercados altamente cambiantes. Entre estas metodologías se encuentra la filosofía de lean manufacturing, la cual permite la optimización de los procesos productivos y administrativos a partir de la eliminación de desperdicios (Omogbai & Salonitis, 2016). No obstante, para incorporar la filosofía de lean manufacturing en la estructura organizacional debe existir una estrategia corporativa y de operaciones clara (Drohomeretski, Gouvea da Costa, Pinheiro, & da Rosa, 2014; Gonçales, Campos, & Pontes, 2016) que brinde los lineamientos para su planeación, gestión y control en el largo plazo.
Asimismo, la adopción de la filosofía de lean manufacturing se encuentra asociada con la generación de valor y eficiencia en términos ambientales, lo que implica repensar las metas y estrategias de las organizaciones para atender el ciclo de vida de los productos y servicios ofertados (Abreu, Alves, & Moreira, 2017). De aquí que los resultados derivados de la ejecución de las herramientas del lean manufacturing como elementos de la estrategia corporativa y de operaciones no sean inmediatos y tarden tiempo en manifestarse (Norani, Md Deros, Abdul Wahab, & Ab Rahman, 2011).
Ahora bien, la filosofía de lean manufacturing se ha implementado de manera paulatina desde los años cincuenta, involucrando la coordinación de las herramientas técnicas con las buenas prácticas de gestión de recursos humanos (Cirjaliu & Draghici, 2016; Baril, Gascon, Miller, & Côté, 2016). Entre estas se destacan las herramientas de características mixtas que optimizan el uso de los recursos organizacionales para satisfacer a tiempo los requerimientos de los diferentes stakeholders, las cuales para el mercado actual se encuentran orientadas al mass customization (Onyeocha, Khoury, & Geraghty, 2015; Omogbai & Salonitis, 2016).
Además, el lean manufacturing se ha integrado con un nueva área de estudio conocida como Green Productivity, que vincula el desempeño industrial con procesos sostenibles (Verrier, Rose, & Caillaud, 2016). Asimismo, la filosofía lean manufacturing ha migrado al sector servicios (López, González, & Sanz, 2015) debido a la flexibilidad que ofrecen sus herramientas.
Si bien las herramientas de lean manufacturing se encuentran muy estandarizadas, resulta fundamental identificar la tipología o la clasificación de las herramientas, las cuales pueden ser pilares de la filosofía, operativas, de diagnóstico o de seguimiento. Además, se deben resaltar aquellos aspectos comunes que existen entre ellas, como el flujo de material, personal e información; la estandarización de procesos; el empoderamiento del personal y los canales de comunicación entre las diferentes áreas organizacionales (León, Marulanda, & González, 2017).
Con base en lo anterior, las herramientas que soportan la filosofía lean manufacturing son Just in Time (Cuatrecasas, 2006; Hay, 2003; Gaither & Frazier, 2000; Heizer & Render, 2007), células de manufactura (Villaseñor & Galindo, 2009; Salazar, Vargas, Añasco, & Orejuela, 2010; Cardona, 2013; Chang, Wu,& Wu, 2013; Jajodia, Minis, Harhalakis, & Proth, 1992), Jidoka, Poka Yoke y Single-Minute Exchange of Die (SMED) (Hernández & Vizán, 2013; Villaseñor & Galindo, 2009), Kaizen (Alukal & Manos, 2006; Imai, 2012), Value Stream Mapping (VSM) (Rother & Shook, 2003; Keyte & Locher, 2004; Sullivan, McDonald, & van Aken, 2002; Nash & Poling, 2008).
Asimismo, se destacan las 5 s (Villaseñor & Galindo, 2009; Rajadell & Sánchez, 2010; Pérez Rave, 2011; Villaseñor & Galindo, 2011), Total Productive Maintenance (TPM) (Cuatrecasas & Torrell, 2010; Hernández & Vizán, 2013), Kanban (Monden, 1996), gestión visual (Alukal & Manos, 2006; Hernández & Vizán, 2013), Six Sigma (Youssouf, Rachid, & Ion, 2014; Aguirre, 2010), Point-to-Pont Flow Chart (Sheldon, 2008), Lean Action Item List (Plenert, 2007) y Evaluación nivel de madurez (Urban, 2015).
Ahora bien, existen un conjunto de elementos que determinan el éxito en la implementación de lean manufacturing en una organización; entre estos se encuentran la comunicación, el cambio en la cultura, el compromiso de la alta dirección, el involucramiento de los empleados, la educación y el entrenamiento (Alhuraish, Robledo, & Kobi, 2017).
Con respecto al sector textil, se encontró que el éxito de aplicación de las herramientas lean en este tipo de compañías depende del nivel de empoderamiento que posean los colaboradores (Kordoghli & Moussa, 2013). Por otro lado, el uso de herramientas de lean manufacturing en las compañías del sector textil permite optimizar los recursos físicos y responder de forma eficiente a los cambios en la demanda en periodos cortos de tiempo (Maia, Alves, & Leão, 2015). Sin embargo, en el mencionado sector la implementación de herramientas lean se ha ejecutado sin un entendimiento real de su significado (Chiromo, Nel, & Sebele, 2015).
En el caso colombiano, el sector textil-confecciones aporta el 9,2% del PIB manufacturero (Superintendencia de Sociedades, 2015). En términos de estudios realizados sobre lean manufacturing en Medellín, Colombia, el sector textil ocupa el tercer lugar, con una participación del 9% (Arrieta, Domínguez, Echeverri, & Gutiérrez, 2011).
Sin embargo, la implementación total de las herramientas de lean manufacturing y la obtención de resultados en las organizaciones del sector textil pueden tardar más de dos años, lo que representa un periodo de tiempo muy largo para compañías que se gestionan desde una demanda cíclica (Barón & Rivera, 2014).
Por otro lado, para abordar la estrategia de operaciones, puede ser descrita con base en cuatro componentes (Slack & Lewis, 2011): estrategia corporativa, requerimientos del mercado, experiencia operacional y recursos operacionales.
Otros autores consideran que dicha estrategia se encuentra conformada por la misión empresarial, la ventaja competitiva, los objetivos y las decisiones estratégicas de la organización (Schroeder, Meyer, & Rungtusanatham, 2011;Chary, 2009; García, García, Pérez, Sánchez, & Serrano, 2013). También puede considerarse que está compuesta por metas a largo plazo, planes, políticas, cultura, recursos, decisiones y acciones que afectan las operaciones (Waters, 2006).
Con base en lo anterior, la estrategia operacional debe responder a un plan de acción que contenga los elementos diferenciadores de la estrategia corporativa (Ballou, 2004; Collis & Montgomery, 2005), como lo son los objetivos de la empresa, procesos visionarios, stakeholders y dirección de las estrategias funcionales; además de la cobertura geográfica de los negocios, tipología de productos y servicios ofertados y el poder competitivo en el mercado (Smit & Moraitis, 2015).
Por su parte, la estrategia de operaciones también considera la estrategia de negocios, la cual se constituye de manera particular para cada operación comercial ejecutada en la compañía (Schroeder et al., 2011; Becerra, 2009). Además de las operaciones, precio, producto y servicio (Roth, Schroeder, Huang, & Kristal, 2008). Finalmente, innovación, entendimiento de los riesgos y competitividad (Covin & Slevin, 1989).
Lo anterior contribuye con el logro de la ventaja competitiva, optimizando el uso de recursos y capacidades para superar a los competidores (Porter, 1991), además de garantizar el sostenimiento de los resultados en el largo plazo (Longenecker et al., 2009; Kumar, 2016).
Más aun, el éxito de la estrategia de operaciones suele evaluarse con base en el cumplimiento de sus objetivos o dimensiones de desempeño. Si bien diversos autores han diseñado un conjunto de objetivos operacionales, la presente investigación se desarrollará teniendo en cuenta dos de estos elementos: flexibilidad y entrega. Las otras dimensiones son costo y calidad.
Se entiende por flexibilidad la satisfacción de los requerimientos del mercado con base en la adopción de diversos estados. Por ende, una operación es más flexible si puede hacer más cosas; es decir, exhibir un rango más amplio de habilidades (Slack & Lewis, 2011). Los beneficios derivados de la flexibilidad pueden ser internos, como la respuesta a eventos no previstos, o externos, como el volumen de oferta de bienes servicios. A su vez, la flexibilidad involucra la reducción de tiempo, incremento de la capacidad, compra de equipos más flexibles o rediseño de producto (Schroeder et al., 2011).
Con respecto a la entrega, esta puede definirse como la confianza en el cumplimiento de los tiempos inicialmente pactados con el cliente o el tiempo de entrega interno programado para cada operación (Slack & Lewis, 2011). Su objetivo es reducir el tiempo malgastado en las operaciones, como reprocesamientos, desperdicios, inspección y otros pasos que no agregan valor y deben ser eliminados de las operaciones (Schroeder et al., 2011).
Por otro lado, para garantizar la operación futura de las organizaciones es importante definir un conjunto de decisiones denominadas «estratégicas», entre las cuales se encuentran las decisiones proceso, calidad, capacidad e inventario. La presente investigación tendrá en cuenta las dos últimas decisiones estratégicas.
La capacidad se refiere a la distribución de los espacios, el tamaño de cada uno de ellos y el volumen de atención que pueden brindar bajo operación normal (Slack & Lewis, 2011). Además busca suministrar los recursos correctos, en el lugar correcto y en el momento indicado (Schroeder et al., 2011).
A nivel de operaciones, las decisiones de inventario especifican el tipo y el nivel en que deben mantenerse las existencias en función de la incertidumbre. Se soporta en el uso de las TIC y sistemas de información a fin de garantizar la cantidad mínima necesaria y su ubicación (Schroeder et al., 2011). Antes de implementar una decisión de inventario, es necesario conocer cuál será su impacto no solo en la organización sino también en los demás eslabones de la cadena de suministro (Aiello, 2008).
En cierta medida, la implementación de lean manufacturing desde la gestión de operaciones representa un reto organizacional para atender los diferentes tipos de producción, desde niveles bajos hasta volúmenes altos de producto en proceso y producto terminado (Gómez & Godinho, 2017). En el caso del sector textil, la integración de ambos elementos puede generar ventaja competitiva a través del diseño, programación y control de los procesos corporativos (Gonçales et al., 2016; Klingenberg, Timberlake, Geurts, & Brown, 2013). Además, es fundamental que las empresas textiles desarrollen una estrategia competitiva mixta (costo y diferenciación) para mejorar los objetivos de entrega y flexibilidad (Castro, Castrillón, & Giraldo, 2011; Jayaram, Tan, & Laosirihongthong, 2014)
Con base en lo anteriormente tratado, se plantea la siguiente pregunta de investigación: ¿En qué medida las decisiones estratégicas de capacidad e inventario, y los objetivos operacionales de flexibilidad y entrega, se relacionan con la implementación de la filosofía de lean manufacturing en compañías del sector textil?
Metodología
La metodología empleada es de carácter cuantitativo. A su vez posee un alcance descriptivo-correlacional. Se basa en un estudio de caso realizado en siete compañías ubicadas en el Valle de Aburrá pertenecientes al sector textil, las cuales han implementado herramientas de lean manufacturing. Para la selección de las unidades del estudio se empleó un muestreo no probabilístico por conveniencia. Se realizó un contacto inicial con la Cámara de Comercio de Medellín para Antioquia, Sede Aburrá Norte y con representantes del Clúster Textil/Confección, Diseño y Moda, quienes proporcionaron un listado de 12 compañías que hubiesen ejecutado alguna de estas herramientas. Luego de establecer contacto, siete organizaciones decidieron participar a través de los líderes de procesos, cuyos cargos varían desde supervisores hasta gerentes de las compañías.
Una vez fueron seleccionadas las compañías participantes, se procedió con el levantamiento de información primaria a partir del diseño de un formulario y aplicación de una encuesta a los líderes de procesos. El formulario se encuentra dividido en tres secciones: generalidades de la empresa (preguntas de control), implementación de herramientas de lean manufacturing y relacionamiento del lean manufacturing con la estrategia de operaciones. Las preguntas empleadas son cerradas y las opciones de respuesta se basaron en la Escala de Likert de cinco opciones, siendo 1 totalmente en desacuerdo y 5 totalmente de acuerdo.
Para el análisis estadístico descriptivo de los componentes se empleó la correlación lineal entre el par de variables de Pearson. Dicho coeficiente varía en el rango −1 ≤ rxy ≤ 1, a fin de medir la fuerza de relacionamiento perfectamente positiva o negativa entre el par de variables que son estudiadas. No obstante, es fundamental calcular si la correlación es o no significativa. Para el caso específico de estudio se emplearon las siguientes hipótesis:
Donde:
i, j = PI1, PI3, PI6, PI8, PI9, PI10, PI11, PII2, PII4, PII5, PII6, PII7, PII8, PII14, PII15
Para la prueba de significancia se utilizó un ∝=0,05. Así pues, si el Valor p ≤ 0,05, se rechaza la hipótesis nula y se tendría un índice de correlación significativamente diferente de cero (0), con un nivel de confianza del 95%.
Por otro lado, la información secundaria se obtuvo a partir de la revisión detallada de la literatura en diversas bases de datos, repositorios institucionales, archivos, informes y revistas especializadas en el área. Con la información recabada, se procedió a la tabulación de los datos y a la selección de las preguntas a analizar.
Resultados
Preguntas de control
Se realizaron siete preguntas de control para conocer algunas de las generalidades de las compañías y de los líderes participantes. Es de aclarar que la principal característica que debían cumplir las organizaciones es que hubiesen implementado alguna de las herramientas del lean manufacturing en sus procesos productivos.
Ahora bien, los cargos de los líderes de proceso se ubican en los niveles gerenciales del organigrama organizacional: gerentes, directores de operaciones, coordinadores y jefes de calidad. El 57,2% de ellos tenían un tiempo de vinculación con la organización superior a 9 años. El 42,8% restante tenían un tiempo de vinculación entre 1-2 años.
Con base en el número de empleados y de acuerdo a la Ley 905 del año 2004, el 71,4% de las organizaciones poseen un tamaño mediano y el 28,6%, grande. El tamaño se definió teniendo en cuenta el número de colaboradores fijos de planta, eximiendo el número de empleados temporales. Además, el 57,2% de las compañías son administradas por sus propietarios y el 42,8% por personal independiente. Finalmente, para proteger la privacidad de los entrevistados se excluyen las preguntas relacionadas con su identidad, datos de contacto y nombre de la compañía para la cual laboran.
Caracterización de lean manufacturing y estrategia de operaciones
Aproximadamente el 84% de las compañías dieron una valoración muy favorable a la implementación de herramientas de lean manufacturing (PI1). No obstante, en el 28,57% de las organizaciones participantes no todos los miembros de los diferentes niveles jerárquicos tienen conocimiento sobre la filosofía lean (PI3) (fig. 1).
Por lo que se refiere a la estrategia de operaciones, en promedio el 85% de las empresas objeto de estudio incorporan dentro de esta estrategia el desarrollo de herramientas lean (PI6). Hay que mencionar, además, que para el 57% de los participantes la decisión estratégica de capacidad de las instalaciones físicas favorece la adopción de las herramientas de lean manufacturing (PI8). En relación con el número de clientes y ventas, para el 100% de las compañías estos valores tuvieron un incremento favorable a partir de la adopción de la filosofía lean (PI9, PI11). Sin embargo, el 14,27% de las compañías consideran que si bien hubo un aumento en el porcentaje de clientes y ventas a partir de la puesta en marcha de alguna de las herramientas de la filosofía lean, dicha mejoría no se vio reflejada en las utilidades de las organizaciones (PI10).
Avanzando en el razonamiento expuesto, el 71,43% de los participantes lograron aumentar su liderazgo en costos a partir de la adopción del lean manufacturing (PII2). No solo el liderazgo en costos, sino también la estrategia de enfoque se encuentra influenciada por la filosofía de lean manufacturing (fig. 2).
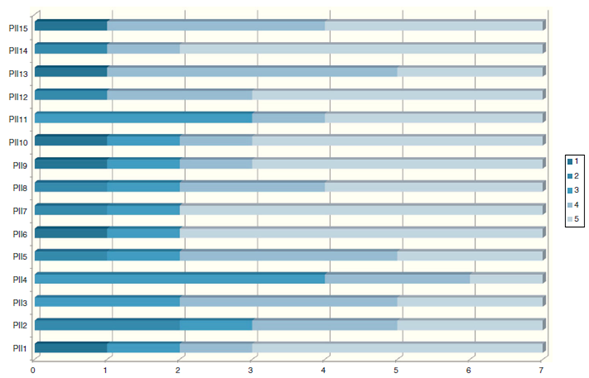
Fuente: elaboración propia.
Figura 2 Respuestas relacionamiento de lean manufacturing y estrategia de operaciones.
Desde otro punto de vista, el 71,43% de las compañías consultadas lograron optimizar la capacidad de los recursos físicos, humanos y tecnológicos mediante la adopción de componentes de la lean manufacturing (PII7). En contraste con lo anterior, para el 14,29% de los participantes, la interiorización de la filosofía de lean manufacturing en los procesos organizacionales no facilitó el cumplimiento de los tiempos de entrega (PII6). Cabe señalar que la incorporación de la filosofía lean logró reducir la incertidumbre en el nivel de inventarios en el 86% de las organizaciones indagadas (PII8). En la misma proporción, la estrategia de negocios de las compañías también respaldó el desarrollo de las herramientas de lean manufacturing en sus operaciones (PII14). Además, el 42,8% de las compañías estuvieron de acuerdo en que su estrategia corporativa también respalda la incorporación de la filosofía en su razón social y en la ejecución de sus actividades diarias (PII15).
Variabilidad compartida entre variables
La figura 3 muestra el coeficiente de correlación de Pearson en la primera fila y el valor de p en la segunda. Las parejas de variables que cumplen ambas condiciones se encuentran resaltadas en color verde y las que no las cumplen, en color rojo.
Ahora bien, el coeficiente de correlación adquiere mayor relevancia si se interpreta en términos de la proporción de variabilidad compartida o explicada, es decir, a partir del coeficiente de determinación representado por la expresión rij 2.Así pues, la implementación de herramientas de lean manufacturing en una compañía (PI1) y el conocimiento de dicha filosofía por parte de todos los miembros de la organización (PI3), comparten el 93% de los elementos. De aquí que el desarrollo de la lean manufacturing en las organizaciones requiera el involucramiento de todos los miembros y el establecimiento de canales de comunicación efectivos. Además, las acciones a ejecutar durante la incorporación de herramientas lean en los procesos organizacionales deben quedar contempladas y planeadas en la estrategia corporativa y la estrategia de negocios (PI1, PI3, rPI 1,PI6 2 = 0,76), (PI1, PII14, rPI1,PII14 2 = 0,69) (PI1, PII15,rPI1,PII15 2 = 0,69), a fin de que queden institucionalizadas en políticas de corto, mediano y largo plazo.
En este orden de ideas, también se encontró una fuerte variabilidad explicada entre el uso de herramientas de lean manufacturing y el incremento de las utilidades operacionales (PI1, PI10, rPI1,PI10 2 = 0,93), lo cual puede verse reflejado a partir de la disminución de desperdicios y liderazgo en costos que alcanzan estas compañías en el largo plazo. Por otra parte, también existe una fuerte correlación positiva y varianza compartida entre la adopción de herramientas de lean manufacturing y los objetivos de la estrategia de operaciones de flexibilidad y entrega (PI1, PII5, rPI1,PII5 2 = 0,77) (PI1, PII6,rPI1,PII6 2 = 0,81). Por consiguiente, la filosofía lean se convierte en una alternativa de gestión para afrontar las condiciones cambiantes y la incertidumbre de los mercados actuales. Además, contribuye con la satisfacción de los tiempos pactados con los stakeholders internos y externos.
Por lo que se refiere a la concepción de la filosofía lean manufacturing desde la estrategia corporativa, esta posee una fuerte variabilidad explicada con el cocimiento que deben tener todos los colaboradores sobre las herramientas lean. Es desde este componente donde se diseñan los procesos de inducción, capacitación, incentivos y seguimiento a las curvas de aprendizaje (PI3, PI6, rPI3,PI6 2 = 0,9) y se constituyen las estrategias de negocio a emplearse en los diferentes segmentos del mercado (PII14, PII15, rPII14,PII15 2 = 0,87).
A su vez, se establecen las metas con respecto a las utilidades esperadas (PI6, PI10, rPI6,PI10 2 = 0,85), volúmenes de producción a ser atendidos (PI6, PII5, rPI6,PII5 2 = 0,84), políticas de gestión de inventario (PI6, PII8, rPI6,PII8 2 = 0,69), tiempos en los cuales los pedidos serán entregados a los clientes (PI6, PII6,rPI6,PII6 2 = 0,89) y estrategia de negocios (costo, diferenciación y enfoque) (PII6, PII14, rPII6,PII14 2 = 0,64). Sin embargo, dichas metas solo pueden ser alcanzadas si para la implementación de herramientas lean se optimiza y documenta la capacidad de los recursos (PI6, PII7, rPI6,PII7 2 = 0,91) (PI1, PII7, rPI1,PII7 2 = 0,72), favoreciendo las acciones de control y seguimiento.
También se encontró una fuerte variabilidad explicada entre la flexibilidad con respecto al volumen de producción y el cumplimiento de los tiempos de entrega (PII5, PII6, rPII5,PII6 2 = 0,82). Por ende, el lean manufacturing facilitó el intercambio entre órdenes de pedido para respetar los compromisos pactados con los clientes en las compañías objeto de estudio. Igualmente, el objetivo de flexibilidad posee una correlación fuertemente positiva con las decisiones estratégicas de capacidad e inventario (PII5, PII7, rPII5,PII7 2 = 0,82) (PII5, PII8, rPII5,PII8 2 = 0,89).
Y es que no pueden variarse los volúmenes de producción sin tener en cuenta las instalaciones físicas, la maquinaria y el equipo de las compañías, al igual que los sistemas de información. Más aún, la capacidad de los recursos (físico, maquinaria y equipo) también comparte una fuerte variabilidad explicada con el cumplimiento de los tiempos de entrega (PII6, PII7, rPII6,PII7 2 = 0,98). Por cierto, la disminución en la incertidumbre del inventario parece tener una variabilidad explicada con la reducción de los tiempos de entrega (PII6, PII8, rPII6,PII8 2 = 0,84) y estar soportada en la capacidad de las instalaciones (PII7,PII8, rPII7,PII8 2 = 0,85).
Finalmente, el incremento de las utilidades a partir de la incorporación de herramientas lean manufacturing parece tener una fuerte variabilidad explicada con la flexibilidad en los volúmenes de producción (PI10, PII5, rPI10,PII5 2 = 0,75), el cumplimiento en los tiempos de entrega (PI10, PII6, rPI10,PII6 2 = 0,87), la capacidad de los recursos organizacionales (PI10, PII7, rPI10,PII7 2 = 0,78), la reducción en la incertidumbre en los niveles de inventarios (PI10, PII8, rPI10,PII8 2 = 0,62), la estrategia corporativa (PI10, PII14, rPI10,PII14 2 = 0,74) y de negocios (PI10, PII15, rPI10,PII152 = 0,65). Así pues, son las utilidades las que se convierten en el elemento integrador entre la adopción de la filosofía de lean manufacturing, los objetivos y las decisiones estratégicas de operaciones.
Conclusiones
La filosofía de lean manufacturing se constituye como una alternativa para generar ventaja competitiva en las organizaciones del sector textil que fueron estudiadas. Esta ventaja se obtiene a partir de la eliminación de desperdicios en los procesos de manufactura y del empoderamiento que alcancen los miembros de los diferentes niveles jerárquicos. A su vez, una posición sostenida en el mercado para estas organizaciones se logra mediante la coordinación de las herramientas de la lean manufacturing con la estrategia de operaciones, en lo que se refiere a las decisiones estratégicas de capacidad y disminución en la incertidumbre de los inventarios, considerando también los objetivos estratégicos de flexibilidad en el volumen de producción y el cumplimiento con los tiempos de entrega pactados.
A partir de la optimización de recursos, la incorporación de la filosofía de lean manufacturing también permite generar valor a los productos, servicios y procesos organizacionales. Sin embargo, dicha optimización debe incluirse en el componente estratégico de la organización para garantizar una respuesta efectiva a los cambios vertiginosos de los niveles de demanda, variaciones en los volúmenes de producción y transformaciones en las preferencias de los consumidores.
En las organizaciones participantes existe una varianza compartida muy elevada entre la implementación de herramientas de lean manufacturing, el conocimiento de dichas herramientas por parte de los colaboradores y el incremento en las utilidades operacionales. Sin embargo, no todos los miembros de las compañías textiles consultadas han interiorizado las herramientas que se están aplicando en los procesos productivos, lo que demuestra carencia de canales de comunicación efectivos entre los stakeholders internos y externos; y estrategias corporativas claras que guíen el actuar de los colaboradores.
Del mismo modo, no todas las empresas manifestaron un aumento en las utilidades como consecuencia de la incorporación de la lean manufacturing. Lo que va en contravía de la realidad operativa de las compañías textiles, donde los ciclos de producción son cortos y la competencia para atender la demanda no atendida es muy elevada. Asimismo, la capacidad en términos de recursos es reducida, lo que puede interferir en los tiempos de entrega pactados con el cliente, afectándose la reputación de las organizaciones y por ende sus utilidades.
De esta manera, el objetivo estratégico de entrega se convierte en uno de los elementos que mayor atención requieren durante la adopción de la filosofía lean. A su vez, la decisión estratégica de capacidad es fundamental para el desarrollo y la interiorización de cada una de las herramientas de lean manufacturing como filosofía de mejoramiento continuo.