INTRODUCTION
Biomass is an attractive alternative input for the production of fuels [1],[2], as well as a potential driving force for development of bio refineries [3]-[5]. The development of biomass based fuels as an alternative for fossil fuels energy has been encouraged worldwide by governmental policies, seeking to diversify energy sources and reduce environmental pollution caused by emissions from combustion of fossil fuels [6],[7]. Therefore, the production of bio-diesel via transesterification reaction of mainly vegetable oils has gained considerable attention in recent years. For example, the current biodiesel production in the European Union is approximately 11 million tonnes and forecasts suggest that in 2020 it will exceed 15 million tonnes per year [8]-[10]. However, 10% (w/w) of the total biodiesel production is CG [11], [12]. Thus, in the stoichiometry of the vegetable oils transesterification reaction, three moles of methanol react with the glycerides in three stages, in presence of a catalyst to produce methyl esters and glycerol. In the first stage, methanol reacts with triglycerides to form methyl esters and diglycerides. In the second stage, methanol reacts again, this time with diglycerides to form monoglycerides and methyl esters. Finally, in the third stage, monoglycerides react with methanol to form glycerol and methyl esters. According to the reactions described above, one mole of glycerol is produced per 3 moles of methyl esters synthesized.
CG production is exponentially increasing as a result of growth of biodiesel world production and it is forecast to reach 1.54 million tons in 2015 [13]. Oversupply of glycerol has negative environmental effects [14] as well as on the profitability of biodiesel production processes, if not properly managed. Therefore, obtaining products with high added value from glycerol contributes to sustainability and increased profitability for the biodiesel industry, as well as environmental benefits [12],[15].
Currently, glycerol used in industrial applications requires a purity of at least 85%. The purification process to bring the CG to that purity level represents approximately 14% of the total production cost [16]. The high purification costs of CG to obtain purified glycerol are associated with the requirements of separation techniques such as electrochemical [16], ion exchange [17], and vacuum distillation [18], which entail high operation and energy costs. Impurities to remove include catalyst and alcohol residues, free fatty acids, alkyl esters, mono, di and triglycerides [19].
Glycerol application fields, as it is a very versatile compound [20], are mostly related to the production of materials with applications in basic chemical industry, industrial microbiology and oxygenated fuel additives such as glycerol carbonate [21],[22]; acrolein [23],[24] and 1,2-propanediol [25],[26]. Additionally, pure glycerol has applications in the food industry, industrial microbiology, pharmacology and cosmetics; however, these applications require purity levels above 99%, which implies intensive purification procedures [11]. By contrast, the use of CG as raw material for development of industrial use products may not require high purification costs. Therefore, research work is currently focused on finding greater value- added uses for CG that would enable its use in industrial applications such as hydrogen production [27-29], production of polyhydroxyalkanoates (PHAs) [30]-[33], such as polyol in polyurethane foam production [34],[35], and biogas production [36],[37], to transform the current biodiesel industry, into bio refinery based on the oleochemical industry [38].
If glycerol produced as a by-product from the transesterification reaction is discarded as waste stream, it could threat the biodiesel production as a cost-effective process and would constitute an environmental threat. Therefore, there is a need to reevaluate CG using it in industrial applications. Already known applications of CG include: hydrogen production [27]-[29], synthesis of microbial polyhydroxyalkanoates (PHAs) [30]-[33], fumaric acid production [39], synthesis of 1,3 - propanediol [40]-[42], bioconversion into ethanol [43],[44] and polyols for the production of polyurethane [34],[45].
A promising valued-added product of glycerol is polyglycerol, a high molecular weight polymer formed by an inert polyether chain with abundant pendant hydroxyl groups, which makes polyglycerol a building block for diverse polymeric complexes [46]. One of the main characteristics of polymers made out of polyglycerol is that it is biocompatible, biodegradable, and a sustainable material. However, the reported production of polyglycerol, using sulfuric acid as catalyst, comes from purified glycerol [47]. To the best of our knowledge, synthesis of polyglycerol from CG as raw material has not been reported before. The CG composition shows that 60 to 80% is glycerol and the rest are impurities, mainly classified as soap, water, methanol, catalyst residues, free fatty acids, and salts [11],[48]. The purification process of CG to obtain purified glycerol results in a three-time cost increment. The high purification cost is an economic disadvantage that discourages the industrial production of polyglycerol [16],[49].
The use of CG for polymers feedstock is a promising application, among others. For example, Luo et al. [50] found that the CG can be used as biopolyols for polyurethanes foams production. Furthermore, Godinho et al [51] synthesized a pre-polymer of poly(glycerol sebacate), an elastomer with potential biomedical applications, using lipase B as catalyst.
An attractive alternative to revaluate CG is to produce polyglycerol. Polyglycerol is a polymer composed of an inert polyether backbone and abundant highly reactive hydroxyl groups that are exposed and allow for further modification to produce a variety of related compounds [46],[52],[53]. The presence of a catalyst - either of homogeneous or heterogeneous type- which can be either acidic or basic- is required for glycerol polymerization. Din et al [54] polymerized the CG using microwave irradiation and the soap content as the catalyst. The authors found that this process results in the formation of glycerol oligomers, from diglyccerol to pentaglycerol.
Salehpour and Dubé [47] evaluated the use of sulfuric acid as a catalyst of pure glycerol polymerization reactions at reduced pressures and obtained polyglycerols of relatively high molecular weights. Polyglycerol is industrially produced by ring opening polymerization of glycidol, and polymers with narrow distribution and molecular weights in a range between 1000 and 30000 g/ mol are obtained [46],[55]-[57]. Polyglycerols of higher molecular weight and branched structure, directly synthesized from glycerol, could replace hyperbranched polymers obtained from glycidol, a toxic monomer [58] opening the possibilities of application at industrial levels for the production of complex polymeric structures derived from glycerol. However, according to this study, the production of polyglycerol from CG as raw material does not occur. This research is aimed at understanding and identifying the factors that inhibit polymerization of CG using sulfuric acid as the catalyst. Therefore, a sample of CG was characterized to identify impurities. Simulated-CG was prepared adding the impurities, previously identified as purified glycerol. The effect of each impurity on the polymerization reaction, as well as the interaction between them, was analyzed.
An experimental design was conducted to study the effect of the most abundant impurities (soap and sodium) and the concentration of catalyst (sulfuric acid) in the polymerization of CG. As a result, it was found that sulfuric acid in presence of soap produces side reactions that compete with polyglycerol synthesis. Furthermore, a statistical analysis to assess the effect of the presence and absence of impurities, soap and sodium, at a fixed concentration of catalyst, revealed that the presence of soap in CG is the main inhibitory factor of polyglycerol synthesis.
EXPERIMENTAL DEVELOPMENT
MATERIALS
Pure glycerol, sodium hydroxide, and sulfuric acid were obtained from Merck. CG, a by-product from the biodiesel manufacturing process, was kindly provided by BioSC S.A. (Santa Marta, Colombia), which uses palm oil as raw material for biodiesel production.
CRUDE GLYCEROL (CG) CHARACTERIZATION
Physico-chemical characterization
Density of CG was determined using a 2 mL pycnometer. The pH of CG was measured with a digital pH meter Schott HANDYLAB 1 at room temperature (25 ± 1°C).
Glycerol content in the CG sample was determined using the iodometric-periodic acid method in accordance with the AACC 58 technique. Soap content was determined according to a modified version of the AOC Cs method [59]. Ash content was determined following the ISO 2098-1972 method.
Water content was determined following the AOCS official method (Ea 8-58), using a Volumetric Karl Fischer titrator (Metrohm 870 KF Tritino plus). The presence of methanol was determined by gas chromatography with an Agilent Technologies 6890N system equipped with a flame ionization detector. The method followed was the EN14110. Metals (Ca, K, Mg and Na) were detected by inductively-coupled plasma atomic absorption spectroscopy, using a Perkin Elmer 5300 DV spectrometer. These analyses were carried out in collaboration with the Quality Inspection Coordination, ECOPETROL S.A.
Complementary characterization
A thermogravimetric analysis (TGA) was performed to determined polymer degradation as a function of temperature. A temperature range from 25 to 300°C at a heating rate of 5 °C min-1 was used. This analysis was performed in a TGA 2050 from TA instruments, Inc., equipped with a nitrogen purge gas system (50 cm3 min-1). Infrared spectrum was obtained in transmittance mode in a Shimadzu 8400s spectrometer. Fatty acid methyl esters (FAME) present in the CG sample were identified with a gas chromatography system (Agilent Technologies 6890 series), coupled to a FID detector, using an Agilent DB23 column and SUPELCO 38 FAMES as standards.
All measurements were performed in duplicate. The mass analysis was performed by ESI-MS on a BRUKER DALTONICS INC, AMAZON X mass spectrometer. The molecular weight distributions were obtained using MAL-TOF-MS with a Bruker Reflex mass spectrometer, according to our previous work [60].
EXPERIMENTAL PROCEDURE
The polymerization reaction was carried out on a 50 mL glass reactor equipped with nitrogen inlet, catalyst feeding, thermometer inlet, and a distillation trap for continuous water removal from the reaction mixture. Temperature was maintained at 150°C, using a temperature-controlled heating bath. A vacuum pump was attached to the reactor through the condenser; in the meantime, condensation reactions were carried out at pressures below 33.86 kPa during ~ 3 h and before reaching the gel point. The soap used to simulate CG was made from palm oil saponification [61], and the metal amount was obtained from the neutralization of sodium hydroxide with sulfuric acid.
3. RESULTS ANALYSIS
Three different concentrations of sulfuric acid as catalyst, 0%, 1%, and 4.8% (% w/w), were used to carry out polymerization reactions of CG. The viscosity of CG is 0.28 Pa*s. The highest product viscosity was obtained with the reaction performed with 0% (w/w) sulfuric acid (1.63 Pa*s) compared with the viscosities obtained when using 1% and 4.8% catalyst (0.4 and 1.57 Pa*s respectively). The result can be explained by the presence of soaps in the CG sample, which catalyzes the oligomerization of glycerol increasing product viscosity [62]. Despite the increase of viscosity in the reaction products, there was not polyglycerol formation under any condition tested. The fact that polymerization of CG did not occur, even though the reaction was performed under the same conditions for which successful polymerization of purified glycerol was achieved, encouraged us to study the factors that inhibit polymerization of CG. To find the polymerization inhibitory factors present in CG, simulated-CG samples were prepared according to the composition in the characterization of CG.
CHARACTERIZATION OF CRUDE GLYCEROL (CG)
The physico-chemical characterization of CG from the hydrolysis of triglycerides in the production of biodiesel, suggests that 75% is glycerol with a pH of 6.14, and a density of 1.28 (g/cm3). The moisture content determined was 10.5%, soaps content 13.9%, ashes 3.5%, and methanol 0.025%. The presence of metals found in the sample were mainly sodium (22850±3860 mg/Kg), potassium (46.7±3.54 mg/Kg), calcium (17.1±1.78 mg/Kg), and magnesium (8.6±0.68 mg/Kg). Moreover, the free fatty acid (FAMES) composition was formed by palmitic acid 63.3%, oleic acid 29.6%, stearic acid 5.6%, and linoleic acid 1.6%. As regards metals and FAMES composition, a considerable high amount of sodium with respect to other metals was observed; similarly, palmitic acid was found in a significantly higher proportion with respect to other free fatty acids. This increase in sodium and palmitic acid could be explained by the use of sodium hydroxide or methoxide as a catalyst in the transesterification reaction; as well as African palm oil as raw material for biodiesel production.
A comparison between Fourier Transform Infra-Red (FT-IR) spectra of crude and purified glycerol is shown in Figure 1. The spectra shows the presence of a broad OH stretching band from 3000 cm-1 to 3600 cm-1, C-H stretching between 2883 to 2947 cm-1 and C-0 stretching from 1040 to 1120 cm-1 (Figure la). A carboxyl (C00-) peak only appears in the CG sample, see Figure lb. This peak indicates that soluble soaps present in CG were removed after the acidification stage [63],[64].
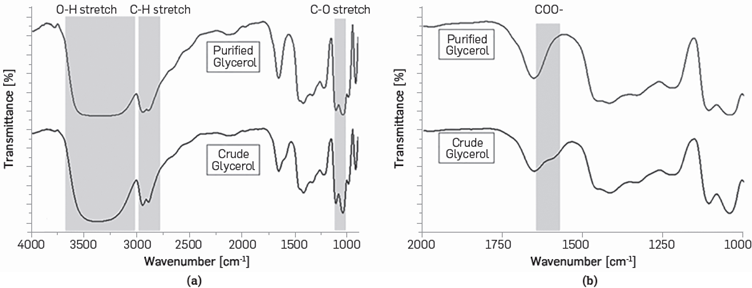
Figure 1 FT-IR spectra of crude and purified glycerol, (a) Shows the presence of stretching bonds in the samples analyzed, (b) Shows a carboxyl (COO-) peak that appears only in the CG sample.
The thermo-gravimetric analysis reveals a 2.45% weight loss in a temperature range between 25-37°C. This weight loss is due to the presence of volatile materials such as methanol. From 37-94°C, there is a 9.46% weight loss due to water evaporation, and between 100-200 °C, there is a significant weight loss attributed to glycerol thermal degradation. The remnant mass observed in the thermogram after 200 °C might be explained by the presence of inorganic salts and fatty acids, as reported in previous studies [65], [66].
SIMULATION OF CRUDE GLYCEROL (CG) COMPOSITION
Based on the composition obtained from the characterization of CG, a simulated-CG sample was prepared by adding the impurities into purified glycerol. Soaps and metals were the most abundant impurities identified and, considering that at 150°C, water and methanol evaporated, the last two were not considered to affect the polymerization of CG to produce polyglycerol. The soap used to simulate CG was made from palm oil saponification [61], and the metal was sodium because in the characterization of CG, there was a significantly higher amount as compared with other metals. The simulated-CG was prepared by adding soap at 14%w/w, and sodium at 22850 mg/Kg.
To confirm if the simulated CG prepared resembles the characterized one, two polymerization reactions were conducted under the same conditions using the simulated and characterized crude glycerols as raw material. The catalyst used was sulfuric acid at 4.8% w/w. Polymerization reactions were performed under conditions previously established in our previous work [60]. Hydroxyl number, mass spectroscopy, and thermogravimetry analysis were performed to compare reaction products obtained from polymerization reaction of the simulated and characterized crude glycerols. Results show a similar hydroxyl number for both glycerols used, simulated and the characterized one, which correspond to 376.25 ±6.68 and 406.76 ±7.35 mg KOH/g, respectively. Mass spectroscopy peaks for both samples were comparable (Figure 2a-2b). Related to ESI-MS results, it seems that the two reaction products exhibited similar mass distributions. Thus, the simulated-CG led to similar products than the original CG. This is also noticed in the TGA analysis, see Figure 3a and 3b. However, the first weight loss region is related to the remaining water molecules in the final reaction product. On the other hand, the second region is associated with glycerol biodegradation that could be catalyzed due to the presence of the impurities in the two samples [67].
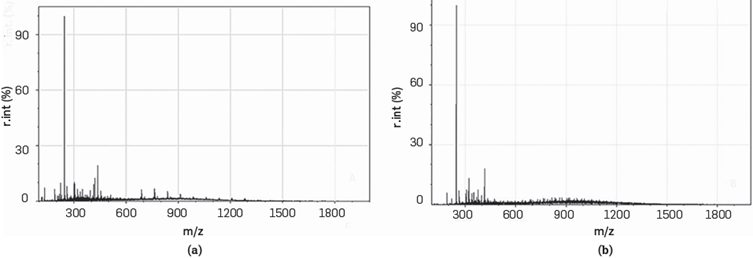
Figure 2 Electrospray Ionization (ESI) mass spectrum comparison between the polymerization reaction products of characterized (a) and simulated (b) CG. The concentration of sulfuric acid used as catalyst was 4.8% w/w. A similar mass distribution of the two samples was observed.
EFFECT OF SULFURIC ACID, SODIUM, AND/OR SOAP IN THE POLYMERIZATION REACTION OF SIMULATED-CRUDE GLYCEROL
A 2k full factorial experimental design was performed to determine the effect of impurities on the sulfuric acid- catalyzed polymerization reaction of simulated-CG. Table 1 summarizes the factors and levels used in the experimental design. Samples for each treatment were prepared adding the impurities corresponding to the factor levels proposed in the factorial design into purified glycerol. The reaction procedure was carried out as described in the experimental procedure section.
The hydroxyl number of the reaction products was selected as response variable, since it is an indicator of etherification or esterif¡cation reactions that may occur from different treatments. If in a treatment, an etherification or esterification reaction occurred, the hydroxyl number of the product should decrease with respect to the initial hydroxyl number of glycerol, as some of the initial OH groups have reacted.
The response variable chosen may also suggest the formation of polyglycerol, as this polymerization reaction is an etherification. The hydroxyl number of the reaction products for each treatment was determined following the ASTM D 4274-11 method. The hydroxyl number of purified glycerol is 1800 [mg KOH/g] [68]. Data reported in Table 2 is the average of two replicates which deviate less than 5% in all the treatments.
*Two independent samples were performed per treatment. The data reported is the average of two replicates that deviated less than 5% for treatments with 14% (w/w) soap, 22850 mg/kg sodium, and 0% sulfuric acid, and less than 1% for other treatments.
The analysis of variance (ANOVA) for the factorial design is presented in Tables 3 and 4. Results from statistical analysis suggest that factors affecting the hydroxyl number are, in order of importance, sulfuric acid, soap, and sodium. The interaction between sodium and sulfuric acid, and among the three factors (soap, sodium, and sulfuric acid) are also significant. The effect from interaction between other factors not mentioned above in the hydroxyl number is negligible. Results suggest that the presence of sulfuric acid propitiates reactions that end up in products with a smaller hydroxyl number than glycerol. As the soap content in the simulated CG increases from 10% to 14 % (w/w), the hydroxyl number of the reaction products decreases. On the other hand, the presence of sodium at 22850 mg/kg and the interaction between sodium and sulfuric acid when there is no sodium, neither sulfuric acid to 22850 mg/kg of sodium and 4.8 % (w/w) sulfuric acid causes the hydroxyl number of the reaction product to increase. Finally the interaction between soap, sodium and sulfuric acid when they go from 10% w/w soap in the absence of sodium and sulfuric acid to a 14% (w/w) soap, 22850 mg/kg sodium, and 4.8% sulfuric acid, the hydroxyl number of the products decrease.
Table 3 Statistical analysis of the factors effect on the hydroxyl number of the reaction products and analysis of variance.
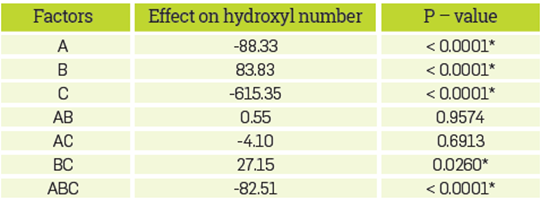
*The factor has a significant effect on the response variable (p<0.05)
Table 4 Treatments, levels, and response variables of the 22 factorial design. Sulfuric acid was fixed at 4.8% w/w.
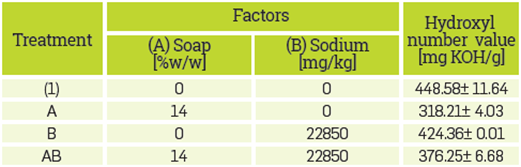
The reaction products obtained from the treatments proposed in the experimental design were analyzed with FT-IR. The spectrum obtained confirmed that the decrease in the hydroxyl number in the treatments was not due to polyglycerol formation, but due to other chemical reactions. The FT-IR spectra performed on all reaction products are presented in Figure 4. The spectra obtained from the reaction products formed are different from the polyglycerol spectra reported hereunder, as well as in others [47]. In the spectrum of treatment (ac), where sulfuric acid and soap factors were 4.8 % w/w and 14 % w/w respectively, there is a pronounced peak in 1735 cm-1 Our hypothesis is that in these cases sulfuric acid does not act as a catalyst and becomes a reagent that forms free fatty acids with soap. These free fatty acids react with glycerol forming esters, as shown in equations 1 and 2. These chemical reactions under similar conditions have been reported to occur in previous studies [69],[70], For treatments (a), (b) and (ab), where sulfuric acid was absent (0% w/w) in the mixture, there is a C-O-C ether stretching peak in the range between 1290 to 1100 cm-1. This result may indicate glycerol oligomerization catalyzed by soaps, as previously reported [62]
In the former experimental design, all the treatments contained soap. To study the effect of the presence and absence of soap in the simulated CG sample, another experimental design was performed: where soap and sodium were the factors. The concentration of sulfuric acid was fixed at 4.8% (w/w), as with this concentration of sulfuric acid, polyglycerol was successfully synthetlzed in previous works using purified glycerol [47]. Table 4 shows the concentration of the factors analyzed (levels) and the response variable of the factorial design, which was again the hydroxyl number of the reaction product. The data reported is the average of two replicates that deviated less than 1%.
The analysis of variance (ANOVA) shows that the presence of soap as well the Interaction between sodium and soap, affect the hydroxyl number, see Table 5. The increment of soap from 0% to 14% (w/w), decreases the hydroxyl number of the reaction product from 448.58±11.64 to 318.21±4.03. In the absence of soap, the effect of sodium in the hydroxyl number Is negligible; however, when sodium and soap are present, the Interaction between these factors causes a significant effect by increasing the hydroxyl number. The FT-IR spectra of products obtained from the reactions in the absence of soap (treatment (1) and (b) presented in Table 4), are similar to the reported polyglycerol spectra [47], see Figure 5.
Table 5 Statistical analysis of the factors effect on the hydroxyl number of the reaction product.

* The factor has significant effect on the response variable (p<0.05)
On the other hand, as expected from the former experimental design the FT-IR spectrum of treatments where soap was present showed an ester peak that Is consistent with the explanation stemming from previous results.
Based on these results, it may be concluded that in the absence of soap, the reduction in the hydroxyl number of the reaction product is caused by a polymerization reaction that forms polyglycerol. The molecular weight distributions of treatments where soap was absent in the reaction (treatment (1) and (b)) using a MALDI- TOF analysis, are shown in Figure 6. Polyglycerol molecular weight distribution in absence of soap and in presence of sodium (treatment (b)) ranges between 2800 to 4100 Da. Polyglycerol molecular weight distribution in absence of soap and sodium (treatment (1)) ranges between 2700 to 4400 Da. These results are consistent with the average molecular weight of polyglycerol previously reported [47]. Results from this study suggest that by removing the soap from CG and using sulfuric acid as catalyst under the reaction conditions described in the experimental procedure section, it is possible to synthesize polyglycerol. Therefore, the bottleneck for successful polymerization of CG to produce polyglycerol is soap removal.
CONCLUSIONS
Soap and sodium are the most abundant impurities in CG and the impurities that affect the most polyglycerol synthesis because of reaction conditions. A statistical analysis using the simulated-CG as the starting monomer confirmed a significant effect caused by three factors: soap, sulfuric acid, and sodium, as well as the interaction between the first two and all the three factors on the hydroxyl number of the reaction product. The FT-IR analysis showed that when CG contains soap, changes in the hydroxyl number of the products formed were not due to polyglycerol. This is because of other side reactions between soaps and sulfuric acid (catalyst) which compete with the reaction where polyglycerol is synthesized The effect of soap and sodium in the product formed revealed that soap is the main factor inhibiting polyglycerol synthesis. MALDI-TOF analysis confirmed that polymerization of CG in the absence of soap results in polyglycerol synthesis. It is worth noting that this study was focused on the CG from biodiesel with high palmitic acid content. Consequently, further work is necessary to establish the effect of other vegetable oils or renewable sources on the CG polymerization.