1 Introducción
La combustión sin llama se da por auto-ignición del combustible, de forma tal que las reacciones toman lugar de manera distribuida en todo el volumen de la cámara de combustión suprimiendo así el frente de llama visible y concentrado, este es el modo de operación de la combustión sin llama, sin embargo esto no significa que no exista sino que se distribuye de manera uniforme por todo el volumen de la cámara de combustión de forma tal que carece de ese espectro luminoso en la longitud visible para el ser humano 1.
En la combustión sin llama, a diferencia de la convencional, las reacciones toman lugar a una temperatura por encima de la auto-ignición (temperaturas mayores a 850oC) en un gran volumen distribuido, sin que se presente un frente de llama definido. Además de no presentase una llama visible, no hay detección UV o de ionización, y lo más significativo en términos ambientales es que las emisiones de CO y N Ox son reducidas a valores muy pequeños 1. El control de la combustión sin llama depende del patrón de mezcla logrado entre el combustible, el aire y los productos de combustión, proporcionado por una gran cantidad de recirculación 2.
Dada las grandes ventajas ambientales y de eficiencia térmica presentes en el régimen de combustión sin llama, se han llevado a cabo diferentes estudios que evalúan los fenómenos fluido-dinámicos, cinético-químicos y térmicos propios de este tipo de combustión y sus variables asociadas a escala de laboratorio. En el laboratorio del grupo GASURE de la Universidad de Antioquia desarrollaron un prototipo de horno de combustión sin llama a gas natural utilizando viciado externo a partir de un motor diésel, sin embargo solo pudieron obtener llamas diluidas en régimen de alta temperatura (HiTAC) y llamas diluidas desprendidas del puerto 3. Aunque las llamas fueron estables no se logró alcanzar el régimen de combustión sin llama completamente. Posterior a esto, realizó una amplia revisión sobre los modelos de simulación usados en combustión sin llama que permitieran el diseño y posterior desarrollo de un equipo semi-industrial operando en este régimen 4. A partir de esto, se desarrolló un quemador regenerativo dual y una cámara para combustión sin llama donde se obtuvo el régimen de manera estable para una potencia de 20 kW con factores de aireación de 1.1 a 1.3 y a potencias de 25 y 30 kW con un exceso de aire de 20 %, utilizando como combustible gas natural. Además, se conservaron las características del régimen de combustión sin llama como bajos gradientes de temperatura en toda la cámara, emisiones de CO y N Ox menores a 20 ppm y 4 ppm respectivamente, además de eficiencias cercanas al 80 % 5) y (6.
Por otro lado, a nivel internacional los reconocidos autores Wünning and Wünning 7 evaluaron el efecto del régimen de combustión sin llama en la reducción de óxidos de nitrógeno vía térmica, encontrando que la formación de NO puede ser suprimida utilizando aun aire precalentado a alta temperatura, el cual en condiciones de combustión convencional genera temperaturas más altas y la posible generación de estos óxidos a través de la vía térmica. De este modo la combustión sin llama se presenta como una tecnología prometedora y segura para hornos industriales.
Veríssimo et al. 8 examinó la importancia de la velocidad de entrada del aire para lograr la combustión sin llama con un quemador de 10 kW utilizando metano como combustible y una cámara de combustión cilíndrica de cuarzo. Para ello cambio los diámetros de las boquillas de aire cambiando de esta manera la velocidad de entrada (las velocidades estudiadas van de 113.2 a 311 m/s) y manteniendo constante todos los parámetros de entrada restantes. La zona de reacción principal, tipificada por la distribución de OH en el plano de simetría de la cámara de combustión para las diferentes velocidades estaba localizada prácticamente en la misma región debido a que el flujo aerodinámico, particularmente la localización y extensión de la zona de recirculación, son análogos para todas las condiciones estudiadas. En cuanto a las emisiones de N Ox y CO estas estaban debajo de 7 ppm y 21 ppm respectivamente, independientemente del valor de la velocidad del aire, además el campo de temperatura es consistente con la zona de reacción principal identificada a través de las imágenes de OH.
A pesar de estos estudios, las condiciones de operación a las que puede ser sometido un horno operando bajo dicho régimen a nivel industrial, como puede ser el aumento o disminución de la producción no han sido estudiadas en un amplio rango. Estas variaciones generan dentro del horno un cambio en la carga térmica del mismo y por lo tanto modifican la transferencia de calor y las temperaturas de operación, siendo esta última variable un parámetro clave en la estabilidad del régimen de combustión sin llama. Por ello este estudio se enfocó en presentar y analizar los efectos de la variación de la carga térmica dentro de un horno de combustión sin llama semi-industrial de 20 kW, cambiando el fluido de simulación de carga. Para esto se utilizarón diferentes flujos de aire y una mezcla Aire-Helio como fluido de carga, de forma tal que se logró variar las condiciones térmicas dentro horno y estimar el intervalo de operación adecuado para dicho sistema.
2 Metodología
2.1 Instalación experimental
El horno de combustión sin llama desarrollado por el grupo de Ciencia y Tecnología del Gas y Uso Racional de la Energía -GASURE está conformado básicamente por cuatro componentes: un quemador autoregenerativo ubicado lateralmente y de forma horizontal, la cámara de combustión, el módulo de auxiliares y el módulo de control, ver Figura 1.
El quemador está conformado por un sistema de suministro central de aire y gas a través del cual se realizan la descarga radial de combustible cuando el horno opera en modo llama, la descarga axial de combustible para el modo de combustión sin llama y un coflujo que suministra el aire de combustión en modo llama. Adema cuenta con dos pares de boquillas de aire, que permiten la descarga y succión de manera alternada (el tiempo de conmutación es de 40 segundos), del aire precalentado y de los productos de combustión. Estas boquillas contienen unos regeneradores del tipo honeycomb permitiendo el precalentamiento del aire y el enfriamiento de los productos de combustión.
La cámara de combustión tiene una sección transversal interna de 600 x 600 mm y una longitud de 1350 mm, además el espesor del aislamento (manta ceramica y pyroblock) es de 25 mm. En el interior de la cámara se encuentran cuatro tubos de acero inoxidable que funcionan como un intercambiador de calor a contraflujo para simular la carga térmica, usando diferentes flujos de aire y una mezcla aire-helio como fluido de carga. Once termocuplas tipo K (Ni-Cr) ubicadas en la pared superior del horno permiten la medición de la temperatura en la pared superior. La pared posterior del horno cuenta con tres orificios para incetar una sonda de muestreo de temperatura y especies en el plano medio de la camara de combustión.
En el módulo de auxiliares se encuentran ubicados: el ventilador para el suministro del aire de combustión y aire de eyección, la válvula de cuatro vías para la conmutación entre los puertos de descarga y succión, el eyector para generar el vacío necesario para evacuar los productos de combustión, y el ventilador y las pipetas de helio con sus respectivos sistemas de regulación para suministrar el aire o la mezcla Aire-Helio para simular la carga térmica.
2.2 Simulación numérica
Antes de realizar la evolución experimental se realizaron simulaciones numéricas utilizando el software de CFD (Computational fluid dynamics) FLUENT 2015 con el fin de tener una idea previa de cómo será el comportamiento del régimen ante la variación de la carga. Con las simulaciones numéricas se obtuvo el perfil de temperatura y CO en el plano medio horizontal de la cámara de combustión además del factor de recirculación Kv. Las condiciones empleadas para realizar las simulaciones numéricas se presentan en la Tabla 1. Como criterio de convergencia se monitorearon los residuales de energía, continuidad y velocidad en x hasta alcanzar valores estables de 10 − 6, 10 − 5, 10 − 5 respectivamente.
2.3 Evaluación experimetal
Los parámetros usados para la evaluación experimental fueron la temperatura del fluido de carga a la entrada y salida del horno, la temperatura en la pared superior, perfil de temperatura y especies en el plano medio horizontal de la cámara de combustión, las emisiones en chimenea y la estabilidad de la combustión (la aparición o ausencia de llamas visibles).
Como carga térmica se utilizó aire con flujos de 43, 63, 83 scfm y una mezcla de aire-helio con un flujo de 82.024 scfm aire y 7.063 scfm He. Esta mezcla de aire-helio tiene un flujo másico equivalente al flujo de aire de carga de 83 cfm, el cual es de 0.047907 kg/s, teniendo así una composición de 1.18 % He y 98.82 % Aire en porcentajes másicos. Los resultados obtenidos al utilizar solo aire como fluido de carga (83 cfm) y la mezcla aire-helio se compararon para mirar cómo afecta el régimen al utilizar helio, el cual tiene un calor especifico a presión constante 5,16 veces mayor al del aire. Los flujos de aire de 43, 63, 83 scfm y la mezcla aire-helio representan una carga térmica equivalente de 11 kW, 13.93 kW, 12.96 kW y 12.13 kW respectivamente. Para cada caso evaluado la potencia térmica del horno fue de 20 kW utilizando como combustible gas natural y un factor de aireación de 1.2.
Para la medición de la temperatura en la pared superior del horno se utilizó once termocuplas tipo K localizadas al mismo nivel del aislamiento. La temperatura en el plano medio horizontal del horno fue registrada mediante una sonda de inserción a lo largo de tres líneas con seis puntos de medición cada 200 mm de la pared posterior de la cámara de combustión (pared opuesta al quemador), una línea corresponde al eje central del horno y las dos restantes se ubican a una distancia de 145 mm de la primera. La medición de las especies se realizó a lo largo del eje central del horno considerando cuatro puntos de medición cada 300 mm y empezando a una distancia de 30 mm de la pared posterior de la cámara de combustión. Estas mediciones se realizaron durante el mismo ciclo de descarga de aire y succión de productos de combustión en el quemador. Para la medición de las especies en el plano medio y en la chimenea se utilizó un analizador de gases con un sensor Infrarrojo no dispersivo para CO 2 (0-25 % vol), CH 4 (0-100 % vol), CO (0-50000 ppm), O 2 (0-100 % vol) y un analizador de N Ox de quimioluminiscencia (NO y N O 2 0-5000 ppm ± 0.01).
3 Resultados
3.1 Simulación numérica
3.1.1 Peril de temperatura Debido a la uniformidad de los perfiles de temperatura obtenidos de la simulación numera Figura 2, es posible establecer que el régimen de combustión sin llama no se ve afectado al incrementar el flujo de aire de carga de 43 scfm a 63 scfm y 83 scfm como también al utilizar la mezcla Aire-Helio, la cual representa un incremento de 4.9 % en el calor especifico del flujo de aire de 83 scfm. Dichos perfiles muestran que las zonas con mayor temperatura, a pesar de la uniformidad de esta, se ubican en la mitad de la cámara de combustión para los casos de aire 43 scfm y 63 scfm; y en el final de la cámara de combustión para el flujo de aire de 83 scfm y la mezcla Aire-Helio.
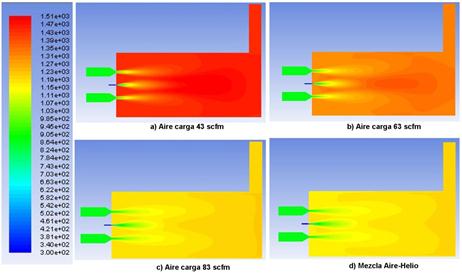
Figura 2: Perfiles de temperatura obtenidos de las simulaciones numéricas para los diferentes flujos de carga
En la Tabla 2 presenta la temperatura máxima al interior del horno, las temperaturas de entrada y salida de la carga para cada uno de las simulaciones realizadas y la eficiencia útil del horno. Se observa que la temperatura del aire de carga es mayor en los tubos superiores que en los tubos inferiores a pesar de que el factor de forma de transferencia de calor por radiación es el mismo para ambos tubos, sin embargo, el régimen de transferencia de calor por convección tiene mayor intensidad en la parte inferior, no aplicando adicionalmente el fenómeno de flotabilidad de los gases. Con respecto a la eficiencia útil, se puede afirmar que el horno opera de una manera más óptima o se obtiene una mejor remoción de calor cuando se trabaja con un flujo de carga de 83 scfm o con la mezcla Aire-helio. Si bien a mayor carga disminuye la diferencia de temperatura entre la entrada y salida de la carga, esta caída en la temperatura es compensada por el aumento del flujo másico de la carga y por ello aumenta la eficiencia útil.
Tabla 2: Temperatura máxima en el interior de la cámara de combustión y temperaturas del fluido de carga
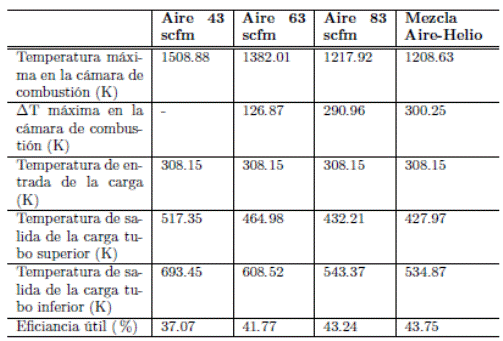
3.1.2 Peril de CO De los perfiles de especies en el interior de la cámara de combustión, solo se presenta el perfil de CO puesto que a partir de este es posible caracterizar, aunque no de manera muy exacta, la zona de reacción principal en el horno. La Figura 3 muestra que la mayor producción de CO se da alrededor de la mitad de la cámara de combustión, sin embargo existen diferencias en la distribución de dicha especie al interior del horno para cada uno de los fluidos de carga. Para el aire de carga de 43 scfm se presenta una fracción molar de CO a lo ancho y lardo de la mitad del horno, mientras que para el aire de 63 cfm esta fracción se reduce ligeramente y se alarga de forma axial en el horno, además para el aire de carga de 83 scfm y la mezcla de aire Aire-Hellio los perfiles de CO son muy similares y aunque la mayor concentración de CO se en estos casos se presenta en la mitad del horno, una considerable cantidad de CO (aproximadamente 6.33E-4) se presenta al final de la cámara de combustión, lo cual puede justificar el hecho de que en esta región se presente una alta temperatura como se mencionó anteriormente, debido a que es donde terminan de ocurrir los procesos de reacción.
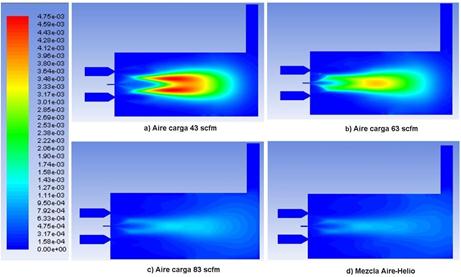
Figura 3: Perfiles de CO (en fracción molar) obtenidos de las simulaciones numéricas para los diferentes flujos de carga
De la Figura 3 es posible observar también que a medida que aumenta el flujo de carga la fracción de CO disminuye, lo cual se puede justificar por dos razones: En primer lugar al aumentar el factor de recirculación (como se verá más adelante), permite que el CO recircule y termine de reaccionar por completo. Y como segundo si bien al aumentar la carga térmica el campo de temperatura disminuye se esperaría que la reacción de oxidación del CO (CO +OH CO 2 +H) no se dé, la cual a temperaturas por debajo de los 700ºC es menos viable, esto no ocurre puesto que la temperatura en la cámara de combustión está por encima de los 1000oC.
3.1.3 Factor de recirculación Kv Una vez obtenidos los resultados de las simulaciones numéricas, se utilizó el programa REFACT desarrollado por Camilo Lezcano, Francisco J. Cadavid y Andrés A. Arrieta miembros del grupo GASURE, el cual permite determinar el factor de recirculación a partir de los resultados obtenidos con FLUENT.
La Tabla 3 muestra en forma resumida los resultados obtenidos para cada uno de los casos evaluados, en ella es posible observar que la masa de gases recirculados y por ende el factor de recirculación aumenta a medida que aumenta el flujo del fluido de carga. Este comportamiento se debe al aumento en la densidad de los gases recirculados como consecuencia de la disminución de la temperatura al interior del horno a medida que se incrementa la carga. También es posible observar que la mayor recirculación ocurre prácticamente en la mitad de la cámara de combustión, además no existe una diferencia significativa entre el factor de recirculación obtenido con el aire de carga de 83 scfm y la mezcla Aire-Helio, es decir, un aumento en el calor especifico de la carga de 4.9 % no afecta el factor Kv debido a que los perfiles de temperatura para ambos casos son muy similares.
Cabe resalta que aunque los factores de recirculación obtenidos sobrepasan el valor máximo de Kv= 10 según A.F. Colorado et al. 9, este no es un límite completamente estricto y se pueden obtener valores un poco superiores manteniéndose la estabilidad del régimen de combustión sin llama como es el caso de los resultados obtenidos en este estudio.
3.2 Resultados experimentales
3.2.1 Perftl de temperatura en el plano medio horizontal La Figura 4 evidencia que a medida que aumenta el flujo de carga, las temperaturas al interior del horno disminuyen. Al aumentar 1.4 y 1.9 veces el flujo de carga con respecto al aire de carga de 43 scfm se observa que la temperatura promedio a lo largo del eje central disminuye 66.08oC y 114.74oC respectivamente (ver Tabla 4). Mientras que al mantener un flujo másico igual al del flujo de carga de 83 scfm (0.0479 kg/s) pero aumentando el calor especifico 4,9 % gracias a la mezcla aire-helio, se obtienen valores de temperatura muy similares a los obtenidos con el flujo de 83 cfm y una disminución de la temperatura ligeramente mayor en el último tramo del horno, con lo cual se puede decir que un incremento en el calor especifico del 4.9 % en el fluido de carga no genera un cambio significativo en la temperatura interna del horno.
En cuanto a la obtención del fenómeno de combustión sin llama, este se mantuvo a pesar de la variación de la carga térmica, no solo por la no presencia de llamas visibles, sino también por el perfil de temperatura al interior del horno.
Como puede observarse en la Figura 4, estos perfiles presentan un alto grado de uniformidad, debido a que no se presentan grandes diferencias de temperatura entre los puntos medidos en la cámara. Es importante resaltar que designar un campo térmico como uniforme puede ser un concepto subjetivo de cada autor, por ejemplo G. Szegö et al. 10 en sus estudios reporto un alto agrado de uniformidad con la presencia de una diferencia máxima de temperatura menor a 150oC, por otro lado Y. Tu et al. 11 y Weber et al. 12 presentaron en su estudio de combustión sin llama que las temperaturas de los gases de combustión en todo el interior del horno estaban entre 1300-1500oC, es decir, se tenía un gradiente de 200oC. Con base en estos criterios los perfiles de temperatura medidos en el eje central de la cámara de combustión para cada uno de los casos estudiados son uniformes puesto que la diferencia entre la temperatura más alta y la más baja a lo largo del eje central no sobrepasó los 200oC como se detalla en la Tabla 5
Tabla 5: Temperaturas máximas y mínimas registradas a lo largo del eje central de la cámara de combustión
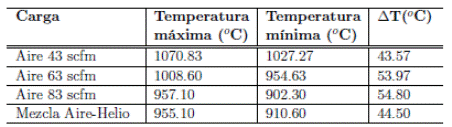
3.2.2 Factor de uniformidad térmico Rtu Para tener una mayor certeza de la uniformidad de la temperatura se calculó el Factor de Uniformidad Térmica Rtu propuesto por Y. Weihong et al. 13 mediante la Ecuación (1)
Donde Ti (K) representa la temperatura medida en cada punto de la cámara que en este caso corresponde a cada uno de los puntos medidos en los tres ejes de la cámara de combustión y los puntos medidos en la pared superior y T¯(K) es la temperatura media en el horno. Si Rtu es igual a cero no hay un gradiente de temperatura en el interior de la cámara, es decir, la temperatura de la cámara es exactamente igual en todos los puntos, mientras que si existen diferencias muy grandes en los diferentes puntos de la cámara el valor de Rtu tiende a ser grande.
Rafidi (2005) 14 encontró un Rtu de 1.1 para condiciones de una llama de combustión convencional y 0.33 para un experimento en condiciones de HiTAC, la cual ha referido como un campo de temperatura uniforme. De acuerdo con este criterio y los valores del factor de uniformidad térmica calculados que se reportan en la Tabla 6, los campos de temperatura en la cámara de combustión se pueden considerar uniformes, puesto que los valores de Rtu no sobrepasan el valor de 0.33, estando entre 0.15 y 0.20.
Tabla 6: Coeficiente de uniformidad térmica Rtu medido a partir de las temperaturas registradas en el plano medio y en la pared superior del horno
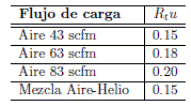
En la Tabla 6 se puede observar que a medida que aumenta el flujo de carga el factor Rtu se va alejando del valor “ideal” de uniformidad que es cero. Cabe resaltar que los factores de uniformidad térmica para un flujo de carga Aire-Helio y flujo de carga de 43 scfm son similares debido a que el primero solo fue posible calcularlo con los valores de temperatura registrados en la pared superior y en la línea central del horno.
Perftl de especies En la Figura 5 se presenta la concentración de CO 2, CO, O 2 y NO (la concentración de CH 4 y N O 2 medido fue de 0 % y 0 ppm respectivamente) a lo largo del eje central de la cámara de combustión. Los perfiles de especies obtenidos no muestran un patrón característico y no permiten determinar con certeza si el aumento en el flujo de carga aumenta o disminuyen cierto tipo de especies. Los únicos comentarios que son posibles realizar a partir de los comportamientos que se muestran en la figura son los siguientes:
Se puede apreciar que para los casos de aire de carga de 63 scfm y 83 scfm, el máximo pico de CO 2 se obtiene en la mitad de la cámara de combustión.
A partir del grafico del CO para un aire de caga de 43 scfm se puede observarse que una fuerte reacción de oxidación se dan en los primeros 450 mm de la cámara, lo cual concuerda con los perfiles de temperatura obtenidos donde las temperaturas mayores se registran alrededor del segundo tercio de la cámara de combustión. Además para todos los casos se obtuvo una oxidación completa del combustible con valores de CO por debajo de 50 ppm y 0 % de CH 4 en la parte final de la cámara, esto debido por un lado a las altas corrientes de recirculación producidas en el régimen de combustión sin llama que aumentan el tiempo de residencia de los gases y por otro lado a la alta turbulencia que mejora el mezclado dentro de la cámara.
El porcentaje de oxígeno disminuye a medida que aumenta la distancia al quemador gracias a las corrientes de recirculación de la mezcla tripartita que permite que este se diluya, permaneciendo por debajo del 8 %, lo que garantiza que se conserve el régimen de combustión sin llama bajo todas las condiciones experimentales empleadas.
En cuanto a las emisiones de NO a medida que aumenta el flujo de carga estas disminuyen, ya que una de las fuentes de formación de NO son las altas temperaturas.
Es importante resaltar que las fluctuaciones en las concentraciones de especies no solo se deben a la conmutación de cada ciclo de regeneración, a pesar de que estas fueron medidas en un ciclo determinado, sino también a la turbulencia inducida por la recirculación interna de los gases de combustión, la cual genera variaciones en las tasas de reacción.
3.2.4 Emisiones chimenea En la Figura 6 presenta la concentración de las distintas especies en los humos evacuados por la chimenea. La concentración de CH 4 y N O 2 no se muestra porque en todos los casos el analizador de gases reportó un valor de 0 % y 0 ppm respectivamente. Las bajas emisiones de CO (por debajo de 30 ppm) y la no presencia de CH 4 es una señal de que el combustible se está quemando completamente y que el horno opera en forma estable bajo el régimen de combustión sin llama. Es posible observar que a medida que aumenta el flujo de carga las emisiones de CO disminuyen, por ejemplo para los flujos de 63 y 83 scfm se obtuvo una reducción con respecto al flujo de 43 scfm del 31.3 % y 33.7 % respectivamente. Este comportamiento llama la atención puesto que es de esperar que un enfriamiento de la zona de reacción ocasione que la conversión de CO en CO 2 no se lleve a cabo por completo aumentando las emisiones de CO, sin embargo estos resultados pueden deberse al aumento en el factor de recirculación como lo mostraban las simulaciones numéricas, el cual ayuda a aumentar el tiempo de residencia y a que el CO reaccione por completo. En cuanto a las emisiones de CO 2 y O 2 estas no presentan una variación significativa, por lo cual se puede decir que la variación en la carga tiene un efecto despreciable sobre estas especies. El porcentaje de O 2 estuvo entre 3.8-4.2 % lo cual asegura un factor de aireación de 1.2.
Las bajas emisiones de NO obtenidas durante la experimentación bajo el régimen de combustión sin llama se deben a los gases de combustión recirculados, los cuales disminuyen la concentración de oxígeno y la temperatura en la zona de reacción, evitando de esta manera la formación de N Ox por la vía térmica. Además se puede evidenciar que a mayor flujo carga menores son las ppm de NO, debido que a que el flujo de carga ayuda también a enfriar la zona de reacción evitando la formación de N Ox por las altas temperaturas.
3.2.5 Balance de energía En el diagrama de la Figura 7 es posible observar que gran parte de la energía es absorbida por el fluido de carga, entre un 55-67 % del total de la energía que sale del sistema, debido a que en el régimen de combustión sin llama se tiene una zona de reacción amplia y uniforme en temperatura, con lo que se incrementa el flux de calor hacia la carga permitiendo una mayor remoción de calor.
Por otro lado es posible observar que las pérdidas de energía por las paredes disminuyen a medida que aumenta el flujo de carga pasando de 4.42 kW para un flujo de 43 scfm a 2.89 kW para un flujo de 83 scfm, debido a que la temperatura de las paredes tiende a disminuir. Un comportamiento similar ocurre para las pérdidas de energía por los gases de chimenea, las cuales están asociadas al calor sensible de los gases, esta perdidas disminuyen a medida que aumenta el aire de carga pasando de un valor máximo de 2.26 kW para un flujo de carga de 43 scfm a un valor mínimo 1.55 kW para la mezcla Aire-Helio, lo cual representa una disminución del 31.4 %, debido a que el aumento en el flujo de carga tiende a remover más energía de los productos de combustión que recirculan y que salen por la chimenea.
Las pedidas por combustión incompleta y vaporización del agua en los productos de combustión son relativamente bajas, entre 2-3 % para cada caso, debido la baja cantidad de ppm de CO en las emisiones. Además estas pedidas no difieren mucho entre cada uno de los casos evaluados. En cuanto a las pérdidas por los gases eyectados, es decir los productos de combustión que pasan por los regeneradores del quemador (honeycomb), pasan de representar un 2 % de la energía total que sale del sistema para los casos de aire de carga de 43 y 63 scfm a representar solo 1 % para los casos restantes, este bajo porcentaje de perdidas energéticas se debe a que los regeneradores cumplen una función adecuada de absorber el calor de los gases eyectados para posteriormente entregar esta energía al aire de combustión entrante.
Cabe resaltar que la energía que sale del sistema denominada como “Otras perdidas” corresponde a las pérdidas no contabilizadas por fugas en el sistema y por las pérdidas de calor en las paredes horizontales del horno.
En la Figura 8 puede observarse el comportamiento de la eficiencia útil del horno ante la variación de la carga térmica. Cuando el aire de carga se incrementa de un flujo de 43 scfm a 63 scfm la eficiencia útil presenta un incremento de 14.71 puntos porcentuales, sin embargo, después de aumenta la carga de 63 scfm a 83 scfm la eficiencia útil presenta una disminución de 4.88 puntos porcentuales, la cual sigue decreciendo ligeramente al utilizar la mezcla Aire-Helio. Con respecto a este último caso al aumentar la cantidad de flujo de carga y mantener la potencia térmica constante, la energía aportado por el flujo de combustible no es lo suficiente para calentar de manera rápida el fluido a pesar del aumento en el calor específico de este y por ello se obtiene la menor eficiencia útil de los cuatro casos evaluados. Con base en estos resultados se puede decir que el punto donde se obtiene la mayor eficiencia útil en el horno se encuentra entre una carga térmica de 43 y 83 scfm de aire.
4 Conclusiones
El aumento en el flujo del aire de carga de 43 scfm a 63 y 83 scfm ocasiona que las temperatura promedio a lo largo de la eje central del horno disminuyan 66.08oC y 114.74oC respectivamente, además un incremento del 4.9% en calor especifico del fluido de carga de 83 scfm (mezcla Aire-Helio) no genera un cambio significativo en la temperatura interna del horno. A pesar de esta disminución en la temperatura se obtuvieron perfiles de temperatura uniformes a lo largo del eje central y en la pared superior del horno; además de un factor de uniformidad térmica por debajo de 0.33 que es lo que recomiendan algunos autores.
Aunque los gradientes de temperatura en el interior del horno son pequeños dada la uniformidad del perfil de temperatura, las mayores temperaturas para los casos donde se tiene un aire de carga de 43 y 63 scfm se encuentran en la mitad de la cámara de combustión, es decir, en este lugar se encuentra la mayor cantidad de volumen de la zona de reacción y por tanto donde se libera la mayor cantidad de calor. Mientras que para los casos donde la carga es la mezcla Aire-Helio y 83 scfm de aire las mayores temperaturas se concentran en el último tercio de la cámara de combustión.
El punto donde se obtiene la mayor eficiencia útil se encuentra entre un flujo de carga 43 y 83 scfm, es decir cuando se tiene una remoción de calor entre 11 kW y 12.96 kW respectivamente. Además a partir de los resultados de la eficiencia útil del horno es posible afirmar que esta no tiene un comportamiento lineal al aumentar la carga puesto que el tiempo de residencia de esta última al interior del horno es también es un factor clave para que se obtenga una remoción de calor adecuada.
Las pérdidas en las paredes disminuyen al aumentar la carga puesto que al disminuir el campo de temperatura en la cámara de combustión, disminuye la temperatura interna de la pared y con ello la temperatura de la pared exterior. Sin embargo, las pérdidas en las paredes tienen valores considerables, entre 14 % y 22 %, lo cual conduce a que hay que realizar una revisión del estado del aislamiento del horno.
Adicionalmente se puede concluir que la capacidad que tiene el horno de operar en un régimen de combustión sin llama estable a pesar de la variación en la carga térmica, lo hace un equipo apropiado para algunos tratamientos térmicos del sector metalmecánico donde la producción (carga térmica) varía de acuerdo a la demanda del mercado, dichos tratamientos térmicos icluyen el temple, revenido y recocido de acero inoxidable y temple y revenido austenítico de hierro.
Agradecimientos
Los autores agradecen a Colciencias por la financiación del Programa Nacional de Investigación e Innovación en Combustión Avanzada de Uso Industria-Incombustiòn, proyecto "Desarrollo y Evaluación de un Quemador de 5 kw que Opere en el Regimen de Combustión Sin LLama y Que Emple como Combustible Carbón o una Mezcla de Este con Gas Natural", de cuyos resultados es el presente artículo. También al Programa de Sostenibilidad 2016-2017 grupo GASURE, de la Vicerrectoria de Investigación de la Universidad de Antioquia.