1. Introduction
China has achieved leading technical levels in the mining of medium and thick coal [1], but there are still difficulties in mining thin coal and complex coal seams. These seams have limited mining space, and manual operations are difficult, leading to low mining efficiency and insufficient economic returns, resulting in the abandonment of thin coal seams [2,3]. Thin coal seams contribute only 10.4% to the total output of coal mining [4], and their mining conditions are depicted in Fig. 1.
Thin coal seams often contain hard concretions, leading to significant stress changes in the coal seam during mining. The distribution of stress affects the collapse patterns of coal and hard concretion. By studying the rules governing coal stress changes and the forms of hard concretion breakdown when cutting teeth act on different positions of the hard concretion, it is possible to reduce energy consumption during the cutting process and minimize the impact of hard concretion on cutting teeth. This can improve the stability and reliability of coal mining machines, and has important academic significance and engineering implications. Therefore, scholars both domestically and abroad have conducted extensive research on this topic.
British scholars Evans et al. [5,6] have researched the sharp knife cut tooth broken rock theory and passivation of the knife cut teeth rock damage theory. They proposed that the pick applies compressive stress on the surrounding coal and rock, forming an arc fracture line with the increase of compressive stress, which then causes tensile failure of coal and rock. They obtained the mechanical model of peak cutting force during coal and rock fracture. Wang QK [7], a former Soviet Union scholar, elaborated on the theory of coal breaking by shearer and experimentally verified it. Liu [8] proposed the accumulation algorithm covering the total number of curve boxes, and clearly defined the physical meaning of evaluating the fractal dimension and other characteristic quantities of the cutting resistance curve. Wang [9] conducted a simulation of cutting coal walls using a self-made test bench and monitored the cutting force. Turkish scholar Yilmaz et al. [10] predicted the cutting force of hard rock cut by the pick, establishing the relationship between cutting force and various factors. They also provided the calculation method and theoretical formula of hard rock cutting force for a crushing compressive strength of the pick ranging from 85 to 180 MPa. Wang [11] developed a coal-rock cutting experimental platform and collected stress data from the roof and floor. Bakar [12] simulated the process of cutting coal and rock using shearer teeth, while Luo [13] established a mechanical model for cutting homogeneous coal strata and coal-bearing rock sections with pick cutters and roller rotators.
Due to the complexity of shearer cutting technology and the challenging working environment, it is difficult to conduct underground experiments. However, numerical simulations are low-cost and can generate multiple sets of data in a short period, making them easy to perform. Therefore, they provide a basis for studying the stress distribution law of coal rock with hard concretion fractures.
Zhao and Dong [14] conducted simulations of three loads of drum shearer using ADAMS and verified the results with theoretical formulas. He [15] used LS-DYNA to simulate the coal breaking process of the drum shearer and analyzed the relationship between the dynamic change of the plastic domain of coal seam and stress distribution. Wyk [16] performed a finite element analysis by comparing the cutting process of picks with different shapes, while keeping the cutting speed of the coal seam constant, and found that the stress of the picks is affected by the feed force and the tool wear history. Zhang [17] used FLAC3D to analyze the stress distribution of coal and rock under different mining rates and concluded that the stress distribution of coal and rock exhibits a two-stage characteristic, with the maximum concentration value acting as the cut-off point. Liu [18] utilized the finite element method to investigate the stress distribution of coal seams under the influence of picks with different structural parameters. Zhou [19] established a coal-rock coupling model of the spiral drum using LS-DYNA software under complex coal seam conditions and analyzed the stress of broken gangue coal and rock. Liu [20] established a coupling model of a screw drum for cutting gangue coal and rock using LS-DYNA, and studied the variation in the maximum stress of coal and rock under different kinematic parameters. Liu [21] simulated the process of a disc cutter crushing coal and rock using ABAQUS and analyzed the stress distribution of coal and rock under different cutting thicknesses. Menezes et al. [22] utilized the finite element method to simulate the interaction between the cutter and rock. They investigated the cutting process of rock with different cutting depths and speeds and derived the rock breaking law. Wang [23] employed ABAQUS to simulate the rock breaking process of hob crushing coal and rock. He analyzed the stress changes of coal and rock under various kinematic parameters. Liu [24] calculated the elastic energy based on SHPB dissipation energy, studied the energy release characteristics of coal and rock under different initial stress levels and strain rates, and explored the impact of energy release on rock breakage.
The scholars mentioned above have used different methods to simulate the cutting process of picks and have obtained reliable data and conclusions through analysis. This verifies that the numerical simulation method is effective in simulating the coal breaking process, thus laying a foundation for the study of the stress distribution law of coal with hard concretion broken by picks.
In addition, numerous studies have been performed on homogeneous coal rocks, while only a few scholars have researched stratified coal rocks. In the mining of thin coal seams, the equipment is more affected by induration, which impacts its reliability. If we can define the grid and contact problems of hard concretion and coal seam reasonably, simulate various cutting conditions, and analyze the stress of the hard concretion coal seam when it breaks, it will aid in reducing energy consumption during the cutting process, minimizing impact, and ultimately enhancing the reliability of the entire machine. This has great theoretical guiding significance for efficient and environmentally friendly mining of hard concretion coal.
2. Establishment of 3D model for cutting hard concretion coal with pick
2.1. Determination of mechanical parameters of hard concretion and coal
To ensure the accuracy and reliability of the numerical simulation results, it is important to consider the impact of coal and concretion properties, as well as the shape and size differences of hard concretions when establishing the coal seam model. In this study, samples of coal from the 17th layer of Yangcun Mine in the Yanzhou mining area, Jining City, Shandong Province (China), were collected and tested for their physical and mechanical properties. The results are presented in Fig. 2, and the physical and mechanical property parameters of coal and hard concretion are summarized in Table 1 and Table 2, respectively.
2.2 Establishment of hard concretion coal model
The UG tensile sketch command was used to construct a coal seam with a height of 1200mm and a drum with a diameter of 800mm. A rotary sketch was used to construct a U95 pick and an ellipsoid-shaped hard concretion with a triaxial length of 200mm×150mm×150mm, respectively. Finally, the individual parts of the structure were assembled, resulting in the 3D model of the hard concretion coal being cut by a single pick, as illustrated in Fig. 3.
3. Model mesh preprocessing based on Hypermesh
We imported the aforementioned 3D model in STEP format into the Hypermesh software, and used solid map to create drum mesh, and tetra mesh to obtain pick holder, pick and alloy head mesh. Then, we selected appropriate unit sizes to ensure accurate depiction of geometric features.
To analyze the stress distribution of hard concretion coal, it is necessary to consider the contact between hard concretion and coal seam in the finite element analysis. In order to analyze the internal contact between multiple parts, we treated them as a common grid. At the same time, mesh quality has a significant impact on simulation results. During the process of pick breaking of hard concretion coal and rock, the instantaneous load of the pick and the coal and rock will increase sharply when they collide, and the stress and strain of coal and rock are nonlinear, time-varying, and strongly coupled [25]. Therefore, the quality of the coal and hard concretion mesh affects the accuracy of the analysis. Traditional tetrahedral mesh has low quality, is difficult to converge, and has a large discretization error. Hexahedral grid calculations are more accurate, controllable, and less prone to negative volumes. Therefore, we divided coal and hard concretion into hexahedral grids.
To ensure accurate grid generation, the coal is initially sliced into 1/8 segments along the x, y, and z directions, followed by geometric cleaning to remove any redundant boundaries that may affect grid generation. In Hypermesh, the mapping technique is used for hexahedral mesh division, which requires the segmented coal to be split into mapping segments. The hard concretion is initially selected according to the "from difficulty to simplicity" principle after the model analysis. The geometric model of the hard concretion body resembles an ellipsoid shape. To create the model, a cuboid is constructed with 1/4 of the length and width of the ellipsoid as its center, after which it is cut into 1/8 of the ellipsoid’s size. Using the ‘trim with surface’ technique, a portion of the cuboid is separated from the ellipsoid’s body. Next, the 1/8 ellipsoid is divided into trim nodes, as shown in Fig. 4.
Clicking Merge selected adjacent tetrahedral regions and merged them. Once completed, the mapped sections should be visible in the Mappable view. Then, Select the mapped sections and set the unit size to 5.0 before clicking the Mesh button. To restore 1/8 coal to the entire coal, use the Reflect button as indicated in Fig. 5. To complete the joint of coal and hard concretion, preview edges and tolerance values are selected at 0.1 of the element size.
This method results in a model comprising of 5 parts, with 200,146 nodes, and 175,408 solid elements, as illustrated in Fig. 6.
4. Establishment of LS-DYNA coal-breaking simulation model
4.1. Model freedom constraint setting
To ensure that the boundary nodes of the coal and hard concretion model have zero displacements in all six degrees of freedom, the *SET_NODE command was used to define a NODE group consisting of the two sides, upper and lower surfaces, and the back surfaces of the coal. Then, the coal boundary conditions were set on *BOUNDRY_SPC_SET with 6 degrees of freedom [26].
4.2 Non-reflective boundary setting
Using a fixed boundary for the coal model has a disadvantage. When the reflected stress wave reaches the fixed boundary, the coal elements are subjected to a reflected wave and a shear wave that are not consistent with the actual situation. To address this, the other five faces of the coal except for the cut face are designated as a *segment set. Then, a non-reflective boundary condition is applied to the set node group using the *BOUNDARY_NON_REFLECTING keyword to eliminate this effect.
4.3. Setting of wall materials containing hard concretion
The mechanical parameters of coal and hard concretion, as listed in Tables 1 and 2, were used for the Drucker-Prager model for simulating the plastic constitutive relationship of coal wall with hard concretion [27-30].
4.4. Pick type pick alloy head contact setting
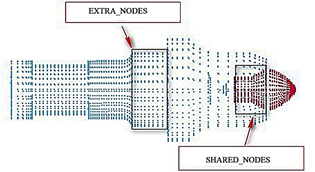
Source: Simulation acquisition, 2022.
Figure 7 Shared nodes of the pick and alloy head SHARED-NODES.
Considering that the simulation model primarily analyzes the stress of coal, the pick holder and pick body are designated as rigid bodies, whereas the alloy head is considered a flexible body. This makes it a rigid-flexible coupling problem. The node located on the contact surface of the pick and pick holder is fixed to the pick holder using the keyword *CONSTRAINED_EXTRA_NODES. The common node method is used to connect the alloy head and pick body using *SHARED_NODES, as illustrated in Fig. 7.
4.5. Contact setting of coal
In this experiment, the roller’s operation efficiency was improved by attaching the pick and pick table as a rigid body. As a result, the model needs to define two contact modes: erosion contact between the pick and the hard concretion coal, and binding contact between the hard concretion and the coal. To do this, the *CONTACT_ERODING_SURFACE TO SURFACE command should be used, with the pick and coal as the primary and secondary elements, respectively. The dynamic friction coefficient for both is set to 0.01, and the static friction coefficient is set to 0.55.
To output the contact interface cloud picture of the pick, the SPR and MPR control options for the output of the master and slave slices of the contact need to be enabled. Additionally, the *EROSOP internal erosion option should be turned on, as shown in Fig. 8.
To account for the actual connection between coal and hard concretion, a contact between the hard concretion complex and coal is established. To do this, use the *CONTACT_TIEBREAK_SURFACE TO SURFACE command, with the primary element set to coal and the secondary element set to hard concretion. The THKOFF option should be turned on to control the offset of the surface elements, as described in [31]. The other parameter settings should be consistent with those used for the erosion contact card, as shown in Fig. 9.
4.6. Setting of kinematic parameters of the roller
During actual operation, the roller should rotate and translate simultaneously. For instance, the Yanzhou Mine MG2*70/325-BWD shearer has a drum speed of 90r/min and a traction speed of 3m/min. The *BOUNDARY-MOTION -RIGID command should be used to define the drum’s movement and rotation speed.
4.7. Output solution control
Based on the size of the hard concretion coal model and the kinematic parameters of the roller, the *CONTROL_ TERMINATION value is set to 0.2. The energy control card is configured to include hourglass energy and slip energy calculation. To ensure accurate results, the average hourglass energy should not exceed 10% of the total energy, as recommended in [20].
5. Analysis of simulation results
5.1. Stress variation law of coal and hard concretion
Due to the feeding speed of the shearer and the size of the pick, it was not possible to reach the back end of the hard concretion in actual working conditions. Therefore, the simulation only studied five positions of the pick acting on the front end of the long axis of the concretion body, namely 1/10, 1/5, 3/10, 2/5 and 1/2, corresponding to points A, B, C, D and E in Fig. 10.
For example, when cutting hard concretion at point C (b), click on the Effective Stress tab in the Fringe Component to view the Effective Stress cloud. At t 1=0.027s, the pick begins to cut the coal, and when the surface stress value reaches 6.277MPa stress, the element fails. At this point, the hard concretion has not been touched, so the surface stress is almost 0, as shown in Fig. 11(1). At t 2=0.074s, the pick completely enters the coal, and the local stress value reaches 178.9MPa due to the large area collapse of internal units of the coal, as shown in Fig. 11(2). At t 3=0.100s, the cutters cut above the hard concretion, and the coal unit was subjected to 166.0MPa stress. As the upper surface of hard concretion is extruded by the plastic deformation of the coal element, the hard concretion is subjected to 79.60MPa stress, as illustrated in Fig. 11(3). At t 4=0.115s, the pick acts on the inside of the hard concretion, and the maximum stress value of the coal unit is 59.23MPa due to the extrusion of the hard concretion. The hard concretions were locally broken and subjected to 86.84MPa stress, as shown in Fig. 11(4). At t 5=0.145s, the pick cuts out from the concretion body and destroys the compacted core, while the uncut hard concretion remains in the coal. At this time, the maximum stress value of the coal unit is 78.06MPa, and the maximum stress value of the hard concretion unit is 92.37MPa, as illustrated in Fig. 11(5).
Select the analysis element in the history menu and set the value to the maximum. Then, click on the coal and hard concretion to obtain the time history curve of the extreme effective stress of both materials (refer to Fig. 12). Based on the schematic diagram in Fig. 10(b) depicting the cutting stage, it can be observed that the entire cutting process can be divided into four stages: (Ⅰ) between 0s and 0.027s, the pick does not touch the coal, and the stress value remains at zero; (Ⅱ) from 0.027s to 0.100s, the stress curve undergoes significant changes due to the continuous extrusion and breakage of the coal element; (Ⅲ) at 0.100s, the stress curve of coal decreases while the stress value of hard concretion increases sharply because of the compacted core in the extruded coal seam; and (Ⅳ) at 0.145s, the pick is cut from the inside of the hard concretion, marking the completion of the entire cutting process at 0.200s.
Open the RCFORC item in the ASCII TAB and click on Contact1 to view the cutting force curve as depicted in Fig. 13. Once the pick started cutting the coal, the cutting force remained stable at around 20kN. As the pick entered hard concretion from coal, the cutting force experienced a sudden increase, and the maximum cutting force reached 166kN.
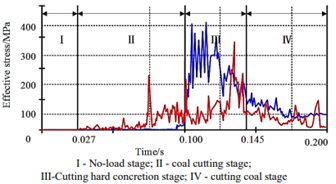
Source: Simulation acquisition, 2022.
Figure 12 Time history curve of the maximum effective stress in the hard concretion coal.
5.2. Study on the influence of cutting location parameters on coal stress peak
The coal stress cloud map was examined using d3plot, which showed that the maximum stress experienced by coal during the cutting process was 129.36MPa when cutting 1/10 of the hard concretion. Cutting 1/5 of the hard concretion resulted in a maximum stress value of 256.60Mpa for coal. Cutting 3/10 of the hard concretion resulted in the maximum stress value of coal and concretion during the cutting process, which was 361.64MPa. Cutting 2/5 of the hard concretion resulted in a maximum stress value of coal during the cutting process of 659.98MPa. Cutting half of the hard concretion resulted in the maximum stress value of coal during the cutting process of 673.08Ma. Based on the stress cloud map obtained, it can be seen that hard concretion will break when the pick cuts at A, B and C, while hard concretion will be cut off from coal when the pick cuts at positions D and E. Fig. 14 shows that the stress peak increases as the cutting position approaches point E (1/2) on the hard concretion.
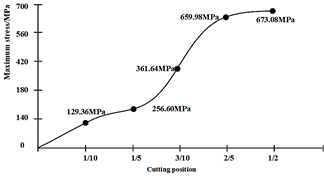
Source: Simulation acquisition, 2022.
Figure 14 The maximum effective stress of the hard concretion.
6. Experimental verification
6.1. Deployment of hard concretion coal model based on the similarity theory
To validate the LS-DYNA simulation of the coal breaking process and uncover the accuracy of the stress variation law of hard concretion coal under pick action, a similarity model of hard concretion coal was created using the similarity theory. The physical and mechanical properties of the hard concretion coal used in the experiment were designed to be similar to those of actual coal rock by analyzing the main parameters in the MLT dimensional system, as shown in Table 3.
Based on the dimensional indices listed in Table 3, a rank 3 coefficient matrix was obtained by eliminating linearly correlated parameters:
Since coal and hard concretion share the same parameters and dimensions, the basic quantity L was chosen, and the resulting dimensionless quantities are G, ρ, L.
By using Eq. (1):
Similarly, using Eq. (2):
By applying the corresponding values of each parameter for hard concretion coal, the similarity criterion can be calculated using Eq. (3):
According to the first principle of similarity, the similarity index of a similarity phenomenon is 1, and the mathematical expression of similarity coefficients can be obtained as shown in Eq. (4):
The geometric similarity ratio is determined based on the occurrence conditions of coal and the working environment of the project laboratory, C L = 1/5. The material density can be controlled around 1050 kg/m 3 - 1100 kg/m 3, so C p = 0.83. According to formula (4) and the dimensional matrix, the parameters whose similarity coefficient is 0.166 are: σ m ; σ y ; E m ; E y ; C m ; C y . The parameters whose similarity coefficient is 0.83 are ρ m and ρ y , and the parameters whose similarity coefficient is 1 are φ m and φ y . The firmness coefficient f of coal and concretion mass is related to its compressive strength σ, and the relationship that satisfies it is indicated in Eq. (5):
The parameters of the similar experimental coal model are shown in Table 4.
Based on the derived parameters, the ratio of sand, cement and gypsum was adjusted to 5:1.5:0.3 to simulate coal, while the ratio for simulating hard concretion was adjusted to 5:0.7:0.3. Water was then added and stirred with the material in a weight ratio of 9:1 to create the coal model, as shown in Fig. 15.
Table 4 Physical and mechanical properties of similar coal wall models.
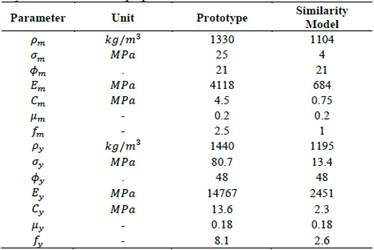
Source: Simulation experiment Acquisition, 2020.
6.2. Cutting experiment verification
A cutting test bench is constructed based on the similarity principle and the requirements of the cutting experiment, as illustrated in Fig. 16. The experimental process of cutting coal that contains hard concretions using a shearer is presented in Fig. 17, while Fig. 18 shows the resulting coal model after cutting.
The experiment measured the torque curve, as shown in Fig. 19. The torque peaks during cutting of coal and hard concretion were T 1=2.6N·m and T 2=18.6N·m, respectively.
Based on the structural size and transmission ratio of the reducer, the peak cutting forces of the cutter for coal and hard concretion were calculated to be 141.5N and 1026.6N, respectively. According to the similarity criterion, the peak cutting force and hardening force values obtained from the cutting force curve (Fig. 13) were multiplied by the similarity coefficient of 1.66×105N and 2×104N, respectively, resulting in multiplication coefficients of 132.8N and 1102.2N. The relative error rate between the experiment and simulation was less than 7%. It can be concluded that LS-DYNA accurately simulated the coal breaking process and revealed the stress change rule of coal with hard concretion under the action of the pick.
7. Conclusions
1. The hexahedral mesh for the hard concretion and coal was divided using the Hypermesh software, creating a common grid that serves as the foundation for accurately calculating the simulation model in LS-DYNA.
2. LS-PREPOST was utilized to simulate the cutting process of a single pick and reveal the stress change rules of hard concretion coal under the pick’s action. Results show that when the pick is at 1/10, 1/5 and 3/10 of the long axis of hard concretion, hard concretion will break, and the coal’s peak stress is 129.36MPa, 256.60MPa and 361.64 MPa respectively. When the pick is at 1/2 and 2/5 of the long axis of hard concretion, hard concretion will be cut off, and the stress peak is 659.98MPa and 673.08MPa, respectively. The closer the pick is to the center of the long axis of hard concretion, the greater the stress peak.
3. Based on the similarity theory, a coal-containing test was conducted, and an experiment was carried out on the single pick test bench. The cutting force curve obtained from the experiment was compared to the simulation results. The relative error between the two was less than 7%. Thus, LS-DYNA’s ability to accurately simulate the coal breaking process is demonstrated.