Introducción
La distribución en planta incide directamente en el uso eficiente de los recursos y guarda una relación con los costos y los tiempos de entrega de los productos elaborados (Ahmadi, Saman, Reza & Jokar, 2017); por tanto, establecer nuevas alternativas de distribución representa un aporte al desempeño de las organizaciones (Ahmad, Basir & Imam, 2006; Fafandjel, Rubeša & Matulja, 2009; Tompkins, White, Bozer & Tanchoco, 2011) .
La distribución en planta busca que todas las áreas de una instalación tengan los espacios necesarios para el desarrollo de las actividades que forman parte del proceso productivo, incluyendo el equipo y el personal operativo (Muther, 1970). Su principal objetivo es crear un sistema de producción ordenado que elabore productos de alta calidad y a bajo costo; representa la integración de arreglos físicos que incluye máquinas, materiales, departamentos, estaciones de trabajo, áreas de almacenamiento y otras áreas comunes para buscar una producción más eficiente (Maniya & Bhatt, 2011; Muther & Hales, 2015).
El problema de distribución de planta ha recibido gran atención por diferentes investigadores en la última década (Azadeh & Izadbakhsh, 2008; Drira, Pierreval & Hajri-Gabouj, 2007; Hosseini-Nasab, Fereidouni, Fatemi-Ghomi & Fakhrzad, 2017; Ingole & Singh, 2017; Leyva, Mauricio, Salas-Bacalla & Bacalla, 2016; Lin, Liu, Wang & Liu, 2013; Pourvaziri & Naderi, 2014). La generación y evaluación de diseños de planta a menudo se considera una tarea difícil, que consume muchos recursos (Ali-Naqvi, Fahad, Atir, Zubair & Shehzad, 2016).
Se consideran diferentes tipos de problemas de distribución de planta, según la característica del producto, tales como por procesos, por producto, de posición fija y células de trabajo (Leyva et al., 2016). De estos, una distribución por procesos se diferencia de los otros tipos porque permite a la organización mantener una mayor flexibilidad con relación a la variedad de productos. Sin embargo, representa un problema complejo al ser combinatorio (NP-Hard).
Dada la complejidad del diseño de distribuciones de planta en entornos por procesos, es importante proporcionar un soporte que facilite la obtención de una solución de manera oportuna (Atieh, Kaylani, Almuhtady & Al-Tamimi, 2016).
Para abordar los problemas generales de distribución de plantas por procesos y su complejidad, se han empleado comúnmente dos tipos de técnicas de solución que permiten satisfacer los requerimientos de este entorno: las técnicas de optimización exacta y las técnicas aproximadas.
Las técnicas de optimización exacta se emplean para problemas de mediano tamaño con optimización combinatoria, o para problemas más grandes con transformaciones continuas (Zhou, Love, Teo & Luo, 2017). Otros trabajos con optimización exacta se encuentran en Amaral (2006, 2008) .
Las técnicas aproximadas que no garantizan solución óptima, pero arrojan buenas soluciones en tiempos aceptables, se basan en inferencias lógicas en función de atributos del problema (Hosseini-Nasab et al., 2017; Leyva et al., 2016), y otras son inspiradas en procesos evolutivos (Ramkumar, Ponnambalam & Jawahar, 2007; Tao, Wang, Qiao & Tang, 2013), de las cuales los algoritmos han gozado de mucha aceptación (Hasda, Bhattacharjya & Bennis, 2017; Hu & Wang, 2004; Niebles, Escobar & Agudelo, 2017).
Por otro lado, según las características del espacio en que se realiza la distribución, los enfoques desarrollados se pueden clasificar en discretos y continuos (Allahyari & Azab, 2018). El enfoque continuo es más común cuando se está planificando por primera vez la distribución, mientras que el discreto es más empleado cuando se realizan redistribuciones.
Con el propósito de poder abordar ambos enfoques, en esta investigación se propone una metodología en la que al enfoque continuo se le hace una aproximación discreta con técnicas tradicionales, a lo que se le denominó aproximación semicontinua. En esta se emplea como estrategia de solución inicial.
La estructura de este documento se compone, primero, de la metodología propuesta, en la que se incluye una descripción de los métodos de generación de alternativas y de selección. Luego se presenta la validación de la metodología aplicándola a una empresa de fabricación de muebles metálicos. Posteriormente se presentan los resultados sobre la base de un análisis de sensibilidad y robustez, para finalizar con las conclusiones.
Metodología
La propuesta metodológica multicriterio para la distribución semicontinua consta de seis etapas, que se pueden observar en la figura 1.
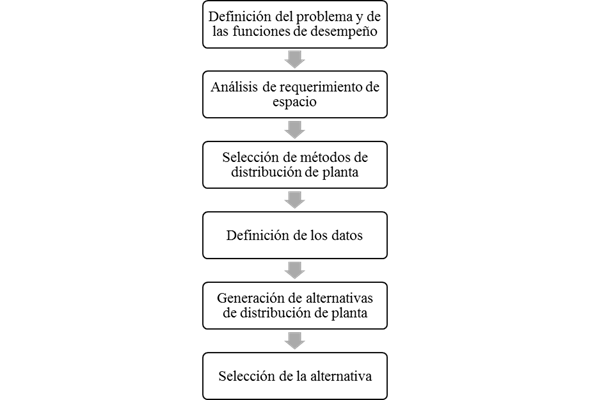
Fuente: elaboración propia.
Figura 1 Metodología propuesta para el mejoramiento de la distribución de planta
Etapa 1: definición del problema y selección de las funciones de desempeño
Definición del problema
Tal como se ha mencionado, los enfoques de distribución de planta (en adelante, problemas de distribución de planta) pueden ser discretos y continuos. En el problema discreto se tienen localidades definidas y se debe establecer la ubicación de los centros de trabajo en esas localidades. Cuando se trata de un problema continuo, se conocen los requerimientos de forma y área de los centros de trabajo, y estos pueden ubicarse en cualquier lugar del continuo espacio de la instalación. En esta investigación se propone una manera para abordar el problema de distribución de planta continuo, al que se le denominará problema semicontinuo, dado que se definen a priori localidades convenientes en el espacio continuo, que cumplan con las restricciones del problema, para luego tratarlo como un problema discreto, asignando los centros de trabajo a dichas localidades.
Selección de las funciones de desempeño
En el problema de distribución de planta se hacen arreglos físicos con el fin de mejorar uno o más objetivos (Leyva et al., 2016). Diferentes autores han analizado algunas medidas de desempeño para las distribuciones de planta (tabla 1) .
Tabla 1 Funciones de desempeño que han sido utilizadas
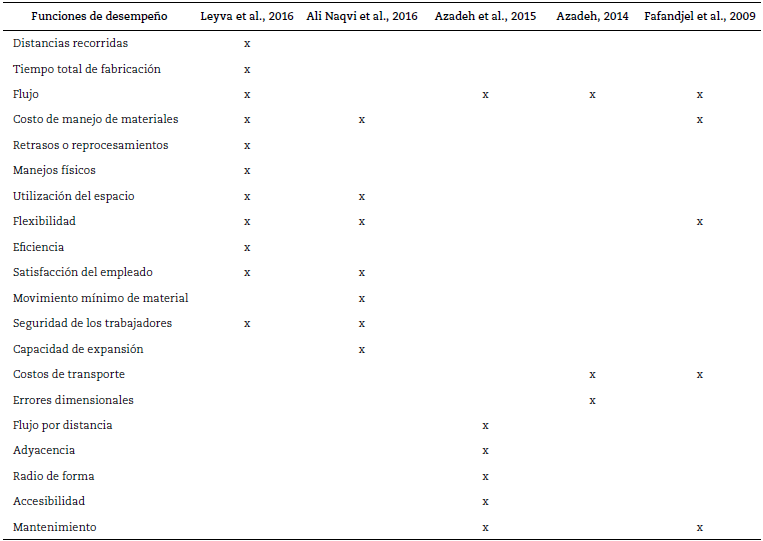
Según la necesidad de la empresa, se pueden escoger uno o varios objetivos.
Fuente: elaboración propia.
En los problemas de distribución de planta comúnmente se utiliza un enfoque multicriterio (Azadeh, 2014; Azadeh, Moghaddam, Nazari & Sheikhalishahi, 2015; Azadeh & Izadbakhsh, 2008; Aiello, Enea & Galante, 2006; Aiello, La Scalia & Mario, 2013; Subramanian & Ramanathan, 2012; Ying, Nyeoh, Ab-Samat & Kamaruddin, 2016).
Etapa 2: análisis de requerimiento de espacio
Se debe hacer un análisis del espacio utilizado actualmente, el espacio requerido y el espacio disponible, con el fin de establecer la base de parámetros y la disponibilidad final para generar las nuevas alternativas de distribución de planta.
Primero, se analizan las dimensiones actuales de los centros de trabajo para obtener el espacio utilizado. Posteriormente, mediante la aplicación del método Guerchet utilizado por Parra (2017), se analiza el espacio requerido por cada centro de trabajo, según sus procesos.
Después se proponen los pasos del diagrama de flujo de la figura 2. El análisis inicia de la siguiente manera: si el espacio requerido es menor al espacio disponible, se puede resolver el problema con las técnicas seleccionadas; por el contrario, cuando el espacio disponible es menor, si hay capital K, se puede hacer un ajuste al espacio disponible; si no, se deben hacer ajustes al espacio actual de los centros de trabajo para que se asemejen al espacio disponible. Una vez realizados estos ajustes, se procede a utilizar las técnicas.
Etapa 3: selección de los métodos de solución de distribución de planta
Según la definición del problema, se establecen algunos métodos para representarlo y solucionarlo, que también guardan una relación con los objetivos que se buscan mejorar en la nueva distribución. Existen diferentes métodos de solución que pueden consultarse en Hosseini-Nasab et al. (2017) y Leyva et al. (2016). En la tabla 2 se presenta una clasificación de la representación de algunos que tienen una relación directa con los objetivos o resultados esperados.
Tabla 2 Tipo de representación y método de solución para el problema de distribución de planta
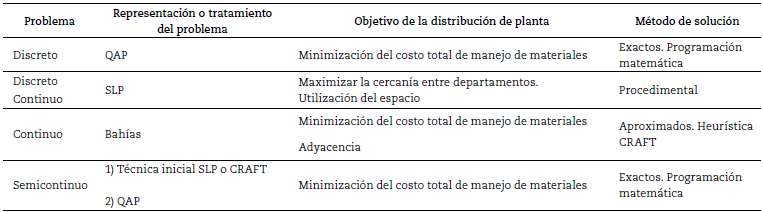
QAP (por sus siglas en inglés) se refiere al “problema de asignación cuadrática”; SLP (por sus siglas en inglés) significa “planeación sistemática de instalaciones” y CRAFT, “asignación relativa computarizada de la técnica de instalaciones”.
Fuente: elaboración propia.
Etapa 4: definición de los datos
Algunos datos generales pueden utilizarse en la aplicación de diferentes métodos de solución. En la tabla 3 se presenta un consolidado de estos, de tal manera que puedan ser recolectados y organizados en diagramas o tablas (tabla 4).
Tabla 3 Datos requeridos por cada método de solución del problema de distribución de planta
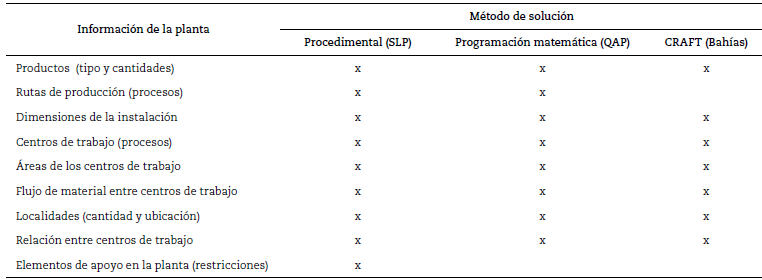
Fuente: elaboración propia.
Los elementos de detalle para la construcción de los diagramas o parámetros de la tabla 4 se pueden encontrar en diferentes documentos. Ali-Naqvi et al. (2016) presentan los elementos requeridos por el método SLP; Ramkumar, Ponnambalam y Jawahar (2009) y Salazar, Vargas, Añasco y Orejuela (2010) plantean los requerimientos del método QAP, y Atieh et al. (2016) lo relacionado con el método CRAFT.
Etapa 5: generación de alternativas
En esta etapa se deben aplicar los métodos de solución del problema de distribución en planta, es decir, generar alternativas de solución utilizando la información organizada en la etapa anterior. El proceso de generación de alternativas se propone en la figura 3.
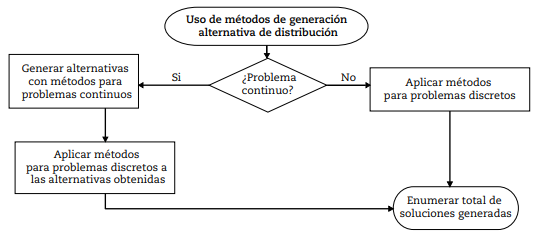
Fuente: elaboración propia.
Figura 3 Generación de alternativas utilizando métodos de distribución de planta
A continuación, se detallan algunos de los métodos discretos y continuos, comúnmente empleados para la generación de alternativas.
Planeación sistemática de instalaciones (SLP)
Esta técnica fue creada por Muther en 1973, es considerada cualitativa porque admite la inclusión de relaciones de dependencia cualitativa entre centros de trabajo (Paredes, Peláez, Chud, Payan & Alarcón, 2016); donde se incluyen elementos como la cantidad de productos que se transportan, los movimientos de personas y el uso compartido de equipos entre centros de trabajo (Van Donk & Gaalman, 2004). Es una de las más utilizadas para analizar el diseño de una planta, ya que es de uso práctico (Galindo & Tapia, 2008; Mejía, Wilches, Galofre & Montenegro, 2011). Esta técnica se resume como en el diagrama de la figura 4, excluyendo los pasos de recolección y análisis de datos que ya fueron considerados en la etapa anterior.
Asignación relativa computarizada de la técnica de instalaciones (CRAFT)
El método de asignación relativa computarizada de instalaciones técnicas se introdujo en 1963, por Buffa y Vollman, como una herramienta que permite mejorar el formato actual de las instalaciones (Hadi-Vencheh & Mohamadghasemi, 2013; Mohamadghasemi & Hadi-Vencheh, 2012). Su objetivo es disminuir el costo de transporte en una distribución (Hari-Prasad, Rajyalakshmi & Sreenivasulu-Reddy, 2014). Hace un intercambio de pares para desarrollar un diseño y tiene en cuenta las dimensiones del edificio y de las áreas, el flujo de material o la frecuencia de los viajes entre pares de instalaciones y el costo por unidad de carga y por unidad de distancia (Paredes et al., 2016; Pinto-Wilsten & Shayan, 2007).
Los pasos generales para obtener las alternativas de distribución de planta usando CRAFT se presentan en la figura 5. Para el desarrollo de estas etapas se puede utilizar un complemento de Layout de instalaciones de Microsoft Excel (add in) que permite el desarrollo del algoritmo.
Problema de asignación cuadrática (QAP)
Este método de “problema de asignación cuadrática” (QAP) fue el primero que se utilizó para modelar el problema de distribución de planta en 1957, por Koopmans y Beckmann. Actualmente, diferentes autores lo siguen utilizando como un modelo para formular el problema de distribución de instalaciones (Şahinkoç & Bilge, 2018). Leyva et al. (2016) buscan minimizar los costos del manejo de materiales que causa ubicar cada uno de los centros de trabajo en cada una de las localizaciones posibles.
El QAP como método clásico ha sido usado ampliamente, dado que por la definición de su variable permite adicionar funciones de desempeño como el costo de asignar a una localidad y también otras restricciones como las de capacidad, tal como se presenta a continuación. Sin embargo, es importante aclarar que, dado que la función objetivo base no es lineal, se presentan grandes dificultades a la hora de resolver problemas de gran tamaño.
La formulación del modelo QAP es la siguiente:
Función objetivo
Sujeto a las restricciones
área mínima requerida por el centro de trabajo
área disponible de la localidad
flujo entre centros de trabajo
distancia entre las localidades
, costo de mover entre las localidades j, k; NC es el conjunto de parejas centro de trabajo y localidades que ya han sido asignadas y no se pueden modificar por razones propias del problema.
Las variables de decisión son:
La función objetivo es minimizar el costo de movimiento de materiales. La ecuación E2 garantiza que cada centro de trabajo sea asignado al menos a una localidad, la E3 garantiza que la suma de áreas de las localidades asignadas a un centro de trabajo sea mayor que el área requerida por este, la E4 garantiza que a todas las localidades se les asigne a lo más un centro de trabajo, la E5 garantiza las asignaciones previas que no se pueden modificar y, finalmente, la E6 define el dominio de la variable.
Etapa 6: selección de la alternativa de distribución de planta
Se reconoce la naturaleza multicriterio del problema de distribución de planta (Maniya & Bhatt, 2011), en el que se han usado técnicas como AHP (Singh & Singh, 2011; Ying et al., 2016), TOPSIS (Yang & Hung, 2007), TOPSIS difuso (Hadi-Vencheh & Mohamadghasemi, 2013; Yang & Hung, 2007), DEA (Azadeh, 2014) y ELECTRE (Aiello et al., 2006, 2013; Liu, Zhang, He & Jiang, 2018). Otros métodos se presentan y se desarrollan en Venkata (2013).
En esta metodología propuesta se sugiere TOPSIS, que permite generar un ranking de prioridades según las medidas de desempeño de las alternativas. La descripción de aplicación del método se puede consultar en Ishizaka y Nemery (2013).
Resultados
La validación de la metodología se hizo en una empresa del sector metalmecánico. A continuación, se presentan los resultados de la aplicación de la metodología por cada fase.
Etapa 1
Problema
La empresa elabora piezas metálicas para las líneas de oficina y escolar como archivadores, lockers, módulos divisores, pupitres. La planta tiene un área de 547 m2, en la que los centros de trabajo están ubicados sin separaciones precisas de los mismos, no se conocen de manera exacta los requerimientos de forma y área. Por tanto, se define como un problema continuo que requerirá definir unas localidades convenientes iniciales para que posteriormente sea tratado como un problema discreto, para asignar los centros de trabajo a dichas localidades.
En la figura 6 se presenta el esquema de distribución actual con los 13 centros de trabajo (denotados por las letras en mayúscula) y las 16 localidades (Lj).
Medidas de desempeño
Se consideraron las siguientes medidas de desempeño:
Flujo por distancia: suma de los productos del volumen del flujo por la distancia rectilínea entre los centroides de dos localizaciones (Azadeh et al., 2015).
Desviación total del área: suma de los cuadrados de la diferencia entre el área requerida por el centro de trabajo y el área asignada.
Relación de radio M (SHAPEM): suma del producto entre el área asignada a un centro de trabajo por el SHAPE de dicha localidad. Busca dar prioridad en la asignación a aquellos centros de trabajo cuya área requerida es lo más cercana a un cuadrado.
Donde,
SHAPE: es el máximo de la relación largo-ancho y ancho-largo del rectángulo más pequeño que puede rodear completamente la localidad que alberga el centro de trabajo (Azadeh et al., 2015; Yang & Hung, 2007).
Costo de asignación: costo de asignar un centro de trabajo a una localidad. Cambiar un centro de trabajo a otra localidad puede implicar realizar ajustes, lo que determina que se incurran en costos.
Etapa 2
Se analizaron los requerimientos de espacio de los centros de trabajo. El área total de estos corresponde a 372 m2 y 82 m2 de pasillos; es decir, un total de 454 m2, siendo este menor al área total disponible de 574 m2, lo que indica que no es necesario ajustar el área y que se pueden utilizar las técnicas o métodos de generación de alternativas y solución de distribución de planta. En la tabla 8 se presentan en detalle el área requerida por cada centro de trabajo y se incluye la salida del producto terminado.
Etapa 3
Considerando la naturaleza semicontinua del problema, se seleccionaron los métodos SLP y CRAFT para generar las alternativas de distribución iniciales. Se seleccionó el método QAP, que pretende generar alternativas partiendo de las obtenidas por la aplicación de los otros métodos.
Etapa 4
En esta etapa se obtuvieron los siguientes datos requeridos por las técnicas seleccionadas:
Los productos que se analizaron son los archivadores metálicos. El flujo general dentro de la empresa (figura 7) se ve representado por la línea roja, es decir, el curso que sigue la materia prima principal (lámina) para su transformación, y la azul representa el curso de otras materas primas o insumos que complementan el proceso de producción.
Por otro lado, en la tabla 5 se presenta la matriz de flujo entre centros de trabajo, correspondiente al flujo de materiales, productos en proceso y terminados (archivadores).
Se definieron los criterios de proximidad (tabla 6), de acuerdo con la relación en términos del flujo que puede presentarse entre centros de trabajo y la matriz de relación de centros de trabajo (tabla 7).
Los centros de trabajo con mayor cantidad de movimiento tienen una calificación “A” que significa “absolutamente necesario” y representa la importancia de proximidad que deben tener.
Las áreas de las localizaciones, considerando el estado actual de la figura 6, tienen las dimensiones presentadas en la tabla 8.
También se tiene el parámetro costo de asignación por metro cuadrado a cada localidad, que se multiplicará por el área del centro de trabajo que sea asignada a cada localidad. En este caso, se asume que el costo de ajustar 1 m2 de área requerida por un centro de trabajo es un costo promedio de los costos requeridos para asignar ese centro de trabajo en cada localidad. Sin embargo, también se puede manejar un costo que dependa de la relación que hay entre la localidad y los ajustes que se deben realizar para el centro de trabajo, como se menciona, en este caso se emplea un costo promedio.
Teniendo los datos de la distribución actual, se encontraron los centroides de las localidades y las distancias entre ellas, con esto se calcularon las diferentes medidas de desempeño: costo de manejo de materiales o flujo por distancia, equivalente a $ 23.993; costo de asignación, cero; la desviación total del área, 1398; la relación de radio fue 129.3; los centros de trabajo no se dividieron.
Etapa 5
En el enfoque semicontinuo, primero se aplicaron los métodos SLP y CRAFT, se obtuvieron tres soluciones con cada uno, posteriormente se tomaron dichas soluciones y se aplicó QAP, obteniendo 13, a las que se le calcularon las respectivas medidas de desempeño. En la tabla 9 se observan las 14 alternativas, el método de solución y el valor de cada medida de desempeño.
Etapa 6
Se utilizó el método TOPSIS para seleccionar la mejor alternativa de distribución de planta, debido a los datos específicos requeridos para su aplicación (Ishizaka & Nemery, 2013).
Los pesos de los criterios fueron dados por la empresa: flujo por distancia 0.4, costo de asignación 0.15, utilización de área 0.15, número de centros de trabajos divididos 0.1, relación de radio-M 0.2. Después de comparar las alternativas frente a la solución ideal positiva y negativa, se encontró el índice de proximidad y se obtuvo como resultado el orden de alternativas de la tabla 10. Como se puede observar, la mejor alternativa es la solución CRAFT2, con un índice de proximidad de 0.8169. Los resultados de desempeño de esta alternativa presentados en la tabla 9, muestran el mejor resultado en flujo por distancia, uno de los mejores en utilización de área y resultados intermedios en costo por asignación, aunque en las otras medidas no era la mejor opción. El método indica que representa la más cercana a la solución ideal positiva y la más lejana de la solución ideal negativa.
Análisis de sensibilidad
Debido a la dependencia que tienen los pesos de los criterios con la selección final y considerando que en entornos dinámicos con múltiples actores se puede presentar una variación en los pesos, producto de los cambios en el entorno, además teniendo presente que la distribución de plantas es una decisión de mediano plazo que no se puede modificar con facilidad al ritmo que cambia el entorno en ambientes con poco flexibilidad, se propuso un análisis de sensibilidad variando dichos valores para establecer la solución más robusta ante la variación de los criterios. Es decir, aquella que sea la mejor en el mayor número de escenarios. En la tabla 11 se especifica cada escenario con sus respectivos pesos por criterio.
Generados los escenarios del análisis de sensibilidad, los resultados en la tabla 12 muestran que la mejor alternativa cambia dependiendo del escenario.
Se consideró importante analizar cuál es la solución (distribución de planta) robusta (tabla 13), es decir, aquella que obtiene mejores posiciones en todos los escenarios. Para esto, se utilizó el método Condorcet, con el que se analiza el número de ganancias o victorias de cada alternativa (Fernández & Soares de Mello, 2015). Se identificó que la alternativa A11 (solución CRAFT2) tuvo el mayor número de victorias, equivalentes a 109. Además, dividiendo las victorias por las pérdidas (109/21), se obtiene que en promedio es mejor esta que las otras en más de cinco escenarios. En la figura 8 se presenta el esquema de la distribución obtenida por la solución CRAFT2.
La estrategia para seleccionar la alternativa más robusta ante los diferentes escenarios, producto del dinamismo del mercado, también es extensible para el caso en el que se tienen diferentes áreas funcionales o grupos de involucrados y cada uno tiene sus propios pesos para los criterios; con lo cual, de nuevo, para cada área funcional existirá un ranking de las alternativas de distribución y, por tanto, puede ser interesante escoger aquella alternativa que satisfaga el mayor número de áreas funcionales.
Por otro lado, la generación de las diferentes alternativas mediante técnicas metaheurísticas, y la posibilidad de emplear estrategias de optimización multiobjetivo para encontrar fronteras de Pareto, representan una oportunidad para investigaciones futuras.
Conclusiones
La propuesta de distribución de planta presentada permite abordar problemas continuos y discretos, ya que el problema continuo se aborda mediante técnicas discretas; es decir, presenta una mayor generalidad en el tipo de problemas abordados, los cuales pueden provenir de distribuciones de plantas completamente nuevas o redistribuciones de planta.
La correcta identificación del problema de distribución de planta permite tener claridad en el tipo de estrategias a utilizar para la solución y en la definición de funciones de desempeño más apropiadas a dichas características. En el caso de validación se consideró como una de las medidas de desempeño la desviación del total de área, obteniendo un coeficiente de variación cercano a uno en las diferentes alternativas de distribución, lo cual indica que es sensible a las asignaciones. La medida busca garantizar que los centros de trabajo queden asignados en localidades, de tal modo que los excesos de área se distribuyan de manera uniforme, a su vez permite una mejor utilización y brinda una cierta flexibilidad de área distribuida para todos los centros de trabajo.
El enfoque multicriterio en la distribución de planta facilita la toma de decisiones en entornos donde pueden existir diferentes tomadores de decisiones con intereses y criterios distintos, y permite el cumplimiento de uno de los principales criterios de distribución de planta, el de unidad, en la medida que estas estrategias buscan soluciones convenientes en los diferentes criterios.
En momentos diferentes de la compañía y con distintos actores, es posible que los pesos de los criterios cambien dinámicamente; por tanto, es necesaria la selección de distribuciones de planta que tengan un grado de robustez ante dicho dinamismo, dado que es una decisión a mediano plazo. Por ello, el análisis de robustez propuesto con Condorcet permite identificar la alternativa que brinda mejores resultados frente a una de las variaciones de los pesos de los criterios.