1. Introduction
The cyclic monoterpene d-limonene is the main constituent of citrus essential oils extracted from the peels of oranges, tangerines, lemons, and grapefruits, whereas the levo isomer l-limonene is usually found in pine oils in low concentrations [1-3]. Carvone is a cyclic ketone obtained from limonene oxidation with a high commercial cost (>10 USD kg-1) and is used in the synthesis of specialty chemical products for the food, pharmaceutical, agrochemical, and perfume industries [4-6]. However, from the oxidation of limonene with t-butyl hydroperoxide (TBHP) as the oxidizing agent and perchlorinated iron phthalocyanine on modified silica catalyst (FePcCl16-NH2-SiO2), Figure 1, other by-products such as limonene 1,2-epoxide and carveol are obtained (acetone, 313 K, 6 h, 750 rpm, TBHP/limonene = 2.6 mol/mol, 84 mg catalyst), with a limonene conversion of 76% and TBHP of 97%; additionally, t-butanol is obtained from the decomposition of TBHP [7].
Distillation is a physical separation process by selective evaporation and condensation of the components in a mixture regularly carried out continuously, in batch or semi-continuously, which results in a total or partial separation increasing the concentration of some components in the mixture due to the differences in volatility [8]. The continuous distillation is thermodynamically and economically efficient to purify large quantities of material of constant composition [8,9]; In contrast, the batch distillation is more versatile [10] and is often used to produce small quantities of products with high purity of variable compositions, commonly in biochemical, biomedical, pharmaceutical and fine chemical industries [9]. In the usual operation of a conventional multi-stage batch distillation system, Figure 2, the distillate is continuously removed from the system until the distillation ends. If a very high purity of a product (distillate or bottoms) is needed, a multi-stage column is added to the discontinuous distillation system. In general, the relationship for multi-stage distillation can be obtained by performing step-by-step calculations [8,9]. This technique has been extensively used in experimental and simulation studies to fractionate mixtures containing essential oils and monoterpenes such as the combination of supercritical CO2 and vacuum distillation for the fractionation of bergamot oil (0.35-0.4 kPa, 298-338 K, recovery oxygenated compounds > 85%) [11]. The separation of essential oil constituents by batch vacuum distillation to the recovery of a 98.89% eucalyptol fraction from E. globulus and a 98.53% citronellal fraction from E. citriodora (18 trays, column holdup of 5%, 10 kPa, reflux ratio = 8) [12]. The fractionation of citronella (Cymbopogon winterianus) essential oil and concentrated orange oil phase by batch vacuum distillation (0.1 - 2 kPa) has also been reported with a high efficiency affording complete separation of limonene, with a rich citronellal fraction and stream constituted mainly by citronellol and geraniol [13]. The simulation of limonene epoxide distillation from a mixture containing limonene, acetonitrile, water and limonene epoxide has also been reported [14].
Regardless of the operation mode, modeling approaches for distillation equipment can use approximate and rigorous mathematical models [15]. Approximate or simple models usually assume that the dynamic behavior of the column can be approximated as a sequence of steady states (pseudo-stationary state approximation), which is true when both the holdup of liquid in the column stages and the reflux tank can be neglected compared to the holdup of liquid in the reboiler. The main advantage of these models is their calculation speed, although they may have lower precision than rigorous models in some cases, and most of them are limited to mixtures of constant relative volatility. They are used in preliminary studies of process design and optimization, when it is necessary to evaluate a large number of cases, as in this study. Rigorous models are used when a more realistic representation of column dynamics is required; however, they usually require more calculation speed. This paper presents the evaluation of the experimental separation process of carvone by batch distillation of the reaction mixture obtained from the limonene oxidation and the simulation of the separation process to determine the operating conditions that increase the recovery of carvone using an approximate model.
2. Experimental section
2.1. Catalyst synthesis and chemical reactions
(1R)-(+)-Limonene (97%) and aqueous TBHP solution (70%) from Sigma-Aldrich and acetone (99.5%) from Merck, were used without further purification. The FePcCl16-NH2-SiO2 catalyst was synthesized according to the procedure reported in the literature [7]. The oxidation of limonene with TBHP was carried out in a batch reactor of 8 mL, 318 K, 750 rpm, 6 h, TBHP/limonene molar ratio of 2.6, with acetone as a solvent and 120 mg of FePcCl16-NH2-SiO2 (55.5 μmol Fe/g). The catalyst was filtered out from the reaction mixture and the filtrate was analyzed in a gas chromatograph (GC) Agilent 7890A equipped with FID, TCD and mass spectrometer (MS) Agilent 5975C detectors, with a HP5 column (0.20 mm x 50 m x 0.5 µm). Several batches were carried out and mixed for the distillation experiments.
2.2. Batch distillation tests
The filtered reaction mixture was fractionated at atmospheric and vacuum pressure in an 800-Micro-Fractional-Distillation system from B/R-Instruments Corp., under batch conditions and using a cyclic total reflux (CTR) operation policy; i.e., alternating the internal reflux ratio r between 0 and 1. The distillation equipment uses a spinning band column that rotates at high revolutions, forcing the contact between the vapors with the condensed liquid that falls on the column wall. This contact takes place in a thin layer renewed thousands of times per minute, providing a very efficient separation. The quantification of the distillation fractions was also carried out with a GC-MS.
2.3. Modeling and simulation
The purification of carvone after removing the most volatile compounds from the reaction mixture was evaluated with an approximate mathematical model for the distillation process and executed using Matlab® software. The model assumes constant relative volatilities and constant internal reflux ratio. The ode15s function was used to solve numerically the ordinary differential equations of the mathematical model; the relative volatilities estimated through simulation in Aspen Plus® V.8 software with the NRTL-RK thermodynamic method.
Approximate model of the batch distillation for carvone purification
The approximate mathematical model for the batch distillation equipment in Figure 2 was based on the assumptions of constant molar holdups in the condenser (H c) and the internal stages (H j), total condensation without subcooling, negligible vapor holdup, perfect mixing between liquid and vapor in the stages, insignificant heat losses, theoretical stages, feed mixture at its bubble point, adiabatic column, negligible pressure drop across the column and constant relative volatilities [8,9]. The set of equations used to model the column with a separation capacity of N ideal trays is given by Equations (1) to (14). The accumulation of liquid in the pot or reboiler holdup is described by Equation (1), and the liquid molar composition of components i by Equation (2):
The liquid molar composition in the internal stages is given by Equation (3). The holdup of liquid in the condenser tank by Equation (4) and the liquid molar fraction in the condenser or distillate by Equation (5):
The distillate accumulator molar holdup and compositions are defined by Equation (6) and (7), respectively:
The estimation of the vapor molar fraction at each stage using thermodynamic equilibrium relationships is given by Equation (8), distribution coefficients by Equation (9), and inequality constraints for the compositions of liquid and vapor by Equations (10)-(11). The molar flow of liquid in the column is described by Equation (12), in the distillate by Equation (13), and the relationship between internal and external reflux ratio by Equation (14):
3. Results and discussion
3.1. Experimental evaluation of carvone separation
After the reaction, the catalyst was removed and the GC-MS analysis of the resulting liquid sample showed as main components the solvent acetone, t-butanol from TBHP decomposition, the remaining unreacted reagents (limonene and TBHP), and the main monoterpene-derived reaction products (carvone, carveol and limonene 1,2-epoxide), among others terpenes [7], Table 1. Additionally, the large amount of water entering with the oxidizing agent remains almost constant during the reaction, since just small amounts can be obtained from the limonene transformation and secondary TBHP reactions [7]. The liquid reaction sample was fractionated by batch distillation and the separation was conducted under a cyclic total reflux policy with intermittent internal reflux ratio, i.e., varying r intermittently between 0 and 1. At 90.7 kPa and 4.5 h of operation, the most volatile components of the reaction mixture (acetone, t-butanol and limonene) were withdrawn. Then, under vacuum conditions (0.27 kPa, 1 h) and after having removed the aqueous phase from the reaction mixture, carvone concentration increased (see Figure 3].
The reaction mixture was initially placed into the reboiler at 298 K and 90.7 kPa. The heat was added at total internal reflux ratio (r = 1), reaching the first steady-state equilibrium zone SS1 with a boiling point of 339 K. The first distillate cut F1 (Dist) was collected between 339 and 352 K at r = 0, its free-water composition was mainly 82.5% acetone, 16% t-butanol and 1.5% limonene. The secondary distillate cut F2 (Dist) was analyzed considering the fractions between 356-357 K and 360-363 K after reaching the steady-state equilibrium zones SS2 and SS2’, respectively. The main free-water components of this second cut were t-butanol, limonene, acetone, and TBHP, Table 1. Although the fractions F1 (Dist) and F2 (Dist) were visually in one phase and the boiling point of the mixture is below the normal boiling point of pure water, this does not guarantee the absence of water in the cuts. Ternary L-L equilibria simulation of aqueous systems containing acetone, t-butanol and TBHP (see Figure 4], suggests that the distillate cuts should probably be water-free or having small amounts of it, as the obtained fractions are in a single liquid phase.
On the other hand, the distillation at atmospheric conditions after collecting the second fraction resulted in the formation of an immiscible L-L mixture in the reboiler because of the presence of a large amount of water and terpenes, as was predicted by the ternary L-L aqueous mixtures, Figure 4. Reports of the liquid-liquid equilibrium experimental data of the ternary system containing water + acetone + limonene at 298.15 K, and its simulated correlation by the modified UNIQUAC model [16], are in agreement with our simulation results. Thus, it is expected that this mixture has the largest amount of water to be removed from the reboiler. Additionally, it is not desirable to separate water as the previous cuts to avoid bottom products damage, due to the sudden temperature increasing up to 433 K when the last drop of the aqueous phase is evaporated (results are not presented here). Thereby, after 4.52 h of operation, the distillation was stopped, the L-L reboiler mixture was separated by centrifugation in a third aqueous and organic bottom fractions.
The third aqueous bottom fraction F3,AQ (bott) mainly contained TBHP, acetone and t-butanol, among others. On the other hand, the organic bottom fraction F3,ORG (bott) was mainly constituted by limonene, 13% carvone, acetone, and t-butanol, among others, Table 1. The fractionation of the F3,ORG (bott) under vacuum conditions (300 K and 0.27 kPa) gave the last bottom fraction F4 (bott) after 357 K. However, the third aqueous bottom fraction F3,AQ (bott) mainly consisted of TBHP, acetone and t-butanol, among others. On the other hand, the organic bottom fraction F3,ORG (bott) was mainly constituted by limonene, 13% carvone, acetone, and t-butanol, among others, Table 1. The fractionation of the F3,ORG (bott) under vacuum conditions (300 K and 0.27 kPa) gave the last bottom fraction F4 (bott) after 357 K. However, it was not highly enriched due to the remaining material in the bottom was not enough to complete the recirculation in the distillation column. The free-water composition of the F4 (bott) sample after 0.75 h was mainly 14% carvone, 11% acetone, 9% t-butanol, 4% limonene, 1% limonene 1,2-epoxide, 1% carveol, among others, Table 1.
Table 1 Experimental composition of the reaction mixture and the liquid fractions during the fractional batch distillation
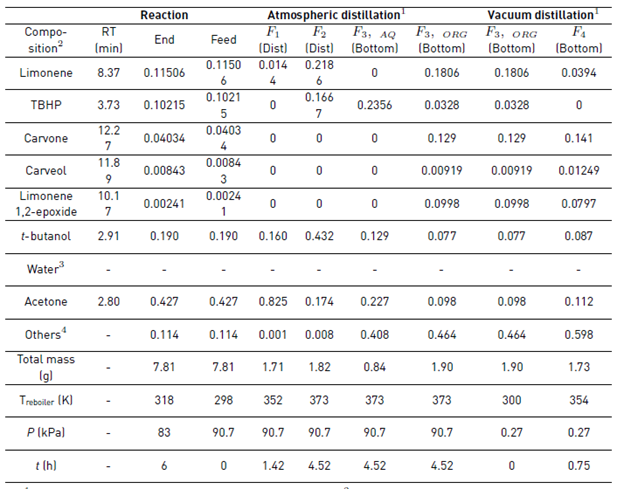
1800-Micro-Fractional-Distillation B/R-Instrument system.2Free-water composition of i obtained by GC-MS as Areai/Total-Area. 3Water composition cannot be quantified using a Flame Ionization Detector (FID). 4Complementary composition includes several compounds, mainly terpenes, products that were not identified with good accuracy by GC-MS. RT: retention time.
3.2. Computational simulation of the approximate batch distillation model for carvone purification
The rectifier batch distillation was selected as a technique for separating carvone from the mixture obtained from limonene oxidation; carvone has important applications in the fine chemical industry, where the production capacity is low, but the purity is important.
Continuous distillation simulation
As a first approximation, a continuous simulation of the carvone separation by continuous distillation was carried out in Aspen Plus® software with the thermodynamic method NRTL-RK, and by using the shortcut DSTWU and the rigorous RadFrac blocks, Table 2. Since the presence of water allows the formation of immiscible L-L phases in equilibrium, which causes a more difficult separation of carvone and the requirement of more rigorous models for the simulation that should consider the LLV equilibria in the column [17,18], the reaction mixture in the feed of this model simulation was established from the results obtained in a flash evaporation of the reaction mixture to remove volatiles and large amounts of water. These preliminary calculations were executed to obtain optimized parameters of the number of ideal stages N = 13, adjusted distillate flow rate L D = 0.4745 kmol h-1 and internal reflux ratio r to be used as approximate design parameters for the batch distillation model. The values of relative volatility α were calculated for the feed composition in Table 2 using the NRTL-RK thermodynamic method; after a sensitive analysis of the bubble and dew points at different thermodynamic models were compared, Figure 5. Since no significant differences were observed for the simulation of the dew points among the selected thermodynamic methods, the Redlich-Kwong equation of state was selected to model the vapor phase. Likewise, the activity coefficient model NRTL was selected to model the liquid phase, as the simulation of the bubble points was similar, except by the ideal model. Although there are intrinsic differences among the selected thermodynamic models [19], there are several studies that properly correlate the physical and thermodynamic properties of mixtures containing terpenes that were simulated by models such as UNIQUAC, WILSON, UNIF-DMD, NRTL, among others [16,20-23].
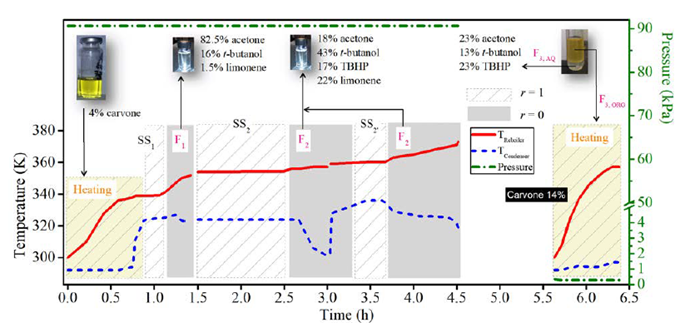
Figure 3 Spinning Band fractional distillation of limonene reaction mixture in a batch mode. Conditions: CTR operation policy, 7.8 g mixture, 0.27 kPa, 90.7 kPa. SS: steady-state, F: distillate fraction, r: internal reflux ratio
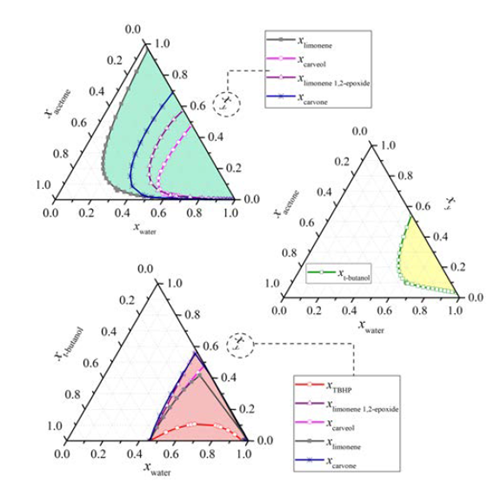
Figure 4 Ternary L-L equilibrium of the main components in limonene oxidation. Conditions: Aspen Plus® simulation, NRTL-RK, 90.7 kPa, 363 K
Batch distillation simulation
The fractional batch distillation simulation results using the approximate model and the design parameters obtained by the continuous simulation (13 ideal stages, r = 0.084, 7.5 kPa, L D = 0.4547 kmol h-1) are presented in Figure 6. The molar holdups in the internal stages H j and in the condenser drum H c, were defined in terms of the reboiler holdup H N. The internal stages to reboiler holdup ratio was specified as ϕ j-N (H j/H N) = 0.21%. Likewise, the condenser drum to reboiler holdup ratio was indicated as ϕ c-N (H C/H N) = 0.67%.
Table 2 Continuous fractional distillation simulation for carvone separation
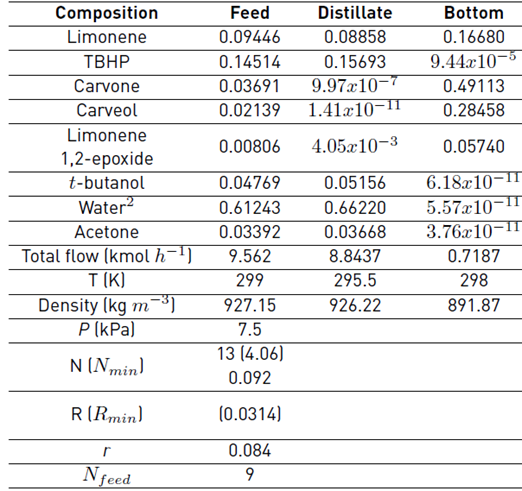
1Feed composition established from the results obtained in a flash evaporation of the reaction mixture to remove volatiles. 2Water content obtained considering mainly the amount entering the reactor. Conditions: Aspen Plus® simulation considering only the main compounds detected by GC-MS, NRTL-RK, DSTWU, and RadFrac blocks.
The total operation time for the separation is predicted as 5.25 h, excluding the time to achieve the steady-state in the startup that was set as 0.25 h. Three distillate cuts were proposed to achieve a higher carvone purification as a distillate product, since carvone concentration in the reboiler x 13,carvone was predicted to increase only from 4% at the feed to around 50% after 5.0 h or operation, Figure 6a. Additionally, a constant internal reflux ratio per cut policy was established for the simulation instead of the CTR operation policy, since the last one usually requires more energy due to the intermittent steady-state equilibrium zones in which there are not products withdrawn. The liquid molar fraction in the accumulator of the first distillate cut (Cut1) is mainly composed of 71% acetone, 27% t-butanol and 2% water after 0.17 h. The second distillate cut (Cut2) required 4.91 h after the first cut was collected. The simulation of its composition resulted in a mixture containing 67% water, 16% TBHP, 10% limonene, 4% t-butanol, 1% acetone and 1% limonene 1,2-epoxide. The operating time of the final cut (Cut3) was 0.17 h after the collection of Cut2. Here a sensitive analysis of the internal reflux ratio r was performed to improve carvone separation. A larger internal reflux ratio r = 0.5 increases the contact time of the phases and the carvone molar fraction in the third accumulator was predicted as 86.5%, with 11% TBHP and 2% limonene, Figure 6b. In this case, the molar fraction of carvone in the reboiler decreased from 38% to zero [Figure 6a) because it was concentred in the condenser [Figure 6c).
In summary, the simulation of carvone separation by batch distillation can be carried out in four stages. Using total internal reflux ratio (r = 1) at start-up, small constant internal reflux (r = 0.084) to collect the first (Cut1) and second (Cut2) distillate fractions and the final stage at larger constant internal reflux ratio (r = 0.5) to recover the carvone as a distillate product with a purity of 86.5% (Cut3), Figure 7. Although ideal equipment was assumed in the conceptual design of the distillator, the results on the correction of the ideal stages using some correlations for the estimation are outside the range of application. The distillation occurs at vacuum pressure, the average relative volatility between the light and heavy key components is 50 (relatively large); and the viscosities of the initial mixture is 0.472 cP at the bubble point. The most commonly used empirical correlations for estimating stage efficiency include the Drickamer and Bradford equation as a function of the viscosity of the mixture [24]; the tray efficiency estimated from this correlation was E DN = 35%. However, the expression is limited to a range of efficiencies from 41% to 88% (with a deviation of 5 to 13%), which covers temperatures from 342 to 488 K, positive pressures (100 to 2500 kPa), and liquid viscosities between 0.066 to 0.355 cP.
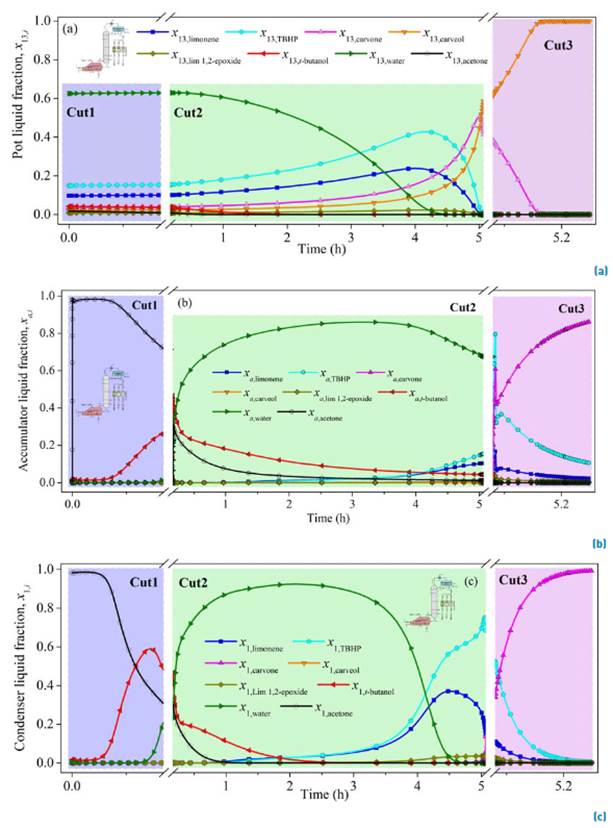
Figure 6 Simulation of liquid molar composition in the reboiler (a), accumulator (b), and condenser (c) in the batch fractional distillation of carvone. Conditions: constant internal reflux, LD = 0.4745 kmol h-1, 7.5 kPa, ϕj-N = 0.21%, ϕc-N = 0.67%, Cut1 (0.17 h, r = 0.084), Cut2 (4.91 h, r = 0.084), Cut3 (0.17 h, r = 0.5). Matlab® simulation by ode15s
The O'Connell formulation [24], which is a function of the viscosity and the relative volatility, predicted a slightly lower value of the tray efficiency, E OC = 25%. Although this expression covers a wider range of relative volatilities, the data used only covers a relative volatility from 1.16 to 20.5. Although, in both cases, the tray efficiencies are small, i.e., real distillation equipment must have a higher number of stages to achieve the separation of carvone with higher purity, it is recommended to estimate the tray efficiency fitting experimental data because the correlations are not adequate for the process conditions.
Nomenclature
EStage efficiency
H Molar holdup (kmol)
K Distribution coefficient (-)
L Molar liquid flow rate (kmol h-1)
NStage N or number of ideal stages (-)
n c Number of components (-)
r Internal reflux ratio (-)
TTemperature (K)
tTime (h)
PPressure (kPa)
RExternal reflux ratio (-)
xMolar liquid fraction (-)
yMolar vapor fraction (-)
Greek letters
α Relative volatility (-)
ϕ Holdup ratio (-)
Sub- and Superscripts
aDistillate accumulator
cCondenser-drum
DDistillate
iComponent
jInternal stages
Abbreviations
DB Drickamer and Bradford
DSTWU DiSTillation-Winn-Underwood Block
FID Flame Ionization Detector
GC-MS Gas Chromatography-Mass Spectroscopy
OC O'Connell
NRTL Non-Random Two-Liquid
RK Redlich-Kwong
TCD Thermal Conductivity Detector
UNIQUAC Universal Quasichemical
4. Conclusions
Carvone, a naturally occurring compound with relevant applications in the specialty chemical industry, was synthesized from limonene over the heterogeneous catalyst FePcCl16-NH2-iO2 and using TBHP as an oxidant in a batch reactor. The further fractionation of the reaction mixture by distillation leads to the increase in carvone concentration. Non-ideality of liquid phase has to be corrected by adequate selection of thermodynamic models for the activity coefficients such as NRTL, UNIQUAC, UNIFAC or WILSON and compared with experimental data to validate the most adequate model. Redlich Kwong vapor phase seems to behave similarly as predicted with the ideal thermodynamic model. Since terpenes usually have high normal boiling points, it is preferable to fractionate them under vacuum conditions. After a large number of volatile compounds (acetone, t-butanol, and water) are removed from the reaction mixture, carvone purity by fractional distillation is predicted as 86.5% in a third distillate cut, according to the approximate model used. Both experimental and simulation results showed that fractional distillation is a suitable technique for concentrating carvone. However, the presence of water allows the formation of immiscible L-L phases in equilibrium, which causes a more difficult separation of carvone and the requirement of more rigorous models for the simulation that should consider the LLV equilibria in the column. Additional experimental data obtained using the constant reflux policy are required to compare and validate the approximate model of the batch distillation, since the data obtained by the CTR policy requires further parameters for a simulation and it is not an attractive operational mode from the economical point of view. Thus, a more efficient carvone separation could be reached by optimization of the operating conditions in the distillation column.