Introduction
Water is one of the most important substances on the planet, covering about 71% of the Earth's surface, and it is vital for all known forms of life, although only 2.5% of the Earth's water is fresh water [1].
Rapid urbanization and industrialization releases huge volumes of wastewater, which is increasingly used as a valuable resource for irrigation in urban agriculture, as it leads to significant economic activity, supports and sustains farmers and producers, and substantially changes the water quality of natural water bodies. Due to increasing industrialization and urbanization, this wastewater is becoming more polluted, and the risk of consuming this polluted water and the sanitation problem is increasing progressively in most developing countries [1].
The emissions of domestic and industrial wastewater towards water objects can cause changes in their chemical and biological conditions, the quality of the water and an irreversible environmental impact [2].
Water pollution comes mainly from domestic and industrial wastewater. Industrial wastewater incorporates highly toxic and dangerous chemical compounds which impact human health and aquatic life. These compounds consist mainly of heavy metals such as aluminum, copper, zinc, iron, cadmium, manganese, and chromium [3]. Heavy metals are one of the most widespread sources of industrial water pollution, due to their toxicity, non-biodegradable nature and accumulation in living organisms [4]. Chromium is an important heavy metal for both humans and the environment, often found in industrial wastewaters, which is introduced into water streams through the mining, tanning, electroplating, paint and textile dye industries, as well as in industrial plants producing inorganic chemical compounds and pigments [5]. Chromium most frequently exists in both the trivalent [Cr(III)] and hexavalent [Cr(VI)] states in aquatic environments. Trace amounts of Cr(III) is an essential micronutrient for the metabolism of sugar, protein and fat in mammals, while Cr(VI) is a primary pollutant, which is considered a potential carcinogen that induces liver cancer [6]. Therefore, it is necessary to treat industrial wastewaters containing chromium before discharge them into the environment [7].
At present, a great variety of industrial wastewater treatment technologies are available, which are applied depending on the purification rate, complexity of the required equipment, and the capital and operating costs involved [2]. The purpose of wastewater treatment is to reduce or remove water pollutants that pose threats to humans and the environment if they are discharged into surface waters or groundwater without proper treatment [8].
Conventional wastewater treatment consists of a combination of physical and biological processes to remove solids, organic matter, heavy metals, and nutrients from wastewater. The general terms used to describe the different levels of treatment, in the order of increasing levels of treatment, are preliminary, primary, secondary and tertiary or advanced treatment [9].
However, the first important information to design any wastewater treatment system is the strength and characteristics of the wastewater to be treated. The strength of the wastewater is normally expressed in terms of pollutant load, which is determined from the concentrations of the significant physical, chemical or biological contents of the wastewater [10].
Treatment processes can also remove or neutralize many toxic industrial pollutants. In principle, the processes for the treatment of toxic chemicals and industrial waste should be carried out in the same industrial establishments, and should not be discharged into the sewers without treatment and without complying with the regulations established regarding the industrial effluents allowed for their discharge into the sewerage [8]. The water obtained in wastewater treatment plants must meet certain quality standards before being discharged into receiving sources (bodies of water) or reused depending on the need [11]. Mathematical methods, data mining and software (simulators) can be used to carry out the evaluation and simulation of industrial wastewater treatment systems, plants and processes [11]. Several authors have simulated wastewater treatment systems of various characteristics and particularities. In this sense, Gontarski et al. [12] developed a way to predict the environmental properties of the outlet stream of an industrial wastewater treatment system located in a terephthalic acid production plant in Brazil, using Artificial Neural Network. Also Oliveira-Esquerre et al. [13] carried out the simulation of an industrial wastewater treatment plant using the Artificial Neural Network and principal component analysis, in order to predict the Biochemical Oxygen Demand of the outlet stream of this treatment plant, which is located in a pulp and paper company in Brazil. In addition, Banaei et al. [14] evaluated the long-term performance and process stability of a large-scale integrated industrial wastewater treatment system with respect to the removal of organic matter, using the Artificial Neural Network for this. In another study Zakharov & Bondareva [2] generated a mathematical model to describe the treatment and disposal of industrial and domestic wastewater in flooded mine works, in order to develop and analyze the mathematical model of the flow and distribution of suspended impurities. On the other hand, Moragaspitiya et al. [15] studied the dynamic behaviors (dependent on time) of a wastewater treatment plant in Australia, using the implemented mathematical modeling technique with Bio-Win software, in order to obtain a developed and calibrated model that can be used to study important unmeasured parameters of the treatment plant. Likewise, Chandraseagar et al. [3] carried out a simulation and optimization study of a spent caustic wastewater treatment system using the Aspen Plus simulator, based on the wet air oxidation method. Likewise, Mtynski et al. [16] modeled the operation of a wastewater treatment plant using the Monte Carlo method and modeling the probability distributions of different random variables, including in the analysis the Biochemical Oxygen Demand, Chemical Oxygen Demand, Total Suspended Solids, Total Nitrogen and Total Phosphorus. Finally, Asami et al. [11] developed, compared and evaluated the performance of an Artificial Neural Network model and M5 model tree to evaluate the treatment performance of a wastewater treatment plant at the Ramin thermoelectric plant in Ahvaz, Iran, and also to estimate the quality of the effluent obtained. The techno-economic analysis (TEA) is essential to determine the feasibility of a project, and these must be adapted to the area of interest. TEA commonly combines process modeling, engineering design, and economic evaluation by evaluating the economic feasibility of a process and identifying cost risk and sensitive points during the development and implementation stages [17]. The selection of the ideal software to carry out the evaluation of a TEA is usually based on the technical knowledge, time and process data available by the researcher [18]. SuperPro Designer® is a process simulator marketed by Intelligen, Inc. (Scotch Plains, NJ, USA) that facilitates the modeling, evaluation, and optimization of integrated processes. It was developed specifically for the simulation of bioprocess unit operations, so it can handle both batch and continuous processing schemes. It can also be used in all stages of process development, from conceptual design to process operation and optimization. Apart from process modeling, the software presents several features and functions that can be used for the calculation of mass and energy balances, and extensive databases of chemical components and mixtures, as well as equipment sizing and costing, determination of economic parameters and profitability indicators, and characterization of residual streams [19]. It presents a user-friendly interface that facilitates its use by non-expert users, especially during the technology development stages, when the TEA can help identify cost-sensitive factors [18]. SuperPro Designer® simulator has been used to simulate wastewater treatment plants of various types and conditions, referring to municipal wastewater [20]; five treatment alternatives for cheese whey-rich wastewater from a Cheddar cheese factory [21]; the analysis of a biological wastewater treatment process using activated sludge [22]; the remediation of the increase in the concentration of ammonia or nitrite/nitrate in municipal wastewater effluents based on the Bardenpho-type treatment process [23]; the introduction of the simulator in the laboratory practices of water and wastewater treatment in the Chemical Engineering career at the University of Camagüey, Cuba [24]; the development of industrial-scale models of a wastewater treatment process in order to reduce the concentration of sulfate and heavy metals in the effluent coming from mining processes [25]; a covered lagoon process for the treatment of effluents from the palm oil production industry, coupled with the generation of biogas [26]; the optimization of a waste treatment plant from the poultry industry [27] the simulation and optimization of an anaerobic co-digestion process [28]; the optimization of an integrated anaerobic-aerobic bioreactor for the treatment of effluents from the palm oil industry, to obtain the highest possible biogas yield while taking into account the economic and environmental tradeoff [29], and two treatment schemes in order to develop a more sustainable process that involves the recovery of polyphenols and water reutilization, depending on the characteristics of the residual water produced in the olive oil industry [30].
The Mayor General "Ignacio Agramonte y Loynaz" Military Industrial Company of Camagüey, Cuba (also named "Mechanical Plant") is dedicated to the manufacture and repair of mechanical metal elements. To fulfill its mission, it presents a group of technological processes and services within the metal-mechanical and chemical divisions, which complement the necessary conditions to guarantee the quality established for the main products. However, this company generates a volume of wastewaters that contains significant amounts of Cr(VI), which currently do not have adequate treatment. Due to the above, there is a need to design a wastewaters treatment plant proposal to process these chromic wastewaters stream generated in the Mechanical Plant, with the aim of discharging them into the environment with the required environmental quality. In the present work, the techno-economic evaluation of a proposed chromic wastewater treatment plant with a processing capacity of 9 t/batch of wastewater is carried out, in order to know its main feasibility and profitability parameters under current Cuban economic conditions, as well as to determine the mass composition of the main outflow streams. For that, the commercial simulator SuperPro Designer® was employed.
Materials and methods
Description of the industrial wastewaters treatment process
The chromic wastewater treatment plant proposal evaluated in this work begins with the reception of 9 t/batch of a wastewater stream whose percentage mass composition is shown in Table 1, in a metal tank of 10.5 m3 of capacity where it is stored for a time of 10 min. Then, this wastewater stream is pumped into a stirred tank with a total volume of 10.5 m3 (Reduction tank), in which 238 kg of sulfuric acid (H2SO4) and 100 kg of sodium bisulfite (Na2S2O5) are added. The reaction No. 1 described in Table 2 (Reduction reaction) [31] occurs in this tank with a reaction time of 2 h, where chromium sulfate [Cr2(SO4)3] and sodium sulfate (NaSO4) are formed. The addition of H2SO4 in this stage makes it possible to achieve the appropriate pH in the water, which generally reaches a value lower than 3, leading to the reduction of Cr6* to Cr3+. Next, the water contained in the reduction tank is pumped into a metal tank provided with agitation (Neutralization tank 1) where 47 kg of the reagent calcium hydroxide [Ca(OH)2] are added in order to reach an alkaline pH between 8.5 and 9.5, which favors the precipitation of Cr3+. In this stage, reactions No. 2 (Neutralization reaction 1) [32] and No. 3 (Precipitation reaction) [33] shown in Table 2 occur, thus forming calcium sulfate (CaSO4) and chromium hydroxide III [Cr(OH)3] with an agitation time of 1 h.
Table 1 Percentage mass composition of the wastewater.
Component | % Mass |
---|---|
Aluminum | 0.0090 |
Chrome oxide VI | 0.0080 |
Iron | 0.0040 |
Nickel | 0.0085 |
Phosphorus | 0.0090 |
Suspended solids | 0.0953 |
Water | 99.8647 |
Zinc | 0.0015 |
Table 2 Stoichiometry of the chemical reactions that take place in the different stages of the wastewater treatment process, and its conversion percentage.
No. | Stoichiometric reaction | Conversion (%) |
---|---|---|
Reduction: | ||
1 | 2CrO 3 + Na 2 S 2 O 5 + 3H 2 SO 4 → Cr 2(SO 4)3 + 2N aSO 4 + 3H 2 O | 90.0 |
Neutralization 1: | ||
2 | Ca(OH)2 + H 2 SO 4 → CaSO 4 + 2H 2 O | 95.0 |
Precipitation: | ||
3 | 3Ca(OH)2 + Cr 2(SO 4)3 → 3CaSO 4 + 2Cr(OH)3 | 90.0 |
Neutralization 2: | ||
4 | 2NaOH + H 2 SO 4 → Na 2 SO 4 + 2H 2 O | 95.0 |
Coagulation: | ||
5 | FeCl 3 + Cr(OH)3 → F e(OH)3 + CrCl 3 | 98.0 |
Figure 1 shows the block diagram of the chromic wastewater treatment process described above.
Subsequently, the neutralized water is pumped into a second agitated neutralization tank with a capacity of 12 m3, where 165.5 kg of sodium hydroxide (NaOH) and 454.44 kg of ferric chloride (FeCl3) are added, to carry out reactions No. 4 (Neutralization reaction 2) [34] and No. 5 (Coagulation reaction) [35] shown in Table 2, where sodium sulfate (NaSO4), chromium chloride (CrCl3) and iron hydroxide III [Fe(OH)3] are formed. The addition of NaOH makes it possible to adjust the pH of the water in the 6.5 - 8.5 range, with a mixing time of 2 h.
Water is then pumped from the second Neutralization tank to the Flocculation tank, which is a metal tank provided with agitation of 12 m3 capacity where 533.3 g of Magnafloc 2025 coagulant are added, and the resulting mixture is stirred for 2 h to promote coagulation and agglomeration of suspended and previously agglomerated substances contained in the water. Once the agitation time in the flocculation tank is completed, the water is sent to a circular clarifier in order to favor the sedimentation and precipitation of the coagulated particles in the previous stage, and to obtain a clarified water at the equipment supernatant.
The clarified water at the clarifier outlet then flows to the acidification tank, which is a metal tank provided with agitation, where 224 g of sulfuric acid are added to make the final adjustment of the water pH between 8.0 - 8.5 approximately, prior to the filtration operations. Once the sulfuric acid has been added, the mixture is stirred for 30 min in this tank to promote the correct mixing of the reagent in the water.
Once the mixing time has elapsed, the resulting acidified mixture is pumped into a reservoir tank, where it is stored for 15 min, to be pumped then into the silica filter, where a large percentage of the different salts minerals and heavy metals contained in the inlet water stream are removed. Afterward, this filtered stream is sent to two activated carbon filters in series, where the remaining amounts of chemical compounds still contained in the water stream are removed, with a cumulative removal percentage of 98%.
The final treated water is obtained at the outlet of these activated carbon Alters, ready to be discharged into the sewer or to be reused in a specific process. On the other hand, the sludge stream obtained in the clarifier, as well as the concentrated streams obtained in the Alters, are mixed together and sent to a cylindrical metal tank of 15 m3 capacity (Thickener tank), where they are stored for 10 min.
Next, the mixture obtained in the thickener tank is pumped towards a plate-and-frame filter, in which it is filtered until a treated water is obtained that can be recirculated back to the wastewater treatment process, or reused as water for agricultural plantations irrigation, for washing and cleaning, among other applications.
The reagents used in this work were selected based on experimental studies carried out at laboratory scale by specialists of the Military Industrial Company, in correspondence with indications and suggestions made by various Cuban engineering consulting firms.
Economic and profitability indicators
The preliminary economic evaluation of any chemical plant proposal usually involves estimating capital investment, operating costs, and profitability analysis. In this work, the SuperPro Designer® simulator was used to determine different economic and profitability indicators of a proposed wastewater treatment plant, among which we can mention the Net Present Value (NPV), Internal Rate of Return (IRR), Payback Time (PT), Return on Investment (ROI), gross margin and unit production cost. The NPV is the sum of the present values of the future cash flows, while the IRR is the interest discount rate that makes the NPV of all the cash flows equal to zero. It is a measure of the maximum interest rate at which the project can break even at the end of the project's life. If the NPV is positive and an IRR of 7% is obtained, it indicates that the projected income exceeds the anticipated costs (all in current dollars) and that the investment will be profitable. The PT is the time required to pay the initial investment from income, and it is estimated by dividing the total capital cost by the average annual income where taxes and depreciation are not taken into account. Typically, a PT of 2 - 5 years is expected. The ROI is defined as the annual operating income after taxes divided by the total capital cost and is expected to be in the range of 20 - 30%. It is a measure of how effectively the company uses its invested capital to generate profit. Gross margin is the sum of product earnings minus raw material costs and represents the proportion of each dollar of profit that the company retains as gross profit. Finally, the unit production cost is obtained by dividing the annual operating cost by the annual production rate [36].
Simulation of the wastewater treatment process in SuperPro Designer® simulator
As previously established, the chromic wastewater treatment plant proposal was simulated in the SuperPro Designer® simulator, in order to know the mass concentration of the main outlet streams, as well as to obtain the main techno-economic and profitability indicators of the plant. The plant will have a construction period of 10 months, a start-up and commissioning time of 4 months and a project life of 25 years. An interest rate of 11% was considered to determine the value of the NPV indicator, that the plant works at 100% capacity throughout its life, and that treated water is not discarded because it does not meet the standard quality parameters established by the process before its discharge. A 25% income tax was also taken into account, while there are no expenses related to advertising and sales operations, that the start-up and validation costs were estimated as 10% of the Direct Fixed Capital, and that the working capital was estimated to cover expenses of 15 days of labor and raw materials.
The facility-dependent costs were determined based on the capital investment parameters, thus selecting the maintenance (using specific multipliers of each equipment) and depreciation (using the contribution of the non-depreciated purchase cost of each equipment) options, a salary of USD $ 0.73/h and $ 0.95/h was set for operators and supervisors, respectively, while the cost related to quality assurance and control in the laboratory was considered as 15% of the total labor cost. Expenses for research and development activities were not taken into account, an electricity unit cost of USD $ 1.20/kW-h was considered, and that USD $ 10,000 per year is disbursed for process validation operations.
The wastewater treatment plant does not consume auxiliary services such as steam, cooling water, glycol or hot water; it was considered that the plant operates 11 months a year with one month to carry out maintenance operations of equipment and accessories; that the plant will have a processing capacity of 9 tons of wastewater per batch; that it will charge an income tariff of USD $ 0.50 for each kg of wastewater received, while 250 batches will be carried out per year.
The plant will operate in batch mode due to the fact that the chromic wastewaters are generated during the operations of a metallurgical process that is carried out in batch mode in the Mechanical Plant, where this wastewater is accumulated in a metal tank (Homogenization) for its subsequent treatment in the different stages of the treatment plant. That is, the wastewater is not generated continuously, but only when the metallurgical processing batches are carried out in the Mechanical Plant annexed to the proposed chromic wastewaters treatment plant. It is worth noting that all the tanks present in the treatment plant will operate in batch mode since a certain reaction time is needed between the reagent that is added in the tank and the chemicals contained in the wastewater volume, in order to increase the extension of the reaction that occurs there, with its consequent effect on the subsequent stages, as well as to promote a holding time for the residual water that has been treated. Finally, both the silica and activated carbon filters, as well as the circular clarifier and the plate-and-frame filter, will operate continuously in the proposed wastewaters treatment process.
Cost of raw materials
Table 3 shows the costs of the different raw materials consumed in the proposed wastewater treatment plant [37,38].
Table 3 Costs of the raw materials consumed in the wastewater treatment plant.
Raw material | Chemical formula | Cost |
---|---|---|
Calcium hydroxide (USD $/MT†) | Ca(OH)2 | 185.00 |
Ferric chloride (USD $/MT) | FeCl3 | 500.00 |
Magnafloc 2025 (USD $/kg) | - | 15.01 |
Sodium hydroxide (USD $/MT) | NaOH | 320.00 |
Sodium bisulfite (USD $/MT) | Na2S2O5 | 300.00 |
Sulfuric acid (USD $/MT) | H2SO4 | 250.00 |
+MT - Metric Ton
Characteristics and acquisition costs of the main equipment
Table 4 shows the characteristics of the main equipment included in the wastewater treatment plant, as well as their acquisition costs, which were taken from various references [39-42] and updated to August 2021 using the corresponding cost index [43].
Table 4 Characteristics and acquisition cost of the main equipment included in the wastewater treatment plant.
Equipment | Characteristic | Amount | Cost (USD $) |
---|---|---|---|
Homogenization tank | 10.5 m3 | 1 | 12,000 |
Pump 1 | 10 m3/h; 3 kW | 1 | 6,300 |
Reduction tank | 10.5 m3; 0.55 kW | 1 | 16,000 |
Pump 2 | 10 m3/h; 3 kW | 1 | 6,300 |
Neutralization tank 1 | 10.5 m3; 0.37 kW | 1 | 16,000 |
Pump 3 | 10 m3/h; 3 kW | 1 | 6,300 |
Neutralization tank 2 | 12 m3; 0.37 kW | 1 | 18,000 |
Pump 4 | 10 m3/h; 3 kW | 1 | 6,300 |
Flocculation tank | 12 m3; 0.18 kW | 1 | 18,000 |
Pump 5 | 10 m3/h / 3 kW | 1 | 6,300 |
Clarifier | 15 m2; Depth: 2.50 m; 3.4 m3 | 1 | 20,000 |
Acidification tank | 10.5 m3; 0.55 kW | 1 | 16,000 |
Pump 6 | 18 m3/h / 5 kW | 1 | 7,500 |
Reservoir tank | 10.0 m3 | 1 | 10,900 |
Pump 7 | 18 m3/h / 5 kW | 1 | 7,500 |
Silica filter | Diameter: 1.5 m; Height: 3 m | 1 | 18,000 |
Activated carbon filter | Diameter: 1.5 m; Height: 3 m | 2 | 20,000 |
Thickener tank | 15 m3 | 1 | 13,700 |
Pump 8 | 18 m3/h / 5 kW | 1 | 7,500 |
Plate-and-frame filter | 100 m2 | 1 | 124,100 |
Results and discussion
The main techno-economic results obtained during the simulation in SuperPro Designer® simulator of the chromic wastewater treatment plant proposal are shown below.
Figure 2 presents the flowsheet obtained by simulating the proposed wastewater treatment plant in SuperPro Designer®.
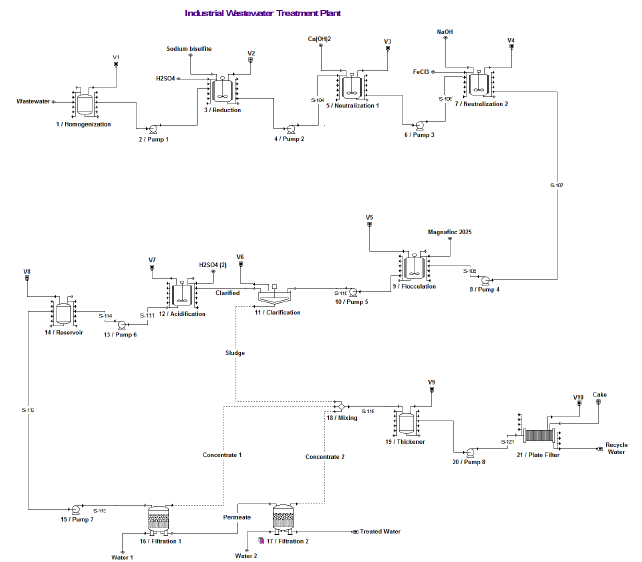
Figure 2 Flowsheet of the chromic wastewater treatment plant obtained from SuperPro Designer® simulator.
Composition of the outflow streams
Table 5 expresses the mass concentration of the three main outflow streams from the wastewater treatment plant, that is, Treated Water, Cake and Recycle Water. It's worth to mention that 1,815.85 and 1,863.63 kg/batch of washing water are consumed in the silica Alter and activated carbon Alters, respectively, while 6,959.90 L/ batch; 1,051.53 kg/batch and 5,881.89 L/batch are obtained for treated water, cake and recycled water, respectively.
Table 5 Mass concentration of the three main outflow streams.
Component / Stream | Mass concentration (mg/L) | ||
---|---|---|---|
Treated water | Cake | Recycle water | |
Aluminum | 0.05819 | 0.9150 | 6.8820 |
Calcium hydroxide | 0.09780 | 1.9226 | 14.4604 |
Calcium sulfate | 0.11958 | 98.9199 | 14.1502 |
Chrome chloride | 0.01625 | 1.0228 | 7.6933 |
Chrome oxide VI | 0.00051 | 0.0813 | 0.6120 |
Chrome sulfate | 0.00913 | 0.1435 | 1.0796 |
Chrome hydroxide | 0.00086 | 0.0135 | 0.1020 |
Iron hydroxide | 0.04387 | 0.6898 | 5.1887 |
Ferric shloride | 0.06516 | 539.4909 | 7.7103 |
Iron | 0.01293 | 0.4067 | 3.0594 |
Magnafloc 2025 | - | 0.6027 | 4.5334 |
Nickel | 0.05495 | 0.8641 | 6.4997 |
Phosphorus | 0.029095 | 0.9135 | 6.8838 |
Sodium hydroxide | 0.19837 | 32.8168 | 4.6943 |
Sodium bisulfite | 0.28559 | 118.1168 | 16.8962 |
Sodium sulfate | 0.03528 | 291.9019 | 41.7557 |
Sulfuric acid | 0.16002 | 10.8395 | 1.5505 |
Suspended solids | - | 10.2040 | - |
Water | 980,708.61 | 140.99 | 987,292.52 |
Zinc | 0.004849 | 0.1525 | 1.1473 |
Main techno-economic and profitability indicators
Table 6 shows the results of the main techno-economic and profitability indicators obtained when simulating the proposed wastewater treatment plant in SuperPro Designer®. According to Table 6, a total capital investment of USD $ 3.549 million is needed, with a working capital of USD $ 5,000 and a start-up cost of USD $ 322,000. The annual operating cost is of USD $ 486,000, with total earnings of USD $ 1.125 million and a unit processing cost of USD $ 0.22/kg. The batch time is approximately 64 hours, with a gross margin value of 56.94%, ROI of 22.16% and annual net profit of USD $ 786,000. Finally, the process can be considered profitable and feasible from the economic point of view, since the NPV obtained is positive (USD $ 3,361,000), the IRR is greater than 25% (29.61%) and the payback time is less than 5 years (4.51 years) [41,44,45].
Table 6 Main techno-economic and profitability results.
Indicator | Value |
---|---|
Total capital investment (USD $) | 3,549,000 |
Working capital | 5,000 |
Start-up cost | 322,000 |
Operating cost (USD $/year) | 486,000 |
Total revenues (USD $/año) | 1,125,000 |
Unit processing cost (USD $/kg) | 0.22 |
Batch time (h) | 63.85 |
Gross margin (%) | 56.94 |
Net profit (USD $/year) | 786,000 |
ROI (%) | 22.16 |
NPV (at 11,0% interest) (USD $) | 3,361,000 |
IRR (After taxes) (%) | 29.61 |
PT (years) | 4.51 |
In [21] the SuperPro Designer® simulator was applied for the comparison of Ave alternatives scenarios for the treatment of cheese whey wastewater originated in a Cheddar cheese factory. In this study, scenario 1 deals with a cheese whey wastewater treatment plant that produces butter, whey protein concentrate and food-grade ethanol. In scenario 2 the butter-making section is similar to scenario 1 with some differences in the concentration of whey proteins and in the removal of residual minerals from water. In scenario 3 the plant produces Manouri (a type of cream cheese) instead of butter. In scenario 4 the plant produces two types of whey protein concentrate, namely, a rich in whey lipids and the other a highly purified protein concentrate possessing improved functional properties. In scenario 5 the plant produces butter; whey protein isolate containing 95% protein and hydrolyzed-isomerized whey permeate syrup. The results obtained of total capital investment; NPV (at 7% interest) and PT for the Ave scenarios are as follows:
Scenario 1: USD $ 101,167,000; USD $ 162,310,000 and 2.50 years.
Scenario 2: USD $ 113,713,000; USD $ 140,942,000 and 2.85 years.
Scenario 3: USD $ 104,707,000; USD $ 297,599,000 and 1.76 years.
Scenario 4: USD $ 54,916,000; USD $ 326,802,000 and 1.01 years.
Scenario 5: USD $ 124,227,000; USD $ 284,209,000 and 2.03 years.
Other authors [26] modeled in SuperPro Designer® a covered lagoon process for palm oil mill effluent treatment coupled with biogas production, obtaining as a result that the simulated process is economically viable, with a NPV of USD $ 2,830,000, IRR of 14.3%, and PT of 4.66 years, while the total capital investment for this project is USD $ 5,649,000. Finally, in [29] SuperPro Designer® simulator was employed to determine the techno-economic parameters of an innovative piece of hybrid technology, named integrated anaerobic-aerobic bioreactor (IAAB), where the combination of anaerobic and aerobic processes into a single reactor is accomplished in order to surpass the limits of conventional methods of treating palm oil mill effluent. In this study, the IAAB was further optimized with this simulator for maximum biogas yield, while addressing its economic and environmental trade-offs. The results obtained of the total capital investment, NPV (at 7% interest), IRR and PT indicators for the Base Case are USD $ 5.3 million, USD $ 2.1 million, 13.2% and 5.1 years, respectively, while the values of these indicators for the Optimum Case are USD $ 5.8 million, USD $ 4.4 million, 17.9% and 4.1 years, respectively.
Estimation of direct fixed capital
Table 7 describes the main items included during the estimation of the direct fixed capital of the proposed wastewater treatment plant.
Table 7 Estimation of Direct Fixed Capital.
Item | Value (USD $) |
---|---|
Total Plant Direct Cost (TPDC) | |
Equipment purchase cost | 538,000 |
Installation | 222,000 |
Process piping | 323,000 |
Instrumentation | 108,000 |
Insulation | 0 |
Electrical | 54,000 |
Buildings | 242,000 |
Yard improvement | 81,000 |
Auxiliary facilities | 81,000 |
TPDC | 1,649,000 |
Total Plant Indirect Cost (TPIC) | |
Engineering | 412,000 |
Construction | 741,000 |
TPIC | 1,153,000 |
Total Plant Cost (TPC) = TPDC + TPIC | 2,802,000 |
Contractor’s fee (CF) | 140,000 |
Contingency (C) | 280,000 |
Direct Fixed Capital (DFC) = TPC + CF + C | 3,222,000 |
As can be seen in Table 7, the total direct cost of the plant amounted to USD $ 1.649 million, while the total indirect cost of the plant had a value of USD $ 1.153 million, to obtain a total cost of the plant of USD $ 2.802 million. Finally, the Direct Fixed Capital required by the project had a value of USD $ 3.222 million.
Annual operating costs
Table 8 shows the annual operating costs of the wastewater treatment plant. Taking into account the values described in Table 8, it can be indicated that the cost item that most influences the annual operating costs is the facility-dependent costs with USD $ 345,000/year (70.99% of the total). This is due to the strong depreciation and maintenance that the plant will tolerate, which were the options selected to estimate this item, as previously described. In second place are the costs for raw materials consumption, with USD $ 97,000/ year (19.96%), which has to do with the relatively high consumption of chemical reagents to carry out the different reactions of reduction, neutralization, precipitation and coagulation throughout the entire treatment system, while in third place is the labor-dependent (salary), with USD $ 19,000/year (3.91%).
Table 8 Annual operating costs.
Cost item | Value (USD $/year) | % |
---|---|---|
Raw materials | 97,000 | 19.96 |
Labor-dependent | 19,000 | 3.91 |
Facility-dependent | 345,000 | 70.99 |
Electricity | 15,000 | 3.09 |
Miscellaneous | 10,000 | 2.06 |
Total | 486,000 | 100.00 |
The annual operating costs determined in [21] for the Ave scenarios evaluated are the following:
Scenario 1: USD $ 37,973,000/year.
Scenario 2: USD $ 41,318,000/year.
Scenario 3: USD $ 43,436,000/year.
Scenario 4: USD $ 25,671,000/year.
Scenario 5: USD $ 33,356,000/year.
In [26], the annual operating cost is USD $ 3,217,000/year, while in [29] the value of this parameter is USD $ 3.0 million/year and USD $ 3.2 million/year for the Base Case and Optimum Case, respectively.
Annual costs for raw materials consumption
Table 9 breaks down the annual costs for the consumption of raw materials in the proposed wastewater treatment plant.
Table 9 Annual costs for raw materials consumption.
Raw material | Annual amount | Annual cost (USD $/year) | % |
---|---|---|---|
Calcium hydroxide | 12 MT | 2,174 | 2.25 |
Ferric chloride | 114 MT | 56,805 | 58.80 |
Magnafloc 2025 | 133 kg | 2,001 | 2.07 |
Sodium hydroxide | 41 MT | 13,240 | 13.70 |
Sodium bisulfite | 25 MT | 7,500 | 7.76 |
Sulfuric acid | 60 MT | 14,889 | 15.41 |
Total | - | 96,609 | 100.00 |
Analyzing the values in Table 9, it can be deduced that the reagent that most influences the annual costs for consumption of materials is ferric chloride, with USD $ 56,805/year (58.80% of the total), because it constitutes the reagent with the highest unit cost (USD $ 500/MT) and, in addition, is the reagent with the second highest consumption in the treatment process, with 114 MT. Sulfuric acid constitutes the reagent with the second greatest influence on this cost, with USD $ 14,889/year (15.41%), which is mainly due to the fact that it is the reagent with the third highest annual consumption, with 60 MT/year. Finally, the third reagent that most influences these costs is sodium hydroxide, with USD $ 13,240/year (13.70%), since it is the reagent with the fourth highest consumption (41 MT/year) and the second highest unit cost (USD $ 320/MT).
Conclusions
Through the use of the SuperPro Designer® simulator, a proposal for a chromic wastewater treatment plant was evaluated from the techno-economic point of view, in order to determine its main indicators of profitability and feasibility under the current economic conditions of Cuba. About 6,959.90 L/batch; 1,051.53 kg/batch and 5,881.89 L/ batch are generated for treated water, cake and recycled water, respectively. The item that most influences the annual operating costs is the facility-dependent costs (70.99%), followed by raw materials (19.96%) and salary (3.91%) costs. The reagent that most influences the annual costs for materials consumption is ferric chloride (58.80%), followed by sulfuric acid (15.41%) and sodium hydroxide (13.70%). A total capital investment of USD $ 3.549 million is required, with a direct fixed capital of USD $ 3.222 million and a start-up cost of USD $ 322,000. The annual operating cost, annual net profit, gross margin, and return on investment reached values of USD $ 486,000, 56.94%, USD $ 796,000, and 22.16%, respectively. The batch time is approximately 64 hours, while the unit processing cost is USD $ 0.22/kg. From the values obtained of NPV (USD $ 3,361,000), IRR (29.61%) and PT (4.51 years) it can be concluded that the proposal is profitable and feasible from the economic point of view.