Serviços Personalizados
Journal
Artigo
Indicadores
-
Citado por SciELO
-
Acessos
Links relacionados
-
Citado por Google
-
Similares em SciELO
-
Similares em Google
Compartilhar
Ingeniería e Investigación
versão impressa ISSN 0120-5609
Ing. Investig. v.30 n.2 Bogotá maio/ago. 2010
Thermistor formation using BaTiO3 powders synthesised by the Pechini method
Claudia P. Fernández Perdomo1 and Jorge E. Rodríguez Páez2
1Engineering Physics. Universidad del Cauca, Colombia. M.Sc. Student, Universidade Federal de São Carlos, Brasil. Researcher Grupo CYTEMAC. Physics Department, Universidad del Cauca, Cauca, Colombia. cpfernandez@unicauca.edu.co 2 M.Sc., in Science and Technology of Materials, Universidad Nacional de Mar del Plata, Argentina. Ph.D., Physics, Materials Physics specialty, Universidad Autónoma de Madrid, España. Professor, Coordinator Grupo CYTEMAC, Physics Department, Universidad del Cauca, Colombia jnpaez@unicauca.edu.co
ABSTRACT
Barium titanate (BaTiO3) is a compound of interest in the field of electroceramics which is widely used in the manufacture of capacitors, piezoelectric transducers and resistive devices having a positive temperature coefficient (PTCR) and in manufacturing pyroelectric and optoelectronic devices. Most of these devices are obtained by consolidating high purity, suitable sized particle ceramic powders; structured synthesis methods are required to ensure such requirements. BaTiO3 powders were synthesised by a polymeric precursor method (Pechini) in this work. Very pure, small particle sized, raw material was obtained. These powders were characterised using thermogravimetric and differential thermal analysis (TGDT), X-ray diffraction (XRD) and differential scanning calorimetry (DSC). The results indicated that samples treated at 650°C presented cubic BaTiO3 as unique crystalline phase. If a sample were treated at 1,100°C, the tetragonal phase having a c/a < 1.007 relationship was the main crystalline phase. Samples treated at 1,100°C showed ferroelectric-paraelectric transition at T ≈ 123°C. BaTiO3 tetragonal ceramic powders were uniaxially pressed and then synthesised at 1,200°C for 2 hours. These samples were electrically characterised. These samples' curves of electrical resistance versus temperature (R-T) showed their PTCR thermistor behaviour. Current-voltage (IV) variation was also measured at different temperatures.
Keywords: BaTiO3; electrical characterisation; Pechini; synthesis; thermistor.
Received: jun 19th 2009
Accepted: jun 25th 2010
Introduction
Thermistors having positive temperature coefficient (PTCR), based on the Ba-Ti system, are important functional materials having diverse applications, including demagnetisation in colour TV, starting devices for engines and compressors, surge protectors, thermal sensors and self-regulation heating components (Wegmann et al., 2007). Amongst such applications, their use as overload protection has awakened great interest because they help to improve the safety and reliability of electrical and electronic products. Overall demand for PTCR materials has become increasingly markedly during recent years. However, PTCR thermistors represent a great challenge for reducing transition temperature with the rapid development of computers, information systems, telecommunications technology and automobiles (Zhou et al., 2004, Wegmann et al., 2005). Normal technology requires high quality electronic ceramics, thereby leading to greater demands in processing these materials, including the synthesis of ceramic powder and its subsequent densification (Vinothini et al., 2005). One concern is thus to determine the effect of grain size on BaTiO3 dielectric properties (Frey et al., 1996), (Shih et al., 1994). There is also the problem of having a synthesis process guaranteeing certain properties of ceramic powders, mainly purity and particle size. Another problem is related to the difficulty of obtaining pieces of high density BaTiO3 using conventional sintering methods. This problem increases when powders having nanometric sized particles are used (Caballero et al., 1994). Current actual interest is thus focused on obtaining well-densified nanostructured ceramics for studying their properties (Cahn et al., 1990). BaTiO3 powders have been synthesised by sol-gel (Wang et al., 2006), mechanochemical (Ohara et al., 2008) and hydrothermal techniques (Habib et al., 2008). Unfortunately, there has been little interest in determining the effect of synthesis method on the functionality of devices shaped using such ceramic powders. The objective of this work was to obtain samples sintered from tetragonal BaTiO3 using ceramic powders which were synthesised by the polymeric precursor method (Pechini). These ceramic powders were characterised using thermogravimetric and differential thermal analysis (TGDT), X-ray diffraction (XRD) and differential scanning calorimetry (DSC). The electrical functionality of these samples was determined after they had been pressed and sintered at 1,200°C for 2 hours. The effect of the synthesis method on BaTiO3 microstructurale and electric properties was then analysed; the potential application of the BaTiO3 as thermistor and/or humidity sensor was considered for this analysis.
Experimental procedure
BaTiO3 ceramics powders synthesised by the polymeric precursor method (Pechini).
The ceramics powders were obtained using the Pechini method. Ethylene-glycol (Mallinckrodt 99.5%) was heated at 70°C and citric acid added (Mallinckrodt 99%) to obtain a 4:1 ratio between the compounds; it was necessary to ensure complete dissolution of citric acid. The system was cooled to room temperature. Barium carbonate (Mallinckrodt 99%) was separately dissolved in a 0.5M aqueous solution of nitric acid (Merck, 99.9%). This solution was added to the ethylene glycol-citric acid solution, leaving the mixture in agitation for 15 min. Titanium alkoxide, titanium tetrabuthoxide (TBT, 99.9% Acros) were diluted in 50 ml ethanol (Merck, 99.9%) to prevent the formation of a precipitate in the system .This was added slowly to the previous solution and kept in continuous agitation for 30 min to ensure complete homogenisation. One acidic condition was maintained in the system.
The mixture was then heated to 120°C-140°C, with constant stirring, to promote polyesterification reactions. These reactions led to the formation of a black resin which was heated at 250°C for 24h. The solid resulting from pre-calcination was ground using an agate mortar.
Characterising the ceramic powders obtained
The solid obtained was characterised using thermogravimetric and differential thermal (TGDT) analysis (DTA/TG V3.0G Universal TA Instruments) to determine the temperature at which the main physical-chemical events occur in a barium-titanium system.
X-ray diffraction was used to determine the crystalline phases in ceramic powders. A Philips PW1710 diffractometer was used for this with Cu Kα radiation (λ = 1.54A) in a 2θ range between 10° and 70° at 0.04° s-1 speed. The synthesised powders were analysed using differential scanning calorimetry (DSC) to determine whether a sample showed the tetragonal-cubic phase transition when temperature was increased.
Preparing the devices
The synthesised powders were uniaxially pressed using a hydraulic press (Carver 4350.L) and a 13 mm diameter die. The compacts obtained had a thickness of about 1mm.
Pressing curves were obtained to determine conditions for the "green" sample's optimum density. These curves recorded the sample's change of density as a function of applied pressure. The green density of pressed material was calculated measuring the pellets weight and volume (ρ = m / v). These samples were thermally treated by heating the tablets between 500 and 1,300°C for 2 hours to promote their densification.
Density changes were measured as a function of temperature to determine the best sintering parameters.
Microstructural and electrical characterisation
The electrical response of sintered samples was determined by registering the change in their resistances with temperature. Curves of current versus applied voltage were also obtained using the four-point standard method. A Keithley 2400 current source (50Pa resolution), a digital Keithley nanovoltmeter 182 (1 nV resolution) and a 330 Lakeshore temperature controller were thus used. The sintered samples' microstructure was analysed using a scanning electron microscope (SEM, Jeol 6460 LV). The sintered material was fractured and its "fresh" surface observed. These observations led to ascertaining average grain size and its morphology.
Results and Discussion
Differential thermal analysis (DTA) and thermogravimetric analysis (TG)
DTA/TG curves for one solid sample obtained by the Pechini method, and pre-calcined at 250°C for 24 hours, are shown in Figure 1.
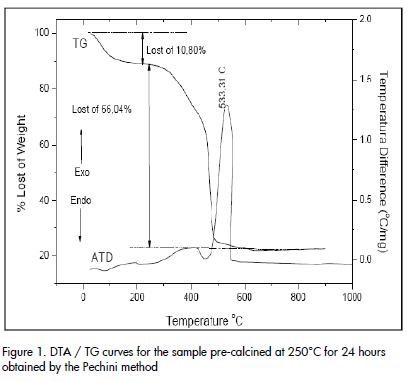
The TG curve ( Figure 1) showed a 10.08% weight loss from 50°C to 250°C which should be associated with the elimination of water present in the solid. Another weight loss occurred between 250°C and 500°C causing a loss of 66.04% due to the oxidation of the organic phase that existed in the sample. Two physical-chemistry processes should occur in this region as described in the literature (Duran et al., 2001). These processes are represented in the curve for two sections having a different slope: one between ~ 250°C and ~ 450°C and another between ~ 450°C and ~ 500°C. The first event was associated with the formation of a barium-titanium oxycarbonate and the second corresponded to its decomposition. No mass loss occurred above 500°C and the sample became a constant weight. The DTA curve (Figure 1) complemented the above information. The curve presented two exothermic peaks, one wide one around ~ 400°C and another sharp one at 533°C. They should be associated with oxycarbonate formation and sample decomposition favouring the crystallisation of the inorganic compound of interest for this work. The exothermic peak at ~ 533°C should also include information on BaTiO3 formation and crystallisation (Figure 1).
X-ray diffraction (XRD)
Figure 2a shows the XRD patterns of ceramic powder obtained by the polymeric precursor method (Pechini). The patterns showed the evolution of crystalline phases regarding temperature. The pre-calcined sample was completely amorphous and it crystallised when it was treated at 650°C for 2 hours. In this case, the only crystalline phase present was cubic BaTiO3 (PDF 75-0212) without the presence of impurities.
Figure2b shows the peaks corresponding to the crystal planes (200) and (002). If these peaks are carefully observed, and Lorentzian deconvolution used, they would indicate that the only crystallographic phase existing in BaTiO3 was the cubic one at 650°C. However, tetragonal BaTiO3 having c/a> 1.007 ratio was obtained when the sample was thermally treated at 1,100°C, during the same time.
Differential scanning calorimetry (DSC)
XRD patterns (Figure 2), indicated that was possible to obtain BaTiO3 at 650°C. The solid samples were subjected to thermal treatment between 900°C and 1,100°C, for 2h, to determine the most suitable synthesis temperature for promoting the presence of tetragonal phase and tetragonal to cubic transformation. (Figure 3), shows that the DSC curve for each of these solids indicated that the presence of the tetragonal phase only began to become evident from 1,000°C and therefore the tetragonalcubic transformation phase. The transformation was evident in solid thermally treated at 1100°C, for two hours, meaning that this temperature was selected for synthesising the raw material used in forming the thermistor.
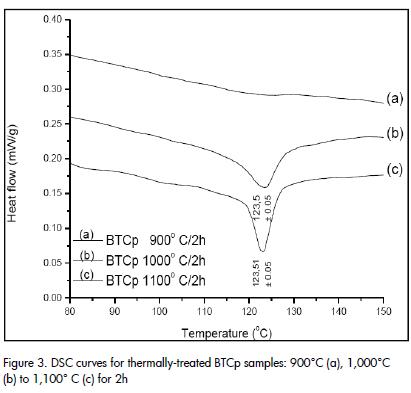
Forming ceramic devices
Figure 4a shows the density curve as a function of pressure for the solid formed from ceramic powders obtained by the Pechini method and treated at 1100°C. Figure 4 (a) indicates that density increased with increasing pressure. A 3.673 g/cm3 density was obtained by applying~ 170 MPa pressure. It was also noted that a constant maximum density value was not reached. Ceramic powders were uniaxially pressed at ~ 170 MPa pressure due to equipment limitations.
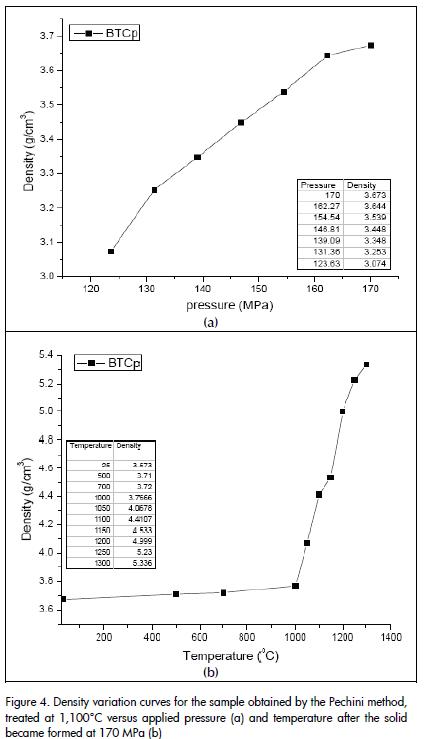
Once the green material was formed, it was then further sintered. These materials were thermally-treated between 500°C and 1300°C for 2 hours to help promote densification. The density of each sample was evaluated and averaged after each heat treatment. The same methodology was used for determining "green" solid density. Density curves were drawn from this data as a function of temperature (Figure 4b). It can be seen that there was no appreciable densification for temperatures below 1,000°C; higher temperatures only activated sintering mechanisms favouring rearrangement of the particles within the compact. This behaviour can be justified if the presence of agglomerated in the sample is considered. "Intra-agglomerate" sintering usually predominates for temperatures below 1,000°C (mass diffusion without contraction of the piece) and "inter-agglomerate" sintering is promoted above this temperature (neck formation and growth accompanied by contraction of the piece). The higher density obtained was 5,336 g/cm3 (89% ρteórica) at 1,300°C.
Electrical and microstructural characterisation
Once the sintered powder compact had been synthesised by the Pechini method at 1,300°C for two hours, its electrical response to changes in temperature was evaluated. Figure 5a shows a characteristic curve of resistance versus temperature (R-T curve), between 100°C and 170°C for a commercial PTCR thermistor. Comparing this curve with that for the solid obtained by the Pechini method Figure 5b), it can be concluded that the solid showed behaviour typical of a PTCR thermistor; resistance variation was becoming evident from 115°C onwards for the study material. Figure 6 shows hysteresis curves of resistance versus temperature, environmental conditions and in a vacuum to increase and then reduce heat. As can be seen, the sample showed more hysteresis when vacuum was increased in the analysis chamber (70 Pa); transition temperature also shifted to higher temperature.
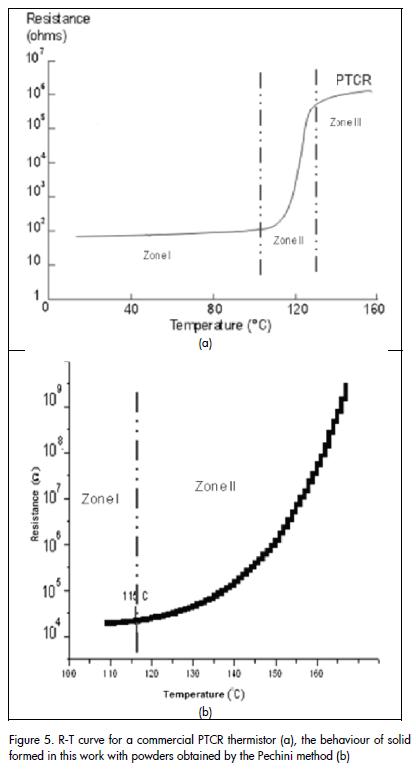
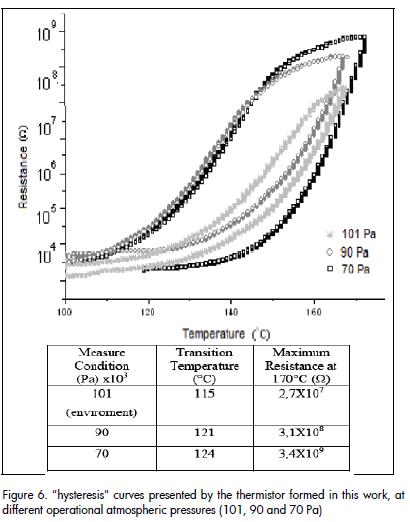
The current-voltage curves (I-V) for different temperatures and ambient pressure (Figure 7) indicated that increasing temperature increased resistance (higher slope value) which is typical behaviour expected for a PTCR device (i.e. they had ohmic behaviour within the measurement range used).
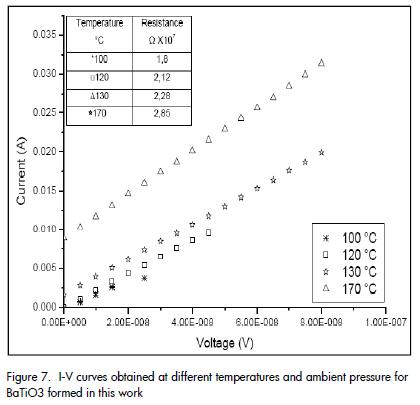
The presence of intergranular porosity can be noted from observing the microstructures of the sintered sample using SEM (Figure 7) and uniform grain size having spherical morphology; average grain size was ≈ 3.0679 μm. The average was obtained by analysing 50 data, using DMP 1000 ZView software. The porosity of the sintered sample presented may have been mainly generated by the presence of agglomerates in the powder. SEM observation of the sintered sample's microstructure (Figure 7) revealed the presence of intergranular porosity and uniform grain size, having spherical morphology and ≈ 3.0679 μm average grain size. This average was obtained by analysing 50 data, using DMP 1000 ZView software. The porosity of the sintered sample presented may have been produced by the presence of agglomerates in the powder.
Conclusions
PTCR thermistors were thus formed using powders synthesised by the Pechini method. The powders obtained showed BaTiO3 as a single phase from ~ 650°C onwards. Thermal treatment of these solids at T> 1,000°C favoured the presence of tetragonal versus cubic phase which prevailed for lower treatment temperatures. Tetragonal to cubic transition was evident in the powders treated at 1,100°C.
Shaped pieces were sintered with these powders synthesised by the Pechini method. These solids exhibited PTCR type thermistor behaviour which showed hysteresis when performing a heating-cooling cycle during the test. This electrical behaviour was affected by the atmosphere surrounding the device.
The results constitute an important basis for work being done in our research group. Our interest lies in shaping both capacitors and thermistor devices (Fernández et al., 2009) and humidity sensors using BaTiO3 powders synthesised by the Pechini method and shaped by the colloidal method.
Acknowledgements
This work was financed by Banco de la República Foundation project number 2348.
Special thanks are due to Dr. Ruben Vargas from the Universidad del Valle, Colombia, for the DSC measurements and the University of Cauca for project resource management.
Caballero, A. C., Fernández, J. F., Duran, P., Moure, C., Titanato de bario Cerámico., Boletín de la Sociedad española de cerámica y vidrio, Vol. 33, No.1, 1994, pp.5-21. [ Links ]
Cahn, R. W., Nanostructured materials., Nature, Vol. 348, No. 6300, Nov. 1990, pp. 389390. [ Links ]
Duran, P., Capel, F., Tartaj, J., Gutierrez, D., Moure, C., Heating-rate effect on the BaTiO3 formation by thermal decomposition of metal citrate polymeric precursors, solid state ionics, Vol. 141-142, May. 2001, pp. 529539. [ Links ]
Frey, M. H., Payne, D. A., Grain size effect on structure and phase transformations for barium titanate., Physics Review B, Vol. 54, No. 5, Aug.1996, pp. 3158 3168. [ Links ]
Fernández, C. P., Rivera, E. F., Rodriguez-Paez, J. E., Conformacion de Dispositivos Termistores con Coeficiente Positivo de Temperatura (PTCR)., tesis presentada a la Universidad del Cauca, para optar por el título de Ingeniero Físico, 2009. [ Links ]
Habib, A., Haubner, R., Stelzer, N., Effect of temperature, time and particle size of Ti precursor on hydrothermal synthesis of barium titanate., Materials Science and Engineering B, Vol.152, No. 1-3, Aug. 2008, pp. 6065. [ Links ]
Ohara, S., Kondo, A., Shimoda, H., Sato, K., Abe, H., Naito, M., Rapid Mechanochemical synthesis of fine barium titanate nanoparticles., Materials Letters, Vol. 62, No. 17-18, Jun. 2008, pp. 2957-2959. [ Links ]
Shih, W.Y., Shih, W.-H., Aksay, I.A., Size dependence of the ferroelectric transition of small BaTiO3 particles: effect of depolarization., Physics Review B, Vol. 50, No. 21, Dec. 1994, pp. 1557515585. [ Links ]
Vinothini, V., Paramanand, S., Balasubramanian, M., Synthesis of barium titanate nanopowder using polymeric precursor method., Ceramics International, Vol. 32, No. 2, Mar. 2005, pp. 99103. [ Links ]
Wang, X., Lee, B.I., Hu, M., Payzant, E.A., Blom, D.A., Nanocrystalline BaTiO3 powder via a sol process ambient conditions., Journal of the European Ceramic Society, Vol. 26, No. 12, May. 2006, pp. 23192326. [ Links ]
Wegmanna, M., Brönnimann, R., Clemens,F., Graule, T., Barium titanate-based PTCR thermistor fibers: Processing and properties., Sensors and Actuators A , Vol. 135, No. 2, Apr., 2007, pp. 394404. [ Links ]
Wegmann, M., Clemens, F., Hendry, A., Graule, T., Dispersion of lanthanoid-coated barium titanate in a paraffin-based extrusion binder system., Ceramics International, Vol. 32, No. 2, May. 2005, pp. 147-156. [ Links ]
Zhou, D., Chen, Y., Zhang, D., Liu, H., Hu, Y., Gong, S., Fabrication and characterization of the multilayered PTCR ceramic thermistors by slip casting., Sensors and Actuators A, Vol. 116, No. 3, Oct., 2004, pp. 450454. [ Links ]