1. Introduction
Sustainable energy means that human activities achieve a balance among economic, social, and environmental needs, covering the current requirements without harming the ability of future generations [1]. Most of the energy used today comes from fossil fuels, a non-renewable resource that has caused serious environmental problems, which have motivated the development of alternative energy sources, such as solar, wind, and biomass energies. Recently, environmental regulations have increased the production of biofuels as an alternative energy source and, in this context, hydrogen (H2) production from ethanol has been identified as an ideal energy carrier for the short-term [2] [3]. Currently, H2 is mainly produced from steam reforming of fossil fuels, however, the production of hydrogen from natural gas is always associated with the emission of greenhouse gases and local pollutant [4] [5]. Therefore, it is highly desirable to incorporate renewable sources for H2 generation to develop a more sustainable energy model. The Steam Reforming of Ethanol (SRE) is one of the most promising methods for H2 generation, because it can produce more H2 per mole of ethanol than other methods [6].
In addition, the most promising application for H2 as a power energy is a Proton-Exchange Membrane (PEM) fuel cell technology. Fuel cells not only eliminate toxic emissions, but also have a higher efficiency than internal combustion engines for converting the chemical energy of the fuel to electrical energy [7].
Currently, the commercially available and reliable PEMs convert directly the hydrogen into electricity, hence a fuel processing unit is required in order to transform the energy content of the ethanol into a hydrogen-rich stream [8]. Besides hydrogen, SRE also produces a small amount of CO (about 1%) that reduces the energy efficiency of the PEM fuel cell.
Since the electrodes of the fuel cell are typically made of platinum, which is very sensitive to CO poisoning, the CO concentration must be below 10 ppm [9]. Several methods for the removal of carbon monoxide exist, such as the preferential CO oxidation (PROX-CO), selective CO methanation, and selective diffusion through membranes. However, the preferential oxidation of CO (PROX-CO) is the most efficient and economic method [10] [11].
The design of an appropriate catalyst system for simultaneous catalytic reforming and PROX-CO allows to improve the overall efficiency of the fuel cells [11]. The nature of the support also plays an important role towards product selectivity and the deactivation behavior of the catalyst. Acidic supports like Al2O3 are more prone to deactivation on account of coke formation [12]. Suitable basic supports, such as CeO2 and La2O3 or mixed oxides, can inhibit carbon deposition to some extent [6] [13]. CeO2 has been broadly reported as an active support for both steam reforming and oxidation catalysts due to its structural properties [14] [15]. This oxide has a redox behavior that allows high oxygen mobility and enhance the oxygen exchange with the medium [16].
Additionally, it has been found that the addition of ZrO2 improves the redox properties, thus, oxygen mobility can be improved throughout the generation of a mixed system with a strong interaction, preferably as a solid solution in order to promote electronic distortions in the oxide framework. CeO2 also contributes to homogeneous dispersion of the metal, stability of the catalyst to high reaction times and temperatures, and reduces the sintering problems in the catalyst [7] [13] [17]. Biswas and Kunzru [13] studied the SRE for hydrogen production over Ni/Ce1-xZrxO2 (x = 0, 0.26, 0.59, 0.84 and 1) catalyst. They reported that Ni/Ce0.74Zr0.26O2 catalyst with 30 wt% metal load exhibited high catalytic activity and hydrogen selectivity (5.8 mole/mole of ethanol reacted) at a temperature of 600°C. At this temperature, the ethanol conversion was 100% and CO selectivity was 0.47. They suggest that the reason for the high activity could be the high oxygen storage capacity of cubic Ce0.74Zr0.26O2.
Noble metal catalysts based on Pt, Rh, Ru, Au [5] have showed good catalytic activity and resistance for SRE. Nonetheless, their main disadvantage is their high cost and the relatively low availability of noble metals. Among non-noble metals, Ni and Co are the most used in steam reforming processes [12] [18] [19] [20] [21] [22] [23]. Ni-supported catalysts showed good ethanol conversions and good selectivity for hydrogen production. However, the main drawback of these catalysts is their relatively poor stability in time, as the catalyst deactivation occurs mainly by carbon deposition. An option to improve the Ni-based catalysts activity and to diminish the catalyst deactivation is promotion with other elements. Promotion of Ni-based catalysts with rare earth oxides proved their efficiency for steam and, thus, these oxides were identified as promoters of carbon removal from the catalysts [24] [25]. Likewise, gold supported catalysts are more active and selective in the CO conversion at low temperature, than other noble metals [16] [26]. Haruta and coworkers [27] showed that gold nanoparticles with a diameter between 2 and 4 nm are very effective for the CO oxidation. Several factors, such as the size of the gold particle, its oxidation state [28] [29] and the nature of the support [30] [31] affect the catalytic activity in the PROX-CO reaction at low temperatures in the presence of H2. In this way, the choice of the synthesis method is crucial to control all these factors.
Therefore, the aim of this work is to obtain CO-free hydrogen suitable for fuel cell (PEM). For this purpose, a reaction system with double catalytic bed was used: the steam reforming of ethanol (SRE) was studied using Ni/CeO2-ZrO2 catalyst (Ni-CZ) and, subsequently, the reforming products gases passed through a second fixed bed reactor containing Au/CeO2-ZrO2 catalyst (Au-CZ) in order to carry out the selective CO oxidation (PROX-CO).
Initially, the effect of the temperature and the initial concentrations of ethanol and water were evaluated at space velocities above 55,000 h-1 to determine the conditions that maximize the H2/CO ratio. Conversion of ethanol was kept at 100% and the catalyst stability was evaluated at 600°C, during more than 160 h on stream. In the second part of the work, in order to obtain H2 grade PEM, the effects of O2 concentration in feed stream on the selective CO oxidation with Au-CZ catalysts were studied in the temperature range of 50-250°C. Catalytic stability test was also performed.
2. Experimental method
2.1 Catalyst preparation
The fluorite oxides Ni/Ce0.75Zr0.25O2 (Ni-CZ) were synthesized by a pseudo sol-gel method, based on the thermal decomposition of propionate precursors [32] [33] [34]. Ni load was applied in 3%, 5% and 7 wt%, resulting in catalytic systems labeled CZ, 3Ni-CZ, 5Ni-CZ and 7Ni-CZ, respectively. The precursor materials for Ce, Zr and Ni were cerium (III) acetate sesquihydrate, zirconium (IV) acetylacetonate and nickel (II) acetate tetrahydrate. These salts were separately dissolved in boiling propionic acid using a concentration of 0.12 mol l-1 in cation, at 100°C for 1 h, leading exclusively to propionate precursors. The three boiling solutions were mixed during 2 h under reflux and, then, the solvent was evaporated until resin was obtained. Finally, the resin was calcined under air at 500°C for 6 h, with a heating ramp of 2°C min-1. To load gold, the procedure reported by Lin et al. was followed [35]. A suitable amount of chloroauric acid (HAuCl4•3 H2O) was dissolved in 250 ml of stirred deionized water and sodium hydroxide solution was added for adjusting the solution pH at 6. Then, 2 g of Ce-Zr oxide were added, followed by heating the solution to 80°C and mixing it for 2 hours. After filtration and washing until Cl- ions-free, the resulted gold samples were dried at 60°C for 12 h under air.
2.2 Catalysts characterization
2.2.1ICP-AES and EDX
The Ni and gold load of fresh catalyst was determined by Inductively Coupled Plasma Atomic Emission Spectroscopy (ICP-AES, Perkin Elmer Optima 3300DV).
2.2.2 Temperature Programmed Reduction (TPR)
H2 - TPR experiments were performed in home-made equipment. A sample of 50 mg was reduced by flowing 25 cm3/min of 5% H2 in Ar through the reactor. The temperature of the reactor was raised from room temperature up to 900°C at a heating rate of 10°C/min.
Hydrogen consumption was measured by means of a Thermal Conductivity Detector (TCD). A desiccant (silica gel) trap was used to retain the H2O produced during the reduction reaction between the oxides on the catalyst and the H2 of the reaction stream.
2.2.3 X-Ray Diffraction (XRD)
Powder X-Ray Diffraction (XRD, Siemens D-5000) patterns were used to obtain information about the structure and composition of crystalline materials.
2.2.4 BET surface area
The Brunauer-Emmett-Teller (BET) method was used to determine the surface area and pore size of the catalysts by N2 adsorption/desorption at 77 K. Specific surface area was determined using an Asap 2020 surface area analyzer and Quantachrome Autosorb-1.
2.2.5 Scanning Electron Microscopy (SEM)
The morphology, shape and dimensions of prepared calcined catalyst powders were analyzed using a Scanning Electron Microscopy (SEM) JSM-6490LV equipped with Energy Dispersive X-ray (EDX) analyzer and SEM images were obtained.
2.3 Activity measurement
The effects of temperature, the initial concentrations of water and ethanol in SRE and the effect of O2 concentration on PROX-CO were tested. For the test, two tubular reactors in series were used. SRE was conducted at atmospheric pressure in a quartz, U-shaped, 6 mm ID fixed bed reactor located in an electric furnace.
The catalyst Ni-CZ was heated from room temperature to the reaction temperature (500- 700°C) under a flow of He gas controlled by Brooks Electronic gas flow meters. The reactant flow added to the inert stream was a liquid mixture of ethanol: water (steam to ethanol molar ratio, S/E = 3-7) pumped into the system using a 303 Gilson HPLC pump and introduced into the reactor using a needle device.
The steady state condition was reached approximately after 30 min of reaction. The carbon balance was close to 95% in all the experiments. The Gas Hourly Space Velocity (GHSV) was calculated by the flow rate input (Fo, L/min) at standard conditions divided by the catalytic bed volume (V, L). The catalysts were reduced in situ, prior to reaction, in a stream of H2 for 3 h with a total flow gas of 45 ml min-1 at 700°C and a heating ramp of 5°C min-1.
PROX-CO reactions were carried out in a system similar to the SRE reaction. Air was added to the effluent gases from the SRE, before entering the PROX-CO reactor, and the individual stream flow rate was controlled by mass flow controllers to achieve O2 concentration between 1 and 2%.
The reactor effluent was analyzed by an in-line assembly of two, in series, gas chromatographs. The first one was a GC HP 5890 series II equipped with a HP-PLOT/Q column (0.53 mm ID and 30 m length, Agilent Technologies, USA) for CO2, ethanol, and acetaldehyde. The second one was a GC HP 5890 A equipped with a Molecular Sieve 5A column (Agilent Technologies, USA) for H2, O2, CH4, and CO. The selectivity of CO oxidation was defined as the oxygen consumption during CO oxidation divided by the total oxygen consumption. There was no methane formation under the reaction conditions on PROX-CO reactor.
3. Results
3.1 Chemical and textural analysis
BET surface areas of the support CeO2-ZrO2, and the catalysts Ni/CeO2-ZrO2 and Au/CeO2-ZrO2 are given in Table 1. The surface area of the support CZ was 38.1 m2/g and decreased after metal impregnation.
These results suggest that the incorporation of metal significantly reduced the surface of the support, as reported by others [13] [15]. Presumably, the area reduction is due to the partial blockage of the pore surface by metal oxide particles. However, it can be observed that the surface area increases as Ni load increases.
3.2 ICP-AES and EDX
The compositions of the calcined catalysts, determined by ICP-AES and Energy Dispersive X-ray (EDX) coupled to SEM techniques are shown in Table 1.
Table 1 Catalyst surface area and metal loading on various catalysts

a Determined by ICP-AES
b Determined by EDX analysis
The measured compositions were close to experimental metal load. Furthermore, the EDX analysis of nickel catalyst performed in different points of the sample suggest that nickel concentration is homogeneously dispersed on the support.
3.3 XRD
Fig. 1 shows the XRD patterns of Ni-CZ and Au-CZ catalysts. The samples clearly evidenced the reflections corresponding to (1 1 1), (2 0 0), (2 2 0), (3 1 1), (2 2 2) and (4 0 0) planes of the Ce0.75Zr0.25O2 fluorite cubic structure (JCPDS Card No. 28-0271). In addition, no segregation phases of CeO2 or Z1O2 were detected; hence, Z1O2 is totally incorporated into the CeO2 lattice to form a homogeneous solid solution. [32] [33]. The results agree with those reported by Biswas and Kunzru [13] who prepared and characterized Ce1-xZrxO2 catalyst with different Ce/Zr ratios (x = 0, 0.26, 0.59, 0.84 and 1). They reported that diffraction peaks of ZrO2 were not observed up to a ZrO2 content of 59%, when Zr content increased to 84%. The peaks due to the crystal plane of ZrO2 were clearly observed, suggesting the incorporation of ZrO2 into the CeO2 lattice to form a solid solution.
3.4 TPR
The reduction profile of pure CeO2 is characterized by two peaks (not shown) widely reported [13] [36] [37]: one at low temperature centered at 503°C, which is generally attributed to the reduction of the surface layer of CeO2, and another small peak at a higher temperature centered around 752°C, which is attributed to the reduction of the material in the bulk. In the case of pure ZrO2, the TPR pattern did not show any evident reduction peak. Furthermore, for the studied support CeO2-ZrO2, the reduction peak at higher temperature was not present (Fig. 2).
This indicates that in the presence of ZrO2, the bulk reduction of CeO2 does not occur easily, most probably because the interaction between CeO2 and ZrO2 formed a solid solution, such as suggested by Biswas el at [13].
The TPR profile of unsupported NiO shows a board peak between 370°C and 420°C, which indicates the complete reduction of NiO [15] [21]. For Ni-CZ, a broad peak appears in the range from 350 to 550°C, however, the maximum peak around 580°C observed in CZ support disappears in all the supported Ni catalysts. It seems that the peak corresponding to Ce-ZrO2 shifts to lower temperatures and, thus, overlaps the NiO reduction peak.
Dong et al. [21] obtained similar results with Ni/Ce-ZrO2 and they explain that a strong interaction of Ni incorporation into Ce-ZrO2 makes ceria more reducible, which helps to produce mobile oxygen during the reforming reaction. It also can be noted that the intensity for the reduction peak of Ni-CZ catalyst increased significantly, indicating that the presence of Ni enhanced the reducibility CZ support. In another work, Moretti et al. [18] reported the multiplicity of reduction peaks at low temperatures with Ni samples, and they attributed it to the low interaction of the reduction of NiO with the support. Thus, the absence of reduction peaks at low temperature is in agreement with the XRD result showing the high nickel dispersion strongly interacting with the support.
3.5 Scanning Electron Microscopy (SEM)
SEM image of 7Ni-CZ are shown in Fig. 3. It shows that metal particles are uniformly dispersed on the CZ support. The NiO crystallite sizes in the prepared (fresh) catalysts are less than 100 nm with the exception of a few larger particles, which is in agreement with the results obtained from XRD data.
3.6 Catalytic activity
3.6.1 Steam reforming of ethanol
Blank tests in an empty reactor (thermal homogeneous reaction) of the reaction system, under the same conditions as the catalytic tests, were presented in a previous study [6]. The ethanol conversion was over 90% in the blank test, and although some H2, CH4, CO, and CO2 appeared at higher temperatures, the product distribution agreed with the decomposition and dehydration reaction, and the coke formation took place. Table 2 summarizes the effect of the Ni load over Ni-CZ during the SRE, as well as the effect of water on the SRE for a 4% mol ethanol sample.
Fig. 4 displays the product distribution after the SRE at different temperatures when H2O was varied from 12 to 25 mol% for 7Ni-CZ, which shows the best performance. In Table 2, it is appreciated that the maximum hydrogen production approach to equilibrium 5.9 mole per mole of ethanol consumed was obtained with the catalyst 7Ni-CZ at 700°C and S/E = 7, and for these conditions the ethanol conversion was 100%. According to the thermodynamics of the reaction, H2 production is favored at high temperatures by an excess of water. Sun et al. [38] reported the highest H2 yield and lower CO production at T > 627°C and S/E > 6 in the thermodynamic analysis of the SRE. Otherwise, it has been reported that using Ni(II)-Al(III) layered catalyst can be found an ethanol/water molar ratio that maximizes the ethanol conversion [6] [39] That decrease was attributed to a competition between ethanol and water for the same active sites. As observed in Fig 4, H2 yields continuously increased with H2O and temperature. Since there is not a significant difference in hydrogen production between 600°C and 700°C at 25 mole% of water, 600°C was selected as the temperature for stability test, considering additional energy requirements
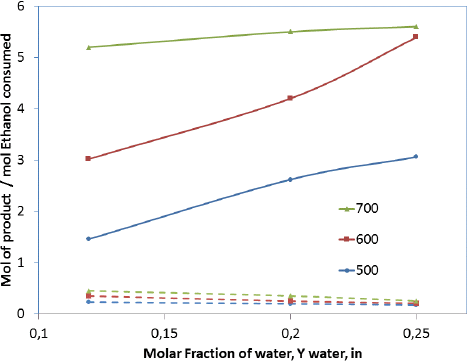
Figure 4 Selectivity of H2 and CO vs. water molar fraction and temperature in the steam reforming of ethanol over the 7Ni/CeO2-ZrO2 catalyst. For reaction conditions refer to Table 1.
3.6.2 PROX-CO
Fig 5 shows the effect of the pretreatments on the activity and selectivity of 2 Au-CZ catalyst. Before reaction, the catalyst was activated by oxidation (Oxd) in air at 300°C for 1 h or by reduction (Red) in a 10% H2/H mixture at 300°C for 1 h. It is noteworthy that both oxidative and reductive treatments lead to a similar catalytic behavior, since the light-off curves in both cases begin at 50°C and the conversion increased with the temperature until it reached a maximum of 99% and 95% at 100°C, with oxidative and reductive pretreatment, respectively.
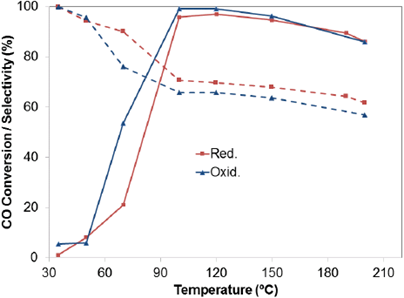
Figure 5 Effect of pretreatment. Reactant composition: 2% CO. 2% O2. 50% H2 and helium. Selectivity (dotted line); CO conversion (full line). Catalyst Au/CeO2-ZrO2.
This temperature is the most suitable temperature for the fuel cell operating conditions, and thereafter a slightly decrease was observed as the temperature of the reactor increased, indicating the activation of H2 oxidation reaction that competes with the oxidation of CO [40].
The oxidative pretreatment was selected considering that the nature of the reduced active sites leads a deactivated of the catalyst under the reaction stream [41] The nature of the reduced active sites makes the catalyst more vulnerable to be deactivated under the reaction stream.
The CO conversion and selectivity as a function of O2 concentration in the feed for the 2Au-CZ catalyst is shown in Figures 6a and 6b. As expected, the CO conversion (Fig. 6a) and the selectivity (Fig. 6b) strongly dependence on the O2 concentration. The catalytic activity rises with an increase of the oxygen amount in the reaction feed stream, while CO selectivity decreases. The same behavior has been observed with different types of catalysts in several reports in the literature [36] With O2/CO ratios 1.49, 0.75 and 0.46, the CO conversions are -99%, 99% and 84% at 100°C, respectively. The selectivity at the same temperature was 37%, 65%, and 97% for the O2/CO ratios of 1.49, 0.75 and 0.46, respectively. According to the results, 0.75 was selected as the best O2/CO ratio needed for oxidizing CO with high activity and minimal loss of hydrogen.
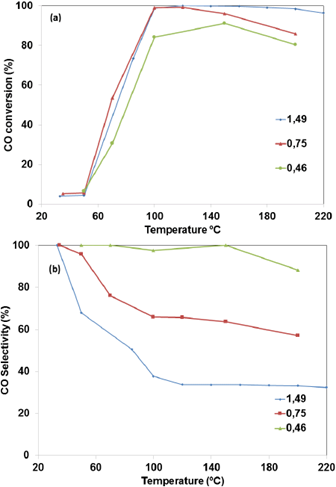
Figure 6 Effect of O2 concentration in reactant gas. Over Au- CeO2-ZrO2 (c) catalyst. Reactant composition: 2% CO. 0.5-2% O2. 50% H2 and helium. Selectivity (dotted line); CO conversion (full line).
It must be considered that the gases analyzed in PROX-CO reactor contained water and CO2. According to the products distribution in the effluent stream of the SRE reactor, the composition was 60% H2, 1-2% CO, 10-20 % CO2 and 210% H2O in volume. Jardim et al. [36] reported a negative effect of water and CO2 on catalytic behavior due to a competitive adsorption on the active sites and to the formation of surface carbonaceous deposits.
3.7 Stability tests
Stability is an important characteristic of any catalyst that determines its efficient use in a reaction. Figures 7a and 7b show the stability tests in SRE and PROX-CO, respectively. As explained before, the test was performed using two in series reactors. In the first one, SRE was carried out using 7Ni-CZ as catalyst and, then, effluent gas pass through the second reactor containing the catalyst 2Au-CZ, where PROX-CO reaction is carried out.

Figure 7 Stability test over 7Ni-CZ on the Steam reforming of ethanol (a) and 2Au-CZ on PROX-CO (b) catalyst. Reforming reaction condition: 3.5 mol% ethanol 21 mol%.
The results show that 7Ni-CZ and 2Au-CZ are active and selective for SRE and PROX-CO, respectively, during the time of the test. According to the results, the produced hydrogen (5.4 mole of hydrogen per mole of ethanol consumed) accomplish the requirements for use in a fuel cell, since CO conversion was about 100% with low hydrogen consumption
4. Conclusions
The steam reforming of ethanol and subsequent PROX-CO was accomplished over a Ni-CZ and Au-CZ, respectively. The variation of the initial concentrations of water showed a complete ethanol conversion and a maximum H2/CO ratio, when 25 mole% H2O and 4 mole% C2H5OH (S/E = 7) were used in the SRE over 7Ni-CZ at 700°C. The effect of the O2 concentration in the feed on Au-CZ catalysts showed that O2/CO ratio 0.75 is the suitable for higher oxidation of CO without lower hydrogen consumption.
The SRE stability was assessed under the selected conditions at 600°C, during more than 160 h on stream, obtaining ethanol conversions above 99% during the entire test and H2 productivity close to the ideal, 5.4 mole of hydrogen per mole of ethanol consumed. The PROX-CO test shows CO conversion of about 99% and selectivity around 64% for 50 h on stream.
The TPR, XRD and SEM characterization techniques confirm that the good metal dispersion and the promoted strong interaction in the Ni-CZ and Au-CZ catalysts contribute to the high activity selectivity and stability of the catalyst.