1. Introduction
Hybrid material, especially polymers based on nanocomposites represent a new class of material, and they are the object of a great deal of research. The interest in such systems (organic-inorganic material) is due to the fact that the ultrafine or nanodispersion of the filling, as well as the local interactions between the filling and the matrix, lead to a higher level of properties than their micro or macro composite equivalents [1]. The addition of nanoparticles as filling in a polymer matrix and an effective dispersion favor with the reinforcement of the polymers by changing their mechanical behavior. The barrier, thermal and rheological properties are improved depending on the dispersion degree, the type of polymer and organic clays [2]. Understanding the property changes as the particle (or fiber) dimensions decrease to the nanoscale level is important to optimize the resultant nanocomposite [3]. Among all the potential nanocomposite precursors, those based on clay and layered silicates have been most widely investigated, probably because the starting clay materials are easily available and because their chemical intercalation has been extensely studied for a long time [4]. Polymer-layered silicate nanocomposites, which are the subject of the present contribution, are prepared by incorporating finely dispersed layered silicate materials in a polymer matrix [5]. Nanocomposites, can be prepared by in-situ synthesis of inorganic particles or by dispersion of fillers in a polymeric matrix [6]. A correct selection of the preparation technique is critical to obtain nanomaterial with suitable properties [7]. However, the nanolayers are not easily dispersed in most polymers due to their preferred face-face stacking in agglomerated tactoids. Dispersion of the tactoids into discrete monolayers is further hindered by the intrinsic incompatibility of hydrophilic layered silicates and hydrophobic engineering plastics. Therefore, layered silicates first need to be organically modified to produce polymer-compatible clay (organoclay). In fact, it has been well-demonstrated that the cavities or galleries of the native clay silicate structure by alkylammonium surfactants can compatibilize the surface chemistry of the clay and a hydrophobic polymer matrix [8].
Among the potential nanocomposites precursors, those based on layered silicates (montmorillonite-MMT) have been more widely investigated. The phyllosilicates are naturally hydrophilic and, in order to increase their organophilic characteristics, the cationes in the gallery can be exchanged by cationic modifiers (e.g., quaternary ammonium salt). The modified clay (or organoclay) tends to show higher compatibility with organic polymers [9].
PET containers have a low weight and no emission of pollutants when burned, which confirm it as one of the most suitable materials for recycling and to promote environment conservation. From the environmental point of view, the resin is the one which shows the best suitability for recycling. Researchers and experts around the world are searching for alternatives to stop pollution generated by PET containers, and one of these alternatives is to reuse these materials.
The purpose of this research was to investigate mixtures of recycled PET (RPET) with Cloisite 10A to produce a higher viscosity product for recycling. Cloisite 10A is an organically modified montmorillionite with organic cations. The mixture was processed in a single screw extruder with an L/D=20 die, in order to produce high shear strain and promote dispersion of the clay in the polymer matrix, increasing the viscosity of the RPET. The resulting mixtures were characterized by XRD and SEM. The measurements of the flow properties at a laboratory can help describe the behavior taking place in the process. A single screw extruder capillary rheometer provides shear energy to the material during the test. The measurements are usually different from those obtained with an ASTM D 5422 - 93 piston-type capillary rheometer [10].
2. Materials
Cloisite 10A from Southern Clay Products, 2MBHT Organic Modifier with a concentration of 125 meq/100 g of clay, Moist ˂ Tactoidal Geometry. Typical particle sizes of the Cloisite 10A: Less than 10%: 2μm less than 50%; 6μm less than 90%; 13μm. Recycled polyethylene terephthalate (RPET) from Coca-Cola bottles in presentation of 500 mL and 1L and intrinsic viscosity of 0.77 dl/g. PET virgin (PET) was provided by M&G Polimeros.
3. Experimental
The preparation of mixtures of RPET/Cloisite 10A was carried out as follows. RPET was processed in a Besutelspacher single screw extruder with a temperature profile of 270°C at the feeding zone and 280°C at the fusion zone, at a speed of 30 rpm. The resulting material was in the form of pellet, with a diameter between 4-5 mm. the RPET/Cloisite 10A mixtures with 1, 3, 5 and 7% of clay by weight were integrated physically and then reprocessed in a Beutelspacher single screw extruder with a temperature profile of 270°C at the feeding zone and 280°C at the fusion zone, at a speed of 35 rpm. The resulting material was evaluated in a capillary rheometer-type single screw extruder according to the standard ASTM D 5422-93 with a capillary die at the outlet with L/D=20 at 10, 15 and 20 rpm. Later it was ground in a grinder with tempered steel blades and couter-blades, stainless steel screens, and a 6 mm opening net.
XRD experiments were performed in a Siemens D-500 diffractometer. The materials were scanned in the reflection mode using an incident. X-ray of CuK with wavelength of 1.54 A° at a stop size of 0.05°/min from 2ϴ=4 to 40.
The materials obtained from an extruder were analyzed in a rotational rheometer using plate geometry with diameter of 25 mm.
Surfaces of the prepared materials were analyzed and measured using a Scanning Electron Microscopy (SEM) JEOL model JSM-7401F with an acceleration voltage of 5 kV and a magnification of 50,000X. The samples were fractured cryogenically and coated with Au / Pd.
4. Results
Physical characteristics of the materials
Table 1 shows physical appearance of RPET/Cloisite 10A mixtures. All RPET/Cloisite 10A mixtures presented a light brown color and crisp consistency. Davis and collaborators in 2002 [11] report similar characteristics for PET nanocomposites and organic clays with ammonium salts.
During the measurements, the Delta pressure did not stabilize when measuring for RPET and for RPET/Cloisite 10A mixtures at a speed of 10, 15, and 20 rpm with concentrations of 0, 1, 3, 5, and 7% by weight of clay. Low viscosity of the RPET mixture prohibited a continuous flow during 2 minutes, as established by the standard. Although the measurement in the capillary rheometer-type single screw extruder was not successful, the collected data in each run are shown in Table 2 at different concentrations and 20 rpm of speed. Calculated mass and volumetric flow range data was extrapolated by software due to a lack of continuous extruder output flow, which is reflected in scatlered shear stress and shear rate volumes obtained with 10 and 15 rpm.
Table 1 Description of the physical appearance of RPET/Cloisite 10A mixtures with 0, 1, 3, 5 and 7% by weight of Cloisite 10A
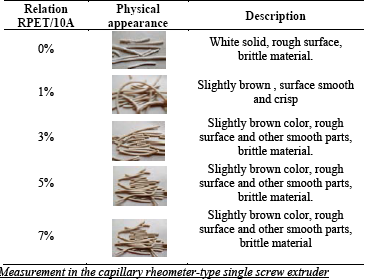
Source: The authors.
Table 2 Collected data with different concentrations of Cloisite 10A and 20 rpm of speed.
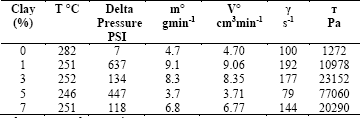
γ shear rate, т shear strain
Source: The authors.
X-Ray difraction (XRD)
Due to its ease and availability, XRD is the most common technique used to test the crystal structure of nanocomposites. By monitoring position, appearance and intensity of basal reflections of the distributed silicate layers, the structure of the nanocomposites (intercalated or exfoliated) is identified. In an exfoliated nanocomposite, extensive separation is associated with delamination of the original silicate layers in the polymer matrix. It happens if the resulting peaks are extremely wide or disappear completely. This indicates a complete exfoliation. On the other hand, for interspersed nanocomposites, finite expansion of layers associated with the intercalation of the polymer results in the appearance of a new basal reflection which corresponds to a higher elevation of the galleries. Intense peaks between 3° and 9° indicate an intercalated composite [12].
The resulting mixtures at the outlet of the capillary rheometer-type single screw extruder evaluated at a speed of 20 rpm were typified. Fig. 1 shows the diffractograms for the RPET/Cloisite 10A mixtures with 0, 1, 3, 5 and 7% by weight of Cloisite 10A. The lack of signal for the mixture with 1% by weight of Cloisite 10A indicates exfoliation of clay in RPET, Calcagno and collaborators in 2007 [13] report that the lack of signal in XRD is an indication of exfoliation of the clay, and with clay contents of 2% by weight, the presence of the intercalated state. The mixtures with 3, 5, and 7% by weight of clay showed a peak at 2ϴ=5.6° with a decrease in the intensity attributed to a high degree of periodic order present in the material. Barber and collaborators in 2009 [14] prepared mixtures of PET with Cloisite 10A, and the XRD analysis show that for pure Cloisite 10A, a peak appears at 4.60° with a d001= 19.1, corresponding to the lamellar arrangement of the clay. Kracalik et al. in 2007 [15] prepared mixtures of RPET/Cloisite 10A and obtained in XRD two peaks, one at 3° and another one at 5.6° with a decrease in intensity, which is attributed to a partial exfoliation.
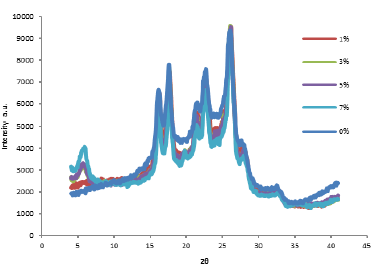
Source: The authors.
Figure 1 XRD patterns of the mixtures of RPET/Cloisite 10A to 0, 1, 3, 5, and 7% by weight of clay.
As the clay content increases in the mixtures, the peak at 5.6° reaches slightly higher values of intensity due to the presence of a higher number of tactoids in the mixtures. Wang and collaborators in 2006 [16] found in XRD that for mixtures of PET/MMT, a signal corresponding to MMT at 3.8° appears, which increases in intensity upon the increase of MMT concentration in PET. Similar patterns to those obtained for RPET in the 10-60° rank also appear when clay is added to the mixtures. This is an indication that thecrystalline form of PET remains the same after mixing with the organo-clay [17].
Rotational rheometry
Fig. 2 shows the graphics of viscosity against shear rate for PET, RPET and mixtures RPET/Cloisite 10A which were prepared at 20 rpm. At low shear rate in the rank of 1 to 87 1/s, the viscosity for the mixtures was lower than for PET and RPET due to the incorporation of clay in the mixtures, which causes degradation of RPET [18]. The viscosity of RPET/Cloisite 10A mixtures decreases as the shear rate increases. The decrease of the viscosity with increase of clay content may be due to a lubrication effect of the clay during the process of PET [19]. At shear rates higher than 309 1/s, the viscosity values were increased for the RPET/Cloisite 10A mixtures with contents of 1-7% by weight of clay, in comparison with PET and RPET due to the strengthening by clay in the polymer matrix. The properties of dynamic flow for RPET/Cloisite 10A composites reveal structural changes, both of them associated with the strengthening (formation of a physical net with the clay load) and aspect of degradation [15]. Very similar interactions are taking place between RPET and the clay for clay concentrations between 3-7% by clay weight, while there are greater interactions between RPET and clay with 1% by weight of clay due to the presence of the exfoliation state specified in XRD.
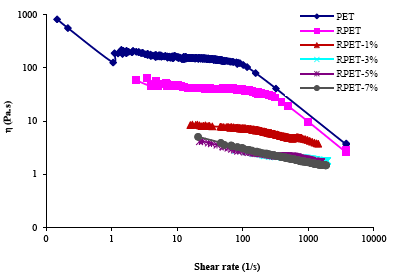
Source: The authors.
Figure 2 Graph of viscosity (η) (Pa.s) against shear rate (1/s), of the mixtures RPET/Cloisite 10A to 20 ppm with 0, 1, 3, 5 and 7 % by weight of clay.
Scanning Electron Microscopy (SEM)
Fig. 3 (a) shows the micrography of RPET at 3000 times where degraded fibers of RPET were found. Shirin and Izadyar in 2012 [20]report fibers of virgin PET. Fig. 3 (b, c, d, e) show the morphology of the RPET/Cloisite 10A mixture with 1, 3, 5 and 7% by weight of clay and 20 rpm; with 1% by weight of clay (Fig. 4 b) a great amount of particles smaller than 1 µm, and a small amount not larger than 5 µm were found. The value, according to specifications of reagent grade with regard to the size of the particle of clay varies from 2 µm to 13 µm. These results show that there is a good dispersion of clay in the RPET with a 1% of clay in the mixture because the size of the particles obtained is smaller than 1 µm. Fig. 3(c) shows the micrography for the mixture prepared with 3% by weight of clay. Both the morphology of RPET as well as the morphology of the clay is present. The surface presented particles with a size between 1 and 5 µm length, which are greater than those obtained for the mixture with a 1% by weight of clay. There are two fundamental factors in preparing nanocomposites: the mixing speed and the amount of clay present in the mixtures [14]. Fig. 3 (d) shows the micrograph for the mixture with 5% clay. The morphology of RPET is present, as well as big clay agglomerates on the surface, with sizes between 1 and 10 µm are obtained. In 2007, Lin and collaborators [2] report the presence of these forms of agglomerates for mixtures of different polymers with Cloisite 30B. Fig. 3 (e) shows the micrograph of the mixture with 7% by weight of clay. The presence of RPET fibers is observed as well as the existence of large particles of clay agglomerates in a rank of 1 to 13 µm, which indicates low integration of the materials. Other authors [13], [14], report the presence of this type of morphology in PET/Cloisite 10A nanocomposites, when this particular state is present. The XRD results show the presence of the tactoid state, pointing out that the speed at which the mixtures were prepared, as well as the concentration of clay is affecting dispersion, obtaining by this a low breaking in the tactoid order. The disappearance of RPET fibers also may also be a function of high clay content.
4. Conclusions
It is possible to synthesize RPET mixtures with Cloisite 10A. Measurement in the single screw presented instability at Delta pressure caused by the low viscosity of the RPET/Cloisite 10A at 10, 15 and 20 rpm.
XRD showed a lack of signal for the RPET/Cloisite 10A mixture with 1% by weight of clay, pointing out the exfoliation state generated when passing the mixture through a capillary rheometer-type single screw extruder with an L/D=20 at 20 rpm. For concentrations of RPET/Cloisite 10A mixtures with 3, 5, and 7% by weight of clay, XRD showed signals of decrease in intensity, indicating an increase in the spacing of interlayer by polymer interspersing. The XRD experiments show that there is no alteration in the crystalline form of RPET even after the process with clay, indicating that there is no total degradation of RPET due to the process to which it is subjected. There is a strengthening of clay in the RPET to shear rates higher than 309 1/s, which is reflected in the values of viscosity of the RPET/Cloisite 10A mixtures when percentages of clay increased. SEM indicates that the dispersion of clay is decreased with the increase of concentration of clay in the mixtures even when subjected to high shear to make them pass through a given capillary.