1. Introduction
Currently, Brazil is the largest sugar cane producer. In the first survey of the 2014/2015 crops, the estimated national production of sugar cane is 671.69 million tons, and only in the South Central region, production is estimated at 612.91 million tons. However, during the process of extracting the broth through milling, sugar cane bagasse is generated as residue. In Brazil, 95% of bagasse is used as fuel for generating electricity in steam boilers, process that results in the formation of bagasse ash [1].
In order to establish an average estimate of bagasse waste generation, it is provided that for each ton of processed sugarcane, 270-290kg of bagasse are generated [2], and each ton of bagasse produces 23.8kg of sugar cane bagasse ash [3].
Waste from agricultural processes have been currently used to improve the mechanical properties in concretes and mortars, such as rice hull ash containing a high amount of silica. The use of this residue brings innumerous advantages from the environmental point of view by reducing the impacts on the consumption of clinker, main component of cement, and a new provision for this residue [4].
The production of clinker emits CO2 due to thermal processes to which limestone is put through. Therefore, the inclusion of this type of waste reduces consumption of clinker, decreasing CO2 emissions without affecting the physical properties and mechanical cement. Another addition that could present pozzolanic activity is sugar cane bagasse ash, which also could replace clinker in certain proportion in cement manufacture [5].
In chemical composition of sugar cane bagasse ash, it is possible to find percentages of inorganic carbon (approximately 15%) which could damage the manufacture of concrete; therefore it is necessary to evaluate the real potential of this type of material as an addition in cement production and its subsequent application as a binder in concrete [6].
This residue has a large amount of silica in amorphous and/or crystalline state, and for this reason investigations are being conducted, which have shown that sugar cane bagasse ash has a great potential for incorporation into mortars and concretes [7-16]. Studies were also conducted in the production of ceramics [17-18], fibrocement compounds [19] and soil cement bricks [20]. In addition, cement production is one of the biggest responsibles for global CO2 emissions, mainly due to the calcination of limestone and burning of fossil fuels, being amongst the most carbon intensive industrial activities [5].
This study aims at evaluating the potential of replacing contents of SCBA to Portland cement, depending on its pozzolanic activity, assessing the feasibility of applications of this residue in the construction industry.
2. Material and methods
2.1. Materials
2.1.1. Sugar Cane Bagasse Ash (SCBA)
Samples of Sugar Cane Bagasse Ash (SCBA) were extracted directly from a settling pond (Fig. 1 (a)) of a sugar and alcohol plant in the city of Astorga, State of Paraná - Brazil. The ash extracted from the settling pond comes from a gas scrubber system (Fig. 1(b)). The sample was subjected to sieving through a sieve #30 (0.60mm) and was subsequently dried in an oven for 24h.
When the SCBA was dry, an in-natura sample was collected to pass through the calcination process in a muffle furnace with a heating rate of 10ºC/minute for 6h, at a temperature of 600°C [21].
2.1.2. Portland cement
The cement used was of High-Early-Strength (CPV-HES) [22]. This cement is free of additions, with superior characteristics to common cement. High Early Strength Cement is more finely ground than common cement.
2.1.3. Sand and water
Normalized sand was used [23], retained in the sieves #4 (4.8mm), #8 (2.4mm), #30 (0.6mm) and #50 (0.3mm). Drinking water was used to the manufacture of mortars.
2.2. Methods
The experimental work was divided in two stages. In the first stage, in-natura ash (INA) was sampled, prepared and characterized. Part of the collected sample was calcined at a temperature of 600ºC for 6h, generating calcined ash (CA). These two samples were characterized by X-Ray Diffraction, Infra-Red Spectroscopy, Differential Thermal Analysis (DTA) and Thermogravimetry (TG), to determine which of the samples had evidence of a greater amount of amorphous material.
In the second stage, the CA that presented more characteristics of amorphous material in the first stage was ground in a ball mill for 1h and 2h (CA-M1 and CA-M2), in order to increase the specific surface of the sample, enhancing the reaction area. The new samples, together with INA, were submitted to tests of bulk density, laser particle size, and specific surface area by the B.E.T method [24], Scanning Electron Microscopy (SEM), pozzolanic activity index and Thermogravimetry. Finally, compressive strength tests with partial replacement of SCBA of 10%, 20% and 30% to Portland cement were performed in order to verify capability of this substitution.
2.2.1. X-Ray diffraction
The mineralogical characteristics of INA and CA were determined by X-ray diffraction using a Diffractometer Philips X´Pert, with a 40kV voltage and 30µA electrical current. Measurements were obtained by the powder method, using radiation Cu Ka1, with λ 1.54056Å. The scan in 2θ was performed at 0.02 degrees every 1 second. Identification of the peaks was performed using the Philips software, based on the JCPDS.
2.2.2. Infra-Red spectroscopy (FIRTS)
FIRTS was performed in order to investigate the chemical composition of the sample. The analysis of vibrational spectroscopy in the infrared region was performed using a spectrophotometer 2000 model ABB BOMEM FTLA, operating in the region of 4000 to 400cm-1, with resolution of 2cm-1 and 12 accumulations by spectrum. Samples of INA and CA were analyzed using the KBr tablets technique.
In this analysis, when a molecule presents itself symmetric according to a continuous order, it means that the atoms are arranged in a crystalline network. However, a crystalline compound may exhibit symmetric and asymmetric vibration in a specific wavelength, while an asymmetric molecule has a high degree of disorder in its network, being classified as amorphous material, which points to the same type of vibration, though at various wavenumbers, then performing a deformation in the spectrum.
2.2.3. Differential thermal analysis and thermogravimetry
These tests are intended to verify the glass transition temperature and the loss on ignition, respectively. For this, the equipment NETZSCH STA 409 CD was employed. Samples of INA and CA were submitted to a heating rate of 10ºC per minute until reaching 1000ºC, under nitrogen atmosphere.
2.2.4. X‐Ray fluorescence spectrometry
To determine the composition of INA and CA, a semi-quantitative analysis of X‐Ray Fluorescence Spectrometry was performed in a Phillips equipment, model PW 2400, with a 3kW tube and rhodium target (Rh).
2.2.5. Specific mass, specific surface and particle size
With these tests begins the second experimental stage, where calcined ash was ground for two periods, of 1 and 2h, using a ball mill of 400mm diameter.
To obtain the specific mass of the cement and ash samples (INA; CA; CA-M1 and CA-M2), a test was performed using the Le Chatelier bottle [25]. The specific surface analyses of the same ash samples were performed using the equipment QUANTACHROME model NOVA 1200. Samples were prepared in a vacuum system at a temperature of 150ºC for 3h, where the surface area was measured by nitrogen gas adsorption according to the B.E.T. method (Brunauer, Emmet e Teller). The particle size characteristics of the samples were determined through laser particle size tests with a Cilas 1064 Granulometer.
2.2.6. Analysis by Scanning Electron Microscopy (SEM)
Analysis by Scanning Electron Microscopy (SEM) was performed to evaluate the morphology of the INA, CA-M1 and CA-M2 particles. The equipment used was a spectrophotometer model FEI Quanta 200, with operating voltage and current of 20kV and 94μA, respectively.
2.2.7. Pozzolanic Activity Index (PAI)
The pozzolanic activity index has the purpose of presenting the reactivity of the material to be tested. The test was performed with cement CPV-ARI and with INA, CA, CA-M1 and CA-M2.
The test involved the replacement of 35% in mass of Portland cement by the material with possible pozzolanic characteristics to produce a trace of mortar 1:3 (cement: aggregate) [26]. The consistency of these mortars was set at 225 ± 5mm, obtained by the test in the consistency table.
2.2.8. Compressive strength in mortar
In order to determine the compressive strength of mortars, three cylindrical specimens of 5x10cm were molded. The ratio water/cement (w/c) of the samples was fixed at 0.48 and the reference mortar had a ratio of 1:3 (cement: aggregate) in mass. In this trace, substitutions were performed of 10, 20 and 30% of HES cement by sugar cane bagasse ash, calcined and ground for 1 and 2h (CA-M1 and CA-M2). Table 1 shows the mix proportions for compressive strength tests.
At 24h, the mold is removed and the specimen is stored in a standard curing room. After cured for 28 days, the compressive strength tests are performed according to brazilian norm 7215 [27].
2.2.9. Statistical analysis
For the study of pozzolanic activity index and compressive strength, a statistical analysis was performed by Tukey’s test in the software Statistica. Therefore, it was taken into account that when the p-value was less than 5% (0.05) there would be a significant difference between the values studied [28].
3. Results and discussion
3.1. X-Ray diffraction
The INA and CA diffractograms are presented in Fig. 2, where the presence of quartz is detected, which is an undesirable material because it is inert and therefore does not present any reactivity in terms of pozzolanic activity.
The presence of SiO2 in the form of quartz can be attributed to several factors, such as contamination while cutting cane and the contamination of the bagasse that is exposed in the industry patio, because not every residue enters the furnace after the grinding process, and some remain in the open until returning to the furnace. Moreover, in the case of industries that use the gas scrubber system, where the ash is deposited in settling ponds, contamination can occur due to the action of the winds.
According to the diffratograms, INA and CA silica showed peaks in the crystalline form. However, it can not be affirmed that there is no presence of amorphous silica in the samples as amorphous structures are difficult to detect by the diffractometer, especially when they are present in small amounts.
3.2. Infra-Red spectroscopy (FIRTS)
Fig. 3 shows spectrograms of INA and CA, respectively. All the bands observed in the spectrum are assigned to the fundamental vibrations of silica, which are listed in Table 2, except for the band observed in 1881cm-1, which is attributed to the symmetric stretch C=O of CO2 adsorbed in the sample. The bands were very wide and poorly defined for each wave number, which can be attributed to a vibrational deflection in the network, i.e., the spectrum shows the presence of intermediate structures (amorphous and crystalline). However, the spectrum did not show large noise, confirming that most of the sample is in crystalline form.
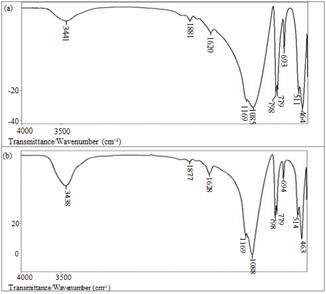
Source: Authors.
Figure 3 (a) Infrared spectrum of in-natura ash. (b) Infrared spectrum of calcined ash.
The differences shown between in-natura and calcined samples refer to a minimal change in the CO2 band in the spectrum of the calcined ash, and there was also an increase and a greater narrowing of the band around 690cm-1 for calcined ash, which is assigned to the band of deformation of the Si-O-Si ring characteristic of the quartz type silica.
The spectra of INA and CA may be pointing to amorphous structures around the bands 1189 and 1085cm-1, due to bandwidth and asymmetric stretching of Si-O-Si ring.
3.3. Differential thermal analysis and thermogravimetry
The differential thermal analysis in INA and CA corroborate the results found in X-ray Diffraction and Infrared Spectroscopy for the presence of quartz fragments in the samples, shown in Fig. 4 (a) and (b).
For mass loss, the thermogravimetric curve for INA and CA showed an insignificant change, as presented in Fig. 4. The values show a loss in mass of 0.2% for in-natura ash and 0.6% for calcined ash. This demonstrates that the burning of the SCBA occurred efficiently, with minor amounts of carbon in the samples.
The minimum CA mass loss occurred as expected, for having gone through a calcination process. The mass loss values were close to those reported in the literature, 0.8% [4], 0.9% [31], and 1% and 0.9% [7].
3.4. Scanning Electron Microscopy (SEM)
The particle morphology of the INA is presented in Fig. 5. We can observe a major presence of quartz particles in Fig. 5 (a) with different grain size and rounded edges. The INA is composed of particles with highly porous cell structure, as shown in Fig. 5 (b).
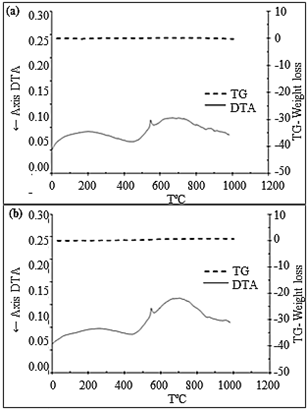
Source: Authors.
Figure 4 Differential Thermal Analysis and Thermogravimetry of INA (a) and CA (b) under inert condition (nitrogen gas)

Source: Authors.
Figure 5 Scanning electron microscopy showing the morphology of in-natura ash - (a) quartz particles with 200x magnification and (b) particles of porous cellular structure with 600x magnification.
Fig. 6 (a) presents the CA-M1 sample with 8.000x magnification, and Fig. 6 (b) shows CA-M2 with the same magnification. There is a reduction in much of the grain size and even a certain homogenization, compared to in-natura ash (Fig. 5). It is observed that the structures of ground ash (1 to 2h) are similar in size and have different shapes. A similar result was found in the literature [4-6; 32-33].
3.5. X‐Ray fluorescence spectrometry
Table 3 shows the chemical composition of samples obtained by X‐Ray Fluorescence Spectrometry. It is observed that, after calcination, the CA did not suffer large variations in chemical composition, in mass, in relation to INA.
The chemical analysis revealed the presence of 92.9% to 93.1% of SiO2, higher values than those found in studies performed by [6-8,7-11,18,31-39]. Furthermore, the samples tested in the experiment showed a low concentration of MgO, K2O and P2O5 impurities when compared to the studies performed by the same authors.
3.6. Specific mass and specific surface
The results of specific mass are presented in Table 4. It is believed that the increase in density of the CA-M1 and CA-M2 ashes may be related to the mineralogy of the material, because the mineral composition could influence the specific mass, porosity and water absorption of a rock [40].
According to Table 4, it is observed that the grinding of the ash calcined for 1h increased fineness of the sample twice, while the grinding for 2h increased three times the specific surface area of the ash, in relation to ash in-natura, whereas higher specific surfaces tend to influence the speed of the pozzolanic reactions.
3.7. Particle size distribution
The particle size curve allows distinguishing and quantifying different diameters of grains as well as identifying the distribution of grains of a given material. Fig. 7 shows the particle size curve determined as a function of mass retained or accumulated retained mass in percentage.
It is observed that the particle size curve of gray in nature (INA) presented a D50 equal to 0.075mm. Regarding ground SCBA, CA-M1 had D50 equal to 0.0037mm, which is approximately 20 times smaller than the INA. CA-M2 had D50 equal to 0.0030mm, approximately 25 times smaller than the ash in-natura.
3.8. Thermogravimetry of cement pastes
The results of thermogravimetry for assessing the pozzolanic activity in cement pastes with 35% cement replacement by CA-M1 and CA-M2 are listed in Table 5 and Fig. 8.
Table 5 Estimation of Ca(OH)2 content in Portland and SCBA cement pastes through thermogravimetry
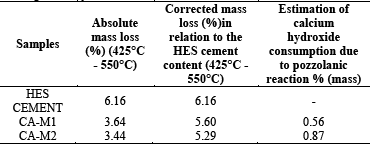
Source: Authors
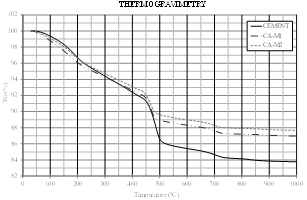
Source: Authors
Figure 8 Thermogravimetry of the cement paste and the cement pastes with ash ground for 1 to 2h
Calcium hydroxide consumption can be obtained through the mass loss between temperatures of 425°C and 550°C, when comparing the reference cement paste with the SCBA cement pastes. As illustrated in Fig. 8, it is noted that there was a weight loss for the CA-M1 and CA-M2 ashes, indicating the consumption of Ca(OH)2 in pastes.
Thus, it can be said that sugar cane bagasse ash presented pozzolanic reactivity characteristics similar to fly ash, at 21 days for 35% substitution [41].
3.9. Pozzolanic Activity Index (PAI)
For the material to be considered as pozzolanic, PAI should not be less than 75% of the compressive strength of the reference mortar [42]. As demonstrated in Fig. 9, INA and CA did not present PAI greater than 75%. Thus, it is shown that the grinding times of 1 and 2h made the ashes reactive, confirming the pozzolanic activity.
For this analysis, the Tukey’s test was performed in the software Statistica. The test result (Table 6) showed no significant differences at the 5% level of probability between the ash samples ground for 1 and 2h, though these samples were significantly different from reference mortar, in-natura ash and calcined ash, indicating that the grinding process is critical to making the SCBA reactive.
Therefore, for compression strength tests only substitutions with CA-M1 and CA-M2 were used, replacing 10, 20 and 30% of Portland cement.
3.10. Compressive strength of mortars
Fig. 10 shows the compressive strength of mortars with SCBA replacement and reference mortar.
Table 6 Results of Tukey’s test for PAI
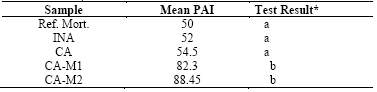
* Different letters in the column indicate significant differences at 5% by the Tukey’s test.
Source: Authors
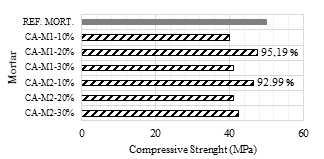
Source: Authors
Figure 10 Compressive strength in mortar with partial substitution of 10, 20 and 30% SCBA, ground for 1 and 2h, to Portland cement.
After the grinding process of SCBA for 1h, an increase of the compressive strength was observed for the mortar produced with replacement of 20% of cement by SCBA, namely a 5.8% increase in the mechanical strength. This percentage of replacement was the same found in the literature [7,9,10].
For the ash ground for 2h, there was a small decrease in compression strength in the proportions of 20 and 30% of replacement, corresponding to a decrease of 8.2% and 6.4% of resistance, respectively. As occurred with the ash CA-M1-20%, the ash CA-M2-10% presented higher mechanical strength than the reference mortar, of 3.3%. This percentage of replacement was the same found in the literature [5,8,43-44].
The ashes CA-M1-20% and CA-M2-10% presented the same water/cement ratio and the same consistency, of about 285mm. Since the ash ground for 2h has nearly twice the specific surface of the ash ground for 1h, it is understood that 10% of the addition is sufficient to achieve the same properties of the ash CA-M1-20%, thus justifying an increased mechanical strength greater than the reference mortar for the fraction with 10% replacement of SCBA to Portland cement. A study shows that the replacement of 10% of SCBA results in better results of compressive strength [5].
Table 7 shows the results of the statistical analysis from the Tukey’s test, at 5% level of probability, in order of increasing resistance to medium compression.
The only sample that significantly differed from the reference was CA-M1-10%, which also obtained the lowest average resistance. Since the other samples showed no significant differences from the reference, all of them could be used. However, since the number of repetitions was small (n=3), it is recommended that studies with more samples are conducted to ensure this condition.
4. Conclusion
The silica present in the in-natura ash is presented largely in crystalline form, decreasing the reactivity of the material, hence presenting low pozzolanic activity. However, the calcined ash that passed through the grinding process led to increased reactivity confirmed by specific surface, laser particle size, scanning electron microscopy and pozzolanic activity index, since the ashes presented a specific surface area of 3.52m²/g for 1h of grinding and 4.67m²/g for 2h of grinding.
Mortar compressive strength tests indicated that the greater average resistance to compression obtained was for substitutions of up to 20% of cement by CA-M1 and up to 10% of cement by CA-M2, with increased mechanical resistance compared to the reference mortar, at 28 days.
According to the results of the experimental program, it was possible to confirm the potential use of sugar cane bagasse ash in partial replacement of Portland cement in the production of mortars. SCBA presents the physical and chemical properties of a pozzolanic material [42], evidenced by physical and chemical testing and by the pozzolanic activity, since the pozzolanicity of SCBA was confirmed by the thermogravimetry test.