1. Introducción
La escoria de aluminio es uno de los principales residuos que resultan del proceso de fusión de aluminio y se produce debido a la reacción química que ocurre entre el metal líquido y la atmósfera. En general este residuo representa más del 4% de la producción total de aluminio primario y 20% de la producción secundaria [1]. Aunque la composición exacta de la escoria de aluminio depende de la aleación que se está fundiendo y los parámetros del proceso, la escoria proveniente de la industria primaria está compuesta principalmente por aluminio en forma metálica, óxido de aluminio, nitruros y otros óxidos.
La escoria de aluminio se puede clasificar en tres tipos: escoria blanca, escoria negra y saltcake [2]. La escoria blanca proviene de la industria primaria, contiene grandes contenidos de aluminio y su color es claro, de ahí se deriva su nombre. La escoria negra se produce durante la producción secundaria de aluminio, es decir, por reciclaje en el que se utilizan flujos salinos los cuales oscurecen la escoria resultante. Saltcake resulta del reciclaje de escorias blancas y negras, y en este proceso también se utilizan sales que la hacen oscura, tiene menos cantidad de aluminio que los otros dos tipos de escorias.
A pesar de ser un residuo, la escoria de aluminio es considerada un material valioso principalmente por su alto contenido de aluminio metálico, el cual puede ser recuperado utilizando diferentes procesos [3-5]. Además, posee otros compuestos que la hacen apta para otras aplicaciones, como por ejemplo: fabricación de cemento de aluminato de calcio [6], obtención de materiales compuestos [7-8], fabricación de refractarios [9], refuerzo de materiales compuestos [10], y síntesis de diferentes compuestos [11-13].
Se ha considerado que debido a su estabilidad térmica hasta temperaturas de 1100 °C [14] tiene potencial para ser utilizada en almacenamiento de energía térmica. A pesar de todo esto, aún no se le ha encontrado un uso a la escoria a gran escala, lo cual es una preocupación ya que es descartada en rellenos sanitarios bajo condiciones especiales, esto acarrea costos para las empresas, y lo que es más preocupante un costo ambiental.
Los diversos usos de la escoria de aluminio muestran la importancia de su caracterización, ya que el primer paso para la reutilización de un material es saber su composición. Algunos trabajos muestran la caracterización química de este tipo de material [6,14], sin embargo, en estos casos se utiliza la técnica de fluorescencia de rayos X que en realidad solo detecta la presencia de los elementos presentes y no las fases cristalinas que se formaron durante el proceso de oxidación. La técnica de difracción de rayos X ha sido utilizada para identificar las fases cristalinas presentes en escorias de aluminio [4] y hasta para hacer análisis semicuantitativos [8].
El análisis cuantitativo de la escoria de aluminio es difícil debido a su heterogeneidad y a la gran cantidad de fases que la componen, sin embargo, la técnica de difracción de rayos X (DRX) es un método viable en este caso, pues permite no solo identificar las fases cristalinas presentes en un material, sino que también posibilita la cuantificación de las fases de una forma precisa [15].
La determinación de la relación entre el tamaño de partícula y la composición de la escoria es interesante con la finalidad de encontrar los posibles usos que se le podría dar, es decir, en términos de escoger el material con la composición más adecuada para una aplicación específica. Por ejemplo, la escoria con contenidos de Aluminio superiores al 20% se reprocesa para producción de aluminio secundario, sin embargo, si el contenido de aluminio es inferior se dificulta el reciclaje y es descartada. Por otro lado, la utilización de escoria con contenidos de aluminio de aproximadamente el 10%, que generalmente es el residuo del proceso de reciclaje, podría ser utilizada como una fuente de hidrógeno a partir del AlN [16] y para reducir las emisiones de CO2 en la industria del acero [17]. Además, uno de los problemas de descartar la escoria de aluminio en rellenos es la generación amonia debido a la reacción del AlN con vapor de agua, por lo tanto, la cantidad de AlN debe ser lo suficientemente baja para poder descartarla en rellenos de manera segura [5].
Todo lo anterior muestra la importancia de conocer la composición de la escoria y su relación con el tamaño de partícula, sin embargo, poco trabajo ha sido realizado al respecto. Por ejemplo, Hiraki y Nagasaka (2015), encontraron el contenido de aluminio, nitruro de aluminio y cloro, para escorias con tamaño de partícula entre 20 y 800 µm.
El objetivo principal de este trabajo es determinar si hay una relación entre el tamaño de partícula y la cantidad de cada una de las fases cristalinas presentes en una escoria blanca de aluminio. Para el cálculo del porcentaje de cada una de las fases se utilizó la técnica de difracción de rayos X, específicamente el método de Rietveld [18]. Para determinar estadísticamente si la composición del material es influenciada por el tamaño de partícula, se realizó un análisis estadístico utilizando ANOVA.
2. Metodología
2.1. Caracterización del material
En este estudio se utilizó una escoria blanca proveniente de la producción primaria de aluminio, con tamaño de partícula inferior a 3.35 mm y una masa aproximada de 6 kg. Inicialmente, se realizó la separación granulométrica del material utilizando tamices con abertura de malla de 0.42, 0.85 y 1.68 mm. Se obtuvieron cuatro fracciones granulométricas: E1 (-0.42mm), E2 (+0.42mm, -0.85mm), E3 (+0.85mm, -1.68mm), E4 (+1.68mm, -3.35mm). De cada una estas fracciones se tomaron dos muestras representativas, de aproximadamente 10 g cada una. Los elementos químicos presentes en las muestras fueron determinados por microanálisis de rayos X (EDS) en un microscopio electrónico de barrido (SEM). Las fases cristalinas se identificaron utilizando los espectros de difracción de rayos X.
2.2. Método de Rietveld
Para el análisis cuantitativo con difracción de rayos X el tamaño de partícula fue reducido a un tamaño de 0.45 µm utilizando un molino de hierro de vibración excéntrica. Los ensayos de difracción se realizaron en un difractómetro Rigaku Multiflex operando a una potencia de 40 kV y 20 mA, geometría Bragg-Brentano θ/2θ, y radiación Cu kα. El barrido se hizo en el rango de 2θ desde 6 hasta 110°, a un paso de 0.02° y con un tiempo de barrido por paso de 8 s. Para determinar el porcentaje en peso de cada una de las fases se realizó un refinamiento de los espectros de difracción utilizando el método de Rietveld, utilizando el programa GSAS+EXPGUI [19-20]. La línea de base fue ajustada con la función analítica de Chebyschev, el perfil de los picos de difracción se ajustó utilizando una función Pseudo-Voigt modificada. Los factores refinados fueron: factor de escala individual, desplazamiento de la muestra, parámetros de red, factor de Gauss y factor de Lorentz del perfil de pico. El parámetro de asimetría se refinó únicamente para las fases que presentan picos a bajos ángulos. La orientación preferencial se corrigió utilizando la función de armónicos esféricos implementada en el programa. Finalmente se aplicó la función de Suortti para corregir rugosidad.
La calidad del refinamiento fue evaluada por el análisis de los factores RE , Rwp y S (goodness of fit) que se definen a continuación [21]:
Donde N es el número de puntos medidos, P es el número de parámetros que se están refinando, yi es la intensidad medida en el paso i, y wi = 1/ yi .
RE es el valor esperado de Rwp que se define como:
Donde yci es la intensidad calculada en el paso i. Unos buenos resultados llevan a un valor de Rwp entre 2 y 10% [22]. Y finalmente,
Donde:
Sy se denomina residuo y es el valor mínimo de ajuste al realizar el refinamiento de los datos.
2.3. Análisis estadístico
Con el propósito de evaluar la precisión de los datos y determinar la variación en la composición del material con el tamaño de las partículas, se planteó un diseño experimental completamente al azar tomando como factor principal el tamaño de partícula con cuatro niveles, donde cada nivel es una fracción granulométrica (-0.42, +0.42 -0.85, +0.85 -1.68, +1.68 -0.35 mm). Como se explicó en la sección 2.1, de cada una de estas fracciones se analizaron dos muestras, teniendo como variables de respuesta cada una de las fases cristalinas encontradas en las muestras de escoria blanca de aluminio mediante al análisis de los espectros de difracción (Al, α-Al2O3, MgAl2O4, Mg0.388Al2.408O4, NaAl11O17, AIN).
Los cálculos estadísticos se realizaron utilizando el paquete estadístico Minitab versión 15.0. Con el fin de observar la dependencia del tamaño de partícula sobre la cantidad encontrada en cada una de las fases cristalinas, se realizó un análisis de varianza (ANOVA) con un nivel de confianza del 99% y se validó el cumplimiento de los supuestos de normalidad, igualdad de varianzas y aleatoriedad e independencia de los errores, para cada una de las variables de respuesta evaluadas.
3. Resultados y discusión
3.1. Caracterización del material
En la distribución del tamaño de partículas de la escoria se obtuvieron los siguientes resultados: el 36.9% del material tiene un tamaño inferior a 0.42 mm (muestra E1), el 18.5% tiene un tamaño entre 0.42 mm y 0.85 mm (muestra E2), el 21.8% tiene un tamaño entre 0.85 mm y 1.68 mm (muestra E3), y el 22.8% tiene un tamaño entre 1.68 mm y 3.35 mm (muestra E4).
Los análisis de EDS mostraron que el material está compuesto principalmente de Al y en menor cantidad de O, Fe, Na, Mg, Si y K.
En la Fig. 1 se observa el difractograma de las muestras E1, E2, E3 y E4, donde se puede observar la presencia de las siguientes fases: aluminio metálico (Al), óxido de aluminio o corundo (α-Al2O3), espinelio (MgAl2O4), espinelio defectuoso (Mg0.388Al2.04O4), diaoyudaoite (NaAl11O17) y nitruro de aluminio (AlN). Como se observa se identificaron la totalidad de los picos.
Las fases MgAl2O4 y Mg0.388Al2.04O4 presentan picos en las mismas posiciones, sin embargo, al refinar las muestras solo con la fase MgAl2O4 no se obtenía un buen ajuste del patrón teórico al patrón experimental, este ajuste solo se obtuvo al refinar ambas fases al mismo tiempo. Las fases NaAl11O17, Na2O11(Al2O3) y K1.5Al11O17.25, denominadas alúminas-beta [23-25], también presentan picos en las mismas posiciones y con intensidades similares, por lo tanto, fue necesario hacer refinamientos con cada una de estas fases, al final los mejores ajustes se obtuvieron con la fase NaAl11O17.
3.2. Método de Rietveld
El método de Rietveld se aplicó en todas las muestras con el fin de determinar el porcentaje en masa de cada una de las fases cristalinas presentes. La calidad del refinamiento se verificó con los criterios numéricos y con la observación del ajuste, confirmando siempre que hubiera un buen ajuste de la curva teórica a los datos experimentales. En la Fig. 2 se puede observar el refinamiento de la muestra E1-1, en donde los puntos corresponden a los datos experimentales, la línea continua oscura es la curva ajustada con el método de Rietveld, y la curva clara corresponde a la diferencia entre los datos y el ajuste. Se puede observar en general un buen ajuste entre los datos y el modelo teórico, la calidad del ajuste fue muy similar en todas las muestras.
En la Tabla 1 se presentan los resultados de los refinamientos para cada par de muestras correspondientes a cada fracción granulométrica. Como se observa, en general cada par de muestras presenta porcentajes de composición muy similares, excepto para las muestras con porcentajes de composición inferiores al 5%.
3.3. Análisis estadístico
A través del ANOVA se obtuvieron los siguientes coeficientes de determinación (R2) para cada par de muestras: 99.93% para el Al, 99.9% para el α-Al2O3, 96.1% para MgAl2O4, 98.67% para Mg0.388Al2.04O4, 72.19% para NaAl11O17 y AlN. Según estos resultados los R2 estuvieron en su mayoría por encima del 94%, lo que indica que la variación en el contenido encontrado de cada fase cristalina es explicado en un alto porcentaje por el tamaño de partícula, la única excepción a este resultado se encontró en la fase NaAl11O17. Es interesante observar que esta fase es la única que presenta un contenido inferior al 5% en masa para todos los tamaños de partícula estudiados.
En la Fig. 3 se presentan los resultados de la variación de la composición, obtenido con el ANOVA, en función del tamaño de partícula para el Al y el α-Al2O3. Con las pruebas de comparación de medias para la fase cristalina de Aluminio, se comprobó con un nivel de confianza del 99% que existen diferencias significativas en la cantidad de Aluminio entre cada tamaño de partícula. También se observa que a medida que aumenta el tamaño de partícula, se incrementa significativamente el porcentaje de Aluminio, el mismo comportamiento fue observado por Hiraki & Nagasaka (2015), pero para escorias con tamaño de partícula mucho menor, 75 y 500 µm.
Para el material tamaño de partícula inferior a 0.42 mm se puede observar que el porcentaje de aluminio es muy bajo (24.635 ± 0.559) comparado con los tamaños de partícula mayores a 0.42 mm, los cuales presentaron cantidades de aluminio superiores al 55%.
Con base en las pruebas de comparación de medias para la fase cristalina de α-Al2O3, se comprobó con un nivel de confianza del 99% que existen diferencias significativas en el porcentaje de α-Al2O3 para cada uno de los tamaños de partícula. Además, a medida que aumenta el tamaño de partícula, disminuye el porcentaje de α-Al2O3.
Al contrario de lo ocurrido con el aluminio, se encontró que el material con un tamaño de partícula inferior a 0.42 mm presenta los valores más altos de α-Al2O3 (28.855% ± 0.276) en comparación con el material con tamaño de partícula superior a 0.42 mm donde el porcentaje de esta fase es inferior al 17%.
En la Fig. 4 se presentan los resultados de la variación de la composición, obtenido con el ANOVA, en función del tamaño de partícula para el NaAl11O17 y el AlN. En general se observa que la cantidad de ambas bases disminuye con el aumento del tamaño de partícula. Las pruebas de comparación de medias para la fase cristalina de NaAl11O17, con un nivel de confianza del 99%, mostraron diferencias significativas en el porcentaje de NaAl11O17 entre los diferentes tamaños de partícula, conformando dos grupos, como puede observarse en la Fig. 4.
El análisis realizado con el ANOVA muestra un alto error experimental sin embargo se evidencia diferencias significativas en el contenido de esta fase entre el tamaño de partícula 0.42 y los otros tamaños de partícula evaluados. Es importante anotar que para esta fase siempre se encontraron porcentajes inferiores al 5%.
Las pruebas de comparación de medias para la fase cristalina de AlN con un nivel de confianza del 99%, muestran que se forman tres grupos que son significativamente diferentes. El primer grupo consiste en el material con tamaño de partícula inferior a 0.42 mm, el segundo grupo conformado por los materiales con tamaño de partícula (+0.42 -0.85 y +0.85 -1.68) y el último grupo conformado por los materiales con tamaño de partícula (+1.68 -3.35), estos tres grupos presentan diferencias significativas en el porcentaje de AlN. El material con tamaño de partícula inferior a 0.42 mm presentó el mayor porcentaje de esta fase (6.705 % ± 0.092), en comparación con los tamaños de partícula superiores a 0.42 mm que presentaron un porcentaje por debajo del 6%. En general se observa que la cantidad de AlN disminuye al aumentar el tamaño de partícula, este mismo comportamiento también fue observado por Hiraky & Nagasaka (2015) para escorias de aluminio con tamaño de partícula entre 75 y 500 μm. Este material se forma debido a la reacción del aluminio fundido con el nitrógeno presente en la atmósfera.
En la Fig. 5 se pueden observar los resultados de la variación de la composición, obtenidos con el ANOVA, en función del tamaño de partícula para las fases MgAl2O4, y Mg0.388Al2.408O4. Las pruebas de comparación de medias para la fase cristalina de MgAl2O4, con un nivel de confianza del 99%, muestran que se forman tres grupos que son significativamente diferentes en el porcentaje de MgAl2O4. Los dos primeros grupos lo conforman los tamaños de partícula -0.42 y +0.42 -0.85, el tercer grupo está conformado por los tamaños de partícula +0.85 -1.68 y +1.68 -3.35 pues estos dos últimos tamaños de partícula no presentan diferencias significativas en el porcentaje de MgAl2O4.
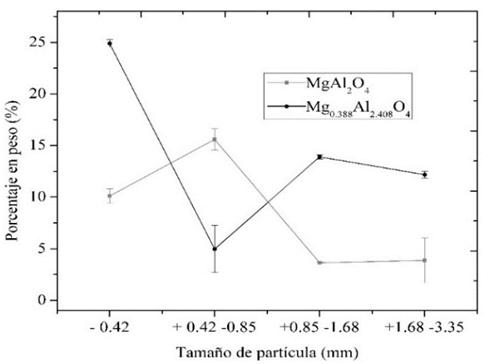
Fuente: Los autores
Figura 5 Cantidad de MgAl2O4, y Mg0.388Al2.408O4 en función del tamaño de partícula.
Para la fase cristalina Mg0.388Al2.408O4, se observó con un nivel de confianza del 99% que se forman tres grupos que son significativamente diferentes en el porcentaje de esta fase. Los dos primeros grupos lo conforman los tamaños de partícula (-0.42 y +0.42 -0.85) y el tercer grupo está conformado por los tamaños de partícula (+0.85 -1.68 y +1.68 -3.35) pues estos dos últimos tamaños de partícula no presentan diferencias significativas en cuanto al porcentaje de Mg0.388Al2.408O4.
Debido a que las fases MgAl2O4 y Mg0.388Al2.408O4 son muy similares y presentan picos en posiciones muy próximas, el programa las puede confundir al momento de hacer el refinamiento, por lo tanto, se decidió analizar que ocurre al sumarlas. Se hizo nuevamente el análisis de varianza con la suma de estas fases con un nivel de confianza del 99% y se validó el cumplimiento de los supuestos de normalidad, igualdad de varianzas y aleatoriedad e independencia de los errores, y se obtuvo R2 de 98.88%. La Fig. 6 muestra la cantidad de la suma de estas dos fases en función del tamaño de partícula.
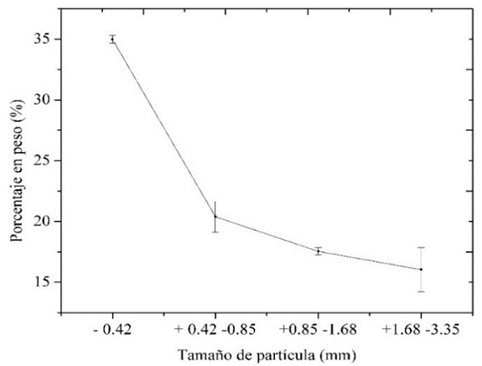
Fuente: Los autores
Figura 6 Cantidad de la suma MgAl2O4, y Mg0.388Al2.408O4 en función del tamaño de partícula.
Al realizar las pruebas de comparación de medias para la suma de las fases cristalinas MgAl2O4 y Mg0.388Al2.408O4, con un nivel de confianza del 99%, que se forman dos grupos que muestran diferencias significativas. El primer grupo conformado por el material con tamaño de partícula inferior a 0.42 mm y el segundo grupo conformado por el resto del material (+0.42 -0.85, +0.85 -1.68 y +1.68 -3.35), los materiales con estos tres tamaños de partícula no presentan diferencias significativas en el porcentaje de la suma de MgAl2O4 y Mg0.388Al2.408O4.
Al sumar las dos fases, MgAl2O4 y Mg0.388Al2.408O4 se observa en los resultados del ANOVA que el coeficiente de determinación aumentó a 98.88% lo que indica que al sumar estas dos fases se explica en mayor porcentaje la variabilidad de las fases en cada tamaño de partícula y tendrá mayor precisión reflejada en los intervalos de pronóstico más estrechos. Por otro lado, se observa en general una tendencia más clara, donde la cantidad de estas dos fases disminuye con el tamaño de partícula.
4. Conclusiones
En este trabajo se analizó una escoria de aluminio con tamaño de partícula inferior a 3.35 mm. Se encontró que este material está compuesto por Al metálico, α-Al2O3, MgAl2O4, AlN, Mg0.388Al2.04O4 y NaAl11O17. El material fue separado por tamaño de partícula con el fin de determinar la influencia del tamaño de partícula en la composición del material.
Con respecto al análisis cuantitativo de las fases se pudo concluir que el contenido de aluminio presentó una tendencia a aumentar con el incremento del tamaño de partícula. Con tamaños de partícula superiores a 0.42 mm se observó que el porcentaje de aluminio es superior al 55%, llegando hasta 69.4%. Para las fases restantes se observó, en general, una tendencia contraria.
Del análisis estadístico se pudo concluir que los coeficientes de determinación estuvieron en su mayoría por encima del 94%, lo que indica que el contenido encontrado de cada fase cristalina es explicado en un alto porcentaje por el tamaño de partícula. La única excepción a este resultado se encontró para la fase NaAl11O17 donde se obtuvo un R2 de 72.19%; es interesante observar que esta fase es la única que presenta un contenido inferior al 5% en masa para todos los tamaños de partícula estudiados.