1. Introduction
Super-hard nanostructured metallic nitride coatings have improved the service life and the maintenance cycle of cutting tools, aeronautical parts, and automobiles. The latest advances in the development of new materials and techniques for producing thin films have focused on the use of hard and wear-resistant applications. These results have been very well received thanks to the efforts to increase the duration of materials in the diamond range. These coatings are divided into two groups, depending on the hardness value. The first is called hard coatings, which have a hardness of >12 GPa, and the second super-hard coatings, which have a hardness of >40 GPa. Currently, significant efforts are devoted to improving the formation of nanocomposite coatings using magnetron sputtering, since this technology can be easily extended for industrial use [1].
Titanium nitride (TiN) coating has wide applications in the fields of space, biomedicine, and microelectronics, given its excellent physical, chemical, electrical, and mechanical properties. The properties that allow titanium nitride to be applicable in so many fields are its high hardness, good adhesive wear, high resistance to corrosion, high melting temperature, and biocompatibility. However, one of the most significant developments in hard coatings has been the synthesis of the Ti-Si-N system, with hardness values above 40 GPa [2,3]. These improved properties of the Ti-Si-N system are attributed to the formation of transition metal nitride nanocrystals embedded in an amorphous matrix of a second phase of the material [4]. The above can be explained by the mechanism of spinodal decomposition, through which an alloy is decomposed into equilibrium phases. This is a medium for the rapid separation of a mixture of liquids or solids from a thermodynamic phase to form two coexisting phases. For the Ti-Si-N system, there is an amorphous phase of SiN and TiN nanocrystals.
Zirconium nitride (ZrN) coatings are used as diffusion barriers in microelectronics, wear-resistant coatings in cutting tools, or as corrosion-resistant layers in mechanical and optical components [5], and furthermore they show high hardness and low electrical resistivity. The incorporation of silicon in coatings, such as in the Zr-Si-N system, increases the films’ hardness, improves the oxidation resistance of the films, and reduces the friction coefficient [6]. Hasong Choi et al. [5] mention that the addition of silicon from 0 to 5.8 at% into the ZrN columnar coating transforms it into a nanocomposite structure composed of ZrN nanocrystals that are embedded in the amorphous matrix of Si3N4; if a higher silicon percentage is added, amorphous coatings can be produced [4].
However, the quaternary system of ZrSiTiN has not been thoroughly studied. Nevertheless, there are references that show the behavior of the coating and its characteristic properties of hardness, oxidation resistance, and structure. This coating has been deposited using various techniques, such as high-frequency arc evaporation (HF) and the co-sputtering technique. The presence of alloying elements such as Zr contributes to better wear resistance, while Si increases hardness and thermal stability [7]. Pogrebnjak et al. [7] determined that the nanograin size of the solution changed from 10 nm to 12 nm, and at the same time the size of the intermediate layer of α− 𝑆𝑖 3 𝑁 4 that enveloped the nanograins of (Ti,Zr)N varied from 6 nm to 8 nm, while the hardness varied from 39.6 GPa to 53.6 GPa [7]. On the other hand, I. A. Saladukhin et al. [8] found that the increase in hardness in the ZrSiTiN thin film is due to the formation of SiN, which has the function of hindering the growth of the transition metal nitride grains, which entails a refinement of grain size [8]. However, an additional increase in silicon can reduce the hardness, which is attributed to the progressive thickening of the amorphous interfacial phase of Si3N4 and the concurrent decrease in size and amorphization of the solid solution grains [9,10].
In recent years, hard coating properties have been improved by the addition of nickel. For example, Chu et al. [11] show that the addition of Ni to TiN improves the hardness by approximately 60% over the values of the mixing rule. A value of 3,200 kgf/mm2 was reported for a layer thickness ratio over the period (𝑙Ni/Λ) of 𝑙𝑁i/Λ= 0.3. Zhang et al. [12] demonstrate that for films with 2.1% Ni, a maximum temperature of 850°C was determined, below which an excellent resistance to oxidation prevails, but above which oxidation takes place at an exponential rate, accompanied by a sudden increase in surface roughness. Likewise, nickel does not participate in the oxidation process within the temperature range studied but rather exists in a metallic state. Suna et al. [9] researched into the microstructure of Zr-Ni-N films with low nickel content deposited by reactive sputtering; the findings show that due to the columnar microstructure, the grain size, and the shape of the crystallites, the hardness improves to 32 GPa and the residual stresses are compression, with values of -2GPa. Yet the addition of nickel favors Zr-Ni-N films with normal nanocolumns to the substrate, thus obtaining a columnar structure that improves the hardness and residual compression effects [9]. Likewise, the FCC (Zr, Ti)N phase oriented in the planes (111) and (200), the amorphous or crystalline Si3N4 compound oriented in the planes (201), (210), and (202), and ZrN in planes (111), (200), and (311) have been found via XRD [7].
The objective of this paper is to research into the structure and anticorrosive properties of the system composed of Zr-Si-Ti-N with different Ni contents, deposited on Ti6Al4V substrates via the co-sputtering technique. This material was characterized by means of SEM, EDS, and X-ray diffraction, and the electrochemical behavior was studied through potentiodynamic polarization curves to determine the corrosion current density.
2. Experimental procedure
2.1. Deposition and coating growth
Zr-Si-Ti-N coating with added nickel was deposited via the co-sputtering technique in a combined atmosphere of nitrogen-argon on silicon wafer, glass, and Ti6Al4V alloy. The sputtering equipment has two magnetrons of 4-inch targets, each inside a vacuum chamber. The system can generate the vacuum with a rotary vane mechanical pump and a turbomolecular pump with a pumping speed of 10 m3 /h and 1,800 m3 /h, respectively. The co-sputtering system has an arrangement with two magnetrons in a confocal configuration locating the targets at 30° with respect to the normal of the target surface and a working distance of 10.16 cm (4 in). During the coating’s growth, the substrates were rotating at 10 rpm, with the aim of achieving better homogenization of the nickel in the coating.
The procedure used targets of a transition metal or an alloy composed of two transition metals, which have commercial composition with a purity of 99.9% and a dimeter of 10cm. To enerate the discharge, a Zr target was used connected to a pulsed-DC source with a power of 200 W and a target of Ti5Si2 connected to an RF source with a power of 170 W. Argon and nitrogen were introduced with fluxes of 14 sccm and 2 sccm, respectively. The working pressure was 4x10-3 mbar, and the base pressure of the chamber was below 9x10-6 mbar. The deposit time of the films was 80 minutes.
The coating’s production was carried out while varying the amount of 99.99% high purity nickel metal squares to cover the area of greatest erosion of the Zr target, also known as the “race track.” Fig. 1 shows a diagram of the distribution of Ni pieces of 3x3x3 mm on the target of Zr.
2.2. Characterization of the coatings
A Bruker GT optical profilometer was used to measure the thickness, taking 3 measurements per test piece. The measurement was made on silicon that had a laminar shape and allowed the measurement to be optimal. The structural characterization was performed by X-ray diffraction with Panalytical X-PerTPro equipment in Bragg-Brentano mode and a ground beam. The measurements were made with a monochromatic line K of copper, wavelength 1.54 Å, current intensity 40 mA, and radiation source 45 kV. The sweep range was within the range of 10° to 100°, with a step size of 0.02° in continuous mode. From the Williamson-Hall method and the Debye Scherrer equation [9].
The crystallite size and the microdeformation were determined, using a non-linear adjustment with the Pseudo-Voight function through Origin pro9.0 software.
The surface morphology of the coating was determined by scanning electron microscopy (SEM) using a FEI QUANTA 200 scanning electron microscope. Images of backscattered X-ray electrons (BSI) and BSI point map images were obtained from the surface of the films to characterize the surfaces or areas of corrosion that were produced in the electrochemical tests. The chemical composition was evaluated with an EDS detector coupled to a microscope in order to determine the chemical composition at different points of the sample. The usual conditions under which the equipment is operated are the same as for SEM, but the potential difference is higher, since it is required to generate the X-ray emissions that are characteristic of the elements present in the coating.
The corrosion resistance of the ZrSiTiN+Ni coatings was studied using a three-electrode system in a Gamry 600 potensiostat at room temperature. The samples were mounted in a special cell, in which the exposed area was 0.196 cm². In the corrosion resistance experiments, the substrates were used as a working electrode with a platinum one as the counter electrode, and a 3.5% NaCl solution was used as the electrolyte (pH 7.9). Before performing each experiment, the corrosion potential was allowed to stabilize for 45 minutes of immersion in the solution. In the potentiodynamic polarization conduction (PP) experiments, the initial potential was -0.3V and the scanning speed was 0.5 mV/s. The corrosion current density (Icorr) was estimated by a linear adjustment using extrapolation by Tafel in the Gamry Echem Analyst Software.
3. Results and discussion
Table 1 shows the semiquantitative analysis of the coatings produced as a function of the number of Ni pellets added to the Zr target. It can also be seen that the coatings have high contents of Zr, attributed to the high current density applied to the Zr target. However, it can be seen that as the Ni percentage increases, the Zr decreases. The percentage of nickel increases up to 6.9% as Ni is added to the Zr target, and the Zr percentage decreases from 72.05 to 58.21 at%, while the Si and Ti contents do not vary significantly.
Table 1 Chemical composition for Ti6Al4V alloy depending on the nickel addition.
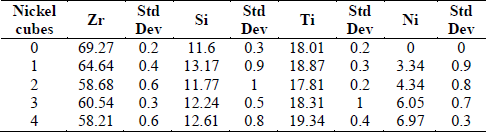
Source: The authors.
Fig. 2 shows the results for deposit rates in the produced coatings. It can be seen that the coatings deposited without nickel showed the highest values of thickness, 1.31µm ± 0.15 µm, while the addition of nickel reduced the films’ thickness, with values of 1.14 µm ± 0.13 µm (3.34 at% Ni), 1.069μm ± 0.12μm (6.05 at% Ni), and 1.133μm ± 0.13μm (6.97 at% Ni). It is possible that the nickel in the erosion zone of the Zr target produces a decrease in the polarization of the target due to the lower emission of secondary electrons; that is, the efficiency of the sputtering decreases.
Fig. 3 shows how the discharge current for the Zr target decreases with the addition of Ni. There is definitely a lower emission of electrons from the plasma at the target surface, i.e., a decrease in the ionization of the plasma and a reduction of sputtering efficiency.
Fig. 4 shows the X-ray diffraction results in the coatings produced as a function of the Ni content, and Fig. 5 shows the 2θ = 34-44° interval of the XRD pattern, in order to better observe the most important signals found in the material. In general, it is possible to see the presence of the related peaks of the substrate and the signals of the FCC (Zr, Ti)N phase in the planes (111) and (200) and the TiN in the plane (311) with cubic structure. These results correspond with the works of Pogrebnjak [7] and Sobol [13], who explained their results by a substitution mechanism in solid solution of Ti and Zr atoms when they deposited TiZrN and TiZrSiN coatings.
A decrease in the intensity of the peaks can also be observed as the percentage of nickel increases; that is, the addition of nickel favors the formation of an amorphous material. In these coatings, the formation of amorphous regions due to the low deposition temperature is favored. For example, the Si3N4 produced by sputtering is amorphous, because the temperature for the formation of Si3N4 crystals is higher than 800°C [14,15]. It was also found that Ni can be incorporated in a crystalline form in a solid solution when the substrate temperature is higher than 600°C [15]. The low temperatures and the in the amount of nickel definitely reduce the mobility of the absorbed atoms, avoiding the diffusion of the atoms and their occupation of places of minimum energy or the formation of an ordered material.
The results of the crystallite size (D) and microdeformations (ε) are shown in Fig. 6. It can be seen that coatings without Ni have the largest crystallite size, and that the crystallite size of the coating decreases as nickel is added. The average crystallite size estimated by the Scherrer equation (Eq. 1) is between 53.43 nm and 16.69 nm. The effect of reducing or refining the crystallite size can be associated with the presence of a small amount of metallic Ni in addition to the Ni dissolved in the (Zr, Ti) N lattice. In the TiN coating with Ni, a decrease in the grain size was found to be the result of the crystallization of the metallic Ni. In addition, the presence of nickel in the thin film is probably found in isolation, but it is not creating solutions of SiNi or TiNi, due to the low diffusion between the atoms of Ni with Si, N, or Ti at room temperature by sputtering [16]. The results of this research also show an increase in the microdeformation of the coatings with the increase of nickel. This may be associated with the amorphous regions restricting the growth of crystallites in the material, generating an increase in residual stresses [16].
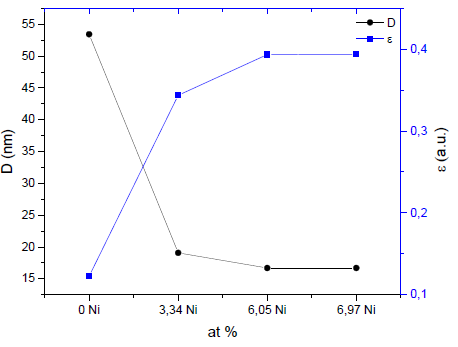
Source: The authors.
Figure 6 Crystallite size (D) for the (Zr.Ti)N phase and microdeformations (ε) depending on the nickel addition.
Fig. 7 shows the results of the potentiodynamic polarization test on the Ti6Al4V alloy, as well as the results of the ZrSiTiN coatings based on the Ni content. The results of the test carried out on the alloy show a corrosion potential value of -4.39 E-2 V and a corrosion current density of 1.86 E-8 A. Nonetheless, when comparing the potential of corrosion of the substrate, it is possible to observe a slightly more positive value than that of the deposited coatings, and on the horizontal axis the polarization curves exhibit a shift to the left, which means a lower corrosion density with respect to the alloy.
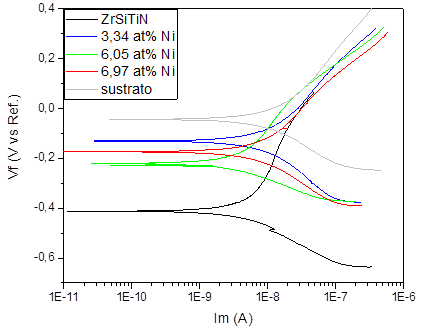
Source: The authors.
Figure 7 Comparative potentiodynamic polarization curves of the ZrSiTiN coating with addition of nickel on teh Ti6Al4V substrate.
Fig. 8 shows the change in the corrosion current density of the ZrSiTiN thin films with the addition of nickel on the Ti6Al4V substrate. The thin film that has the best corrosion resistance for the lowest corrosion density is the film with 6.05 at% Ni. When the coating has 6.97 at% Ni, the corrosion resistance increases in relation to the value of the thin film with 6.05 at% Ni; this indicates that up to a certain percentage of added nickel, the coating has greater resistance to corrosion. In general, the corrosion current has lower values each time the nickel increases, and the corrosion potential varies depending on the amount of nickel in each film.
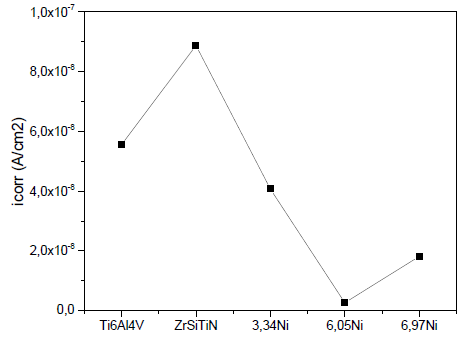
Source: The authors.
Figure 8 Corrosion density curve based on the nickel addition for the Ti6Al4V alloy.
Nickel, a metallic material and a natural resource, proves to be a versatile element and highly resistant to corrosion and high temperatures. It also can be alloyed with many metals. The increased production of nickel is used to improve the mechanical properties of stainless steels, and these steels are used in the aeronautical, automotive, naval, and biomedical industries. According to some research on the microstructures of the compounds of Ti-Zr-Si-N, several factors can illustrate the improvement of the resistance to corrosion [17,18]. This improvement in the resistance to corrosion can be attributed in part to the combination of Ni, Si3N4, and the phase of (Zr, Ti) N. At the same time, nickel is a corrosion inhibitor and in thin films favors the formation of an amorphous material, which reduces the paths or crystalline defects so that the corrosive solution does not reach the substrate. Furthermore, it is also possible that the Ni embedded in the phase (Zr, Ti) N can help prevent the growth of corrosive regions, and the incorporation of oxides of Si, Ti and Zr that can accelerate the process of passivation of the material [17].
4. Conclusions
Coatings of (ZrSiTi)N with added nickel were produced up to 6.9 at%. As Ni was added to the Zr target, the Zr percentage decreased from 72.05 to 58.21 at%. However, the silicon and titanium contents did not vary significantly in the films produced.
In general, the presence of the related peaks of the substrate and the signals of the FCC phase of (Zr, Ti) N in planes (111) and (200) can be seen. A decrease in intensity of the peaks can also be observed as the percentage of nickel increases; i.e., the addition of nickel favors the formation of an amorphous material. When nickel is added, the crystallite size of the coating decreases. The average crystallite size estimated by the Scherrer equation is between 53.43 nm and 16.69 nm. The results of this research also show an increase in the microdeformation of the coatings with the increase in nickel.
In general, the corrosion current density in the deposited coating takes lower values with an increase in nickel. The Ni inhibits corrosion and promotes the growth of a less crystalline material; that is, it reduces the paths or crystalline defects so that the solution cannot chemically interact with the substrate, thus delaying the degradation of the coating-substrate system.