1. Introducción
El costo de la abrasión es alto y ha sido estimado dentro de un rango de 1 a 4% del producto bruto nacional de un país industrializado [1]. El efecto de la abrasión es particularmente evidente en las áreas industriales de agricultura, minería, procesamiento de minerales, movimiento de tierra, y esencialmente trabajo con rocas y minerales. El desgaste por partículas duras ocurre en muchas situaciones diferentes como por ejemplo en el movimiento de tierra, fluidos en tuberías y bombas, taladrado de rocas, molinos de piedra, etc.
En el siguiente trabajo se llevó a cabo el análisis de la problemática presentada en componentes mecánicos sujetos a la acción abrasiva en minería, tema que abarca una actividad productiva de casi todos los países de la región y a nivel mundial, ya que este ítem juega un papel preponderante en el desarrollo productivo de cada uno de los países
En la aplicación de recubrimientos duros se buscan microestructuras específicas que posean alta resistencia al desgaste [2,3], los materiales que posean en sus estructuras carburos, especialmente de cromo, han mostrado grandes beneficios cuando son sometidos a desgastes de tipo abrasivo [4].
En estos tipos de recubrimientos duros se ha evaluado la influencia que la composición química tiene en cuanto a las propiedades del recubrimiento, en este sentido se ha analizado la influencia que tiene el cromo (Cr) y el tungsteno (W) en la resistencia al desgaste abrasivo[5,6], además de las variables mencionadas, se encuentra un gran interés en estudiar la relación existente entre la entrada de corriente, definida por el amperaje y las propiedades antidesgaste del recubrimiento obtenido.
Una de las principales líneas de investigación en esta área es lograr determinar las diferentes microestructuras presentes en el material depositado y la relación existente entre esta y la resistencia al desgaste obtenida. Las estructuras encontradas cuando se depositan materiales con alto contenido de cromo (Cr>15%), son las de tipo M7C3, las cuales brindan elevados valores de dureza y de resistencia al desgaste de tipo abrasivo [7-9].
Este trabajo tuvo como objetivo general el evaluar el efecto del tipo de material depositado y de la temperatura de precalentamiento y sostenimiento entre pases, de depósitos antidesgaste aplicables a sustratos de acero de baja aleación y bajo carbono, sobre la microestructura del depósito y la relación entre ésta y la resistencia al desgaste abrasivo evaluado bajo norma ASTM G 65. Además, se buscó analizar diferentes tipos de electrodos, tanto los utilizados como recubrimientos duros, como los que se usan como relleno y en los que se busca propiedades intermedias entre el material base y el recubrimiento.
La resistencia al desgaste fue evaluada bajo norma ASTM G65-04, posteriormente se tomó una muestra representativa por tratamiento realizado y a esta muestra se le realizaron los ensayos de rugosidad, composición química en última capa, microdureza, análisis por microscopia SEM, análisis metalográfico con microscopio óptico y difracción de rayos X (DRX).
Después de realizar el análisis de desgaste abrasivo, se determinó que la capa depositada con electrodos West Crome ® el cual posee altos contenidos de cromo (25%) y carbono (3,1%) presentó el mejor comportamiento al desgaste de tipo abrasivo bajo norma ASTM G65-04, además se encontró que el material de relleno que presentó la mejor resistencia al desgaste abrasivo fue el depositado con electrodos West Hard 400®, depositando un acero austenítico (tipo Hadfield), esto debido a su alto contenido de manganeso, ver tabla 1, que al presentar un alto endurecimiento por deformación permitió una mejora en los valores de resistencia al desgaste, esta alta deformación se obtuvo por martilleo sobre la superficie obtenida.
2. Parte experimental
2.1. Factores utilizados
Se tomaron en cuenta dos (2) factores que afectan las características finales de los recubrimientos duros aplicados por soldadura, cabe aclarar que en la soldadura existen numerosos factores que pueden analizarse, pero por el alcance de este trabajo se seleccionaron los siguientes:
2.1.1. Tipo de electrodo a aplicar
Este es uno de los factores que afectan en mayor medida los recubrimientos duros, ya que este determina el material, la microestructura y las propiedades físicas, químicas y mecánicas, así como el comportamiento al desgaste de tipo abrasivo. Se seleccionaron cinco (5) tipos de recubrimientos, de variadas características y con un amplio uso en la industria especialmente de reconstrucción de piezas. Todos los recubrimientos se depositaron sobre piezas de acero ASTM A-36 con dimensiones de 3 in x 1in x 0,25in.
2.1.2. Temperatura de precalentamiento y de sostenimiento
Un factor primordial en el estudio de soldaduras es la temperatura de precalentamiento y de sostenimiento, ya que en estas se genera un alto choque térmico debido a los grandes cambios de temperatura, que pueden pasar de zonas donde existe material líquido hasta zonas con material a temperatura ambiente, lográndose una amplia gama de microestructuras, tamaños de grano y así mismo propiedades físicas. En este estudio se aplicaron tres temperaturas de precalentamiento y de sostenimiento, comenzando con temperatura ambiente, la segunda temperatura de estudio fue de ciento cincuenta grados centígrados (150°C), y se tomó como tercera temperatura el valor de trescientos cincuenta grados centígrados (350°C), con estos tres valores se pretendió estudiar un amplio espectro y observar cómo afectan estas temperaturas los datos de resistencia al desgaste y las demás variables de respuesta.
2.2. Material base
Se determinó el uso de acero ASTM A 36 para la aplicación de los recubrimientos duros, esto tomando en cuenta la composición química, la amplia aplicación de este tipo de aceros en producción de piezas y además que la investigación se basa en el estudio de los recubrimientos y no en cómo afecta al material base o a la dilución presente en la interfase acero - recubrimiento.
2.3. Obtención de los recubrimientos
La aplicación de la soldadura se realizó mediante un equipo para soldadura con electrodo revestido marca Miller. Este tipo de soldadura permite tener un mayor control en cuanto a la generación de la capa, además tiene la ventaja de poder introducir elementos aleantes en el revestimiento del electrodo.
El control de la temperatura se realizó con termómetro láser marca Fluke 62. Los rangos de temperaturas que se utilizaron fueron veinte grados centígrados (20°C), ciento cincuenta grados centígrados (150°C) y trescientos cincuenta grados centígrados (350 °C), se usó un horno con control de temperatura para obtener la temperatura de precalentamiento.
La principal variable de respuesta es el valor de resistencia al desgaste de las probetas, en el cual se usó el procedimiento B de norma ASTM G65[10]. A partir de estos valores se encontró la media y la desviación estándar de cada uno, después se procedió a seleccionar la probeta que se encontrara más cercana a la media y que representara en mejor medida a todo el rango del ensayo, seleccionada la probeta representativa se le realizaron los ensayos descritos en este numeral, se tomaron imágenes de microscopia SEM (Referencia FEI modelo Quanta 200), microscopia confocal (Marca Zeiss), análisis metalográficos (microscopio LECO 500), microdureza (microdurómetro marca referencia M-400-G2), composición química en la última capa (espectrómetro de emisión y difracción de rayos x (Equipo Xpert Pro), con la información obtenida de los anteriores ensayos se obtuvo la correlación entre esta y el valor de resistencia al desgaste.
3. Resultados
3.1. Ensayo de desgaste
Desde la Fig. 1 a la Fig. 3 se grafica el comportamiento al desgaste bajo norma ASTM G65-04 contra temperatura de precalentamiento y de sostenimiento de los electrodos aplicados, se observa que los electrodos con altos contenidos de cromo y carbono (West Crome®), mostraron los mejores comportamientos al desgaste abrasivo, así como los electrodos con altos contenidos de manganeso (West Hard 400®) mostraron una importante disminución en el valor de pérdida de peso por desgaste (especialmente las probetas que fueron martilladas para aumentar su dureza superficial), respecto a los electrodos de baja aleación y medio a bajo carbono (West Hard 65®, West Hard 30® y AWS E 11018).
3.2. Resultados composición química de última capa
De la superficie desgastada de cada probeta escogida se extrajo una muestra con la suficiente área para determinar la composición química de la última capa depositada, para tal fin se utilizó un espectrómetro de chispa, en la Tabla 2 se muestran los principales elementos químicos, tomando en consideración la composición química de cada electrodo.
3.3. Resultados microdurezas en última capa
En sección metalográfica transversal en la zona cercana a la superficie de desgaste se determinó el valor promedio y la desviación estándar de cada probeta escogida, los datos se tabulan en la Tabla 3.
Los valores más altos de dureza Knoop (801 HK), fueron obtenidos por los recubrimientos aplicados con mayor contenido de cromo (20,28%Cr - 26,83%Cr) y carbono (3,06%C - 4,07%C), correspondientes al electrodo West Crome®.
Por otro lado los recubrimientos obtenidos de electrodos con contenido de cromo de siete coma cinco por ciento y de carbono de cero coma siete por ciento (West Hard 65®), presentaron durezas desde trescientos diez (310 HK), lo cual concuerda con su composición química y con el valor de contenido de cromo, que varía entre cinco coma siete (5,7%Cr) y siete (7%Cr) y con el valor del contenido de carbono que varía entre cero coma sesenta y dos (0,62%C) y cero coma ochenta y dos por ciento(0,82%C).
Los recubrimientos obtenidos con electrodos de bajo carbono y bajo cromo (West Hard 30®), obtuvieron valores de dureza promedio de trescientos diez (310 HK).
Es interesante mencionar los recubrimientos obtenidos a partir de electrodos con alto manganeso (West Hard 400®), los cuales aumentaron en gran medida su valor de dureza cerca de la zona superficial, que pasó de valores cercanos a los ciento ochenta y nueve (189 HK) en probetas sin martilleo en su superficie, a valores de quinientos veinte y dos (522 HK) en probetas que fueron deformadas plásticamente por martilleo antes de la prueba de desgaste.
3.4. Cálculo del coeficiente de desgaste
Para los resultados obtenidos de pérdida en volumen en desgaste y dureza se calculó el coeficiente de desgaste K, en la ec. 1 se observa la relación que brinda este valor entre volumen, dureza, carga y longitud de deslizamiento, esto con el fin de poder compararlo con valores encontrados en la literatura
Donde:
V: Volumen de desgaste del material más blando.
K: Coeficiente de desgaste.
F: Fuerza normal.
L: Longitud de deslizamiento.
H: dureza de penetración.
En la tabla 4 se muestran los valores obtenidos para este coeficiente de desgaste K, junto con los valores de desviación estándar, el valor medio se determinó para cada familia de electrodos. Estos valores coinciden con los reportados por Zum [11].
3.5. Resultados difracción de rayos X.
Se analizaron seis probetas por difracción de rayos x, recubrimientos con alto cromo (West Crome®), recubrimientos de baja aleación (11018), recubrimientos de media aleación (West Hard 30® y West Hard 65®) y recubrimientos con alto contenido de manganeso (West Hard 400®). Los resultados se muestran para cada una de las anteriores muestras.
3.5.1. Recubrimiento de alto cromo.
En este tipo de recubrimiento se obtuvo el difractograma mostrado en la Fig. 4, donde se observa la presencia de carburos de cromo y de hierro del tipo M7C3 [12], presencia de martensita y austenita. Al observar la figura 8 se encuentra la presencia de carburos de cromo con forma hexagonal (zona blanca). Estos carburos influyen en el aumento en la dureza de estos recubrimientos, alcanzando valores de 800HK, además de generar una barrera contra el desgaste abrasivo [13].
3.5.2. Recubrimientos de electrodos de baja aleación.
En este tipo de recubrimientos de acuerdo a los difractogramas mostrados en la Fig. 5, se encontró que sus principales componentes son la ferrita y la cementita. Debido a sus bajos contenidos de elementos aleantes se encuentra una conformación típica de aceros de bajo carbono, lo cual influye en su dureza (310HK) y en los valores de desgaste obtenido.
3.5.3. Recubrimientos de media aleación
Para este material depositado se encontró como componentes principales los carburos de cromo y de hierro (aleados) y la martensita, ver Fig. 6. En la Fig. 19 se pueden observar zonas blancas (carburos de cromo) más pequeñas que las encontradas en los recubrimientos obtenidos con alto cromo, al disminuir el tamaño del carburo no se presenta la misma barrera al paso de las particulas abrasivas, lo cual afecta el comportamiento a desgaste.
3.5.4. Recubrimientos acero alto manganeso.
De acuerdo a la composición química obtenida de este recubrimiento, principalmente su alto contenido de manganeso, se encontró austenita como principal componente, ver Fig. 7. Este material tiene la particularidad de endurecerse por deformación, lo cual aumenta los valores obtenidos de dureza hasta 190HK.
3.6. Resultados metalografía
De acuerdo a la composición química encontrada en la Tabla 1 y comparando estos valores con las imágenes obtenidas por microscopia óptica y los difractogramas de las principales probetas, se encontraron las microestructuras mostradas en las Figs. 8 - 12. El material base principalmente mostró formaciones de ferrita y perlita ver Figura 9; los depósitos a partir de electrodos West Crome®, formaron altos contenidos de carburos aleados con cromo del tipo M7C3 y en matriz martensítica y austenítica, fig. 8, los electrodos West Hard 30® generaron depósitos de martensita, bainita, ferrita y carburos aleados con cromo finos en su mayoría, ver Figura 10; los recubrimientos obtenidos a partir de electrodos West Hard 400® debido a su alto contenido de manganeso produjeron depósitos de austenita, ver fig. 12; los electrodos West Hard 65® generaron depósitos compuestos de martensita con carburos de cromo finos, ver Fig. 11
3.7. Mecanismos de desgaste encontrados
En las Figs. 13 - 15, se muestran los mecanismos de desgaste encontrados por microscopia SEM de los recubrimientos aplicados, en general, en los recubrimientos depositados con electrodos West Hard 30, West Hard 65 y AWS E11018, se encontró la formación de surcos de desgaste con desplazamiento plástico en los bordes, característico de materiales dúctiles y con deformación en la zona plástica [14]. En los recubrimientos depositados con electrodos West Crome, ver Fig. 14, se encontró la no formación de surcos ni se encontró desplazamiento plástico en la zona desgastada, esto debido a sus altas concentraciones de carburos de cromo, los cuales brindan elevadas durezas y resistencias al material

Fuente: Los Autores.
Figura 13 Recubrimiento baja aleación sin ataque. Se observa claramente las ranuras producidas en el ensayo de desgaste, asi como la fluencia plástica en los bordes de las ranuras.
4. Análisis de resultados
Se estudiaron dos factores los cuales fueron material depositado en la última capa (cinco materiales depositados), y temperatura de precalentamiento y sostenimiento (ambiente, ciento cincuenta y trescientos cincuenta grados centígrados), se realizaron análisis de varianza a cada uno de estos factores para poder determinar su influencia en el resultado de desgaste.
4.1. Influencia del electrodo de la última capa en la resistencia al desgaste
De acuerdo con cada uno de los materiales depositados, tomando en cuenta el tipo de electrodo se encontraron una gran variedad de estructuras, pasando por altas concentraciones de carburos para los electrodos de alto cromo y alto carbono, aceros austeníticos para el electrodo de acero Hadfield, hasta estructuras basadas en ferrita, cementita, martensita y bainita en aceros de bajo y medio carbono. En las secciones restantes de este numeral se observarán los resultados en cada una de las aplicaciones, tomando en cuenta el electrodo aplicado en la última capa. Ver Figs. 16 - 19.
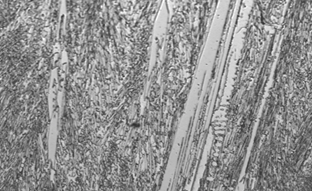
Fuente: Los Autores.
Figura 16 Micrografías obtenidas de recubrimientos aplicados con West Crome®. Se observa carburos en forma laminar. 800x. Ataque químico con Vilella.
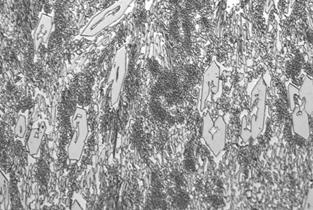
Fuente: Los Autores.
Figura 17 Micrografías obtenidas de recubrimientos aplicados con West Crome®. Acá se puede ver la formación de carburos tipo M7C3 con su característica forma hexagonal. 800x. Ataque químico con Vilella.
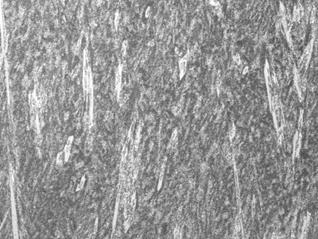
Fuente: Los Autores.
Figura 18 Micrografías obtenidas de recubrimientos aplicados con West Crome®. Las zonas blancas son ricas en carburos de cromo, pero sin presentar la forma hexagonal. 800x. Ataque químico con Vilella.
4.2. Análisis de dureza contra resistencia al desgaste
En la Fig. 20, se muestra la relación existente entre la dureza y el valor obtenido en la prueba de desgaste, se muestra claramente que la dureza no presenta una relación directa con la resistencia al desgaste de todos los materiales depositados. Al hablar de una familia de acero en particular, se puede decir que la dureza si tiene influencia en el valor de desgaste, un ejemplo de lo anterior se puede ver con los resultados obtenidos del recubrimiento aplicado con aceros tipo Hadfield, el cual a durezas bajas muestra valores menores de resistencia al desgaste, que cuando se eleva la dureza superficial por deformación, lo anterior siempre debe ser verificado con un análisis de microestructura y con la respectiva prueba de desgaste.
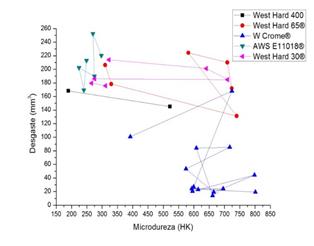
Fuente: Los Autores.
Figura 20 Resultados microdureza Knoop contra valores de desgaste. El electrodo es el aplicado en última capa.
4.3. Análisis del comportamiento a desgaste relacionado con la dureza, deformación plástica en zona desgastada, y material depositado
Los depósitos realizados con electrodos de alto cromo (West Crome®), mostraron los mejores desempeños cuando se evaluó su comportamiento al desgaste de tipo abrasivo, lo anterior se sustenta en la formación de carburos de tipo M7C3 en matriz martensítica y austenítica, esto como se apreció en el análisis realizado por difracción de rayos X, apoyado con los valores obtenidos de composición química en última capa, además estos recubrimientos presentaron las mayores durezas en relación a los demás recubrimientos aplicados, en las imágenes obtenidas por microscopia SEM no se aprecia deformación plástica, no presentan desprendimiento y sumado al gran tamaño de los carburos respecto a las superficies de corte de la arena, presentan una resistencia al desgaste superior.[15,16].
En lo referente a electrodos de baja aleación y propuestos como material de relleno (West Hard 30®, West Hard 65 ®, AWS E 11018), no se encontró diferencia en sus comportamientos al desgaste abrasivo, a pesar de los cambios encontrados en su microestructura, pasando de estructuras ferrito-perlíticas, a estructuras bainitica-martensítica o solo martensíticas con carburos aleados, cambios observados por los análisis de las imágenes metalográficas y los difractogramas obtenidos por Rayos X. Para estos depósitos se encontró que en general, existió una alta formación de surcos sobre la superficie de desgaste y deformación, producto del pequeño tamaño de los carburos vs. las superficies de corte de la arena.
La temperatura de precalentamiento y de sostenimiento presentó influencia cuando se analizaron los recubrimiento realizados con electrodos AWS E11018 seguido de electrodos West Hard 400® y con material de última capa West Crome®, con dos y tres capas, esto debido al tratamiento térmico de revenido, aplicado a este material cuando se aumentaron las temperaturas hasta valores de trescientos cincuenta grados, generando mayor cantidad de martensita la cual mostro menor resistencia al desgaste vs. la austenita endurecible por deformación. Lo anterior no se encontró para los recubrimientos aplicados con soldadura AWS E11018, la cual presento una estructura con alta presencia de estructuras de tipo ferrita y perlita acicular, generando corte y deformación plástica en la zona desgastada. Igualmente, se encontró este comportamiento en los recubrimientos realizados con electrodo West Hard 65®, donde se encontró que los factores temperatura y número de capas si influyeron en el valor obtenido de desgaste, este depósito presenta una cantidad de elementos aleantes apreciable, dentro de ellos el cromo, formador de carburos, y que se ve afectada por procesos de dilución, lo anterior explicado por el endurecimiento secundario por precipitación de carburos [17].
De acuerdo a las imágenes obtenidas por microscopia SEM en la zona de desgaste, se puede concluir que los recubrimientos obtenidos con soldadura de alto carbono y alto cromo promueven la formación de carburos del tipo M7C3, de variadas formas y tamaños, los cuales actúan como barrera para la formación de surcos de desgaste, debido a su alta dureza, en el caso de los demás recubrimientos (West Hard 30, West Hard 65, West Hard 400 y AWS E11018) se encontró la formación de desgaste en general por la generación de surcos y desplazamiento plástico en el borde de estos surcos, esto debido principalmente a que estos recubrimientos están formados en su mayoría por estructuras compuestas de fases como ferrita, bainita, martensita y los carburos de hierro, estas fases tienen comportamientos dúctiles y promueven la generación de deformación de tipo plástico. La presencia de los carburos aleados finos en estas estructuras no fue suficiente para limitar la deformación plástica y aumentar así la resistencia al desgaste. En el material depositado por el electrodo West Hard 400®, la deformación genero un endurecimiento suficiente para incrementar la resistencia al desgaste.
5. Conclusiones
Los depósitos realizados con electrodos de alto cromo (West Crome®), mostraron los mejores desempeños cuando se evaluó su comportamiento al desgaste de tipo abrasivo en este estudio.
En los electrodos de baja y media aleación y propuestos como material de relleno (West Hard 30®, West Hard 65 ®, AWS E 11018), no se encontró diferencia estadística en su comportamiento al desgaste y mostraron el mismo mecanismo de desgaste: corte y deformación plástica. Sin embargo, cuando se usó la temperatura de precalentamiento y de sostenimiento de 350°C se observó un aumento en la resistencia al desgaste de los electrodos West Hard 30 y West Hard 65, posiblemente asociado a la precipitación de carburos secundarios en la estructura; y se notó una leve disminución en la resistencia al desgaste del AWS E11018 para esta misma temperatura asociado probablemente a una merma en las tensiones internas.
En los depósitos obtenidos con electrodos West Crome® se encontró por su gran cantidad en porcentaje de cromo (25%) y carbono (3,1%), formaciones ricas en carburos de cromo del tipo M7C3, carburos que poseen una gran dureza y que tienen propiedades antidesgaste derivadas del gran tamaño de los mismos vs. las superficies de corte de la arena. Los carburos se formaron en una matriz mixta de austenita y martensita, lo que hizo prevalecer como mecanismo de desgaste en este caso el microcorte y agrietamiento de los carburos.
Para los depósitos generados con electrodo West Crome se encontró que para la temperatura de precalentamiento y de sostenimiento de 350°C, disminuía la resistencia al desgaste asociado probablemente a la transformación de austenita en martensita producto del revenido.
En los depósitos obtenidos con electrodos AWS E 11018 se encontró que en su mayoría se produce una micro estructura de tipo ferritico-perlitica no acicular en los primeros cordones y posteriormente se promueve la formación de una estructura de tipo ferritico-perlitica acicular, la cual es de baja resistencia al desgaste por su elevada ductilidad y bajo nivel de endurecimiento por deformación, desencadenando como mecanismo de desgaste preferente el microcorte y la deformación.
Los recubrimientos obtenidos con electrodos West Hard 400® presentan un alto contenido en manganeso, característico de los aceros tipo “Hadfield”, el alto contenido de manganeso (aproximadamente 14 %) le confiere a este acero la propiedad de una alta capacidad de endurecimiento por deformación lo cual aumenta su resistencia al desgaste, pasando en las pruebas de microdureza Knoop de valores cercanos a los ciento cincuenta y nueve (159HK), hasta llegar a durezas de quinientos veinte y dos (522 HK). En este caso el mecanismo de desgaste predominante fue le microcorte y la deformación.
Los electrodos West Hard 30® y West Hard 65®, presentaron valores bajos de resistencia al desgaste por la presencia de carburos aleados finos comparados con las superficies de corte de la arena, notándose que a la temperatura de 350°C el West Hard 65 mejoró su resistencia al desgaste haciéndose comparable con el electrodo West Hard 400, vía la precipitación de carburos secundarios.