1. Introduction
The quality of products or services is a reflection of company’s ability to improve by process management [1]. The accomplishment of a quality product or service is the reason why quality management systems (QMS) have been created or improved to assure this characteristic, and at the same time, achieve customer satisfaction. The usage of a QMS is fundamental to support an organization’s performance, providing a range of benefits for improvement; thus, it has a positive effect on organizations [2]. The literature shows many QMSs that are related to attainment of quality in products or services, such as Total Quality Management (TQM), the Malcolm Baldrige National Quality Award (MBNQA), European Foundation for Quality Management (EFQM), Six Sigma (SS), Lean Manufacturing (LM) and the ISO 9001 standard, among others. The main focus of this research is the international ISO 9001 standard, created by the International Organization for Standardization (ISO). The most recent version of the standard is the ISO 9001:2015, which focuses on the adequate management of activities in order to accomplish and exceed customer requirements [3].
The ISO 9001 standard is by far the most implemented and recognized QMS and helps companies to achieve continuous improvements; hence, the standard allows for the guidelines to improve the operational systems of the company. According to the requirement manual of the ISO 9001:2015, the standard is a set of almost 20 complementary standards that provide the theoretical and practical support in almost all the functional areas of an organization for the accomplishment of regulatory requirements and customer requirements.
In this respect, the objective of this paper is to recognize the current situation of the ISO 9001 standard and its critical factors, which allows for the implementation of the standard in the manufacturing sector in Mexico (MSM). To achieve this objective, a survey was first designed to collect data, and secondly, a statistical analysis was carried out to describe the current situation of the standard in Mexico.
2. Literature review
2.1. ISO 9001 standard review
The International Organization for Standardization was founded in 1947 and has created over 21,000 international standards, covering almost all aspects of technology and manufacturing [4]. The first ISO 9000 series from the international quality management standards was published in 1987, and was created to enable a mutual understanding of quality requirements in national and international trades [5]. The ISO 9001 standard defines what the business should do to consistently provide products that meet customer expectations and applicable statutory and regulatory requirements. In addition, businesses will seek to enhance customer satisfaction by continuous improvement of the QMS, regardless of the size or industry type [6].
The ISO 9001 standard uses three approaches as the bone structure of its functionality: (1) Process Approach, which incorporates the PDCA cycle (Plan-Do-Check-Act), enabling an industry to plan the process related to its resources and internals interactions; (2) Risk-Based Thinking, which enables an industry to find circumstances that could cause troubles or malfunctions in the QMS placing preventive controls to minimize negative effects, and also ensures the maximum usage of opportunities as they occur; and (3) the Seven Quality Management Principles (QMPs) [7,8]. Likewise, Heuvel [9] detailed how the standard takes the process approach to improve organizational and financial performances with a specific focus on quality management, process control and quality assurance techniques in order to achieve planned outcomes and to prevent unsatisfactory performance or non-conformance.
The reviewed literature exhibits a variety of concepts concerning the standard. For example, [10] describes the ISO 9000 series as a basic standard used for external quality assurance purposes and is designed for internal use focusing on quality aspects consistency in the production of a product or service. Uzumeri (1997), cited by [11], defined the ISO 9001 standard as the most prevalent management standard certification, spanning a variety of industries. Anttila and Jussila [12] mentioned that the starting point in implementing the ISO 9001standard should be the organizational needs related to the QMS, and [13] described the performance of the standard as including long term contributions and potentially positive, neutral or negative effects, depending on the company’s objective. According to [14], the standard is a provider of an excellent framework that empowers the company to develop a customized QMS to facilitate the optimal deployment of valuable resources into its key processes. In addition, [15] describes the ISO 9001 standard, in the context of Small and Medium Enterprises (SMEs), as one of the legitimation strategies to cope with external pressure and to overcome the liabilities of newness and smallness. Additionally, the ISO 9001 standard is considered to be the first step to develop a QMS and encourages companies to incorporate a continuous improvement culture [10,16-20].
The ISO 9001 standard is a set of formalized processes to evaluate the ability of any organization to consistently design, produce, and deliver quality products and services. This standard provides an important contribution to achieving improved product/service performance [21]. None of the guidelines of the standard contain requirements or acceptance criteria for a product; that is, the standard cannot inspect a product against the standard terms and guidelines. Therefore, the main interest of the ISO 9001 standard is only the QMS of the business [5].
Since the standard update in the year 2000, the ISO began to use the term “principle” as a basic belief, theory or rule, and this has a major influence on the way in which an activity is done. In this case, the QMPs are sets of fundamental beliefs, rules and values that can be used as a basic template or guideline for a QMS to accomplish performance improvement [22]. Taking the idea from [23], these principles can be theorized as the essential components or characteristics that must be achieved by any industry or business in order to produce the greatest advantages and to complete the implementation of the ISO 9001 standard. Organizations trying to implement a QMS continuously seek to identify factors that are believed to be critical for successful implementation. These factors are often defined as Critical Success Factors (CSFs). The CSFs can be theorized as the essential elements that the business must align for successful QMS implementation [2]. Some authors report different factors in the implementation of the standard [13,16,24-26]; however, the CSFs reported essentially match the QMPs. Consequently, these elements can be recognized as CSFs that simplify or empower the adequate implementation of the standard in an industry or business. Below is a list of QMPs (CSFs) and their definitions based on [27] and [7]:
Leadership (LD): Leaders at all levels establish unity of purpose and direction and create the conditions in which people engage the business’s objectives.
Customer Focus (CF): Primary focus of quality management is the satisfaction of customer requirements and the effort to exceed their expectations.
Engagement of People (EP): Essential for the business that people are competent and empowered at all levels to enhance its capability to create and deliver value.
Process Approach (PA): Consistent and predictable results are achieved more effectively and efficiently when activities are understood and managed as interrelated processes that function as a coherent system.
Improvement (IMP): Successful businesses have an ongoing focus on improvement.
Evidence-based Decision Making (EDM): A decision based on the analysis and evaluation of data is more likely to produce desired results.
Relationship Management (RM): For sustained success, a business manages its relationships with interested parties.
2.1.1. ISO 9001 barriers and benefits
Some obstacles prevent the development of the standard. Santos et al., [28] described how these barriers can be associated with a lack of focus on the critical factors for an adequate implementation. The literature classifies the most common barriers in two ways: the barriers related to leadership and those related to the engagement of people. Destitute leadership carries problems such as: misunderstanding ISO 9001 standard requirements, lack of communication between the business areas, financial issues, lack of strategic thinking, poor auditing systems, stationary issues and lack of a continuous improvement focus [29-31]. Barriers related to the engagement of people creates problems such as: lack of cooperation and involvement of people, lack of discipline following new work methods, resistance to change, insufficient training and lack of motivation to improve [32,33]. Another barrier reported is the large time needed for implementation, since some business do not have time to develop this kind of project or the business resources are limited to a very short amount of time [33,34]. Additionally, [31] mentions that the paper work bureaucracy within the business and procedures could stop the fluency of information and decision-making in some cases.
In the context of benefits, the literature consulted reports that these can be acquired by implementing the ISO 9001 standard in all types of businesses or industries. For example, [35] reported a decrease in manufacturing times and the redesign of pieces to reduce waste, which means an increased improvement to the business’ quality system. Moreover, some authors describe how the quality management achieved by the ISO 9001 standard addresses the business to work with TQM [13,20,25]. Some benefits of the ISO 9001 standard are related to the improvement in the manufacturing systems, which leads to the production of quality products, as well as the productivity of the business increasing [33,36,37]. Additionally, [38] described how the ISO 9001 standard improves the speed of services and reduces customer complaints related to banking services. In addition, [39] describes how the SMEs food enterprises can achieve some benefits by implementing the ISO 9001 standard, such as continuous improvement, prevention of nonconformities and customer satisfaction focus. Some authors [30,40,41], agree that a business acquires wide competitive characteristics, which means that the effectiveness of its systems increase the profits, and described how the benefits are related to the effective implementation of the standard; in other words, the organization must maintain the benefits acquired by the standard as long as the organization develops and practices a continuous improvement that focus on increasing profit and productivity. Likewise, [33,37,42] described that, when the industries increase productivity, customer complaints tend to minimize, and as a result, customer satisfaction is improved. Customer satisfaction is synonymous to better customer service, which means the business is accomplishing as many requirements, asked for by the customer, as possible. Additionally, the business involves the customer feedback to improve its systems and services; performance in customer satisfaction may strengthen business relationships that encompass and reach new market shares and marketing tools [12,43]. Another study by [44] describes 20 benefits that are acquired by SMEs in Soudi Arabia, such as: (1) increased quality awareness, (2) efficiency improved in the quality system and quality products, and (3) improved customer service, to mention a few. Dowlatshahi [45] defines how the ISO certified companies placed more emphasis on the relationship with main suppliers in a management supply chain system, obtaining more competitive advantages than those that were not certified, which tended to place more emphasis on price and delivery issues.
The literature reported a variety benefits that were developed by the implementation of the ISO 9001 standard, as well as many barriers that preclude its implementation; however, no literature on these topics was found in the MSM, which represents a lack of information in this context. Hence, this research will analyze the data acquired related to barriers and benefits perspectives, in order to acknowledge the current situation in the MSM.
2.2. ISO 9001 in the manufacturing sector in Mexico
Recently, the ISO survey of Management System Standard Certification [46] reported more than 400,000 organizations certified with ISO 9001:2015 worldwide, of which 2,577 were in Mexico. In accordance with this information, Table 1 represents the subsector classification certified with the ISO 9001:2015 standard in Mexico.
Table 1 Manufacturing subsectors certified with ISO 9001:2015 standard in Mexico.
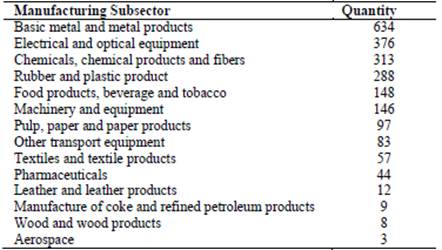
Source: ISO Survey 2018.
The MSM is the second greatest contributor to the Gross Domestic Product (GDP) after the primary activities sector, and has the lowest annual rate of variation of all economical sector in the country, as reported by the National Institute of Statistics and Geography (INEGI, for its acronym in Spanish) [47]. According to the National Statistical Directory of Economic Units (DENUE, for its acronym in Spanish) [48], nearly 36,000 manufacturing industries exist and are classified as SMEs and large companies. It is worth mentioning that, in this paper, the SME classification is the one used in Mexico. Finally, data from the Economic Ministry [49] mentioned that until 2012, 1,442 manufacturing industries, certified in ISO 9001:2008 in Mexico, existed, but unfortunately, this database is not currently operational. Additionally, [46] shows the number organizations with ISO 9001 standard from 2010 to 2017 in North America (United States, Canada and Mexico), as shown in Fig. 1. In the first period of time from 2010 to 2013, an increase in the number of certified organizations can be seen in three countries where, in 2013, the highest number of certified organizations was in the United States and Canada. In the second period of time from 2014 to 2017, Mexico had a remarkable increase, with a tendency to keep growing, while in the United States and Canada, a decrease in the number certified organizations can be observed, where 2017 registered the lowest number of organizations certified.
This resembles the results of [50], which identifies a perspective for certification growth of most countries, with the exception of the United States and Canada mainly after the revision of the standard in the year 2000.
The ISO/TC 176 Technical Committee (TC) on quality management and quality assurance has been a leader in the development of standards in the field of QMS since 1979. The TC 176 develops standards through its three subcommittees (SC), which are responsible for the development and maintenance of the ISO 9001 standard, as well as all adjacent standards within the ISO 9000 series [51]. In Mexico, the management of the standard comes directly from the General Direction of Standardization (DGN, for its acronym in Spanish), which is an internal institution of the Economic Ministry responsible for arranging the Mexican Norms (NOM) in order to coordinate the standardization and conformity assessment systems to promote the competitiveness of the industry and commerce in a national and international approach. The DGN, with The Mexican Institute of Standardization and Certification (IMNC, for its acronym in Spanish), created the NOM series NMX-CC-9001-IMNC-2015, which is in accordance with the ISO 9001:2015 standard in every guideline established by the ISO.
The Mexican Accreditation Body (EMA, for its acronym in Spanish) is a private institution that is responsible for the accreditation of the Conformity Assessment Bodies to evaluate and certify the business once it accomplishes the requirements of the ISO 9001 standard. Fig. 2 shows a representative diagram of the standard management in Mexico.
3. Method
The target population for the study consisted of the manufacturing industries in Mexico that have or have had the ISO 9001 standard certification, preferably in the 2008 or 2015 version, within the SMEs and large company classification. The study relayed the survey made for this research, based on the literature, with 55 items in a five-point Likert scale (1: never, 2: rarely, 3: regularly, 4: almost always, 5: always) that was related to the level of use of each QMP. This survey was divided in four main sections: the first section with 10 items for demographic data; the second corresponded to the items for the QMPs (7 items for LD, 4 items for CF, 6 items for EP and PA and 5 items for IMP, EDM and RM); the third section had 7 items related to benefits; and the last section had 7 items that were associated with barriers. The survey was mainly focused on quality or manufacturing managers; however, any personnel with a position of middle management, related to the QMS of the organization, could respond. Likewise, the sample size was calculated using eq. (1), which considered a finite population. To do this, a population (N) of 37,148 SMEs and large companies, established in Mexico at the time of the study, was used according to [46]. Additionally, a 99% confidence level (Z α ) and a 50% sample proportion (p), and therefore, an equivalent value for q were considered. Finally, a 10% error margin (i) was used to obtain a sample size (n) of 166 responses. The survey was shared by e-mail and the social network LinkedIn, obtaining 537 responses; however, a total of 172 complete responses were used in the study to accomplish the required data for significant results at this level of confidence.
4. Results
4.1. Demographic data analysis
First, Fig. 3 shows the participation percentage in the study by states in Mexico. The principal states with the major participation in the study were Baja California, at 22.10%, follow by Mexico State at 16.90% and Nuevo Leon at 8.70%. According to [48], more manufacturing industries exist in Nuevo Leon, Mexico State and other states than Baja California; however, the geographic location of the authors in this state facilitated the required data.
Regarding the participation of the sub-sectors in the MSM, Fig. 4 shows that the larger percentage of answers were obtained from the machinery and equipment sector, represented as 19.20%, and by the metallic industries and derivatives from petroleum and coal, chemical industries from plastic and rubber, which represented 15.70%. Then, food products, beverages and tobacco represented 15.10%. Finally, the textile industries, clothing and leather industries and paper, printing and related industries contributed 5.20% and 2.30%, respectively. According to these results, the metallic industries and its derivatives from petroleum and coal, chemical industries are the most encouraged manufacturing sectors to achieve the ISO 9001 standard certification in Mexico, which is in accordance with the results of the [46], as displayed in Table 1, as the sectors with more certification acquired. However, food products, beverages and tobacco and machinery and equipment industries have a high percentage of participation in Table 1; meanwhile, the quantity of certified industries in the MSM is not that remarkable. It should be noted that the sub-sectors classification of the MSM in Fig. 4 is the one established by [48].
Furthermore, Fig. 5 represents the industries, certified by size, where large companies identified have higher participation ratios, with 46.50%, followed by medium industries at 38.40%, small industries at 12.80%, and finally, micro industry at 2.30%. Even though this last sector was not the subject of this study, the authors decided to exhibit this result to show the considerations of this kind of company to implement QMS in order to meet customer satisfaction. Finally, these results should be expected, since in the MSM, most of the companies belong to the SMEs and large company sector, according to [48].
4.2. CSF analysis
Table 2 shows the median value, based on the Likert scale previously described, along with the mean and standard deviation (SD) of each factor. LD and CF, with median value of 5, can be considered to be the most significate and important factors in the MSM; however, the remaining factors have a median value of 4; therefore, these factors should not be considered less important since some relation between them could exist that generates the essential characteristics for a successful implementation of the ISO 9001 standard, considering the attainment of more data.
4.3. Barriers and benefits analysis
In the context of the barriers that limit or prevent the implementation of the standard in the MSM, Table 3 shows the results attained. It should be noticed that the questions about this topic were not obligatory; thus, from the 531 responses, only 40 participants described the reasons why their companies do not work under this QMS. The results showed that the main barrier was customers not demanding the industry to work under the guidelines of the standard representing 35%. Another barrier mentioned was the high investment representing 15%. Then, participants described the industry as managing a better QMS than the ISO 9001 standard, representing 10%, and, taking the business line of the industry into account, the standard became unnecessary representing 10%. Additionally, the results showed that the bureaucratic paper work of the standard into the flow of information within the industry restricted the implementation of the standard representing 7.50%. Finally, 9.50% described reasons differently from those included in the survey and the remaining 13% did not specify or select any response.
However, Table 4 presents the benefits obtained by the implementation of the ISO 9001 standard. The percentage of each benefit is related to the number of times it was selected in the survey, considering that each participant could select more than one benefit. According to the information, the benefit with the highest amount of mentions is the increase in customer satisfaction mentioned 72% of the time, besides, 71% of participants emphasized that the reduction errors/defects is another benefit that is obtained by implementation. Another benefit that stands out is integration into the culture of the continuous improvement representing 67%, and, the participants also mentioned the waste or the non-value-added activities of products or services are diminished representing 59%. Finally, the efficiency in decision-making by management and increases in sales are two benefits obtained by the standard implementation mentioned 56% and 50% of the time, respectively.
5. Discussion
In the context of industry size, some similar results were reported in [8,52,53], describing size as an influencing factor in the decision to achieve the ISO 9001 standard, even for [54] the size of a company, which certainly influences the implementation of the QMS, where large companies obtain better results with greater tolerance to changes from the introduction and the subsequent maintenance of the QMS. Additionally, Stainslaus et al., [55] described how the SMEs should learn from the QMS used by large companies.
According to the CSF, the results reported in the literature resembles those obtained in this study. For example, [8,55,56] described top management leadership as one of the main characteristics to arrange a QMS into the organization procedures developing goals and objectives. Further, [57] described how top management leadership and the engagement of people provides for the implementation of the standard. In the same matter, [58] showed that the customer focus, human resources management and the strategic planning of the quality should have the highest consideration when implementing the standard. Finally, [59] revealed that the industries certified in the ISO 9001 standard have an excellent relationship management, and, the organization with engaged personnel also, significantly facilitates the accomplishment of the standard guidelines.
Similar results in the context of barriers were obtained by [60], which described the standard as a beneficial tool for the industry, but at the same time, turns to bureaucratic and complex procedures, which demotivates top management to start the implementation of the standard. Additionally, [61] mentioned that the bureaucracy of the standard in the process, the lack of interest of the management, the high investment and the long time required for its implementation are some of the obstacles and limitations in application. Furthermore, [62] mentioned how the lack of commitment by top management and the financial or resource limitations preclude the assessment of the standard. According to the results, the high investment required and the bureaucracy style of the standard are barriers to implement the standard in the MSM, which resembles the one reported in the literature; however, the lack of demand of the ISO 9001 certification by customers is not reported in the literature as a barrier, while in Mexico, according to the data obtained, this is the main barrier of manufacturing companies not implementing the standard.
The results related to the benefits agree with the findings in the literature, for example, [33,36,39,42], which described how the implementation of the standard increases customer satisfaction and productivity of the company. Likewise, [35,37,44] reported that, when implementing the standard, the integration of the continuous improvement in the company is developed, increasing productivity into the work systems and errors and waste are reduced, thus increasing the benefits. Finally, [63] described the adaptation of the standard to improve the efficiency of operations and marketing strategies, increasing the commitment of people with the accomplishment quality and transforming the organization to work as a synchronized system in order to fulfill the enterprise’s goals.
6. Conclusion
As was previously mentioned, the objective of this research is to recognize the current situation of the ISO 9001 standard in organizations in the manufacturing sector in Mexico taking SMEs and large companies as a reference. This research was focused on describing the critical success factors, as well as the benefits and barriers, which are associated with the implementation of this standard in this kind of organization. According to the literature consulted, the ISO 9001 standard is recognized worldwide as a quality management system that allow companies to implement possible improvements into the quality processes, fulfilling expectations of clients and at the same time profiling the organizations towards continuous improvement. In this sense, it could be mentioned that the implementation of the ISO 9001 standard in the MSM is, nowadays, one of the primary strategies to manage quality and to accomplish clients’ requirements, mainly in large companies and machinery and equipment sectors, as was stablished in the aforementioned results.
Additionally, this work also remarked that the recognition of the CSFs for the ISO 9001 standard as the essential elements that must be accomplished for its successful implementation. The CSFs could be mentioned as a basic task to facilitate the standard’s adoption, and consequently, to get the benefits it could provide, highlighting an increase in customer satisfaction, the reduction of errors or defects, and also the integration of a culture that is based on continuous improvement as was most frequently reported by the surveyed personnel. If this is adequately managed, it could be converted into competitive advantages. In this case, the leadership and customer focus were found to be the most important factors for the adequate and successful implementation of the ISO 9001 standard in the MSM. In other words, top management should lead the continuous improvement of the company, based on wise decisions, to ensure the engagement of employees to comply with work processes and to always focus on customer satisfaction.
Additionally, some barriers that are difficult for the adoption of the standard were analyzed, and according to the results, the lack of demand by customers to work with the ISO 9001 standard is reported to be the main barrier that could lead to organizations not seeking adoption. Therefore, because of the existence of these barriers, the adequate identification of the CSF is highly important because, by focusing on these key elements, the negative effects of the barriers could be counteracted, thus increasing the probability of a successful implementation, and so, access to the corresponding benefits.
Finally, a model could be fitted to define the relationships among CSFs and potential benefits that were reported in this research; hence, future research should focus on analyzing the factors in developing a Structural Model to help decision-makers determine the activities and actions that must be undertaken to facilitate the adoption of this still broadly used standard.