1. Introduction
Titanium is a metal of low density and high hardness, resistant to corrosion, it can be melted, forged, welded and subjected to other processes such as additive manufacturing where the material is processed at a micrometric scale from the use of data and thus produce a real model in three dimensions [1]. Titanium alloy is used as a biomaterial due to its biocompatibility and resistance to corrosion, it forms an oxide layer on the surface that protects the biological environment, being useful within the medical, naval, chemical, and automotive industries.
There are different processes to produce a layer of coarser oxide on the surface of the alloy one, of the most viable methods is anodization due to the intimate and strong chemical link between the titanium-based metal substrate and the coating. Two of the most commonly used electrolytes in the anodization of titanium and its alloys are sodium hydroxide and sulfuric acid, for this reason they were defined as electrolytes for anodizing. The high oxidation resistance of H2SO4 improves anodic oxidation by producing thicker, crystalline coatings [2].
Surface treatment of anodizing has shown that the voltage range for the formation of a more stable layer, is between 27 and 55 volts for H2SO4 + oxalic acid and NaOH, i.e. thicknesses between 70 and 130 nms, managing to decrease the current density [3]. Therefore, anodizing has been used to produce a more stable oxide layer achieving greater corrosion resistance and with fewer metal ions delivered to the solution [4]. TiO2 nanotubes after anodizing have also been shown to increase surface area, which speeds up osseointegration allowing bones and implants to come together faster [5].
This layer of oxide that forms on the surface of the alloy of Ti6Al4V after anodizing has presented surface hardenings greater than 1000 HV and thus increases wear resistance in joint prostheses [6]. It was also observed that the wear resistance of Ti6Al4V alloy with biphasic microstructure alpha+ beta is higher than that of Ti Grade 2 with phase alpha microstructure [7].
The investigation determined the level of wear and corrosion of the alloy Ti6Al4V fabricated by additive manufacturing as in the titanium specimen made by forging both subjected to an anodizing process. During the experimental procedure, the specimens were subjected to microstructural characterization, chemical composition test, microhardness test, and wear resistance test on Pin on Disk, they were anodized with sulfuric acid and sodium hydroxide, also, Ringer´s lactate and Hank’s solution were used to determinate samples’ corrosion resistance.
2. Methodology and materials
We used 12 samples of Ti6Al4V alloy fabricated by additive manufacture by Electron Beam Melting (EBM) with a diameter of 17.7mm, this EBM process is carried out in a vacuum and the construction chamber is maintained at an elevated temperature throughout manufacturing. Table 1 shows the parameters used to manufacture the Ti6Al4V alloy by additive manufacturing through the electron beam melting process.
Table 1.EBM process parameters.
Material: | Ti6Al4V |
Melting point: | 1168°C |
Layer thickness: | 0.05 mm |
Electron beam power: | 3000 W |
Build Volume: | 200 x 200 x 380 mm (x, y, z) |
Source: Arcam EBM data sheet.
Similarly, 12 samples of pure titanium produced by forging, with a diameter of 11 mm, were used. These specimens passed through a cutter with a diamond disc until a thickness of 4 mm was obtained, as shown in Fig. 1.
First, for the anodizing process, a solution of sulfuric acid and sodium hydroxide was used as can be seen in Table 2, in an electrochemical cell containing 200 ml of the electrolyte, which closes the circuit and provides a means for the metal ions to be transported from the anode to the cathode. The cell has an immersed 316 stainless steel cathode that receives the electrons from the circuit and the anode is the titanium alloy. The anodizing process time was defined as 5 minutes for all voltages, at 20 and 40 V, and direct current (DC) was used.
Table 2 Anodizing parameters.
Electrolyte: | Sulfuric acid solution (1M) |
Sodium hydroxide solution (0.1M) | |
Anode: | Ti6Al4V - 3D |
Ti - Forging | |
Cathode: | Steel stainless 316 |
Time: | 5 minutes. |
Voltage: | 20 V |
40 V |
Source: Authors.
The mineralogy of anodized coatings was analyzed by X-ray diffraction (GAXRD; PAN-analytical materials research diffractometer X'pert, PANalytical). A Cobalt anode (CoKα) was used with an energy of 1.79 Armstrong, the angle of incidence of 1° and with the configuration for thin film, the starting position was 10° and the final 90°, a step of 0.012° was defined and the period for this step was 16 seconds.
To evaluate the behavior of the 3D printing and forging samples against wear it was necessary to use the Pin on Disk tribometer brand micro-test. A weight of 3 N was used, with a speed of 120 rpm, the material of the ball is made of cow bone with a diameter of 6 mm and a distance of 500 m. Once the tests were carried out, the morphology of the wear mark in the specimens was observed with an optical microscope to establish their area, depth and height.
Finally, tests of resistance to linear polarization and potentiodynamic polarization (Tafel) were performed and they were obtained using a Gamry brand potentiostat. The reference electrode was Ag/AgCl and the counter electrode was Platinum, the evaluation electrolyte were Hank’s solution and ringer’s lactate, because these simulate the body’s fluid composition. Hank’s solution was prepared at the laboratory, its pH was 7.2. Tafel’s polarization curves were made for each one of the voltages and electrolytes, it was using Hank´s solution and Ringer’s lactate. The initial potential was E=-0.25 V regarding Eoc, and E= 1 mV regarding reference electrode (SCE). The potential scanning speed corresponded to 1 mV/s. Through these tests, the active/passive areas of the specimens were determined.
3. Results and discussion
Through Energy Dispersive X-ray Spectroscopy (EDS) technique, specimens’ chemicals compositions were obtained as Table 3 shows. This analysis allowed us to determine the percentage by weight of the elements, Titanium, Aluminum and Vanadium.
Table 3 Composition of the samples.
Samples | Ti | Al | V | Total |
---|---|---|---|---|
Ti6Al4V - 3D | 89.15 | 6.42 | 4.43 | 100.00 |
Ti - Forging | 99.68 | 0.25 | 0.06 | 100.00 |
Source: Authors.
3.1. Microstructural characterization
Fig. 2, show the alloy of Ti6Al4V has a biphasic microstructure consisting of the phase’s alpha; (rich in Al) and beta; (rich in V), where the alpha phase offers little plasticity and tends to exhibit anisotropic mechanical and physical properties, while the phase beta it has good formability due to its high ductility [8]. Biphasic alloys (alpha+ beta) of titanium are usually classified according to the geometric arrangement: Laminar, equiaxial and mixed (laminar and equaxial known as bimodal). In this case a laminar phase with larger beta grains is presented with a higher density and significantly finer, due to the rapid cooling of the melt bath. Light zones are identified that refer to the α phase and dark zones correspond to the β phase.
The microstructure's chemical composition affects its electrochemical reactions, the β structure promotes a faster growth rate of TiO2 nanotubes than the α structure, causing a difference in morphology of TiO2 nanotubes between the non-anodized and anodized samples. Overall, this is beneficial to bio-implants fabricated out of Ti-6Al-4V because the parts gain the ability to tolerate additional forces that result in enhanced durability during service [9].
Fig. 3 shows a micrography of the grade 4 titanium specimen with a pure α phase microstructure with a larger grain size than Ti6Al4V alloy and the absence of β phase. It allows to observe the edges, grain size and homogeneous distribution, in terms of light and dark areas, they are related to different orientations of the crystallographic planes of grain [10].
3.2. X-ray diffraction
3.2.1. Ti6Al4V alloy manufactured by 3D printing
Tests performed on the Ti6Al4V specimen manufactured by 3D printing revealed high peaks of titanium, and the presence of TiO2 rutile, as Fig. 4 shows. Of tetragonal crystal structure, aluminum and aluminum oxide Al2O3 whose crystalline structure corresponds to hexagonal. The creation of such compounds can be explained by equation (1) where M represents the metallic element (M: Ti and Al) and Z represents the oxidation state of each element (4, 3 for Ti and Al respectively). Results consistent with previous phase analysis studies of oxide films on Ti6Al4V alloy prepared in sulfuric acid solutions [11].
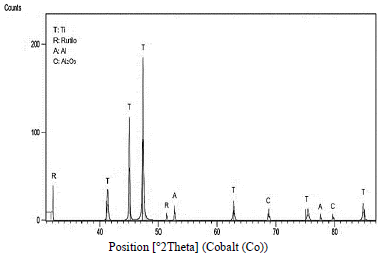
Source: Authors.
Figure 4. Diffractogram of Ti6Al4V alloy manufactured by 3D printing, anodized with H2SO4 at 40V.
The tests allowed to observe the absence of a vanadium oxide aspect that favor the resistance to corrosion since in the research carried out by Metikos-Hukovic it was observed that vanadium can diffuse to the Surface or titanium alloys and oxidizes to form small amounts V2O5, VO2 y V2O3 on the outermost surface. The formation of any of these Vanadium oxides impairs the passivity of Ti6Al4V because they are not strong protectors as Titanium oxides [12].
Source: Authors.
3.2.2. Titanium specimen manufactured by forging
When evaluating the oxide layer formed in the anodized and un-anodized specimens by x-ray diffraction, titanium peaks were found as Fig. 5 shows. The Ti peaks of the substrates are dominating in all coatings, indicating the depth of lightning penetration was greater than the thickness of the substrate ≤34,24μm. The Oxide thin consists mainly of rutile TiO2 and is linearly voltage-dependent, rutile belongs to the Titanium dioxide group being the most abundant and is presented in tetragonal form, it is of great importance in the process of osseointegration of medical titanium implants, because when exposing titanium to oxygen, a continuous layer of native rutile a few nanometers thick naturally forms that completely coats it [3]. This oxide is very stable, adherent, biocompatible and has good mechanical properties. It offers enormous resistance to the action of corrosive substances and prevents the diffusion of harmful metal atoms from the implant to the organism that contains it.
3.3. Wear resistance
3.3.1. Ti6Al4V alloy manufactured by 3D printing
Fig. 6 shows that exposing the alloy of Ti6Al4V to anodizing with sulfuric acid with 40V yields a coefficient of friction of 0.3181 in comparison with the un-anodized sample whose average coefficient of friction is 0.4929, that is to say in the latter the friction causes greater wear which reduces the useful life of the material.
The depth of the wear mark is low after the EBM process because this alloy has a high hardness due to its natural aging, which prevents the cow bone ball from penetrating it. The un-anodized fingerprint depth is 11.72 µm and in the specimen anodized with sulfuric acid a wear mark depth of 5.83 µm, reducing the level of wear. The bone ball loses 2.57% of mass while the specimen anodized with sulfuric acid with 40V loses a minimum amount of 0.59% adhering to small particles in the alloy of Ti6Al4V, an aspect that coincides with the loss of mass of the ball used in the study: Use of Ti alloys as dental implants: Study of tribo-corrosion in biological media [13].
The loss of mass is ratified by performing the weight before and after the wear test, in the same way when evaluating the composition of the oxide layer after the test is found the presence of phosphorus and calcium elements that constitute the composition of the bone ball as observed in Fig. 7. Therefore, the increase in hardness is corroborated when exposing the material to the anodizing treatment, presenting adhesive wear understood as the transfer of material from one surface to another during its relative movement. In the same way the figure shows the wear mark and some of the adhesions of the alloy surfaces, however some of the material detached from the bone ball and attached to the titanium specimen is released in the form of chips.
3.3.2 Titanium specimen manufactured by forging
Fig. 8 shows the coefficient of friction of the specimen manufactured by forging, the level of wear is reduced when performing the surface treatment since a coefficient of 0.3601 is obtained, and in turn the un-anodized material raises the average coefficient of friction to 0.5537 evidencing the usefulness of that treatment.
Similarly, the data obtained establish that the Ti6Al4V alloy manufactured by 3D printing has a lower average friction coefficient, which stands out the feasibility of the use and application of this alloy.
The maximum depth of the wear mark in the specimen manufactured by un-anodized forging is 13.45 µm when contrasted with surface damage The resulting surface in the 3D printed 3D un-anodized Ti6Al4V alloy is lower at 11.72 µm it has a hardness of 354.2 HV due to the fact the microstructure has α+β phase this agrees with the research entitled Improvement of the wear resistance of titanium and its alloys used for joint prostheses made by Manero in which he explained that the wear resistance of ti6Al4V alloy with α+β phase microstructure is higher than that of Ti Grade 2 with α phase microstructure [6].
The specimen manufactured by the forge presents adhesive wear as shown in Fig. 9 identifying surface adhesions, the product of friction between the bone ball and the study material. It is noteworthy that the sample without anodizing presents a greater number of adhesions. When performing the wear test and evaluating the specimen, phosphorus and calcium elements belonging to the ball of cow bone were found. The specimen manufactured by the forge presents adhesive wear as shown in Fig. 9 identifying surface adhesions resulting from friction between the bone ball and the study material. It is important to highlight that the sample without anodizing presents a greater number of adhesions. When performing the wear test and evaluating the specimen, phosphorus and calcium elements belonging to the ball of cow bone were found.
As for the wear values, there is a remarkable difference in the lost mass of the un-anodized specimen, this being 1.36% compared to the result obtained for the specimen anodized with sulfuric acid at 40 V corresponding to 0.74% where a decrease in the percentage of lost mass is seen.
3.4. Corrosion resistance
3.4.1 Polarization curves (Tafel) of Ti6Al4V alloy manufactured by 3D printing
Fig. 10 shows that anodizing with a voltage of 40 V improves the passivity property by decreasing the current density current influencing the material used and delaying its deterioration due to the formation of the oxide layer. It also shows that the corrosion rate decreases when anodizing the specimens because the oxide layer formed causes the titanium to be protected by a non-conductive phase of electronic traffic and in this way the reaction of the metal with the electrolyte is avoided as presented by Sevilla et.al in their work “Anodización del Titanio para la Mejora ante la Degradación Química de Material Quirúrgico” [14].
When working with Ringer's lactate in the specimen without anodizing the corrosion rate rose to 1,735 mpy and when using Hank's solution, it was 1,496 mpy, as for the specimen anodized with sulfuric acid with 40 V in Hank solution the speed was significantly reduced to 0.772 mpy, which means that it becomes more resistant, establishing that the appropriate electrolyte to perform the anodizing process is sulfuric acid since when anodizing with sodium hydroxide a higher corrosion rate was presented in the specimen.
As shown in Fig. 11 the corrosion rate obtained by anodizing the specimen with sulfuric acid at 40 V was 0.772 mpy and for 20 V it was 0.931 mpy, when comparing these results because the corrosion rate decreases, for this reason, the higher the voltage the oxide layer that forms on the specimen is thicker and more resistant.
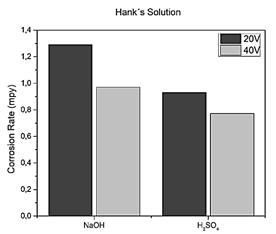
Source: Authors.
Figure 11 3D printed Ti6Al4V alloy, anodized with H2SO4 y NaOH at 20V y 40V in Hank's solution.
As shown in Fig. 12, when using Ringer's lactate for electrochemistry testing, the corrosion rate is higher than when using Hank's solution, therefore the alloy corrodes further with this electrolyte, agreeing with Chiua Tse-Ming and Mahmoudib in their research where they manufactured the Ti6Al4V alloy by powder bed laser melting, evaluating corrosion in Ringer's solution, showing that ringer solution supplied Cl- ions that compromised the oxide layer by the penetration mechanism where aggressive ions diffused within the oxide layer destabilizing the film and causing the active dissolution of the substrate, which led to a more severe loss of the material [15].
3.4.2. Polarization Curves (Tafel) the titanium specimen manufactured by forging
The graphed data make it visible that the current density decreases and the surface treatment with sulfuric acid in the specimen manufactured by forging exposed in Hank's solution, significantly improves the natural passivity properties of titanium by generating a thin layer which increases corrosion resistance.
The corrosion rate in the titanium specimen manufactured by un-anodized forging and exposed to Hank's solution is 1.197 mpy aspect shown in Fig. 13, the specimen anodized with sulfuric acid and voltage of 40 V has a corrosion rate of 0.457 mpy, evidencing the importance of anodizing treatment, the use of sulfuric acid as an electrolyte causes the oxide formed to be denser and thicker than native oxide. The corrosion potential increases making the titanium specimen nobler, this is reaffirmed in the research carried out by D.M. Bastidas and E. Cano where it also increased the corrosion potential by using H2SO4 and HCl thus achieving spontaneous passivation and an improvement in corrosion resistance by thermal anodization-oxidation due to the formation of a stable hydroxide film it acts as a barrier layer [16].
By comparing the results obtained and exposing the two samples in Hank's solution as shown in Fig. 14, the specimen manufactured by forging anodized with sulfuric acid has less deterioration, that is, the corrosion rate is 0.4574 mpy, on the contrary, the corrosion rate increases to 0.7723 mpy in the specimen manufactured by 3D printing, each of them worked at a voltage of 40 V, in this sense the specimen manufactured by the forge that is pure titanium stands out for having more corrosion resistance, so it can be said that the layer is more stable when anodized with sulfuric acid. Hank's solution helps maintain optimal physiological pH (approximately 7.0 to 7.4) due to its inactive nature and its small concentration in solution therefore better results are obtained when using this solution as an electrolyte in corrosion tests.
4. Conclusions
Ti6Al4V alloy manufactured by 3D printing has valuable features that make it an efficient biomaterial in different branches of medicine, it has mechanical properties such as hardness, wear and corrosion resistance that are improved and potentiated with the anodizing treatment. Regarding 3D printing, the social benefit is highlighted by reducing the carbon footprint and the energy consumption is lower than in traditional manufacturing.
The alloy of Ti6Al4V manufactured by 3D printing presents a biphasic microstructure type alpha + beta, aluminum stabilizes the phase alpha preserving the mechanical properties of pure titanium and Vanadium stabilizes phase beta which maintains corrosion resistance. On the other hand, the Ti manufactured by forging presents a microstructure of phase alpha with a larger grain size and the absence of phase beta.
Sulfuric acid, is a strong acid in which protons dissociate completely in water and provide more free ions for oxidation, by acting as an electrolyte in the anodizing process in both the alloy manufactured by 3D printing and forging improves the mechanical properties, corrosion, resistance, in terms of the formation of the oxide layer is uniform.
Previous studies on the behavior of titanium are ratified and complemented with the results obtained during the research as it is confirmed that the anodizing process with a voltage of 40 V in sulfuric acid significantly favors the mechanical properties of hardness and wear on Ti6Al4V alloy. In this regard, several advantages are generated when performing the surface treatment both in the alloy and in its application to the environment, reducing costs and harmful emissions in the manufacturing process that benefit the utility of the material in different fields.