1. Introduction
Self-compacting concrete (SCC) flows under its own weight and occupies the formwork completely, maintains its homogeneity even with the presence of reinforcement [1], the high fluidity and viscosity of this concrete is due to a proper mix design and the use of an extremely water-reducing admixture [2].
The use of SCC has been growing for different reasons over the years, the main reason is its high fluidity without the use of vibrators, ease of placement and better compaction, however, it can have a low resistance, such limitations can be solved by using steel fibers as reinforcement [3], there is research where it was shown that the addition of drawn steel fiber to concrete, manages to enrich its properties, giving greater strength, durability and toughness, achieving a high strength concrete [4].
There is a variety of fibers, either by length or geometric shape. Fiber content is commonly represented as a volume fraction or percentage; shorter fibers give a greater number of fibers than longer fibers for the same volume fraction; smaller fibers can intervene more effectively in the development of microcracks, while longer fibers can improve ultimate strength by controlling the propagation of macrocracks. [5]
High-strength concrete with fiber additions achieves better resistance to tensile and flexural stresses [6]. The incorporation of fibers in concrete favors its resistance to bending and after the first crack, having the capacity to absorb energy [7]. It can be said that the use of fibers helps to reduce the thickness of the structural elements, since it avoids the use of minimum coatings to ensure the integrity of the reinforcement, while the different fibers sew better the concrete matrix, which translates into a better control of cracks and improves its durability [8].
Consequently, to all the above mentioned, research can be found to demonstrate if the SCC with steel fiber additions brings improvements compared to a traditional concrete.
The analysis of prisms tested at 28 days, show that there is an increase in the compressive strength with the concrete mix added with 1% of fiber, on the other hand, shows a constant increase in the flexural strength with the increase of the percentage (%) of steel fiber [9]. In another investigation, a better performance was obtained with the concrete mix, to which fibers were added, with a percentage of 1.50% reaching a modulus of rupture of 99.93 kg/cm2 in an almost linear increase from 0.75% of fiber addition [10].
According to Iqbal [11] in his study, he found a varying influence of steel fiber in hardened concrete, with an increase of steel fiber content from 0.5 % to 1.25 %, showing that it decreased 7% its compressive strength and splitting tensile strength and flexural strength increased to 70% respectively, Therefore, adding higher fiber content improves cracking mechanisms, it was also seen an increase in flexural and tensile strength but reduces the workability of concrete. [12]
The addition of steel fibers to a SCC improves its mechanical properties, but decreases its workability. In this study, it was found that the concrete mix with 20% silica fume and 0.50% of steel fibers achieved self-compatibility, without compaction or vibration, and also its compressive strength increased up to 12.5%. [13]
On the other hand, in the study that used 1% to 3% fiber volume compared to concrete volume, taking into account that an increase in total fiber at 2% or even as high as 3% may not be effective in improving flexural parameters, again the most effective mix percentage was obtained at 1%. [14]
According to Khaloo [15], the use of steel fiber reinforced SCC with a percentage greater than or equal to 2% results in a reduction of machinability well below the recommended limit. The results obtained by Chavez [16] for the SCC design with f'c = 210 kg/cm2, in relation to the normal diameter of the concrete, when adding 0.8% of the amount, the flexural test of the test is 34.97 kg/cm2. The capacity is increased by 8.03%, by adding 1.0% fiber, the flexural strength is increased to 14.03%.
The principal objective of this investigation was to evaluate the physical and mechanical properties of concrete by adding drawn steel fibers to the mix, focusing on the progress of the strengths according to the curing ages.
2. Materials y methods
2.1. Materials
In this research, materials were used that complied with the normalized standards of the American Society for Testing and Materials (ASTM), particularly Type MS cement, with a density equal to 3.12, complied with ASTM C-1157(2010). The fine aggregate was extracted from the Pátapo La Victoria quarry, located in the district of Pátapo, province of Chiclayo, and the coarse aggregate from the Herrera Batangrande quarry, located in the province of Ferreñafe, both in the region of Lambayeque - Perú. The natural aggregates used in the mix underwent a granulometric test according to ASTM C-136 (2006) in which the particle size was obtained, from 0. 15 to 4.75 mm and from 1.19 to 12.70 mm, respectively, whose particle size distribution is shown in Fig. 1 and Fig. 2.
The additive used in the mixture is a polycarboxylate-based hyper-plasticizer, which complies with ASTM C 494 - type F. No control tests were performed on the additive, since the technical data sheet was provided by the supplier
High quality commercial drawn steel fibers CHO 80/60 NB and 65/35 NB were used for the evaluation, with a length of 60 and 35 mm respectively, complying with ASTM A 820 (2019) "Steel Fibers for Reinforced Concrete" Type I, no control tests were performed, since they have a technical data sheet. The materials in question are shown in Fig. 3.
2.2. Mix design
At this point, the proportions of the materials required for each design are determined. Two standard concrete (CP) designs were made, for strengths f'c = 480 kg/cm2 (CP1) and 380 kg/cm2 (CP2) with an admixture percentage of 1.8% and 1.4% respectively, according to the ACI 211.1 (1998) committee method. With the standard design, the 16 mixtures were made with additions according to the volume of concrete in 1%, 1.5%, 2% and 2.5% of drawn steel fibers. The proportions for the addition of fibers in the mixes are shown in Table 1. The mix design was elaborated as established in ACI 211.1(1998), the designs to be used in the SCC are shown in Table 2 and Table 3.
Table 1 Blend designs of SCC with additions of CHO 80/60 and 65/35 NB steel fibers.
Materials (kg/m3) | F’c = 480 kg/cm2 | F’c = 380 kg/cm2 | ||||||||
---|---|---|---|---|---|---|---|---|---|---|
C.P1 | 1% | 1.5% | 2% | 2.5% | C.P2 | 1% | 1.5% | 2% | 2.5% | |
Cement | 480 | 480 | 480 | 480 | 480 | 473 | 473 | 473 | 473 | 473 |
Water | 213 | 213 | 213 | 213 | 213 | 221 | 221 | 221 | 221 | 221 |
Stone | 826 | 826 | 826 | 826 | 826 | 957 | 957 | 957 | 957 | 957 |
Sand | 828 | 828 | 828 | 828 | 828 | 711 | 711 | 711 | 711 | 711 |
Additive | 8 | 8 | 8 | 8 | 8 | 6.13 | 6.13 | 6.13 | 6.13 | 6.13 |
Steel Fiber (80/60; 65/35) | - | 23.46 | 35.20 | 46.93 | 58.66 | - | 23.63 | 35.44 | 47.25 | 59.07 |
Source: Own elaboration
Table 2 SCC mix design for 380 kg/cm2 with relation w/c 0.48.
F’c | Material | Proportion (Weight) | Weight (kg) | % Mix |
---|---|---|---|---|
380 kg/cm2 | Cement | 1 | 473 | 19.97% |
Water | 19.9 | 221 | 9.33% | |
Stone | 2.02 | 711 | 30.02% | |
Sand | 1.5 | 957 | 40.41% | |
Additive | 0.551 | 6.13 | 0.27% | |
Total, for 1 m3 | - | 2368.13 | 100% |
Source: Own elaboration
2.3. Experimental testing
For the preparation of the samples to be tested, first the addition materials were weighed according to the volume of the concrete and then mixed, the mixture after presenting the expected fluidity was poured into cylindrical molds, in this case two types of molds of 30 cm high by 15 cm in diameter and 20 cm high by 10 cm in diameter were used, in the case of the specimens this procedure was performed in a single operation without any type of consolidation. For the beams, molds of 15 cm high by 15 cm wide and 60 cm long were used in the same way.
2.3.1. Physical properties
To determine the physical properties of the fresh concrete, cone flow, "L" box, "V" funnel and "J" ring tests were carried out. The filling capacity tests were carried out as stipulated by ASTM C1611 (2005), by measuring their diameters and time, using the Abrams cone, a tool that is placed on a metal base, in which the entire mold is filled in a single operation, and then vertically lift the cone in a short time, and allow the concrete to spread, to obtain their values, the time it takes to reach some point of the first circle of 500 mm is measured with an accuracy of 0. 1 s, also the four measures of the diameters in perpendicular forms are measured, see Fig. 4(a).
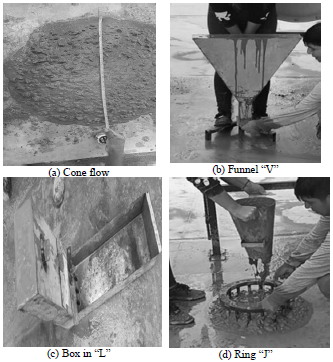
Source: Own elaboration
Figure 4. Photograph of fresh concrete tests: (a) cone flow, (b) funnel "V", (c) box in "L", (d) ring "J".
In the case of flowability, it is evaluated from the ASTM C 1611 (2005) standard, by means of the flow time of the V-funnel, it is performed by firmly placing the V-funnel on the soil to proceed to fill it completely without compacting, wait a few seconds after filling to proceed to open the gate and record the time, as shown in Fig. 4(b). The passage capacity is measured by the L-box and J-ring test, to elaborate the L-box test, first secure the gate to proceed to fill the vertical section with concrete, let stand for a few seconds and then raise the gate and let the concrete flow through the horizontal section, record the time it takes for the concrete to reach the 200 and 400 mm marks, measure the two heights, it can be seen in Fig. 4(c). The Japanese ring test is measured through the diameters in perpendicular forms, it is made by placing the Abrams cone in an inverted way on a rigid plate that will have marked the diameters 500, 650 and 750 mm, then the Abrams cone is filled in a continuous way and flush the surface with a rod to do, proceed to lift the cone, this test should not be elaborated in more than 5 minutes, see Fig. 4(d).
For the hardened state of the concrete, the cores were tested at different curing ages, at 7, 14, 28 days, all were in a curing process as established in ASTM C-192 (2007), to analyze the mechanical properties, the cores were tested in compression, cylindrical tensile and flexural beams.
For the concrete compression test, the parameters provided by ASTM C-39 (2012) were complied with; a concrete electric press was used to break the cylindrical specimens and find the highest compressive strength that supports each specimen at different curing ages, as shown in Fig. 5(a). The same for the tensile test, the cylindrical cores were tested in the electric concrete press, they were placed horizontally for breaking, analyzing the same curing ages, see Fig. 5(b), this test was performed according to ASTM C-496 (2011).
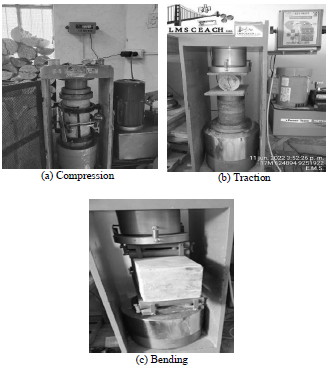
Source: Own elaboration
Figure 5 Photograph of tests performed on hardened concrete: (a) compression, (b) traction, (c) bending.
In flexure the beams were tested, according to ASTM C-293 (2011) the procedure was followed for breaks in an electric concrete press, for different curing ages, see Fig. 5(c).
3. Results and discussion
3.1. Physical properties
3.1.1. Filing capacity
The results of the slump flow test by Abram’s cone show the filling capacity, it is observed that CP1 and CP2 comply, they are within the value of cone runout that varies between 550 and 750 mm, while in the mixtures with additions of 2% and 2.5% of both fibers, there are some cases of flow slump between 510 - 540 mm for the resistance of 480 kg/cm2, in the same way happens 380 kg/cm2 with a flow slump that varies between 500 - 525 mm. All the designs developed for this test are shown in Fig. 6. These variations are due to the addition of drawn steel fiber, which reduces the flow of the concrete, so the higher the percentage of fiber addition, the lower the filling capacity we will obtain. Therefore, it is considered that the presence of drawn steel fiber should be in lower percentages, since the concrete will be more difficult to work.
It can be observed that the data obtained are similar to the results of the studies of Alrawashdeh & Eren [17] that indicated that adding steel fibers slightly decreased the value of slump flow of self-compacting concrete, however, it achieves sufficient workability during its fresh state, being 4.60% the maximum reduction of slump shown with the addition of 0.55% of fiber. The flowability of the SCC in its fresh state is impaired by the amount of steel fibers added, but in this case, they do not affect the workability of the mix.
In the study by Rojales Arce [18], it is mentioned that a decrease in physical properties of concrete such as slump is examined, with a reduction of 40% to 60% with steel fiber additions between 0.5% and 1%.
3.1.2. Fluency
For this test, the time it takes for the concrete to flow through the V-shaped funnel is measured. The test that was elaborated with the funnel in V, showed that the standard concretes 480 kg/cm2 and 380 kg/cm2 are of self-compacting concrete is within the range of a high fluidity, in the experimental samples it is observed that 1% of addition of fiber 80/60 and 65/35 has a fluidity with a range of time that varies between 6 to 7 seconds, with the 1. 5% of addition of both fibers already the concrete takes in flowing in a range of 8 to 9 seconds, for 2% of addition of both fibers the concrete will flow in a slow way, with a little difficulty it will be in a range of 17 to 18 seconds for the concrete of 480 kg/cm2, for the concrete 380 kg/cm2 did not pass the concrete with fiber additions. The experimental sample with 2.5% addition of both fibers is not fluid and presented problems to pass through the V-funnel, as can be seen in Fig. 7.
Sánchez Pérez [19], in his study when performing the V-funnel test, obtained as a result a time of 4.56 sec. with a fiber content of 0.4%, which is respectively low. According to Carrillo [20] in his research concludes that when using the percentage of 1.5% of steel fibers, this affects the flowability of SCC, reducing 7.57%, however, this mixture still complies with the parameters for an SCC.
3.1.3. Passing capacity
The data obtained for CP1 and CP2, in the "J" ring test were for the two diameters 710 - 700 mm and 640 - 630 mm, in compliance with ASTM C162 standard, as shown in Table 4, the percentages of 1% and 1.5% addition vary their diameters from 550-7710 and 540-700 mm, which are acceptable according to the standard already mentioned, for the percentages 2% and 2.5% it is shown that the diameter decreases and therefore decreases its flow capacity.
Table 4 Results of the "J" ring test of the standard and experimental concrete.
Fiber Additions | CP1 | CP2 | ||
---|---|---|---|---|
D1 (mm) | D2 (mm) | D1 (mm) | D2 (mm) | |
C.P | 700 | 710 | 630 | 640 |
1% 65/35 | 690 | 700 | 610 | 630 |
1.5% 65/35 | 600 | 630 | 540 | 550 |
2% 65/35 | 420 | 440 | 410 | 430 |
2.5% 65/35 | 410 | 420 | 400 | 410 |
1% 80/60 | 665 | 670 | 600 | 610 |
1.5% 80/60 | 645 | 650 | 550 | 560 |
2% 80/60 | 465 | 480 | 450 | 470 |
2.5% 80/60 | 435 | 450 | 430 | 440 |
Source: Own elaboration
For the "L" box test, the parameters established by the UNE 83363:2007 standard were followed, for CP1 and CP2, a blocking coefficient of 0.89 and 0.92 respectively was obtained, see Fig. 8. We can observe that up to the addition of 1.5% of the 80/60 and 65/35 fibers it is optimal, its capacity of passage is between 0.73 and 0.9, for the percentages of 2 % and 2.5% its capacity of passage decreases.
Sanchez Perez [19], in his study obtained as results when performing the L-box test, 0.77 which is within the parameter in the norm (0.75-1.00); this indicates that the SCC with steel fiber complies with the corresponding norm; the SCC has a percentage of 0.4% of fiber, obtaining similar data to the research.
It was demonstrated that by increasing the amount of fibers the docility of the concrete decreases and also reduces the passing capacity, this is due to the fact that the fibers increase the cohesion of the composite [21].
3.2. Mechanical properties
3.2.1. Compression resistance
The compression resistance of concrete with different combinations of 80/60 and 65/35 drawn steel fiber as a function of concrete volume, for a design f'c = 480 kg/cm2, shows that, after 7 days of curing, the standard concrete reached a strength of 429.36 kg/cm2. The experimental concrete with the highest strength was obtained with the addition of 1.5% of 80/60 fiber resulting in 455.89 kg/cm2, and for the 65/35 fiber the highest strength was reached with the addition of 1.5% resulting in 490.51 kg/cm2, that is, they reached a percentage of 94.98% and 102.19% corresponding to their required strength with respect to that curing age. Also at 14 days, a significant increase is shown in the concrete with the addition of 1% of 80/60 fiber with a resistance of 526.14 kg/cm2 unlike the previous one mentioned, which is below with 9.02%. In the case of the 65/35 fiber, its maximum resistance continues to be with 1.5% addition. On the other hand, it is observed that, at 28 days, the most favorable percentages are 1% of 80/60 which obtains a resistance of 547.68 kg/cm2 and 1.5% of 65/35 with a resistance of 560.32 kg/cm2, which means that they comply with the design resistance, surpassing that of the standard concrete which reached a resistance of 527.68 kg/cm2. In the same way, it can be seen that for the addition percentages of 2% and 2.5% for the 80/60 fiber, the resistance drops up to 8.86% with respect to the resistance of the standard concrete, in the other additions of the 65/35 fiber, the resistances remain within the expected design up to a minimum of 1% above the standard concrete.
Similarly, it is presented in the compressive strength for a design of f'c = 380 kg/cm2, showing that the most optimal percentage for the 80/60 fiber is 1% of addition, with a strength of 420.85 kg/cm2 at 28 days of curing. For the 65/35 fiber, it was obtained that the most optimum percentage is 1.5% of addition, by which it reaches a resistance of 403.43 kg/cm2, that is to say, they reached a percentage of 110.75% and 106.17% corresponding to their required resistance.
Summarizing the tests carried out at different ages to the SCC with the corresponding fiber additions, Fig. 9(a) and 9(b) are generated for a target strength of 480 kg/cm2 and Fig. 10(a) and 10(b) for an objective strength of 380 kg/cm2.

Source: Own elaboration
Figure 9 Compression resistance of standard and experimental concrete for a f'c= 480 kg/cm2.
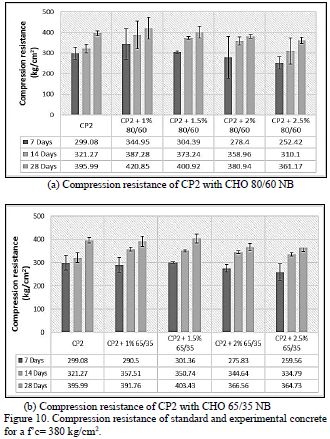
Source: Own elaboration.
Figure 10 Compression resistance of standard and experimental concrete for a f’c= 380 kg/cm2.
The statistical results show that according to the Analysis of Variance (ANOVA) for the samples of the standard concrete and the experimental concrete for f'c= 480 kg/cm2 and f'c= 380 kg/cm2, only some of the samples complied with this test (p>0.05), that is, the additions of the 80/60 and 65/35 drawn steel fibers in the compressive strength of the concrete show that there are significant differences between the results obtained for the strengths obtained. This verifies that the drawn steel fibers, when incorporated into the concrete, influence the properties of the concrete.
After obtaining the data, the DUNNET mean comparison test (0.05) is performed to determine if there is a significant difference between the means of all groups, therefore, the rates of compressive strength values are different. Obtaining from the statistical analysis, the treatment that gave the optimum result for 28 days to achieve a maximum compressive strength for a design of 480 kg/cm2 with 80/60 fiber addition was (CP1 + 1%) and with 114.86% and for 65/35 fiber is that of (CP1 + 1%) with 113.91%, however the maximum compressive strength for a 380 kg/cm2 design with 80/60 fiber addition were (CP2) and (CP2 + 1%) with 103.53% and 105.82% respectively, and for 65/35 fiber is that of (CP2 + 1%) with.
The results obtained are in agreement with the research carried out by Orbe [22], in which he indicates that with the addition of drawn steel fiber, the compressive strength is significantly increased by 21% compared to the standard concretes with percentages of 1.07% and 1.18% of fiber. On the other hand, Farfán Córdova [23] determined that the best result was obtained from the 65/35 steel fiber, since the compressive strength had an increase of 1.1% compared to the control sample. According to Rodríguez de Sensale [24] in his study, a small increase in compressive strength is observed, between 9% and 15%, this commonly occurs with a percentage of fibers greater than 1% in volume.
3.2.2. Traction resistance
The tensile strength in a design of 480 kg/cm2 shows that at 7 days the additions of the experimental concrete have high strengths as in the case of 2% addition of fiber 80/60 obtaining a strength of 43.35 kg/cm2 (92.18%), followed by 1.5% addition of fiber 65/35 which has a value of 44.88 kg/cm2 (95.31%), these being higher than the standard concrete which obtained a value of 40.49 kg/cm2 (95.79%). On the other hand, it is shown that after 28 days, the percentages of 2% addition of 80/60 fiber reached the maximum tensile strength of 53.86% and 1.5% addition of 65/35 fiber, which has a value of 53.35 kg/cm2 (113.34%). Similarly, the results of the experimental concretes designed for a resistance of 380 kg/cm2, that the highest tensile strengths in the experimental concrete were of 2% addition of fiber 80/60 obtaining a resistance of 42.64 kg/cm2 (114.41%) followed by the 1.5% addition of fiber 65/35 that has a value of 53.35 kg/cm2 (53.35%), being these higher than the standard concrete that obtained a value of 39.27 kg/cm2 (105.37%) the two companies achieved a percentage of 110.14% and 113.31% of their required strength.
Summarizing the tensile tests performed at the different ages and with the corresponding fiber additions, Fig. 11(a) and 11(b) for a target strength of 480 kg/cm2 and Fig. 12(a) and 12(b) for a target strength of 380 kg/cm2 are generated.
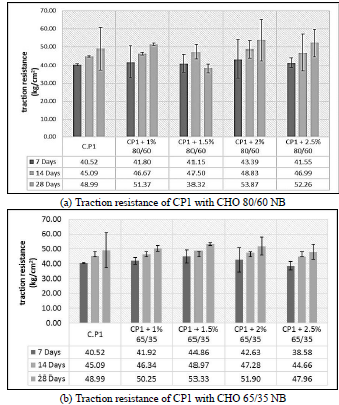
Source: Own elaboration.
Figure 11. Traction resistance of standard and experimental concrete for a f'c= 480 kg/cm2.

Source: Own elaboration
Figure 12 Traction resistance of standard and experimental concrete for a f'c= 380 kg/cm2.
Likewise, the Analysis of Variance (ANOVA) for the samples of the standard concrete and the experimental concrete for f'c= 480 kg/cm2 and f'c= 380 kg/cm2, only some of the samples complied with this test (p>0.05), that is the additions of the 80/60 and 65/35 drawn steel fibers in the traction resistance of the concrete, show that there are significant differences between the results obtained for the resistances obtained.
Obtaining from the statistical analysis performed with the DUNNET mean comparison test, the treatment that gave the optimum result for maximum traction resistance at 28 days for a 480 kg/cm2 design with the addition of 80/60 fiber was (CP1 + 2.0%) with 114.44%, for the 65/35 fiber that gave the highest value in traction was (CP1) and (CP1 + 1.5%) with 104.07% and 111.14% respectively. However, the maximum traction resistance for a 380 kg/cm2 design with 80/60 fiber addition was (CP2 + 2.5%) with 107.68%, for 65/35 fiber it was (CP2 + 2.0%) with 114.29%.
The results obtained are in agreement with the research carried out, in their research by Moya & Cando Lara found that the indirect traction resistance of concrete at 28 days reaches high values with the incorporation of recycled steel fibers, obtaining a favorable increase of 39.08% with respect to standard concrete and 11.64% with respect to concrete with commercial metallic fibers, the recycled fibers achieve higher resistance due to the spiral shape and the roughness shown on the surface. [25]
In this research Saba [13] indicates an improvement of 12% in the division of the traction resistance with respect to the control sample, which contains 1.0 % of steel fibers, with an increase of the steel fiber content from 0.5 % to 1.25 % to the concrete, the traction resistance increased to 70%.
3.2.3. Bending Resistance
The results of the flexural strength for a f'c of 480 kg/cm2, at the age of 7 days show that the highest value is obtained with the addition of 2.5% of 80/60 fiber, which is 63.24 kg/cm2 (134.35%) followed by the concrete with addition of 2.5% of 65/35 fiber, which acquired a flexural strength of 65.79 kg/cm2 (139.77%). These strengths exceeded the standard concrete, which ranked below them with 54.77 kg/cm2 (116.36%). The flexural strength at 28 days shows that the 2.5% percentage of 80/60 addition to the concrete reaches a strength of 78.34 kg/cm2 (166.43%) and for the 65/35 fiber the optimum percentage is 2.5%, obtaining a strength of 76.70 kg/cm2 (162.95%).
The results of the flexural strength in a concrete with a f'c = 380 kg/cm2, the experimental concrete samples achieved an increase over the standard concrete which had 64.57 kg/cm2 (173.25%), Fig. 14 shows that the highest strengths are given by the 2.5% of 80/60 and 65/35 fiber with a strength of 71.40 kg/cm2 (191.57%) and 70.48 kg/cm2 (189.11%) respectively. It can be observed that the higher the percentage of fiber, the higher the flexural strength.
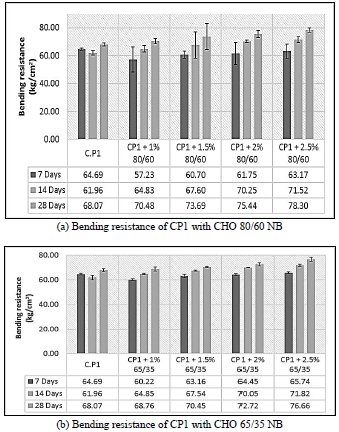
Source: Own elaboration
Figure 13 Bending resistance of standard and experimental concrete for a f'c= 480 kg/cm2.
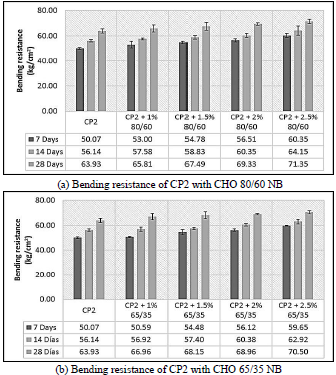
Source: Own elaboration
Figure 14 Bending resistance of standard and experimental concrete for a f'c= 380 kg/cm2.
Summarizing, the flexural tests performed at the different ages and with the corresponding fiber additions, Fig. 13(a) and 13(b) for a target strength of 480 kg/cm2 and Fig. 14(a) and 14(b) for a target strength of 380 kg/cm2 are generated.
The results at the statistical level indicate that the bending resistance data for a design of f'c= 480 kg/cm2 and f'c= 380 kg/cm2, all the samples complied with this test (p>0.05), that is the additions of 80/60 and 65/35 drawn steel fibers in the bending resistance of the concrete.
From the statistical analysis, the mean comparison test of the treatments under study DUNNET test (0.05) shows that the treatment with the highest flexural strength F'c = 480 kg/cm2 for 28 days with the addition of 80/60 fiber was (CP1 + 2. 5%) with a strength of 77.87 kg/cm2, followed by the treatments (CP1 + 1.5%) and (CP1 + 2.0%) with values of 74.65 kg/cm2 and 74.22 kg/cm2 respectively.
The same was done with the 65/35 fiber and we can observe that the treatment with the highest flexural strength at 28 days was (CP1 + 2.5%) with 76.33 kg/cm2, followed by the treatments (CP1 + 2.0%) with 72.91 kg/cm2. For the maximum flexural strength at 28 days for a 380 kg/cm2 design with addition of CHO 80/60 fiber were (CP2 + 2.0%) and (CP2 + 2.5%) with 185.89% and 189.70%, followed by treatments (CP2 + 1.0%) and (C.P2 + 1.5%) with 177.76% and 178.35% respectively, and with the 65/35 fiber were (CP2 + 2.0%) and (CP2 + 2.5%) with 184.57% and 188.36%, followed by the treatments (C.P2 + 1.0%) and (C.P2 + 1.5%) with 177.57% and 179.29% respectively, these two statistically similar.
The results obtained are in agreement with this research of Chavez [16] where they obtained that for concrete of f'c=210 kg/cm2 with normal concrete design had a flexural strength of 34.97 kg/cm2 and by adding the amount of 0.8% of steel fibers increased 8.03% its flexural strength, and by adding 1.0% of fibers increased to 14.03% the flexural strength.
Pająk & Ponikiewski [14] in their research obtained as results that the increase of the total amount of fibers for 2% even up to 3% can be ineffective to improve the flexural parameters, likewise it was obtained that the most effective percentage for the mixtures was 1%. According to Carillo [26] in his study, he concludes that concrete reinforced with steel fiber improves its flexural stress, increasing its resistance by 45%.
4. Conclusions
When measuring the physical properties of concrete with different percentages of steel fiber used, they tend to have a considerable drop in flowability as the percentage of fiber increases.
The percentages of 2% and 2.5% of 80/60 and 65/35 drawn steel fiber added to concrete cause it to lose its properties in the fresh state, such as the passing and filling capacity, which decreases by 40.23% and 43.11% for f'c=380 kg/cm2, 44.55% and 51.60% for f'c=480 kg/cm2, this for both types of fiber.
With respect to the mechanical properties, the addition of drawn steel fiber increases, it increased 1.30% and 3.07% in compressive resistance with respect to the standard concrete of 380 kg/cm2, with 80/60 and 65/35 fiber additions, respectively. It also had an increase of 3.11% and 6.77% in compressive resistance with respect to the standard concrete of 480 kg/cm2, with 80/60 and 65/35 fiber additions, for all cases with 1.5% of fibers.
The traction resistance increased 5.04% and 6.92% with respect to the 380 kg/cm2 standard concrete, with 80/60 and 65/35 fiber additions, respectively. There was also an increase of 7.07% and 9.24% in the compressive resistance with respect to the 480 kg/cm2 standard concrete, with 80/60 and 65/35 fiber additions, in all cases with 1.5% of fibers.
There is an increase of 23.05% and 17.63% in bending resistance with respect to the standard concrete of 380 kg/cm2, with 80/60 and 65/35 fiber additions, respectively, as well as an increase of 21.73% and 18.25% in bending resistance with respect to the standard concrete of 480 kg/cm2, with 80/60 and 65/35 fiber additions, for all cases with 1.5% of fibers.