1. Indroduction
Over the decades, countries all over the world have been committed to adopting solutions to reduce dependence on fossil fuels and lessen their impact on the environment, especially the impact of internal combustion engines [1,2]. Biofuels, such as alcohols, vegetable oils, and biomass, can partially replace petroleum derivatives, thus attenuating environmental damage. From a socioeconomic perspective, the use of biofuels (e.g., biodiesel) has some advantages, such as their production in several areas, renewability, nontoxicity, and smaller amount of NOx emissions during the combustion process. Biofuels create jobs and income in their production chain and help reduce the use of fossil fuels [3].
Nevertheless, when only biodiesel is used, some physicochemical properties are affected, resulting in higher viscosity and higher fuel consumption, which reduces the thermal efficiency of engines, in addition to the high cost associated with biodiesel transesterification [4]. The solution proposed by several studies to improve the properties of diesel lies in its binary and ternary blend with other fuels, such as alcohols. In Brazil, ethanol is one of the most widely used alcohols in the industry because of the huge amount of feedstock and low production costs [2,5]. The low solubility of biodiesel, however, is a limitation for its use in compression ignition engines [6]. Nonetheless, the blends are advantageous, as they compensate for some properties such as the high viscosity of biodiesel, improving its flow rate and, consequently, fuel injection, thanks to the low viscosity of ethanol, thereby ensuring a more complete combustion reaction and reducing pollutant emissions [7].
To circumvent the problem with ethanol solubility, some studies have demonstrated different ways of blending ethanol into diesel or biodiesel, but some precautions and modifications in the engine are required [5]. The percentage of ethanol in the biodiesel-diesel blend should be kept to a minimum, with a purity level around 99% [8], not exceeding 5% by volume, given that higher percentages can cause loss of power. Other authors claim that the percentage can be kept to a maximum of 10% of the volume, unless solubility additives are used because of the miscibility between diesel-biodiesel and ethanol [9].
Regarding the different ratios of ethanol to diesel-ethanol-biodiesel blends, many authors have proposed to perform tests using different changes in operating parameters and blending ratios. Kim et al. [10] used diesel-biodiesel blends at concentrations of 3%, 5%, and 10% of anhydrous ethanol by volume in a four-cylinder compression ignition engine with direct and electronic fuel injection running at a slow load, which eventually decreased efficiency and increased specific fuel consumption (SFC) as the percentage of ethanol increased. According to those authors, when the percentage of ethanol increases, combustion occurs at a slower pace, increasing the ignition delay and affecting other operating parameters. Wu et al. [11] injected 10% and 30% of ethanol into a six-cylinder diesel engine equipped with an electronic injection system, causing a decrease in efficiency when compared to diesel. Ramachander et al. [12] blended 5% ethanol and 20% biodiesel into pure diesel, increasing SFC and reducing efficiency, thus affecting engine power. Alcohols have a low net calorific value (NCV) and lower viscosity as compared to diesel, which affects the blends, leading to an increase in SFC, because a larger fuel consumption is required to have the same power, and efficiency then tends to decrease.
Chockalingam et al. [13] blended 10% ethanol into diesel in a single-cylinder diesel engine and noticed that thermal efficiency was close to that of pure diesel. They also observed a reduction in exhaust fume output and an increase in Nox emissions when the engine was running at full load. However, the use of a stabilizer during the tests could explain their findings.
Some authors, such as Prbakaran and Viswanathan [14], found different results when higher percentages of ethanol were used in biodiesel blends. They observed a decrease in SFC and an increase in thermal efficiency for higher loads containing 50% ethanol and 50% biodiesel, in addition to an increase in the ignition delay and a high heat release rate. This resulted from the reduction of viscosity and density after the addition of ethanol, especially in the presence of high viscosity. Therefore, ethanol allows enhancing the saturation of the injected fuel, providing greater atomization and better air-fuel ratio and improving combustion, which ends up increasing thermal efficiency [2,14].
By drawing upon the studies cited hitherto, the present study aims to experimentally verify the consequences and feasibility of ethanol-biodiesel-diesel blend in a diesel generator set, using commercially available diesel blends (S-10) combined with 1%, 2% and 3% anhydrous ethanol, examining both energy and combustion parameters to demonstrate the pros and cons of using ethanol as an alternative energy source.
2. Materials and methods
As the initial step, commercial diesel oil (S10) was used to obtain reference data (baseline). S10 contains 10% biodiesel, with a maximum sulfur content of 10 ppm. After obtaining the reference data, anhydrous ethanol (with a purity level of 99.90%) was directly blended with S-10 in 1 L beakers at the concentrations of 1%, 2% and 3% by volume, referred to as B10E1, B10E2, and B10E3, respectively. The chosen anhydrous ethanol ratios were employed to verify how the single-cylinder compression ignition generator set (Table 1 and Fig. 1) would behave at minimum concentrations when combined with commercial diesel fuel, considering that, according to the literature, previous tests had been conducted with blends containing percentages greater than 5% v/v [15-17]. Table 2 shows the properties of the fuels used.
Table 1 Diesel generator set technical specifications.
Manufacturer/Model | Branco/BD-6500 CFE |
---|---|
Engine | Single-cylinder, four-stroke, and air-cooled diesel engine |
Type of fuel injection | Direct |
Ignition system | Electronic |
Fuel injection angle | 22° APMS |
Diameter (mm) x stroke (mm) | 86 x 70 |
Engine capacity (cm3) | 406 |
Compression ratio (-) | 19:1 |
Revolutions per minute (rpm) | 3600 |
Source: Manufacturer’s Manual.
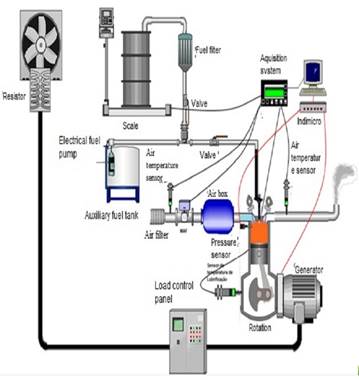
Source: Figure produced by the authors.
Figure 1 Experimental apparatus for analysis of the generator set performance.
Table 2 Characteristics of the fuels used.
Properties | S-10 diesel | Anhydrous ethanol |
---|---|---|
Specific weight at 25 °C (kg/m3) | 791 | 747 |
GCV (kJ/kg) | 43,133.0 | 31,120.0 |
NCV (kJ/kg) | 39,705.7 | 28,260.3 |
Viscosity at 40 °C (cP) | 2.0 - 4.5 | 1.08 |
Cetane number | 40 at least | 8 |
Purity (%) | - | 99 |
Latent heat of vaporization (kJ/kg) | 250* | 903* |
Source: Table built by the authors; *Guedes, 2017.
The tests with B10E1, B10E2, and B10E3 fuels were performed without any modification to the engine and under the same operating conditions. A test using the 3% ethanol blend (B10E3*) was carried out to verify and compare performance after changes in the engine parameters, adjusting the injection pressure of the nozzle from 18 bar to 22 bar. Other fuel injection pressures were tested but, for operational reasons, only the 22 bar pressure was used.
The test time for each fuel amounted to 60 minutes, split into two parts: 1) stabilization and 2) data collection. The averages of 500 cycles were computed every 10 minutes, always checking the exhaust gas and lubricating oil temperature stabilization, fuel consumption, and airflow for approximately 30 minutes. Triplicates of the data were then obtained and used to calculate the averages.
The electrical quantities at the generator’s output, including effective electrical power (Pelec), were measured using a MULT-K Grafic device (Kron®, São Paulo/SP, Brazil). A resistor bank was used to generate different load values in relation to the total engine load. A test was conducted with S-10 diesel, applying different loads to verify the most efficient one, which would then be used in the blends. A load of approximately 79% of the maximum power (3.5 kW) was chosen for testing the blends.
An AVL Encoder 365C rotation sensor was installed on the crankshaft to obtain the crank angle (θ), top dead center (TDC), and engine speed. A GU21D piezoelectric pressure sensor was installed in the engine cylinder head near the intake valve, in addition to an Indimicro 602 charge amplifier, both manufactured by AVL.
The AVL indicom program was used to obtain the in-cylinder pressure curve for each tested fuel, and the start of combustion (SOC) was then determined using the pressure derivative method, given that this method contains fewer reading errors. The mass fraction burned (MFB) is calculated in relation to the net heat release rate. This rate is calculated from the integral heat release fraction, which relates the amount of net heat released at the crank angle to a percent mass of fuel burned [18,19], as shown in Eq. (1)
γ is the ratio between specific heats, c p and c v , which change as a function of temperature; V is the volume of the piston stroke; and p is the pressure of the cylinder gas.
The end of combustion (EOC) was determined by the angle at which 90% of the fuel mass was burned. The ignition delay time (IDT) was obtained by the time span between the start of injection (SOI) and the start of combustion (SOC) [18].
The temperature was read by using type K thermocouples installed in the lubricating oil drain nozzle (T_lubric), in the exhaust gas outlet (T_gas), and in the air intake manifold (T_air) after the air box (expander), in order to verify the moment in which the engine reached the permanent state of combustion and then collect the data. Fuel consumption (
) was directly determined by a DIGIMED precision digital scale, model DG-15WT, which calculates the variation in fuel mass fraction (
) consumed by the engine at a given time (∆t), as shown in Eq. (2). A Bosch mass airflow (MAF) sensor was used to measure the mass airflow rate (
) consumed by the engine.
The signals obtained by the thermocouples, digital scale, and MAF sensor were sent to the A202 data collection and processing system (Contemp Ind.) The system then sent the data to the DAQFactory-Pro software program, v16.2, which analyzed and monitored the variables in real time (Fig. 1).
Specific fuel consumption (SFC), expressed in g/kW-h (see Eq. 3), takes into account the total mass flow rate of all fuels used during the tests (
) (g/h) and Pelec (kW), which is the electrical power of the engine.
i = B10, B10E1, B10E2, B10E3, and B10E3* (pressure: 22 bar)
Moreover, the heat release of fuel in terms of energy was quantified, taking into account
and NCV (Eq. 4) [20]:
The NCV of the blends used during the test was determined by applying the law of conservation of mass to the fuels, considering the energy available in the fuel (
) when ethanol is introduced (Eq. 4) [20].
By considering as a function of the volume flow rate given by
and isolating
and substituting it in Eq. 5., we have:
By isolating the NCV i , one obtains Eq. (5) as a function of the volume fraction of the fuels (x i ):
3. Results and discussion
Calorific value plays an important role in the increase or decrease of SFC, aiding in the analysis of engine performance. Table 2.1 shows the results obtained for the specific mass and NCV of the blends, using Eq. 5.
3.1. Fuel mass flow rate and effective electrical power
The mass flow rate (
) is used to assess consumption when different fuels are utilized. The data provided by the precision scale during the tests (Table 4) show a decrease in fuel consumption with 1% ethanol (1,407 g/h) when compared to S-10 (1,485 g/h), followed by an increase in consumption for the other blends. This increase occurs because the fuel injection system tends to add a larger amount of fuel to accomplish the same displacement, considering that energy is lost when ethanol is added. Fuel consumption increased as ethanol was added to S-10 diesel, accounting for 1,504 g/h (B10E2) and 1,541 g/h (B10E3).
Table 3 Properties of fuel blends
B10E1 | B10E2 | B10E3 | |
---|---|---|---|
ρmix (25°C) kg/m3 | 791 | 790 | 790 |
LHVmx (kJ/kg) | 39.593 | 39.480 | 39.367 |
Source: Manufacturer’s Manual
Table 4 Mass flow rate of fuels used.
Diesel S-10 | B10E1 | B10E2 | B10E3 | B10E3* | |
---|---|---|---|---|---|
Mass flow rate [g/h] | 1,485 | 1,407 | 1,504 | 1,541 | 1,666 |
Power[kW] | 3.54 | 3.30 | 3.04 | 2.64 | 2.92 |
Energy [kW] | 16.4 | 15.5 | 16.5 | 17 | 18.2 |
Source: Manufacturer’s Manual
When the fuel injection pressure was changed from 18 bar to 22 bar, the fuel consumption observed for B10E3* was higher than that of the other blends.
Note that power decreased as ethanol was added to the S-10 diesel blend. This explains the findings obtained for the fuel mass flow rate (Table 4). Power also increased when the injection pressure, 22 bar, was altered in B10E3*.
The thermal energy of each fuel, shown in Eq. 4, can be calculated based on the consumption and NCV of each fuel. Table 4 shows a reduction in thermal energy when B10E1 rather than diesel was used, as there was a small increase in energy when a larger percentage of ethanol was added to the S-10 blend.
3.2. Specific fuel consumption
The findings demonstrate an increase of 426 g/kWh in SFC for B10E1, of 495 g/kWh for B10E2, and of 584 g/kWh for B10E3 (Figure 2), as the anhydrous ethanol to S-10 ratio increased. When the injection pressure was changed to 22 bar, the SFC of the 3% ethanol blend slightly decreased (568.53 g/kWh) compared to the 3% blend at 18 bar.
The lower SFC indicates a better outcome for the S-10 diesel. In percentage terms, we have 1.69% for B10E1, 18.19% for B10E2, and 39.51% for B10E3, when compared to S-10 diesel. Regarding the 3% blends at 18 and 22 bar, SFC decreased by 2.71%.
The significant increase in SFC observed in Figure 2 does not originate from the increase in NCV, because it slowly decreases with the blends, from 39.706 (S-10) to 39.593 (B10E1) kJ/kg, nor does it originate from the variation in the specific mass of the blends, because the specific mass remains approximately constant at 790 kg/m3 (Table 3).
This means that the increase in fuel consumption (Table 4) did not occur because of the new fuel, but rather as a result of the speed of the combustion process. It is known that the delay in SOC causes a reduction in the mean effective pressure (Pme) of the thermodynamic cycle, thereby reducing shaft power. Thus, to be able to keep the shaft rotation and load constant, the frequency control system increases fuel delivery to the cylinder, injecting more fuel, thus increasing SFC and decreasing the thermal efficiency. This hypothesis is checked further ahead.
Kim et al. [10] obtained similar results for SFC for all ternary blends of ethanol-diesel-biodiesel, but at higher percentages (3%, 5%, and 10%), with a different engine running at idle speed. Wu et al. [11] used 10% and 30% in the ethanol to diesel ratio, increasing consumption and decreasing efficiency. This phenomenon is caused by the slower SOC.
3.3. Thermal efficiency
Thermal efficiency, calculated by the ratio between engine electrical power (Pelec) in relation to the mass flow rate (
) and the NCV, can describe the phenomena that occur in the engine in terms of energy performance [9]. The values observed in Figure 3 for the fuels used show a decrease in thermal efficiency as the percentage of ethanol in S10 increases, yielding 21.35% for B10E1, 18.42% for B10E2, and 15.65% for B10E3. These values corroborate those found for SFC, which increases with the ratio of ethanol. Regarding injection pressure, an increase in efficiency was observed for B10E3* at 22 bar when compared to B10E3, at 18 bar.
The engine was running with a high load, thus increasing engine efficiency when the S-10 commercial diesel was used, because of its high NCV, aided by the high temperature inside the combustion chamber. However, the high latent heat of ethanol reduces the combustion temperature, thus reducing the thermal efficiency between ethanol blends as its percentage increases.
Kim et al. and Wu et al. [10,11] report similar findings regarding the decrease in efficiency and increase in SFC, which can be explained by the influence of the lower cetane number of alcohols, the increase in IDT of alcohol mixtures, and the consequent increase in SFC. The increase in fuel injection pressure helps with good fuel atomization, thus improving the combustion process, making it faster, and consequently improving efficiency [13].
3.4. In-cylinder pressure
Figure 4 shows the in-cylinder pressure curves for S-10, B10E1, B10E2, B10E3, and B10E3* fuels with a constant load. There is a decrease in peak maximum pressure when ethanol is added to the S-10 commercial diesel blend. Note that maximum pressure rises (67.76 bar) in the diffusion combustion zone when only S-10 is used, followed by a reduction of 59.69 bar, 50.10 bar, and 49.79 bar for the B10E1, B10E2 and B10E3 blends, respectively, as the ethanol to diesel ratio increases.
In addition to a slight deviation from the TDC, there was an increase in the combustion delay for the blends. The B10E1 blend tended to be similar to the S-10 diesel, as shown on the graph. The high latent heat and low cetane number of ethanol in relation to diesel cause a decrease in the temperature inside the chamber, leading to slower combustion and to lower peak pressure. Can et al. [21] used ethanol, compared with various blends (15%, 30%, 45%, 55%, and 75%), and an injection angle of 17° for the engine used, and high-pressure peaks were verified in comparison to diesel. Data on pressure increases can be found in Wu et al. [11].
In the B10E3* blend (50.50 bar) with an injection pressure of 20 bar, there is a percentage increase in pressure in relation to B10E3, equivalent to 1.45%. The increase in injection pressure led to a faster combustion process, which caused an increase in efficiency and a reduction in SFC, resulting in a greater conversion of heat into work in relation to B10E3, as described in the previous sections. However, the combustion process was slower than for the S-10 fuel. Discrepant results were found by Sayin et al. [22] for injection pressure.
3.5. Heat release rate
Figure 5 shows the heat release rate, which indicates the speed of the combustion process. The faster the heat release, the higher the Pme and the shaft power. The maximum heat release rates recorded during the tests were 86.97, 67.52, 46.32, 39.1, and 38.65 kJ/kg-θ for S-10, B10E1, B10E2, B10E3, and B10E3* fuels, respectively. The height of the peaks decreases with the increase in the percentage of ethanol in the blends, indicating that the presence of ethanol, even in small percentages, increases the activation energy of the blend, causing an ignition delay, as it requires a higher temperature of the blend for SOC. This initial delay also affects the final delay of diffusion combustion.
When the B10E3 and B10E3* blends are compared with different injection pressures, both blends reach a similar maximum pressure at the end of premixed combustion, indicating similar fuel consumption, but diffusion combustion is faster at a higher pressure, and that is expected because a higher injection pressure causes smaller drops of fuel, which evaporate faster. Kim et al. [10] found different values from those shown in Fig 5, higher heat release rates with the increase in the percentage of ethanol.
3.6. Temperature in the combustion chamber
The temperature curves inside the cylinder for S-10, B10E1, B10E2, B10E3, and B10E3* blends are shown in Figure 6. This temperature is crucial for the evaluation of gas emissions resulting from the combustion of different types of fuels, requiring a more in-depth study. However, a more detailed analysis of exhaust gases is not within the scope of the present study.
High temperatures are observed when only S-10 diesel is used, with a maximum peak temperature of 1241 K, which decreases as ethanol is added to the diesel, B10E (1180.5 K), B10E2 (843.84 K) and B10E3 (773.38K). The high cetane number contributes to short IDT, leading to a low premixed combustion temperature and increasing the maximum cylinder pressure due to rapid combustion, resulting in higher temperatures, as observed for S-10, which can eventually increase Nox emissions [23]. The results show an ignition delay, followed by a decrease in the temperature inside the cylinder and a decrease in the combustion duration because of the reduction in temperature at the EOC caused by the higher latent heat of evaporation of ethanol, thus reducing the temperature of the blends. When an injection pressure of 22 bar was applied to the B10E3* blend, when compared to B10E3, an increase in the temperature of the exhaust gases and a slight reduction in the ignition delay were verified, triggered by the elevation of the temperature inside the chamber caused by the evaporation of ethanol. Furthermore, the increase in injection pressure generates faster combustion rates, increasing the temperature of the cylinder gas (Fig. 6). A reduction in the temperature in the combustion chamber was observed by Gnanamoorthi and Devaradjane [24], as a result of the evaporative cooling effects of ethanol, which leads to a decrease in temperature.
3.7. Analysis of the combustion process
3.7.1. Start of combustion
The start of combustion (SOC) was determined by the derivative method using in-cylinder pressure data. The values obtained by the derivative method proved to be more consistent. The SOC results are shown in Table 5.
Table 5 Combustion process parameters.
Fuels | SOC[°] | Ignition delay [°] | EOC [°] | Combustion duration ΔDOC [°] |
---|---|---|---|---|
S-10 (B10) | -1.68 | 22.68 | 24.95 | 26.63 |
B10E1 | 3.31 | 18.69 | 33.2 | 29.89 |
B10E2 | 10.71 | 11.29 | 41.25 | 30.54 |
B10E3 | 10.6 | 11.4 | 70.15 | 59.55 |
B10E3* | 7.81 | 14.19 | 77.75 | 69.94 |
Source: Data compiled by the authors.
Note that, as the percentage of ethanol in the S-10 diesel blend increases, the SOC is delayed. The differences in SOC were due to the speed of the combustion process, triggered by the difference between the cetane numbers of the fuels (S-10 diesel and anhydrous ethanol), which ended up affecting their blends. The high cetane number of the S-10 diesel allowed ignition to start before most of the fuel had been injected into the cylinder, generating high rates of heat release and a more controlled pressure increase. On the other hand, the low cetane number in ethanol with a considerable volume fraction (Table 1) increased SOC, as the percentage of ethanol also increased, leading to a longer ignition delay.
3.7.2. Combustion delay
Combustion delay or ignition delay would be the difference between SOI and SOC at the crank angle (°). According to the manufacturer’s manual, SOI occurs at 22° APMS. Table 5 shows a shorter ignition delay when B10 is used. As expected, the delay increases when ethanol is added to the diesel at 18.69, 11.29, and 11.4° APMS for B10E1, B10E2, and B10E3, respectively. The longer ignition delay is related to the high rate of latent heat of vaporization of ethanol because the temperature inside the cylinder does not reach the temperature required for SOI [11].
The cetane number affects the combustion delay. The high cetane number of diesel caused a shorter ignition delay while the low cetane number of ethanol caused a longer combustion delay because only some fuel was injected and ignition started instantaneously, resulting in faster fuel burning, and this may be one of the causes of the non-development in the premixed combustion phase of B10E2 and B10E3 blends (Table 5). Longer combustion delay was verified in several studies using different percentages of ethanol in diesel-biodiesel blends. Veza et al. [15] perceived a delay in all loads used, with lower peak pressures and low rates of heat release, for low loads. Kim et al. [10] and Ramachander et al. [12] also observed a long ignition delay when they increased the percentage of ethanol in the blend.
The injection pressure increased by 24.47% in B10E3* as compared to B10E3. One of the reasons for that could be the high volatility of ethanol, which enhances fuel atomization, resulting in faster combustion.
3.7.3. Combustion duration and end of combustion
Combustion duration (ΔDOF) is defined as the difference between the SOC and EOC at the crank angle (°). EOC occurred when 90% of the fuel mass was burned (MFB90). Table 5 shows that increases in the percentages of ethanol in the blends delayed the EOC. This is observed in the pressure and heat release rate curves (end of the curve).
The results show the combustion duration for the fuels. The longest interval of combustion duration was observed in the S-10 diesel (26.63°). After the addition of 1%, 2%, and 3% to the diesel, a slower combustion occurred. The shorter combustion duration at the concentration of 1% and 2% resulted from slower combustion, as the temperature for the fuel to burn up could not be reached. With the addition of 3% ethanol, the combustion duration started to increase because of the temperatures inside the cylinder, which had already been heated by the SOI, helping with the autoignition of the blends in premixed combustion, which was extended in the diffusion combustion phase, even with a high ignition delay, observed at the EOC (Table 5). When the injection pressure was augmented to 22 bar, the combustion duration of B10E3* increased, as a result of higher temperatures inside the cylinder, causing the fuel to burn up faster.
In the study conducted by Rocha [25], the combustion duration decreased, but the cycle efficiency increased. Emiroğlu and Şen [23] and Gnanamoorthi and Devaradjane [24] found a decrease in combustion duration because ethanol decreased the cooling time inside the chamber, improving the cycle efficiency. Their findings are at odds with the ones of the present study, in which there was a decrease in efficiency as the percentage of ethanol in the blends increased.
4. Conclusions and suggestions
The tests performed in this study showed that the addition of anhydrous ethanol to S-10 diesel increased SFC, triggered by the speed of combustion in the blends, which is reflected in the shaft power, causing a decrease in effective electric power and also in effective thermal efficiency. As a result, the in-cylinder pressure decreases as ethanol is added. Also, the higher the percentage of ethanol added to the blend, the lower the heat release rate and the lower the temperature inside the cylinder, but SOC and ignition delay increase and the combustion duration is shortened.
The rise in fuel injection pressure from 18 bar to 22 bar attenuated the effects of ethanol on the generator set, with a decrease in the SFC of B10E3*, but power remained high. Similar heat release rates were observed in B10E3 and B10E3*. This change delayed SOC, affected the ignition delay, and increased combustion duration.
In conclusion, the smaller percentage of ethanol affects the combustion process and engine performance under predefined operating conditions, causing changes in various parameters. The factors that contributed to this phenomenon were the low cetane number and high latent heat of ethanol, affecting mainly the ignition delay. Based on the findings obtained in this paper, it is essential that further studies be carried out, making other modifications in compression ignition engines, such as variations in injection pressure and injection angle, in order to find the best alternatives for the use of ethanol as fuel. Ethanol, as an alternative source of renewable energy, can replace petroleum-based fuels.