1. Introduction
Hydraulic turbomachines transform energy efficiently, either from hydraulic to mechanical and electrical energy, as in the case of a turbine, or a transformation of electrical energy to mechanical and hydraulic power, as in the case of centrifuges pumps.
When discussing clean and renewable energy generation, hydraulic turbomachines have played a fundamental role in developing nations. In addition, they have been one of the most widely used renewable energy sources [1], presenting certain advantages over non-conventional renewable sources [2]. Among these advantages, it can be found that hydraulic turbomachines can deliver their energy in a regulated and controlled manner, thanks to the storage of potential energy in reservoirs. The generation of electrical power from renewable sources plays a fundamental role in the sustainable development of a country, especially in those countries that have great hydraulic potential, the vast majority of which are paradoxically developing countries [3], or for countries with a high energy demand that comes from non-renewable sources such as coal and oil [1].
A solution to this problem is the generation of electrical energy in a localized and non-centralized manner, that is, the generation and distribution of power on a small scale near the final centers of consumption, using the available water sources in the areas from the use of reversible and easy-to-handle technologies, such as turbine pumps [4-6].
Characterizing turbomachines, including all their modes of operation, is vital to know their operational limits, zones of maximum efficiency, hydrodynamic, and structural instabilities. This characterization becomes essential for pumps working as a turbine since, thanks to its description, not only operating points can be found but also low-efficiency zones with a high probability of failure, and these characterizations, allow predicting the behavior in a wide operating margin [7].
Although there are advantages when using a pump to work as a turbine, such as an assembly, maintenance, easy access to spare parts, and low initial cost [2, 8-11]. Also, there are some drawbacks when putting them into operation [12-19] because they were not explicitly designed for that purpose. This article is an extension previously presented in Expo Ingeniería 2022 [20].
2. Methodology
A commercial stainless-steel ITT-Gould’s SSH series pump was used, particularly the 5SH [21-22], which has a power of 2 HP. This pump was installed in the turbomachinery test bench of the hydraulics laboratory of EAFIT University, which has a second model 8SH recirculation pump. This schematic assembly can be seen in Fig. 1. The relevant technical information of the turbomachinery study is presented in Table 1.
For data acquisition, a digital platform based on LabVIEW® was used with cRIO-type controllers, especially cRIO-9045 and cRIO-9076, whose technical specifications are in Table 2.
Table 1 Main technical characteristic of the pump as a turbine.
Characteristic | Specification |
---|---|
Inlet diameter | 0.14764 [m] |
Discharge diameter | 0.08104 [m] |
Number of impeller blades | 6 [un] |
Rotor speed | 1750 [rpm] |
Flow rate | 0.009 [m3/s] |
Dynamic head | 10 [mWC] |
Mechanical power | 1491.4 [W] |
Efficiency | 65 [%] |
Motor Power | 2.0 hp - 1491.4 [W] |
Source: Authors.
In addition, instruments for measuring main variables such as flow, pressure, torque, dynamic pressure, and temperature acceleration, among others, were used in the characterization. All sensor specifications can also be found in Table 3.
For the characterization of turbomachines, the international technical standard IEC 60193 is used [23], in which the construction of the four-quadrant characteristic curve is proposed. This curve is constructed using two dimensionless terms, one referring to the flow rate and the other to the rotational speed of the machine, Q ED , and n ED [23]. This characteristic curve shows five typical turbomachine operation forms: pump mode, pump-brake, turbine mode, turbine-brake mode, and pump reverse mode [24-26], explained below.
Table 3 Test ring instrumentation.
Instrument | Output | Range | Span | Linearity |
---|---|---|---|---|
Accelerometer Dytran-3055D6T | ±5 [V] | ±25 [g] | 50 [g] | ±1 [%FS] |
Dynamic pressure Dytran-2005V | 0 - 5 [V] | 0-50 [psi] | 50 [psi] | ±1 [%FS] |
Encoder Omron E6B2-C-CWZ3E | TTL 0 - 5 [V] pulse | 0-6000 [rpm] | 6000 [rpm] | - |
Optical Tachometer DT2234C+ | TTL 0 - 5 [V] pulse | 2.5-99999 [rpm] | 99994 [rpm] | 0.05 [%] +1 digit |
GE TransPort PT878 | 4 - 20 [mA] | 0-0.033 [m3/s] | 0.033 [m3/s] | ±0.25 [%FS] |
PT - Yokogawa-EJA530E | 4 - 20 [mA] | -1-2 [bar] | 3 [bar] | ±0.055 [%FS] |
Source: Authors.
In the pump-type mode operation, mechanical energy is input through the shaft by turning the impeller. It transfers the energy to the fluid, causing it to flow from a state of lower to higher energy seen; otherwise, the flow goes in the opposite direction to gravity.
The pump-brake mode operation is in which, although the rotation system rotates in the direction of the pump, the flow goes from a state of higher to lower energy. This operation can be seen when the pump turns on, and the flow is in the direction of gravity. You can also have this process mode if the rotation speed decreases and the power available in the shaft needs more to overcome the hydraulic power.
In the turbine operating mode, the direction of rotation of the impeller is inverted; that is, it rotates in the opposite direction of the pump mode, and in the brake pump mode, the flow direction goes from a state of higher to lower energy. It goes in the direction of gravity; this flow is generated due to the gravitational impulse, and the hydraulic power makes the rotor’s movement or impeller. This, in turn, transmits it to the axis, transforming it mechanically; this mode of operation is in which hydraulic energy is used to generate other types of fuel, mainly converting it into mechanical energy, and later it is transformed into electrical power.
The turbine-brake operation mode is in which the impeller rotates with energy more significant than that which the fluid can generate; that is, instead of generating power, it spends energy braking the flow, developing resistance to the flow in such a way that the flow This mode of operation tends to be used when a hydroelectric plant must be shut down quickly in a case where valves cannot be closed or the main valve commands so flow slowed down by using high-speed rotation impeller in its turbine rotation mode.
If the rotational speed of the impeller is further increased, the flow no longer goes from the high to the low energy level but starts to pump. This is the pump-reverse mode of operation. Said mode of operation can be obtained in a pump mode by placing the system to work in a rotation opposite to that for which it was designed; this mode of operation can be easily found if you have a bad electrical connection in such a way that the sense engine rotation is opposite. All the modes of operation can be found in Fig. 2.
3. Results and analysis
It was proposed to maintain a hydraulic load or total dynamic head of 4 meters of the water column through the power supplied by the recirculation pump to make the characterization curves. It is essential to be clear that as the rotational speed of the study turbomachine is increased, the speed of the recirculation pump must be decreased and vice versa to guarantee said stable head.
This process was carried out for the two rotation directions of the study turbomachine, from 2000 rpm in its pump mode of operation to 2000 rpm in its turbine mode. Remember that the pump rotation mode is a negative direction of rotation, while the turbine rotation mode is a positive direction of rotation.
A total of 125 measurements were presented in Fig. 3 using the 4-quadrant diagram. Given the limitations of minimum rotation speeds due to the use of frequency inverters to control electric motors, it was not possible to have rotation speeds lower than 200 rpm, which is why there is an interruption in the data around n ED = 0.
It can be evidenced in Fig. 3, all the typical operating modes of reversible hydraulic turbomachines in the turbine quadrant. This quadrant is essential in the characterization of a pump since the fact that there is data in this quadrant demonstrates the possibility of using the pumps as a turbine for recovery energy [27-29].
The traditional way of measuring a turbomachinery’s efficiency, especially of a pump such as a turbine, is through the ratio of hydraulic and electrical power. This process was carried out for all the measurement points; from there, it was possible to estimate the best efficiency point (BEP), as shown in Fig. 3.
Thanks to the dynamic sensors and accelerometers, it is possible to analyze what happens in each turbomachine revolution using the average phase technique [24, 25, 30], allowing us to see a characteristic moderate revolution. This analysis was carried out mainly with the dynamic sensor’s signal, as seen in Fig. 4, in which you can see the blade passage frequency (BPF), which is 6 in total. In addition, this measurement point is the maximum efficiency of the pump working as a turbine, which allows us to see the passage of blades without distortions or hydrodynamic phenomena.
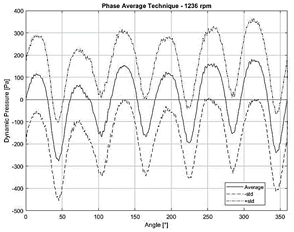
Source: Authors.
Figure 4 Phase Average Technique at the best efficiency point on the turbine quadrant.
This is evidenced in Fig. 5, where a frequency analysis of the point of maximum efficiency is carried out; in addition, the horizontal axis is presented in order, that is, the frequency is divided by the rotation frequency of the turbomachine, thus obtaining the 1X components, which corresponds to something that occurs once every revolution, the 6X that fits a phenomenon that happens six times per revolution, which corresponds to the blade passing.
Due to the different dynamic sensors with which the experimental installation was carried out, it is possible to have the signal for two active sensors and two accelerometers located tangentially next to each other. This allows us to observe how non-invasive sensors can see the same behavior as invasive sensors. In addition, non-invasive sensors or accelerometers will enable us to see other structural and dynamic components that are important in characterizing the pump as a turbine. An example is seen in Fig. 5 since the 3X element appears in the accelerometers, a symptom of misalignment [31], which cannot be seen by invasive or dynamic sensors that can only provide information on the hydraulic component.
Due to the advantages of having a sensor dedicated exclusively to observing the hydraulic dynamic components, hydrodynamic characterizations beyond the 4-quadrant characteristic curve can be carried out, as is the case of defining operating points where instabilities or phenomena occur. Hydrodynamic, as is the case presented in Fig. 6. Initially, nothing different from the principal components 1X and 6X are shown in the accelerometers. In contrast, the dynamic sensors give elements at 0.7X, which offers a sub-synchronous phenomenon which can be classified as a Rotating Stall [16,17,32].
Some turbomachines can find their maximum efficiency points or, failing that, the design point thanks to dynamic sensors [25]. In this case, it is expected that the amplitudes of both vibration and pressure fluctuations will be minimal, thanks to the lower interaction of the rotor-stator area at this point [33,34].
The cavitation analysis is another significant result of characterizing pumps as turbines. Cavitation can be seen in a spectral analysis in areas between 20X and 30X, as shown in Fig. 6.
Appreciating the importance of different dynamic sensors, such as active pressure and accelerometers, is crucial. In this case, apparent differences between what these sensors can observe; for example, in Fig. 6, the dynamic pressure sensors do not present phenomena near the cavitation zone.
On the other hand, in the case of accelerometers, components are present in the cavitation zone, indicating that this phenomenon can be characterized by non-invasive sensors (such as accelerometers). In addition, this can help describe the type of failure that occurs in a turbomachine and how a hydrodynamic phenomenon can affect the machine structurally and new designs [35-37].
4. Conclusions
Through experimental analysis, it was possible to generate the characterization of a hydraulic turbomachine in its different modes of operation, a centrifugal pump working as a turbine, corroborating those centrifugal pumps are reversible machines and that they can be used to generate energy in their mode of operation turbine.
The phase average technique analysis helps us to know in an averaged way the typical behavior of a characteristic revolution of the turbomachine, allowing us to see the passage of the blades of the machine, and even, if it were to occur, this methodology can help to identify a hydrodynamic imbalance in the blade passage.
Spectral analyses allow components based on rotation speed or orders that would identify operating points or hydrodynamic phenomena of interest, such as the point of maximum efficiency or the end with a hydrodynamic instability presented, which can be a rotating stall. This is important for the characterization of turbomachinery since these points with hydrodynamic phenomena must be avoided, or failing that, the pump as a turbine must operate for the least amount of time possible at said points to prevent damage.
Through the characterization process of the pump as a turbine, a maximum efficiency of 57% was obtained in its turbine operation mode. Its pump operation mode obtained a maximum efficiency value of 65%.
It is essential to continue with the characterization of pumps as turbines to define safe operation zones, types of hydrodynamic phenomena presented, typical generation powers and efficiencies, and mechanical and structural problems that can be generated due to the use of a reversible machine in one mode of operation for which it was not designed.