1. Introduction
Particleboard are widely used in the building and furniture sectors [1]. According to FAO data, world production of wood-derived panels was 380 million m3 in 2020 with a 60% growth in the last 10 years. The growing demand for these materials has stimulated the search for alternatives that reduce the environmental impact generated by the excessive consumption of wood. In this sense, following the principles proposed by the circular economy, the use of agricultural wastes as feedstock is a viable alternative for the manufacture of panels [1-4]. Agricultural wastes such as rice straw [5], wheat straw and corn stalk [6], sugarcane bagasse [7,8], hazelnut [9], rice husk [2,10-13] sunflower and topinambour stalks [14] waste tea leaves [15] and green coconut fiber [16] have been proposed as candidates to replace wood in the formulation of particleboards. In particular, rice husk is one of the main agricultural wastes available around the world (more than 150 million tons per year) [17]. Rice husk has a uniform size and can be used without previous grinding for the manufacture of the panels, reducing industrial scale production costs [10,11,18,19].
On the other hand, formaldehyde emissions from commercial panels raise issues of health and safety. Formaldehyde was classified as a carcinogenic agent in 2005 by the International Agency for Research on Cancer or IARC [20]. Several researchers have carried out different strategies to reduce formaldehyde emission levels in wood-based panels, including change of process conditions, treatments with waxes, the use of copolymerizing substances, scavengers and non-toxic hardeners [21,22]. However, although the formaldehyde emission in these boards was reduced, it was not possible to eliminate it completely. Vegetable proteins, such as soy proteins, have emerged as completely formaldehyde-free potential adhesives for wood-derived products, mainly for use in indoor or protected environments, since their adhesive capacity, renewable origin, non-toxicity, annual availability and reasonable costs [23-27]. Although soy adhesives meet the requirements for various applications, their use in humid environments is restricted by their inherently hydrophilic nature. Soybean protein can be modified by means of physical or chemical treatments with denaturing agents such as alkalis, urea, guanidine hydrochloride, and different anionic and cationic surfactants, as a means of unfolding the protein structure, promoting interaction with the substrate and improve the moisture resistance and bonding strength [18,25,28,29].
Another strategy employed is the use of chemical crosslinking agents in the formulation of the protein-based adhesives. Protein chains have reactive groups, such as -OH, -SH, COOH, -NH2, that can react with different crosslinking agents, such as glutaraldehyde, furfural, epoxies, among others [30]. Ghahri and Pizzi [31] incorporated tannins and hexamine (hardener) as modifiers to soy flour adhesives, obtaining plywoods with good water resistance and bonding properties. In a previous study [18], we have modified soy protein concentrate (SPC) with boric acid, alkali, citric acid and urea in order to improve its adhesiveness and moisture resistance. In that study, the effects of the chemical treatments were analyzed by means of Fourier transform infrared spectroscopy, differential scanning calorimetry, thermogravimetric analysis and apparent viscosity measurements, confirming the changes in the secondary structures of protein and crosslinking reactions with the lignocellulosic substrate [18]. Besides, we found that boric acid treated SPC adhesive applied to rice husk composites resulted in panels with better mechanical properties and water resistance, being appropriate for indoor applications as an alternative to those that contain formaldehyde [18,19].
However, the use of soy-based adhesives has been limited since their sensitivity to biological degradation, due to the exposure to microorganisms of these aqueous adhesives during preparation and/or storage (SPC is disperse in water or aqueous solution prior to its application as binder) [32,33]. The use of natural preservatives can help to provide the adhesive a fungus resistance, without modifying the bio-based content [34]. In this case, the incorporation of a biobased phenolic compound to SPC adhesive, as carvacrol, which is recognized as an active component for its antifungal properties, could be an interesting election [35]. In a previous work, the protection effectiveness of carvacrol was studied evaluating the microbiological and storage stability of SPC-based adhesive [3]. In that work, the incorporation of carvacrol reduced the microbiological sensitivity to yeast and environmental molds at high water content SPC based adhesives, maintaining their organoleptic characteristics for at least 30 days.
On the other hand, the improvement of moisture resistance, physical and mechanical properties of composites have been analyzed by applying different materials as coatings, including the use of waxes [36], tung oil [2] and lacquered paints [37], obtaining finished products with a good effect over these properties.
In order to get better understanding of the performance of these completely formaldehyde-free boards, it is essential to evaluate their properties over time under real conditions of use. In this sense, the aim of the present work is to evaluate, over time and under indoor conditions, the performance of highly biobased rice husk boards elaborated with soybean adhesive. Two alternatives were also evaluated: the incorporation of carvacrol as a natural preservative to the SPC based adhesive and the coating of the particleboard with a polyurethane lacquer.
2. Materials and methods
2.1. Materials
Soybean protein concentrate (SPC, Solcon S), with mean composition 69% protein, 15% non-starch polysaccharides, 7% moisture, 5% ash, 3% fibers and 1% fat, was provided by Cordis S.A. (Villa Luzuriaga, Buenos Aires, Argentina). Rice husk was provided by a rice milling industry of Entre Ríos (Argentina). Boric Acid (H3BO3) was obtained of Sigma Chemical Co. (St. Louis, MO) (purity ≥ 99.5%, analytical grade reagent). Carvacrol (CRV, Sigma-Aldrich) was used as natural preservative agent and sodium dodecyl sulfate (SDS, Anedra) was used as surfactant. A water-based commercial polyurethane lacquer (WPL, Sinteplast), with 1.01 g/cm3 of density, was used as coating.
2.2. Soy protein concentrate adhesives
Two types of soybean adhesives were prepared: base adhesive (SPCb) and adhesive with carvacrol (SPCa). SPCb was elaborated according to procedure reported by Ciannamea et al., [18]. Briefly, SPC was dispersed (1:10) into a solution of 3 % w/v of boric acid at 500 rpm for 2 h. On the other hand, the adhesive with carvacrol was prepared according to Larregle et al., [3]. SPCa was obtained similarly, but in this case the SPC was dispersed into a solution of boric acid (3% w/v), CRV (0.5% v/v) and SDS (0.25% w/v) that was previously homogenized for 10 min at 20,000 rpm (Ultra Turrax IKA T18 Basic, Germany). Each adhesive obtained was used immediately in panel preparation.
2.3. Particleboards processing
Medium density boards with a target density of 800 kg/m3 (ANSI A208.1., 2016) were obtained following the same procedure used previously [11,19]. The impurities of rice husk were first removed by washings with water at room temperature. The washed rice husk was dried at 80 ± 2 °C to equilibrium moisture (about 8 wt%). Rice husk and SPC-based adhesives (10 %wt solids of SPCb or SPCa) were blended for 10 min at room temperature in an orbital paddle mixer (Silcook, China). The resulting mixture was dried in an oven at 80 °C ± 2 °C until reaching 40 wt% moisture. The panels were finally obtained by hot pressing (E.M.S. Argentina) at 140 °C and 5 MPa for 25 min, using a steel mold (30 x 30 cm2) equipped with stops to achieve a constant thickness (0.5 cm). The mass of RH-SPC mixture placed in the mold was calculated to achieve the target density. Three groups of panels were prepared: glued with SPCb (RH-SPCb), glued with SPCa (RH-SPCa) and RH-SPCb coated with WPL (RH-SPCbc). Coating was applied using a paintbrush on the top and bottom sides of the panels (~0.03 g WPL/cm2 panel). The three groups of panels were stabilized for 7 days in an environmental chamber at 20 °C and 65% relative humidity. Afterwards, two boards of each experimental group were evaluated (considered as “0 days” board) and the remaining panels were placed in a rack equipped in a laboratory, recording the temperature and relative humidity at intervals of 15 min (Fig. 1). Physical and mechanical properties were determined immediately on two boards of each group taken from rack after 60, 120 and 180 days.
2.4. Particleboard characterization
Density, moisture content, thickness swelling (TS), water absorption (WA) and flexural properties of the boards were determined according to ASTM D1037 [38]. Density and moisture content were determined using six different samples of 50 x 50 mm2 obtained from each type of board (RH-SPCb, RH-SPCa and RH-SPCbc).
At each measurement time, four specimens of 50 x 50 mm2 from each set of panels (RH-SPCb, RH-SPCa and RH-SPCbc) were immersed in distilled water at room temperature in order to measured their TS and WA. The weight and thickness of specimens before and after submersion were determined at 2 and 24 h.
Flexural tests of boards were performed in an Instron-EMIC 20-50 universal test machine (Sao Jose dos Pinhais, Brasil) using 140 mm of span and 2.9 mm/min of head speed. At each measurement time, the modulus of rupture (MOR) and modulus of elasticity (MOE) were determined on rectangular strips of 50 x 200 mm2 from each set of boards. The mechanical behavior of the panels was compared with those requirements established for ANSI standard (ANSI A208.1) [39] for three grades of medium density panel, identified as M-1, M-2 and M-3. Four different samples of each group were measured at each time.
Data for each test were analyzed statistically. Significant differences were analyzed using ANOVA and Tukey’s test (α = 0.05) using the statistical analysis software OriginPro version 8.5.0.
3. Results and discussion
An important parameter in order to produce sustainable boards is the biobased content. The same can be defined as the mass percent of biogenic materials respect to total mass [40]. In this case, polyurethane coating is defined as a petroleum-based material and contribute as the only source of non-biogenic material in the board. Polyurethane coating reduced the biobased content in the RH-SPCbc sample to 91% while the other panels can be considering practically as 100% biobased. Accordingly, all the panels developed in this work can be considered as highly biobased materials. These sustainable boards were subjected to indoor environmentally conditions for 180 days in order to evaluate its stability in the time.
Relative humidity and temperature over time, registered in the laboratory where the indoor experiment was undertaken, are shown in Fig. 2. Temperature and relative humidity varied between 13 °C - 26 °C and 51 % - 84 %, respectively. Temperature exhibited an increasing trend, in accordance with the seasonal weather change (from winter to summer), showing a rise of 13 °C along180 days. Relative humidity mean values did not show significant variations within the frame of the experiment (Table 1).
Table 1 Average temperature and relative humidity in each range of time.
Period (days) | T (°C) | Relative Humidity (%) |
---|---|---|
0 - 60 | 18 ± 1 | 69 ± 4 |
60 - 120 | 20 ± 1 | 70 ± 4 |
120 - 180 | 24 ± 1 | 68 ± 4 |
Source: Self-made.
Average density of each experimental group at the beginning of the experiment (0 days) did not show significant differences and were within the values established for medium density boards grades: RH-SPCb: 813 ± 6 kg/m3, RH-SPCbc: 840 ± 30 kg/m3, RH-SPCa: 820 ± 20 kg/m3. Moisture content values showed a decreasing tendency with time (Table 2), finding significant differences (p < 0.05) between samples measured at 0 and 180 days. This behavior was related with the temperature and humidity recorded in the indoor condition (Table 1 and Fig. 2). Average temperature increased 6 °C over 180 days, inducing a drop in moisture content of 10% approximately for all panels. Similar results were found by Wang and Sun [6] for panels elaborated with wheat straw and corn stalks as temperature increased.
Table 2 Moisture content (%) of boards RH-SPCb, RH-SPCbc and RH-SPCa
Sample/ Time (Days) | 0 | 60 | 120 | 180 |
---|---|---|---|---|
RH-SPCb | 7.9 ± 0.0 a,B | 7.8 ± 0.2 b,B | 7.6 ± 0.2 a,B | 7.2 ± 0.1 b,A |
RH-SPCbc | 7.8 ± 0.1 a,C | 7.5 ± 0.1 a,B | 7.3 ± 0.2 a,AB | 7.0 ± 0.1 a,A |
RH-SPCa | 7.9 ± 0.1 a,C | 7.6 ± 0.1 ab,B | 7.4 ± 0.2 a,B | 7.1 ± 0.1 ab,A |
Mean values in the same column followed by different lowercase letters (comparison between types of boards at each test time) are significantly different (p < 0.05) by the Tukey’s Test. Mean values in the same row followed by different uppercase letters (comparison over time of each type of panel) are significantly different (p < 0.05) by the Tukey’s Test.
Source: Self-made.
The coating can act as a barrier to water, reducing the equilibrium moisture content of the panels. Chalapud et al., [2] and Lesar and Humar [36], obtained boards with low moisture content using tung oil and wax emulsions, respectively, as impregnating/coating agents. However, in this work, despite slight differences were detected (Table 2) between the average equilibrium moisture content of coated (RH-SPCbc) and control boards (RH-SPCb), differences were not statistically significant (p>0.05).
Figs. 3 and 4 display the evolution of thickness swelling (TS) and water absorption (WA) of the boards, respectively, with time. Uncoated boards (RH-SPCb and RH-SPCa) exhibited similar TS and WA values at 2 and 24 h. Contrarily, RH-SPCbc registered the lowest TS and WA values (p < 0.05) at 2 h and 24 h. The coating applied over the surface of the particleboards restricts the possibility of water molecules to diffuse inside the core of the panels, limiting TS and WA. Our results agreed well with those reported by Nemli et al., [37], who found that surface coating improved the TS of panel. The TS and WA of RH-SPCb, RH-SPCbc and RH-SPCa were lower than those reported in the literature, such as Li et al., [5] and Jonoobi et al., [41], who measured TS and WA in composites from rice straws and sugarcane bagasse, respectively, both bonded with urea-formaldehyde resin (UF). Moreover, TS and WA of RH-SPCbc at 24 h of immersion were competitive with those reported by Leiva et al., [11], for boards elaborated with rice husk and UF adhesive, and with those reported by Kwon et al., [13], for rice husk boards using phenol-formaldehyde as binder.
Modulus of rupture (MOR) and elasticity (MOE) obtained for RH-SPCb, RH-SPCbc and RH-SPCa, along with the values established by ANSI standard for medium-density boards, are presented in Table 3. As expected, RH-SPCa showed a similar behavior respect to RH-SPCb, which means that CRV addition had not a significant effect (p > 0.05) in flexural properties of panels. However, coated samples (RH-SPCbc), displayed higher MOR values (p < 0.05) probably due to the effect of the polyurethane coating acting as an additional binder on board surface. In flexural tests the maximum stress value is exerted on the upper and lower panels surface, thus, the presence of the polyurethane binder in both surfaces improved the flexural strength compared with uncoated boards [37]. MOR values of RH-SPCb, RH-SPCa were similar to those reported by Ciannamea et al., [10] who studied medium density rice husk-based boards using phenol-formaldehyde as binder; while MOE values of RH-SPCb, RH-SPCbc and RH-SPCa were higher. Kwon et al., [13] determined the flexural properties of rice husk and phenol-formaldehyde panels with and without the incorporation of wood strands as layers. MOR and MOE results of RH-SPCb and RH-SPCa were comparable with those reported by Kwon et al., [13] for panels without wood layers, while RH-SPCbc presented MOR and MOE values comparable with those obtained for composite panels elaborated with 20% of wood layers. Moreover, comparing flexural results of RH-SPC boards with those obtained from other alternative composites with target density of 600 kg/m3 studied by Klímek et al., [14], RH-SPCb exceed the MOR and MOE of spruce wood composites with methylene diphenyl diisocyanate (MDI) and UF resins as adhesives, while MOR and MOE values of RH-SPCb and RH-SPCbc were similar and exceeded, respectively, those obtained from sunflower, topinambur and cup-plant stalks panels using MDI and UF resins.
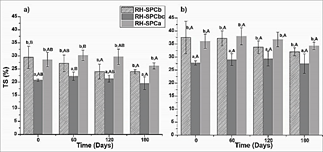
Source: Self-made.
Figure 3 Thickness Swelling (%) of boards a) 2 h b) 24 h. Different lowercase letters (comparison between types of panels at each test time) are significantly different (p < 0.05) by the Tukey’s Test. Different uppercase letters (comparison over time of each type of panel) are significantly different (p < 0.05) by the Tukey’s Test.
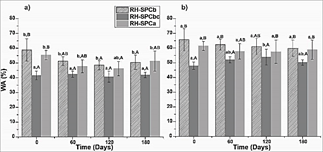
Source: Self-made.
Figure 4 Water absorption (%) of boards a) 2 h b) 24 h. Different lowercase letters (comparison between types of panels at each test time) are significantly different (p < 0.05) by the Tukey’s Test. Different uppercase letters (comparison over time of each type of panel) are significantly different (p < 0.05) by the Tukey’s Test.
Table 3 Modulus of rupture (MOR) and Modulus of elasticity (MOE) means values of composite panels.
Time (Days) | MOR (MPa) | MOE (GPa) | MOR (MPa) | MOE (GPa) | MOR (MPa) |
---|---|---|---|---|---|
0 | 12.3 ± 1.6 a,A | 2.65 ± 0.38 a,A | 17.7 ± 1.1 b,A | 2.79 ± 0.09 a,A | 12.4 ± 1.9 a,A |
60 | 11.4 ± 1.0 a,A | 2.30 ± 0.31 a,A | 17.0 ± 1.5 b,A | 2.53 ± 0.25 a,A | 11.7 ± 1.5 a,A |
120 | 12.2 ± 2.5 a,A | 2.19 ± 0.41 a,A | 17.9 ± 1.1 b,A | 2.49 ± 0.29 a,A | 12.2 ± 1.5 a,A |
180 | 11.9 ± 0.8 a,A | 2.26 ± 0.06 a,A | 18.1 ± 0.9 b,A | 2.68 ± 0.19 b,A | 11.6 ± 1.7 a,A |
ANSI/ A208.1 Grade 1 | M1 | MS | M2 | M3 | |
MOR (MPa) | 11 | 12.5 | 14.5 | 16.5 | |
MOE (GPa) | 1.725 | 1.9 | 2.225 | 2.75 | |
12.3 ± 1.6 a,A | 2.65 ± 0.38 a,A | 17.7 ± 1.1 b,A | 2.79 ± 0.09 a,A | 12.4 ± 1.9 a,A |
Mean values in the same column followed by different lowercase letters (comparison between types of panels at each test time) are significantly different (p < 0.05) by the Tukey’s Test. Mean values in the same row followed by different uppercase letters (comparison over time of each type of panels) are significantly different (p < 0.05) by the Tukey’s Test. 1 M1 and MS are for commercial usage, M2 and M3 are for industrial usage.
Source: Self-made.
MOR and MOE values of RH-SPCb, RH-SPCa and RH-SPCbc panels did not show significant differences over time (p>0.05), and met the requirements established by the ANSI standard. Along the 180 days of study RH-SPCb and RH-SPCa match the standard for M1-grade medium density composite panels, while RH-SPCbc presented a different behavior, exceedingly slightly those values established for M-3 grade. These results suggest that these non-wood free-formaldehyde composite panels show a property profile suitable for standard applications.
4. Conclusions
Highly biobased RH-SPC boards were evaluated under indoor conditions over 180 days in order to study their mechanical behavior and stability in time. Results showed that 100% free-formaldehyde ecofriendly panels have good physical and mechanical stability under the effects of indoor conditions at least up to six months. Besides, the polyurethane coating added to the boards contributed to obtain lower TS and WA at all times. Regarding flexural properties, MOR and MOE obtained for all boards evaluated over time met the requirements established by ANSI Standard A208.1 along the 180 days of study. The higher modulus of rupture (MOR) obtained from the coated panels indicated that the presence of the coating on both surfaces increased the flexural strength.