1. Introduction
Metallic oxides with spinel-type crystal structure have many technological applications due to their various structural, electrical, and magnetic properties [1]. Spinel can be of natural, synthetic, or mixed origin [1-3]. Synthetic spinels can be generated as by-products of various industrial processes, such as iron spinels associated with aluminothermic process slag [4], or spinel-type compounds present in steelmaking powders generated during steel production processes [5,6]. The synthetic formation of metallic oxides with spinel-type crystal structure generally occurs in association with high-temperature processes involving mixtures of aluminum or its oxides with different precursors such as metallic oxides or metallurgical process slags [7-9].
Hercynite is an Fe and Al oxide with a spinel-type crystal structure and a developed chemical formula:
where the values of x and y depend on the stoichiometric Fe/Al ratio and the degree of inversion of the spinel structure [10]. Hercynite can also be found naturally as a dark green or black mineral with a vitreous luster. The iron and aluminum content of this mineral exceeds 30 % by mass, with magnesium being the most common impurity. It occurs naturally in iron-rich clay sediments with a high degree of alteration, in mafic and ultramafic igneous rocks, or in surface mineral deposits with a high degree of alteration. Hercynite is characterized by its high hardness (7.5 on the Mohs scale) and its high melting temperature (1780 °C), so it can be used as a component in abrasive mixes or in the formulation of refractory bricks. The occurrence of natural deposits rich in this mineral is relatively scarce in the earth's crust, but it can be obtained synthetically from its constituent oxides by solid-state reactions at high temperatures or by the electrofusion method [11,12].
Among the industrial by-products that can be used as precursors in the synthetic obtaining of hercynite is steel rolling mill scale. This material is produced during the hot rolling process of steel and is made up of a mixture of iron oxides with small amounts of metallic iron and other impurities [13]. Globally, 13.5 million metric tons of rolling mill scale are generated each year, representing approximately 2 % of the steel produced on a global scale [14]. Its chemical composition may vary depending on the type of steel and on the rolling, process used, but generally has a high iron content (~70 %), accompanied by traces of non-ferrous metals and alkali compounds [15,16].
High-temperature self-propagating synthesis (SHS) has been used to produce a variety of hard and wear-resistant powders and composite materials. This type of synthesis has the advantage of being able to be performed on small-scale processing units and does not require large investments in equipment and facilities. Previous research has proposed the use of aluminothermic reactions for the treatment of iron-rich byproducts from the steel industry, verifying that corundum, hercynite, and metallic iron are among the most common final products of the SHS reaction between aluminum and iron oxides [4,17].
The aim of this work is to propose a methodology for obtaining abrasive ceramics through aluminothermic processing of steel rolling mill scale and aluminum chips, intended for its use in the manufacture of abrasive wheels for polishing floors and terraces.
2. Experimental part
2.1. Raw materials
The raw materials used in this research are steel rolling mill scale and aluminum chips, from the hot rolling process of steel carried out in ACINOX-Tunas and the cutting and machining processes of aluminum laminates in the Empresa de Antenas de Santa Clara, respectively, whose chemical composition is shown in Table 1. The aluminothermic ceramic (slag), added as an inert component, was obtained in the same process and under similar working conditions.
2.2. Formulation of the reacting charges
With the chemical composition data of the raw materials (Table 1), the reacting charge formulations are made based on feasible chemical reactions (reactions 1, 2, 3, and 4). Considering that all the iron present in the mill scale is reduced during the aluminothermic process, the base charge 1 is prepared, to which 15.7 % excess Al is added. Additional charges (Table 2) were prepared from the base charge, progressively increasing the amount of processed charge. Thus, charge 2G is 36 times greater than the initial charge, maintaining equal proportions between the components of the mixture (1).
The theoretical mass balance for the process is carried out from redox reactions 1, 2, 3, and 4, as shown below:
From the calculations of the heat release for each of the reactions, the chemical composition of the raw materials (Table 1), and the mixing data (Table 2), it is determined that the mixture must be able to generate 736.2 cal/g of mixture during its processing, so that the reaction is capable of self-sustaining over time by exceeding 550 cal/g as indicated by Zhemchuzuy [20].
As a result of the mass balance, it is determined that after processing each of the charges, the final product will consist of an iron-rich alloy and a ceramic product, according to the quantities shown in Table 3. The theoretical composition of the metallic product is 93.70 % Fe, 5.90 % Al, and 0.22 % Si, while for the ceramic product it is 99.80 % Al2O3 and 0.20 % MgO.
2.3. Synthesis of Ceramics and Alloys
The different components of the charge, once weighed according to the established proportions, are added to the mixer in the following order: aluminum chips, ceramic, and steel rolling mill scale. Mixing is carried out in a rotary mixer for 30 minutes, and then subjected to preheating in an oven at 250 °C before being processed in a graphite reactor. The reaction is initiated by the action of the electric arc, and the feeding of the charge to the furnace is carried out quickly and uninterrupted in the same proportion as the reaction progresses. Once the melting process is completed, the mixture is allowed to cool, and the metal and ceramic are extracted, with the metal at the bottom and the ceramic at the top. The obtained ceramics were ground in a steel ball mill to achieve a fineness lower than 1 mm in particle diameter.
3. Results discussion
3.1. General considerations
The classic reaction of thermite between iron oxides and aluminum produces high temperatures (≈3000 K), above the melting point of both reactants and even the intermediate and final products of the reactions [16,21]. Generally, inert components are added to the mixture to solve this difficulty, which consume part of the energy generated by the redox chemical reactions [22-24]. The choice of additional components can be evaluated according to the goals of the process, using, for example, fluxing elements in alloy production processes [20] and ferroalloys for aluminothermic welding [25].
Orru, et al. [17] studied the incorporation of alumina and silica as a diluent of the mixture, evaluating the influence of each one on the process and the products, and Perdomo, et al. [26,27], have studied the use of mixtures of high-purity minerals or concentrates with other minerals or solid industrial residuals as a way to recover the metallic elements present in both minerals and industrial residuals.
In the present work, the obtaining of a ceramic with the required hardness for the manufacture of abrasive powders is studied, using only solid industrial residuals as raw materials. For this reason, ceramics generated from the same aluminothermic process are selected as the inert component (diluent), which allows reducing the amount of heat generated per unit mass while maintaining stability in the chemical composition and properties of the new ceramics obtained.
3.2. Results of metallurgical processing
The results of the processing of each charge in terms of the amount of metal and ceramic are summarized in Table 4, while Fig. 1 shows photos of the products obtained in each of
Table 4 Results of aluminothermic processing.
Mixture | Obtained metal (g) | Yield (%) | Obtained ceramics (g) | Yield (%) |
---|---|---|---|---|
1 | 100 | 88.1 | 112 | 116.9 |
1G | 1114 | 81.7 | 1393 | 121.3 |
2G | 2865 | 70.1 | 4585 | 133.1 |
Source: Own elaboration
the processed charges. In all cases, the ignition process of the charges was adequate, maintaining the reactivity of the mixtures self-sustained until the end of the process, achieving a good separation between the metal and the ceramic, as can be seen in Fig. 1. This aspect allows us to confirm that the amount of inert component (ceramic) added to the charge was appropriate.
Table 4 shows that the metal yield decreases as the amount of processed mixture increases, while the ceramic yields increase. It should be noted that in the case of charge 2G, the reactor was completely filled with melted material once the process was concluded without any spills of molten material outside, as shown in Fig. 2.
The combustion products of Fe2O3/Al thermite comprise at least one heavy metallic phase (reduced metallic iron and intermetallics) and a light ceramic phase (Al2O3). Since these phases are mutually insoluble and have very different densities (metal/ceramic density ratio ≈1.9), phase separation occurs during cooling, which influences the structure of the final products. In none of the processed charges was there any evidence of unreacted mixture, so it is considered that the process design favors the formation of iron-aluminum spinels. The decrease in the contents of the metallic fraction in the final products is associated with an increase in the iron content in the ceramic fraction, mainly forming iron spinels. Although different types of spinels could be formed during aluminothermic processing depending on the composition of the raw materials that make up the initial charge, in the case of the studied mixture, the amount of present magnesium is low, so a mixture of Al2O3 (corundum) and FeAl2O4 (hercynite) should be obtained as the primary ceramic product, and a heavy metallic phase.
Multiple mechanisms have been proposed to study the reduction processes of iron oxides with aluminum. Orrú et al. [28] analyzed the mechanism proposed by Korchagin and Podergin, which suggests the occurrence of several chemical reactions as shown below:
Although in their work Orrú et al. [28] ruled out the use of equations 8, 9, and 10 due to the lack of evidence of the presence of metallic phases in their process, in the case studied in this research, a metallic phase was obtained, so all reactions can occur, and the extent of each one depends on the processing conditions. Based on these reactions and the chemical composition of the raw materials (Table 1), a new mass balance is performed, allowing the determination that the process will result in a ceramic with a theoretical composition of 56.1 % FeAl2O4, 43.7 % Al2O3, and 0.2 % MgO and an alloy consisting primarily of 87 % Fe and 13 % Al. Additionally, the theoretical amounts of metal and ceramic that will be obtained are calculated, which allow determining the yields of metal and ceramic for the new evaluated conditions. These results are provided in Table 5.
Table 5 Results for formulated loads (g).
Mixture | TM (g) | OM (g) | Y (%) | TC (g) | OC (g) | Y (%) |
---|---|---|---|---|---|---|
1 | 100.22 | 100 | 99.8 | 109.07 | 112 | 102.7 |
1G | 1202.69 | 1114 | 92.6 | 1308.79 | 1393 | 106.4 |
2G | 3608.06 | 2865 | 79.4 | 3926.38 | 4585 | 116.8 |
TM: theoretical metal, OM: obtained metal, TC: theoretical ceramic, OC: obtained ceramic, Y: Yield.
Source: Own elaboration
If the results of Tables 4 and 5 are compared, it can be observed that the mass balance performed based on the formation of spinels allows obtaining results closer to reality. Naturally, the same tendency to increase ceramic yields as the amount of processed material increases while decreasing the amount of metal is observed.
If highly exothermic aluminothermic reactions are considered as the active agent in a quasi-adiabatic process, since they only exchange heat with the walls of the reactor, the energy source will depend only on these reactions. Therefore, adding more reactant mixture will only increase the amount of heat generated and the time it takes for the heat to transfer to the crucible (the cooling time of the molten material). As a result of the reduction process, a phase rich in metallic and intermetallic compounds and a ceramic phase (slag) with very different densities are generated, causing the metal to immediately go to the bottom while the ceramic stays on top. This temporal phenomenon favors the consolidation of the ceramic component formation reactions at their different stages, since these have a solidification temperature much higher than that of the metal, favoring the formation of spinel-type compounds from the longer time spent in the liquid state, which coincides with the lower presence of metal in the ceramic. This behavior explains the increase in ceramic yield and the decrease in metallic content as the amount of processed load increases.
If hercynite is decomposed into the oxides it contains, it can be obtained that the ceramic will be composed of approximately 77 % Al2O3 and 23 % FeO. If this composition is placed on the FeO-Al2O3 phase diagram at point A in Fig. 3 [29], it can be seen that at temperatures of approximately 1870 °C, corundum crystals begin to be released, producing a mixture of corundum and liquid until reaching the eutectic point (≈1750 °C) where the mixture crystallizes completely. As a result of this process, a solid phase composed of the previously mentioned corundum + spinel mixture must be generated, which due to its chemical and phase composition and slow cooling conditions will have refractory characteristics (melting temperature between 1750 - 1860 °C) and abrasive due to its high hardness, greater than 8 on the Mohs scale.
Characterization of the ceramic by XRD
Fig. 4 shows the X-ray diffraction pattern of the ceramic product obtained in the aluminothermic process of the Fe2O3/Al system. The diffraction pattern was obtained using a Panalytical Empyrean diffractometer employing CuKα radiation and a Pixel1D solid-state detector. The diffraction patterns were obtained between 5 and 65° (2θ), with an angular step of 0.017° and a time per step of 80 seconds, using a high-definition X-ray mirror to improve the monochromaticity of the X-ray beam. Phase identification and quantitative analysis using the Rietveld method were performed using the XPert HighScore Plus 3.11 (2010) software and the ICSD 2009 database. The content of amorphous phases or those with very low degrees of ordered crystalline structure was estimated using the external standard method from the calculation of the K factor using a reference sample of high purity and crystallinity α-Al2O3 whose diffraction pattern was obtained under the same experimental conditions.
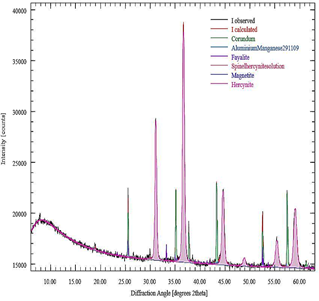
Source: Own elaboration
Figure 4 X-ray diffractogram of the ceramic product obtained by aluminothermy from aluminum chips and mill scale.
Table 6 Results of the quantitative analysis by XRD of the ceramic product obtained by aluminothermy from aluminum chips and mill scale.
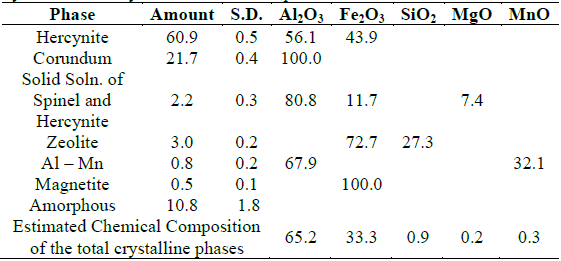
S. D.: Standard deviation
Source: Own elaboration
The results of the quantitative phase analysis are presented in Table 6, along with the estimated chemical composition for the sample. This chemical composition was calculated from the chemical formulas of the different crystalline phases detected in the XRD analysis and therefore does not include the contribution of those chemical elements that may be part of the amorphous or poorly crystalline phases present in the analyzed material.
Table 6 shows the results of the quantitative phase analysis using the Rietveld method, where a high degree of agreement was obtained between the experimental diffractogram and the calculated X-ray pattern, with a goodness of fit index of 1.84. The results obtained are consistent with the theoretical analyses performed on the occurrence of the process. The main products obtained, hercynite and corundum, constitute more than 80 % by mass of the ceramic obtained. The similarity between the densities of hercynite and corundum contributes to a greater homogeneity in the distribution of the ceramic phases during the crystallization process. In addition to the main phases, small amounts of non-stoichiometric crystalline substances (≈ 6 %) and vitreous (≈ 11 %) are present, which make up approximately 15 % of the ceramic obtained.
Based on the quantitative results of the XRD analysis, it can be estimated from the FeO-Al2O3 binary diagram that the fusion temperature of the ceramic is between 1750 and 1800 °C (point B of Fig. 3), which has a high degree of agreement with the values estimated from the mass balance considering the formation of spinels. In the case of the vitrified phase, it is very likely to be composed of alumina and iron oxide (II) and will be distributed throughout the ceramic mass of the aluminothermic reaction, acting as an interface binder between the corundum and hercynite grains, which guarantees its use as an abrasive material. Overall, the results obtained are promising for the use of the ceramics obtained in the manufacture of abrasive wheels for the polishing of floors and terraces, which was confirmed under real production conditions.
In liquid-phase products of aluminothermic reactions, alumina and Fe spinels with contents > 58.7 % alumina are the first phases to crystallize, and depending on the experimental conditions, especially the spinel, can continue to crystallize during the evolution of the ceramic phase, varying in composition and morphology [30][31]. Variations in their composition and morphology, combined with the fact that they are relatively refractory, very hard, and weather-resistant, have made them useful abrasive, polishing, and cutting tools, which is an incentive to study the variations in the chemical and physical conditions of the aluminothermic ceramic from the conditions under which they crystallized.
4. Conclusions
The study of the composite charge of steel slag (70 %), aluminum chips (23 %), and ceramic (7 %) allowed, through the appropriate selection of raw materials and aluminothermic processing, the obtaining of an iron-aluminum alloy and a ceramic, self-sustained (Q = -736 cal/g of mixture) with adequate separation of the metal and ceramic, which improves with the increase of the pyrometallurgical charge mass processed.
The use of mass balances to evaluate the results of pyrometallurgical processing offers more extensive forecasts when formulated from the chemical reactions of complex compound formation (such as hercynite), determining that as a result of the process, an alloy consisting of 87 % Fe and 13 % Al and a ceramic formed by 56.1 % FeAl2O4 and 43.7 % Al2O3 should be obtained, with a melting temperature between 1750 - 1860 ºC.
During the aluminothermic processing of the formulated mixtures, it was observed that the ceramic yields increased as the amount of pyrometallurgical mixture processed increased, while the metallic yields decreased, which is associated with the increase in hercynite content in the ceramic obtained, which is related to the increase in real heat released and the increase in solidification time of the obtained ceramic.
Based on the results of XRD, it was established that the ceramic phase is essentially constituted by hercynite (61 %), corundum (22 %) with small amounts of non-stoichiometric crystalline substances (≈ 6 %) and vitreous substances (≈ 11 %), which corresponds to a hardness on the Mohs scale of around 8 and a melting temperature between 1750 and 1800 ºC, results equivalent to those obtained with the mass balance. It is feasible to affirm that these ceramics can be used in the manufacture of abrasive wheels for the polishing of floors and terraces.