Introducción
Los esfuerzos del mundo en la reducción de las emisiones de gases de efecto invernadero junto con el abastecimiento renovable de energía está orientado en reducir la dependencia a los combustibles fósiles. El principio de la bioeconomía es la utilización de los recursos renovables y/o residuos de otros procesos para la generación de bienes y/o servicios [1,2]. Estas energías renovables toman cada vez mayor relevancia. Tecnologías como la gasificación de biomasa, la cual es un proceso termoquímico de combustión incompleta en donde la biomasa y el agente gasificante generan gas pobre [3,4]. Este gas está compuesto de H2, CH4, CO, CO2 e hidrocarburos ligeros o pesados, conocidos como alquitranes (tar). Esta tecnología es amigable con el medio ambiente, utiliza un combustible no fósil para la generación de diferentes productos químicos, energía eléctrica o térmica y podría alcanzar, con algunas configuraciones, balances neutros de emisiones de CO2. El gas generado se puede acoplar a sistemas de calderas, motores de combustión interna, quemadores y turbinas de gas [5,6]. La eficiencia energética de un gasificador puede alcanzar rendimientos superiores al 50 %%, dependiendo del tipo de gasificador, la calidad de la biomasa y del agente gasificante (aire, oxígeno, vapor de agua, entre otros) o mezcla de estos [7,8]. El componente principal de la tecnología es un reactor de gasificación donde ocurren diferentes procesos como el secado, volatilización, reacciones de oxidación, craqueo y reformado. Para esta tecnología existen diferentes tipos de reactores, entre los que se tienen: lecho fijo (de tiro ascendente o descendente) o lecho fluidizado (burbujeante o circulante). Este último, ha sido menos estudiado por la complejidad en el proceso operativo del fluidizado, pero tiene grandes ventajas como la posibilidad del escalado debido a su mayor capacidad de gasificación, contenido de alquitrán medio-bajo y control de las variables operativas [9-11].
Una limitante de la tecnología de gasificación es el acondicionamiento del gas obtenido, debido al efecto nocivo de los alquitranes en los sistemas, causando corrosión, obstrucción, entre otros. Las tecnologías clásicas para el acondicionamiento del gas se basan en procesos físicos o químicos. Los procesos físicos como el filtrado y lavado de gases son métodos sencillos de diseñar y operar, pero su principal inconveniente es el volumen de efluentes a tratar que genera. Dentro de los químicos se encuentran, los métodos térmicos no catalíticos, los alquitranes son craqueados a temperaturas mayores a 1000 °C con tiempos de residencia altos, generando sobrecostos y grandes volúmenes de residuos carbonosos (char). Otra alternativa, es el método térmico catalítico, en el cual usa catalizadores que transforman los alquitranes a temperaturas más bajas y con mayores rendimientos a gases y con calidades aceptables según el uso.
Se han estudiado diferentes tipos de catalizadores en la gasificación de lecho fluidizado, como metales de transición soportados Ni/Al2O3 [12], Fe/ olivina [13,14], Fe/carbón activado [15], entre otros [16,17]. Los catalizadores a partir de minerales naturales como la dolomita u olivina son de gran interés; estos catalizadores de bajo costo y en determinadas condiciones de operación pueden alcanzar porcentajes de conversión de alquitrán superiores al 90 % [ 18,19]. La principal desventaja que presentan es el desgaste y desactivación por la deposición de carbón. En la actualidad, en los procesos de gasificación catalítica se han ido incorporando catalizadores que son reciclados de otros procesos. Esto dando solución al gran volumen de residuos industriales generados, como son los char/biochar de la pirólisis y/o la gasificación de diferentes materiales. La característica más llamativa es que este material puede utilizarse nuevamente en el proceso para ser gasificado, sin dejar huellas ambientales. La actividad del char/biochar como catalizador, se atribuye a sus especies catalíticas (metales alcalinos y alcalinotérreos) inherentes o incorporados a través de un proceso de síntesis [20- 22]. El objetivo de este trabajo fue construir y optimizar un sistema de gasificación con un reactor de lecho fluidizado autotérmico y catalítico a escala banco. El residuo de biomasa seleccionado para los ensayos fue aserrín de pino. Las condiciones de operación estudiadas para la optimización del proceso no catalítico fueron el flujo másico de alimentación y tamaño de partícula de biomasa, el flujo volumétrico del agente gasificante como el aire y vapor de agua, perfiles de temperatura, entre otros. Con las condiciones óptimas se evalúo el proceso catalítico, utilizando dos sólidos de bajo o nulo costo como dolomita (Dol) y un residuo de un proceso de pirólisis (RP).
Experimental
Reactor de lecho fluidizado burbujeante
La elección del reactor de gasificación a construir es de gran importancia debido a que existen distintos tipos de reactores. La elección está sujeta al tipo de biomasa a tratar, la capacidad y los requerimientos de calidad del producto obtenido (syngas) [7]. En este trabajo se construyó un reactor de lecho fluidizado de acero inoxidable con características similares a lo reportado por Pengmei Lv et al. [23]. Se eligió, este tipo de reactor de lecho fluidizado, debido a la posibilidad futura de un mayor escalado y al contenido de alquitrán que se obtiene en el gas, lo que permite evaluar la actividad de los catalizadores en el proceso. A lo largo del reactor se distribuyeron 5 puntos para la medición simultánea de la temperatura. Para trabajar en forma autotérmica fue necesario aislar su exterior con una camisa de Abra de vidrio y una cubierta de acero inoxidable. En la parte superior se instaló un punto de medición de presión de marca GV de hasta 60 psi (~4 bar) y una válvula de esfera cuya función es de alivio del sistema y punto de carga del catalizador o material inerte al lecho fluidizado. En la parte inferior del reactor tiene un distribuidor de gas (cámara de viento), el cual está compuesto por una malla de acero inoxidable de 6 cm de diámetro y tamiz #60 (250 mm), que permite que la ceniza pase al colector e ingrese el agente gasificante al reactor fluidizado. También se encuentra el sistema de encendido, compuesto por una entrada de mezcla gas propano-aire y un sistema de bujía que está asociado a un generador eléctrico de arco alto voltaje 8000 v, con este mecanismo se genera la chispa para el encendido del reactor. En la Tabla 1, se observan las pruebas de fluidizado con el material inerte. Estos ensayos se realizaron con un flujo controlado de aire en una réplica del reactor construida en vidrio (parte del fluidizado). A partir de estas pruebas se determinaron diferentes parámetros como: la masa del sólido fluidizado, velocidades y alturas del lecho fluidizado.
Tabla 1 Parámetros del reactor de lecho fluidizado.
Parámetro | Valor |
---|---|
Porosidad lecho de arena | 0,50 |
Diámetro promedio de partícula arena [m] | 0,00037 |
Diámetro de la zona del lecho fluidizado [m] | 0,04 |
Diámetro de la zona del freeboard [m] | 0,057 |
Velocidad máxima de fluidización [m/s] | 0,66 |
Velocidad mínima de fluidización [m/s] | 0,066 |
Altura mínima de fluidización [m] | 0,25 |
Altura de lecho fluidizado [m] | 0,82 |
Altura TDH (Transport Disengaging Height: altura de desenganche de transporte) [m] | 0,56 |
Masa del sólido fluidizado (inerte o catalizador) [g] | 400 |
Unidad de alimentación de biomasa y agentes gasificantes
La unidad de alimentación está compuesta por dos tolvas (principal y secundaria) construidas en acero inoxidable. La capacidad volumétrica de 13 L de la tolva primaria fue determinada asumiendo un flujo másico de aserrín de 1 kg/h, con la densidad del aserrín de pino 0,24 g/cm3 y un tiempo de operación continua mínima de 3 h. Debido a inconvenientes observados como la formación de arco y/o formación de eje rat holing, se instaló un visor en la tapa superior y en la parte externa una hélice acoplada a un motor giratorio que hace vibrar constantemente la tolva, proporcionando movimiento al material del interior para asegurar una alimentación continua. En la parte superior de la tolva principal se encuentra la tolva secundaria, la cual está conectada por una válvula hermética que hace posible el llenado de la tolva principal durante las pruebas sin generar problemas operativos y permitiendo la continuidad en la operación. Esta tolva secundaria tiene una capacidad volumétrica ~7 L y tiene en su parte superior una válvula que permite su llenado.
La alimentación de la biomasa se realiza a través de un tornillo sinfín que tiene una longitud de 40 cm y diámetro de 1,5 cm en forma de hélice con un espaciado de 3 cm. El tornillo va desde la tolva hasta el centro del reactor de lecho fluidizado. Funciona acoplado a un motor trifásico SIEMENS 1LA7063-4AB10 de 0,18 Kw, controlado por un variador de frecuencia (50 Hertz), que hace posible cambiar la velocidad de dosificación de la alimentación.
En el caso de los agentes gasificantes (AG), se empleó aire y vapor de agua. El sistema de alimentación de aire está compuesto por un compresor de marca BTA TOOlS, que cuenta con una serie de filtros trampa de humedad y un rotámetro marca ODIN con válvula aguja con capacidades de flujo de alrededor de 10 - 100 L/ min. Mientras que para la generación del vapor de agua se usó una bomba dosificadora Dosivac, con capacidad máxima de 2 L/h, que inyecta agua a un intercambiador de calor y luego es dirigido al reactor de lecho fluidizado. La elección del flujo y tipo de agente gasificante es de gran relevancia en los diferentes rendimientos del proceso y propiedades del gas generado. A continuación, se mencionan los parámetros relacionados a los tipos de agente gasificante empleados en este trabajo:
Relación equivalente (ER); es la relación entre el oxígeno alimentado y el requerido estequiométricamente para una combustión completa, por lo que siempre es menor a 1 y se considera que el valor óptimo para la gasificación esta entre 0,25 - 0,40 [24,25].
Relación gasificación (GR): cuando el agente gasificante es una mezcla de oxígeno o aire y vapor de agua, es la relación entre el oxígeno más el vapor de agua alimentado y la biomasa, se considera que el valor optimo esta entre 0,7 - 1,2 [4,26].
Unidad de retención de material particulado
La unidad de retención de partículas está compuesta por un ciclón, un colector de partículas y un filtro de Abra de vidrio calefaccionado; ambos construidos en acero inoxidable. El ciclón es una operación unitaria que aprovecha la fuerza centrípeta para separar las partículas del gas a través de la fuerza gravitatoria [27]. Para una construcción eficiente del ciclón se tienen en cuenta la velocidad del gas que entra al ciclón. De acuerdo a los trabajos de Mujumdar [28] el rango de velocidad es de 15 - 30 m/s para asegurar una correcta eliminación de las partículas. Se calcularon los parámetros para la construcción del ciclón dando valores de velocidad similares a la curva de Mujumdar, lo que indica una buena eficiencia de separación del particulado. Las características del ciclón construido se detallan en la Tabla 2.
Tabla 2 Dimensiones del ciclón y colector de partículas.
Dimensiones Valor | |
---|---|
Velocidad de entrada del gas [m/s] | 21,5 - 31,1 |
Diámetro del ciclón [mm] | 85 |
Diámetros de salida del gas [mm] | 24 |
Altura del cuerpo del ciclón [mm] | 80 |
Altura total del ciclón [mm] | 260 |
Diámetro de salida de sólidos [mm] | 22 |
Volumen colector de partículas [L] | 1 |
Eficiencia del ciclón [%] | 90 |
El filtro de partículas es una unidad de operación que permite retener los sólidos que no fueron separados por el ciclón. Es un filtro cilíndrico de diseño radial compuesto por un vaso en malla (tamiz #14) recubierto con fibra de vidrio. Las dimensiones del filtro son 15 cm de altura y 10 cm de diámetro. Se encuentra calefaccionado por una resistencia de 1000 w y 220 v; que lo mantiene a 350 °C. Además, posee un control automático de temperatura y aislado por una camisa de fibra de vidrio y una cubierta de acero inoxidable para evitar que se condensen allí los alquitranes.
Unidad de acondicionamiento de gases
La unidad de enfriamiento y lavado de gases se emplea para enfriar la corriente gaseosa evitando simultáneamente la condensación de los alquitranes que no fueron eliminados aguas arriba [5]. Está conformada por una torre de lavado de gases con recirculación de agua y un reservorio, construidos en acero inoxidable. La torre de lavado es una columna a contracorriente, el agua ingresa por la parte superior a un distribuidor tipo ducha mientras que los gases ingresan por la parte inferior lateral. La capacidad de la torre es de aproximadamente 1 L y las dimensiones se determinaron asumiendo una relación de ~20 entre la altura y el diámetro de la torre (L/D: 90 cm / 4 cm), para asegurar el contacto entre el gas y el agua. El reservorio se construyó con una capacidad de aproximadamente 6,5 L de los cuales se deja un volumen libre del 30 %. Entre la torre de lavado y el reservorio se tiene una bomba periférica marca Lusqtoff elevadora de agua, la cual bombea ~2 L/min de manera continua en el sistema cerrado, hasta que la temperatura del agua recirculada es ~50 °C, momento en el que se realiza el cambio de agua. Los gases son dirigidos al medidor volumétrico de salida, modelo G6K con una capacidad máxima de 10 m3 / h.
Acondicionamiento de biomasa y catalizadores
La biomasa sometida a gasificación fue el aserrín de pino previamente tamizado entre 0,50 - 0,85 mm y secado a 120 °C por 48 h. El catalizador de residuo de pirólisis (RP) fue provisto por la empresa WENTEN S.R.L. Este residuo carbonoso (char) fue obtenido al someter una mezcla de materiales como el polietileno, poliestireno, aceite de moto, caucho, entre otros, a una pirólisis a 550 °C por 32 h. El catalizador de dolomita (Dol) fue provisto por José Luis Calvo -Explotación Minera. Previo a su uso, fue calcinada en aire a 700 °C por 24 h. Los catalizadores y material inerte (arena) usados en el reactor lecho fluidizado requieren una distribución de tamaño de partículas de 0,25 - 0,50 mm.
Caracterización de biomasa y catalizadores
La caracterización de la biomasa involucra conocer los siguientes parámetros: Análisis último o elemental: es el que reporta el porcentaje de peso del oxígeno (O), carbono (C), hidrógeno (H), azufre (S) y nitrógeno (N) y análisis próximo: es aquel que determina el contenido de carbono fijo, material volátil y cenizas (de acuerdo a norma ASTM). Mediante la técnica de análisis elemental (CHONS) se determinó la composición del aserrín de pino, en un equipo CHN628 series and Sulfur Add-On Module and TruSpec Micro Oxygen Add-On Module Elemental Determinators, marca: LECO ®. Para determinar su comportamiento térmico con flujo oxidante se realizó el análisis de termogravimetría (TGA) en un equipo Mettler Toledo STARe con módulo TGA/SDTA851.
Se utilizaron las técnicas de ICP y BET para caracterizar los catalizadores RP y Dol. La técnica espectroscopia acoplada a plasma inductivo (ICP-OES) en un equipo Perkin Elmer OPTIMA 2120 fue utilizada para determinar el contenido metálico y la técnica de fisisorción de N2 en un Micromeritics ASAP 2020 [29] para conocer sus parámetros texturales como la superficie específica expuesta.
Procesamiento de las muestras gaseosas, líquidas y sólidas
Para el análisis cromatográfico de las muestras gaseosas se utilizó la técnica de adsorción en fase sólida (SPA), la cual adsorbe los alquitranes de la muestra gaseosa en una fase estacionaria sólida. Las muestras gaseosas se toman manualmente con una jeringa que tiene acoplado un cartucho con 350 mg del adsorbente (Bondelsil NH2, marca: Agilent Technologies) en el cual quedan adsorbidos los alquitranes [30]. Para evitar pérdidas por la volatización de alquitranes livianos, el cartucho se refrigera hasta el momento de la elución (se recomienda realizarla dentro de las 24 h posteriores) [31,32]. Por otro lado, los gases no condensables que pasaron a través del cartucho SPA son analizados en un GC-TCD Shimadzu 2014 con columna empacada marca Carbosphere y N2 como gas carrier. Los datos obtenidos permitieron determinar la composición de gas, relación H2:CO y poder calorífico inferior (LHV) a través de las siguientes ecuaciones:
Donde:
Ni: Flujo molar i en el producto gaseoso (mol/h).
Nt: Flujo molar total de gases generados (mol/h).
Donde:
LHV: poder calorífico inferior (MJ/Nm3: kJ/L).
Xi: Fracción molar i en el producto gaseoso.
LHVi: poder calorífico inferior (MJ/Nm3): LHVH2:11,2;
LHVco:13,1; LHVCH4:37,1; LHVCO2:0; LHVn2:0.
Para el análisis de la composición de los alquitranes de la corriente gaseosa se emplea la técnica de extracción en fase solida (SPE); es un método común para la extracción de compuestos adsorbidos que se separan en función de sus propiedades químicas y físicas [32]. Como esta reportado en la literatura, la elución de los alquitranes se realizó en 2 etapas: una elución aromática y una fenólica. Antes de la elución se agregan directamente al cartucho 200 µL de un estándar interno (hexadecano: 750 ppm) y un estándar interno fenólico (4-etoxifenol: 750 ppm), los cuales se disuelven en los solventes de elución. Para eluir la fracción aromática, primero se agregan 2 mL de diclorometano (DCM) y luego para la fracción fenólica, 2 mL de una solución (1:1) DCM e isopropanol (IPA). Las 2 muestras liquidas, son analizadas en un GC-FID Shimadzu 2014 con columna capilar HP INNOWax de Polietilenglicol. Para determinar los tiempos de retención de los compuestos de alquitrán por familia se realizó el análisis con cromatografía de gases acoplada a un detector de masas con un equipo Thermo Scientific ISQ-Trace 1300. Durante la gasificación de biomasa también se generan productos sólidos como el char y las cenizas, los cuales quedan depositados en el fondo del gasificador de lecho fluidizado (colector de cenizas), mezclados con el material fluidizante y/o en los sistemas de retención de solidos conformado por el ciclón y el filtro de partículas. Dada la necesidad de cuantificar y discriminar las cenizas del char, se realiza un tratamiento termogravimétrico; el cual consiste en pesar los residuos sólidos del fondo (Rf), del ciclón (Rc) y del filtro de partículas (Rfp); seguido de un tratamiento térmico a 700 °C por 24 h. Se asume que la pérdida de masa durante el tratamiento térmico corresponde al char mientras que la masa que se mantiene corresponde el material fluidizante y las cenizas generadas durante la gasificación.
Resultados
Sistema de gasificación construido
En la Figura 1 se observa el esquema del sistema de gasificación a escala banco construido. Está compuesto por la unidad de alimentación de la biomasa (1 y 2) y de los agentes gasificantes (4, 5 y 6), pasando por el reactor de gasificación de lecho fluidizado autotérmico (7), seguido del acondicionamiento de gases, retención de partículas (9 y 10) y el acondicionamiento de gases con recirculación (11) y Analmente, la medida volumétrica del gas generado (12).
En la Figura 2 se muestra el diagrama de flujo con cada uno de los pasos que conforman una prueba de gasificación, incluyendo las etapas previas y posteriores. La prueba inicia con el encendido del equipo a través de una llama generada con una mezcla de aire y gas propano. Cuando T1 y T2 llegan a ~350 °C se inicia la alimentación del aserrín de pino. La selección de esta temperatura fue determinada con el análisis de TGA y la temperatura de autoignición [33]. Con el ingreso de biomasa se corta el suministro de propano y se ajusta el flujo del agente gasificante (aire o mezcla aire y vapor de agua) para llevar a cabo la prueba de manera autotérmica. El análisis de las muestras se realizó cada 60 min con el objetivo de observar los resultados de contenido de alquitranes, composición de gases, relación H2:CO y el poder calorífico (LHV).
Optimización del sistema de gasificación
Alimentación de biomasa y agentes gasificantes
Las pruebas de alimentación de la biomasa se realizaron con el propósito de llegar a una operación continua, estable y autotérmica. Para obtener una alimentación continua se probaron tres tamaños de partícula de aserrín de pino: (1) >1,4 mm, (2) 0,85 - 1,4 mm y (3) 0,50 - 0,85 mm (Figura 3). La prueba fue realizada en frio (sin gasificación) con el tornillo de transporte en su capacidad máxima de 30 rpm. Los resultados mostraron un flujo discontinuo de aserrín con los mayores tamaños de partícula (1) y (2); este comportamiento podría estar relacionado con la heterogeneidad de los tamaños de partículas. En cambio, el tamaño de partícula (3) 0,50 - 0,85 mm mostró un flujo continuo de alimentación debido a su menor y homogéneo tamaño, lo cual mejora la distribución en el tornillo de alimentación. Por lo anterior, se determinó que el tamaño adecuado de aserrín de pino para la alimentación durante las pruebas de gasificación es 0,50 - 0,85 mm. Para determinar el flujo másico optimó de alimentación de aserrín de pino se realizaron ensayos con diferentes valores: 0,240, 0,420, 0,840 y 1,680 kg/h de biomasa con el tamaño de partícula (3). En la Figura 4 se observan los perfiles de temperatura versus el tiempo de gasificación, para cada uno de los flujos de alimentación. Estas graficas muestran los valores de temperatura T1 a T5, con un flujo de agente gasificante correspondiente a una relación equivalente de 0,35; este valor de ER es sugerido en varios reportes bibliográficos como óptimo para los procesos de gasificación [24,25]. Los perfiles de temperatura inician en ~40 min, debido a que durante este tiempo ocurre el encendido del gasificador. En la Figura 4 se observa para la alimentación de aserrín de 0,240 kg/h un perfil inestable en T1 y T2 que corresponden a los primeros 50 cm del reactor, lo que puede deberse al bajo flujo de alimentación, ocasionando que la temperatura sea fluctuante y no alcance la temperatura de equilibrio, además T4 y T5 que corresponden a los 50 cm superiores del reactor están por debajo de 300 °C lo que puede generar la condensación del alquitrán en la parte superior y traer consigo problemas operativos.
Para el flujo de alimentación de 0,420 kg/h, se observa un perfil de temperatura más estable, con temperaturas por encima de los 300 °C a lo largo del reactor, con T1 y T2 temperaturas en equilibrio entre 550 - 650 °C, esto nos indica que este es el valor de flujo de alimentación mínimo para el reactor estudiado. Por otro lado, los perfiles de temperatura con alimentación de 0,840 y 1,680 kg/h evidenciaron temperaturas >400 °C a lo largo del reactor. Para ambas pruebas T1 y T2 es de ~ 650 °C, esta temperatura de equilibrio es alcanzada a ~65 min y se mantiene durante toda la gasificación (~180 min).
Para los flujos másicos evaluados, el de 0,840 kg/h es tomado como óptimo; debido a que permite una operación de manera continua, más estable y autotérmica. Teniendo en cuenta que el sistema de gasificación tiene una capacidad mínima y máxima de alimentación de 0,420 y 1,680 kg/h, respectivamente. Con el flujo másico de alimentación de biomasa óptimo, se determinó el flujo volumétrico óptimo del agente gasificante. Se trabajó con aire (AG) y una mezcla de aire con vapor de agua. Se realizaron 4 pruebas de gasificación con el mismo flujo de alimentación de aserrín de pino (0,840 kg/h), variando el flujo de aire entre 18 - 40 L/min que equivale a una relación equivalente (ER) de 0,25 - 0,55. La Figura 5, muestra que para ER:0,25 las temperaturas (T1-T5) se mantienen entre (300 - 550 °C), por los bajos flujos de aire (ER bajo), favoreciendo los procesos de pirólisis generando una mayor cantidad de alquitranes. Además, se observa que las temperaturas T4 y T5 son bajas, lo que podría traer problemas operativos. Para un ER: 0,55 se observa que las temperaturas (T1-T5) se mantienen entre (650 - 950 °C), este alto flujo de aire favorece los procesos de combustión, aumentando el rendimiento a gases con mayor formación de CO2 y compuestos contaminantes como NOx, entre otros [34,35]. Las altas temperaturas (> 850 °C) traen problemas operativos como el desgaste de los materiales, afectando la durabilidad y estabilidad del reactor de gasificación.

Figura 5 Perfiles de temperatura variando el ER (flujo de alimentación: 0,840 kg/h y 400 g de arena).
Por el contrario, con un ER de 0,35 y 0,45 las temperaturas (T1-T5) se mantienen entre 400 - 650 y 500 - 750 °C, respectivamente. Estas temperaturas favorecen la operatividad del equipo evitando la condensación del alquitrán en el reactor y beneficiando térmicamente las reacciones que ocurren durante la gasificación como el craqueo, reformado, etc., obteniendo una corriente gaseosa compuesta por los gases de interés H2, CO y CH4. A partir de estos resultados, se eligen los ER de 0,35 y 0,45 como óptimos a estudiar con temperaturas de gasificación de ~650 y 750 °C, respectivamente.
Para evaluar el efecto del vapor de agua y seleccionar el flujo óptimo, se realizaron 4 pruebas en el gasificador con un flujo de alimentación de aserrín de pino (0,840 kg/h) y un flujo de aire correspondiente a un ER: 0,45. Esta relación presenta la mayor temperatura de equilibrio (750 °C) esperando que, con el ingreso de vapor de agua al reactor, la temperatura de equilibrio Anal esté por encima de 600 °C. Esta caída de la temperatura es ocasionada por el proceso endotérmico del aporte de vapor de agua en el sistema autotérmico estudiado. Los flujos de agua que ingresan al vaporizador son 0, 6, 12 y 18 mL/min; equivalentes a un GR:0,9, valor óptimo según los reportes bibliográficos [4,26].
En la Figura 6, se observan los perfiles de temperatura con los diferentes flujos volumétricos de agua en función del tiempo. El perfil de temperatura sin vapor de agua muestra que T1 a T5 se mantienen entre 500 - 750 °C. Por el contrario, el perfil con mayor aporte de agua (20 mL/min) muestra un descenso en las temperaturas a ~60 min, alcanzando T1-T5 entre 350 - 550 °C; desfavoreciendo las reacciones de gasificación. Para los flujos intermedios de 6 y 12 mL/min, los perfiles muestran un comportamiento similar de T1 a T5 de 500 - 650 °C, siendo la temperatura de equilibrio promedio en T1 y T2 de ~650 °C. Por la similitud en los perfiles y condiciones operativas, se eligió el mayor de los dos, 12 mL/min, el cual podría favorecer en mayor medida reacciones de reformado con vapor durante la gasificación [34]. En este sentido, se determinó como valor optimó 12 mL/min correspondiente a 0,0005 kg/min de vapor de agua (200 °C) y un GR:0,9.
Caracterización de biomasa y catalizadores
En la Tabla 3, se presentan algunas características del aserrín de pino usado como alimentación. Los resultados del análisis próximo, último y poder calorífico superior e inferior son muy similares a los reportados en la literatura para este tipo de residuo biomásico [36 - 38]. Estos valores se emplearon para comprender la naturaleza de la biomasa, establecer pautas en el proceso de gasificación y para realizar los balances de materia de las pruebas. En la Figura 7 se muestran las curvas TGA y DTG (rampa de temperatura de 10 °C/min de 30 a 900 °C) del aserrín de pino en aire. Se observa una primera región que va desde 30 °C hasta 150 °C, la cual corresponde a la etapa de secado en la que ocurre la desorción de humedad y fusión de la cera. Seguido, hay dos regiones de descomposición; una correspondiente a la hemicelulosa, celulosa y lignina que esta entre 200 - 400 °C y que en la curva DTG corresponde al segundo pico el cual tiene su máximo valor ~330 °C. La segunda región corresponde a la descomposición del char que se degrada entre 400 - 550 °C con un máximo en ~500 °C [39,40]. Este análisis nos permite determinar que, durante la gasificación, la temperatura de autoignición del aserrín y donde comienza a descomponerse es de ~ 330 °C, lo cual es determinante para el sistema de encendido del reactor autotérmico a escala banco.
Tabla 3 Caracterización del aserrín de Pino Elliotis. Análisis próximo, elemental y poder calorífico.
En la Tabla 4, se presenta el contenido metálico y las propiedades texturales de los 2 catalizadores evaluados. En el caso del ICP, para Dol se observa que los resultados concuerdan con la naturaleza química del mineral, con componentes principales el CaCO3, MgCO3, MgO y CaO. Para el catalizador RP se observa gran variedad de elementos, debido a la heterogeneidad de la materia prima pirólizada en su composición. RP contiene mayoritariamente Si, Ca, Fe, Zn y en menor cantidad otros elementos como Cu, Ni, Mo. La presencia de estos elementos concuerda con algunos estudios sobre char/ biochar obtenidos de procesos como la pirólisis [22,41]. Los elementos presentes componen fases activas que podrían tener un buen carácter catalítico favoreciendo algunas reacciones [29]. Los catalizadores RP y Dol presentan bajas áreas BET (< 5,7 m2/g) con tamaños de poro muy bajos. Lo anterior, concuerda con lo reportado en la literatura [42].
Tabla 4 Resultados ICP y parámetros texturales de los catalizadores [29].
Pruebas de gasificación catalítica
Las pruebas de gasificación se realizaron con las condiciones óptimas previamente determinadas; se empleó un flujo másico de aserrín de pino de 0,840 kg/h, usando 400 g de material inerte o catalizador en el lecho fluidizado (RP o Dol), lo que corresponde a una relación Catalizador/Biomasa (C/B): 0,16. Los parámetros estudiados fueron la relación equivalente (ER) de 0,35 - 0,45 y la relación agua+aire/biomasa (GR) de 0 y 0,9; para dos temperaturas 650 y 750 °C. En la Figura 8 se observan los resultados de contenidos de alquitrán y el porcentaje de los compuestos clasificados por familia. En esta clasificación los compuestos de referencia: tolueno, fenol y naftaleno, se agruparon con su respectiva familia química. Los resultados muestran contenidos de alquitrán de 60, 40 y 30 g/ Nm3 para el material inerte con ER: 0,35, 0. 45 y 0,45 con aporte de vapor de agua (GR: 0,9), respectivamente. Comparado con la arena, la eficiencia de remoción del alquitrán para los catalizadores fue de 10 - 28 °% para la condición 1, de 15 - 28 °% para la 2 y de 40 - 45 °% para la 3. Presentando los mayores porcentajes de remoción de alquitrán con Dol en comparación con RP en las pruebas evaluadas.
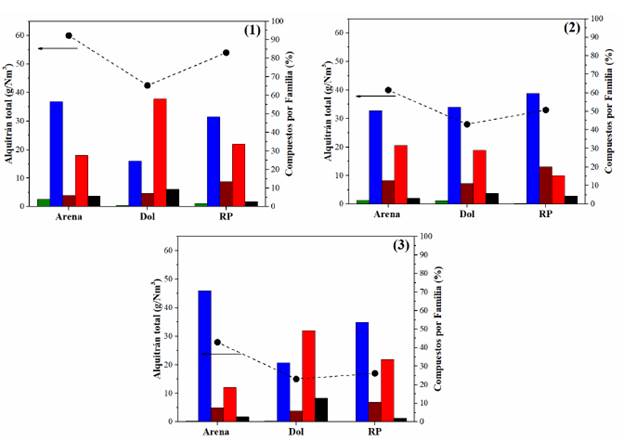
Figura 8 Alquitrán total (●) y Composición por familia (%) ■ alifáticos, ■ aromáticos de 1 anillo, ■ aromáticos de 2 anillos, ■ fenólicos y ■ otros. (1) ER: 0,35, (2) ER: 0,45, (3) ER: 0,45 y GR: 0,9.
Lo anterior, se puede atribuir a las propiedades encontradas en los catalizadores (Tabla 4). Mostrando que Dol tiene en mayor proporción compuestos como el CaCO3 y MgO que favorecen el craqueo catalítico por su característica básica, mientras que en RP la presencia de Fe, Zn, SO2, CaO, C y otros, permiten el craqueo de las moléculas y además el reformado de compuestos de alquitrán, pero su actividad catalítica es menor comparada con Dol, lo que puede atribuirse a que los elementos observados en RP están en menor proporción.
En las pruebas se evidencia una disminución en el contenido de alquitrán al aumentar el ER (condición 2), esto puede atribuirse a la mayor temperatura (~750 °C) en el sistema comparado con el menor ER; tal como se observó en la Figura 5, esta temperatura puede favorecer termodinámicamente reacciones como craqueo, reducción, entre otras; disminuyendo el contenido de alquitrán en el sistema autotérmico. Por otro lado, el mayor porcentaje de eliminación de alquitrán para los catalizadores se evidenció en la condición 3; este efecto está relacionado con el mayor ER y el aporte de vapor de agua en la gasificación catalítica, mostrando que el agua contribuye a la disminución del contenido del alquitrán en un 50 °%, en comparación con el blanco y las demás condiciones. Como se mencionó anteriormente, el vapor de agua favorece las reacciones de reformado de alquitrán + nH2O → (n + m/2)H2 +nCO]. La distribución de alquitranes por familias de compuestos, muestra que predominan los aromáticos de 1 anillo, en las pruebas con el material inerte para las condiciones evaluadas. Con los catalizadores y bajo condición 1, se ve el efecto en la disminución de los compuestos aromáticos de 1 anillo, pero un mayor porcentaje de fenólicos. Un comportamiento similar se evidencia en la condición 3, donde el vapor de agua disminuye los compuestos aromáticos de 1 anillo y aumentan los fenólicos, aromáticos de 2 anillos y otros. Por último, para la condición 2 se favorece la eliminación de compuestos fenólicos y aromáticos de 2 anillos, mientras aumentan los compuestos de 1 anillo. Los resultados anteriores concuerdan con la tendencia decreciente en el contenido total de alquitranes en las condiciones evaluadas.
En la Figura 9 se observan los resultados de composición de los gases y poder calorífico LHV. La composición del gas es principalmente CO, CH4, CO2 y no se detectaron óxidos de nitrógeno, ni hidrocarburos livianos (etano, propano, etc). El uso de los catalizadores en todas las condiciones evaluadas genera un aumento en el porcentaje de H2 y una disminución en el CO y CO2, en comparación con el inerte. En cuanto a la relación H2:CO, ambos catalizadores presentan valores de ≈ 0,38 a 0,45. Mientras que el inerte tiene valores de relación H2:CO < 0,22 en las 3 condiciones estudiadas. Se observa que los catalizadores aumentan en un 50 % la relación H2:CO en comparación con el inerte.

Figura 9 Composición de gases (%) ■H2, ■CO, ■CH4, ■CO2 y ■ LHV (kJ/L). (1) ER: 0,35, (2) ER: 0,45, (3) ER: 0,45 y GR: 0,9.
Se destaca que, RP presenta los mayores valores de poder calorífico (LHV), debido a los mayores porcentajes de H2 y menores de CO2; estos resultados pueden estar atribuidos a las características del catalizador RP (Tabla 4) que favorecen su propia gasificación por su naturaleza a base de carbono (C + H2O → H2 + CO) y reacciones de reformado del alquitrán. Mientras que Dol presenta los menores porcentajes de CO, ocasionando menores poderes caloríficos. Es importante destacar que los valores del poder calorífico son bajos (LHV < 3 kJ/L), dado que el gas generado está compuesto mayoritariamente por N2 (~68 °% y CO2 (~14 %), los cuales no contribuyen al poder calorífico. lo anterior debido a que el principal agente gasificante usado fue aire lo que genera un gas pobre. No obstante, los resultados muestran un gas susceptible a mejoras a través de la variación en las condiciones de gasificación catalítica, tales como: uso de diferentes agentes gasificantes, tratamientos como reformado catalítico aguas abajo de la gasificación, entre otros.
Conclusiones
Se construyó y optimizó un sistema de gasificación catalítica a escala banco con diferentes unidades, teniendo como principal el reactor de lecho fluidizado y autotérmico. Para este sistema se establecieron valores óptimos de flujo másico de alimentación de aserrín de pino de 0,840 kg/h, flujos volumétricos de agentes gasificante con aire equivalentes a ER: 0,35, 0,45 y con mezcla de aire con vapor de agua correspondiente a un GR: 0,9. Los perfiles de temperaturas mostraron condiciones óptimas a 650 y 750 °C para las pruebas de gasificación autotérmica. Se estableció el protocolo de gasificación, desde el encendido del equipo hasta la obtención del gas generado a través del proceso. Entendiendo que los puntos críticos del sistema están en la unidad de alimentación de la biomasa (tolva y tornillo de transporte) y el reactor de gasificación; lo anterior por la exigencia de continuidad y constancia en la alimentación de la biomasa, debido a la condición autotérmica y de lecho fluidizado del reactor. Se concluye que hay un efecto positivo en el proceso de gasificación con los catalizadores estudiados con y sin vapor de agua comparado con el material inerte (arena). Se observaron contenidos de alquitrán menores entre 10 - 45 °% siendo los mejores cuando el agente gasificante es la mezcla aire más vapor de agua y alcanzado relaciones H2:CO de 0,45. En cuanto al poder calorífico inferior se obtuvieron valores de 3kJ/L, sin desconocer que la calidad del gas generado es pobre, por lo que es susceptible a mejoras a través de la variación en las condiciones de gasificación como el uso de catalizadores aguas abajo del gasificador (reformador catalítico) y el uso de aire enriquecido con oxígeno como agente gasificante. El sistema de gasificación catalítica a escala banco y autotérmico construido permitió gasificar residuos biomásicos, empleando catalizadores como dolomita y residuo de pirólisis promisorios para usar en estos procesos, teniendo en cuenta que ambos son de bajo costo y no requieren una modificación para su uso por tratarse de un mineral natural y un residuo de otro proceso, evidenciando la viabilidad de este tipo de tecnologías para disminuir residuos biomásicos e industriales y generar gases con posibles usos energéticos