1. Introducción
La minería es un renglón de vital importancia para el desarrollo económico de cualquier país y fuente de riquezas que contribuye a la sustentabilidad de la comunidad. Su desarrollo generalmente se caracteriza por el movimiento de considerables volúmenes de materiales, por lo que se requiere de equipos preparados para operar de forma continua durante toda su vida útil, capaces de realizar este trabajo. Para cumplir con la producción planificada, estas máquinas con frecuencia son expuestas a condiciones severas causadas por grandes esfuerzos y jornadas continuas, que con el transcurso del tiempo ocasionan desgastes prematuros en algunos de sus componentes.
Los desperfectos técnicos y los altos costos operativos son las principales causas por las cuales se decide retirar el equipamiento minero. La primera, relacionada con la destrucción física del equipo, provoca dificultades para llevar a cabo los trabajos de forma óptima para los cuales fueron adquiridas. Los altos costos operativos comprometen la competitividad del equipo, con el tiempo se produce una degradación del rendimiento económico por necesidad de mantenimiento excesivo y aumento del consumo de energía, llamándose a esto envejecimiento, el cual se evidencia cuando es preciso gastar cada vez más, obteniendo cada vez menos disponibilidad y productividad. Por otra parte la obsolescencia por la evolución del contexto socioeconómico y especialmente el progreso tecnológico en el cual se desarrollan las actividades de la empresa también ejercen una influencia negativa [4].
A medida en que envejecen los equipos se hacen más frecuentes las fallas por diversas causas que generan paros, por lo que deben ser sometidos al mantenimiento correctivo, de esta manera, a los costos estimados de operación se le adicionan los costos por concepto de corrección de averías. Aunque la misión del mantenimiento es la de conservar los equipos en la mejor forma posible, muchas fuerzas se oponen a este empeño, de modo que tarde o temprano el equipo pierde por completo las condiciones técnicas que lo habilitan para prestar determinado servicio [12].
El mantenimiento es una de las principales partidas que se consideran en el presupuesto de cualquier proyecto minero a gran escala en el que se utilice transporte automotor y arranque mecánico. Su planificación es cuidadosamente elaborada partiendo del análisis de criterios técnicos y económicos que permiten establecer plazos y procedimientos capaces de asegurar rentabilidad y seguridad en el proceso extractivo.
El mantenimiento preventivo ofrece una disminución de paradas no programadas, mejor conservación de los equipos, menores costos de mantenimiento comparado con el mantenimiento correctivo, generación de información de programación y buena relación entre producción y mantenimiento. Por otra parte, el mantenimiento predictivo al evitar paradas por roturas, mejora considerablemente la disponibilidad de los equipos. Un servicio de mantenimiento, para que sea óptimo, debe ser una combinación del mantenimiento preventivo y predictivo, pero esta mezcla debe ser tal, que cada componente del activo sea sometido a las prácticas justas que hagan posible su disponibilidad en tiempo y forma en el proceso productivo [9].
Según estudios preliminares, los problemas operacionales del equipamiento provocan un incremento del costo total del mantenimiento en la en la minería, estos problemas traen consigo un deterioro precoz del equipamiento, afectando su disponibilidad e imposibilitándolo para realizar la operación para la cual fue destinado.
El problema que fundamenta este estudio es la necesidad de establecer la relación entre la productividad, el mantenimiento y el reemplazo del equipamiento minero en la minería a gran escala, que permita trazar estrategias para la adquisición de maquinaria en el tiempo preciso, evitando reducciones de productividad e incrementos de costos operativos.
2. Materiales y métodos
2.1. Descripción del flujo tecnológico de la unidad básica minera
La unidad básica minera trabaja para suministrar la materia prima a la planta de preparación de minerales bajo los criterios técnicos y económicos que rigen la ley de corte, garantizando la rentabilidad del proceso extractivo. La planta de tratamiento de minerales proporciona un material preparado mecánicamente a la planta metalúrgica, que cuenta con un esquema tecnológico basado en la lixiviación carbonato amoniacal del mineral reducido o proceso Caron. Para dar cumplimiento a su objeto social, la unidad básica minera desarrolla las actividades que se relacionan a continuación:
Desarrollo geológico.
-
Preparación minera.
El Desbroce, se ejecuta con buldóceres marca KOMATSU D85ex. Durante esta operación es retirada la capa vegetal con la finalidad de realizar posteriormente el destape. En la actualidad se hace énfasis en la sostenibilidad de la minería, la conservación de la capa vegetal durante su almacenamiento permitirá ejecutar los planes de cierre adecuados, que permitan al final de la minería reestablecer la flora autóctona, partiendo de la reposición de la capa vegetal que cuenta con los nutrientes necesarios para lograr un elevado índice de supervivencia de las especies plantadas.
En el Destape, actualmente los equipos más usados son las retroexcavadoras hidráulicas R974, R984, EC-460, dragalinas andantes ESH5/45, camiones articulados VOLVO A40D y A40E.
En la construcción de los caminos mineros y drenajes, se utilizan principalmente:
-
Extracción y Transporte del mineral.
Actualmente esta operación se lleva a cabo con dragalinas andantes modelo ESH 5/45, con un alcance de 36,7 m y una profundidad de corte máxima de 22 m, óptimas en relación a las condiciones de potencia de los yacimientos en explotación, pero contraproducentes debido a la complejidad del cuerpo mineral por su baja capacidad de selectividad, lo que conduce a desventajosas pérdidas y empobrecimiento de la mena. La introducción de retroexcavadoras hidráulicas marca VOLVO, DOOSAN y LIEBHERR, ha permitido la extracción en zonas donde existen intercalaciones de gabros o bloques flotantes y en áreas con condiciones hidrogeológicas difíciles. El mineral se transporta hasta la planta de recepción de minerales o hasta depósitos intermedios con camiones articulados VOLVO A-40D, VOLVO A40E y camiones rígidos TEREX TR-60.
Protección al medio ambiente.
2.2. Equipamiento minero en explotación en la unidad básica minera
Para desarrollar el proceso de explotación de yacimientos en condiciones de rentabilidad y seguridad, la unidad básica minera cuenta con un parque de máquinas agrupado por tipo de equipos, mostrando además el estado técnico por línea y modelo (Tablas 1, 2 y 3).
2.3. Productividad de los equipos mineros
La productividad de los equipos mineros está catalogada como un parámetro de máxima importancia en la explotación de yacimientos minerales, pues marca la posibilidad del cumplimiento de los planes de producción planificados cuidadosamente a partir del análisis de criterios técnicos y económicos. Dentro del proceso productivo se pueden encontrar pérdidas que influyen de manera significativa en el desempeño de la maquinaria, muchas de ellas han pasado a formar parte de la rutina de explotación por lo que su detección constituye una tarea difícil que adquiere más complejidad conforme aumenta el número de equipos que componen el parque.
La correcta planificación y ejecución del mantenimiento es una herramienta de efectividad comprobada para reducir estas pérdidas, su control y monitoreo posibilitan evaluar su impacto a través del comportamiento de indicadores prestablecidos que permitirán determinar si se ha optimizado el desempeño de la maquinaria o caso contrario, se han incrementado los costos operativos sin obtener un aumento proporcional de la productividad.
Se definen como pérdidas del proceso productivo a todas las actividades que no agregan valor, pero que consumen tiempo, recursos y espacio, generando costos en el proceso de producción [2].
La disponibilidad técnica es una de las principales causas del descenso de la productividad en equipos mineros, su efecto se traduce en la reducción de los volúmenes que han dejado de moverse y en el incremento del costo operativo por concepto de mantenimientos correctivos. Para atenuar el efecto de este problema se hace necesario atacarlo partiendo del análisis de sus principales componentes: las pérdidas de materiales y energía y las pérdidas por el rendimiento del equipamiento utilizado y de la mano de obra.
2.4. Situación del reemplazo
El reemplazo de los equipos juega un papel fundamental en cualquier empresa de producción, favoreciendo un aumento de la disponibilidad técnica y con esto un aumento de la productividad de explotación del parque de equipos, aparejado a esto también se logra disminuir los costos de producción al reducirse los costos por concepto de mantenimiento tanto preventivo planificado como correctivo.
En una primera instancia, para validar la decisión del reemplazo de los equipos mineros, se emplea la depreciación como uno de los criterios principales, que no es más que la reducción progresiva de su valor de adquisición durante el plazo de vida útil planteado.
Actualmente el equipamiento minero de arranque, carga y transporte en la mayoría de las empresas mineras se adquiere por dos vías: compra y arrendamiento. Los contratos de adquisición de los equipos incluyen servicios técnicos y de mantenimiento [6].
2.5. Parámetros claves del servicio de mantenimiento
En proyectos de gran minería a cielo abierto, el mantenimiento tiene un fuerte impacto en el cumplimiento de la capacidad productiva y se considera un elemento clave para alcanzar unas condiciones de rentabilidad y seguridad de la operación, garantizando la implementación de políticas ambientales acordes con las premisas del desarrollo sostenible. Es por tanto y desde todo punto de vista, una actividad que adquiere un papel preponderante en la viabilidad de un proyecto o de una empresa [8].
Una vez iniciado el proceso de mantenimiento, es necesario monitorear el progreso alcanzado a través de observaciones y comparaciones a lo largo del tiempo, de parámetros que definan claramente el nivel de calidad del desempeño organizacional, constatando sin subjetivismo, si se ha mejorado o no respecto a la situación inicial [3].
En referencia a la actividad de mantenimiento que tiene lugar en la gran minería, la necesidad de un procedimiento establecido bajo criterios concretos que validen los planes de trabajo es mucho más reconocida. Con la finalidad de evaluar el desempeño de la planificación del mantenimiento se han establecido los siguientes indicadores:
Índice de productividad total
Aprovechamiento de los equipos.
Disponibilidad técnica.
Rendimiento.
Efectividad neta de los equipos
2.5.1. Índice de productividad total de los equipos
El índice de productividad total de los equipos (T) (ec.1) es un parámetro muy útil para la planificación de las operaciones, ya que indica la productividad real y efectiva [1]. Se compone de los siguientes factores:
Aprovechamiento del equipo (A): medida de utilización del equipo, representa el porcentaje del tiempo que realmente se utiliza.
Efectividad global del equipo (G): Representa el estado de funcionamiento general del equipo. Se han considerado dos índices fundamentales para el caso de estudio: disponibilidad técnica y rendimiento, esto con la finalidad de ajustar la metodología a la maquinaria pesada de minería.
Para obtener la productividad real de los equipos se parte de la estimación del tiempo total en el que teóricamente estos deberían funcionar, estos tiempos se describen en la Fig. 1.
Tiempo calendario (Ñ): Es el tiempo total expresado en horas que el equipo puede trabajar. El valor máximo que puede tener este parámetro son 8760 horas, equivalente a los 365 días del año trabajando 24 horas al día. Es un parámetro teórico, ya que en condiciones normales aparecen afectaciones que disminuyen el tiempo efectivo de trabajo.
Tiempo no programado (TNP): Se mide en horas y está constituido por el tiempo que el equipo no debe trabajar según la planificación.
Tiempo de operación (TO): Es el número de horas efectivas en las que se espera que el equipo trabaje a plena capacidad. Excluye el tiempo por concepto de paradas programadas, ya sean por mantenimiento o tiempos improductivos vinculados a cuestiones intrínsecas del proceso de la maquinaria.
Paradas programadas (PP): Incluye el tiempo empleado para realizar acciones de mantenimientos periódicos y de rutina, paradas anuales y reparaciones importantes. En cada turno de trabajo como parte de las tareas cotidianas destinadas a la información de los operarios, es necesario suspender el equipo durante un corto periodo de tiempo, estas paradas deben ser consideras dentro de las programadas.
2.5.2. Aprovechamiento del equipo (A)
Los factores que se consideran para efectuar el cálculo de este parámetro [1] (ec. 2), son:
Donde:
D: Tiempo total de paradas programadas (h) (ec. 3).
2.5.3. Disponibilidad técnica
La disponibilidad técnica (S) (ec. 4) es una excelente medida de la capacidad de uso del equipo durante el tiempo programado. Representa el tiempo que se dispone de este para que funcione sin detenerse durante el tiempo esperado.
Otros parámetros relacionados con la disponibilidad son: tiempo efectivo de operación, averías y fallos de los equipos, ajustes a los programas de producción, fallos en la operación de los equipos y tiempo total por paradas no programadas.
Tiempo efectivo de operación (TO): es el número de horas del tiempo de operación del equipo que trabaja efectivamente (Fig. 2). Se obtiene restando del tiempo de operación, el tiempo que se pierde debido a paradas por averías internas, fallos en el proceso por factores externos y cambios en el programa de producción que implican parar para realizar modificaciones [1].
Averías y fallos de los equipos (V): Son el resultado de desperfectos técnicos que se producen en los equipos, no permitiéndoles ejecutar el trabajo en condiciones óptimas, inducen paradas prolongadas no programadas para corregir la falla. Sus principales inconvenientes son la pérdida de la productividad y los gastos por corrección de la avería. Tiene una influencia directa significativa en la disminución de la Efectividad Global del Equipo.
Ajustes a los programas de producción (d): Son pérdidas expresadas en tiempos que tienen lugar cuando la maquinaria se detiene o disminuye su ritmo de trabajo por ajustes en la planificación, por ejemplo cambios de frentes de minería, cambios de maquinaria tanto en planta como en el frente de minería.
Fallos en operación de los equipos (E): Se deben a problemas diferentes a los producidos por averías, pero que también detienen su funcionamiento. Estas paradas pueden tener su origen en las características del material que se procesa (humedad y granulometría) y otros fenómenos físicos que lo afectan como suciedad o atascamiento. Estos factores deterioran el funcionamiento del equipo y en numerosas oportunidades son el resultado de una mala operación. Esta clase de problemas se deben atacar de forma independiente a los producidos por fallos en del sistema mecánico [1].
Tiempo total por paradas no programadas (TT) (ec. 5): Se obtiene sumando el total del tiempo que ha estado detenido debido a las averías y fallos de operación delas máquinas auxiliares y ajustes de los programas de producción. Se mide desde que se detecta el fallo y se para el equipo hasta que queda apto para el trabajo y es puesto en operación con los parámetros de calidad y seguridad requeridos [1].
2.5.4. Rendimiento del equipo
El nivel de rendimiento del equipo (R) (ec. 6) permite evaluar el funcionamiento del equipo con base en los parámetros de diseño. En ocasiones se tiene una disponibilidad técnica elevada con eficiencia muy baja, en el caso de la maquinaria minera, esto puede estar provocado por fallas de fábrica que no permiten alcanzar los estándares normales de las líneas de equipos, así, permanece disponible por el tiempo previsto pero no opera a plena capacidad o presenta consumos y desgastes muy elevados.
Generalmente, y como parte de las especificaciones técnicas que ofrece el fabricante, es posible obtener un valor referencial del rendimiento, que al ser un valor teórico es muy difícil de alcanzar. Su empleo solo queda como valor de referencia para realizar estimaciones teóricas y valorar desempeños.
Representa el nivel de efectividad del proceso asumiendo que el equipo no tiene paradas programadas de ningún tipo. Se puede obtener dividiendo el nivel de producción real sobre el nivel de producción teórica, tomando el valor de diseño del equipo [1].
La determinación de las pérdidas de rendimiento se realiza considerando las siguientes pérdidas:
Pérdidas de producción normal (PPN): Se traducen en los tiempos que se pierden durante la puesta en marcha de los equipos, empieza desde la arrancada y culmina en el momento exacto en el que se alcanzan las productividades proyectadas bajo condiciones óptimas de seguridad y rentabilidad. Lo más relevante es la diferencia de productividad que tiene lugar por concepto de la disminución del ritmo de trabajo con el que se arranca.
Pérdidas de producción anormal (PPA): Son el resultado de la explotación del equipo a una capacidad inferior a la de diseño, que entre otras cosas, se relaciona con la fluctuación de velocidades. Esta pérdida se acrecienta en el caso del equipamiento de transporte, pues está sujeto a las condiciones de las pistas y las plataformas de trabajo donde se realiza la carga. La mala calidad de las primeras obliga al operador a reducir la velocidad constantemente para evitar saltos bruscos que afectan su comodidad. Las segundas, al ser zonas de elevado tráfico de máquinas pesadas, bajo ciertas condiciones relacionadas con las propiedades de los materiales que la componen y condiciones climatológicas, puede favorecer al atascamiento de estas unidades. En ambos casos es necesario contar con el apoyo de maquinaria auxiliar para solucionar tales situaciones.
Total de pérdidas de rendimiento y velocidad (TRV) (ec. 7): Se expresa en tiempo y se definen como la sumatoria de las pérdidas de producción normal y las pérdidas de producción anormal.
2.5.5. Efectividad global del equipo
2.5.6. Efectividad neta de los equipos (N)
La efectividad neta de los equipos (ec. 9) muestra claramente la verdadera efectividad y calidad del equipo mientras está en funcionamiento. Es una medida orientada a valorar la calidad técnica del equipo ya que no considera las paradas programadas y los tiempos de preparación, cambios de herramientas y ajustes [1].
Donde:
F: Relación de funcionamiento.
Para obtener la relación de funcionamiento (F) (ec. 10) debe ser calculado el tiempo de funcionamiento del equipo (TF) (ec. 11), que es el resultado de sustraerle al tiempo de operación las pérdidas de preparación y ajustes realizados (TPA). Representa el tiempo en que el equipo realiza las actividades mineras planificadas.
Se obtiene como resultado de la relación entre el tiempo de funcionamiento y el tiempo de operación. El resultado permite evaluar la capacidad del equipo para trabajar sin detenerse, permitiendo además valorar el efecto que causan las averías durante la explotación.
Esta es una medida de fiabilidad de los equipos.
Tiempo de funcionamiento:
3. Resultados
3.1. Afectación a la vida útil de los equipos
Según la experiencia en la minería del níquel cubana, la vida útil de los equipos puede tener un comportamiento diferente al estimado por los suministradores, lo que interfiere en los planes que se hacen cuando estos son adquiridos. Esto ocurre como resultado del daño prematuro que sufren los componentes de los sistemas de los equipos, dentro de las principales causas que lo provocan están:
Largos períodos de detención por deficiente presupuesto para la ejecución de los mantenimientos.
Problemas operacionales.
En la medida que pasan los años de explotación de los equipos, se produce una disminución en la productividad anual de estos como se expone la Fig. 3. Se muestra el comportamiento de este parámetro para el equipamiento de trasporte y de arranque - carga partiendo del análisis desde el primer año de explotación del equipamiento.
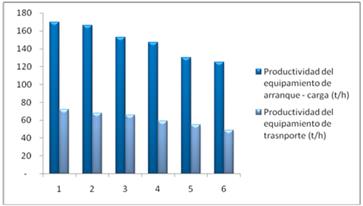
Fuente: elaboración propia
Figura 3 Comportamiento de la productividad del equipamiento de transporte y de arranque - carga durante su vida útil.
La afectación a la productividad en la mina no es el único problema que resulta del deterioro gradual de los equipos, también los costos operativos aumentan cada vez más debido a las reiteradas averías que estos van presentando. En la Fig. 4, se describe el comportamiento de la productividad y de los gastos de operación para los buldóceres en un tiempo medio de vida útil igual a 6 años. Estos se consideran usualmente como parte del equipamiento auxiliar, pero por su imprescindible actuación para la continuidad de la explotación en los yacimientos lateríticos, se ha considerado como equipamiento principal.
3.2. Situación del reemplazo
Para el desarrollo de las actividades extractivas en la minería cubana del níquel, se ha adquirido equipamiento por contratos de compra, por arrendamientos sin opción de compras (Leasing) y por contratos de servicios a empresas de movimiento de tierra, este último sin implicaciones directas en el incremento de los costos de mantenimiento debido a que el proveedor se encarga de garantizar las disponibilidad pactada en los contratos de servicio.
Con el paso del tiempo es inevitable el deterioro de los componentes del parque de máquinas de la mina, la disponibilidad técnica cae gradualmente debido al aumento delas interrupciones por averías, esto se muestra en la Fig. 5, donde se describen las horas anuales de averías del equipamiento de transporte, de arranque - carga y buldóceres.
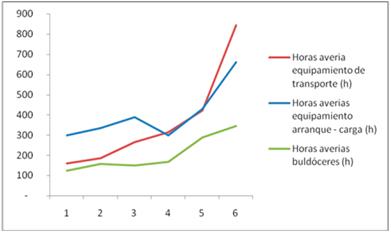
Fuente: elaboración propia
Figura 5 Comportamiento de las horas de averías del equipamiento de transporte, de arranque - carga y del parque de buldóceres durante su vida útil.
Los contratos de arrendamiento sin opción de compra se pactan con un tiempo de vigencia que puede variar entre 3 y 5 años dependiendo del comportamiento de los equipos durante su vida útil, en ocasiones este contrato puede extenderse un año más si los indicadores establecidos lo permiten. Después de vencido el plazo de vigencia del contrato se gestiona la reposición del arrendamiento valorando solo las cuestiones legales negociadas.
La determinación de la propuesta de equipos a adquirir debe corresponder con el objeto social de la entidad, e incluye la evaluación económica financiera, el costo de la inversión, el capital de trabajo, el costo de operación y la fuente de financiamiento.
3.3. Cálculo del índice de productividad total de los equipos
La Tabla 4 muestra los resultados del cálculo de cada uno de los parámetros claves del servicio de la mina, mientras que la Tabla 5 muestra los resultados del índice de productividad para el equipo de transporte, excavación-carga y buldóceres al 6to año de explotación.
Tabla 5 Resultados del cálculo del índice de productividad para el equipamiento de transporte, excavación - carga y buldóceres al 6to año de explotación.
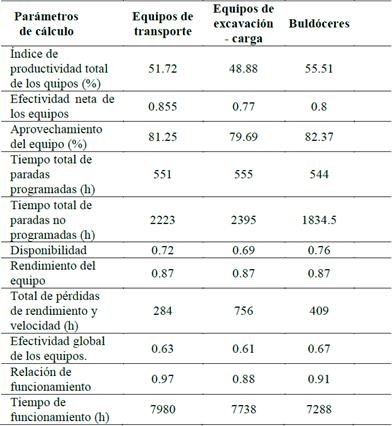
Fuente: elaboración propia
Al llegar al 5to año de operación, ya se presentan indicadores técnicos económicos desfavorables por problemas operacionales y deficiencias en el mantenimiento, lo que se traduce en unos costos operativos elevados y productividades insuficientes. En la Tabla 6 se muestra una comparación de estos indicadores que son los principales a tener en cuenta a la hora de evaluar el reemplazo de un equipo. Los resultados han sido expuestos de manera independiente para las máquinas de transporte, de arranque - carga y buldóceres, demostrando el significativo aumento de los costos de operación y la disminución de la eficiencia del equipamiento al acercarse el fin de su vida útil.
3. Conclusiones
El estudio de la productividad del equipamiento minero en la minería a gran escala es de vital importancia por el volumen de inversión que representa la maquinaria tanto como costo de inversión como costo operativo. Las principales pérdidas que influyen en la productividad de los equipos son las de rendimiento, de aprovechamiento y de utilización de los equipos de minería, relacionadas entre otras cosas, con la correcta ejecución de la planificación del mantenimiento y de la organización de las operaciones mineras.
La planificación y ejecución del mantenimiento ejerce gran influencia en la operatividad de los equipos conforme avanza los años de explotación, aunque este no puede garantizar valores de productividad y costos operativos óptimos a medida de estos envejecen, por lo que el estudio de su comportamiento junto al estudio del indicie de productividad total, es un buen indicador para la decisión de reemplazo.
Este estudio ha demostrado que el índice de productividad total del equipamiento minero cae entre el 44 % y el 51% al 6to año de explotación, lo que implica un empeoramiento de su régimen de trabajo al ser forzados a operar bajo condiciones extremas, poniendo de manifiesto la necesidad de adquirir maquinaria nueva por concepto de reemplazo o como complemento para alcanzar las productividades planificadas.