Serviços Personalizados
Journal
Artigo
Indicadores
-
Citado por SciELO
-
Acessos
Links relacionados
-
Citado por Google
-
Similares em SciELO
-
Similares em Google
Compartilhar
Ingeniería e Investigación
versão impressa ISSN 0120-5609
Ing. Investig. v.25 n.2 Bogotá maio/ago. 2005
Gabriel Camargo Vargas,1 Hugo Martín Galindo V.2
1 Ingeniero químico. M. Sc. Profesor Universidad de los Andes, Bogotá. e-mail: gcamargo@uniandes.edu.co
2 Ingeniero químico. M. Sc. Profesor Universidad Nacional de Colombia, Bogotá. e-mail: hmgalindov@unal.edu.co
RESUMEN
En este proyecto, primeramente se elaboraron soportes para membranas inorgánicas usando a Al2O3 como componente base y empleando como aglutinantes pseudoboehmita y silica coloidal, y como coadyuvante de sinterizado un oxido hidratado de magnesio; todas estas sustancias fueron sintetizadas mediante el empleo de procesos Sol Gel. También se analizó el efecto que sobre las propiedades físicas y mecánicas de los soportes ejercen la presión de compactación y la temperatura de sinterización. Los aglutinantes preparados se caracterizaron por sedigrafía de rayos X y los soportes elaborados se les midieron la resistencia a la compresión y porosidad y fueron caracterizados por microscopia electrónica de barrido (SEM) análisis EDX.
Palabras clave: sol gel, membranas, soportes, sinterización, a Al2O3.
ABSTRACT
This project investigated the effect of compacting pressure and sintering temperature on supports’ physical and mechanical properties. The supports were prepared by axial compacting of a Al2O3 powders using pseudoboehmita and silica gel as binder. Hydrated magnesium oxide was used as sintering helper. The prepared agglutinants were characterised by x-ray sedigraphy. The supports were synthesised by SEM and their compression strength and porosity were evaluated and characterised by EDX sweeping electron microscope (SEM). These binders and the helper were prepared by the sol-gel process.
Keywords: solgel, membrane, support, sintering, SEM.
Recibido: octubre 16 de 2004
Aceptado: junio 24 de 2005
Introducción
Las membranas empleadas en distintos procesos industriales, consisten casi siempre, de una delgada capa depositada sobre un sustrato cerámico (Ananthakumar y Warrier, 2001; Barrera, 2001; Belin y Briois, 2003; Bhave, 1991; Binner, 1990; Brinker, 1990). El interés de las investigaciones se centra, además de la obtención de las películas, en las técnicas que permitan obtener los sustratos cerámicos, con la distribución de tamaño de poro deseada, de manera confiable y reproducible.
La manufactura de membranas cerámicas ha experimentado un rápido crecimiento durante los últimos veinte años. El desarrollo de nuevos procesos y de nuevas aplicaciones ha provocado un aumento en el interés por el estudio de este tipo de membranas.
Aunque se dispone, con facilidad, de una extensa información relacionada con la manufactura de membranas micro y nanofiltrantes elaboradas con base en materiales cerámicos (Carberry, 1995, pag. 423-426; Chang y otros, 1994; Chaudhuri y otros, 2002; Conde y otros, 2003: Dilsiz y otros, 2002; Dima y otros, 2003, Dongare y otros, 2002; Duran y otros, 2002), la documentación existente para la fabricación de los soportes de dichas membranas es poco abundante. No son muchas las referencias bibliográficas que se encuentran sobre la elaboración de soportes para membranas y las que están disponibles contiene generalidades sobre los métodos de obtención de los mismos. Los fenómenos que ocurren en la elaboración de un soporte son de diversa naturaleza e involucran una gran variedad de disciplinas científicas.
Los soportes cerámicos deben poseer una distribución de tamaño de poro comprendida entre 0.1 y 15 µm. Los soportes con diámetros promedio de poros superiores a 1 µm se consideran macro partículas filtrantes. Estos soportes se producen mediante procesos de compactación y extrusión en seco. Los soportes macro porosos se recubren, por dip coating, con una serie de capas, cada una de las cuales tiene un menor tamaño de poro que la capa precedente.
La alúmina usada como material de soporte para membranas o especies activas catalíticas tiene que ser conformada para que adquiera la forma requerida para el empleo al cual se va a destinar. El conformado de alúmina comercial o de cualquier otro material de soporte, en una geometría específica es un proceso conformado por las siguientes etapas:
- Preparación de una pasta moldeable, mediante la aglomeración de las partículas de alúmina(o de cualquier otro material.
- Compresión o compactación del aglomerado.
- Sinterización de las piezas compactadas.
Cada uno de los pasos anteriores posee variables particulares y la combinación de las mismas tiene influencia en el producto final, el soporte para la membrana (Eksi y Saritas, 2002; Erdogan y Seker, 2002; Espinoza y otros, 2001; Falamaki y otros, 2001). En la etapa de preparación de la pasta moldeable se deben considerar aspectos como tamaño de partícula, tipo de aglutinante, solventes lubricantes internos y externos, agentes para el control de la viscosidad y porosidad, etc.
La variable fundamental durante la etapa de compresión del aglomerado es la presión de compactación, la que tiene como parámetro importante el tamaño del aglomerado, ya que este determina la homogeneidad de llenado del dado, aspecto que determina la porosidad de la pieza moldeada y la resistencia mecánica de la pieza en verde entre otras cosas. (Falamaki, 2004; Galindo, 2000; Galusek y Riley; Gaponenko, 2001; Garcia y otros, 2002).
El soporte para una membrana tiene como función dar resistencia mecánica a los esfuerzos causados a la capa superior (membrana) por la diferencia de presión aplicada sobre ella; debe presentar baja resistencia al flujo de filtrado y una superficie lisa para que pueda aplicarse la película superior sin que se presenten defectos en la misma. El soporte debe satisfacer exigencias tales como permeabilidad, una distribución cerrada de tamaño de poro y superficie uniforme. (Garcia-Miquel y otros, 2003, Giannelis y otros, 1998; Gonzalez, 2003; Guillard y otros; Guillen y otros, 1999; Gutierrez y otros, 1998, A., Hofacker y otros, 2002; Humphrey, 1997, pag. 300-390; Hwang y otros, 2002; Ibrahim y otros, 1999; Ivanova y otros, 2003; Jayavel y otros, 2003; Jones y otros, 2001; King y otros, 2002; Kirszensztejn y otros, 2003).
La obtención de sustratos cerámicos para membranas inorgánicas implica un equilibrio entre la resistencia mecánica y la porosidad abierta de la pieza cerámica, debido a lo previamente descrito. El desarrollo del sinterizado incide sobre el nivel de asociaciones químicas que se establece entre las partículas y por ende en la resistencia mecánica de la pieza (Kwang y Lin, 2001); adicionalmente este factor controla el grado de densificación del sustrato por lo que se debe evitar altos niveles de este cambio estructural del material. De acuerdo con lo anterior y debido a las propiedades de la alúmina comercial empleada, (material tratado a 1300 C), para la elaboración de los sustratos es necesario establecer formulaciones basadas en aglutinantes inorgánicos, con los que se puedan lograr mayores niveles de cohesión química entre las partículas, y baja densificación para que después pueda servir como soporte.
En el presente trabajo se estudia la obtención de soportes para membranas inorgánicas, empezando con la obtención de los precursores empleados en la síntesis de los aglomerantes para el compuesto base en la elaboración de los sustratos, la alfa alúmina. También se obtiene el precursor de un coadyuvante del proceso de sinterizado para la misma sustancia, el Metóxido de magnesio, que por posteriores reacciones da lugar a óxidos hidratados, que son los que intervienen finalmente en la sinterización.
Diferentes formulaciones de aglomerantes y coadyuvantes son evaluadas con base en su incidencia en la formación de una masa plástica y a la resistencia en verde del conformado. Finalmente se estudia el efecto de la presión de compactación y de la temperatura a la cual se lleva a cabo el proceso de sinterizado, sobre la resistencia a la compresión y la porosidad de la pieza.
Materiales y equipos
Los sustancias químicas empleadas; alfa alúmina, alcohol metílico e isopropílico, aluminio en laminas y magnesio en gránulos fueron reactivos grado analítico marca MERCK. las pruebas de microscopia electrónica de barrido se efectuaron en un microscopio FEI Phillips Quanta 200 de alto vacío, con voltaje de 25 kV y corriente de emisión de 103 µA; el equipo contó adicionalmente con un accesorio EDAX para el análisis semicuantitativo de elementos.
Procedimiento experimental
El procedimiento experimental de este trabajo estuvo compuesto por las siguientes tres etapas:
- Síntesis de los aglutinantes y del coadyuvante del sinterizado de la alúmina comercial empleada para la obtención de los sustratos. Los aglutinantes empleados fueron pseudoboehmita y sílica, y el coadyuvante óxido de magnesio, todos ellos en estado coloidal.
- Preparación de un aglomerado plástico y granulado
- Moldeado de la alúmina comercial granulada y tratamiento térmico de los sustrato.
La obtención de los precursores y del coadyuvante de sinterizado se realizo mediante la técnica de sol gel.
Síntesis de aglutinantes y del coayudante de sinterizado
Óxido de magnesio hidratado
El óxido de magnesio hidratado se obtuvo a partir del metóxido de magnesio; este alcóxido se hidrolizó, condensó, en forma simultanea con el alcóxido de aluminio. El producto sólido fue dispersado coloidalmente con ácido nítrico.
- Síntesis del Metóxido de Magnesio. El Metóxido de magnesio, empleado en este proyecto, fue sintetizado, a partir de metanol y magnesio, siguiendo los pasos recomendados por Patarroyo y Molina, 2004. El proceso es similar al seguido para la síntesis del isopropóxido de aluminio. La relación empleada entre los reactivos fue de 3 veces la cantidad estequiométrica de alcohol con respecto a la cantidad de Mg. El magnesio se sometió a un proceso de secado; luego se activó con yodo y posteriormente se puso en contacto con el metanol por un tiempo de 2 horas. La temperatura de reacción fue 86 °C. Todo el sistema permanecía a reflujo. La reacción efectuada corresponde al tipo:
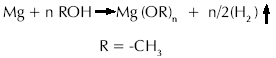
La Figura 1, describe el procedimiento de síntesis del metóxido de magnesio.
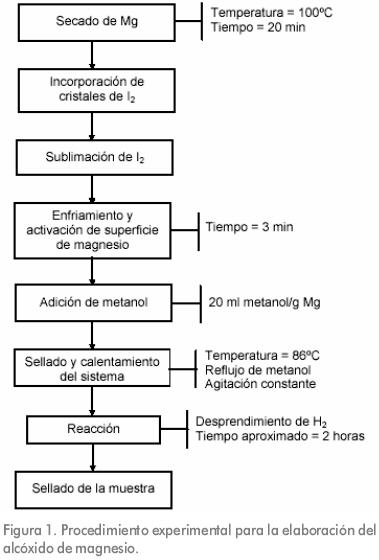
Esta muestra de metóxido se sometió a una reacción de hidrólisis y condensación simultanea con el isopropóxido de aluminio. La relación de alcóxidos fue de 1 parte del alcóxido de magnesio por 100 partes del alcóxido de aluminio.
El producto obtenido fue filtrado y el precipitado formado fue secado y molido `para ser sometido a un a caracterización por análisis termogravimétrico.
Pseudoboehmita
La pseudoboehmita fue preparada usando, como precursor de la misma, el triisopropóxido de aluminio; el último compuesto mencionado fue usado en las reacciones sol gel, y el producto sólido obtenido al final de estas reacciones fue dispersado, de forma coloidal, por restitución de la doble capa eléctrica.
La preparación de la pseudoboehmita coloidal abarcó las etapas de Síntesis del precursor molecular, hidrólisis y condensación, y peptizado del precipitado de oxohidróxido de aluminio (boehmita). El procedimiento seguido se detalla en la Figura 2.
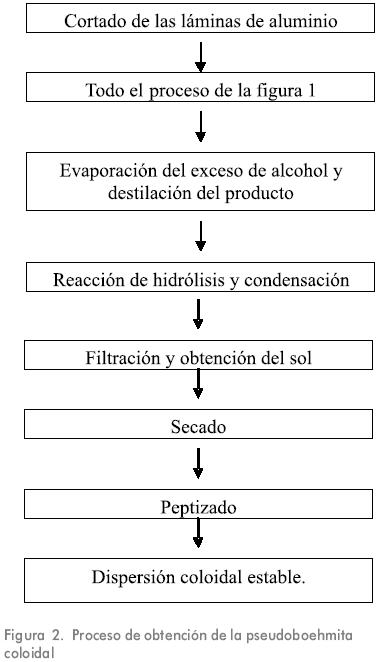
Obtención del triisopropóxido de aluminio
El triisopropóxido de aluminio fue el precursor molecular empleado para la elaboración de la pseudoboehmita.
En la reacción de síntesis entre el isopropanol y el aluminio se empleó un exceso del 20 % de isopropanol con respecto a la cantidad estequiométrica necesaria. La cantidad de catalizador utilizada fue del 1 % en peso con respecto al aluminio. La síntesis del compuesto se llevó a cabo en un reactor con condensador, para evitar la pérdida del alcohol en exceso, y con un conducto a la atmósfera para liberar el hidrógeno producido.
La reacción involucrada en esta síntesis es la siguiente:

En este proyecto se empleó una metodología diferente, a la propuesta por Galindo, 2000, para la elaboración del compuesto, debido a que se utilizo como catalizador un compuesto menos tóxico, el yodo. Esto marca una novedad al compararlo con el ioduro de mercurio empleado anteriormente.
El aluminio se somete a un proceso de secado a 60 °C, por una hora, antes de ponerse en contacto con el yodo sublimado, que actuará como catalizador. Una vez que el aluminio ha sido activado se agrega al balón donde se encuentra el alcohol y se da inicio a la reacción, a la temperatura de 70 °C, utilizando un reflujo de agua, para condensar los vapores que se puedan formar. La reacción comienza con una formación muy lenta de burbujas de hidrógeno, y sigue con una evolución rápida de burbujas que homogenizan la mezcla reaccionante. La etapa final de la reacción vuelve a caracterizarse por una lenta evolución de burbujas. La apariencia de la mezcla reaccionante cambia de translúcida a grisácea con el transcurso de la reacción.
Al final del periodo de reacción el exceso de alcohol es eliminado por medio de un proceso de destilación. El alcóxido de aluminio termina de purificarse por una destilación a vacío, obteniéndose el triisopropóxido de aluminio, un líquido transparente y viscoso que destila entre 120 y 130 °C.
Reacciones de hidrólisis y condensación
En las reacciones de hidrólisis y condensación se empleó agua desionizada, tipo cromatográfico, en una relación molar de 100:1 alcóxido agua. La reacción se realizó en un reactor de vidrio enchaquetado. La temperatura de reacción fue de 80 °C, y la mezcla reaccionante siempre estuvo sometida a una continua agitación.
Las reacciones de hidrólisis son las siguientes, (donde R es C3H7O)

La reacción de condensación se puede esquematizar como
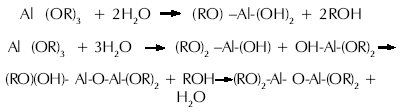
El tiempo empleado para esta transformación fue de 1 hora; después del cual el gel formado se filtró a vacío, para retirar el exceso de agua, y el precipitado formado, quedó retenido en un papel filtro número cuatro. El precipitado fue posteriormente sometido a un proceso de secado por un lapso de 12 horas, a una temperatura de 105 °C. Al final de todos estos pasos se obtuvo la pseudoboehmita.
El material seco se molió y se caracterizó mediante un análisis termogravimétrico. La pseudoboehmita caracterizada por este método registraba una perdida de peso del 25 %.
Dispersión coloidal de la pseudoboehmita
El peptizado de este compuesto, es equivalente a la dispersión coloidal del mismo se realiza para modificar la actividad superficial de sus partículas.
Este paso se inició con la disolución en agua desionizada, del producto sólido, obtenido al final de las reacciones descritas en el paso anterior. La cantidad de agua fue tal que la pseudoboehmita formó una suspensión coloidal cuya concentración fue 1M. A esta suspensión se le agregó el agente peptizante, que en este caso fue el ácido nítrico, en proporción molar de 0.07 H+/Al (0.07 (moles de ácido/mol de aluminio presente en el oxido hidratado). La reacción se lleva a cabo por 5 horas, a una temperatura de 70 °C, utilizando un reactor de reflujo para evitar la perdida de agua. El tiempo de reacción es importante pues modifica las propiedades del aglutinante.
Sílica coloidal
El otro aglutinante empleado en este proyecto fue la sílica coloidal, la cual se obtuvo a partir de las reacciones de hidrólisis y condensación del silicato de sodio disuelto en agua y promovidos por un medio ácido suministrado por una resina acidificada.
Obtención de la sílica coloidal
Para la obtención de este material se utilizó la técnica empleada por Virguez y Sepúlveda. En este procedimiento, se utiliza una resina de intercambio ácida, la cual se activa sometiéndola al proceso descrito por Orjuela, 2003 y consistente en lavados sucesivos con HCl, empezando con soluciones 1.5 molar de ácido y dejando la resina en agitación por dos horas, después de lo cual se repetía el procedimiento con soluciones cada vez menos concentradas de ácido. El lavado se suspendía cuando el pH final, del agua era de 6.5 -7. Una vez que la resina se encontraba activa, se empacaban unos 25 gramos de esta, en un reactor tubular, al que se le agregaba una solución de 1 parte silicato de sodio por 4 partes de agua, y finalmente se le adicionan 10 mililitros de agua pura. La cantidad de silicato empleada depende de la relación final de material aglutinante a alúmina, requerida para la elaboración del soporte. Las reacciones sol gel en el medio acuoso ácido produjeron una dispersión transparente que, se sometió a un proceso de maduración a 65 °C, y en continua agitación. El proceso de gelificación se suspende cuando la solución comienza a adquirir un carácter turbio. Esta turbidez señala un incremento apreciable del tamaño de las partículas de silica. En este punto se adicionó una suspensión de la alúmina comercial que constituyó el material del sustrato cerámico. Esta mezcla se agitó y se sometió a evaporación para retirar el exceso de agua y lograr las propiedades reológicas requeridas en el paso de conformado.
Uno de los ensayos con sílica evaluó su desempeño no como dispersión coloidal sino como gel, que se obtuvo con el sol que abandonaba el reactor; es importante recalcar que esta transición fue inmediata y no se dio por evaporación o maduración del sol. A esta sílica se le denominó pregelificada para diferenciarla de la aplicada como sol.
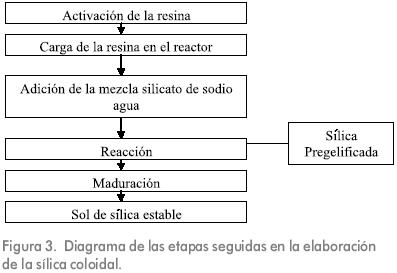
Preparación del aglomerado plástico y conformado
La secuencia de pasos utilizados en esta etapa, para el caso de las formulaciones con pseudoboehmita o las mezclas pseudoboehmita magnesio, fue la siguiente:
- Adición de una solución de gelatina.
- Adición de una suspensión de la alúmina comercial.
- Evaporación parcial del solvente.
- Obtención de una masa plástica
- Elaboración de los filamentos a partir de la masa plástica mediante extrusión.
- Secado de los filamentos.
La masa plástica obtenida se extruyó para obtener unos filamentos delgados que fueron posteriormente sometidos a un proceso de secado por 12 horas. Los filamentos pasaron luego al proceso de moldeado para obtener las piezas en verde.
El procedimiento experimental seguido para la obtención de los aglomerados que usan bentonita en su formulación fue similar al anteriormente descrito, excepto en que se preparaba una suspensión acuosa de este compuesto en lugar de la solución de gelatina.
Moldeado y tratamiento térmico de los sustratos
Los filamentos de las distintas formulaciones que se obtuvieron, al final de las etapas, anteriormente descritas, fueron cortados para disminuir su longitud, y luego tamizados en un intento de controlar los tamaños de los gránulos que se iban a compactar. En el tamizado se descartaron únicamente los finos y los gránulos retenidos fueron posteriormente mezclados con ácido esteárico, en una proporción de 0.5% de ácido (medido con respecto a la masa de filamentos, de cada una de las diferentes formulaciones.). La función del ácido es servir como lubricante externo en el proceso de compactación.
El moldeado, mediante la técnica de compactación por compresión axial, se realizó a dos presiones diferentes 70 y 140 kgF/ cm2. Los valores de presión anteriormente mencionados fueron seleccionados para determinar el efecto de la presión sobre la porosidad y para evitar una densificación más elevada si se operaba a valores de presión más altos
Sinterizado
Los gránulos compactados, que constituyen la pieza en verde, fueron sometidos a una etapa de tratamiento térmico, con el fin de realizar el sinterizado. Este proceso se llevó a cabo a dos temperaturas diferentes. Las temperaturas empleadas fueron de 900 y 1200 °C, ya que, en la revisión bibliográfica, (Langlade y otros, 2002; Lee y otros, 2003; Legrand y Malibert, 2002; Liu y otros, 2002) se encontró que a temperaturas más altas se podía alcanzar una densificación elevada de las piezas.
La sinterización se llevo a cabo en el laboratorio de control de calidad de la empresa Alfagres, en un horno marca Thermolyne modelo Furnace 1400, con dispositivos para el control de la temperatura y que permitía alcanzar los 1200 °C. El tiempo de sinterizado empleado fue de tres horas en cada uno de los casos; En este proyecto se decidió no analizar la influencia que el tiempo de sinterizado ejerce sobre las propiedades finales de los productos.
Resultados
Se realizaron unos ensayos preliminares para determinar cuales eran las formulaciones que se emplearían en los ensayos definitivos. En la Tabla 1 se registran los resultados obtenidos.
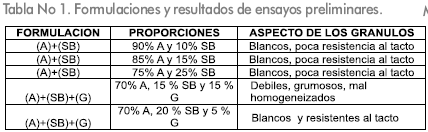
Con estos resultados se determino realizar ensayos definitivos, variando en el caso de la silica la forma del coloide. Las formulaciones empleadas se indican en la Tabla 2.
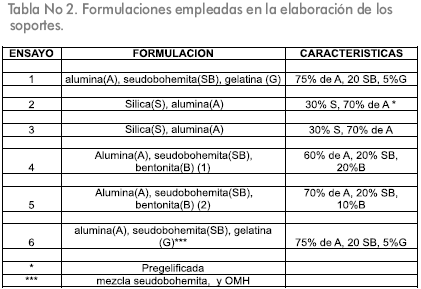
Estas muestras se sometían a los procesos de moldeado y tratamiento térmico y a las mejores muestras se les realizaban pruebas de caracterización por microscopia electrónica. Las micrografías obtenidas se muestran a continuación.
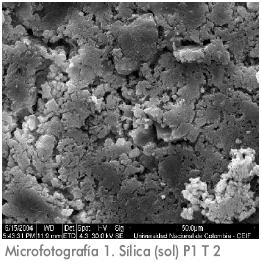
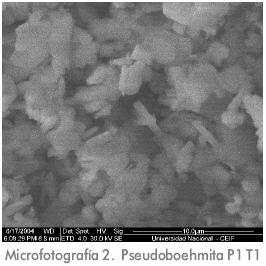
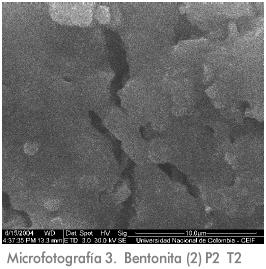
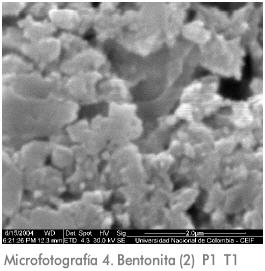
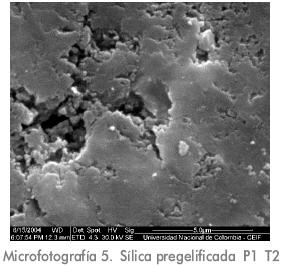
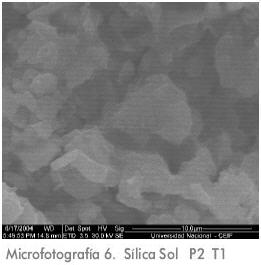
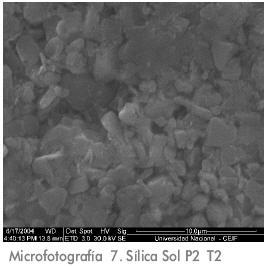
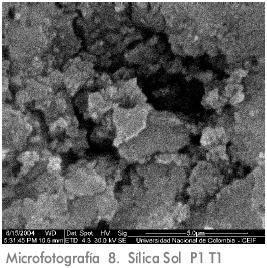
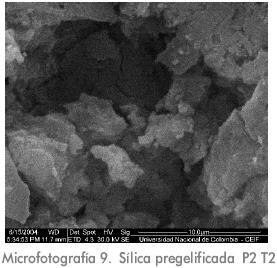
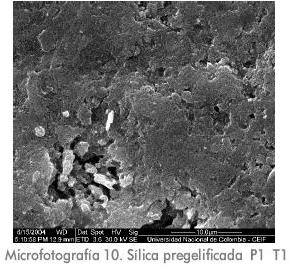
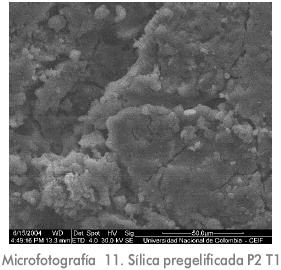
A estas micrografías se les realizó un procesamiento digital con MatLab para determinar porosidad obteniéndose los resultados que se registran en la Tabla 3, correspondiendo el número 1 a la muestra con mayor porosidad y el número 11 a la menos porosa.
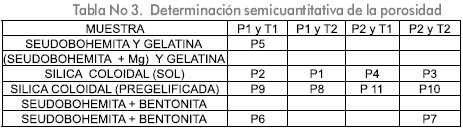
A estas muestras, se les determino la resistencia a la compresión y se obtuvieron los resultados que se reportan en la Tabla 4.
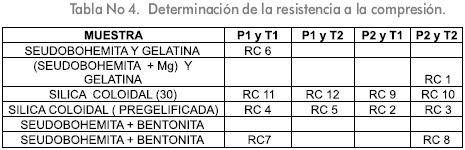
Donde RC significa resistencia a la compresión y el número 1 corresponde a la muestra con mayor resistencia a la compresión y el número 12 con la menor.
Análisis de resultados
Las morfologías observadas en el análisis de las microfotografías permiten establecer diferentes niveles de densificación de los sustratos preparados con las formulaciones empleadas y compactadas y tratadas térmicamente bajo las condiciones establecidas.
En general, se observa que las piezas aglomeradas con silica coloidal presentan mayor porosidad que las preparadas empleando los otros aglutinantes estudiados. Las piezas aglutinadas con la muestra de sílica pregelificada, presentan la mayor densificación lo que se puede atribuir al tamaño de las partículas y al mecanismo de sinterizado (flujo viscoso) exhibido por este material; al no permitirse la maduración del sol (por la transición sol gel que experimento), las partículas de sílica no crecieron y por lo tanto son más pequeñas que las del sol (ya que este experimento maduración), por lo que bajo las circunstancias experimentales empleadas, la velocidad de densificación que se alcanzo, fue mayor que en las otras muestras cuyo aglutinante se adiciono como sol. Esto también contribuye a explicar la baja porosidad de estas muestras y su elevada resistencia a la compresión, pues en las mismas se alcanzó un mayor nivel de densificación.
En las microfotografías se aprecia, de forma clara, el aspecto que presentan las muestras que contienen silica coloidal en su formulación. Esta imagen es la que se espera que presenten los compuestos amorfos en los cuales, el mecanismo de sinterizado se da por flujo viscoso. En dichas microfotografías no se observan gránulos con una geometría definida; en lugar de ello se aprecian masas corpusculares, que se pueden comparar, recurriendo a una analogía visual, con el aspecto que presenta una muestra de queso fundido.
Lo anterior puede explicarse con base en el conocimiento de que, al ser la silica coloidal un material amorfo su mecanismo de sinterizado es fuertemente influenciado por la temperatura, y de hecho para los materiales siliceos la viscosidad se incrementa en un orden de magnitud por un aumento de temperatura comprendido entre 20 y 40 ºC. Por lo anterior al empezar a elevarse la temperatura, durante el proceso de sinterizado, la sílica coloidal fluye y rodea a los cristales de alúminas, dando como resultado la apariencia antes mencionada; luego estas piezas exhiben baja porosidad y alta resistencia mecánica a la compresión
El anterior análisis puede aplicarse tanto a las muestras en estado sol, ya que al presentar diferentes tamaños de partículas, por el tratamiento de maduración, puede establecerse un comportamiento diferente para las dos formulaciones que contienen sílica, la velocidad de sinterizado es mayor, en muestras con menor tamaño de partícula.
Bibliografía
Ananthakumar, S. y Warrier, K.G.K., Extrusion Characteristics of Alumina Aluminium Titanate Composite Using Boehmite as a Reactive Binder., Journal of the European Ceramic Society, Vol. 21, No 1, Ene. 2001, pp. 71 78. [ Links ]
Barrera, V. y Barón,W., Empleo de la técnica Sol Gel en la elaboración de membranas cerámicas porosas soportadas. Fase I., Tesis presentada a la Universidad Nacional de Colombia, para optar por el titulo de Ingeniero químico, 2001. [ Links ]
Belin S, Santos L.R y Briois V., Preparation of Ceramic Membranes from Surface Modified Tin Oxide Nanoparticles., Colloids and Surfaces A: Physicochemical Eng. Aspects, Vol. 216, N° 1-3, Abr. 2003. [ Links ]
Bhave, R., Inorganic Membranes: Synthesis, Characteristics and Applications., Chapman Hall, 1991. [ Links ]
Binner, Jon G. P., Advanced ceramic processing and Technology., Vol.1, Noyes publication, 1990. [ Links ]
Brinker, C y Scherer, W., Sol Gel Science: The physics and Chemistry of Sol Gel Processing., Academic Press, 1990. [ Links ]
Carberry J. J., Varma A., Chemical Reaction and Reaction Engineering., Marcel Dekker, 1995. [ Links ]
Chang, C.H., Gopalan, C., Lin, Y.S., A Comparative Study on Thermal and Hydrothermal Stability of Alumina, Titania and Zirconia Membranes., En: Journal of Membrane Science, Vol. 91, N° 1-2, May 1994, pp. 27-45. [ Links ]
Chaudhuri S., Bhattachartjee B. y Ganguli D., Pal, A.K., Synthesis and Optical Characterization of SolGel Derived Zinc Sulphide Nanoparticles Confined in Amorphous Silica Thin Films., Materials Chemistry and Physics, Vol. 78, N° 2, Feb 2002, pp 372379. [ Links ]
Conde A., Durán A., De Damborenea J.J., Polymeric Sol Gel Coatings as Protective Layers of Aluminium Alloys., Progress in Organic Coatings, Vol. 46, N° 4, Jun 2003, pp. 19. [ Links ]
Dilsiz, Nursel y Akovali, G., Study of SolGel Processing For Fabrication of Low Density Alumina Microspheres., Materials Science and Engineering A, Vol. 332, N° 1-2, Jun 2002, pp. 9196. [ Links ]
Dima A., Dima O., Moldovan C., Cobianu, C., Savaniu, C., Zaharescu M., Substrate Influence on The Response of Sol Gel Derived SnO2 Gas Sensors., Thin Solid Films, Vol. 427, N° 1-2, Mar 2003, pp. 427431. [ Links ]
Dongare, M.K., Sonawane, R.S., Hegde, S.G., Preparation of Titanium (IV) Oxide Thin Film Photocatalyst By SolGel Dip Coating., Materials Chemistry and Physics, Vol. 77, N° 3, Ene. 2002, pp. 744750. [ Links ]
Duran A., Gallardo, J., Di Martino, D., Almeida, R., Structure of Inorganic and Hybrid SiO2 solgel coatings studied by variable incidence infrared spectroscopy., Journal of Non-Crystalline Solids, Vol. 298, N° 2-3, Mar. 2002, pp. 219225. [ Links ]
Eksi, A., Saritas, S., Effects of powder hardness and particle size on the densification of cold isostatically pressed powder., Turkish J. Eng. Env. Sci., Vol. 54, N° 7-8, Jun. 2002, pp. 377 384. [ Links ]
Erdogan, G., Seker, E., Single Step Sol Gel Made Gold on Alumina Catalyst for Selective Reduction of NOx Under Oxidizing Conditions: Effect of Gold Precursor and Reaction Conditions., Applied Catalysis A: General, Vol. 232, N° 1-2, Jun. 2002, pp. 203217. [ Links ]
Espinoza Beltran, F.J., Diaz-Flores L.L., Mendoza-Galvan, R., Gonzalez Hernandez J., Qualitative evaluation of solgel SiO2 as a protective layer for soft surfaces., Surface and Coatings Technology, Vol. 148, N° 1, Nov. 2001, pp. 17. [ Links ]
Falamaki, C., Aghaie A., Ardestani N., Membranes/Catalitic Supports with Enhanced Permeability., Journal of European Ceramics Society, Vol. 21, N° 13, Nov. 2001, pp. 2267 2274. [ Links ]
Falamaki, C., Shafiee, A., Aghaie A., Initial sintering stage pore growth mechanism applied to the manufacture of ceramic membrane supports., En Journal of European Ceramics Society, Vol. 24, N° 8, Jul. 2004, pp. 2285 2292. [ Links ]
Galindo, V. Hugo., Estudio de los Procesos sol gel para la Obtención de un Aglutinante Apropiado para el Peletizado de Alumina., Tesis presentada a la Universidad Nacional de Colombia, para optar al grado de Magíster, 2000. [ Links ]
Galusek, D., Riley F., The Influence of Sintering Additives on the Indentation Response of Liquid Phase Sintered Polycrystalline Alúminas., Philosophical magazine A., Vol. 82, No 10, Oct. 2001, pp. 2041 2057. [ Links ]
Gaponenko N. V., Sol Gel Derived Films in Mesoporous Matrices: Porous Silicon, Anodic Alumina and Artificial Opals., Synthetic Metals, Vol. 124, N° 1, Oct. 2001, pp. 125 130. [ Links ]
Garcia-Cerda L.A., Mendoza-González, O., Pérez-Robles, J.F., Structural Characterization and Properties of Colloidal Silica Coatings on Copper Substrates., Materials Letters, Vol. 56, N° 4, Oct. 2002, pp. 450453. [ Links ]
Garcia-miquel, J.L., Zhang Q., Allen S.J., Rougier A., et al., Nickel Oxide SolGel Films from Nickel Diacetate for Electrochromic Applications., Thin Solid Films, Vol. 424, N° 2, Ene. 2003, pp. 165170. [ Links ]
Giannelis E.P., Podeghirero, E.D., Moore, B.C., Wolkenberg, M., Wuthenow, O.K., SolGel Synthesis of Ceramic Matrix Composites., Materials Science and Engineering A., Vol.244, N° 1, Mar. 1998, pp. 1121. [ Links ]
Gonzalez - Hernandez, J., Preparation And Characterization of SolGel Silica Based Neutral Optical Density Coatings by The Addition of Graphite Particles., Thin Solid Films, Vol. 423, N° 2, Ene. 2003, pp. 196 200. [ Links ]
Guillard C., Beaugiraud, B., Dutriez, C., Herrmann, J.M., Jaffrezic, H., Jaffrezic-Renault, N., Lacroix M., Physicochemical Properties and Photo Catalytic Activities of TiO2 Films Prepared by Sol Gel Methods., Thin Solid Films, Vol. 340, N° 1-2, Feb. 1999, pp. 280-287. [ Links ]
Guillen, C., Gandía, J., Morales, A., Herrero, J., SiO2 SolGel Coated Conducting Substrates for CuInSe2 Electrodeposition., Surface and Coatings Technology, Vol. 115, N° 1, Jun. 1999, pp. 4551. [ Links ]
Gutierrez, A., Gonzalez-Cruz, M., Trombetta, G., Ramirez, J., Characterization of AluminaTitania Mixed Oxide Supports. Part II Al2O3 based supports., Microporous and Mesoporous Materials, Vol. 23, N° 5-6, Sep. 1998, pp. 265275. [ Links ]
Hofacker, S., Menchelt M., MangeL, M., Kraus H., Sol Gel: A New Tool for Coatings Chemistry., Progress in Organic Coatings, Vol. 45, N° 2-3, Oct. 2002, pp. 159-164. [ Links ]
Humphrey, K. L., Keller, G.E., Separation Process Technology., Mc Graw Hill, Cap 5, 1997. [ Links ]
Hwang, Y., Liu, M., Jiang S., Preparation and Electrical Properties of ZnOGlass Ceramic Films., Microelectronic Engineering 1, Article in press, 2002. [ Links ]
Ibrahim, D. M., Khalil T., Mostafa, A.A., Densification of Alumina Produced by Urea Formaldehyde Sol - Gel Polymeric Route., Ceramics International, Vol. 25, N° 3, Abr. 1999, pp. 273-280. [ Links ]
Ivanova, T., Harizanova, A., Surtchev, M., Nenova, Z., Investigation of solGel Derived Thin Films Titanium Dioxide Doped with Vanadium Oxide., Solar Energy Materials and Solar Cells, Vol. 76, N° 4, Abr. 2003, pp. 591-598. [ Links ]
Jayavel, R., Madeswaran S., Giridharan, N. V., SolGel Synthesis and Property Studies of Layered Perovskite Bismuth Titanate Thin Films., Materials Chemistry and Physics, Vol. 80, N° 1, Abr. 2003, pp. 23-28. [ Links ]
Jones, C.D., Hidalgo, Maria, Wiesner, M., Barron, A., Alumina Ultrafiltration Membranes Derived from Carboxylate Alumoxane Nanoparticles., Journal of Membrane Science, Vol. 193, N° 2, Nov. 2001, pp.175-184. [ Links ]
King, D. J., Hang, H., Oh Hoon S., Kim, J., Influence of Calcination Temperature on Structural and Optical Properties of TiO2 Thin Films Prepared by Sol Gel Dip Coating., Materials Letters, Vol.57, N° 2, Dic. 2002, pp. 355-360. [ Links ]
Kirszensztejn, P., Szymkowiak, A., Marciniak, P., Martyla, A., Przekop R., Texture of Al2O3 SnO2 binary oxides system obtained via Sol Gel Chemistry., Applied Catalysis A: General, Vol. 245, N° 1, May. 2003, pp. 159-166. [ Links ]
Kwang Hsien y Lin Bor-Horng, The Effect of Sol - Gel Particle Reaction on Properties of Two Dimensional Ceramics Matrix Composites., Materials Letters, Vol. 48, N° 3-4, Abr. 2001, pp. 230-241. [ Links ]
Molina, D., Patarroyo Diana, Estudio De La Síntesis De Geles De Oxido De Magnesio A Partir De Procesos Sol - Gel Por Precursores Metalorgánicos., Tesis presentada a la universidad Nacional de Colombia, Bogota, para optar al titulo de Ingeniero químico, 2004. [ Links ]
Sepúlveda, J., Virguez, M., Remoción De Fenol En Medio Acuoso Diluido Por Medio De Catálisis Heterogénea En Operación Continua., Tesis presentada a la universidad Nacional de Colombia, Bogotá, para optar al titulo de Ingeniero químico. [ Links ]
Orjuela A., Tesis presentada a la Universidad Nacional de Colombia, Bogotá, para optar al titulo de Maestra en Ingeniería, 2003. [ Links ]