Services on Demand
Journal
Article
Indicators
-
Cited by SciELO
-
Access statistics
Related links
-
Cited by Google
-
Similars in SciELO
-
Similars in Google
Share
Ingeniería e Investigación
Print version ISSN 0120-5609
Ing. Investig. vol.26 no.1 Bogotá Jan./Apr. 2006
Johnny F. Obando B1, Álvaro Castro P.2 y Carlos Alexander Trujillo3
1 Ingeniero químico, estudiante de la maestría en materiales y procesos de manufactura de la Universidad Nacional de Colombia, Bogotá. fobandob@unal.edu.co
2 M Sc,, Instituto Tecnológico de Aeronaútica, Brasil. Ingeniero mecánico, profesor titular Universidad Nacional de Colombia, Bogotá. castrop@unal.edu.co
3 Dr. Sc, Químico. Profesor, Universidad Nacional de Colombia, Bogotá. catrujillo@unal.edu.co
RESUMEN
En esta investigación se realizó el diseño, construcción y prueba de un equipo a escala de laboratorio para tratamientos térmicos con atmósfera controlada para el estudio de la carburización gaseosa de aceros con alcoholes. El equipo posee las siguientes características: producción controlada de una atmósfera gaseosa compuesta hasta por tres gases y dos líquidos volátiles, una zona de reacción isotérmica, inerte y hermética, y una zona de análisis de gases que retiene sólidos y líquidos condensables y que cuenta con sensores de presión y de dióxido de carbono. Se hicieron ocho ensayos con el alcohol metílico, etílico, n-propílico, isopropílico y tertbutanol, encontrándose que el alcohol metílico carburiza y produce una baja cantidad de hollín pero profundiza poco en la pieza, el etanol descarburiza y forma grandes cantidades de hollín, el n-propanol, isopropanol y el tertbutanol proveen buenos potenciales de carbono y profundidades de capa con una gran formación de hollín y alquitrán, siendo en orden ascendente en producción de hollín y alquitrán el n-propanol, el tertbutanol y el isopropanol.
Palabras clave: equipo para tratamientos térmicos con atmósfera controlada, carburización gaseosa utilizando alcoholes, caracterización de capas carburizadas.
ABSTRACT
This article deals with designing, constructing and testing a laboratory scale apparatus for heat treatment with controlled atmosphere. The equipment was used for studying steel carburisation with alcohols. The equipment has an area for the controlled production of a gas atmosphere composed by up to 3 gases and 2 volatile liquids, an inert and hermetic isothermal reaction area and a gas analysis area which retains solids and condensable liquids. The equipment was provided with pressure and carbon dioxide concentration sensors. Eight experiments were carried out with methanol, ethanol, n-propanol, isopropanol and tertbutanol as carbon source. The results showed that methanol caused carburisation but layer depth was small and produced a low quantity of soot, ethanol caused decarburisation and formed large quantities of soot, n-propanol, isopropanol and the tertbutanol provided good carbon potential and layers having good depth with good soot and tar production. Soot and tar production followed this order: n-propanol < tertbutanol < isopropanol.
Keywords: heat treatment equipment with controlled atmosphere, gas carburisation using alcohols, carburised layer characterisation.
Recibido: enero 16 de 2006.
Aceptado: febrero 28 de 2006.
Introducción
Muchos de los elementos de máquinas, herramientas, equipos y demás piezas en acero que actúan bajo condiciones de desgaste necesitan de procesos que aumenten su dureza superficial sin modificar la tenacidad del núcleo, para aumentar el tiempo de servicio. Este objetivo se puede alcanzar por varios métodos, pero los más comunes son los tratamientos termoquímicos, donde al aumentar la concentración superficial de un elemento químico las características mecánicas cambian notablemente; es el caso de la carburización gaseosa con alcoholes, donde se aumenta la concentración superficial de carbono por la diferencia de concentración entre la pieza y una atmósfera rica en carbono, procedente de alcoholes.
Este tratamiento térmico ha sido estudiado desde mediados del siglo XX (Wyss, 1963, 1978 y 1979; Main, 1980; Béguin, 1981; Slycke y Sproge, 1988; Holm, 1989; Lanham, 1997; Sullivan 1997), dado que es una mejor alternativa respecto de técnicas como la carburización en fase sólida, carburización en fase líquida, y la carburización gaseosa por generación endotérmica. La carburización con alcoholes, desde sus inicios, fue bautizada como gaseosa por goteo de alcoholes Drip feed (Wyss, 1963, 1978 y 1979) debido a que el método típico de ingreso del alcohol al horno es el goteo; sin embargo, por la metodología utilizada en el presente artículo el nombre más preciso es el de carburización gaseosa con alcoholes.
Desde mediados de los años ochenta la carburización gaseosa con alcoholes ha sido estudiada por la industria y por los centros de investigación. En la Universidad Nacional (Baldrich, 1986; Bohórquez, 2001; Meléndez, 1993; Nieto, 1987; Quijano, 1989; Rodríguez y Junca, 1984; Vargas y Fajardo, 1997), se dio inicio a esta investigación en 1986 (Baldrich) con el diseño y construcción de un horno a escala para carburización gaseosa con alcoholes. El horno se construyó como una réplica a menor escala de los hornos industriales usados para estos procesos.
Con ese equipo se han desarrollado varios trabajos (Nieto, 1978; Rodríguez y Junca, 1984; Quijano, 1989; Meléndez, 1993; Vargas y Fajardo, 1997; Bohórquez, 2001) tendientes a adaptar tecnología y a estudiar la forma como influyen las variables del proceso. A través de esos trabajos se identificaron algunas mezclas de metanol e isopropanol que presentaron buenos resultados también se encontró que el método de seguimiento de la carburización midiendo la temperatura de rocío no es válido sino hasta dos horas después de iniciado el tratamiento, que los elementos aleantes al acero pueden ayudar o retrasar la carburización, etc. Durante los estudios se hizo latente la necesidad de mejorar el equipo (Nieto, 1978; Quijano, 1989; Rodríguez y Junca, 1984) teniendo en cuenta que tiene varias restricciones de diseño que evitan tener resultados muy precisos, como falta de hermeticidad, interferencia en la carburización por el material de construcción del horno, dificultad de control de la producción de atmósfera e imposibilidad de capturar los subproductos y cuantificarlos.
Para continuar con la investigación de la carburización se requirió dar paso a un estudio más pormenorizado acerca de los procesos de transferencia de masa, de las reacciones químicas involucradas, de la influencia del alcohol en las características finales de las piezas tratadas, de la formación de hollín y de alquitrán y de su relación con el alcohol y la pieza, entre otros tantos interrogantes. Surgió entonces la necesidad de construir un equipo que pudiera estudiar los factores más importantes que intervienen en la carburización para realizar el estudio de cada variable e identificar su influencia en el tratamiento.
Consideraciones de diseño
La carburización gaseosa con alcoholes requiere de tres procesos que son: preparación de la atmósfera o de la mezcla gaseosa a utilizar, proceso de carburización y seguimiento del proceso por el análisis de los gases de salida, con base en estos criterios se planeó que el equipo estuviera constituido por tres zonas, denominadas de preparación de atmósfera, de carburización o de reacción, y de tratamiento y análisis de los gases de salida.
Cada zona se diseñó de tal manera que fuera un módulo autónomo que cumpliera con los objetivos asignados y que al unirlas formaran el equipo. Esta planeación permitió que el equipo fuera versátil, fácilmente modificable, y que permitiera su transporte, su fácil desmonte y reparación.
Dentro de los requerimientos de diseño se presentaron las siguientes necesidades para cumplir con las exigencias de la investigación: producción controlada de atmósferas para carburización, ingreso de mezclas gaseosas homogéneas, condiciones de hermeticidad en el horno, condición inerte del reactor de carburización, zona isotérmica de trabajo en el reactor, disponibilidad de un amplio rango de temperaturas, capacidad de captura de los subproductos sólidos y líquidos condensables, análisis de los gases de salida, y cuantificación por métodos directos y/o indirectos de los subproductos atrapados.
Por las condiciones de trabajo a las cuales trabajaría el equipo, por la precisión y exactitud de los datos, y por la ubicación espacial del mismo cerca de un equipo de análisis, se decidió que el tamaño del equipo debería ser a escala de laboratorio, con la capacidad justa para tratar piezas con la forma y el tamaño requeridos para utilizar las técnicas comunes de análisis a piezas metálicas como son el ensayo de composición química ensayos de microdureza y estudios de metalografía.
Descripción del equipo
En forma paralela, como se definió anteriormente, en el equipo se identificaron tres procesos, que son descritos como zona de preparación de la atmósfera, zona de reacción y zona de tratamiento y análisis de los gases de salida. En la Foto 1, se observa la imagen del equipo construido.
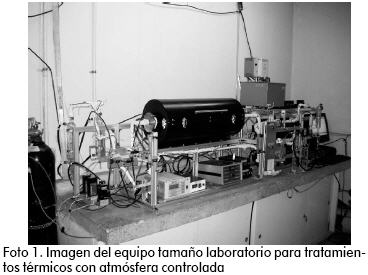
a. Zona de preparación de atmósferas
El diseño de esta parte del equipo consistió en planificar la entrada de máximo tres gases y el arrastre de un máximo de dos líquidos volátiles, para entregar atmósferas a la zona de reacción con una amplia gama de composiciones y concentraciones.
En la Figura 1A se muestra la disposición de los componentes de esta zona. Se aprecia que se dispuso de tres entradas para gas, cada una controlada a través de tres controladores de flujo másico, dos de ellos de marca Aalborg de referencia AFC2600, que pueden proveer caudales a condiciones normales de 100 mL/min (1,67x10-6 m3/s) y 68 mL/min (1,13x10-6 m3/s) de nitrógeno, respectivamente. El otro controlador, de marca Brooks de referencia 5850E, puede manejar un caudal a condiciones normales de 480 mL/min (8x10-6 m3/s) de nitrógeno.
Las líneas de conducción de los gases hasta antes de los saturadores y antes de la válvula E se realizó con mangueras de nylon de ¼ que soportan un máximo de 120 psi (827 KPa) de presión. Se cuenta con un panel de válvulas compuesto por cinco válvulas de ¼ de giro, denominadas A, B, C, D y E. Las conexiones de las válvulas con las mangueras se hicieron con acoples neumáticos, lo que permite efectuar modificaciones a las líneas de dirección de los flujos con gran rapidez y sencillez.
Los líquidos volátiles se administran vía los saturadores o reactores tubulares de burbujeo; estos poseen una chaqueta calefactora y una capacidad de 250 mL (2,5x10-4 m3), donde un gas o mezcla de gases ingresa a condiciones de temperatura del saturador y a la presión del sistema y arrastra una cantidad de líquido en forma de vapor. La tubería que comunica los saturadores con el reactor está construida en acero inoxidable 316 con calefacción eléctrica, para evitar la condensación de los vapores dentro de la tubería.
Cada saturador cuenta con un termostato que permite operar en un rango de temperaturas entre 303 K y 365 K. La línea de ingreso de los gases al horno cuenta con un medidor de presión y se calienta para evitar la condensación de los vapores; varios termopares permiten vigilar la temperatura.
Internamente, en la tubería se encuentra un mezclador estático, dispositivo que ayuda a mejorar la homogeneidad de la mezcla de gases y vapores dado que aumenta la turbulencia; esta pieza está ubicada antes de la posición de la válvula F.
b. Zona de reacción
Esta sección (Figura 1B) inicia con una válvula de tres vías que permite hacer un by-pass al reactor o dar el ingreso de los gases al mismo. La tubería que transporta los gases se une a una brida de acero inoxidable refrigerada, por la cual se hace el empalme entre el reactor de alúmina sinterizada con la tubería metálica.
El reactor es un tubo circular de 0,8 m de longitud, un diámetro interno de 0,042 m y uno externo de 0,05 m. Las bridas están compuestas por dos caras, una unida a la tubería, y otra pegada al tubo de alúmina. La unión metalcerámica se realizó con un pegante a base de alúmina que mantiene la unión, mientras que el sello para obtener hermeticidad se logró con silicona de alta resistencia a la temperatura. La refrigeración de las bridas se hace con aceite térmico y su objetivo es evitar que al aumentar la temperatura de las bridas estas se separen del reactor debido a la gran diferencia entre los coeficientes de dilatación térmica del acero inoxidable y la alúmina sinterizada.
El reactor descansa dentro de un horno de tres zonas de calentamiento, cada una con una resistencia que cuenta con un controlador de temperatura digital PID autónomo que permite hasta ocho programas de calentamiento.
Las tres zonas de calentamiento permiten obtener una zona isotérmica de 0,2 m en el interior del reactor, en su sección media, donde la variación máxima de temperatura es de +/- 2 K. El horno puede llegar a temperaturas del orden de los 1.223 K 1.273 K. El tiempo requerido por el horno para llegar a máxima temperatura es de 2 horas y media.
El reactor es atravesado de extremo a extremo por un termopar tipo K no aterrizado, de cubierta metálica, a la cual se le hizo conexión a tierra, que permite obtener lecturas de la temperatura dentro de la cámara de reacción en cualquier punto de su longitud. Este termopar está conectado en línea con un ordenador vía una interfase LabPro de Vernier.
A 0,15 m de la salida del reactor se dispuso un filtro de fibra cerámica de diámetro externo de 0,042 m y una longitud de 0,05 m, cuyo fin es retener cualquier subproducto sólido que pueda generarse en la zona de reacción y que pueda taponar las líneas de conducción o producir daños en los equipos de medida de la zona de tratamiento y análisis.
c. Zona de tratamiento y análisis
En esta parte del equipo (Figura 1C), los gases de salida son transportados por conductos de acero inoxidable 316 con calefacción hacia un panel de ocho válvulas de aguja que permite enviarlos a un segundo filtro o a un catalizador, o directamente a los elementos de detección.
A la salida del reactor hay una derivación al exterior, cerrada por una válvula de aguja, cuyo fin es reducir la presión del sistema en caso de taponamientos o sobrepresiones, y es útil en la extracción de muestras gaseosas sin tratar.
El filtro secundario está soportado por una columna de acero inoxidable que reposa dentro de un horno en una zona de calentamiento que puede alcanzar 873 K.
Debido a que el detector sólo responde al CO2, para convertir el monóxido de carbono en dióxido y poder realizar el balance de carbono durante la combustión del hollín y del alquitrán, se dispuso de una columna de catalizador de platino soportado sobre asbesto, ubicada en otro horno que puede alcanzar temperaturas de 873 K.
Los gases antes de llegar a los sensores pasan por un condensador que retiene líquidos condensables; pueden ser analizados posteriormente.
Esta zona, como se observa en la Figura 1C, cuenta con una entrada extra de gas que puede ser usada para proveer gas reactivo, en el caso de utilizar el catalizador, o para el ingreso de gases de referencia para posteriores análisis.
El equipo cuenta con un sensor de CO2 marca Vernier Instrument que permite identificar concentraciones entre 20 y 5.000 ppm, y está conectado al ordenador vía la interfase LabPro de Vernier.
Finalmente, los gases libres de partículas y de líquidos condensables son llevados a un espectrofotómetro infrarrojo Nicolet FTIR 510P que identifica las sustancias susceptibles de ser analizadas por espectroscopia infrarroja.
A las probetas metálicas tratadas se les analizó su composición química por medio de un espectrofotómetro óptico de chispa marca Baird Spetrovac, modelo DV-4, y su estructura microscópica a través de metalografía.
Experimentos
Se efectuaron ocho ensayos de carburización con alcoholes para evaluar las capacidades del equipo y hacer una evaluación de las principales características de cada uno de los alcoholes desde C1 a C4, de los cuales se usaron: metanol, etanol, n-propanol, isopropanol y tert-butanol.
Las probetas utilizadas estaban hechas en acero AISI SAE 1020 con la composición promedio presentada en la Tabla 1:

La efectividad de una carburización se mide por el potencial de carbono, la profundidad de capa y el aspecto exterior de la pieza definido como cantidad de hollín y alquitrán formado; se mantienen constantes variables como el tiempo de tratamiento, la temperatura de tratamiento, el tiempo de residencia en el horno y la concentración del alcohol en la atmósfera gaseosa.
El potencial de carbono es la concentración superficial de carbono en la pieza y se desea, como objetivo, que sea de 0,8% en peso (Valencia, 1992) para cumplir con las exigencias de dureza y tenacidad. La profundidad de capa es la zona carburizada desde la superficie hasta donde se obtiene la misma microestructura del núcleo del acero, y su determinación se efectúa a través de mediciones microscópicas de dureza. La capa se cuantifica midiendo la distancia que hay desde la periferia hasta el punto donde la dureza es igual a la que tiene la pieza en el núcleo.
La determinación de la formación de hollín y alquitrán se efectuó cualitativamente comparando las cantidades de los mismos dentro del horno y sobre las probetas.
El tiempo de residencia es una medida de caudal y es el tiempo necesario para renovar el volumen de gases del horno. La concentración molar de alcohol determina la cantidad de carbono que ingresa en el flujo gaseoso. La mezcla nitrógenoalcohol utilizada para generar la atmósfera carburizante se preparó en los saturadores por arrastre de vapor que es controlado con las condiciones de temperatura y presión del saturador.
Las condiciones de tratamiento fueron de 2 horas y una temperatura de 1.183 K. Los ensayos con metanol se realizaron con diferente duración; para el primer ensayo se utilizó una concentración de alcohol de 18% molar, y el tiempo del ensayo fue de media hora, mientras que el ensayo con 20% de alcohol fue de 4 horas. El ensayo se realizó con isopropanol y una concentración molar del 17% de alcohol, con una duración de 4 horas.
Resultados y análisis
En la Tabla 2 se presentan los ensayos efectuados con los resultados obtenidos.
Se puede observar que el potencial de carbono para los ensayos con etanol fueron menores o iguales a las características iniciales del material, mostrando ser una sustancia descarburizante y por tanto perjudicial para la carburización, además de formar gran cantidad de hollín y algo de alquitrán.
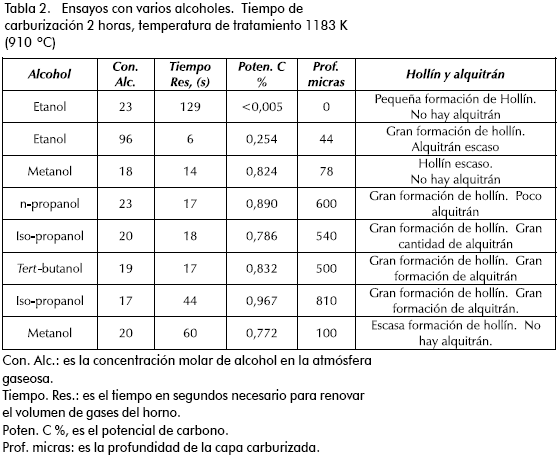
El metanol presenta buen potencial de carbono, pero al comparar las profundidades de las capas obtenidas se encuentra que independientemente del tiempo la capa es muy pequeña, apenas de 100 micras, respecto de 550 micras en promedio obtenido con otros alcoholes con el mismo tiempo de proceso. La formación de hollín es despreciable y no hay formación de alquitrán.
Los alcoholes isopropílico, n-propílico y terbutanol presentan potenciales de carbono similares y profundidades de capa cercanas; se diferencian en su distinta capacidad de formación de hollín y alquitrán, donde el alcohol isopropílico forma más hollín y alquitrán, seguido por el tertbutanol y por último el n-propanol. De estos tres, el alcohol con mejores propiedades carburizantes fue el n-propanol.
El segundo ensayo con isopropanol presentó mayor potencial de carbono y mayor profundidad de capa debido al mayor tiempo a que fue sometido el acero en el proceso de carburización. A mayor tiempo de carburización la concentración superficial de carbono en el acero se acerca más a la concentración de la atmósfera.
El control de la atmósfera fue preciso y versátil, permitiendo manejar concentraciones para estos ensayos que variaron entre el 17% al 96% molar de alcohol en nitrógeno. El reactor es hermético; tiene un rango de temperaturas de trabajo desde 300 K a 1.273 K, y posee una zona isotérmica con una variación no mayor a 2 K., aunque los pequeños caudales que maneja el reactor, presentan flujo laminar dentro del horno generando perfiles radiales de concentración, lo que se evidenció en las probetas. La captura de subproductos fue posible y no se observa presencia de alquitranes en los gases después de atravesar los filtros.
Con los potenciales de carbono obtenidos en la mayoría de ensayos, el acero de bajo contenido de carbono, cuya constitución microscópica es ferrita con pequeñas cantidades de perlita, pasa a estar compuesto mayoritariamente en la superficie por perlita, Figura 2.
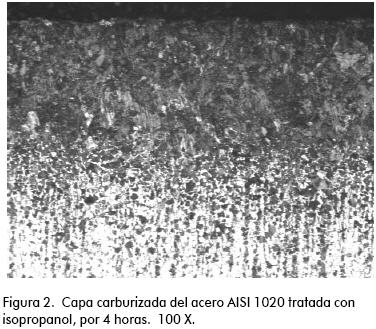
Conclusiones
El equipo tamaño laboratorio para tratamientos térmicos con atmósfera controlada presentó un buen desempeño y permitió obtener datos confiables y reproducibles, mostrando el gran potencial que posee, lo que permitirá realizar estudios profundos de los fenómenos relacionados con la carburización.
En los ensayos realizados con cada uno de los alcoholes, se encontró que:
El etanol es una sustancia que no carburiza, y en bajas concentraciones descarburiza el acero y fomenta la formación de hollín y alquitrán.
El metanol provee una atmósfera carburizante pero no penetra lo suficiente para formar capas profundas. Tiene la ventaja de no formar hollín ni alquitrán.
El alcohol n-propílico presenta buenos potenciales de carbono y una buena capa carburizada; sin embargo, fomenta la formación de cantidades considerables de hollín y de alquitrán, pero en menor magnitud que los alcoholes isopropílico y el tertbutílico
El alcohol isopropílico es una sustancia que provee un buen potencial de carbono y una capa carburizada importante, mas la cantidad de hollín y alquitrán formada es grande.
El alcohol tertbutílico provee una buena carburización con buen potencial de carbono y una capa carburizada importante aunque forma cantidades importantes de hollín y alquitrán.
Estos resultados son apenas una primera aproximación a los efectos que tiene cada uno de estos alcoholes en el proceso de carburización y por lo tanto se requiere profundizar en cada ensayo y formular mezclas entre ellos para mejorar las características finales del acero.
Los métodos utilizados pueden mejorarse para cuantificar el alquitrán y el hollín y con ello poder tener un balance de masa del carbono.
Agradecimientos
Agradecimientos especiales a la empresa Tratamientos Ferrotérmicos Ltda. por la financiación parcial de este trabajo y el apoyo económico que brindó al estudiante J. Obando durante la parte experimental, y a la Universidad Nacional, sin cuyos equipos de laboratorio hubiese sido imposible realizar esta investigación.
Bibliografía
Baldrich, R., Estudio experimental del proceso de cementación gaseosa por goteo de alcoholes Parte I., Trabajo de grado presentado a la Universidad Nacional de Colombia para optar al título de Ingeniero Mecánico, 1986. [ Links ]
Beguin, C., L’Utilisation du Méthanol Craqué Comme Atmosphère Protectrice., Traitament Thermique No. 154, 1981, pp. 53-60. [ Links ]
Bohórquez, C. A., Nitrocarburización austenítica de los aceros AISI 1020 y 8620. Universidad Nacional de Colombia, Tesis presentada a la Universidad Nacional de Colombia para optar al grado magister en materiales y procesos, 2001. [ Links ]
Darken, L. y Gurry R., Physical Chemistry of Metals., Mc Graw Hill, Japón, 1953, pp. 360363. [ Links ]
Holm, T., Synthetic Heat Treating Atmospheres., Advanced Materials & Processes, Vol. 10, 1989, pp. 45 47. [ Links ]
Lanham, M., NitrogenBase Atmospheres: Hardening at Alliedsignal, Advance Materials & Processes, No. 4, 1997, pp. 40 y 41z. [ Links ]
Main J. Production D’Atmosfhères de Traitement Thermique a Partir D’Alcohol. Traitement Thermique, 1980, pp. 39-43 [ Links ]
Meléndez, Córdoba, G., Comportamiento del proceso de Carbonitruración por Goteo de Alcoholes., Tesis presentada a la Universidad Nacional de Colombia para optar al grado de magister en materiales y procesos, 1993. [ Links ]
Nieto, A., Estudio experimental del proceso de cementación gaseosa por goteo de alcoholes Parte II., Trabajo de grado presentado a la Universidad Nacional de Colombia para optar al grado de Ingeniero mecánico, 1987. [ Links ]
Quijano, M, y Rodríguez J., Estudio cinético de la cementación gaseosa mediante alcoholes., Trabajo de grado presentado a la Universidad Nacional de Colombia para optar al grado de Ingeniero mecánico e Ingeniero químico, 1989. [ Links ]
Rodríguez, H. y Junca R., Estudio del proceso tecnológico de cementación por goteo., Trabajo de grado presentado a la Universidad Nacional de Colombia para optar al grado de ingeniero mecánico, 1984. [ Links ]
Slycke, J. and Sproge, L., Assessment of Nitrogen Based Atmospheres for Industrial Heat Treating., Journal Heat Treating, Vol. 5, No. 2, 1988, pp. 97 114. [ Links ]
Sullivan, J., Nitrogen Base Atmospheres: PSA Nitrogen in Heat Treating., Advanced materials & processes, No. 4, 1997, pp. 40U-40W. [ Links ]
Valencia, A., Tecnología del tratamiento térmico de los metales., Editorial Universidad de Antioquia, Medellín, Colombia, 1992, pp.332-363. [ Links ]
Vargas, C. y Fajardo, M., Utilización de la cromatografía de gases para el análisis de atmósferas en tratamientos térmicos., Trabajo de grado presentado a la Universidad Nacional de Colombia para optar al grado de Ingeniero mecánico e Ingeniero químico, 1997. [ Links ]
Wyss, U., Cémentation Avec Instillation de Liquides, Traitement Thermique, No. 139, 1979, pp. 47-53. [ Links ]
Wyss, U., DRIP Feed Carburizing., Metal Progress, noviembre, 1978 pp. 2431. [ Links ]
Wyss, U., Gas Carburizing by the Drip Feed Method in Switzerland., Metal progress, Enero, 1963, pp. 86-89. [ Links ]