Services on Demand
Journal
Article
Indicators
-
Cited by SciELO
-
Access statistics
Related links
-
Cited by Google
-
Similars in SciELO
-
Similars in Google
Share
Ingeniería e Investigación
Print version ISSN 0120-5609
Ing. Investig. vol.30 no.2 Bogotá May/Aug. 2010
Using spent fluid catalytic cracking (FCC) catalyst as pozzolanic addition - a review
Nancy Torres Castellanos1 and Janneth Torres Agredo2
1 Civil Engineer. M.Sc., in structures. Doctoral student in Science and Technology of Materials, Universidad Nacional de Colombia, Bogotá. Colombia. Professor, Escuela Colombiana de Ingeniería, Bogotá, Colombia. nancy.torres@escuelaing.edu.co. 2 Materials Engineer. Ph.D., in Engineering emphasis on matter-les Engineering.Grupo de Investigación Materiales y Medio Ambiente, GIMMA. Professor, Universidad Nacional de Colombia, Palmira, Colombia. jtorresa@unal.edu.co.
ABSTRACT
Spent fluid catalytic cracking (FCC) catalyst is an oil industry by-product from fluidised-bed catalytic cracking units. This residue is mainly formed by an active component (faujasite type zeolite Y) in an amorphous aluminosilicate matrix. It mainly consists of up to 90% silica and alumina. This paper reports an extensive literature review regarding the characterisation and mechanical and durability properties of mortar and concrete added to this material. FCC has been studied lately due to its pozzolanic characteristics and the good performance of concrete mixtures using FCC as cement replacement.
Keywords: Portland cement, additions, catalytic cracking residue, durability.
Received: jun 18th 2009
Accepted: jun 23th 2010
Introduction
Reinforced concrete is one of the most widely used materials today due to its numerous advantages. It has been concluded that the product most consumed by man, after water, is concrete by simple comparison between overall concrete production and the world's population (Fernández, 2002).
The main cementitious material is currently Portland cement; however,its production produces large amounts of greenhouse gas (Gartner, 2004). The emission of these gases can be decreased by reducing fuel consumption or reducing clinker production by incorporating mineral admixtures when manufacturing mortar or concrete (Price et al., 1999). It is thus a common practice to use additions to and replacement for cementitious material in mixtures which are usually by-products from other processes or natural materials.
The most noteworthy benefits obtained by using pozzolans are improved mechanical strength in mortars and concretes and increased durability (ACI 201, 2001). It is considered that using concrete lacking adding pozzolanic or cementitious materials will be an exception to the rule in the future (Malhotra and Mehta, 1996).
Using waste pozzolanic materials brings a double environmental benefit, first by replacing cement and other waste material consumption from other industrial processes and being stored in landfills when not used (Roskovic and Biegovic, 2005).
The pozzolans are classified according to their origin as being natural pozzolans (volcanic ash, volcanic tuff, zeolite, diatomaceous earth) and artificial pozzolans (fly ash, heat-activated clays, silica fume, etc.), (Taylor, 1967; Yu 2002; Xincheng, 1995). The use of other pozzolanic-based materials has been reported in recent years thereby improving the performance of the binders incurporated in it, as in the case of the catalyst used in fluid catalytic cracking (FCC) from the oil industry. It has been found that this material acts as a highly active pozzolan from the early curing times (Soriano, 2008; Payá et al., 2001; Antiohos, et al., 2006).
This article focuses on a description of catalyst waste (FCC) when it is used as a replacement for cementitious material. Its use is important from the environmental and economic perspective. As well as being an industrial waste, its inclusion in the mix as a replacement for cementitious material leads to the development of high performance concrete; hence its local and global interest.
Catalytic cracking residue
Catalytic cracking is a petrochemical process aimed at modifying the molecular structure of certain hydrocarbons, to obtain fuels for high quality engines, or to produce aromatic compounds as well as benzene and toluene from selected naphtha (Domon, 2007). The catalyst used for this cracking process is a material consisting of a type Y zeolite which is a microporous crystalline aluminosilicate consisting of tetrahedra [SiO4] 4- and [AlO4,]5-. The catalyst undergoes rigorous treatments in the regenerator during the catalytic cracking process which changes its behaviour, forming an amorphous material with consequent loss of activity for the cracking process (Agamez Pertuz et al., 2006). Some of these catalysts (ECAT) are removed in the cracking units as they present low activity and are replaced by new catalysts; the others (EPCAT) are collected in electrostatic precipitators (Garcia et al., 2006).
Studies on materials manufactured with this by-product have shown that they are not dangerous as they comply with environmental requirements (Furimsky, 1996, Nan Su et al., 2000).
Pozzolanic activity and mechanical properties
The following are the results of investigations characterising the residue and its inclusion as a replacement for cement to measure its reactivity.
Pacewska compared the lime fixation in several cement paste pozzolans,including FCC, silica fume (SF) and fly ash (FA) (Pacewska et al., 1998).
They concluded that setting time seemed to have been accelerate by the presence of pozzolans, especially FCC. They found that 28 days of curing fixed lime was similar for HS and FCC. Pastes having added FCC resistance showed improved mechanical strength after 7 days of curing, this being superior to the other pastes tested.
In a later study, Pacewska studied the influence of different percentages regarding FCC substitution for cement (Pacewska et al.,2000). They concluded that a small addition of FCC (5-10% cement substitution) acted as a system accelerator. However, higher additions of catalyst (over 10%) led to the heat released after 72 hours decreasing, probably because of smaller amounts of calcium silicate hydrate (CSH) phase being formed.
Studies have also been conducted on the influence of particle size from the two wastes generated in the process (EPCAT and ECAT). Pacewska concluded from calorimetry studies that if the substitution of cement by EPCAT was between 5%-10%, then the hydration process became accelerated, but heat released became decreased for percentages above 10% (Pacewska et al., 2002). Hydration heat was lower for samples with ECAT. They also found that the finer material (EPCAT) fixed more calcium hydroxide compared to ECAT.
Wang-Lung characterised EPCAT and studied lime fixation in pozzolan-added cement pastes (Wang-Lung et al., 2003). Following characterisation, the authors reported that the residue contained irregular shaped particles and were mainly composed of faujasite, silica, kaolinite and mullite. They concluded that lime fixation increased percentage EPCAT substitution. Similar results were found by Hsiu-Jung, Wu et al., (2003). Kung-Chung et al.,(2001) found that mortars containing this residue exhibited greater resistance to compression due to their high reactivity.
Yun-Sheng subjected the material to 650°C to increase ECAT reactivity (Yun-Sheng et al., 2005). The authors reported an increase in mechanical strength of between 8% and 18% for mortars and 7% and 11% in added concrete compared to reference samples.
Similarly, Nan Su studied EPCAT and ECAT properties (Nan Su et al,, 2000) and reported that mortars replaced by EPCAT (5% to 15%) showed greater resistance than mortars replaced with ECAT because EPCAT particles are much smaller than those of ECAT. The same conclusion was reached by Hsiu-Liang (Hsiu-Liang et al., 2004). Figures 1, 2, 3 and 4 show the morphology of the particles from these two residues and the crystalline phases presented by Xray diffraction test.
Pacewska has studied the benefits it can have on FCC milling (Pacewska et al., 2002 pp.133-142). The authors found that the pastes added to the catalyst powder consumed more calcium hydroxide (Ca(OH)2) than control sample and those added to the original catalyst. Other authors have recommended reducing FCC particle size to increase the compressive strength of mortars containing it (Payá J et al., 1999; Basaldella E et al., 2006; Pacewska B et al., 2002). Torres made a preliminary study of the pozzolanic activity of a catalyst residue from a Colombian petroleum industry (Torres et al., 2008, 2009). Compressive strength and lime consumption were measured.
The authors concluded that this material presented good reactivity,thereby making it suitable for producing pozzolan-added mortars and concretes.
Comparative studies have been conducted comparing FCC to metakaolin (MK). Payá found that FCC was similar to MK in both chemical composition and pozzolanic activity (Payá J et al., 2003).Cement pastes were compared, finding an optimum 15% to 20% level for cement replacement by FCC.
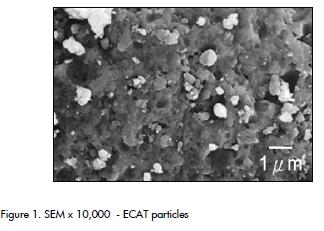
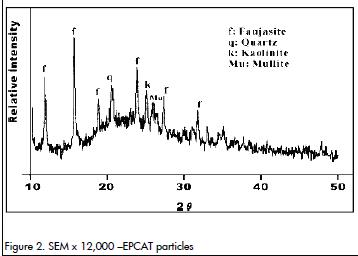
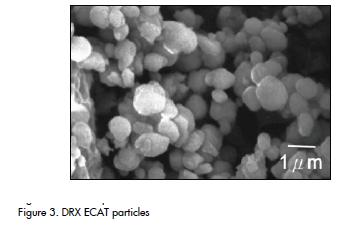
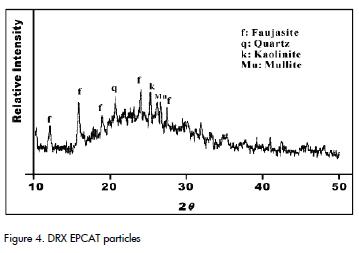
Payá has evaluated FCC pozzolanic activity involving the study of Ca(OH)2 fixation which included adding silica fume (SF) and MK for comparing this property (Payá et al., 2001). They concluded that FCC fixed 34% lime for early curing times, this information being very similar to that obtained with HS and very superior to that for MK.
In another study, Paya prepared samples of mortar for bending tests and compressive strength by adding FA, SF, FCC, rice husk ash (RHA) and sewage sludge ash (SSA) (Payá et al., 2002). The authors found that all the pozzolans (except FA) reduced the mortars'workability when they were replaced by 10% cement. They concluded that combining CV with another pozzolan improved mechanical resistance, especially to longer curing times (28-90 days). They also compared cementing efficiency factor values for pozzolans such as HS, RHA, MK and FCC; they arranged their reactivity in the following way: FCC> MK> RHA> SF.
In a later study, Paya evaluated the properties of mortars having FCC and adding alkali-resistant (AR) fibres (Payá et al., 2003). The authors concluded that incorporating FCC into mortars having AR fibres was positive since flexo-tensile strength was maintained, leading to a very considerable increase in compressive strength.
Additional studies have been carried out using pastes with lime to determine FCC reactivity. In yet a further study, Paya studied FCC pozzolanic activity in lime/catalyst pastes using different chemical activators (Payá et al., 2004). They found the following lime fixation order: NaOH <NaOH-gypsum <control <CaCl2<Na2SO4.The authors concluded that FCC was a very good pozzolan to include in lime pastes and mortars and that adding Na2SO4 or CaCl2 improves reactivity with lime. In a more recent study, Paya established the ideal FCC/cal ratio as being between 1:1 to 2:1 (Payá et al., 2007).
Replacing sand by FCC has also been studied. In this case (Nan et al., 2001), ECAT was used as sand replacement in mortars. It was found that for a 0.55 and 0.485 water/cementitious ratio it was possible to replace up to 10% of sand without reducing the mortar's compressive strength. Rattanasak came to the same conclusion (Rattanasak et al., 2001).
Hydrating FCC in Portland cement pastes
Different compositions of CSH, cal1cium aluminate hydrates (CAH) and calcium aluminosilicate hydrates (CASH) have been found to be the main hydration products for lime - catalyst systems (Payá et al., 2003), these being very similar products to those found in pastes containing MK. The same products appeared to be present in cement-FCC systems.
Borrachero evaluated the first 48 hours of treatment and the evolution of mechanical resistance of Portland cement with added ground FCC (Borrachero et al., 2002). The authors thought that FCC reactivity became raised and that the effects of pozzolanic type and acceleration in cement hydration were evident during very short curing times. Additional reports have stated that more CSH and less calcium hydroxide is formed in cement-FCC systems (Jung-Hsiu Wu et al., 2003; Pacewska et al., 2003).
Durability
Studies of the performance of concrete having added FCC and mortars' durability have been carried out regarding sulphate, carbonation and chloride attack.
Pacewska prepared mortars having 10% to 20% FCC cement substitution and submitted them to attack by sulphates and chlorides (Pacewska et al., 2000). They found that the effect of these two reagents was similar for the contact times studied and the chosen chloride and sulphate concentrations, a decrease being observed in compressive strength. Mortars containing 20% FCC practically did not seem to be affected by the aggressive attacks. Later (Pacewska et al., 2003), the same group concluded that chloride attack was more aggressive than sulphate attack for mortars having added FCC. Nevertheless, (Zornoza et al., 2009), another group suggested that the residue could be used in reinforced concrete structures exposed to chloride attack.
Bukowska evaluated sulphate action on mortars, replacing cement or sand with FCC (Bukowska et al., 2004). Regarding expansion study, they thought that major expansions occurred in mortars where surface pore structure had become degraded due to decomposition of the C-S-H phase. Studies have also been carried out on the behaviour of mortar having added FCC showing an opposite effect to that of assault by ammonium chloride, being proved favourable by the use of the residue (Girbés, 2004).
Piles studied the durability of lime, gypsum and gypsum-lime mortars having FCC and MK incorporation (Piles et al., 2005). They thought that adding pozzolans improved freeze-thaw cycle durability and attack by Na2SO4. The authors thus considered that manufacturing these compound materials was viable as restoration mortars.
Zornoza carried out accelerated carbonation tests, finding that when water/binder ratio was low, then carbonation rate in mortars became hardly noticeable and was not modified by the presence of the FCC (Zornoza et al., 2009). Nevertheless, carbonation rate increased when water/binder ratio was average or high.
Conclusions
FCC is a very active pozzolanic material, presenting high reactivity from early curing times. Incorporating this material into Portland cement mortars and concrete helps improve these materials' mechanical properties and durability.
Hydration products in cement pastes having added FCC were very similar to those produced in a cement-metakaolin system. CSS, CAH and CASH were amongst the mentioned reaction products; here, the mechanical behaviour of mortars having added FCC was similar to or even superior than ones having added MK.
The review presented here would suggest that if notice is taken of the results then this will contribute towards the conservation and preservation of the environment as well as obtaining better behaviour in Portland cement mortars and concrete having this added residue.
ACI Committee 201.2R-01., Guide to durable concrete., Report ACI 201R, American Concrete Institute, Detroit, EUA, 2001. [ Links ]
Agámez, P., Oviedo L., Navarro, U., Centeno, M., Odriozola, J., Análisis de la microporosidad de catalizadores de FCC., Rev. Acad. Colomb. Cienc., Vol. 30, No. 115, 2006, pp. 271-278. [ Links ]
Antiohos, S. K., Chouliar, E., Tsimas, S., Re-use of spent catalyst from oil-cracking refineries as supplementary cementing material., J. China Particuology, Vol.4, No. 2, 2006, pp. 73-76. [ Links ]
Basaldella, E., Paladino, J., Solari, M., Valle, G., Exhausted fluid catalytic cracking catalyst as raw materials for zeolite synthesis., Applied Catalysis, Vol. 66, 2006, pp. 186-191. [ Links ]
Borrachero, M., Monzó, J., Payá, J., Mora, Vunda, Velásquez, S., Soriano, L., El catalizador gastado de craqueo catalítico adicionado al cemento Pórtland: las primeras 48 horas de curado y la evolución de la resistencia mecánica., VIII Congreso Nacional de Propiedades Mecánicas de Sólidos, Gandia 2002. [ Links ]
Bukowska, M., Pacewska, B., Wilinska, I., Corrosion resistance of cement mortars containing spent catalyst of fluidized bed cracking (FBCC) as an additive., Thermal Analysis and Calorimetry, Vol. 74, 2003, pp. 931-942. [ Links ]
Bukowska, M., Pacewska B., Wilinska, I., Influence of spent catalyst used for catalytic cracking in a fluidized bed on sulphate corrosion of cement mortars I. Na2SO4 medium., Cement and Concrete Research, Vol. No 34, 2004, pp. 759-767. [ Links ]
Cheng, Y. C., Yu, C. C., Optimal region for design and control of ternary systems., AIChE J., Vol. 49, 2003, pp. 682-705. [ Links ]
Domone. P. L., A review of the hardened mechanical properties of selfcompacting concrete., Cement and Concrete Composites, Vol. 29, 2007, pp.1-12. [ Links ]
Elliot, T. R., Luyben, W. L., Quantitative assesment of controllability during the design of a ternary system with two recycle streams., Ind. Eng. Chem. Res., Vol. 35, 1996, pp. 3470-3479. [ Links ]
Fernández, M., Hormigón., Colegio de Ingenieros de Caminos, Canales y Puertos, Sexta edición, Enero, 2002. [ Links ]
Furimsky, E., Review of spent refinery catalyst: environment, safety and utilization., Catalysis Today, Vol. No.30, 1996, pp. 223-286. [ Links ]
García de Lomas, M., S. de Rojas, M., Frías, M., Comportamiento científico-técnico de los cementos Pórtland elaborados con catalizador FCC., Monografía No. 412, Instituto de Ciencias de la Construcción Eduardo Torroja, CSIC, 2006. [ Links ]
Gartner, E., Industrially Interesting Approaches to Low CO2 Cements., Cement and Concrete Research, Vol. 34, 2004, pp. 1489-1498. [ Links ]
Georgakis, C., On the use of extensive variables in process dynamics and control., Chem. Eng. Sci., Vol. 41, 1986, pp.1471-1484. [ Links ]
Girbés, I., Evaluación del uso de subproductos industriales de carácter puzolánico en conglomerantes de cemento Pórtland. Influencia de su utilización sobre la durabilidad de los materiales., tesis Doctoral, Universidad Politécnica de Valencia, Valencia, 2004. [ Links ]
Hsiu Liang, Ch., Tseng, Y., Hsu, K., Spent FCC catalyst as a pozzolanic material for high-performance mortars., Cement and Concrete Composites, Vol.26, 2004, pp. 657-664. [ Links ]
Hsu, K., Tseng, Y., Ku, F., Su, N., Oil cracking waste catalyst as an active pozzolanic material for superplasticized mortars., Cement and Concrete Research, Vol.31, 2001, pp. 1815-1820. [ Links ]
Jung-Hsiu, W., Wu, W., Hsu, K., The effect of waste oil-cracking catalyst on the compressive strength of cement pastes and mortars., Cement and Concrete Research, No. 33, 2003, pp. 245-253. [ Links ]
Malhotra, V. M, Metha, P. K., Pozzolanic and cementitious material., Gordon and Breach Publishers, Ottawa, 1996. [ Links ]
Monzó, J., Payá, J., Borrachero, M. V., Mora, E., Velázquez, S., Fluid Catalytic Cracking Residue (FC3R) as a New Pozzolanic Material: Thermal Analysis Monitoring of FC3R/Portland Cement Reactions, Seventh CANMET/ACI., International Conference on Fly Ash, Silica Fume, Slag and Natural Pozzolans in Concrete, Suplementary papers, India, Julio, 2001, pp. 22-27. [ Links ]
Pacewska, B., Wilinska, I., Kubissa, J., Use of spent catalyst from catalytic cracking in fluidized bed as a new concrete additive., Termochimica acta, No. 322, 1998, pp. 175-181. [ Links ]
Pacewska, B., Wilinska, I., Bukowska, M., Hydration of cement slurry in the presence of spent cracking catalyst., Thermal Analysis and Calorimetry, No. 60, 2000, pp. 71-78. [ Links ]
Pacewska, B., Wilinska, I., Bukowska, M., Nocún, W., Effect of waste aluminosilicate material on cement hydration and properties of cement mortar., Cement and Concrete Research, No, 32, 2002, pp. 1823-1830. [ Links ]
Pacewska, B., Wilinska, I., Bukowska, M., Blonkowski, G., An attempt to improve the pozzolanic activity of waste aluminoslicate catalyst., Thermal Analysis and Calorimetry, No. 77, 2002, pp. 133-142. [ Links ]
Pacewska, B., Burowska, M., Ska, I., Swat, M., Modification of properties of concrete by a new pozzolan a waste catalyst from the catalytic process in a fluidized bed., Cement and Concrete Research, Vol. 32, 2002, pp. 145-152. [ Links ]
Pacewska B., Bukowska, M., Wilinska, I., Influence of some aggressive media on corrosion resistance of mortars with spent cracking catalyst., Thermal Analysis and Calorimetry, Vol. 60, 2000, pp. 257-264. [ Links ]
Payá, J., Monzó, J., Borrachero, M., Fluid catalytic cracking catalyst residue (FC3R) an excellent mineral by-product for improving early strength development of cement mixtures., Cement and Concrete Research, Vol. 29, 1999, pp.1773-1779. [ Links ]
Payá, J., Monzó, J., Borrachero, M., Physical, chemical and mechanical properties of fluid catalytic cracking catalyst residue (FC3R) blended cements., Cement and concrete research, Vol. 31, 2001, pp. 57-61. [ Links ]
Payá, J., Monzó, J., Borrachero, M., Velázquez, S., Evaluation of the pozzolanic activity of fluid catalytic cracking catalyst residue (FC3R), Thermogravimetric analysis studies on FC3R-Portland cement pastes., Cement and Concrete Research, No. 33, 2003. pp. 603-609. [ Links ]
Payá, J., Monzó, J., Borrachero, M., Amahjour, F., Girbés, I., Velázquez, S., Ordóñez, L., Advantages in the use of fly ashes in cements containig pozzolanic combustion residues: silica fume, sewage sludge ash, spent fluidized bed catalyst and rice husk ash., Chemical Technology and Biotechnology, No. 77, 2002, pp. 331-335. [ Links ]
Payá, J., Borrachero, M., Monzó, J., Bonilla, M., León, C., Soriano, L., Morteros de cemento compuestos con fibras AR y puzolana procedente de catalizadores FCC usados., V Congreso Nacional de Materiales Compuestos, AEMAC 2003, Asociación Española de Materiales Compuestos, Zaragoza, Junio, 2003. [ Links ]
Payá, J., Monzó, J., Borrachero, M., Velázquez, S., Bonilla, M., Determination of the pozzolanic activity of fluid catalytic cracking residue. Thermogravimetric analysis studies on FC3R- lime pastes, Cement and Concrete Research, No. 33, 2003, pp. 1085-1091. [ Links ]
Payá, J., Monzó, J., Borrachero, M., Velázquez, S., Chemical activation of pozzolanic reaction of fluid catalytic cracking residue (FC3R) in lime pastes: thermal analysis., Advances in Cement Research, No. 19, 2004, pp. 123-130. [ Links ]
Payá, J., Monzó, J., Borrachero, M., Velázquez, S., The chemical activation of pozzolanic reaction of fluid catalytic cracking catalyst residue (FC3R) in lime pastes., Advances in Cement Research, No. 19, 2007, pp. 9-16. [ Links ]
Payá, J., Monzó, J., Borrachero, M., Serna, P., Velázquez, S., Ordonez, L. M., El factor de eficacia cementante de puzolanas síliceas y silicoaluminosas muy reactivas., VII congreso Nacional de Propiedades Mecánicas de Sólidos, Gandia, 2002, pp. 591- 600. [ Links ]
Piles, V., Borrachero, M., Payá, J., Monzó, J., Codoñer, A., Ensayos de envejecimiento acelerado sobre materiales compuestos con base de cal o con base mixta de cal y yeso., VI Congreso Nacional de Materiales Compuestos, AEMAC 2005, Asociación Española de Materiales Compuestos, Valencia, Junio, 2005, pp. 947-954. [ Links ]
Price, L., Worrell, E., Phylipsen, D., Energy Use and Carbon Dioxide Emissions in Energy-Intensive Industries in Key developing Countries., Proceedings of the 1990 Earth Technologies Forum, Washington, DC, September, 1999, pp.27-29. [ Links ]
Rattanasak, U., Jaturapitakkul, C., Sudaprasert, T., Compressive strength and heavy metal leaching behaviour of mortars containing spent catalyst., Waste Management & Research, No. 19, 2001, pp.456-464. [ Links ]
Roskovic, R, Bjegovic, D., Role of mineral additions in reducing CO2 emission., Cement and Concrete Research, Vol. 35, 2005, pp. 974-978. [ Links ]
Su, N., Chen, Z., Fang, H., Reuse of spent catalyst as fine aggregate in cement mortar., Cement and concrete composites, Vol. No. 23, 2001, pp. 111-118. [ Links ]
Su, N, Fang, H., Chen, Z., Liu, F., Reuse of waste catalysts from petrochemical industries for cement substitution., Cement and Concrete Research, Vol. No. 30, 2000, pp. 1773-1783. [ Links ]
Soriano, M. L., Nuevas aportaciones en el desarrollo de materiales cementantes con residuo de catalizador de craqueo catalítico (FCC)., Tesis presentada a la Universidad Politécnica de Valencia, para optar al grado de Doctor, 2008. [ Links ]
Taylor, H. F. W., Enciclopedia de la química industrial, La Química de los Cementos., Traducción de F. Romero Rossi, Escuela de Ingenieros Industriales de Bilbao, Universidad de Deusto. Ediciones URMO, Bilbao, España,1967. [ Links ]
Torres, J., Baquero, E., Silva, A., Evaluación de la actividad puzolánica de un residuo de un residuo de la industria del petróleo., Revista Dyna, Año. 76, No. 158, 2009, pp. 49-53. [ Links ]
Torres, J., Baquero, E., Silva, A., Mejía, R., Estudio del desempeño puzolánico de un residuo de la industrial del petróleo., Memorias Tenth International confrence on non-conventional materials and technologies, NOCMAT 2008, Cali, Universidad del Valle, Noviembre, 2008, Cali, Colombia, 12-14 Noviembre, 2008. [ Links ]
Tseng, Y., Huang, Ch., Hsu, K., The pozzolanic activity of a calcined waste FCC catalyst and its effect on the compressive strength of cementitious materials., Cement and Concrete Research, Vol. 32, 2005, pp. 782-787. [ Links ]
Wan-Lung, W., Jung-Hsiu, W., Kung-Chung, H., Subproductos del fraccionamiento catalítico del petróleo: características, actividad puzolánica y su efecto en las propiedades del mortero., Cemento Hormigón, No. 850, Junio, 2003, pp. 18-25. [ Links ]
Xincheng, P., Investigation on pozzolanic effect of mineral additives in cement and concrete by specific strength index., Cement and Concrete Research, 1995. [ Links ]
Yu, L. H., Ou, H., Lee, L. L., Investigation on pozzolanic effect of perlite powder in concrete., Cement and Concrete Research, Vol. 33, 2003, pp. 73-76. [ Links ]
Zornoza, E., Garcés, P., Monzó, J., Borrachero, M. V., Payá, J., Accelerated carbonation of cement pastes partially substituid with fluid catalytic cracking catalyst residue (FC3R)., Cement and Concrete Composites, Vol. 31, 2009, pp. 134-138. [ Links ]
Zornoza, E., Payá, J., Monzó, J., Borrachero, M. V., Garcés, P., The Carbonation of OPC mortars partially substituted with spent fluid catalytic catalyst (FC3R) and its influence on their mechanical properties., Construction and Building Materials, Vol. 23, 2009, pp. 1323-1328. [ Links ]
Zornoza, E., Garcés, P., Payá, J., Climent, M. A., Improvement of the chloride ingress resistance of OPC mortars by using spent cracking catalyst., Cement and Concrete Research, Vol. 39, 2009, pp. 126-139. [ Links ]