Services on Demand
Journal
Article
Indicators
-
Cited by SciELO
-
Access statistics
Related links
-
Cited by Google
-
Similars in SciELO
-
Similars in Google
Share
Ingeniería e Investigación
Print version ISSN 0120-5609
Ing. Investig. vol.30 no.2 Bogotá May/Aug. 2010
Two-phase kinetic model for epoxidation of soybean oil
Ángela Aurora Beltrán Osuna1 and Luis Alejandro Boyacá Mendivelso2
1 Chemical Engineer. M.Sc., in Chemical Engineering, Universidad Nacional de Colombia, Bogotá, Colombia. aabeltrano@unal.edu.co 2 Chemical Engineer. M.Sc.,in Chemical Engineering. Professor, School of Engineering, Universidad Nacional de Colombia, Bogotá, Colombia. laboyacam@unal.edu.co
Abstract
A two-phase kinetic model was implemented for analysing conventional epoxidation, using a percarboxylic acid generated in situ through adding hydrogen peroxide in a two-phase system having a homogeneous catalyst. Data was adjusted using the least square method (0.88 correlation coefficient). The simulation closely predicted oxirane oxygen content values, especially during the first stage of reaction and deviation at the end of epoxidation due, possibly, to different degradation reactions.
Key words: in situ epoxidation, oxirane ring-opening reaction, two-phase kinetic model.
Received: jan 30th 2009 Accepted: feb 20th 2010
Introduction
Conventional epoxidation of vegetables oils is usually carried out in a two-phase system, using a homogeneous catalyst (Figure 1). Peracetic acid (PAA) is frequently generated in situ in the aqueous phase by adding hydrogen peroxide and a carboxylic acid (acetic acid, AA). PAA has to become diffused to organic phase where epoxidation reactions take place and then multiple degradation reactions are present, due to oxirane ring reactivity. The limiting step in the kinetic scheme is the formation of PAA (Rangarajan et al., 1995) raising times significantly. Reaction conditions have to be chosen to reach maximum conversion (epoxy yield), especially if the product is to be used for further chemical transformations (Petrović et al., 2002).
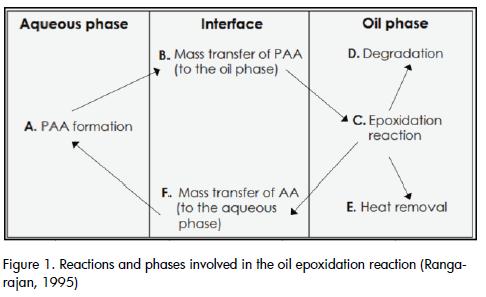
The pertinent literature has described a wide variety of reactions which the oxirane ring could undergo (Campanella and Baltanás, 2004, 2005, 2006) (Petrović et al., 2002). Many authors have obtained the kinetic constants, heat and mass transfer coefficients and activation energies for all the reactions involved for different kinetic models (Kuo and Chou, 1987) (Musante et al., 2000) (Rangarajan et al., 1995) (Sinadinović-Fier et al., 2001). These studies have taken the nature of the catalyser, the solubility of the species in each phase and diffusional issues into account, depending on the system being considered. Only a few papers have centred on epoxidation kinetics: with various vegetable oils (Cai Chuanshang et al., 2008), some soybean oil derivatives (Campanella A. et al., 2008) and using ion-exchange resins (Goud Vaibhav V. et al., 2007).
Epoxidation kinetics
A two-phase kinetic model is used for correlating the results obtained from our epoxidation tests, taking advantage of the information available in the literature. Other kinetic models have been successfully evaluated by other authors (Benavides, 2006) (Rangarajan et al., 1995) for similar systems and different vegetable oils. This model, unlike the pseudo-homogeneous model, takes the heat and mass transfer phenomena inherent in this system into account. The stages of the reaction scheme (Figure 2)included:
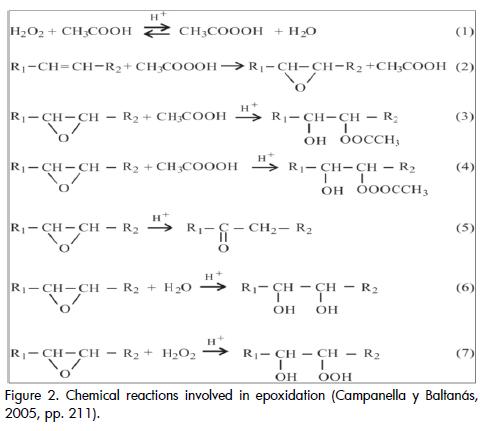
I. Peracetic acid formation in aqueous phase, catalysed by sulphuric acid: reaction (1);
II. Peracetic acid specie transfer from aqueous to organic phase;
III. Peracetic acid reaction with the unsaturated bonds of the oil to generate an oxirane ring and acetic acid: reaction (2);
IV.Oxyrane ring degradation due to reactions with acetic acid, water and/or hydrogen peroxide, catalysed in acid medium: reactions (3)(4)(5)(6)(7); and Acetic acid transfer from organic to aqueous phase to reinitiate the first step.
The following section gives the mass balance equations for each phase and for all reactive species in the reaction medium (Appendix, Table 3).
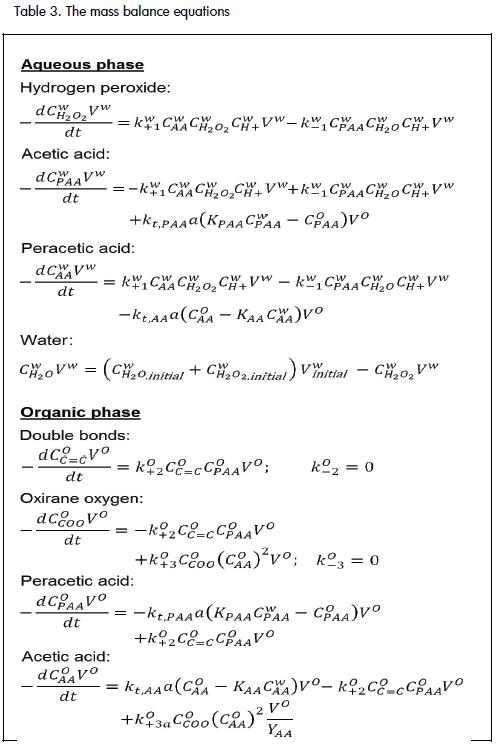
The kinetic model used local concentrations in each phase (moles of the specie in one phase, divided by that phase's total volume) because the reaction took place in a specific phase. Kinetic constants were thus based on local concentrations and individual volumes for each phase (Rangarajan et al., 1995).
The model's assumptions were: 1) Each phase's volume remains constant during the reaction; 2)Reactions occurred within the phase (away from the interface); 3) Heat transfer phenomena were neglected; 4) Acetic and peracetic species, CH3COOOH and CH3COOH, were in both phases but hydrogen peroxide, sulphuric acid and water (H2O2, H2SO4H2O) were insoluble in organic phase; 5) Due to triglyceride insolubility in aqueous phase, all opening-ring reactions took place in organic phase;6) There was only one degradation reaction due to carboxylic acid (Figure 2, reactions 3-7), requiring the use of a yield coefficient, 1/YAA (Rangarajan et al., 1995). 7) Equality between transfer coefficients for acetic and peracetic acid species was assumed (kt,PAA= kt,AA) for a system with no mass transfer limitation; and 8) The catalyst was completely added at the beginning of the reaction time.
Total volume for the system and individual volume for each phase was assumed to remain constant because epoxidised soybean oil (ESBO) density is very similar to that of the subproducts obtained (in degradation reactions) and the polar reagents' molar excess (Campanella and Baltanás, 2006).
Mass balance and all assumptions made were validated by searching the pertinent literature:
-Oxirane ring degradation with solvated acetic acid (in organic phase) using sulphuric acid as homogeneous catalyst has been widely studied (Gan et al., 1992) (Zaher et al., 1989). It has been found to be a first-order reaction regarding epoxide and second-order regarding carboxylic acid concentration. Degradation increases proportionally with the concentration of protons from the catalyst (Campanella and Baltanás, 2005);
-The reaction regime under which the main degradations occurred has been already studied in depth for epoxidation, independently considering transport phenomena and the reactions' intrinsic kinetics (Campanella and Baltanás, 2006). It was concluded that oxirane ring hydrolysis due to acetic acid was not significant in the absence of catalyser. The reaction proceeded immediately in the presence of sulphuric acid, the whole process being controlled by mass transfer;
-Other studies have been concerned with oxirane ring degradation due to peracetic acid. Although specific peracetic acid attack on the ring is 10 times more intense than that due to acetic acid, the latter is constantly regenerated during epoxidation. Acetic acid concentration is thus always higher than that of peracetic acid. Therefore, in conventional high scale conditions, oxirane ring degradation is mostly due to carboxylic acid (Campanella and Baltanás, 2005).
-Oxirane ring degradation due to hydrogen peroxide is minimum in conventional reaction conditions for in situ production (T=60°C, 1:1.1:0.5 molar ratios between C=C/H2O2/CH3COOH and [H2O2]= 50% p/p maximum) (Campanella and Baltanás, 2005). It can also be assumed that the reaction take place during aqueous phase (where H2O2 is present), because of the low solubility of the epoxidised specie in water (although the actual reaction takes place in the interface) (Campanella and Baltanás, 2006); and Epoxide hydrolysis occurs at extremely low speed and requires the presence of an acid catalyst to proceed at a significant velocity during the interphase, besides long induction periods (higher than those during conventional high scale epoxidation production).
Experimental
Materials
Commercial soybean oil (Sigra SA) was used for epoxidation, with glacial acetic acid, hydrogen peroxide (50% p/p) and sulphuric acid (96% p/p), all analytic reagents provided by Merck SA. The experimental setup included a jacket glass reactor (500 mL) with mechanical stirring and openings for taking samples, adding reagent and coupling a glass condenser (to prevent any escape of vapours).
The following were also needed: a peristaltic pump, a submersible copper coil (for cooling), a 4 paddle-blade stainless steel stir and a mechanical stirrer (100-2,000 rpm speed range). Reaction progress was determined by following oxirane oxygen content (norm NTC 2366) using a centrifuge (6 tubes).
Methods
Soybean oil was added to the reactor and the temperature was raised. Acetic acid was then added and the temperature stabilised. The reaction time started by adding the catalyst solution (previously prepared by dissolving sulphuric acid to a hydrogen peroxide solution) into the system reactor during the first 10 minutes (8.8 mL/min). The system remained isothermal. Some samples were taken to determine the reaction's advance. Once the sample was taken out of the reactor, it was washed 4 times with cold water and then centrifuged for 20 minutes at 3,200 rpm. The detailed methodology has been shown in a previous study (Boyacá LA and Beltrán AA, 2010).
Results
Table 1 shows the oxirane oxygen content (OOC) and the time required to reach maximum value for 16 epoxidation tests. Hydrogen peroxide, acetic and sulphuric acid temperature and concentrations were changed at two levels for each variable.
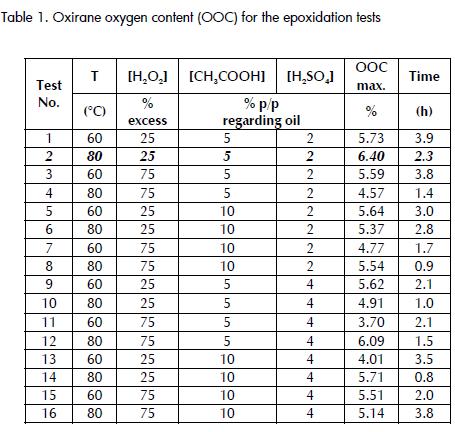
Balance equations for each reactive species constituted a system of differential equations which can be resolved with the values for the initial conditions (volume and concentration). The concentration of all species was obtained. Matlab 5.3 software was used for model resolution with the ode45' tool which uses a Runge-Kutta fourth-order method. The kinetic parameters used have been reported in the literature (Table 2).
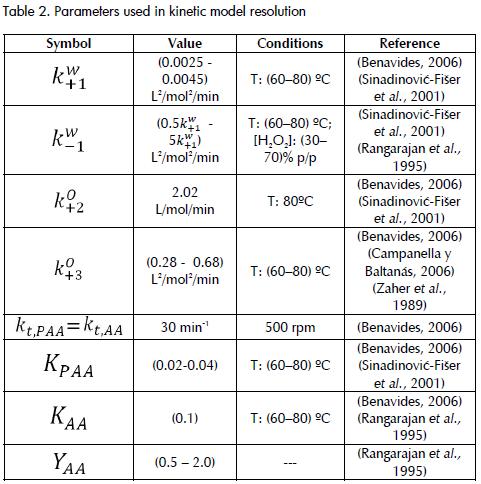
Oxirane oxygen content (OOC), defined as grams of oxirane oxygen per 100 grams of epoxide, was calculated from the specie's molar concentration. The profiles given in Figure 3. were thus obtained. The yield coefficient (YAA) was the only parameter used for adjusting the model to the experimental data (0.88 correlation coefficient using the least squares method).
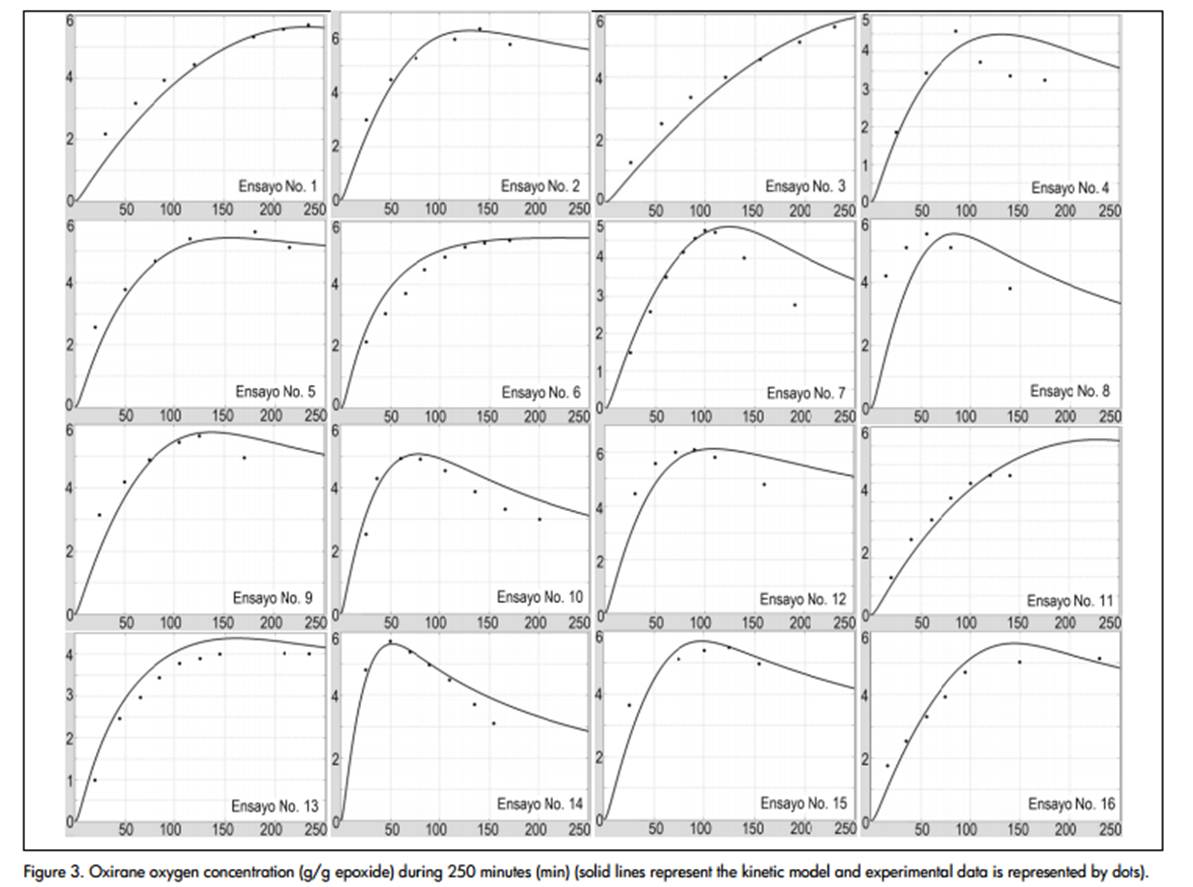
The model correctly predicted reaction kinetics when oxygen concentration was increasing; when it reached the maximum value, the predicted profile tended to veer away from experimental data, showing that degradation kinetics are not properly represented by the proposed model. Some tests predicted higher initial velocity, even when one of the model's limitations was the assumption of complete catalyst addition at the beginning of a reaction.
There were different reasons for curves deviating from the actual data, all related to the assumptions made for the model's resolution. First, acetic and peracetic acid mass transfer coefficients (kt,PAA= kt,AA) were equalised because of the lack of information; this had no theoretical basis, it was only supposed that the system was not controlled by mass transfer for "enough high values" of such coefficients (Rangarajan et al., 1995); however, concentration profiles were not significantly affected when 1030 min-1 values were used (Table 2).. No judicious research could be found determining mass transfer coefficients or interfacial area values for this system. The effect of agitation on reaction kinetics was also neglected and few studies have reported any analysis of this variable. Some authors have even asserted the lack of mass transfer limitations due to the small variations of OOC values using different speed levels in mechanical stirring (Benavides, 2006). On the other hand, the equilibrium constant for in situ peracetic acid formation reaction (in aqueous phase) from acetic acid was given by the following expression K1W=(k+1W))/(k-1W)=(CPWCH20W)/(CAWCH2O2W).
This constant was experimentally calculated from determining kinetic values in the forward (k+1W) and inverse reaction (k-1W). The value of K1W ranged from 0.7 to 5 depending on molar ratios between reactants and peroxide and sulphuric acid concentration. It has thus not been clearly explained why such constant depends on other variables besides temperature. The value of the equilibrium can be most conveniently calculated from its dependence on temperature, rather than from some experimental data (Janković and Sinadinović-Fier, 2005).
Regarding the catalyst, a more evident study of oxirane ring degradation due to sulphuric acid is necessary by using thermodynamic analysis to determine conditions favouring or hindering undesirable collateral reactions. This kind of study should be able to clarify the mechanism of reaction for this specific system, thereby improving the proposed model's precision. So, if degradation reactions are catalysed at low pH and there are three kinds of acids in a particular system (acetic, peracetic and sulphuric), strictly speaking it cannot be assumed that catalyst action is only due to the H+ protons from the sulphuric acid; it should not be any other way though because sulphuric acid has the highest ionic force. Additionally, if this is an interfacial reaction, then it should be evaluated in interface conditions and not using catalyst bulk-fluid concentration (validating the assumption of equality between bulk and interfacial concentrations for the species). Another possible reason the model's deviation from experimental data was oxirane ring degradation by acetic acid. Although this was the main degradation reaction and it has been studied in depth, there were discrepancies in kinetic constant value, thereby changing many orders of magnitude depending on which phase the reaction was taking place in (Campanella and Baltanás, 2005, 2006). The model must thus be corrected by using reliable experimental data to obtain accurate values about the diffusion coefficients and interfacial area for both phases, such information being required for complete modelling of the system.
The oxirane oxygen concentration profiles shown (Figure 3) were similar to those obtained in other studies (Cai Chuanshang et al., 2008). However, those authors obtained a 6.1% OOC maximum value at T=75°C in 4 hours (reagent concentrations were not reported but can be obtained approximately as being [H2O2] = 89% molar excess and [CH3COOH] = 23% p/p, assuming a 130 g iodine value for I2/100 g of soybean oil). This result contrasted with the value obtained in this study where the best result (test No. 2) was 6.4% for maximum oxirane oxygen content, at T=80°C and 2.3 hours, having lower reagent concentrations ([H2O2] = 25% molar excess and [CH3COOH] = 5% p/p) thereby highlighting the importance of this kind of kinetic model for optimising the epoxidation reaction (Boyacá L.A. and Beltrán A.A., 2010).
Conclusions
The two-phase kinetic model proposed for epoxidation reaction successfully represents the experimental data for the reaction's first stage (during oxirane ring formation), having a 0.88 correlation coefficient. However, a deeper study is required to obtain more information about oxirane ring degradation reactions and, therefore, obtain correct predictions for the oxirane oxygen content values. A complete thermodynamic analysis should be able to point to the reaction conditions favouring or hampering multiple collateral reactions. The kinetic constants involved should be determined with higher precision to ensure obtaining values for a wider range of reagent concentrations. Mass transfer phenomena must be studied in detail to obtain accurate coefficient and interfacial area values for the system. Stirring speed can be included in the study variables to ensure a whole set of optimised reaction conditions.
Acknowledgments
This work was supported by the Bogotá Research Division (DIB) and the Engineering Faculty's "Programa Semilleros de Investigación," Universidad Nacional de Colombia, Bogotá.
Appendix
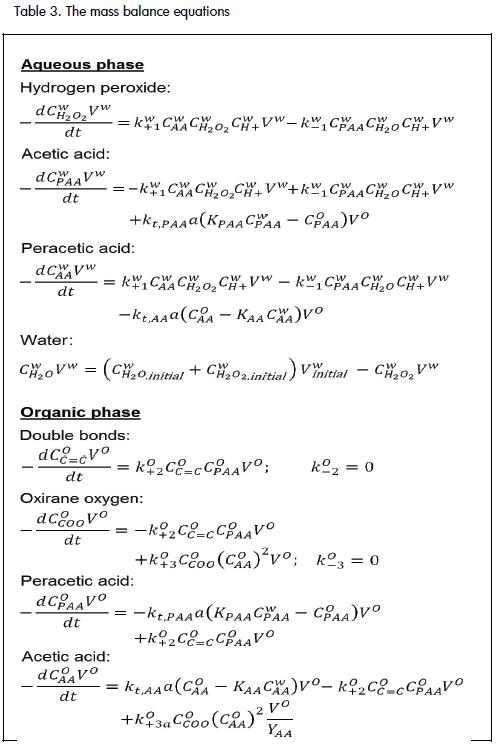
Boyacá, L. A., Beltrán A. A., Producción de epóxido de soya con ácido peracético generado in situ mediante catálisis homogénea., Ingeniería e Investigación, Vol. 30, No.1, 2010, pp. 136-140. [ Links ]
Benavides, R. E., Evaluación de la producción de polioles poliéster a partir de aceite de palma., Tesis presentada a la Universidad Nacional de Colombia para optar al título de Magíster en Ingeniería Química, 2006. [ Links ]
Campanella, A., Fontaninia, C., Baltanás, M. A., High yield epoxidation of fatty acid methyl esters with performic acid generated in situ., Chemical Engineering Journal, Vol. 144, 2008, pp. 466-475. [ Links ]
Campanella, A., Baltanás, M. A., Degradation of the oxirane ring of epoxidized vegetable oils in a liquid-liquid-solid heterogeneous reaction system., Chemical Engineering and Processing, Vol. 46, 2007, pp. 210-221. [ Links ]
Campanella, A., Baltanás, M. A., Degradation of the oxirane ring of epoxidized vegetable oils in a liquid-liquid heterogeneous reaction systems., Chemical Engineering Journal, Vol. 118, 2006, pp. 141-152. [ Links ]
Campanella, A., Baltanás, M. A, Degradation of the oxirane ring of epoxidized vegetable oils with hydrogen peroxide using an ion exchange resin., Catalysis Today, Vol. 107-108, 2005, pp. 208-214. [ Links ]
Campanella, A., Baltanás, M. A., Degradation of the oxirane ring of epoxidized vegetable oils in liquid-liquid systems: I. Hydrolysis and attack by H2O2., Latin American Applied Research, Vol. 35, 2005, pp. 205-210. [ Links ]
Campanella, A., Baltanás, M. A., Degradation of the oxirane ring of epoxidized vegetable oils in liquid-liquid systems: II. Reactivity with solvated acetic and peracetic acids., Latin American Applied Research, Vol. 35, 2005, pp. 211-216. [ Links ]
Campanella, A., Baltanás, M. A, Degradation of the oxirane ring of epoxidized vegetable oils with solvated acetic using cation exchange resins., European Journal of Lipid Science and Technology, Vol. 106, 2004, pp. 524-530. [ Links ]
Gan, L. H., Goh, S. H., Ooi, K. S., Kinetic studies of epoxidation and oxirane cleavage of palm olein methyl esters., Journal of the American Oil Chemists' Society, Vol. 69, No. 4, 1992, pp. 347-351. [ Links ]
Goud, V, V., Patwardhan, A. V., Dinda, S., Pradhan, N. C., Epoxidation of karanja (Pongamia glabra) oil catalysed by acidic ion exchange resin., European Journal of Lipid Science and Technology, Vol. 109, 2007, pp. 575-584. [ Links ]
Jankovic, M., Sinadinovic-Fiser, S., Prediction of the chemical equilibrium constant for peracetic acid formation by hydrogen peroxide., Journal of the American Oils Chemists' Society, Vol. 82, No. 4, 2005, pp. 301-301. [ Links ]
Kuo, M-C., Chou, T-C., Kinetics and mechanism of the catalyzed epoxidation of oleic acid with oxygen in the presence of benzaldehyde., Industrial and Engineering Chemistry Research, Vol. 26, 1987, pp. 277-284. [ Links ]
Musante, R. L., Grau, R. J., Ba1tanás, M. A., Kinetic of liquid phase reactions catalyzed by acidic resins: the formation of peracetic acid for vegetable oil epoxidation., Applied Catalysis A: General, Vol. 197, 2000, pp. 165-173. [ Links ]
Petrovic, Z. S., Zlatanic, A., Lava, C. C., Sinadinovic-Fiser, S., Epoxidation of soybean oil in toluene with peroxoacetic and peroxoformic acids kinetics and side reactions., European Journal of Lipid Science and Technology, Vol. 104, 2002, pp. 293-299. [ Links ]
Rangarajan, B., Havey, A., Grulke, E. A., Culnan, P. D., Kinetic parameters of a two-phase model for in situ epoxidation of soybean oil., Journal of the American Oils Chemists' Society, Vol. 2, No. 10, 1995, pp. 1161-1169. [ Links ]
Sinadinovic-Fiser, S., Jankovic, M., Petrovic, Z. S., Kinetics of in situ epoxidation of soybean oil in bulk catalyzed by ion exchange resin., Journal of the American Oils Chemists' Society, Vol. 78, No. 7, 2001, pp. 725-731. [ Links ]
Zaher, F.A., El-Mallah, M. H., El-Hefnawy, M. M., Kinetics of oxirane cleavage in epoxidized soybean oil., Journal of the American Oils Chemists' Society, Vol. 66, No. 5, 1989, pp. 698-700. [ Links ]