Services on Demand
Journal
Article
Indicators
-
Cited by SciELO
-
Access statistics
Related links
-
Cited by Google
-
Similars in SciELO
-
Similars in Google
Share
Ingeniería e Investigación
Print version ISSN 0120-5609
Ing. Investig. vol.30 no.2 Bogotá May/Aug. 2010
Ángela Aurora Beltrán Osuna1y Luis Alejandro Boyacá Mendivelso2
1 Ingeniera Química. M.Sc., en Ingeniería Química, Universidad Nacional de Colombia, Bogotá, Colombia. aabeltrano@unal.edu.co 2 Ingeniera Química. M.Sc., en Ingeniería Química. Profesor, Facultad de Ingeniería, Universidad Nacional de Colombia, Bogotá, Colombia. laboyacam@unal.edu.co
RESUMEN
Se implementa un modelo cinético de dos fases para el análisis de un proceso convencional de epoxidación, utilizando un ácido percarboxílico generado in situ mediante la adición de peróxido de hidrógeno, en un sistema de dos fases usando un catalizador homogéneo. Los datos obtenidos se ajustan mediante el método de mínimos cuadrados (obteniendo un coeficiente de correlación de 0,88). En general, la simulación predice cercanamente los valores de contenido de oxígeno oxirano, en especial durante la primera etapa de reacción, y una desviación hacia el final de la epoxidación debida posiblemente a las múltiples reacciones de degradación.
Palabras clave: epoxidación in situ, apertura del anillo oxirano, modelo cinético de dos fases.
ABSTRACT
A two-phase kinetic model was implemented for analysing conventional epoxidation, using a percarboxylic acid generated in situ through adding hydrogen peroxide in a two phase system having a homogeneous catalyst. Data was adjusted using the least square method (0.88 correlation coefficient). The simulation closely predicted oxirane oxygen content values, especially during the first stage of reaction and deviation at the end of epoxidation due, possibly, to different degradation reactions.Keywords: in situ epoxidation, oxirane ring-opening reaction, two-phase kinetic model.
Recibido: enero 30 de 2009 Aceptado: febrero 20 de 2010
Introducción
La epoxidación convencional de aceites vegetales por medio de catálisis homogénea se lleva a cabo en un sistema de dos fases (Figura 1). Mediante la adición de peróxido de hidrógeno y un ácido carboxílico, comúnmente ácido acético (AA), se genera el perácido (PAA) en la fase acuosa. Esta especie debe transferirse hacia la fase orgánica, donde toma lugar la reacción de epoxidación luego de lo cual, debido a la reactividad del anillo oxirano, pueden presentarse múltiples reacciones de degradación. El paso limitante en la cinética de reacción es la formación del PAA (Rangarajan et al., 1995) lo que aumenta significativamente los tiempos de reacción. Las condiciones de reacción deben ser escogidas con el fin de alcanzar el máximo rendimiento hacia epóxido, especialmente si el producto va a ser utilizado en posteriores transformaciones químicas, evitando separaciones de los subproductos (Petrovic et al., 2002).
En la literatura se describe la existencia de gran variedad de reacciones que puede sufrir el anillo oxirano (Campanella y Baltanás, 2004, 2005, 2006; Petrovic et al., 2002). Diferentes estudios de degradación del grupo oxirano buscan obtener las constantes cinéticas, los coeficientes de transferencia de masa y las energías de activación correspondientes a las reacciones involucradas, para proponer diferentes modelos cinéticos (Sinadinovic -Fišer et al., 2001; Kuo y Chou, 1987; Musante et al., 2000; Rangarajan et al., 1995;), teniendo en cuenta el tipo de catalizador, la solubilidad de las especies presentes en cada una de las fases y los problemas difusionales propios del sistema en consideración. Recientemente, sólo unos estudios se han centrado en la cinética de epoxidación: con varios aceites vegetales (Cai Chuanshang et al., 2008), diferentes derivados del aceite de soya (Campanella A. et al., 2008), y uso de resinas de intercambio iónico (Goud Vaibhav V. et al., 2007).
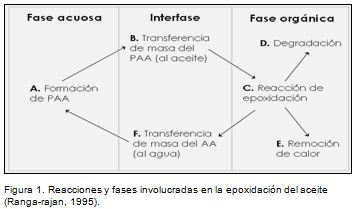
Cinética de epoxidación
Aprovechando la información disponible en la literatura se utiliza un modelo cinético de dos fases para correlacionar los resultados obtenidos en nuestros ensayos de epoxidación. Dicho modelo ya ha sido evaluado con éxito por otros autores (Benavides, 2006; Rangarajan et al., 1995) en sistemas similares pero con aceites distintos. Este tipo de modelo, a diferencia del pseudohomogéneo, tiene en cuenta los fenómenos de transferencia de masa y calor inherentes al sistema de reacción. Las etapas de reacción (Figura 2) que se tienen en cuenta incluyen:
I. Formación del ácido peracético en la fase acuosa, catalizada por ácido sulfúrico: reacción (1).
II. Transferencia del ácido peracético de la fase acuosa a la orgánica.
III. Reacción del ácido peracético sobre las insaturaciones del aceite para formar los anillos oxiranos y liberar ácido acético: reacción (2).
IV. Degradación del anillo oxirano formado por la reacción con ácido acético, agua o peróxido de hidrógeno, en medio ácido: reacciones (3) (4) (5) (6) (7).
Transferencia del ácido acético de la fase orgánica a la fase acuosa para iniciar nuevamente la primera etapa.
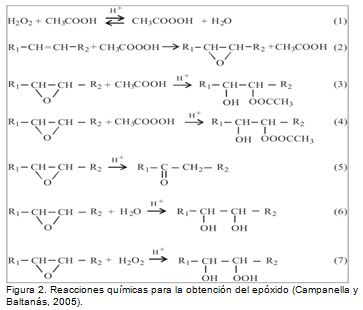
A continuación se muestran las ecuaciones de balance de masa para cada fase y cada una de las especies reactivas presentes en el medio de reacción (Apéndice, Tabla 3).
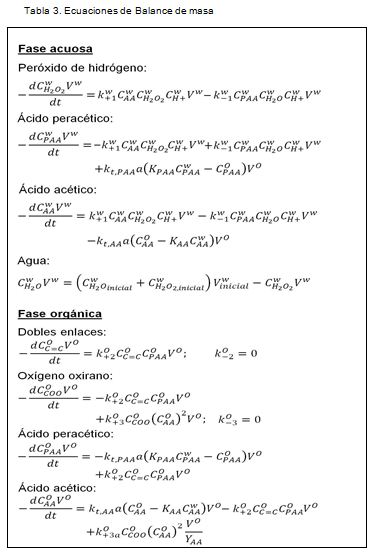
Dado que cada reacción ocurre en una fase en particular, el modelo utiliza concentraciones locales en cada fase (moles de una especie en una fase, divididas en el volumen de dicha fase). Las constantes cinéticas, por lo tanto, también están basadas en concentraciones locales y volúmenes individuales de cada fase (Rangarajan et al., 1995).
Las suposiciones utilizadas en la resolución del sistema incluyen: 1) el volumen de cada fase permanece constante durante la reacción; 2) las reacciones ocurren en el seno de la fase correspondiente; 3) no se consideran fenómenos de transferencia de calor; 4) se considera la presencia de las especies [CH3COOOH] y [CH3COOH] en ambas fases y se asume insolubilidad de las especies [H2O2][H2SO4][H2O] en la fase orgánica; 5) la degradación del oxirano se lleva a cabo en la fase orgánica, dada la insolubilidad del triglicérido en la fase acuosa; 6) se asume como única reacción de degradación la debida al ácido carboxílico entre todas las posibles (reacciones 3-7) requiriendo el uso de un coeficiente de rendimiento, YAA(Rangarajan et al., 1995); 7) se supone igualdad de valores entre los coeficientes kt,PAA= kt,AA para las especies [CH3COOOH] y [CH3COOH], en un sistema no limitado por la por la transferencia de masa. 8) Se supone adición total de la solución catalizadora al inicio de la reacción.
En general, para las diferentes reacciones de degradación se asume que, como la densidad del epóxido de soya (ESBO) es muy similar a la de los productos de degradación obtenidos y los reactivos de la fase polar se encuentran siempre en exceso en el sistema, el volumen total del sistema y los individuales de cada fase permanecen constantes (Campanella y Baltanás, 2006).
El balance de masa y las suposiciones referentes a las reacciones colaterales en la epoxidación del aceite pueden validarse teniendo en consideración las experimentaciones reportadas por otros autores, así:
- La reacción de degradación del oxirano con ácido acético solvatado (en la fase orgánica) usando ácido sulfúrico como catalizador homogéneo ha sido ampliamente estudiada (Gan et al., 1992; Zaher et al., 1989) y se ha encontrado que es de primer orden con respecto a la concentración del epóxido y de segundo orden respecto de la del ácido carboxílico; aumentando proporcionalmente con la concentración de protones provenientes del catalizador (Campanella y Baltanás, 2005).
- Se ha estudiado a profundidad el régimen de reacción bajo el cual ocurren las principales degradaciones en el proceso de epoxidación considerando separadamente los pasos de transporte y de cinética intrínseca de la reacción (Campanella y Baltanás, 2006), concluyendo que la hidrólisis del anillo oxirano debida al ácido acético no es significativa en ausencia de un catalizador: en presencia de ácido sulfúrico la reacción es instantánea y el proceso se ve controlado por la transferencia de masa.
- En cuanto a la degradación del oxirano debida al ácido peracético, se ha evidenciado que si bien el ataque específico sobre el anillo por parte del peracético es diez veces más intenso que el presentado por el ácido acético, este último se regenera constantemente durante el proceso de epoxidación, por lo cual su concentración siempre es mucho mayor a la del perácido; por lo que a condiciones industriales la degradación del anillo oxirano se debe en su mayoría al ácido carboxílico (Campanella y Baltanás, 2005).
- La degradación del oxirano debida al peróxido de hidrógeno es mínima a condiciones normales de producción in situ (T=60 °C, relaciones molares entre C=C/H2O2/CH3COOH de 1:1.1:0.5, [H2O2]= 50% p/p máximo) (Campanella y Baltanás, 2005). Además, debido a la baja solubilidad de la especie epoxidada en agua, se asume que la reacción se da en la fase acuosa (donde se encuentra presente la especie peróxido), aunque en realidad la reacción tome lugar en la interfase (Campanella y Baltanás, 2006).
- La hidrólisis del epóxido formado ocurre a una velocidad extremadamente lenta y requiere de la presencia de un catalizador ácido para proceder a una velocidad apreciable en la interfase y después de largos períodos de inducción, mayores a los tiempos industriales típicos de epoxidación.
Desarrollo experimental
Materiales
Se utilizó aceite de soya comercial (Sigra S. A.) junto con ácido acético glacial, peróxido de hidrógeno (50% p/p) y ácido sulfúrico (96% p/p), todos reactivos analíticos (Merck S. A.). El sistema de reacción incluye un reactor de vidrio enchaquetado de 500 mL con opciones para agitación mecánica, toma de muestras, adición de reactivos y acople con un condensador de vidrio (para evitar el escape de vapores).
Además se utilizó una bomba peristáltica, un serpentín de cobre sumergible para refrigeración, una varilla de agitación de acero inoxidable con aspas tipo pala y un motor mecánico con velocidad regulable entre 100-2.000 r. p. m. Para el seguimiento del avance de reacción se determinó el contenido de oxígeno oxirano (COO) mediante la norma NTC 2366, usando una centrífuga de 6 tubos.
Metodología
El reactor se carga con aceite de soya y se aumenta la temperatura. Posteriormente se adiciona ácido acético y se estabiliza la temperatura. La reacción inicia con la adición de la solución catalizadora, disolviendo previamente el ácido sulfúrico en el oxidante (peróxido de hidrógeno); dicha solución se alimenta en su totalidad durante los 10 primeros minutos de reacción a un caudal de 8,8 mL/min. El sistema se mantiene isotérmico regulando la temperatura del baño con el serpentín y se continúa la reacción en el tiempo requerido. Se toman varias muestras para el seguimiento de la reacción. Cada muestra se lava 4 veces con agua fría y posteriormente se centrifugan a 3.200 r. p. m. durante un intervalo de 20 minutos. La metodología se muestra en detalle en un previo estudio (Boyacá L. A. y Beltrán A. A., 2010).
Resultados
La Tabla 1 ofrece el contenido de oxígeno oxirano (COO) máximo y el tiempo requerido para alcanzar dicho valor en 16 ensayos de epoxidación propuestos, variando la temperatura y las concentraciones de peróxido de hidrógeno, y los ácidos acético y sulfúrico a 2 niveles cada uno.
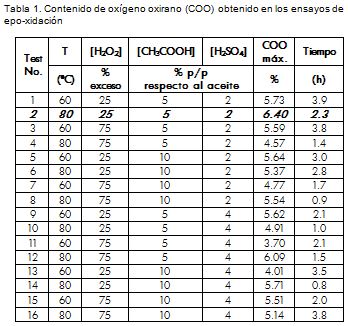
Las ecuaciones de balance para cada una de las especies reactivas constituyen un sistema de ecuaciones diferenciales para cuya resolución se suministran los valores iniciales (volúmenes y concentraciones) y se obtienen como resultado las concentraciones de cada especie en el tiempo; la resolución de este sistema se realizó mediante la herramienta ode45' del software Matlab® 5.3, que utiliza como base numérica el método de Runge-Kutta de cuarto orden, usando como parámetros cinéticos los valores reportados en la literatura (Tabla 2).
El contenido de oxígeno oxirano (COO), definido como los gramos de oxígeno oxirano por 100 gramos de epóxido, puede obtenerse fácilmente a partir de los valores de concentración molar de oxirano arrojados por la simulación, obteniéndose los perfiles que se muestran en la Figura 3. Se utiliza como único parámetro de ajuste el coeficiente de rendimiento (YAA), obteniendo en promedio un coeficiente de correlación de 0,88 mediante el método de mínimos cuadrados.
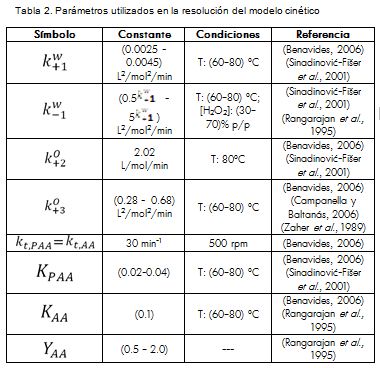
El modelo predice el máximo COO obtenido para el mejor ensayo (No. 2). En especial, el modelo predice correctamente la cinética de reacción cuando la concentración de oxígeno va en aumento; al alcanzar el COO máximo las curvas se alejan de los datos experimentales, indicando que las reacciones de degradación no se ven representadas apropiadamente por la cinética propuesta. Algunos ensayos predicen una velocidad inicial mayor, aun cuando una limitación del modelo es la suposición de adición total del catalizador al inicio de la reacción.
Existen varias posibles causas en la desviación de las curvas calculadas por el modelo respecto de los datos experimentales, todas relacionadas con las suposiciones iniciales realizadas para la resolución del sistema. En primer lugar, la suposición de igualdad entre los coeficientes de transferencia de masa para el ácido acético y el perácido (kt,PAA= kt,AA) se efectúa más por falta de información que debido a algún fundamento teórico, suponiendo valores "suficientemente altos" para un sistema no limitado por la transferencia de masa (Rangarajan et al., 1995), aunque las curvas de concentración establecidas por la simulación no se ven afectadas significativamente usando valores entre 10-30 min-1 (Tabla 2). En efecto, no existe un estudio juicioso que determine dichos coeficientes ni el área interfacial, a, correspondiente al sistema. También se omite el efecto de la agitación sobre la reacción y pocos trabajos reportan un análisis de esta variable; incluso, algunos autores afirman la inexistencia de limitaciones de transferencia de masa al no hallar variaciones significativas del COO con varios niveles de agitación estudiados (Benavides, 2006). Por otra parte, la constante de equilibrio para la reacción de formación in situ (en la fase acuosa) del ácido peracético a partir del ácido acético está dada por la siguiente expresión: K1W=(k+1W))/(k-1W)=(CPWCH20W)/(CAWCH2O2W).
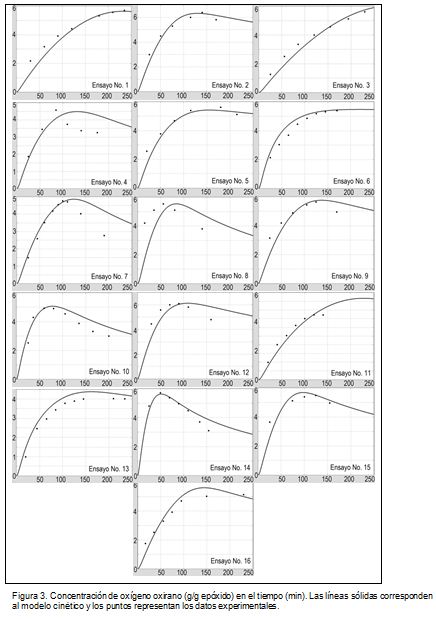
Esta constante puede calcularse experimentalmente determinando los valores cinéticos de la reacción directa (k+1W) e inversa (k-1W). El valor de K1W varía entre 0,7-5 dependiendo de la concentración del peróxido, las relaciones entre los reactantes y la concentración de ácido sulfúrico utilizado, sin explicarse claramente el por qué esta constante depende de otros factores aparte de la temperatura. Por lo tanto, se cree más conveniente calcular el valor de dicha constante de su dependencia con la temperatura, más que a partir de unos pocos datos experimentales (Jankovic y Sinadinovic-Fiser, 2005).
En cuanto al catalizador utilizado, hace falta un estudio más evidente de la degradación del epóxido por parte del ácido sulfúrico mediante un análisis termodinámico que determine las condiciones que favorecen o no las reacciones colaterales previstas y permita aclarar los mecanismos de reacción para este sistema, mejorando la precisión del modelo propuesto. Además, si las reacciones de degradación son catalizadas a bajos pH y existe en el sistema la presencia de tres ácidos (acético, peracético y sulfúrico) no se podría asegurar que la catálisis es debida sólo a los protones H+ provenientes del ácido sulfúrico; sin embargo, no debería ser de otra forma, teniendo en cuenta que el ácido sulfúrico es el de mayor fuerza iónica. También debe analizarse si se trata de una reacción interfacial evaluada a las condiciones de la superficie y no a la
concentración del ácido mineral en el seno de la fase (validando o no la suposición de igualdad entre las concentraciones en el seno y la interfase para las especies). Otra posible causa de la desviación del modelo con respecto a los datos experimentales es la principal reacción de degradación del anillo oxirano, la correspondiente al ácido acético, en la que a pesar de ser la más estudiada, el valor de su constante cinética presenta diferencias de varios órdenes de magnitud según la fase en la cual se lleve a cabo la reacción (Campanella y Baltanás, 2005, 2006). Por lo tanto, conviene corregir el modelo del sistema con la suficiente base experimental para suministrar valores confiables en la estimación de los coeficientes de difusión, área interfacial y transferencia de masa necesarios para las fases continua y dispersa para un completo modelamiento de la reacción de epoxidación.
Los perfiles de concentración de oxígeno oxirano (Figura 3) son similares a los resultados obtenidos en otros estudios (Cai Chuanshang et al., 2008). Sin embargo, dichos autores obtienen COO máximo de 6,1% a T = 75 °C en aproximadamente 4 horas (las concentraciones de reactivos no son reportadas explícitamente, pero se pueden obtener aproximadamente: [H2O2] = 89% exceso, [CH3COOH] = 23% p/p, asumiendo un valor yodo de 130 g I2/100 g aceite de soya). Estos resultados contrastan con los valores obtenidos en la simulación, donde para el ensayo 2 se obtiene un COO máximo de 6,4% a T = 80 °C en 2,3 h con concentraciones de reactivos mucho menores ([H2O2] = 25% exceso, [CH3COOH] = 5% p/p), poniendo en evidencia la importancia del modelo cinético para la optimización de la reacción de epoxidación (Boyacá L. A. y Beltrán A. A., 2010).
Conclusiones
El modelo de dos fases empleado en la cinética de epoxidación es satisfactorio para la primera etapa de reacción, durante la formación del anillo oxirano, con un coeficiente de correlación de 0,88, mostrando las bondades del modelo propuesto; no obstante, se requiere un estudio más profundo acerca de las reacciones de degradación del anillo oxirano para lograr una correcta predicción de los contenidos de oxígeno oxirano esperados. Debe hacerse un análisis termodinámico el cual indique las condiciones que favorecen las posibles reacciones colaterales y determinarse con más precisión las constantes cinéticas involucradas de forma que se puedan obtener dichos valores en un amplio intervalo para las diferentes concentraciones de los reactivos; además, estudiarse los efectos de transferencia de masa presentes, determinando el área interfacial y los coeficientes de transferencia propios del sistema. Por otra parte, puede incluirse la velocidad de agitación como un factor de estudio en la epoxidación y determinar su valor óptimo según las condiciones de reacción.
Agradecimientos
Los autores expresan su agradecimiento a la División de Investigación de Bogotá (DIB), y al Programa Semilleros de Investigación, de la Facultad de Ingeniería (Universidad Nacional), por el financiamiento de este trabajo.
Apéndices
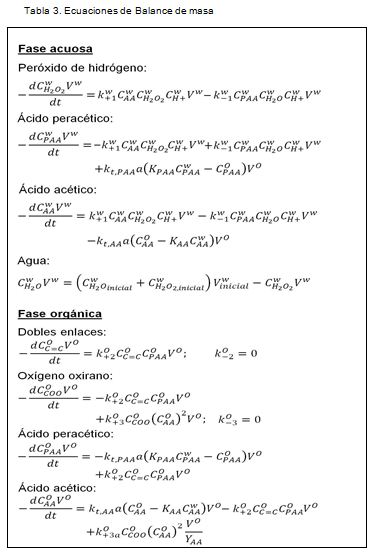
Bibliografía
Boyacá, L. A., Beltrán A. A., Producción de epóxido de soya con ácido peracético generado in situ mediante catálisis homogénea., Ingeniería e Investigación, Vol. 30, No.1, 2010, pp. 136-140. [ Links ]
Benavides, R. E., Evaluación de la producción de polioles poliéster a partir de aceite de palma., Tesis presentada a la Universidad Nacional de Colombia para optar al título de Magíster en Ingeniería Química, 2006. [ Links ]
Campanella, A., Fontaninia, C., Baltanás, M. A., High yield epoxidation of fatty acid methyl esters with performic acid generated in situ., Chemical Engineering Journal, Vol. 144, 2008, pp. 466-475. [ Links ]
Campanella, A., Baltanás, M. A., Degradation of the oxirane ring of epoxidized vegetable oils in a liquid-liquid-solid heterogeneous reaction system., Chemical Engineering and Processing, Vol. 46, 2007, pp. 210-221. [ Links ]
Campanella, A., Baltanás, M. A., Degradation of the oxirane ring of epoxidized vegetable oils in a liquid-liquid heterogeneous reaction systems., Chemical Engineering Journal, Vol. 118, 2006, pp. 141-152. [ Links ]
Campanella, A., Baltanás, M. A, Degradation of the oxirane ring of epoxidized vegetable oils with hydrogen peroxide using an ion exchange resin., Catalysis Today, Vol. 107-108, 2005, pp. 208-214. [ Links ]
Campanella, A., Baltanás, M. A., Degradation of the oxirane ring of epoxidized vegetable oils in liquid-liquid systems: I. Hydrolysis and attack by H2O2., Latin American Applied Research, Vol. 35, 2005, pp. 205-210. [ Links ]
Campanella, A., Baltanás, M. A., Degradation of the oxirane ring of epoxidized vegetable oils in liquid-liquid systems: II. Reactivity with solvated acetic and peracetic acids., Latin American Applied Research, Vol. 35, 2005, pp. 211-216. [ Links ]
Campanella, A., Baltanás, M. A, Degradation of the oxirane ring of epoxidized vegetable oils with solvated acetic using cation exchange resins., European Journal of Lipid Science and Technology, Vol. 106, 2004, pp. 524-530. [ Links ]
Gan, L. H., Goh, S. H., Ooi, K. S., Kinetic studies of epoxidation and oxirane cleavage of palm olein methyl esters., Journal of the American Oil Chemists' Society, Vol. 69, No. 4, 1992, pp. 347-351. [ Links ]
Goud, V, V., Patwardhan, A. V., Dinda, S., Pradhan, N. C., Epoxidation of karanja (Pongamia glabra) oil catalysed by acidic ion exchange resin., European Journal of Lipid Science and Technology, Vol. 109, 2007, pp. 575-584. [ Links ]
Jankovic, M., Sinadinovic-Fiser, S., Prediction of the chemical equilibrium constant for peracetic acid formation by hydrogen peroxide., Journal of the American Oils Chemists' Society, Vol. 82, No. 4, 2005, pp. 301-301. [ Links ]
Kuo, M-C., Chou, T-C., Kinetics and mechanism of the catalyzed epoxidation of oleic acid with oxygen in the presence of benzaldehyde., Industrial and Engineering Chemistry Research, Vol. 26, 1987, pp. 277-284. [ Links ]
Musante, R. L., Grau, R. J., Ba1tanás, M. A., Kinetic of liquid phase reactions catalyzed by acidic resins: the formation of peracetic acid for vegetable oil epoxidation., Applied Catalysis A: General, Vol. 197, 2000, pp. 165-173. [ Links ]
Petrovic, Z. S., Zlatanic, A., Lava, C. C., Sinadinovic-Fiser, S., Epoxidation of soybean oil in toluene with peroxoacetic and peroxoformic acids kinetics and side reactions., European Journal of Lipid Science and Technology, Vol. 104, 2002, pp. 293-299. [ Links ]
Rangarajan, B., Havey, A., Grulke, E. A., Culnan, P. D., Kinetic parameters of a two-phase model for in situ epoxidation of soybean oil., Journal of the American Oils Chemists' Society, Vol. 2, No. 10, 1995, pp. 1161-1169. [ Links ]
Sinadinovic-Fiser, S., Jankovic, M., Petrovic, Z. S., Kinetics of in situ epoxidation of soybean oil in bulk catalyzed by ion exchange resin., Journal of the American Oils Chemists' Society, Vol. 78, No. 7, 2001, pp. 725-731. [ Links ]
Zaher, F.A., El-Mallah, M. H., El-Hefnawy, M. M., Kinetics of oxirane cleavage in epoxidized soybean oil., Journal of the American Oils Chemists' Society, Vol. 66, No. 5, 1989, pp. 698-700. [ Links ]