Services on Demand
Journal
Article
Indicators
-
Cited by SciELO
-
Access statistics
Related links
-
Cited by Google
-
Similars in SciELO
-
Similars in Google
Share
Ingeniería e Investigación
Print version ISSN 0120-5609
Ing. Investig. vol.33 no.3 Bogotá Sept./Dec. 2013
S. R. Kunst1, G. A. Ludwig2, M. R. Ortega-Vega3 and C. F. Malfatti4
1 Sandra Raquel Kunst. Chemical Engineer. MSc. Metallurgical Engineering. Afiliation: Universidade Federal do Rio Grande do Sul, Brazil. E-mail: tessaro.sandra@gmail.com
2 Gustavo Alberto Ludwig. Mechanical Engineer. Afiliation: Universidade Federal do Rio Grande do Sul, Brazil. E-mail: gustavolludwig@gmail.com
3 María Rita Ortega Vega. Chemical Engineer. Afiliation: Universidade Federal do Rio Grande do Sul, Brazil. E-mail: mortegavega811@gmail.com
4 Célia de Fraga Malfatti. Metallurgical Engineer. MSc. Metallurgical Engineering. PhD. Metallurgical Engineer. Afiliation: Universidade Federal do Rio Grande do Sul, Brazil. E-mail: celia.malfatti@ufrgs.br
How to cite: Kunst, S. R., Ludwing, G. A., Ortega, M. R., de Fraga Malfatti, C., The influence of adding corrosion inhibitor and pH on the electrochemical properties of hybrid films applied to galvanised steel., Ingeniería e Investigación, Vol. 33, No. 3, December 2013, pp. 17 - 21.
ABSTRACT
This study was aimed at coating galvanised steel with a hybrid film obtained from a sol consisting of silane precursors 3 - (trimetoxisililpropil) methacrylate (TMSPMA) and tetraethoxysilane (TEOS). The pH of the hydrolysed-silane solution was 1 and 3. The influence of adding corrosion inhibitor (i.e. 0.01M cerium nitrate) was evaluated for all samples. The hybrid films were deposited by dip-coating. The film was characterised scanning electron microscopy (SEM), profilometry, contact angle measurement, potentiodynamic polarisation and electrochemical impedance spectroscopy. The results showed that solution pH influenced hybrid film formation and final surface properties. Additionally, cerium nitrate as corrosion inhibitor addition enhances corrosion resistance of the films.
Keywords: Hybrid film, pH, corrosion inhibitor.
RESUMEN
El objetivo de este estudio es revestir acero galvanizado con un filme híbrido, obtenido a partir de un sol constituido por los precursores de silano 3 - (trimetoxisililpropil), metacrilato (TMSPMA) y tetraetoxisilano (TEOS); los pH de la solución de silano hidrolizado fueron 1 y 3. Se evaluó la influencia de la adición de un inhibidor de corrosión, en este caso, nitrato de cerio 0.01 M, para todas las muestras. La aplicación de los filmes híbridos se realizó por dip-coating y su caracterización se realizó por microscopía electrónica de barrido (SEM), perfilometría, medición del ángulo de contacto, polarización potenciodinámica y espectroscopía de impedancia electroquímica. Los resultados muestran que el pH de la solución influye en la formación de los filmes híbridos y en sus propiedades superficiales finales, además, la adición del nitrato de cerio como inhibidor de corrosión mejora su resistencia.
Palabras clave: filme híbrido, pH, inhibidor de corrosión.
Received: February 8th 2013 Accepted: Octubre 2nd 2013
Introduction
Adding corrosion inhibitors or other compounds to silane films can modify their properties as a barrier layer, increase their thickness and densification (Deflorian, 2006) and enhance anti-corrosive performance. The pertinent literature reports silane films being modified with rare earth salts (Trabelsi, 2006; Mon-temor, 2007) providing good anticorrosive properties when used as single layers on aluminium alloys and galvanised steel (Zhu, 2004). Cerium (Ce) is the most used rare earth element for enhancing corrosion inhibition using cerium compounds as cerium source. Film thickness and hydrophobicity increase when cerium is inserted into a silane matrix and healing properties against defects formed by the attack of aggressive species be-come developed (Tamborim, 2008; Palomino 2009).
The hybrid film acts as a reservoir for inhibitors, releasing them onto damaged and unprotected areas and preventing corrosion from taking place (Palanivel, 2005). When failure takes place in a film due to electrolytic action, the metal becomes exposed to an aggressive environment, producing anodic and cathodic activity. Cathodic activity causes an increase in local pH due to hydroxyl ion formation. As cerium ions have some mobility within the silane matrix, they can move to the location of cathodic activity and react with hydroxyl ions (Ooij, 2001). Ce(III) and Ce(IV) oxide/hydroxide formation precipitates exactly on the cathodic areas, thereby sealing defects in a film.
Although it has been demonstrated that silanes are relatively effective for protecting metallic substrates against corrosion, protection effectiveness depends on parameters such as precursor solution pH which is responsible for silane stability in aqueous solution and, ultimately, hydrolysed-silane solution shelf-life. Moreover, precursor solution pH affects the behaviour of a particular silane during hydrolysis and condensation reactions, since both reactions are catalysed by acids or bases (Ooij, 1998; Ooij, 1999).
Silanol hydrolysis and condensation reactions in aqueous phase occur simultaneously in a hydrolysed-silane solution. However, the hydrolysis rate in slightly acidic aqueous solutions is faster than the condensation rate for most silanes. Thus, mixture pH should be adjusted to a value at which maximum hydrolysis rate and minimum condensation rate are reached (Ooij, 1999).
This paper thus describes coating galvanised steel with a hybrid film obtained from a sol consisting of silane precursors 3 - (trimethoxysilylpropyl) methacrylate (TMSPMA) and tetraethoxysilane (TEOS). Hydrolysed-silane solution pH was varied at pH=1 and pH=3 and both samples were evaluated with and without adding Ce nitrate at 0.01 M concentration by the dip-coating process.
Materials and methods
Surface preparation
The galvanised steel substrates were rinsed with ethanol and dried. They were then immersed in neutral soap solution at 70oC for 10 minutes to degrease them. They were then properly washed and dried.
Preparing hybrid films
Hydrolysis reactions were conducted with silane precursors (TMSPMA) 3-(trimethoxysilylpropyl) methacrylate (C10H20SiO5) and (TEOS) tetraethoxysilane (C8H20SiO4) and hydrolysed-silane solution pH was varied at pH=1 and pH=3. Both formulations were evaluated with and without 0.01 M cerium nitrate having been added. Dip-coating was used to coat the substrates: 10 cm.min-1 removal rate and 10 minute residence time (Kunst, 2011). The substrates were then thermally cured in an oven at 60 ± 2oC for 20 minutes (Table 1).
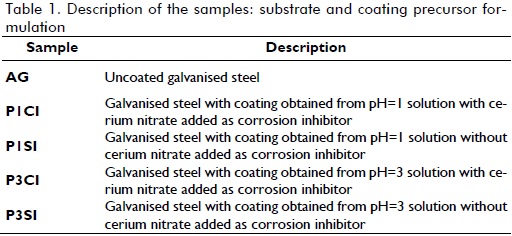
Experimental techniques
Scanning electron microscopy (SEM) was used for morphological characterisation on JEOL 6060 equipment using 20 kV acceleration voltage. The samples were observed from top and cross-section view to determine layer thickness. The surface micro-roughness was evaluated using a contact profilometer (PRO500 3D). Hybrid film wettability was determined by measuring the contact angle, applying the sessile drop method, on equipment developed by the Universidade Federal do Rio Grande do Sul (UFRGS) Corrosion Research Laboratory (LAPEC). The contact angle was determined using image analysis software.
Hybrid film electrochemical performance was evaluated by open circuit potential (EOCP) monitoring, potentiodynamic polarisation and electrochemical impedance spectroscopy (EIS) in a 0.05M NaCl solution. The samples were monitored for 96 hours by EIS, using 10mV EIS perturbation amplitude and 100 kHz to 10 mHz frequency range using a Solartron 1255 frequency response analyser and a potentiostat PAR273. A three-electrode cell was used for electrochemical analysis with platinum as counter-electrode and SCE as reference electrode. The working electrode area was 0.626 cm². The polarisation curves were obtained with potential ranging from -200 mV below the open circuit potential up to 400 mV above this potential, with 1 mV.s-1 scan rate. Corr-view software was used for analysing potentiodynamic polarisation measurement data for determining corrosion current, corrosion potential and polarisation resistance.
Results and discussion
Morphological characterisation
Figures 1 and 2 show the SEM micrographs for samples P1CI, P1SI, P3CI and P3SI. Morphology revealed discontinuity on the films, especially for samples lacking cerium nitrate addition, i.e., samples P1SI (Figure 1-b) and P3SI (Figure 2-b). Samples which had had cerium nitrate added as corrosion inhibitor (Figures 1-a and 2-a) had fewer cracks than samples without cerium nitrate (Figures 1-b and 2-b). Coatings formed in a less acidic environment had fewer discontinuities or cracks, because a more acidic environment (i.e. pH=1) promotes a higher hydrolysis rate regarding condensation rate, thereby provoking cracks in the film (Ooij, 1999). Samples having had cerium nitrate added and higher pH (P3CI, Figure 2-a) developed the most homogeneous and least cracked film.
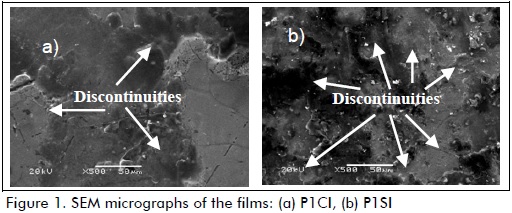
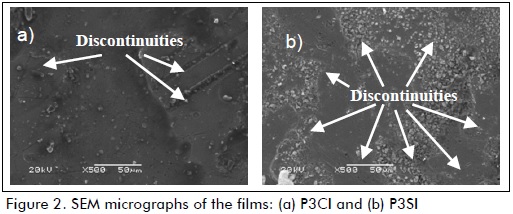
Figure 3 shows the images obtained by profilometry for all samples. Roughness values are shown in Table 2. The films without cerium nitrate had greater roughness than samples with corrosion inhibitor. The effect of pH was reflected as films synthesised from a less acidic solution (pH=3) had lower roughness values and a more uniform surface. These results confirmed the SEM images. Sample P3CI had the lowest roughness value and the smoothest surface (see Table 2 and Figures 2-a and 3).
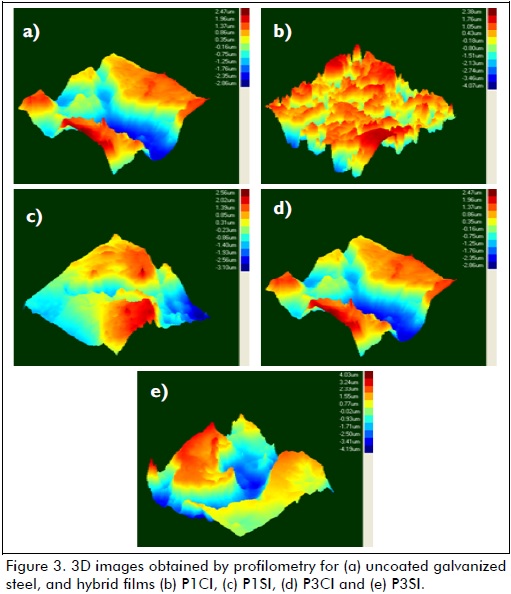
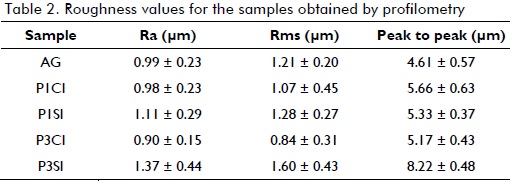
Layer thickness values (Table 3) determined by cross-section SEM image analysis (Figure 4) led to inferring that cerium nitrate enhanced film growth, a thicker layer thereby being obtained. This was because samples P1CI (Figure 4-a) and P3CI (Figure 4-d) (i.e. those having cerium nitrate added) had higher layer thickness values (Table 3). It was also inferred that adding cerium nitrate modified barrier layer properties by increasing layer thickness and densification (Motte, 2005; Palomino, 2007).
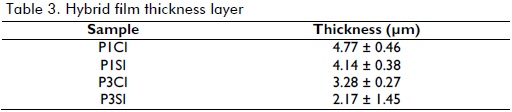
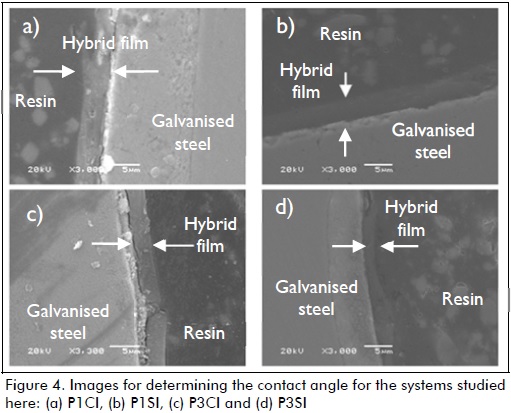
It was observed when analysing the influence of hydrolysed-silane solution pH, that hybrid films obtained from the most acidic solution (pH=1), P1CI and P1SI, had thicker layers than samples synthesised in the least acidic solution (pH=3): P3CI and P3SI. This agreed with that reported in the literature (Ooij, 1998) stating that a hydrolysed-silane solution having more acidic pH had the highest silane hydrolysis rate and the minimum silanol condensation rate. It promotes the formation of siloxane groups which are responsible for barrier layer formation; it also increases film thickness and, hence, improves anticorrosive performance (Ooij, 1999).
Table 4 shows the contact angle values for all the samples. It can be seen that P1CI and P3CI (i.e. those having cerium nitrate added to them) had the highest contact angle values and, consequently, lower wettability compared to samples without corrosion inhibitor and uncoated galvanised steel. This result indicates that adding cerium nitrate to hybrid films increased layer thickness.
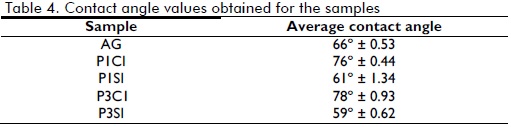
Electrochemical characterization
Open circuit potential (EOCP) for all hybrid films was very close to that for uncoated galvanised steel EOCP (Figure 5). This was due to the fact that all the hybrid films had surface discontinuity, as shown in SEM images (Figure 1).
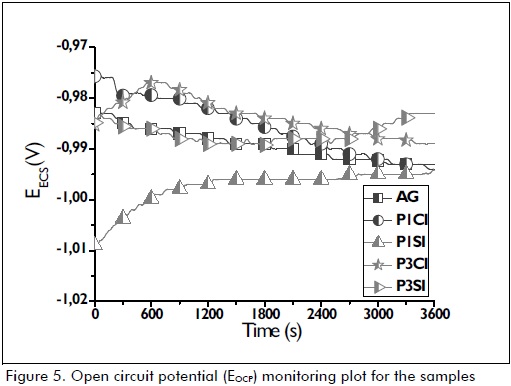
Polarisation test results (Figure 6 and Table 5) showed that hybrid film coatings promoted an increase in polarisation resistance (Rp) and a reduction in icorr compared to uncoated galvanised steel, demonstrating their protective action. However, it was observed that samples obtained from a more acidic solution (pH=1) (i.e. P1CI and P1SI) had a better corrosion resistance pattern than those obtained from less acidic media (pH=3) (i.e. P3CI and P3S1). This result indicated that the more acidic the pH, the thicker the barrier layer (Figure 3 and Table 3) and, consequently, improved anticorrosive performance.
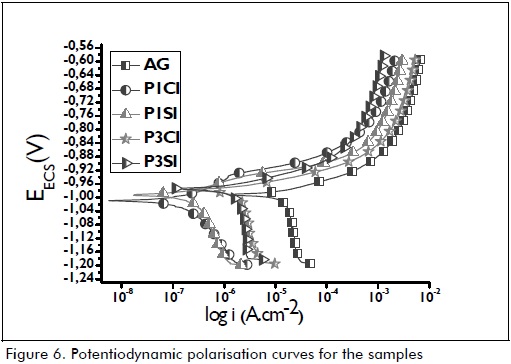
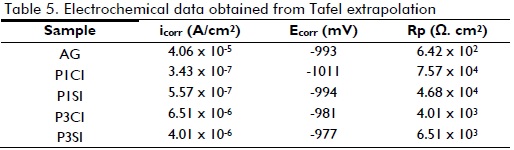
Samples having cerium nitrate as corrosion inhibitor (P1CI and P3CI) had better polarisation resistance results compared to hybrid films without inhibitor (P1SI and P3SI). The good electrochemical performance by samples having cerium nitrate as corrosion inhibitor was associated with the fact that the concentration used was ideal, since the authors verified that adding cerium ion at 0.01M concentration promoted an increase in Rp and decreased icorr values, compared to silane films without cerium (Malfatti, 2012). Higher cerium concentration in a film can modify the silane network due to incorporating cerium atoms leading to silicon atoms being replaced in this molecule (Montemor, 2007). This effect was more important for high cerium ion atomic fraction in the hybrid film.
According to the polarisation curves (Figure 6), at potential close to -1,1 mV, hybrid films' cathodic reaction current density became decreased compared to uncoated galvanised steel. It was due to cerium nitrate corrosion inhibitor action, since cerium nitrate performs as a cathodic inhibitor, decreasing the cathodic reaction rate whilst the anodic reaction does not become significantly affected at high potential. This may have been related to two factors: less oxygen (O2) diffusion and/or reduced cathode area (Papavinasam, 2000).
Figure 7 shows the impedance plot for uncoated galvanised steel and its variation according to immersion time (1, 24, 48, 72 and 96 hours) in 0.05 M NaCl electrolyte. These diagrams were obtained sequentially for the same sample, and thus represent the evolution of electrode response regarding immersion time in the test solution. Concerning uncoated galvanised steel (Figure 7), a phenomenon was observed at medium frequency, possibly associated with the effect of electrolyte permeability through zinc corrosion products. A phenomenon at low frequency was observed as immersion time elapsed (1, 24, 48, 72 and 96 hours), which was associated with the presence of zinc corrosion products. Charge transfer response became shifted to lower frequencies as the active area expanded, thereby increasing capacitance whilst hydroxide precipitation cathodic reaction was observed with very low resistance, at medium frequency (Simões, 2010):

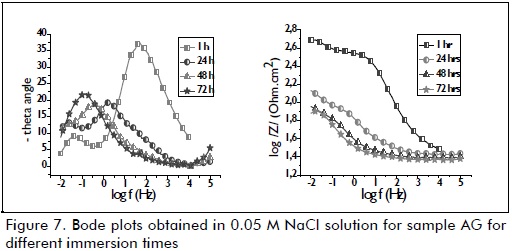
According to the Pourbaix diagram for zinc, zinc hydroxide becomes stable at pH values above 8; this value can easily be reached on steel. Furthermore, carbonates can also react, eventually leading to hydrozincite, according to Ogle (2006):

When analysing samples obtained from more acidic solutions (i.e. P1CI in Figure 8-a and P1SI in Figure 8-bc), a phenomenon often associated with the film's high barrier effect was only observed during the first hour of immersion, as reported by other authors (García-Heras, 2004; Galio, 2010). After 24 hours immersion, this phenomenon became shifted to a new phenomenon at high frequency which is often associated with the average effect of electrolyte permeability through a film. Within 48 hours of immersion, the same pattern remained for the sample with corrosion inhibitor (P1CI), whereas the phenomenon shifted to take place at low frequency for the sample lacking inhibitor (P1SI), this being associated with the presence of zinc corrosion products and the cracks observed in SEM images (Figure 1). pH effects were related to higher impedance modulus and polarisation resistance observed for the samples from the pH=3 solution (P3CI, P3SI). This result indicated that, as seen in polarisation curves (Figure 6 and Table 5), pH influenced barrier layer formation, thereby increasing layer thickness (Figure 4 and Table 3) and enhancing anticorrosion performance.
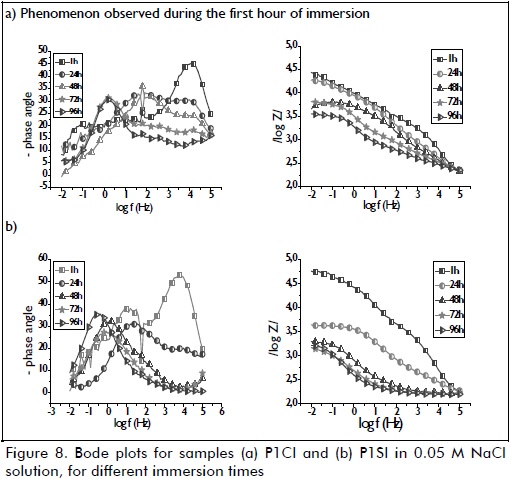
A phenomenon often associated with the film's high barrier effect was only observed during the first hour of immersion for samples P3CI (Figure 9) and P3SI (Figure 10). This high frequency phenomenon became shifted to a low frequency phenomenon after 24 hours' immersion, possibly being associated with the presence of zinc corrosion products. The pattern observed for the samples after 24 hours immersion was maintained until the end of the test (96 hours immersion). Resistance and impedance modulus values for P3CI were related to anticorrosion performance, due to the presence of cerium nitrate as corrosion inhibitor.
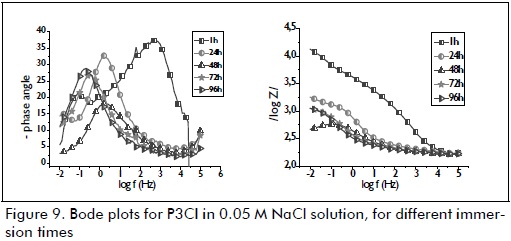
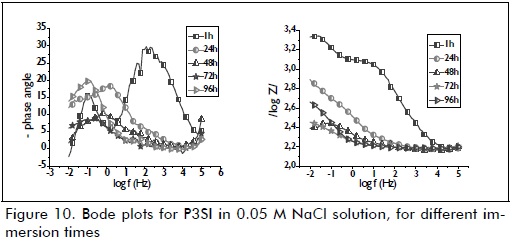
Conclusions
The results showed that adding 0.01 M cerium nitrate as corrosion inhibitor improved the film's corrosion performance and barrier properties compared to samples without inhibitor.
Analysing the systems regarding variable pH, hybrid films obtained from more acidic solution (pH=1) had better electrochemical anticorrosion performance and higher layer thickness than hybrid films obtained from an acidic solution having higher pH: thus, the more acidic the precursor solution, the higher the silane hydrolysis rate and minimum silanol condensation rate. It promoted the formation of siloxane groups which are responsible for barrier layer formation, increased layer thickness and anticorrosive performance, with or without adding cerium nitrate as corrosion inhibitor. When cerium nitrate was added to pH=1 solutions as corrosion inhibitor, anticorrosive performance became even more enhanced.
Adding a corrosion inhibitor (such as cerium nitrate) at non-extremely acidic pH (pH=3 in this case) was a suitable formulation for obtaining hybrid films having low roughness values and a smoother surface and involving less promotion of crack formation, but reducing good anticorrosion performance.
References
Deflorian, F., Rossi, S., Fedrizzi, L., Silane Pre-Treatments on Copper and Aluminium., Electrochimica Acta, Vol. 51, 2006, pp. 6097-6103. [ Links ]
Galio, A. F., Lamaka, S. V., Zheludkevich, M. L., Dick, L. F. P., Muller, I. L., Ferreira, M. G. S., Inhibitor-doped sol-gel coatings for corrosion protection of magnesium alloy AZ31., Surface and Coatings Technology, Vol. 204, 2010, pp. 1479-1486. [ Links ]
Garcia-Heras, M., Jimenez-Morales, A., Casal, B., Galvan, J. C., Radzki, S., Villegas, M. A., Preparation and electrochemical study of cerium-silica sol-gel thin films., Journal of Alloys Compd., Vol. 380, 2004, pp. 219-224. [ Links ]
Kunst, S. R., Matos, J. F., Korb, M. A., Malfatti, C. F., Desarollo de revestimientos protectores a base de silanos para La protecction de aceros galvanizados., Información Tecnológica, Vol. 22, No. 5, 2011. [ Links ]
Malfatti, C. F., Menezes, T. L., Radtke, C., Esteban, J., Ansart, F., Bonino, J. P., The influence of cerium ion concentrations on the characteristics of hybrid films obtained on AA2024-T3 aluminum alloy., Materials and Corrosion, Vol. 63, No. 9, 2012. [ Links ]
Montemor, M. F., Ferreira, M. G. S., Analytical and microscopic characterisation of modified bis-[triethoxysilylpropyl] tetrasulphide silane films on magnesium AZ31 substrates., Progress in organic coatings, Vol. 60, 2007, pp. 228-237. [ Links ]
Montemor, M. F., Ferreira, M. G. S., Electrochemical study of modified bis-[triethoxysilylpropyl] tetrasulfide silane films applied on the AZ31 Mg alloy., Electrochimica Acta, Vol. 52, 2007, pp. 7486-7495. [ Links ]
Motte, C., Maury, N., Olivier, M. G., Petitjean, J. P., Willem, J. F., Cerium treatments for temporary protection of electroplated steel., Surface Coating Technology., Vol. 200, 2005, pp. 2366-2375. [ Links ]
Ogle, K., Morel, S., Jacquet, J., Observation of Self-Healing Functions on the Cut Edge of Galvanized Steel Using SVET and pH Microscopy., Journal of The Electrochemical Society, Vol. 153, 2006, pp. B1-B5. [ Links ]
Ooij, W. J. V., Corrosion Protection Properties of Organofunctional Silanes-An Overview., Tsinghua Science and Technology, Vol. 10, 2005, pp. 639-664. [ Links ]
Ooij, W. J. V., Child, T. F., Protecting metals with silanes coupling agents., Chemtech, Vol. 29, No. 2, 1998, pp. 26-35. [ Links ]
Ooij, W. J. V., Child, T. F., Improved service life of coated metals by engineering the polymer-metal interface., American Chemical Society, Vol. 51, 1999, pp. 354-377. [ Links ]
Palanivel, V., Huang, Y., Ooij, W. J. V., Effects of addition of corrosion inhibitors to silane films on the performance of AA2024-T3 in a 0.5 M NaCl solution., Progress in Organic Coatings, Vol. 53, 2005, pp. 153-168. [ Links ]
Palomino, L. M., Suegama, P. H., Aoki, I. V., Montemor, M. F., Melo, H. G., Electrochemical study of modified cerium-silane bi-layer on Al alloy 2024-T3., Corrosion Science, Vol. 51, No. 6, 2009, pp. 1238-1250. [ Links ]
Palomino, L. E. M., Suegama, P. H., Aoki, I. V., Paszti, Z., Melo, H. G., Investigation of the corrosion behaviour of a bilayer cerium-silane pre-treatment on Al 2024-T3 in 0.1 M NaCl., Electrochimica Acta, Vol. 52, 2007, pp. 7496-7505. [ Links ]
Papavinasam, S., Corrosion Inhibitors. In: R. W. Revie (Ed.), Uhlig's Corrosion Handbook, N. Y., John Wiley & Sons, Inc, 2000, pp. 1089-1105. [ Links ]
Simões, A. M., Fernandes, J. C. S., Studying phosphate corrosion inhibition at the cut edge of coil coated galvanized steel using the SVET and EIS., Progress in Organic Coatings, Vol. 69, 2010, pp. 219-224. [ Links ]
Tamborim, S. M., Maisonnave, A. P. Z., Azambuja, D. S., Englert, G. E., An electrochemical and superficial assessment of the corrosion behavior of AA 2024-T3 treated with metacryloxypropylmethoxysilane and cerium nitrate., Surface and Coating Technology, Vol. 202, 2008, pp. 5591-6001. [ Links ]
Trabelsi, W., Triki, E., Dhoubi, L., Ferreira, M. G. S., Zheludkevich, M. L., Montemor, M. F., The use of pre-treatments based on doped silane solutions for improvide corrosion resistance of galvanized steel substrates., Surface and coating technology, Vol. 200, 2006, pp. 4240-4250. [ Links ]
Zhu, D., Ooij, W. J. V., Corrosion protection of metals by water-based silane mixtures of bis-[trimethoxysilylpropyl]amine and viniltriacetoxysilane., Progress in organic coating, Vol. 49, 2004, pp. 42-52. [ Links ]