Servicios Personalizados
Revista
Articulo
Indicadores
-
Citado por SciELO
-
Accesos
Links relacionados
-
Citado por Google
-
Similares en SciELO
-
Similares en Google
Compartir
Ingeniería e Investigación
versión impresa ISSN 0120-5609
Ing. Investig. vol.34 no.3 Bogotá sep./dic. 2014
https://doi.org/10.15446/ing.investig.v34n3.41938
DOI: http://dx.doi.org/10.15446/ing.investig.v34n3.41938
L. A. Ardila1, J. J. Olaya2 and J. M. Arroyo3
1Laura Angélica Ardila Rodríguez. Mechanical Engineer and MSc in Materials and Processes, Universidad Nacional de Colombia, Colombia. E-mail: laardilar@unal.edu.co
2 Jhon Jairo Olaya Flórez. MSc in Materials and Processes, Universidad Nacional de Colombia, Colombia. PhD in Materials Science, Universidad Nacional Autónoma de México, Mexico. Affilliation: Associate Professor, Universidad Nacional de Colombia, Colombia. E-mail: jjolayaf@unal.edu.co
3 José Manuel Arroyo Osorio. MSc in Systems Engineering, Universidad Nacional de Colombia, Colombia. PhD in Mechanical Engineering, Universidade Estadual De Campinas, Brasil. Affiliation: Associate Professor, Universidad Nacional de Colombia, Colombia. E-mail: jmarroyoo@unal.edu.co
How to cite: Ardila, L. A., Olaya, J. J., & Arroyo, J. M. (2014). Microstructure, morphology, adhesion and tribological behavior of sputtered niobium carbide and bismuth films on tool steel. Ingeniería e Investigación, 34(3), 12-18.
ABSTRACT
NbC, Bi and Bi/NbC coatings were deposited on AISI M2 steel substrates using unbalanced magnetron sputtering at room temperature with zero bias voltage. Were studied the phase structure, the morphology, the adhesion and the tribological behavior of the three coatings. The niobium carbide film crystallized in the NbC cubic structure, and the bismuth layers had a rhombohedral phase with random orientation. The NbC coating had a smooth surface with low roughness, while the Bi layers on steel and on NbC coating had higher roughness and a morphology composed of large particles. By using a ductile Nb interlayer good adhesion between the NbC coating and the steel substrate was achieved. The Bi coating had better adhesion with the NbC layer than with the steel substrate. The tribological performance of the Bi coating on steel was not satisfactory, but according to the preliminary results, the produced NbC and Bi/NbC coatings have the potential to improve the tribological performance of the steel.
Keywords: Niobium carbide, bismuth, magnetron sputtering, friction, wear.
RESUMEN
Recubrimientos de NbC, Bi y Bi/NbC fueron depositados en acero AISI M2, usando pulverización catódica con magnetrón desbalanceado, a temperatura ambiente y con voltaje de polarización cero, además, fueron estudiados: la estructura cristalina, la morfología, la adherencia y el comportamiento tribológico de los tres recubrimientos. De esta manera, la película de carburo de niobio cristalizó en estructura cubica y las capas de bismuto presentaron estructura romboédrica con orientación aleatoria. El recubrimiento de NbC presentó una superficie suave con baja rugosidad, mientras que las películas de bismuto depositadas sobre acero y sobre la capa de NbC, presentaron mayor rugosidad y morfología compuesta de grandes partículas.
Mediante el uso de una capa intermedia de Nb dúctil, se obtuvo buena adherencia entre el recubrimiento NbC y el sustrato de acero, además, el recubrimiento de Bi presentó mejor adherencia con la capa NbC que con el sustrato de acero y el desempeño tribológico del recubrimiento de bismuto depositado sobre el acero no fue satisfactorio, pero según los resultados preliminares, los recubrimientos NbC y Bi/NbC producidos tienen potencial para mejorar el desempeño tribológico del mismo.
Palabras clave: carburo de Niobio, bismuto, pulverización catódica con magnetrón, fricción y desgaste.
Received: February 6th 2014 Accepted: June 16th 2014
Introduction
To improve the performance of many components and tools hard coatings are used because they generally have high melting points, high hardness, good chemical stability and high wear resistance (Carrera et al., 2003; Derflinger et al., 1999; Renevier et al., 2000). One drawback is that these coatings often have a high friction coefficient. Therefore, there is great interest in new developments to reduce friction, thereby improving the tribological performance of the coatings (Daming et al., 1997).
The carbides of transition metals, such as vanadium, chromium, niobium, tungsten or titanium are materials with many technological applications due to their high strength and durability. Among existing hard-coating materials available to date niobium carbide (NbC) is highlighted. This material has high hardness (Amriou et al., 2003), high toughness, high elasticity modulus, excellent chemical stability, high wear resistance (Zoita et al., 2010) and high melting temperature (3873 K) (Bendavid et al., 2003), (Sustarsic et al., 2003). This properties combination makes NbC an excellent candidate for a wide range of industrial applications. NbC also has high conductivity, good corrosion resistance and even a superconducting phase at low temperatures. For these reasons it has been tested in applications requiring biocompatibility and applications in microelectronics components (Eisenbarth et al., 2004).
Solid lubricant coatings are used for components in operating environments where lubricating oils either cannot be used or have limited efficiency (Teer et al., 1997). Such applications include vacuum and aerospace equipment (Watanabe et al., 2004a, 2004b). In order to obtain coatings with simultaneously high hardness and low coefficient of friction (COF), multilayer coatings with combinations of hard ceramic and solid lubricating layers have been developed, in which a combination of the properties in each layer have been obtained (Haider et al., 2005). Multilayer coatings are used in many applications, such as in a wide variety of cutting tools, among others (Carrera et al., 2003).
Among the materials that might be used as a solid coating with tribological purposes is bismuth (Bi), a highly anisotropic semi-metal of the group V with low melting point (544 K) and thermal conductivity with an order of magnitude less than typical metals (Boffoue et al., 1998). Bi crystallizes in a rhombohedral structure and forms layers between which there are weak bonds compared with the internal bonds of the layer itself. This characteristic allows Bi crystals to slide easily between the layers formed by (001) planes (Hofmann, 2006). This behavior resembles that of molybdenum disulfide (MoS2), which has very low friction values (Daming et al., 1997; Teer et al., 1997; Waghray et al., 1995) and is also used as lubricant coating in several applications. Bi nanoparticles added directly as an additive in lubricating oils, form homogeneous and stable distributions. Under mechanical load the Bi melts and provides instantaneous protection by preventing direct contact between the sliding surfaces (Zhao et al., 2004). Films of Bi have been produced by sputtering (Kim et al., 2006), by pulsed laser deposition (Boffoue et al., 1998) and by thermal evaporation (Kumari et al., 2007).
The AISI M2 steel is typically used for the manufacture of cutting tools for machining operations such as turning, drilling and milling; other applications include cutting tools for sheet and forming tools (Arias et al., 2010). This steel has high toughness and maintains its hardness up to approximately 773 K, which is why it has remained in widespread use for more than hundred years of evolution of cutting tool materials (Trent & Wright, 2000). There have been many developments to improve the work properties of AISI M2 steel; among these, the use of hard coatings applied by physical vapor deposition (PVD) especially stands out (Krahmer et al., 2003).
In this work, we try to explore alternatives to improve the tribological behavior of AISI M2 steel by coating this material with films of NbC, Bi and Bi/NbC. We chose to experiment with NbC because this carbide has the highest melting point (3600oC) compared with that of the carbides of vanadium (2830oC), titanium (3067oC) and zirconium (3420oC).
The three types of coatings were deposited to make comparisons and to assess the individual effect of both the NbC and the Bi layers. The coatings were deposited by sputtering with an unbalanced magnetron. With the aim of reducing the presence of residual stresses in the coatings and to avoid structural alterations by heating of the steel substrate, the deposition of the coating was made at room temperature (Zhang et al., 2012; Zoita et al., 2010).
Experimental Procedure
Onto substrates of AISI M2 steel quenched and tempered with a final hardness of 64 HRC were deposited coatings of Bi, NbC and Bi/NbC by sputtering with an unbalanced magnetron. The deposition process was made without heating the substrates and with zero bias voltage. Before the deposition process, the substrates were polished to a mirror finishing using SiC emery paper with 1200-mesh grit and were then degreased using an ultrasonic bath of acetone and alcohol for 120 s.
To produce all the coatings, the base pressure in the deposition chamber was 3×10-3 Pa and the distance between the cathode and the substrates was 5 cm. The NbC coatings were deposited by reactive sputtering using a mix of Ar (99.999%) and CH4 (99.99%) gases in discharging with a niobium (99.95%) target. The Nb target was pre-sputtered by discharging with Ar gas for 300 s to remove the surface NbOx layer, then a Nb interlayer was deposited on the steel substrate for 60 s in order to improve NbC adherence to the substrate (Borawski et al., 2011; Gerth & Wiklund, 2008; Hong et al., 2010). Then, discharge with the mixed Ar and CH4 gases was carried out for 390 s. The applied current on the Nb target was 0.3 A, the total pressure was 0.86 Pa, the Ar flow was 22.0 sccm, and the CH4 flow was 0.008 sccm. The very low flow of CH4 was established after several trial-and-error experiments to overcome a problem of target poisoning by CH4 saturation that hampered the steady-state reaction between Nb and C. Poisoning occurred because with the equipment used was not able to operate at a faster pumping speed. The Bi coatings were deposited by a discharge of Ar (99.999%) with Bi (99.95%) target used as the source material. The target current was 0.11 A, the work pressure was 0.5 Pa, and the Ar flow was 9.0 sccm. The NbC coating had an approximate deposition rate of 29 nm min-1 while the Bi coatings were deposited at 350 nm min-1. As a reference, in Table 1 are listed the hardness values of the materials involved in the present work.
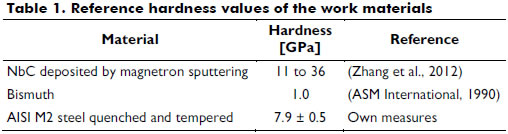
An Xpress Revetest CSM was used as a scratch tester using a 0.2 mm tip radius Rockwell C diamond indenter, under a loading rate of 100 N min-1, a sliding speed of 10 mm min-1 and a scratch length of 9 mm. The crystallographic structure of the films was investigated using a X-PertPro Panalytical X-ray diffraction (XRD) system using Cu Kα radiation (1.5418 Å) with the 2θ/θ set-up over a 20-80o range. An Asylum Research MFP3D-Bio atomic force microscope (AFM) was used to observe the surface morphology and to measure the surface roughness.
The tribological properties of the films were determined using a CETR-UMT-2-110 ball-on-disk tribometer in the unidirectional speed mode with a 6 mm Al2O3 ball as the sliding counterpart in air (293 K temperature, 41-52% humidity). We used the alumina ball because it has a higher hardness than the substrate and the NbC, and in this initial study we primarily intended to observe the wear of the coating and the substrate without significant influence of debris and wear of the test ball. The sliding speed was adjusted at 6 m s-1, and the load was fixed at 4 N. The sliding distance was 120 m. The scratch and wear tracks were observed via stereoscopic microscopy and scanning electron microscopy (SEM) JEOL JSM 6490-LV. The energy-dispersive X-ray (EDS) analysis in the SEM was used to identify chemical elements in the wear tracks.
Results and discussion
Microstructure and morphology
Figure 1 shows the XRD patterns in a symmetric θ-2θ configuration for the coatings and the substrate. For the M2 steel substrate, the characteristic peaks of martensite (α-Fe), iron carbide M6C, tungsten carbide Fe3W3C and vanadium carbide V4C3 can be observed, which match the JCPDS (Joint Committee on Powder Diffraction Standards, 2000a, 2000b) charts 01-087-0721, 01-089-7205 and 00-001-1159, respectively. For the niobium carbide films, the cubic NbC phase is observed with a mixed texture of preferred (111) and (200) orientations although there are also evidence for (220), (311) and (222) orientations (JCPDS card No. 38-1364). The crystallite size calculated from Scherrer's formula (Guinier, 1963) was 26.96 nm, and this value is an approximated reference value because it is assumed that there are no microdeformations. The lattice parameter calculated from Bragg's law (4.4634 Å) is smaller than that reported in JCPDS card No. 38-1364 (4.4698 Å), indicating the existence of compressive intrinsic stresses in agreement with the report by Zhang et al. (Zhang et al., 2012) on niobium carbide coatings also deposited by sputtering on silicon substrates. The texture coefficient calculated for the [111] direction was 2.79, indicating a strong orientation in this direction, which is similar to the case of transition metal nitride films with thicknesses less than 500 nm that have the lowest strain energy in the (111) orientation (Braic et al., 2011; Zhang et al., 2012). Based on the carbon-niobium binary phase diagram and on the NbC phase obtained, it can be estimated that the carbon content is between 40 and 50%. (Kimura & Sasaki, 1961).
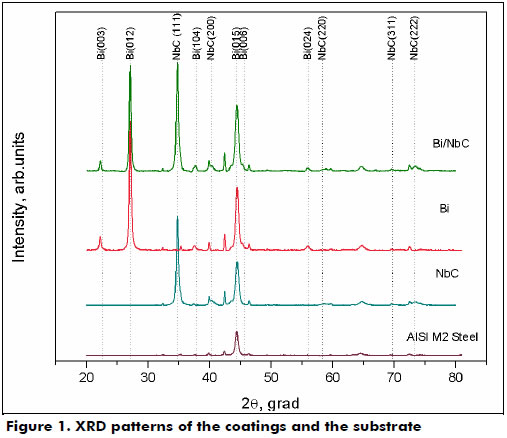
For the bismuth layers (Figure 1) the characteristic XRD peaks of the rhombohedral phase were observed (JCPDS card No. 44-1246) with (003), (012), (104), (015), (006) and (204) mixed orientations. However, as can be observed there is a preferential (012) texture, and this result is similar to that reported by Kim et al. (Kim et al., 2006), who deposited bismuth thin films on glass substrates by RF magnetron sputtering. The calculated crystallite size was 22.4 nm. The comparison between the calculated lattice parameters (a = 4.5297 Å, c = 11.9853 Å) with the values reported in the JCPDS No. 44-1246 chart (a = 4.5460 Å, c = 11.8600 Å) indicate the existence of a combination of intrinsic stresses. For the Bi/NbC coating (Figure 1), peaks are observed from Bi, NbC and the steel substrate. The overlaps in the peaks of the three materials were resolved by applying deconvolution using Origin software.
AFM micrographs of the NbC, Bi/NbC and Bi coatings are show in Figure 2. In other works, it was reported that increasing the absolute value of the bias voltage produces smoother NbC films (Zhang et al., 2012), but that increasing the growth temperature produces greater film roughness due to an increased in grain size (Zoita et al., 2010).
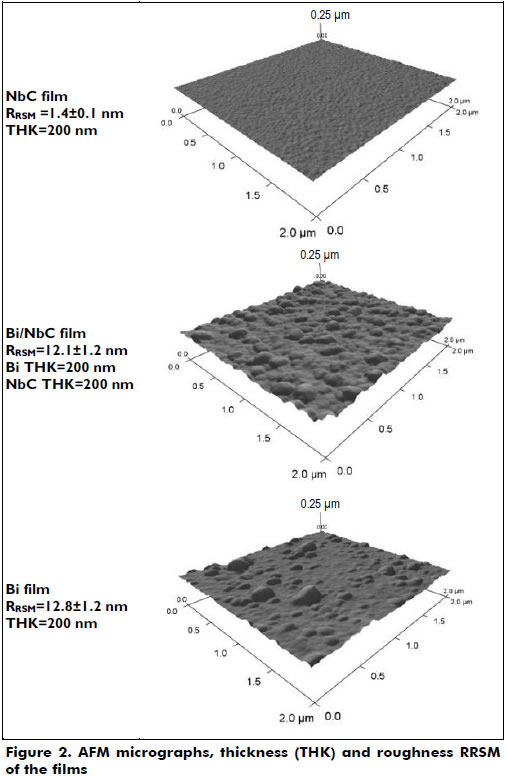
The produced NbC coating (Figure 2) had a smooth surface composed of small peaks with a low roughness value (RRSM =1.4 nm). Although this NbC coating was produced with zero bias voltage, the low roughness obtained is explained by the low temperature of deposition and also by the high Ar gas concentration used, which produces large amounts of Ar+ ions that erode the protrusions on the surface. The effect of high Ar concentration on lowering the roughness was also reported in studies of C:H films produced by unbalanced magnetron sputtering (Dai et al., 2008). In the Bi/NbC coating (Figure 2) a surface topography was observed with particles of homogenous size distributed homogeneously. This coating had a higher roughness (RRSM =12.1 nm) than the NbC coating. The monolayer bismuth coating (Figure 2) has a similar roughness (RRSM =12.8 nm) but with particles of heterogeneous size. These results are in line with the report of Sande et al. (Sande et al., 1996) who stated that bismuth films deposited by DC sputtering showed a high surface roughness, related both to columnar growth and to the presence of abnormally large grains. A similar result was also reported by Kim et al. in studies of bismuth films deposited by RF sputtering (Kim et al., 2006).
Scratch testing of the coatings
The film adhesion was evaluated by scratch testing. In Figure 3 are shown example optical micrographs of the scratch tracks on the NbC, Bi and Bi/NbC coatings. The first fault load (Lc1) was determined visually at the point on the track where the film was pulled off from the substrate with adhesive failure of the flaking.
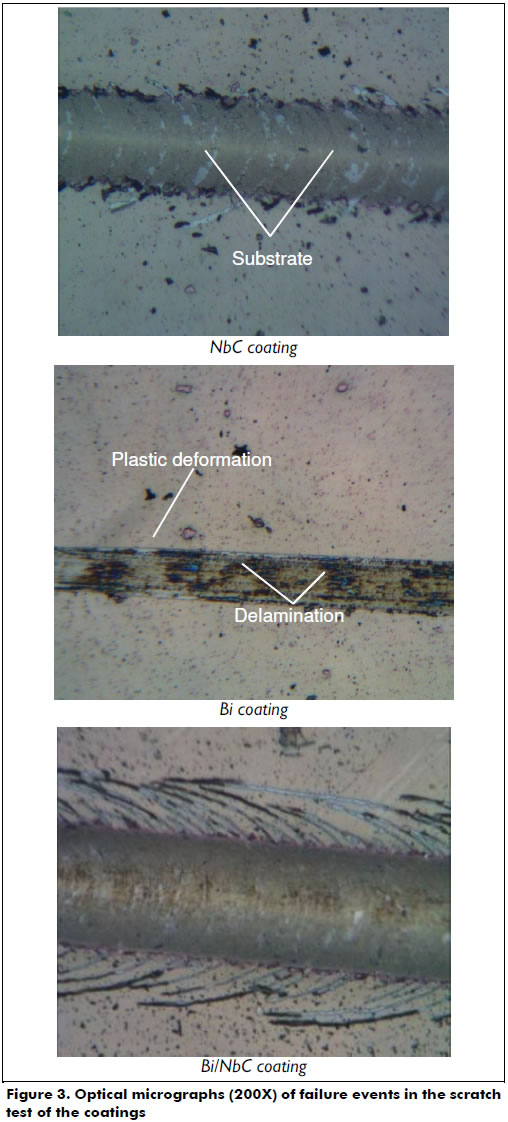
The critical load characteristic of total failure of the coating (Lc2) was determined visually at the point on the track where the complete failure of the coating initiated at the first full contact of the diamond stylus with the substrate. In Figure 3 it is observed that the NbC coating exhibited good adhesion with the steel substrate (Lc1= 10 ± 1.1 N, Lc2= 25 ± 3 N). This good adhesion is seen because the ductile Nb interlayer reduces the shear stress in the coating-substrate interface (Borawski et al., 2011; Gerth & Wiklund, 2008; Hong et al., 2010). A protective effect of the bismuth on the Bi/NbC coating could be verified because both critical loads related to the NbC layer of this coating were higher (Lc1= 30 ± 4 N, Lc2= 45 ± 5 N). In the Figure 3 it is observed that soft Bi layer on the harder substrates exhibit plastic deformation and thinning over the track. The Bi coating had better adhesion with the NbC layer (Lc1= 3.0 ± 0.5 N, Lc2= 14 ± 2 N) than with the steel substrate (Lc1= 2.0 ± 0.25 N, Lc2= 4.5 ± 0.3 N), and this fact is probably because the Bi lattice parameters (rhombohedral, a = 4.5460 Å) are closer to those of NbC (4.4698 Å) than those of steel.
Tribological behavior
Figure 4 shows the coefficient of friction (COF) for the NbC, Bi and Bi/NbC coatings against the Al2O3 ball as a function of sliding distance. As a reference the final stable value obtained for the M2 steel is also included. For the NbC coating a COF between 0.3 and 0.35 has been obtained, in the case of Bi/NbC coating its COF is lower than that of the NbC coating until a distance of 80 m possibly due to a retardant effect of direct contact with the ball produced by the Bi layer.
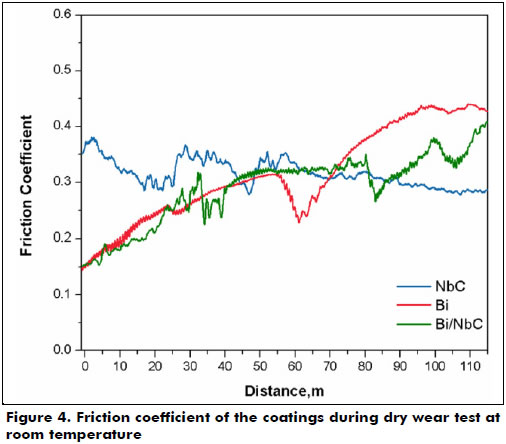
It is worth noting that for the NbC and Bi/NbC films the COF evolution is accompanied by a rattling, which might be because the as-deposited NbC film is partially flaked away until direct contact between the ball and the substrate. Zhang et al. (Zhang et al., 2012) assessed the wear resistance of NbC coatings obtained by sputtering and found a COF of 0.25 with roughness values of the coating between 0.854 nm and 5.69 nm. The results of these authors are similar to the results obtained in this investigation. The COF of the Bi coating exhibits a relatively smooth increase until 55 m at which point it decreases to a minimum at 60 m and again experiences sustained growth until the end of the test. This fluctuation is probably because, substrate exposure occurred at 55 m and continued until complete exposure at the end of the test.
Figure 5 exhibits SEM images with EDS analysis of the wear track after 120 m sliding for the three coatings. The Bi coating was almost completely removed though laminated segments of Bi are observed in the wear track. Those segments exhibit severe plastic deformation produced by sliding contact with the ball. The smooth increase in COF on the Bi coating corresponds to its progressive delamination accompanied by plastic deformation until it had been almost completely removed at the end of the test.
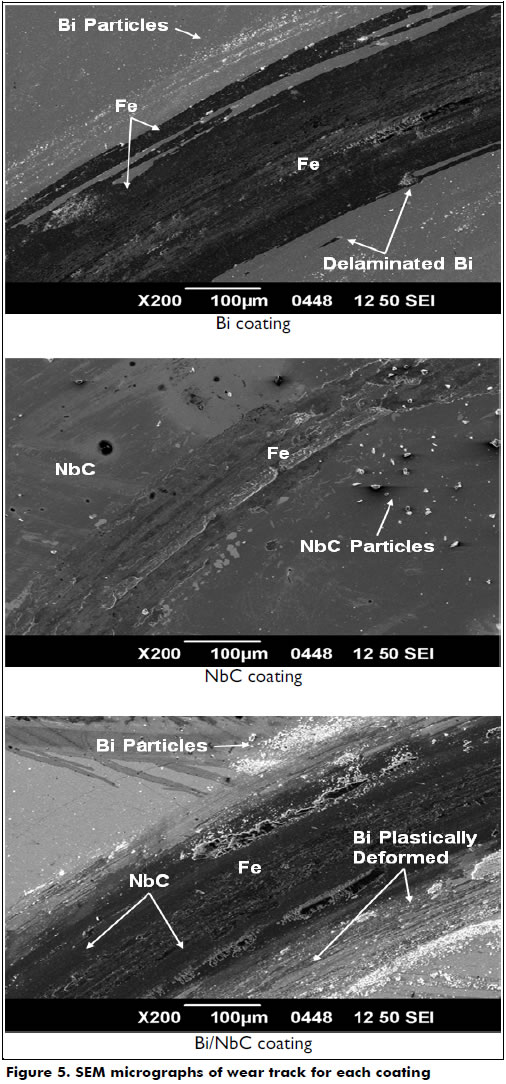
In the wear track of the NbC coating (Figure 5), there is much less substrate exposure than for the Bi coating, NbC particles removed by abrasion are also observed which might be because, during the wear testing, microcracks initiated after several sliding cycles and readily propagated, leading to spalling and delamination of the hard film from the substrate. The repeated deflection of the hard NbC coating onto the tougher steel substrate causes nucleation and propagation of cracks that ultimately lead to detachment of coating particles (Holmberg & Matthews, 1994). In the wear track of Bi/NbC coating severe plastic deformation is observed in the Bi layer and also small Bi particles removed from the surface and located on the border of the wear track can be seen. Also, the worn area of the NbC layer is seen to exhibit spalling and delamination as well as the smaller substrate exposure of the three coatings. Apparently, for the Bi/NbC coating, where the Bi layer had slightly better adhesion, the particles that had been removed from Bi layer offered an additional protection against the direct contact between the ball and the NbC layer. Although the presence of Fe is observed in the traces of the three coatings, the COF increase was not significant because the remaining coating exerted influence on the overall system performance. Sen & Sen (Sen & Sen, 2005) applied the pin-on-disk test to NbC coatings obtained by reactive thermodiffusion. For the test with an alumina ball, they observed abrasive wear with oxidation, while in the test with a steel ball they observed adhesive wear with more oxidation. According to these authors, the fracture of the formed iron oxide increased the friction coefficient, especially in the test with steel ball.
In Figure 6 is illustrated the calculated wear rate for each coating after the pin-on-disk test. The Bi/NbC coating had the lowest wear rate followed by the NbC coating. The Bi coating apparently had a wear rate similar to that of the steel substrate, but this result actually reflects that this coating alone was quickly removed and offered little protection to the substrate. The wear resistance of the NbC coating is consistent with its high hardness (see Table 1), and the lubricating effect provided by the Bi in the Bi/NbC system is also clear.
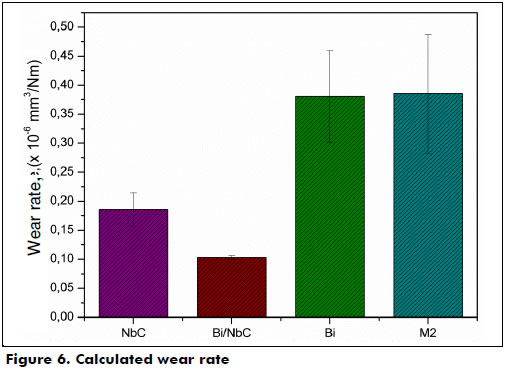
Conclusions
NbC, Bi and Bi/NbC coatings were deposited onto AISI M2 steel substrates using unbalanced magnetron sputtering at room temperature with zero bias voltage. The phase structure, morphology, adhesion and tribological behavior of the three coatings were examined. The niobium carbide crystallized in the cubic structure with a particularly strong (111) texture. The bismuth layers had a rhombohedral phase with random orientation but with preferential (012) texture. The NbC coating had a smooth surface with low roughness, which is explained by the low temperature of deposition and also by the high Ar gas concentration used. The Bi layer on steel and on the Bi/NbC coating had higher roughness than the NbC coating on steel. The morphology of the Bi layer was characterized by large particles distributed homogeneously. By using a ductile Nb interlayer was achieved good adhesion between the NbC coating and the steel substrate. The Bi coating had better adhesion with the NbC layer than with the steel substrate. Mainly due to low adhesion of the Bi coating deposited directly onto the steel substrate, its tribological performance was not satisfactory. The produced NbC coating have the potential to protect the steel from wear, and the Bi layer on the Bi/NbC coating has a moderately beneficial effect as evidenced by the lower exposure of the substrate at the end of the wear tests.
Acknowledgments
This work was financed by the Research Direction of the Bogotá campus of the Universidad Nacional de Colombia (DIB-15859 project) and by the project FP7-NMP-2010 EU-Mexico (Grant Agreement No. 263878).
References
Amriou, T., Bouhafs, B., Aourag, H., Khelifa, B., Bresson, S., & Mathieu, C. (2003). FP-LAPW investigations of electronic structure and bonding mechanism of NbC and NbN compounds. Physica B: Condensed Matter, 325, 46-56. doi:10.1016/S0921-4526 (02)01429-1 [ Links ]
Arias, J., Cabeza, M., Castro, G., Feijoo, I., Merino, P., & Pena, G. (2010). Modificación de los aceros rápidos de herramientas AISI M2 por fusión superficial con láser bajo diferentes condiciones de operación. Revista de Metalurgia, 46(3), 206-218. [ Links ] doi:10.3989/revmetalm.0918
Bendavid, A., Martin, P., Kinder, T., & Preston, E. (2003). The deposition of NbN and NbC thin films by filtered vacuum cathodic arc deposition. Surface and Coatings Technology, 163-164, 347-352. doi:10.1016/S0257-8972(02)00623-0 [ Links ]
Boffoue, M. O., Lenoir, B., Scherrer, H., & Dauscher, A. (1998). Pulsed laser deposition of bismuth in the presence of different ambient atmospheres. Thin Solid Films, 322(1-2), 132-137. doi:10.1016/ S0040-6090(97)00912-7 [ Links ]
Borawski, B., Todd, J. A., Singh, J., & Wolfe, D. E. (2011). The influence of ductile interlayer material on the particle erosion resistance of multilayered TiN based coatings. Wear, 271(11-12), 2890-2898. doi:10.1016/j.wear.2011.06.004 [ Links ]
Braic, M., Braic, V., Balaceanu, M., Vladescu, A., Zoita, C. N., Titorencu, I., & Miculescu, F. (2011). Preparation and characterization of biocompatible Nb-C coatings. Thin Solid Films, 519(12), 4064-4068. doi:10.1016/j.tsf.2011.01.193 [ Links ]
Carrera, S., Salas, O., Moore, J. J., Woolverton, A., & Sutter, E. (2003). Performance of CrN/MoS2(Ti) coatings for high wear low friction applications. Surface and Coatings Technology, 167(1), 25-32. doi:10.1016/S0257-8972(02)00885-X [ Links ]
Dai, H., Jiang, H., Zhan, C., & Huang, N. (2008). Effects of Ratio of Mixed Gases on the Surface Roughness and Nano-hardness of aC: H films. Journal of the Korean Physical Society, 52, s124-s127. Retrieved from http://www.kps.or.kr/jkps/downloadPdf.asp?articleuid=%7BBF83594F-722E-4862-9228-031C88CF173D%7D [ Links ]
Daming, Z., Jiajun, L., Baoliang, Z., & Wenzhi, L. (1997). A study of the friction and wear performance of MoS thin films produced by ion beam enhanced deposition and magnetron sputtering. Wear, 210(1-2), 45-49. doi:10.1016/S0043-1648(97)00039-2 [ Links ]
Derflinger, V., Brändle, H., & Zimmermann, H. (1999). New hard/lubricant coating for dry machining. Surface and Coatings Technology, 113(3), 286-292. doi:10.1016/S0257-8972(99)00004-3 [ Links ]
Eisenbarth, E., Velten, D., Müller, M., Thull, R., & Breme, J. (2004). Biocompatibility of beta-stabilizing elements of titanium alloys. Biomaterials, 25(26), 5705-5713. doi:10.1016/j.biomaterials.2004.01.021 [ Links ]
Gerth, J., & Wiklund, U. (2008). The influence of metallic interlayers on the adhesion of PVD TiN coatings on high-speed steel. Wear, 264(9-10), 885-892. doi:10.1016/j.wear.2006.11.053 [ Links ]
Guinier, A. (1963). X-ray Diffraction in Crystals, Imperfect Crystals and Amorphous Bodies. San Francisco: W. F. & Company. [ Links ]
Haider, J., Rahman, M., Corcoran, B., & Hashmi, M. S. J. (2005). Deposition and characterization of hard-solid lubricant coating by closed-field magnetron sputtering. Surface and Coatings Technology, 200(1-4), 1080-1083. doi:10.1016/j.surfcoat.2005.02.058 [ Links ]
Hofmann, Ph. (2006). The surfaces of bismuth: Structural and electronic properties. Progress in Surface Science, 81(5), 191-245. doi:10.1016/j.progsurf.2006.03.001 [ Links ]
Holmberg, K., & Matthews A. (1994). Coatings Tribology: Properties, Techniques and Applications. In D. Dowson (Ed.), Tribology Series 28 (pp. 1-441), Amsterdam: Elsevier. [ Links ]
Hong, Y. S., Kwon, S. H., Wang, T., Kim, D., Choi, J., & Kim, K. H. (2010). Effects of Cr interlayer on mechanical and tribological properties of Cr-Al-Si-N nanocomposite coating. Transactions of Nonferrous Metals Society of China, 21(1), s62-s67. doi:10.1016/S1003-6326(11)61062-5 [ Links ]
Joint Committee on Powder Diffraction Standards. (2000a). Diffraction Data File 38-1364. Newtown Square, PA: International Centre for Diffraction Data. [ Links ]
Joint Committee on Powder Diffraction Standards. (2000b). Diffraction Data File 44-1246. Newtown Square, PA: International Centre for Diffraction Data. [ Links ]
Kim, D.-H., Lee, S.-H., Kim, J.-K., & Lee, G.-H. (2006). Structure and electrical transport properties of bismuth thin films prepared by RF magnetron sputtering. Applied Surface Science, 252(10), 3525-3531. doi:10.1016/j.apsusc.2005.05.046 [ Links ]
Kimura, H., & Sasaki, Y. (1961). The Phase Diagram of the Niobium-Carbon system. Materials Transactions JIM, 2(2), 98-104. Retrieved from https://www.jim.or.jp/journal/e/2/02/98.html [ Links ]
Krahmer, D. M., Russo, D., Egidi, D., Traverso, M. G., Corengia, P., & Cabo, A. (2003). Rendimiento de brocas helicoidales de acero AISI M2 nitruradas por plasma DC-pulsado y sin nitrurar. In Actas de las Jornadas SAM/ CONAMET/ Simposio MATERIA (pp. 4-7). San Carlos de Bariloche, Argentina: Asociación Argentina de Materiales [ Links ]
Kumari, L., Lin, S.-J., Lin, J.-H., Ma, Y.-R., Lee, P.-C., & Liou, Y. (2007). Effects of deposition temperature and thickness on the structural properties of thermal evaporated bismuth thin films. Applied Surface Science, 253(14), 5931-5938. doi:10.1016/j.apsusc.2006.12.125 [ Links ]
Renevier, N. M. U., Fox, V. C., Teer, D. G., & Hampshire, J. (2000). Performance of low friction MoS2/titanium composite coatings used in forming applications. Materials and Design, 21(4), 337-343. doi:10.1016/S0261-3069(99)00083-7 [ Links ]
Sande, de J. C. G., Missana, T., & Afonso, C. N. (1996). Optical properties of pulsed laser deposited bismuth films. Journal of applied physics, 80, 7023-7027. doi: http://dx.doi.org/10.1063/1.363775 [ Links ]
Sen, S., & Sen, U. (2008) Sliding wear behavior of niobium carbide coated AISI 1040 steel. Wear, 264(3-4), 219-225. doi:10.1016/j.wear.2007.03.006 [ Links ]
Sustarsic, B., Jenko, M., Godec, M., & Kosec, L. (2003). Microstructural investigation of NbC-doped vacuum-sintered tool-steel-based composites. Vacuum, 71(1-2), 77-82. doi:10.1016/S0042-207X(02)00717-0 [ Links ]
Teer, D. G., Hampshire, J., Fox, V., & Bellido-Gonzalez, V. (1997). The tribological properties of MoS2/metal composite coatings deposited by closed field magnetron sputtering. Surface and Coatings Technology, 94-95, 572-577. doi:10.1016/S0257-8972(97)00498-2 [ Links ]
Trent, E. M., & Wright, P. K. (2000). Cutting Tool Materials I: High Speed Steels. In Metal Cutting (pp. 132-174), Woburn, MA: Butterworth-Heinemann [ Links ]
Waghray, H., Lee, T., & Tatarchuk, B. J. (1995). A study of the tribological and electrical properties of sputtered and burnished transition metal dichalcogenide films. Surface and Coatings Technology, 76-77(2), 415-420. doi:10.1016/0257-8972(95)02564-2 [ Links ]
Watanabe, S., Noshiro, J., & Miyake, S. (2004a). Friction properties of WS2/MoS2 multilayer films under vacuum environment. Surface and Coatings Technology, 188-189, 644-648. doi:10.1016/j.surfcoat.2004.07.029 [ Links ]
Watanabe, S., Noshiro, J., & Miyake, S. (2004b). Tribological characteristics of WS2/MoS2 solid lubricating multilayer films. Surface and Coatings Technology, 183(2-3), 347-351. doi:10.1016/j.surfcoat.2003.09.063 [ Links ]
Zhang, K., Wen, M., Meng, Q. N., Hu, C. Q., Li, X., Liu, C., & Zheng, W. T. (2012). Effects of substrate bias voltage on the microstructure, mechanical properties and tribological behavior of reactive sputtered niobium carbide films. Surface and Coatings Technology, 212, 185-191. doi:10.1016/j.surfcoat.2012.09.046 [ Links ]
Zhao, Y., Zhang, Z., & Dang, H. (2004). A simple way to prepare bismuth nanoparticles. Materials Letters, 58(5), 790-793. doi:10.1016/j.matlet.2003.07.013 [ Links ]
Zoita, C. N., Braic, L., Kiss, A., & Braic, M. (2010). Characterization of NbC coatings deposited by magnetron sputtering method. Surface and Coatings Technology, 204(12-13), 2002-2005. doi:10.1016/j.surfcoat.2009.08.050 [ Links ]