Introduction
Ceramic and hydrated cements are the most recognized products of inorganic solids. Ceramics are obtained by compaction of powders and subsequent sintering at high temperatures, resulting in hard and dense ceramics with good properties against corrosion. Its structure is usually highly crystalline with vitreous phases, presenting ionic and covalent bonds. Hydrated cements are chemically-bonded materials with hydrogen bonds that are formed by the chemical reaction of water with some characteristic powders that harden at room temperature, obtaining a product with sufficient compressive strength, to be used in structural applications (Wagh, 2016). These cements are usually united by van der Waals forces, exhibiting a non-crystalline, very porous structure. It is worth noting that the most noticeable difference between ceramics and hydrated cements lies in their consolidation process as a material. To obtain ceramic hard products, materials must be exposed to high temperatures. In contrast, hydrated cements reach hardness at room temperature (Wagh, 2016), although raw materials are subjected to high temperatures for their manufacture and considerable energy consumption is needed to obtain the clinker (Schneider, Romer, Tschudin, and Bolio, 2011), which is the main component of conventional Portland cement.
However, there is an intermediate product among those mentioned above, which consolidates similarly to a hydraulic cement, but resists and behaves structurally as a ceramic. As it presents bonds of the ionic and covalent type, its structure varies from very crystalline to vitreous, showing compressive strengths similar to conventional cement and setting times faster than hydraulic cements (Wagh, 2016). This intermediate product that contains crystalline or noncrystalline phases and sets at temperatures close to that of the environment is known as chemically-bonded ceramics (CBC) (Roy, 1987; Wagh, 2013).
The chemically-bonded phosphate ceramics (CBPC) are a specific type of chemically-bonded ceramics (CBC), formed from reactions of phosphate anions with metal cations. The CBPC have had an important development in the last two decades, mainly due to the search for environmental alternatives for the manufacture of cements (Wagh, 2013).
A significant environmental impact in terms of energy consumption and generation of greenhouse gases is a widely known result of the production of conventional Portland cement (Habert, Billard, Rossi, Chen, and Roussel, 2010; Gartner, 2004). Therefore, the search for different cement alternatives that are friendly to the environment has led researchers to coin the term "eco-efficient cements" or "green cements". Magnesium phosphate cements are recognized as eco-efficient commercial products, due to their low environmental impact, in addition to their good mechanical performance, availability of raw materials and manufacturing facility. Under the names of "Ceramicrete" and "Grancrete", these types of cements are some of the more promising eco cements (Imbabi, Carrigan, and McKenna, 2012).
There is a positive impact of phosphate cements in the environmental context (Wagh, 2013). This article reviews the mechanical performance of phosphate cements and their structural requirements in contrast to Portland-type conventional cements.
Acid-base reaction system of chemically-bonded ceramics (CBC)
Chemically-bonded ceramics are structured as an acid-base reaction. These reactions originate from a base, usually powders of a metal oxide or a silicate, with an acid. The product of the reaction is a complex salt that acts as binding agent or cementing matrix, besides the presence of water. The excesses of the alkaline base that do not react become part of the cement fillers. The great majority of these reactions are fast and exothermic (Wilson and Nicholson, 1994).
The process for forming cements under the acid-base reaction system is described below (Wilson and Nicholson, 1993) and illustrated in Figure 1 (Wagh, 2004).
Dissolution of the alkaline base in an acid solution, to facilitate the formation of cations.
Interaction of anions and cations in the solution to form neutral compounds.
Gelification of the compound and saturation of the solution with the compound.
Precipitation of solids in the saturated gel solution forming connected networks of the types: crystalline, semicrystalline and disordered solids.
In the specific case of phosphate cements, the reactions to combine the cations and phosphate anions can take place in solution at normal or hydrothermal pressures or by combinations at high temperatures to overcome the kinetic barriers. The transformations of phosphates into new structures can be achieved thermally or through ion exchange reactions (Attfield, 2001).
Chemically-bonded phosphate ceramics (CBPC) or phosphate cements
Phosphate cements are essentially an acid-base system that reacts at room temperature (Wagh, 2016). These cements are formed by the reaction of phosphoric acid or an acid phosphate with metal oxides, where the acid component contributes to the phosphate anions and the basic component to the metal cations, necessary for the cement shaping reaction (Figure 2).
Although phosphate cements are more expensive than Portland cements, the former are projected as one of the special cements with the highest development potential (Attfield, 2001; Glasser, 2011). Some of the main reasons are the ease and safety to handle their reagents and that they are non-toxic and stable at high temperatures (1 000 °C) (Attfield, 2001) and have a wide pH range, available raw materials and low environmental impact, in addition to good reported mechanical properties. Five types of cement are recognized as typical phosphate cements: magnesium phosphate, calcium phosphate, zinc phosphate, aluminum phosphate and iron phosphate. Among them, magnesium and calcium phosphate cements stand out for having the highest development in structural applications. Some of the reactions and main products responsible for the mechanical properties in phosphate cements have been presented by Wagh (2016) and Alshaaer, Cuypers, Mosselmans, Rahier and Wastiels (2011), and are listed in Table 1.
Environmental impact of phosphate cements and Portland cements
It is unfeasible to establish a definitive relation of the environmental impact of phosphate cements compared with Portland, due to the low development of the former. However, some of the phosphate cements with the highest impact and development are magnesium phosphate cements, which can be used as reference, specifically the commercial application Ceramicrete with the addition of fly ash, for a comparison with Portland cements. Production of greenhouse gases for Ceramicrete consists mainly in carbon dioxide, under two premises. First, there are greenhouse gases produced in the transformation of raw materials, that is, by the decarbonization of limestone and dolomite, called direct emissions. Second, some gases are associated with the combustion of fossil fuels in different stages of the process, such as calcination, milling, screening, transport and packaging among others. These are called process emissions, in addition to the energy consumed in the transformation processes to obtain the cements (Wagh, 2013). Wagh (2013) establishes a first approach to the environmental impact of the phosphate cements. Table 2 presents a parallel comparing the environmental impact of the two technologies. This parallel allows to conclude that the energy consumed and the greenhouse gases released by the processes of magnesium phosphate cement are approximately 40% less, in comparison with conventional Portland technology (Wagh, 2016).
In addition, phosphate cements can be referred to as eco-efficient or eco-friendly products. Several authors have tried to link alternative raw materials and additives of low environmental impact in the formation of cements. The review of some researches evidenced the use of substitute raw materials that reduce manufacturing costs and reuse of industrial waste as source of raw materials (Formosa et al., 2008; Gardner et al., 2015; Choi, Um, and Choung, 2014; Kinnunen et al., 2018). This fact has a substantial impact, since it allows to diminish the environmental impact produced by the exploitation and transformation of conventional raw materials.
Table 2 Environmental impact of the production of phosphate cements
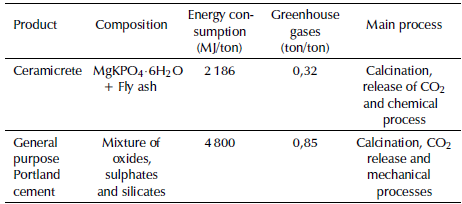
Source: Adapted from Wagh (2016)
Biomaterials of phosphate cements
There is a group of phosphate cements that exhibit relevant mechanical properties, although it is not completely applicable in civil engineering. These cements have generated a great scientific interest in recent years (Dorozhkin and Epple, 2002; Al-Sanabani, Madfa, and Al-Sanabani, 2013; Viani, Sotiriadis, Kumpová, Mancini and Appavou, 2017). The applications are confined to the human body due to biocompatibility, among other reasons. This group of phosphate cements is identified in the group of biomaterials, briefly described below.
Dental cements: Zinc phosphates
Zinc phosphate cements are the oldest known dental cements, as they were developed in 1880. Although at present they are not widely used in comparison with new materials that have emerged (Viani et al., 2017), they still find a subsistence niche in cemented restorations.
Dental cements of zinc phosphate are obtained by mixing phosphoric acid and zinc oxide. Due to the strong reaction that originates, aluminum hydroxide has been used to neutralize the reaction. These cements have reached compressive strengths between 71 and 131 MPa and tensile strength between 4,3 and 8,3 MPa (Wagh, 2016). Dental porcelain cements consisting of alumina, vitreous silica, calcium oxide, sodium oxide, fluorine, zinc oxide and phosphoric acid are probably the inorganic cements with the highest reported mechanical strength. They have a compression strength of 255 MPa, bending stress of 24,5 MPa and tension of 13,6 MPa. However, the fracture tenacity of 0,12 to 0,3 MPa/m2 indicates the fragility of this cement (Wagh, 2016).
Cements for orthopedic applications: Calcium phosphates
Calcium phosphate cements mainly precipitate as hydroxyapatite, which is a basic mineral constituent of the bones. That is why this type of cement will always be one of the main alternatives of use in this field. In addition, these cements are easily grafted with rapid hardening in the bones of the human body and minimal intrusion implications. These cements are used in special applications such as bone augmentation, bone reinforcement, metal implant fixation and spinal fractures (Ginebra, Canal, Espanol, Pastorino, and Montufar, 2012).
The cortical bone is the external part of the bone that represents its main mechanical properties. Table 3 describes these properties compared to calcium phosphate cement. The main aspect is the similarity in the density of these two materials, which is inferior when compared with typical metal prostheses such as titanium (A. Wagh, 2004). There are also great similarities in compression strength and Young's modulus. Advances in future research are expected to improve resistance to stress and fracture.
Table 3 Mechanical properties of calcium phosphate cements
Property | Cortical bone | Calcium phosphate cement |
---|---|---|
Specific Gravity (g/cm3) | 1,7-2,1 | 1,7-2,0 |
Tensile Strength (MPa) | 60-160 | 2,1-14 |
Compressive strength (MPa) | 13-18 | 20-91 |
Young's Modulus (GPa) | 3-30 | 35-105 |
Fracture energy (J/m2) | 390-560 | - |
Resistance to fracture (Mpa/m2) | 2-12 | 0,3-0,8 |
Composition | Inorganic + organic | Inorganic |
Source: Adapted from Wagh (2016)
Phosphate cement for structural applications
Research in phosphate cements began at the start of the 20th century and resulted in the main development of dental cements and biocements. In the year 2003, Wagh, Grover and Jeong published a literature review of abstracts of articles from the years 1988-2002 (Table 4). They described the low percentage of research developed in structural applications. Only 5,6% of applications are structural, perhaps due to the difficulty of industrially scaling this type of cement, where production volumes are considerable. However, the low percentage can also suggest an important development potential.
Table 4 Phosphate Cement Research
Items | Percentage |
Articles on biomaterials and dental cements | 68% |
Structural materials | 5,6% |
Refractory materials | 12,6% |
Structure of materials, properties, etc. | 13,9% |
Total number of articles found relevant to low temperature | 100% |
phosphate cements and ceramics (2 264) |
Source: Adapted from Wagh (2016)
The first cements for structural purposes were developed at Brookhaven National Laboratory (BNL) in the United States (1970). Looking for applications of magnesium phosphate cements, aluminum, pb and iron phosphates were also researched without finding practical applications at the structural level. From the Argonne National Laboratory research in the decade of1990, the possibilities ofapplication of magnesium phosphate cements for structural uses were extended, specifically in the immobilization of dangerous and radioactive waste (Wagh, 2016). The research developed in the Argonne National Laboratory, which is evidenced by numerous publications and patents, is substantiallyimportant to describe the progress of this type of material.
Trying to define a frame that contains the generalities of the mechanical properties of the phosphate cements is a complex challenge, because phosphate cements have a great variability of compositions, offering a wide range of mechanical properties. However, the significant development experienced by magnesium phosphate and calcium phosphate cements can be used as reference to explain the mechanical behavior of these compounds. Table 5 presents a general framework of phosphate cements, with the purpose of contrasting their main differences and similarities.
In many cases, phosphate cements show mechanical properties superior to the conventional Portland cements. However, producing phosphate cements as commercial products (pastes, mortars and concretes) is more expensive than producing a conventional cement. Therefore, specific applications with added value are projected as commercially viable possibilities (Wagh, 2013).
Magnesium Phosphate Cements
Phosphate cement pastes: Phosphate cement pastes comprise the reaction between the acidic and basic components without other additional components. This frames the fundamental model for the analysis and understanding of these cements. However, in practical terms, making cements with only these components promotes additional costs that oppose to the approach of making products of this type of cements more commercially available. Below significant findings are explained on their mechanical properties.
The proportion of raw materials is an important factor that requires differences in terms of mechanical strength. A. Wang, Yuan, et al. (2013) calcined the MgO (1 200 °C) for 3 hours and dried particles of KH2PO4 (100 °C) as acidic component for 6 hours. Then, by grinding, they pre-mixed the two components and dried them for 3 hours forming a powder compound (grams) that was mixed with deionized water in different proportions. The optimum liquid - solid ratio was 1:7, keeping the mixture under stirring until solidification, and the optimum ratio for the MgO/KH2PO4 was 4:1, registering compressive strengths close to 40 MPa (A. Wang, Yuan, et al., 2013). These same authors studied the liquid-solid relationship. They used KH2PO4 and MgO in a weight to weight ratio of 1:1, which constituted the solid component, and used deionized water as liquid component, reporting the formation of cements for liquid (milliliter)-to-solid (grams) ratio of 1:4, 1:3, 2:5, 1:2, 3:5 and 2:3, with compressive strengths between 8 MPa and 22 MPa . The study showed that the compressive strength increased as the water content decreased, linking low porosities with high mechanical resistance (A. Wang, Zhang, Li, Ma, and Liu, 2013).
Composite cements (mortars, concretes and others): Phosphate cements also form composite materials similar to Portland cement mortars and concretes. Del Valle et al. formed a composite material from the magnesium phosphate cement matrix and hemp fibers (Hemp) as a structural phase. The researchers added proportions by weight (wt.%) of the fiber of 8,12,16 and 20%; although the additions with 20% do not substantially outperform mechanical performance. They offer improvements to those found in the literature (Del Valle-Zermeño et al., 2016). Maximum strength σ- MAX = 0, 71 MPa was recorded. The researchers highlight the excellent thermal and hygroscopic properties of this fiber demonstrated during the tests.
They also show that the increase of the curing time is not a significant parameter to increase the mechanical strength, however an increase in the compressive strength is obtained between 10-12% (28 days) reaching values of 79 MPa. The increase of the porosity is due to a greater amount of water and MgO, influencing a decrease in the mechanical strength (Formosa et al., 2008).
The modulus of elasticity has also been studied for the mineralogical phases of the reaction of magnesium phosphate cement, Morales et al. (2015) analyzed the mechanical behavior of the different minerals present in the cement using the Statistical Nanoindentation Technique (SNT) and Scanning Electron Microscope equipped with Energy Dispersive X-ray analysis (SEM-EDX). The elastic modulus that registered a greater resistance corresponds to the Periclase (MgO). It is a phase of aggregation or filler significantly higher than the K-struvite (KMgPO4 6H2O) that is, the cement matrix. It is worth noting the fundamental role of Periclase for the development of mechanical strength of cement (Morales et al., 2015).
Some reactive materials that are part of the acid-base system in phosphate cements, in some circumstances, can provide material that do not react by generating phases of the source material, which behave as filler, These phases of material that do not react contribute significantly to the resistant activity of the cements, classifying these mixtures as mortars (Formosa, Chimenos, Lacasta, and Niubó, 2012).
Formosa et al. (2008) proposed the evaluation of a magnesium phosphate cement, composed of potassium hydrogen phosphate (KH2 PO4) and magnesium oxide (MgO), with contribution percentages between 65%-45% (MgO) and 45%-35% (KH2 PO4) and a water/solids ratio between 0,240,28. The authors found that increasing the water content and/or magnesium oxides decreases the compressive strength.
Various composite materials have been developed from the matrix of magnesium phosphate cement. Lu, Hou, Ma, Fan, and Li (2016) added different proportions of graphene oxide in order to increase their mechanical strength, determining an ideal proportion of 5 wt.% of graphene. The addition of graphene oxide decreases the workability of the magnesium phosphate cement paste, modifying setting times from 15 minutes to 11 minutes. Likewise, fluidity decreases with the increase in graphene oxide. This is attributed to the addition of Graphene oxide that accelerates the hydration of cement by possessing a larger specific area, thus absorbing more water and generating an aggregation of the phosphate cement. The addition of graphene oxide has a negative effect on the workability, similar to what happened in Portland cement. However, the compressive and flexural strength improves, with values of 40,61 MPa and 6,82 MPa, respectively. This can also be explained by the decrease in porosity and a greater degree of hydration of the paste (Lu et al., 2016).
Active additions as in Portland technology are also used in phosphate cements. Hou, Li, Tong, and Zhang (2012) used calcined coal gangue (with 58,73% SiO2 and 26,48% Al2O3) and calcined magnesia as active addition to obtain magnesium phosphate cements. The addition of calcinated coal gangue increases the setting times from 6,5 to more than 8 minutes, since it decreases the concentration of the used acid phosphate (NH4H2PO4). With the addition of the coal gangue, the initial compressive strength (24 hours) increases slightly, then decreases. However, considerable increases in resistance are reported after day 28, reaching resistance of 95 MPa after 360 days with percentages of 10% coal gangue. The authors attribute this phenomenon, to the hydration of the gangue due to the high contents of amorphous silica and alumina (Hou et al., 2012).
Donahue and Aro (2010), applied Ceramicrete (magnesium phosphate cement binder, perfected and patented by Argonne Laboratories) and aggregates such as fly ash, OSB (oriented standard board), fiberboard chip and paper pulp waste to develop consolidated boards under pressure. Physical and mechanical properties were evaluated, complying with all the minimum requirements of the standards for low density boards, except for the modulus of rupture (MOR). The authors showed the great potential of the boards for specific applications.
Additives in magnesium phosphate cements: One of the characteristic factors of phosphate cements is the fast setting time, Formosa et al. (2015) contrasted the setting times and the mechanical properties in phosphate cement pastes added with boric acid. The cement was prepared from magnesium oxide (MgO), monopotassium phosphate (KH2PO4) and boric acid (H3BO3) as retardant. The results showed that the modulus of elasticity increased with the curing time for each formulation, but decreased in the measure that the additive (H3BO3) increased. Therefore, increasing the H3BO3 decreases the strength (Formosa et al., 2015). Likewise, applying statistical techniques such as Design of Experiments (DoE), the same authors refined the findings mentioned above, defining ideal additions of 60 wt.% magnesium oxide (MgO), 40 wt.% monopotassium phosphate (KH2PO4) and boric acid between 0,5 wt.% and 1,0 wt.%, with a liquid - solid ratio of 0,24. They obtained a cement with good workability reaching final setting times of up to 60 minutes, with constant compressive strengths since the seventh day setting higher than 40 MPa (Formosa et al., 2012).
Calcium Phosphate Cements
Calcium phosphate cements for applications in civil engineering, have been generalized under the name of IPC (Inorganic Phosphate Cement), which are made with an initial mixture of wallastonite (CaSiO3) source of calcium and phosphoric acid (H3PO4) source of phosphorus. These compounds react mainly forming brushite (CaHPO4.2H2O), in addition to amorphous silica. Alshaaer, Cuypers, Mosselmans et al., (2011) researched the mechanical response of calcium phosphate cement for high temperature applications. The researchers reported that for a temperature range between 80 and 200 °C the flexural strength decreases from 14 MPa to 7 MPa. This attributed to the appearance of microcracks due to the dehydration of brushite, a situation that does not affect the compressive strength. Between 800 and 1 000 °C, an increase in resistance is observed reaching values of 80 MPa and 12 MPa for compressive and flexural strength, respectively. This occurs due to the healing effect when reaching glass transition temperatures for some phases of the cement. Similarly, the aging effect at room temperature is described, registering an increase in compressive strength of up to 50%. Continuing with the line of research, Alshaaer Cuypers, Rahier and Wastiels (2011) proposed a new , hydrothermal post curing (HTPC) system to provide a solution to problems of dimensional and chemical stability of the IPC. With the application of the HTPC, the cement changes phase to monetite, which describes a decrease in the compressive strength of about 60%. This occurs due to the change in the pore structure, which is a situation that positively affects the flexural strength increase by 30%.
Cements reinforced with fiberglass can present problems of durability due to the chemical attack on the fiber by the hydroxide ions present in alkaline environments. Calcium phosphate cements (IPC) do not presentan alkaline environment, favoring the durability of fiberglass. Cuypers et al. (2006) researched the phosphate cement matrix added with fiberglass to study typical damage mechanisms in relation to mechanical properties. After performing simple tensile tests, Portland cement and a calcium phosphate cement (IPC) were compared, both reinforced with fiberglass. It was reported that Portland cement resistance decreased to 50% of the initial strength after an accelerated aging for 90 days, opposed to phosphate cement that maintained 90-95% of its initial resistance (Cuypers et al., 2006).
Colorado, Hiel and Han (2011) mixed nano graphite platelets into a phosphate cement paste composed of powders of wollastonite (CaSiO3) and phosphoric acid (H3PO4). They formed a composite material of IPC by a very rapid exothermic reaction that produces bubbles, which promote porosity and negatively affect mechanical strength. In addition to evaluating the effect of graphite, the authors provide information on alternative mixing methods (RAM, Resonant Acoustic Mixer), which reduce the formation of bubbles and therefore result in better mechanical characteristics. The research reported mean flexural strengths of 23 MPa and good thermal stability at high temperatures (600 °C).
Functional ceramics that exhibit additional properties to those commonly studied are also analyzed in calcium phosphate cements. Colorado et al. (2015) added on a matrix of IPC, barium titanate (BaTiO3) selected for its good dielectric properties and high thermochemical stability. They effectively showed that the dielectric constant increased as the (BaTiO3) load increased. At the same time, compression strengths of approximately 150 MPa for addition values of BaTiO3 between 15-30 wt.% were reported (Colorado et al., 2015).
Phosphate Geopolymers
The geopolymeric cements include a series of materials in which a reactive source of alumina and silica is mixed with an activator, in an aqueous solution such as sodium or potassium hydroxide and silicate (Glasser, 2011). The alkaline activation of aluminosilicates, such as fly ash or metakaolin, is widely registered to obtain inorganic products known as geopolymers. Similar to conventional geopolymers, phosphate geopolymers have been conceived. These materials have a tetrahedral molecular structure of PO45-, together with AlO43- and SiO44- as their basic components (Y.S. Wang et al., 2017).
From metakaolin and silica, fume reacted with phosphate monoaluminate (mixture of different acidic aluminum phosphates, Al(H2PO4)3, AlPO4, Al2(HPO4)3. Y.S. Wang et al. (2017) performed a geopolymer with mechanical resistances at 7 and 28 days of 7 MPa and 30 MPa, respectively. They also showed good mechanical behavior at high temperatures (1 000 °C) (Y.S. Wang et al., 2017). This geopolymer can be described as an aluminum phosphate cement.
Commercial applications
There are two types of phosphate cements in structural mechanical applications that register commercial products: potassium magnesium and potassium cements. They are developed by Argonne laboratories, who have patented a binder known as Ceramicrete and a calcium phosphate cement, widely studied by the University of Vrije Brussels, which in combination with fiberglass has resulted in a composite material that was patented under the name of VUBONITE.
The Ceramicrete has been widely disseminated in the immobilization of hazardous waste and as a material sprayed on sheets of polystyrene foam to produce housing walls that rise in record time, known as Grancrete (Wagh, 2016). Related to the Ceramicrete matrix, Qiao Chau, and Li (2010) evaluated mortars of magnesium phosphate cements as possible material for the repair of potholes or patches on the roads. They payed special attention to the relations (M/P) magnesium oxide (MgO) and potassium dihydrogen phosphate (KH2PO4), in addition to their corresponding ratio (S/B) sand and binder. They showed that these relationships influence the mechanical properties and setting times of mortars. Magnesium phosphate cement mortars showed superior bond strengths to those of mortars and Portland concretes. The pull-off tests showed flexural strengths of up to 5 MPa (28 days) in contrast to Portland mortars that reached 2 MPa at 28 curing days (Qiao et al., 2010).
The composite material, VUBONITE has had various applications in civil buildings at a structural level. De Roover et al. (2002) used this material for the construction of modular bridges, which took advantage of the tensile strength provided by fiberglass, added to the resistance to corrosion and fire of phosphate cements. In spite of the relatively low rigidity of the material, much lower than for steel or reinforced polymers, a cost-effective, resistant and easy-to-assemble bridge was made.
Immobilization of radioactive waste and hazardous elements
One of the main applications of phosphate cements has been the immobilization of radioactive waste and hazardous elements. A good number of authors have reported research in this field, in addition several to patents registered in this regard. Some of the researches carried out are cited below.
In a patent, Singh, Wagh, and Jeong (2000) present a method to produce phosphate cements and immobilize large amounts of waste of low radioactivity and hazardousness. They reported compressive strengths of 30 MPa obtained in a potassium magnesium phosphate cement (U.S. Patent No. 6,133,498, 2000). The patents of Wagh and Singh (U.S. Patent No. 5,645,518, 1997) and Wagh Singh and Jeong (U.S. Patent No. 5,830,815, 1998) disclose processes for using phosphate ceramics to encapsulate wastes, recording compressive strengths for magnesium phosphate ceramics and phosphate and magnesium ceramics of the order of2923 psi ( 20 MPa) and 6734 psi (46,4 MPa), respectively. In U.S. Patent No. 5,830,815 (1998), the inventors describe a method for producing phosphate-bonded structural products for high volumes of benign waste.
Colorado and Singh (2014) stabilized nuclear waste streams with high sodium content by means of magnesium phosphate cement, elaborated from anhydrous monobasic sodium phosphate (NaH2PO4), magnesium oxide (MgO), waste, water and fly ash as filler. The authors recorded compressive strengths obtained between 40MPa and 5MPa depending on the monobasic sodium phosphate concentration, with observed higher strength at higher concentrations. The nuclear regulation commission (NRC) establishes a minimum compressive strength of 3,45 MPa for cements for immobilization of waste. In the same line of research, Choi et al. (2014) intervened the final waste of the processing of nuclear fuels, through the development of phosphate iron cements obtained mainly from the reaction of basic steel slag (BOF Slag) and phosphoric acid (H3PO4). The slag/acid weight ratios used were 1:1,5, 2 and 2,5, registering compressive strengths between 16 MPa and 19 MPa.
Likewise, in a calcium phosphate cement matrix, lead was added to evaluate its ability to block gamma rays. The powders constituted by wollastonite (CaSiO3) and lead (in proportion of solids weight of 2%, 10% and 50%) reacted with phosphoric acid in a powder-to-acid ratio of 100:120, forming a calcium phosphate cement. The authors reported excellent gamma-ray attenuation coefficients, in addition to compression strengths close to 80 MPa for mixtures with 10% lead dust (Colorado et al., 2012).
Conclusions
In civil building applications, magnesium phosphate cement and calcium phosphate cement stand out. The mechanical strength reported in phosphate cements is important, since most of them have compressive strengths with values equal to or higher than Portland cements used for structural purposes. Besides, their low environmental impact makes cements of phosphate an important material for structural works in Civil Engineering. The final cost of phosphate cements as product is higher than the cost of a traditional Portland cement. However, new applications in specific environments, in addition to the use of fillers, can potentiate this type of cements as commercially viable products.
Phosphate cements that exhibit the best mechanical response at elevated temperatures are calcium phosphate cements, registering much higher values of compressive strength at 1 000 °C than other cements. However, they present problems of dimensional instability.
In the synthesis of composite materials with phosphate cement matrix, the reinforcement materials showed significant support to improve the mechanical resistance, while influencing the decrease in cement costs.
The presence of water is necessary for the formation of phosphate cements, especially in the dissolution of acidic compounds and it helps to provide an aqueous environment for the dissolution of the alkaline bases. The amount of water present in the mixture substantially affects the mechanical strength. Lower water contents increase the resistance to compression and produces low porosities. Water also influences as a retardant in setting. Although the curing time is not a factor of wide interest and frequent research in the available literature, it increases the compression resistance, especially after 28 curing days, and there are no significant changes for curing times of less than 7 days.
One of the most frequently used additives is boric acid. This setting retardant, in adequate proportions, increases the fluidity of cement, improving its workability. The use of this additive does not significantly influence the mechanical strengths of the cement. The durability of the phosphate cements is superior to the Portland cements, and it is another positive aspect of these materials. It presents an environment with neutral pH, which favors the inactivity of other materials present in the cement.
The most frequent application of phosphate cements is the immobilization and neutralization of hazardous and radioactive waste, in which the demands of mechanical resistance of 3,45 Mpaare not so stringent (500 psi) (Colorado and Singh, 2014).