Introduction
ENAMI (Empresa Nacional de Minería - National Mining Company) is a state-owned company from Chile, which promotes the development and growth of small and medium national mining through its metallurgical, economic, and exploration operations. The operational structure of ENAMI is directly related to the production of saleable products such as copper concentrates and copper cathodes, as well as through the purchase of minerals, concentrates, precipitates and different mining estates, including the five beneficiation plants along the country. The copper concentrates and precipitates produced and bought by ENAMI are smelted at the Hernán Videla Lira Smelter (HVL) (Herrera, 2018).
HVL smelter operations started in 1952, and, as of today, it has become a strategic pillar of ENAMI. The capacity of this smelter is 300 kt/y, it and entails concentrate smelting in one Teniente Converter (TC) of 4 x 15 m, the converting of copper matte in two Peirce-Smith converters (PSC), and the recovery of some valuable metals from slag in one electric slag cleaning furnace (SCF) Devia, Parra, Queirolo, Sánchez, and Wilkomirsky, 2019). The flowsheet of the HVL smelter is presented in Figure 1.
The main concentrate supplier from ENAMI for the HVL smelter is the Manuel Antonio Matta concentrator plant (MAM). MAM is the ENAMI main beneficiation plant. It is located 1 km away from the HVL smelter. The operation of MAM started in 1965 with a nominal capacity of 6 500 tons per month, which has increased to 110 000 tons in 2020 (Herrera, 2018).
The decrease in copper prices between 2015 and 2017 generated a decrease in the material fed to the smelter, especially in the product supplied by the MAM plant. In 2015, 100 000 tons of concentrate were produced by MAM, whereas, in 2017, it decreased to 40 000 tons. This shortage increased production costs and decreased the copper concentrate output (Tuck, 2019). The strategy adopted by ENAMI to increase the copper concentrate inventory was reflected on the evaluation and implementation of a new copper source: the flotation of copper slag (CS) from the HVL smelter by using the existing CS flotation circuit in the plant.
Background for the present study
In general, slags from the copper industry are rich in iron oxide, silica, calcium oxide, and alumina, and they are commonly deposited and stocked in landfills as their final destination. The worldwide production of slag in the copper industry is approximately 24,6 Mton, out of which 3,0 Mton is attributable to Chilean producers (Gorai, Jana, and Premchand, 2003; Valenzuela, 2016). Besides the undesirable gangue components such as oxides, silicates and amorphous glass, CS can exhibit valuable metal contents as high as 4-8 mass% Cu in converter slags, while smelter slags usually contain 1-2 mass% Cu. Copper can occur in slags as (a) dissolved copper, present mostly as Cu+ ions, and (b) mechanically entrained droplets of matte (Schlesinger, King, Sole, and Davenport, 2011).
The substantial amount of copper and the massive amount of discarded slags has motivated the reprocessing of this metallurgical waste, which nowadays represents a promising secondary source of valuable products. Additionally, a global concern about the environment and new regulations have brought a reengineering of the mining industry, aimed to integrate the concept of sustainable metallurgy throughout the production process (Sibanda, Sipunga, Danha, and Mamvura, 2020). Extensive research has been carried out in order to maximize the recovery of valuable metals from CS. In general, the methods for copper recovery from slags can be classified into three categories, namely physical separation (flotation, magnetic separation); pyrometallurgy (roasting); and hydrometallurgy (leaching) (Guo, Zhu, Pan, Wu, and Zhang, 2016; Wang and Erdenebold, 2020).
Several studies on CS flotation have been reported in the literature. Sibanda et al. (2020) indicated that copper recovery from CS can be enhanced through a thorough understanding of the mineralogy and liberation profile of the slag, together with an optimization on the flotation reagents. Fan, Li, Wei, Li, and Sun (2017) concluded that three factors affect CS flotation: particle fineness, collector type, and pH. They achieved a concentrate with a copper grade of 14,47% and copper recovery of 79,66%, by milling 80% under 74 um, by using 50 g/t of butyl xanthate as a collector and adjusting to a pH of 10 with Na2CO3.
Shamsi, Noaparast, Shafaie, and Gharabaghi, (2015) studied the effect of collector synergism on flotation recovery of copper from copper smelting slags. To increase copper recovery, a mixture of 6 g/t Z6, 4 g/t Z11, 30 g/t AERO 3477, and 20 g/t AERO 208 was used to determine the synergistic effect of collectors on copper recovery. The flotation tests at optimal conditions (mixture of collectors) resulted in an increase from 62,23 to 80,27%.
Guo et al. (2016) developed a new technology to improve the beneficiation of copper and iron components from copper slag, by modifying the molten slag to promote the mineralization and grain growth of the valuable compounds. Results showed that, under the proper conditions, the copper grade of the rougher stage increased from 6,43% to 11,04%; the iron recovery of magnetic separation significantly increased from 32,40% to 63,26%; and other evaluation indexes slightly changed in comparison with unmodified copper slags.
Tong, Han, Ren, and Yang (2014) studied the effect of grinding fineness, pH, and collector type and dosing on copper slag flotation. The results showed that, after a grinding degree of 90% under 74 um, pH 6,0, 80 g/t of XT-53 as collector, and 30 g/t of 2# oil as collector, a concentrate with copper grade of 23,55% and copper recovery of 85,61% was obtained.
Xue, Li, and Qin (2016) studied the flotation of slowly cooled CS from the Ausmelt furnace. These researchers reported that, by using butyl xanthate as collector, a concentrate with copper grade of 16,11% and copper recovery of 69,90% was achieved. The copper grade on tailings was only 0,2%.
Another aspect that can affect both the milling and flotation of CS is the cooling behavior of the slag. Several researchers have reported that slow cooling of the slag can lead to an improvement in copper recovery because of the segregation of some valuable elements such as copper, silver, and molybdenum during the solidification and further cooling (Mihajlović, Kamberović, Korać, Gavrilovski, and Jovanović, 2015; Voisin, Pizarro, and Ossandon, 2017).
Therefore, this paper describes the evaluation of two industrial circuits for CS flotation in two campaigns: 2016 and 2017. The existing CS flotation circuit in the plant was used in 2016. In 2017, a concentrate flotation circuit with a column flotation cleaning stage was evaluated. The aim was to obtain a copper concentrate with copper contents of 25% or above.
Materials and methods
Characterization of copper slag from HVL smelter
The CS used in the laboratory tests and industrial campaigns was collected from the HVL smelter main slag landfill. Samples were characterized by particle size distribution (PSD), specific weight, Bond Index (Wi), chemical analysis, mineralogical analysis, and flotation tests.
PSD was determined in a Ro-Tap unit with sieves from 6# to 200# ASTM. Specific weight was obtained through the Le Chatelier method. The Bond Index was determined in a milling-classification closed circuit, in a 12" x 12" mill at 70 RPM. The load consisted of 285 balls with diameters from 1½" to –" and a ball mass of 20,125 kg. An ASTM 140# (106 µm) mesh was used for this test.
Chemical composition was determined through an atomic absorption mass spectrometry. The mineralogical analysis consisted of optical microscopy and X-ray diffraction analysis (XRD) with a Shimadzu XRD-6100 (Cu Kα) diffractometer. The quantification of crystalline phases was obtained from Rietveld refinements of the XRD patterns.
The flotation stage was performed in a Denver D-12 cell. It was carried out under the following conditions: PSD from 60% to 80% under 200# (ASTM); pH = 8,0; 40 g/t of F-503 (collector) and 30 g/t of H-70 (froather). These operational conditions were suggested by the Process Engineering and Chemical Laboratory staff from the plant.
Industrial flotation circuits
Figure 2 shows the circuit used during the 2016 campaign. It consists of three ball mills operated in a closed circuit. Hydrocyclone underflow is recycled for regrinding, while the overflow is sent to a conditioning stage before the rougher-scavenger stage. This stage consists of twelve Dorr Oliver cells of 300 ft3, distributed in four cells for each flotation stage (rougher, cleaner and scavenger).The recovery of sulfides takes place in the the rougher and scavenger stages, then the product is sent to the cleaner stage to improve the copper grade of the concentrate. The concentrate is then transported to a thickener and filtered in a ceramic filter.
In 2017, a second alternative was evaluated: an existing flotation circuit for sulfide ores (Circuit Nr. 2) with a columnar cell as a cleaner stage. Figure 3 shows the flowsheet of this circuit. It consists of a set of five ball mills operating simultaneously, which increase the CS flotation capacity up to 100 t/h. The rougher stage consists of seven Outokumpu cells (565 ft3), the cleaner stage of a columnar cell, whilst a scavenger stage processes the tailings from the cleaner stage. The scavenger stage consists of eight Outokumpu cells divided into four cells of 8 m3 cells and six cells of 3,0 m3. The circuit also has Outokumpu mechanical cells (20 m3 and 40 m3) and a regrinding stage for the rougher concentrate.
Results
Characterization of copper slag
Table 1 shows the results of the physical characterization of CS: F80, density, and Bond Index.
Table 1 Physical characterization of the copper slag
F80 (µm) | Density (g cm-3) | Bond Index (kWh ton-1) |
---|---|---|
2 360 | 3,30 | 22,6 ± 1.1 |
Source: Authors
The CS samples showed a density of 3,30 g/cm3, similar to what was reported by Valderrama, Gonzalez, Santander and Zazzali, (2018) for reverberatory furnace slag from the same smelter (HVL). Nazer, Pavez, Rojas, and Aguilar (2010) reported a density of 3,817 g/cm3 for samples obtained from the same deposit as the present study. Velásquez (2018) reported a density of 3,92 for slags from Potrerillos smelter (Atacama, Chile), while Cendoya (2009) reported a density of 4,0 g/cm3 for another Chilean copper smelter slag. The Bond index was 22,6 kWh/t. This value is higher than normal copper ores, which normally present a Bond Index between 13,0 and 20,0 kWh/t (Nazer et al., 2010; Cendoya, 2009; Valderrama et al., 2018).
Table 3 Quantitative XRD analyses of the feed, concentrate and tailings from the laboratory tests
Stream | Mineralogical composition (wt%) |
---|---|
Feed | Fayalite (76,7%); magnetite (23,3%) |
Concentrate | Bornite (37,6%); fayalite (30.4%); magnetite (18,5%); chalcopyrite (13,6%) |
Tailings | Fayalite (80,4%); magnetite (19,6%) |
Source: Authors
In mineral comminution, material abrasiveness, pulp environment and particle size, are the most important factors influencing the wear of the linings and grinding media in ball milling. For the HVL smelter slag, Valderrama et a!. (2018) reported a high abrasion index (0,912 g/h), which would imply a high consumption of steel (linings and grinding media).
Table 2 presents the chemical analysis results of the CS sample. The slag presented 0,53% Cu and high amounts of iron and silicon. Valderrama et al. (2018) reported a similar chemical composition, with a different copper percentage in CS.
Table 2 Chemical composition of the CS (normalized)
Component | FeT | SiO2 | CaO | Al2O3 | Na2O | K2O | MgO | Cu | S |
---|---|---|---|---|---|---|---|---|---|
wt % | 36,32 | 41,11 | 8,36 | 8,10 | 2,22 | 1,23 | 1,53 | 0,58 | 0,55 |
Source: Authors
Chemical and mineralogical analyses indicated 0,58% copper and 0,55% sulfur; high amounts of iron (33,3%) and silica (17,7%); substantial amounts of calcium oxide (5,50%) and alumina (3,95%); and minor amounts of sodium, potassium, and magnesium oxides. These values are consistent with the chemical composition of ancient and recent CS from Atacama (Cardona, Coursol, Vargas, and Parra, 2011; Nazer et al., 2010; Pavez, Nazer, Rivera, Salinas, and Araya, 2019). On the other hand, although copper can be as dissolved oxide, it is commonly found as entrained grains of bornite and chalcopyrite. Nazer et al. (2010) reported a 0,75% copper grade, with iron and silicon as the most important constituents in CS from the same smelter.
Table 2 shows the quantification of crystalline phases of the laboratory flotation tests. The CS (feed) is constitued by fayalite (Fe2SiO4) and magnetite (Fe3O4). No sulfides or copper oxides were detected, probably because their concentrations were below the XRD detection limits. The concentrate contained not only bornite (Cu1,375Fe0,275S) and chalcopyrite (CuFeS2), but also a considerable amount of fayalite and magnetite. The tailings did not show other compounds but fayalite and magnetite (80,4% and 19,6%, respectively).
Nazer et al., (2010) reported fayalite (50%), magnetite (39%) and magnesium fayalite (10%) as main constituents of the CS from HVL smelter. Cardona et al., (2011) studied the solidification of SCF slag from the HVL smelter under fast and moderate cooling rates. They found that, under fast cooling rates the presence of fayalite, magnetite and glassy phases predominate, whilst the main phases to crystallise under moderate cooling rates are magnetite and fayalite (Nazer et al., 2010; Cardona et al., 2011).
The high amounts of fayalite and magnetite in the CS concentrate are due to high the degree ofassociation between sulfides and slag, as shown in Figure 4. However, CS milling must be carried out in a very controlled way, as the excess of fine particles can lead to clogging of the piping and pumping systems. Some sulfides (bright grey) are closely associated and enclosed within larger slag particles (dark grey), which results in the unavoidable transport of slag to the concentrate.
Laboratory flotation tests
Figure 5 shows the flotation test results, with copper recoveries from 59,0% to 62,0% for the total copper, and 62,0% to 64,9% for insoluble copper. There were no considerable differences in recoveries of both total and insoluble copper from 60% to 80% under 200# ASTM (74 µm).
According to the industrial observations of the MAM plant, a coarse PSD (60% to 65% under 200# ASTM) can lead to clogging in the mill discharge pipes, as well as hydrocyclone overflow due to the fact that the pulp settles inside the hoses and pipes. On the other hand, a fine PSD (70% to 80% under 200# ASTM) results from overgrinding, thus increasing the energy cost of the comminution process.
Industrial campaign (2016) - Circuit Nr. 1
Figures 6 and 7 show the copper grades and recoveries achieved by Circuit Nr. I in July (17 days) and August (25 days) of 2016. The copper grade in July was lower than in August, but the recovery in July was higher. During that month, 10 587 tons of CS were processed, and the copper concentration in the concentrate oscillated between 14,69% and 19,97% (16,92% on average). The average copper recovery was 73,93%. In August, the processing of 15 614 tons of CS yielded copper grades in the concentrate from 13,55% to 23,30% (18,22% on average), while the average copper recovery was 71,99%.
The results showed that the copper grade in the final concentrate was not commercially satisfactory. The main limitation of the circuit was the lack of a cleaner stage to increase the copper grade in the final concentrate.
Industrial campaign (2017) - Circuit Nr. 2
Figures. 8 and 9 present the copper grades and recoveries achieved by Circuit Nr. 2 in June (14 days) and August (22 days). In August, the copper grade in the concentrate and recovery were higher than in June. During the latter, the processing of 29 480 tons of CS led to copper grades in concentrate from 12,01% to 27,41% (21,27% on average), while the average copper recovery was 71,93%. In August, the plant beneficiated 34 045 tons of CS resulting in copper grades in concentrate from 7,5% (which is highly unusual) to 32,81% (25,42% on average), with an average recovery of 75,80%.
From Figures 8 and 9, it is clear that Circuit Nr. 2 showed a higher performance than Circuit Nr. 1 in processing capacity, copper grade of concentrate, and copper recovery. There is also a potential further improvement in copper recovery by adding a scavenger stage for rougher tailings. The scavenger stage was not in the circuit design due to the high copper recovery in the rougher stage (-95%) of the sulfide ores processed in the plant.
The summary of the main parameters of the studied circuits is presented in Table 4. From the presented data, it is clear that only in the industrial campaign in 2017 (Circuit Nr. 2) was the obtained concentrate comercially acceptable (copper grade above 25 mass%). The capacity of the second Circuit was substantially higher (about three times) than Circuit Nr. 1, even though the variabilty of Circuit Nr. 2 was considerably higher than the first. Finally, both circuits exhitibed a similar copper recovery.
Table 4 Summary of average copper grades (main streams), capacities and copper recoveries for circuits 1 and 2
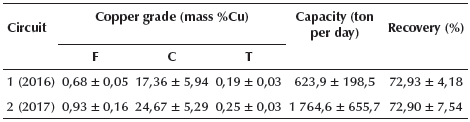
Note: F: feed; C: concentrate; T: tailings
Source: Authors
The higher performance of Circuit Nr. 2 in terms of copper grade is due to the columnar cleaner stage and the presence of five ball mills. Sipunga (2015) reported improvements in copper recovery through the addition of a regrinding stage to the flotation circuit. This researcher reported a recovery of 75,8% in the first flotation stage and an increase of up to 92,2% by adding a regrinding stage for rougher tailings.
General economic considerations
It has been shown the successful implementation of the CS processing is promoted by two main economic factors: the shortage in copper ore supply and a decrease in the price of copper between 2015 and 2017. However, it is necessary to highlight the increased costs associated to slag processing when compared to conventional copper ore processing.
The main parameters affected by CS flotation were the grinding costs and grinding media consumption. The grinding costs reached 9,41 USD/t, made up of a fixed cost of 3,05 USD/t and a variable cost of 6,36 USD/t.
It is worth noting the increase on the consumption of grinding media (1200 g/t) for the processed CS, when compared to the normal copper ore (670-890 g/t). According to Chilean Copper Comission (COCHILCO), the average grinding media consumption for the Chilean copper producers is about 700 g/t (COCHILCO, 2018). Therefore, the processing of CS represents an increase of 56% in grinding media, which notoriously affects the grinding costs.
The steep increase on the steel consumption from the grinding media, is due to the difference in the Bond Index (Wi) of the CS and copper ores. The literature reports values of 15,9-16,7 kWh/t for copper ores (Camus & Tobar, 2017; Delgado, 2013) and about 27,8 kWh/t for CS (Guarda, 2015).
Another important aspect is the reagent consuption of CS processing. Table 5 shows both the type and dosage of the reagents (collector and froather) used in the MAM plant for CS and copper ore processing. According to the literature, the consumption of reagents in CS processing substantially exceeds those ones from the copper ores, doubling the amount of collector and increasing froather consumption by about 50%.
Conclusions
In the 2016 campaign (Circuit Nr. 1) the plant processed 10 587 tons of CS in July. The copper grade of the concentrate ranged from 14,69% to 19,15% (16,92% on average) with a copper recovery of 73,93%. In August, 15 614 tons of CS were processed and the copper grade of the concentrate varied from 13,55% to 23,30% (18,22% on average), and the average copper recovery was 71,99%. The low copper grade in the concentrate is probably due to the lack of a cleaner stage, thus decreasing the copper grade of the final product.
In the second campaign (2017, Circuit Nr. 2), the plant benefited 29 480 tons of CS in June, with copper grades in concentrate from 12,01% to 27,41% (21,27% on average) and an average copper recovery of 71,93%. In August, by processing 34 045 tons of CS, copper grades varied from 7,5% (atypical) to 32,81% (25,42% on average). The average copper recovery was 75,80%.
Circuit Nr. 2 showed a higher performance than Circuit Nr. 1 in terms of mass flow capacity, copper grade in concentrate, and copper recovery. We suggest the addition of a scavenger stage in this circuit to process the rougher tailings. This modification could improve copper recovery in the overall process.
Because of the mineralogical composition of CS (mostly constitued fayalite and magnetite), the Bond Index value of 22,6 kWh/t is higher than the normal copper ores, which normally report a Bond Index between 13,0 to 20,0 kWh/t. This higher abrasiveness of CS when compared to an average copper ore is evidenced in a higher consumption of grinding media of about 60%. Additionally, reagent consumption is also substantially higher, doubling the collector dosage and increasing by about 50% the froather dosage. It is crucial to consider these two key economic parameters in order to have a more thorough description and understanding of the overall process.