Introduction
Lean Manufacturing (LM) has traditionally helped industries in removing the non-value-added (NVA) processes to achieve operational excellence (Sadiq etal., 2021). Wastes are mainly explored by drawing a value stream map of as-is state using the Gemba walk. This "as-is" map aids in capturing the snapshots of how things are currently done and areas of potential improvements (Tyagi, Choudhary, Cai, and Yang, 2015). Lean Thinking thus emerged as an effective way to continuously decrease costs and improve profits by utilizing the minimum required level of essential attributes such as time, space, machine, equipment, and energy to produce a product or provide a service. Liu and Yang (2020) claim that value stream mapping (VSM) is one of the primary analytical tools for identifying waste and optimizing a production line. The value of a product also increases when wastes from transportation, inventory, waiting, over-production, over-processing, defects, and rework are eliminated or reduced (Sullivan, McDonald, and Aken, 2002). The method is based on the Toyota Production System (TPS) and consists of two main phases: value stream analysis, in which the current value stream is visualized; and value stream design, in which sources of waste within the production process are uncovered and reduced (Ono, 1988). VSM is a static lean manufacturing tool that is becoming popular in identifying activities that add and do not add value in production sectors. Through this kind of identification, it is possible to achieve significant performance improvement in the industry. However, VSM has some disadvantages, since each job order must be mapped, and the parameters used in the process and material flows are deterministic. Preuss, Luz, Narayanamurthy, Gaiardelli, and Sawhney (2021) argue that traditional value stream mapping fails in considering the inherent variability of processes, hence reinforcing improvements that might not lead to significant results. Balaji, Venkumar, Sabitha, and Amuthaguka (2020) mentioned that VSM tends to be static and skill dependent. A single calculation is made to estimate the lead time without considering uncertainty in the parameters, as well as the variability in cycle times due to common factors such as manpower, machines, measurement, material, methods, and environment. This paper aims to study the effectiveness of developing a dynamic and fuzzy VSM model to understand the behaviour of its variables at multiple simulations considering the imprecision and variability of the data. Lead time in a VSM consists of identifying and determining the activities that add value (AV) and those that do not add value (NVA). AV activities are the cycle times (CT) of each operation in the process, whereas NVA activities in each operation of the process are related to size order (SO), available time (AT), number of machines (NM), and percentage of efficiency and effectiveness (OEE). The most critical parameter to identify NVA activities is OEE, which frequently presents imprecision in the data. This parameter is based on the following attributes: availability (Ava), quality (Q), and performance (P), which will be used as linguistic variables in DFVSM. The novelty of this study lies in two points: the first one is an integration of Fuzzy Inference Systems Theory (FIS) with the Theory of System Dynamics (SD) in the same interface to identify the variables that are relevant to enhancing lead time behavior; and the second one is the employment of an SD approach, which is not currently used, to present VSM approaches. Through SD, systems thinking provides methods and techniques for viewing problems and human action as interconnected wholes, as well as for understanding the often lagged feedback loops that may make complexity very difficult to address through traditional linear modeling processes (Ricciardi, De Bernardi, and Cantino, 2020).
Literature review
Value stream mapping, dynamic systems and fuzzy logic systems have had applications in various productive sectors with successful results.
Salvador et al. (2021) proposed a model based on the integration of Life Cycle Assessment (LCA) and VSM to improve the environmental and manufacturing aspects of organizations. Wang, Wu, Chi, and Li (2020) did research on the way VSM can be applied as a lean tool to help improve operation training performance through an immersive personalized training program based on virtual reality (VR). Sposito and Santos (2020) proposed an integration of lean manufacturing tools and 4.0 technologies considering the perspectives of the industrial field in the digital era. From interactions, multi-level circular diagrams pointed out the main contributions of Just in Time 4.0 (JIT 4.0), Kaizen 4.0, Kanban 4.0, Poka-Yoke 4.0, Value Stream Mapping 4.0 (VSM 4.0), and Total Productive Maintenance 4.0 (TPM 4.0). Rodríguez, Cervera, López, and Pérez-Fernández (2020) used VSM to identify empty transport and unnecessary CO2 emissions. Their study analyzes VSM as a tool that can enable the objectives of the different Alliance for Logistics Innovation through Collaboration (ALICE) roadmaps for logistics innovation to be achieved, as well as allowing Physical Internet principles to be reached on the established dates. VSM processes enabled the identification of non-value-added activities that threatened the integrity of the process. Standardizing the medication administration process and creating a safe space to facilitate the process successfully reduced interruptions and distractions from all sources (Kavanagh and Donnelly, 2020). A VSM application was proposed by Bin, Petersen, and Schneider (2016), where the combination of VSM and FLOW was evaluated to identify and alleviate information and communication related to challenges in large-scale software development. Baeza-Serrato (2016) proposed an approach called REDUTEX, which is based on theoretical concepts of lean and synchronous manufacturing to help to understand the behaviour of SMEs and to improve the manufacturing process by reducing customer lead times. Each of these studies used VSM to identify and eliminate activities that do not add value to the process integrating industry 4.0 tools. None of them used a dynamic approach to the development of VSM. The proposed approach has used a system dynamics approach to understand the behavior of lead time through VSM integrating a fuzzy system inference in the dynamic model.
Lagos, Mancilla, Leal, and Fox (2019) assessed the performance of a solution to the problem of assigning service squads by incorporating the variability of service times. Cardiel, Baeza-Serrato, and Lizárraga (2017) proposed a dynamic model to analyze the complexity associated with manufacturing systems and improve the performance of the process through the Six Sigma philosophy. Langroodi and Amiri (2016) used a system dynamics approach to design a five-level supply chain consisting of retailer, final product distributor, manufacturer, material distributor, and supplier in four different regions. Babader, Ren, Jones, and Wang (2016) studied the effectiveness of improving the social aspects of reuse behavior and investigated the variables that lead to increased reuse behavior within a short period. This paper selected a quantitative approach, the SD method, which offers a means to highlighting the dynamics and interrelationships between the different social aspects in reuse behavior. Pasaoglu et al. (2016) presented an extensive SD simulation model running up to 2050 and employing an agent-based approach, as well as incorporating major factors that influence the technology transition in the EU light-duty vehicle road transport sector. Gao, Hong, Swaney, Howarth, and Guo (2016) developed and presented a system dynamics model simulating regional N inputs (NANI-SD) based on the concept of net anthropogenic N inputs (NANI), a quasi-mass balance method. Each of these recent studies presents complex dynamic models in which there are multiple interactions and feedback, which enable better decision making as a base reference for the approach proposed in this research.
Keykavoussi and Ebrahimi (2020) developed a new fuzzy approach of cost-time profile (CTP) that has been considered and compared to draw future VSM. Liu and Yang (2020) proposed a fuzzy VSM to consider the variability in manufacturing environments. They used two alternative forms of fuzzy number: triangular fuzzy numbers (TFNs) and normal fuzzy numbers (NFNs). These were applied to depict time intervals, inventories, and other operating variables in VSM. Darvish (2020) designed a robust and intelligent controller that can effectively augment the operational function of the AGC system with a type-2 Fuzzy Logic Controller together with the Fractional Order Proportional Integral Derivative to more abate low-frequency oscillations. Bocklisch and Hausmann (2018) proposed a modelling method using multidimensional fuzzy patterns based on parametric membership functions of the potential type. Baeza-Serrato (2018) proposed a novel multidimensional stochastic Fuzzy Logic System (msFLS) approach to execute a plan with stochastic behavior in knitting SMEs and their evaluation. Fu and Chen (2017) applied the fuzzy theory to study the supply chain partner selection and the task coarse allocation problem under multi-attribute fuzzy comprehensive decision-making and fuzzy constraints. Arsenyan and Buyukozkan (2016) offered an integrated IT planning methodology combining fuzzy quality function deployment, f zzy axiomatic design, and f zzy r le-based systems. Each of the references cited above developed Mamdani f zzy systems integrating conditions of ncertainty in input variables, as well as expert models based on a set of fuzzy rules.
The following limitations or gaps were detected after the literature review:
VSM is a static lean manufacturing tool.
For each job order, it is mandatory to draw a value stream map.
The parameters used in the process and material flows are deterministic.
None of them uses systems dynamics and fuzzy logic integration in the same interface.
This research proposes an system dynamics approach and fuzzy logic integration in the same interface. The proposal allows eliminating the need to carry out advanced programming code in any of the languages available for other platforms, as well as creating links to export and import data. Such an interface can be used as a basis for any dynamic model and can integrate a fuzzy assessment for any qualitative variables or uncertainty in any parameters.
Methodology
The DFVSM methodologyconsists ofthree stages: theoretical conceptualization, problem articulation, and development of a dynamic and fuzzy value stream mapping (Figure 1).
The first stage of this research was the conceptualization of the problem of establishing deterministic planning and stochastic execution of plans for each company, supported by an exhaustive review of the literature on system dynamics, fuzzy logic, and normal probability distribution. Administrators are not aware that, when carrying out deterministic planning of delivery time, variability is integrated in each one of the process operations, which causes non-compliance
In the second stage, current VSM of the cutting process in a textile company was developed using six deterministic parameters, which validated the conceptualization of the problem of establishing a deterministic planning that will contrast with the stochastic execution of daily activities in each of the operations of the process. In the lean manufacturing approach, the cycle times of each operation are the only AV activities. To determine the NVA activities in each operation, the parameters involved are the size of the order, the available time, the percentage of efficiency and effectiveness, and the number of machines.
The main contribution of this research is in the third stage. Fuzzy and stochastic behavior were integrated to consider uncertainty and variability on process efficiency within the dynamic model, which allows companies to establish fuzzy and stochastic planning to compete with other large-scale companies in meeting their deliveries. Supplier shipping time, cycle times, available time and, customer shipping time are determined through the normal probability distribution function. For the critical OEE parameter that presents imprecision and vagueness in the data, a fuzzy system was constructed with its availability, performance, and quality attributes as input variables. The research was validated with real data in the southern region of the state of Guanajuato, Mexico, where there are dozens of knitting SMEs. The proposed approach was simulated using the Stella software.
This article aims to provide an approach to developing a novel dynamic and fuzzy value stream mapping. DFVSM proposes the integration of a fuzzy system to determine OEE at each stage of the process as an output variable. The variables involved in the calculation are imprecise in the collection of records, such as Ava, P, and Q, which represent the input variables of the fuzzy system. This is the reason why this integration is proposed. Another contribution is to validate whether each variable in the study has a normal probability distribution. Otherwise, we use the transformations of the central limit theorem and theJohnson families as mechanisms to obtain a normal probability distribution and a DFVSM.
Results
Problem articulation
The development of a current VSM consists of three classes of flow: process flow, material flow, and information flow (Figure 2).
Key variables
The parameters used in each of the flows are deterministic and fixed: CT, AT, SST, CST, OS, NM, OEE (Figure 2).
Horizon time
The lead time is calculated by identifying AV and NVA activities. A single calculation is made to estimate the corresponding lead time.
Where AV i are the cycle times of each operation.
Where NVA i are the NVA of each operation.
where I = 1,2,3.
SST = 6 days, CST = 8 days, NVA1 = 0,07 days, NVA2 = 0,17 days, NVA3 = 0,20 days
Proposed approach
The perception of the level of efficiency and effectiveness (OEE) generally shows imprecision and vagueness in the data, so a fuzzy system was developed to evaluate the variable, which is a function of three attributes: availability, quality, and performance. The evaluation of a percentage in decimal form has a gradually incremental behavior ranging from 0 to 1. The sigmoidal membership function had a similar incremental behavior in the range from 0 to 1, so the data was fuzzified in the system. For this proposal, the percentage of efficiency and effectiveness was used as a linguistic variable, and a diffuse system was developed in the VSM's dynamic model, where the 3 attributes were used as input linguistic variables and the efficiency percentage and efficiency as an output variable. Each of the variables of the fuzzy system consisted of two linguistic labels: regular and good. The sigmoidal type membership function was used for fuzzification. 3 variables and 2 linguistic labels formed the basis of knowledge of the diffuse system, thus creating 8 fuzzy rules. The maximum fuzzy operator was used in the stages of implication and aggregation. For this model, the defuzzification phase was not implemented, given the similarity of the fuzzified data and the percentage expressed in decimals from 0 to 1, which were used as input values in the simulation of the model. Another modification to the traditional VSM is that the variables of the cycle time, available time were used through a normal probability distribution to add the uncertainty factor in the fulfilment of the activities carried out by the operators.
Input linguistic variables are explained below:
Availability: the proportion of run time (B) between total operative mode time (A).
Performance: the proportion of actual speed (D) versus normal speed (C).
Quality: the proportion of actual good products (F) versus product output (E).
Sigmoidal membership function
Table 1 shows the ranges of the sigmoidal membership function for the linguistic labels (regular and good) by the three input variables (availability, performance, quality) and one output variable (OEE). Figure 3 shows the development of the fuzzification stage, using only auxiliary variables in the dynamic model. The parameters for each linguistic label a, m, and b were determined for the regular and good labels. The linguistic input variables consider each of the 3 processes of the manufacturing system, and their values can be seen in the indicators.
We defined a total of 8 fuzzy rules as the basis of knowledge of the Mamdani fuzzy system integrated into the same dynamic systems interface (Figure 4).
Figure 4 shows the 8 fuzzy rules for each process operation. For the OEE auxiliary variables, the implication stage was carried out, introducing a logical function with the minimun fuzzy operator to related variables. Finally, the aggregation stage of the fuzzy system was performed with the maximun fuzzy operator for the fuzzy OEE variable. These values were used to determine the times of NVA activities in each process operation on the VSM.
Fuzzy rules in each operation process:
IF availability is regular AND performace is regular AND quality is regular THEN OEE is regular.
IF availability is regular AND performace is good AND quality is regular THEN OEE is regular.
IF availability is good AND performace is regular AND quality is regular THEN OEE is regular.
IF availability is good AND performace is good AND quality is good THEN OEE is good.
IF availability is good AND performace is regular AND quality is good THEN OEE is good.
IF availability is good AND performace is good AND quality is regular THEN OEE is good.
IF availability is regular AND performace is good AND quality is good THEN OEE is good.
IF availability is regular AND performace is regular AND quality is good THEN OEE is good.
Aggregation
Maximun fuzzy operator
The parameters used by the membership functions of the sigmoidal type, as well as their function and the fuzzy rules, were integrated into the dynamic model as auxiliary variables.
Forrest diagram
Figure 5 shows the DFVSM design, where process and material flows are displayed. In the final part of the Figure, the timeline that determines the lead time of the product order is observed. AV activities are only the cycle times, and NVA activities are related to waiting times for SST and CST, as well as waiting times in each operation. The parameters used for its determination are, cycle time (CT), order size (OS), available time (AT), machine number (MN), and OEE. They were determined with the following function:
For each operation, a balancing loop was developed to fulfill the specific goal or order size. The contribution of this dynamic model is the integration of a fuzzy system for the OEE% variable, since the evaluation of the availability, quality, and performance attributes are subjective and imprecise, and an uncertainty approach is also integrated into the model when using normal distribution functions for variables such as cycle time, available time, supplier time, and delivery time. A fuzzy system was developed for each operation of the textile cutting process. Parameters for the sigmoidal membership function were defined through auxiliary variables. Eight fuzzy rules were defined. The stage of implication and aggregation was performed through a maximum fuzzy operator. In this way, it contributes to the modelling of systems dynamics for variables that are imprecise or qualitative variables for any case.
120 simulations were performed to be able to explain the process behavior of an order size of 1800 products. The lead time oscillated between 6 and 24 days. The expected lead time after 120 runs was 15,05 days (Figure 6).
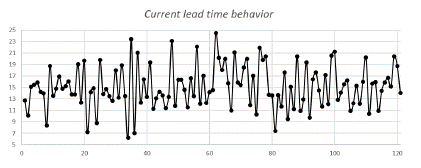
Source: Authors
Figure 6 120 simulations of current lead time behavior for a size order of 1800 products.
The central limit theorem describes the distribution of the mean of a random sample from a population with finite variance. When the sample size is large enough, the distribution of means flows approximately normal. The proposed approach uses a sample of 120 simulations, large enough to estimate the expected value of reliable lead time. Table 2 shows the results of 120 runs in a simulation of the proposed approach DFVSM, support to give the estimate of the expected delivery time of 15,05 days.
Minimun: 6,23 days
Maximum: 24,51 days
Expected lead time: 15,05 days
The results of the DFVSM simulations show significant variability in lead times, based on the vagueness and stochastic uncertainty when using probability distribution functions. The estimate of the expected time is based on the average of the 120 simulations, thusd providing greater reliability to the fulfillment of orders, in comparison with deterministic calculation of conventional VSM.
Conventional VSM through a simple calculation:
Sensitivity analysis
When analyzing the behavior of the dynamic model, the 2 critical activities in the delivery of an order of 1800 products were identified, which are the supplier shipping time (SST) and customer shipping time (CST). A tangible scenario was proposed by asking the supplier for a guarantee of improving their delivery times, as well as guaranteeing a reduction in delivery time to the customer.
Current times:
SST = normal (8,2), mean time = 8, and standard deviation = 2
CST = normal (6,3), mean time = 6, and standard deviation = 3
Improved times:
SST = (6,1), mean time = 6, and standard deviation = 1
CST = (4,1), mean time = 4, and standard deviation = 1
Figure 7 shows the behavior of 120 runs with improved times, significantly reducing by 28% the estimate of the expected delivery time to the end customer and significantly reducing the dispersion of results.
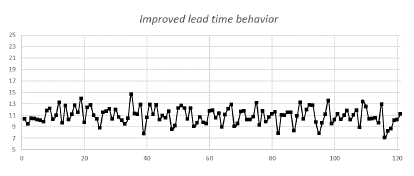
Source: Authors
Figure 7 120 simulations of improved lead time behavior for a size order of 1800 products.
Table 3 shows the results of 120 runs in a simulation of the proposed approach with improved times for SST and CST, which aids in estimating the expected delivery time of 10,89 days.
Minimum: 7,1 days
Maximum: 14,71 days
Expected lead time: 10,89 days
Conclusions
The use of deterministic plans and stochastic execution theory for structuring and deepening the research has proved useful by conceptualizing the DFVSM approach as new knowledge being incorporated to a process in the form of a fuzzy and stochastic planning tool. This article presents a dynamic and fuzzy value stream mapping validated in a cutting production system of a knitting company. The model consists of 3 balanced loops where different order sizes from each of the departments are visualized. A normality test was performed on the variables of the main operations of the process. The cycle times were used through the normal distribution function to generate random numbers in each of the simulation iterations, integrating the inherent statistical variability of the process. One of the main contributions of the research was to develop a fuzzy system in the same system dynamics interface for the variable percentage of efficiency and efficacy that presents imprecision and vagueness in the data as the output variable. This fuzzy system was deployed in three linguistic input variables for their respective calculation: availability, performance, and quality. Each of them was categorized with two linguistic labels (regular and good). Sigmoidal membership function was used to fuzzify data. The implication and aggregation stages were developed. The proposed approach allows estimating the expected lead time from multiples runs in a dynamic simulation integrating conditions of variability and imprecision. The results of the simulation show a significant dispersion in the delivery times of an order of 1800 products, due to the variability in the parameters, which resembles reality. It should be noted that the desired number of runs in the model can be modified to make the estimate more accurate. A 120-run simulation was performed to calculate the corresponding reliable delivery time in order to make improve decision making, in comparison with the simple calculation of the conventional value stream mapping used in recent investigations of VSM applications. A sensitivity analysis of the proposed model was integrated, which identified the critical factors for the delivery of the order, and achievable times were proposed for the delivery times of the supplier and the client, reducing the expected delivery time by 28%. This research contributes to the dynamic systems theory to integrate fuzzy systems for inaccurate variables or qualitative variables in the study.
The proposed approach was implemented and validated with real data of three knitting enterprises of the southern region of the Guanajuato state in Mexico, achieving an estimation of a stochastic lead time execution. The companies provided the records of the parameters of each operation of the process and participated in the development of fuzzy rules and the analysis of the results of the proposed DFVSM, thus validating the reliability of its execution in the field. From the implementations, it could be learned that commitment and employee involvement is fundamental for the proper stochastic execution of the deterministic plans. A proposal for future work would be to design a factory evaluation system for supply chain management with a genetic-neuro-fuzzy approach.