1. Introduction
Regulations becoming increasingly strict both in environmental and safety aspects for the automotive industry has brought interest in developing Internal Combustion Engine (ICE) lubricants aiming to increase fuel efficiency while decreasing the wear to mobile pieces. Approximately 21% of fuel energy in a passenger car is used to overcome undesired friction, and 60% of these undesired energy losses are technologically solvable in the midterm [1]. Multiwall carbon nanotubes (MWCNTs) have been found promising in tribological applications due to their remarkable mechanical and thermal properties [2]. They have been widely studied in tribology applications such as ionic fluids [3], cutting fluid [4], water-based substitutes for oil-based lubricant [5], AP/WP mineral lubricants [6]; tribological applications on ICE evaluation using MWCNTs nanolubricants have been reported both in bio lubricant[7] and mineral based lubricant [8,9]. In particular, for internal engine components, Kałużny et al. [10] showed that lubricants modified with MWCNTs help reduce fuel consumption and wear rate since lower friction-related energy losses would be involved under lower COF lubrication conditions.
The characterization of tribological and rheological properties was carried out by contrasting various concentrations of MWCNTs as the main strategy to evidence the effect of the nanotube’s addition to the lubricant, commonly using pin on disk [11], disk on disk [12] or block on disk [13]. Evaluating the rheological and tribological behavior of nanolubricants in accurate materials probes an adequate concentration finding for further experiments involving engine testing and gives a glance at wear rates and mechanisms changes if further surface characterization could be done. Current research results show evidence of decreasing both coefficient of friction and wear rate when adding MWCNTs to mineral-based lubricant oils for Diesel engines.
2. Methods
This research aims to evaluate the effect of adding MWCNTs to a mineral oil lubricant 15w40 for a Diesel engine by testing both tribological and rheological effects of MWCNTs added to oil lubricant. Figure 1 shows the general methodology, which consisted of MWCNTs production, purification, and dispersion in lubricant samples to evaluate rheological behavior and tribological performance when employing Piston ring-cylinder sleeve tribo-pair.
2.1 MWCNTs Synthesis
Multiwalled carbon nanotubes were synthesized by chemical vapor deposition (CVD) at 700°C, as seen in Figure 2. Acetylene was used as a carbon source and Si-supported nickel nanoparticles were synthesized via sol-gel as a catalyst. The gas mixture was composed of nitrogen (N2), acetylene (C2H2), and hydrogen (H2). The processing sequence included catalyst reduction (H2), MWCNTs growth (C2H2-N2), and cooling (N2). Further details can be found elsewhere [14].
Functionalization and purification
For the process of purification and functionalization of the nanotubes, the methodology previously reported by Cornelio et al. [12] was used. Once synthesized, the MWCNTs were subjected to purification by acid treatment with HF and HCl.
The functionalization of carbon nanotubes was carried out by means of acid for the generation of functional groups. 2 mg per nanotube of a solution composed of 3:1 (V/V) HNO3 and H2SO4 were used and the MWCNTs were subjected to mechanical stirring for 4 H. Subsequently, the MWCNTs were washed in deionized water to eliminate excess acid until reach a pH of around 5 and finally dried [12].
SEM was used in different steps of purifying process in order to determine the synthesis’ success, estimate the average length and check the purity of used MWCNTs. TEM was used to determine the diameter and the average number of layers in MWCNTs.
Dispersion of CNT in the lubricant
Oil concentrations were determined as 0.1%, 0.5%, and 1% according to evidence showing no significant effect obtained from MWCNT over 1% [16], and 60ml oil-based solutions were prepared with concentrations of 0.1%, 0.5%, and 1% wt. of MWCNTs with mechanical stirring for 30 min and ultrasonic stirring for 5 min.
2.2 Pin-on-disk test
The tribological evaluation was performed using the ASTM G-99 procedure on a pin-on-disk test apparatus (see Figure 3] with test conditions according to Table 1.
In order to determine the Coefficient of Friction (COF), a load cell attached to the Pin-on-disk apparatus measures the tangent force applied to the pin so that the friction coefficient can be calculated according to ASTM G99 standard procedure. To evaluate the tribological behavior, a concentration of 1% MWCNTs was selected to be contrasted against the base oil results.
2.3 Material characterization
In order to identify the properties of the materials, metallography of piston rings and cylinder sleeves was made using the standard tests for sample polishing with Al2O3 and 3% nital etching. Figures 4a and 4b show microstructures of both sleeve and retaining ring materials, respectively, being concordant with ASTM A48 microstructure [18].
Both Sleeve and retaining rings were defined as grey cast iron by microstructure comparison; even though etching stains are present in sleeve samples, typical grey cast graphite flakes are evident [18] . Both pin and disk were manufactured using grey cast iron (see Figure 4c), being consistent in microstructure with typical material of Cylinder sleeve and ring (see Figure 4 a,b). Disks were manufactured to a surface finish with Ra=2.87μm and wear track radius=80mm; the same cut variables were used for spherical pin sample machining with a 6mm radius. Both pins and disk hardness were measured as Brinell 260
2.4 Viscosity test
The characterization of the lubricant was carried out in a conventional Brookfield LVDV-II + Pro viscometer with temperature bath, a bidirectional RS-232 PC interface, and Rheocalc software.
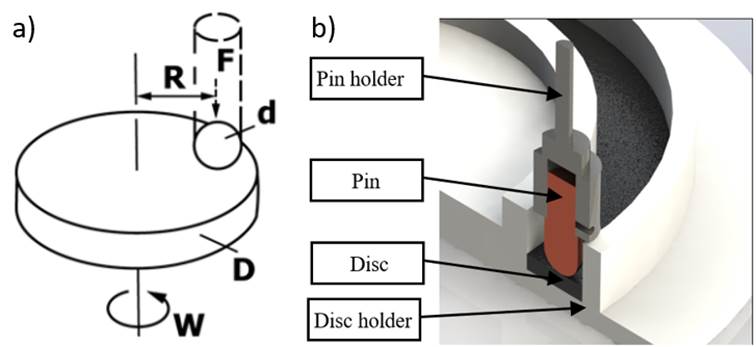
Figure 3 a) Schematic of Pin-on-Disk system: being F the normal force applied to pin, R, the wear track radius, D and d disk, and pin diameters, respectively, W disk angular velocity [17]; b) Pin-on-disk arrangement design
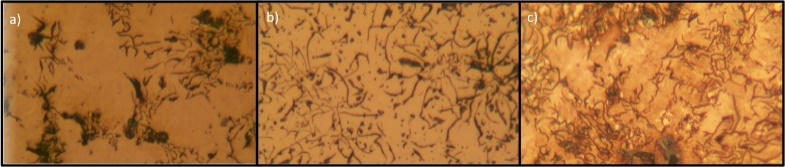
Figure 4 Microstructures at 200x. 3% nital: a) Cylinder sleeve microstructure at 200x, b): Retaining ring microstructure at 200x, c) Locally sourced grey cast iron used for pin-on-disk testing specimen
The equipment has a variable speed capability of 0.01 to 200 rpm, a test temperature range of 0 ° C to 100 ° C, and a maximum cutting speed of 57 s-1 at 195 RPM.
Controlled Rate Ramp tests were performed by using a SC4-16 LV spindle in such a way that the spindle rotational speed increased RPM every 30 seconds, and viscosity changes were recorded to determine the Newtonian or non-Newtonian behavior. The effect of temperature on viscosity was studied by performing tests in the range between 40 °C and 100 °C with a fixed speed of 30 rpm. Finally, the lubricants were tested at a specific shear rate for 600 seconds to observe any change in viscosity over time.
3. Results and discussion
3.1 MWCNTs synthesis
Pre-purified MWCNTs are shown in Figure 5a; the presence of amorphous carbon and other impurities in the samples, which are seen as round-like particles with an average diameter between 1 and 2 (m, is evident. Figure 5b shows purified MWCNTs after removing carbon-based, Si, and Ni impurities. MWCNTs agglomeration is attributed to the drying process after purifying process. TEM examination of purified MWCNTs growth around 50 layers and 40nm out diameter as seen in Figures 6a and 6b. MWCNTs average length was estimated to be around 50 (m by SEM examination.
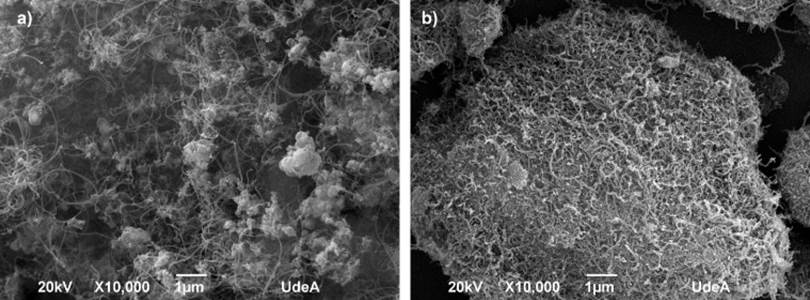
Figure 5 SEM image of MWCNTs grown on nickel catalyst particles. a) Unpurified b) Purified. Amorphous carbon and other impurities in the samples are seen as round-like particles with average diameters between 1 and 2 (m
3.2 Rheological test results
Shear rate effect
The viscosity behavior when increasing shear velocity for temperatures 40°C and 100°C is shown in Figure 7a. The results evidence no substantial change in viscosity among different MWCNTs concentrations. However, at 100°C, the viscosity increases with shear rate until 30 s-1 showing a shear thickening behavior (see Figure 7b). Passing 30 s-1 lubricants show a stable behavior; this could be associated with MWCNTs distribution reorganization on fluid.
Temperature effect
Table 2 shows the variation of the viscosity for different tested temperatures. The obtained results for non-modified lubricant show a slight difference with manufacturer-reported values; this can be attributed to atmospheric conditions of the test place and equipment sensibility. No major viscosity behavior changes were observed between concentrations. Figure 8 shows viscosity variations with respect to time to a fixed 30 s-1 shear rate.
Shear stress vs Shear rate
In order to evaluate the rheological behavior of MWCNTs added lubricants, shear stress and shear rate relation were analyzed for 0.1, 0.5 and 1% wt. at 40 and 100 ° C.
A fluid will behave as Newtonian if shear stresses increase linearly with shear rates. Figure 9 shows shear stress vs. shear rate for 40°C and 100°C; results show regardless of MWCNT concentration, there is a Newtonian fluid behavior.
The rheological results are in accordance with similar studies in lubricant oils, where the Newtonian behavior was maintained with MWCNTs addition, as well as viscosity stability with time and shear stress [19].
3.3 Tribological test results
The coefficient of friction was calculated according to the standard procedure proposed by ASTM [18].
COF was determined as a mean of values in the time range where tribometer control indicated stable measurement, resulting in friction coefficients according to Table 3. Figure 10 shows COF variations over time during the test. The COF of MWCNTs added oil is significantly lower than base oil; this may be attributed to a tribo-layer of nanotubes in the wear surface. The MWCNTs reduce the vibration making a smooth frictional response.
3.4 Wear mechanisms
Pin specimen mass was measured before and after testing using a 0.00001g significance scale to determine mass loss proportion due to wear; results are shown in Table 4. The volume loss was determined by measuring the wear scar diameter in pins, as shown in Figure 11for base oil and 1% wt. MWCNTs oil, and the results are summarized in Table 5. The wear volume was calculated according to ASTM G99 standard method, while the wear rate was given by
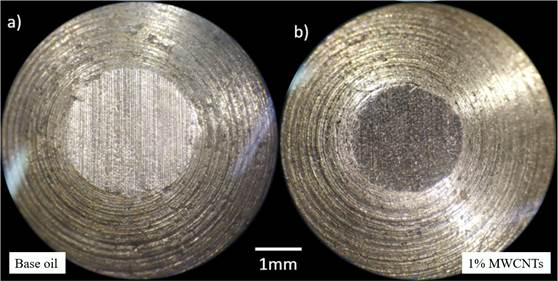
Figure 11 Wear scar textures and measurements of worn pins at 40x: a) Base oil test; b) 1% MWCNT added lubricant
Equation (1):
Figure 11 shows an increment of the contact area for the test with the base oil lubricant. The MWCNTs- modified lubricant shows a lower COF and smaller contact area, making the maximum contact pressure higher in the tests performed with MWCNTs-modified lubricant. Accordingly, a higher-pressure distribution capacity may be attributed to the tribosystem containing carbon nanotubes.
Major signs of abrasive wear are evident in the base oil-lubricated pin [Figure 11a) in comparison with MWCNTs lubricated pin [Figure 11b).
This result, in combination with the higher volume loss of samples tested with a base oil, indicates a positive effect of the addition of MWCNTs to the lubricant. The observed surface texture when MWCNTs are present suggests changes in wear mechanisms with respect to the tests performed with base oil. For instance, the darkening of the contact surface and the presence of small crazes are in concordance with the formation of a protective tribo-layer that helps avoiding metal surfaces from being in direct contact. Additionally, the mechanism of friction reduction known as “roller formation” is expected to occur during the tests [16]. Confirming the relevance of each of these mechanisms requires further characterization in order to determine the details of the interaction between the metal surface and the MWCNTs.
4. Conclusions
In the present work, a tribological and rheological evaluation of MWCNTs as friction modifier additives was developed with the purpose of evaluating their feasibility for further engine tests; the main conclusions are:
The results evidence a reduction in friction coefficient and wear rate when MWCNTs are added to the lubricant, suggesting that a better performance in ICE could also be expected.
The experimental analysis confirms no significant rheological behavior variations, being then feasible to continue further experimental evaluation in operating engines; however, in order to do so, previous research on other possible technical challenges needs to be reviewed.
The results suggest tribo-layer formation on the wear surface, composed of amorphous carbon originated by nanotubes, helping distribute the pressure on the contact area. Further advanced characterization needs to be done in order to have a better understanding of this phenomenon.
Future work: further worn surface characterization may provide information about the wear mechanisms and carbon-based compounds in the wear surface. A more complete experimental design is needed in order to find interactions Load-COF and Velocity-COF to have a better understanding of actual wear mechanisms happening in the Sleeve-cylinder tribosystem as well as friction coefficient sensibility to these variables. Finally, by granting adequate viscosity and a promising coefficient of friction, this research suggests engine performance tests as the next research step.