Introduction
When one evaluates the long-term trends in the real price of crude palm oil (CPO) worldwide in US dollars, a decreasing rate of -1.6% per year is seen for the period from 1950 to 2010. This obviously negatively impacts the income of oil palm growers and the profitability of their businesses (Mesa, 2016). Additionally, the Colombian palm agroindustry is considered a price taker when exporting crude palm oil (CPO) to foreign markets. The latter responds to the fact that Malaysia and Indonesia together represent more than 90% of the global CPO exports (Fedepalma, 2017). Finally, comparative analyses aimed at estimating production costs in different countries indicate that CPO production in Colombia is 20% more expensive than in Malaysia, mostly due to the economies of scale at the mill, land's opportunity costs, and higher wages (Mosquera et al., 2017a). Therefore, alternatives that contribute to increasing labor productivity, specifically in processes that are more labor-intensive, such as the harvest, must be pursued (Ruiz et al., 2017; Mosquera et al., 2017b). This study focuses on improving labor productivity of oil palm harvesters.
The harvest is of critical importance for the production of palm oil because the quality of the final product depends upon the opportune cutting of the fresh fruit bunches (FFB) and bunches need to be cut at the right time to maximize the oil content in the fruits. In consequence, having properly trained workers is a must (Aramide et al., 2015). Given the fact that FFB do not reach the optimal moment to be cut together, it is necessary to visit the same plots every 7 to 15 d (Corley and Tinker, 2015). Therefore, harvest in oil palm crops is a labor-intensive task. In fact, 90% of the harvesting costs are represented by labor payment (Mosquera-Montoya et al., 2019).
The harvest of oil palm is carried out by searching for ripe bunches, cutting them off, collecting FFB from the ground, and gathering FFB at collecting points in the field (Mosquera, 2017a; Sinambela et al., 2020). These operations may be performed by harvest teams (division of labor) or by individual workers, depending on plantation yields and the availability of machinery.
The equipment commonly used to harvest young palms includes a chisel to cut bunches off, a cart pulled by an animal (water buffaloes or bulls) in which the harvester places the FFB, and the picked loose fruit, and a machete to cut off the peduncles from the FFB (Castillo et al.,2017). The average labor productivity for the harvest of young oil palms in plantations in Colombia oscillates between 1.5 t FFB/workday and 2.5 t FFB/workday (Mosquera et al., 2009). When the harvest is performed by a single worker and mechanized equipment is not used, lower labor productivity results (Castiblanco and Mosquera, 2010). When the harvest is divided into two operators (one specialized in cutting off FFB and the other specialized in filling the containers either mechanically with a grabber or manually) and there are devices such as a cableway to help to evacuate FFB from the field, the highest labor productivity results (Castiblanco and Mosquera, 2010; Munévar, 2020).
It is easier to mechanize the process of fruit evacuation from the field than cutting off FFB from oil palm trees. Although research has been conducted with the aim of increasing labor productivity during the harvest over the period from 1995 to 2008, achievements are moderate (Jelani et al., 2008). The lack of substantial achievements may be because oil palm is a perennial crop in which every palm is an individual different from others. Additionally, bunches are ready to harvest at different times, depending on each palm; therefore, the same plot must be regularly harvested. Finally, the ability to access bunches of oil palms is not a straightforward process since harvesters must cut the frond holding the bunch and probably some other fronds that impede access to the bunch.
Palm cutters, such as the Cantas cutters, are among the novel technologies developed for harvesting oil palms and are recommended by Jelani et al. (2008) to help reduce workers effort and increase their productivity. The use of a Cantas cutter for harvesting oil palm trees with bunches located at a height less than 5 m yielded a 40 to 50% increase in the number of bunches cut, and a 30% reduction in the cost of harvesting a ton of FFB. Another device evaluated was the C-kat, a palm cutter suited for palms whose bunches are located at a of height less than 1.5 m (Jelani et al., 2008). Field trials showed that workers using the C-kat may be able to increase their labor productivity by 10% to 20% compared to workers using a chisel (Jelani et al., 2008).
Jelani et al. (2018) surveyed literature on the mechanization of cutting oil palm bunches and concluded that the use of mechanized alternatives instead of a traditional chisel (in young palms) or a long-armed sickle (in tall palms) (Jelani et al., 2018) results in an average 50% reduction in the cost of harvesting a metric ton of FFB. Additionally, cutting was conducted with greater efficiency, which allowed for a timely harvest and required fewer workers to complete the task.
Most studies analyzing the mechanized harvest of oil palm refer to crops planted with Elaeis guineensis (Jelani et al., 2003; Jelani et al, 2008; Alfonso et al., 2009; Khalid and Shuib, 2014; Aramide et al., 2015). To our knowledge, no reports have described the benefits of using these alternatives in crops planted with crosses of Elaeis oleifera x E. guineensis (OxG). OxG crops have been used as an alternative crop by Colombian growers interested in staying in the oil palm business in areas that have experienced outbreaks of bud rot (BR) because of their partial resistance to BR. OxG crosses are more robust than E. guineensis cultivars, and, thus, a study aiming to determine whether these mechanized tools can be used to harvest OxG oil palms that feature thicker fronds and petioles is of great interest.
This manuscript reports the results of a study conducted to assess the implementation of a mechanized oil palm cutter (MOPC) that is suited for harvesting young OxG oil palm (i.e., bunches at a maximum height of 3 m). The use of this device is compared to the use of a chisel in terms of labor productivity and production costs.
The use of a MOPC is expected to improve the performance of harvesters in the field. The MOPC reduces the physical effort by the worker when performing his job. The MOPC is equipped with an engine that converts fuel energy into an oscillatory movement that eases the cutting process through traction. When the worker uses a chisel to cut bunches, he must use his strength to repeatedly strike the frond holding the bunch in order to cut it. Then, he must strike the peduncle of the fresh fruit bunch to cut it. In contrast, when the worker uses the MOPC, he does not need to strike the base of the bunch multiple times as the cutter only needs to be operated once.
Regarding production costs, when cultivating OxG crosses in Colombia, one of the processes responsible for most of the investment in labor is the harvest (together with pollination), and in terms of production costs it occupies the second place, after fertilization, with 18.4% in the share of total costs (Mosquera et al., 2020). In consequence, these results provide insights into mechanized alternatives for increasing labor productivity and reducing production costs in crops planted with OxG oil palms.
Materials and methods
Location
This research was conducted at an oil palm plantation in Colombia located in the municipality of Tumaco (southwest of Colombia) known as Palmeiras. This plantation contains 559 ha planted with OxG crosses of oil palm. These oil palms were planted in 2008 and in 2009, and the data used by the authors were collected when these oil palms were 8 and 9 years old.
Harvesting teams
There are workers responsible for cutting fronds and bunches (cutters) and other workers (pickers) in charge of picking up FFB from the ground, placing the FFB in wheeled containers (pulled by water buffaloes) and locating the fronds the plates. The process of covering the oil palm plates with fronds is conducted at the plantation where the study is performed (i.e., Palmeiras) because of the presence of an insect known as Sagalassa valida Walker (S. valida) that feeds on oil palm tree roots and lays their eggs on oil palm plates. An effective strategy for controlling S. valida consists of using cut fronds to form a barrier that prevents this insect from laying their eggs close to the oil palm roots (Corredor et al., 2016). Table 1 shows the number of workers required to harvest a plot.
Figure 1 illustrates the methods assessed and Table 2 shows the main features of each of the tools used for harvesting young OxG oil palms.
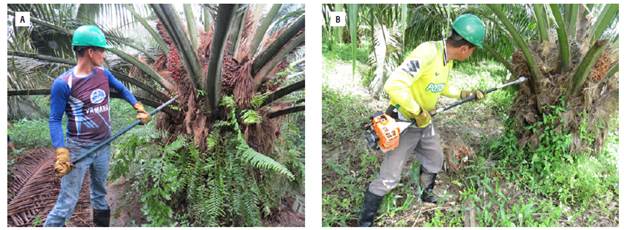
FIGURE 1 Cutting methods for oil palm trees tested in the present study. A) Chisel vs. B) Mechanized oil palm cutter.
Time and motion study
We performed a time and motion study to compare the outcomes of using either the chisel or the MOPC to cut FFB from young OxG oil palms, based on the method proposed by Sánchez et al. (2010). Time and motion studies require a first stage that consists of establishing the sequence of processes required to complete the task, in this case cutting off bunches (harvest). The result of this stage is the process flow diagram for each cutting tool being assessed.
Flow diagram of the process of cutting FFB
The process of cutting oil palm bunches was observed for a period of two weeks. The goal was to characterize not only the processes involved in cutting bunches but also the demand for inputs, tools and machinery required to complete this task. We used the symbols proposed by the American society of mechanical engineers (ASME) (Tab. 3).
Estimation of time length for each subprocess and for labor productivity
The second stage builds flow diagrams for the processes and consists of measuring time for each process. Data on time records must suffice to encompass the observed variability on time length for each process. Additionally, the frequency and the best measure of central tendency (mean or median) must be considered according to the distribution of the collected time data for each process. The result of this stage is the standard time required to complete the task of cutting FFB in OxG young oil palms, which results from the sum of the mean/median times of each process multiplied by their frequency.
We used the information recorded by a GIS system available at Palmeiras known as Click Palm. Click Palm allows data to be collected from the field in real time because every oil palm tree is tagged; thus, the worker records any process performed at any specific palm using a cell phone. Data related to cutting fruit bunches was used in the present study. Click Palm enables an assessment of the daily performance at the worker level. The analysis is possible because each worker is provided with a cell phone equipped with the application and the information is uploaded to the database. The system records the time, enabling an estimate of the amount of time a task requires.
We analyzed the time required to conduct this time and motion study to accomplish the harvest process by four workers that had at least six months of experience using the MOPC. Regarding the chisel, which is the traditional method, specific expertise was not required, but workers must have used the chisel. We analyzed harvest data from a six-month period. Since we are focused on the processes carried out during the harvest, we considered palms with zero bunches to cut as palms harvested, as well as those with one or more bunches to cut. The latter means that each harvested palm has its corresponding work cycle. A work cycle is defined as the set of processes carried out in order to harvest an oil palm tree, and that are repeated many times during a workday (i.e., processes with the greater frequency). We refer to the number of harvested palms considered for the statistical analysis according to the number of records (Tab. 4).
The data from each worker were analyzed using descriptive statistics in order determine their distribution. Subsequently, the proper measure of the central trend representing the data was chosen. These measures were also used to determine records that were too long, which tended to correspond to non-productive times or actions that are not part of the necessary subprocesses, such as resting, maintaining hydration, and attending to personal needs, etc. These activities must be accounted since they are considered non-effective working time that is part of a workday. Additionally, one must consider that people are unable to work for an entire day at the same pace. In fact, fatigue plays a key role in explaining the decrease in labor productivity during a workday. This explains why it is best to account for reliable data for the entire workday, instead of carrying out work sampling during the workday. We evaluated time data from entire workdays, collected by means of Click Palm.
We considered two different indicators, the number of oil palms harvested per workday and the number of fresh fruit bunches cut per workday, to determine the labor productivity according to the tools used. These indicators were calculated using Click Palm records for each of the workers mentioned above.
Cost efficiency analysis of both harvesting methods
We estimated the total costs of cutting one ton of oil palm bunches by considering fixed and variable costs using a previously described method (Edwards, 2015) (Fig. 2). We asked for the market prices of tools and machinery to estimate the fixed costs since they correspond to the initial capital outlay. In other words, the fixed costs represent the expenditure the grower incurs to buy tools and machinery. Additionally, we considered the life span and scrap value of tools and machinery. Then, we estimated the depreciation using the straight-line depreciation method. Regarding variable costs, we considered operating costs such as wages, repair, and maintenance (of tools and machinery), fuel and lubricant oil. We considered the frequencies of payments the grower incurred.
We used information recorded by the plantation (Palmeiras) regarding payments for labor and other expenses, such as caring for the buffaloes (feed and veterinary costs), fuel, grease, and equipment repair. We only considered expenses related to the harvesting process. We estimated these FFB harvest costs in terms of COL$ t-1.
Results and discussion
Flow diagram of the process of cutting FFB
Figure 2 displays the flow diagrams for both FFB cutting processes (chisel and MOPC); the work cycle corresponds to processes 40-70. The work cycle of the process of cutting bunches includes: 1) walking along oil palm rows searching for ripe FFB, 2) confirming that the FFB meets the harvest criteria, 3) cutting the leaf holding the FFB and cutting the FFB, and 4) recording the number of FFB cut from the harvested palm (using Click palm).
The process of cutting FFB using the MOPC requires two extra processes compared to the process using the chisel: starting the engine at the plot before beginning to search for ripe bunches and fueling the engine as required.
The latter occurs a maximum of twice daily, and thus, it does not substantially alter the standard time estimation.
The MOPC eases the process of cutting fronds and, in consequence, cost savings are incurred for pruning oil palm trees. The staff from Palmeiras states that they are paying for pruning once a year when the MOPC is used, while they must pay for pruning twice a year when bunches are cut using chisels.
Estimated time required for processes involved in cutting bunches
Importantly, 30% of the work cycle corresponds to zero FFB identified, 40% to one FFB cut, 24% to two FFB cut and, 4% to three FFB cut (Tab. 2). By analyzing the data, the median time was the central tendency measured used because the frequency distribution is biased to the right (Figs. 3 and 4). Table 5 contains synthetized information on the median time per work cycle, i.e., the median value of the time elapsed while performing processes 40 to 70 (from the process flow diagram), according to the number of bunches to cut.
TABLE 5 Median of time elapsed per work cycle* (sec).

*A work cycle comprehends processes from 40 to 70.
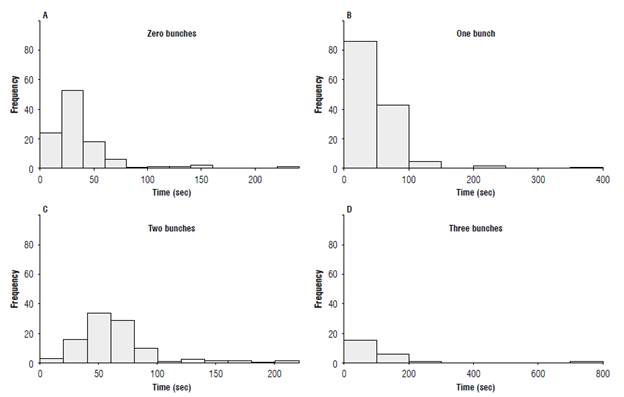
FIGURE 3 Distribution of time elapsed per work cycle according to number of bunches cut using the chisel.
The time elapsed per work cycle is greater when the worker uses a chisel to cut fronds and FFB than when the worker uses the MOPC (Tab. 5). It is likely that a shorter time elapses when no bunches are cut because no fronds interfere with the view of bunches when the palm cutter is used. When palms with ripe FFB to be cut are identified, the time elapsed per work cycle was noticeably shorter when the MOPC was used than the time spent by workers using chisels (Tab. 5).
As shown in Figures 3 and 4, some work cycles are longer than the median value. This increase in work cycles occurs when workers perform actions that lead to non-productive time. These actions are not suggested to be unnecessary and do not indicate that the workers are not committed to the accomplishment of their job (resting, remaining hydrated, addressing personal needs, receiving instructions from the harvest supervisor, eating a snack or lunch, moving through drainage channels or other obstacles, etc.). The existence of non-productive time was assessed using the median value plus a standard deviation. Actions leading to non-productive time tended to increase throughout the workday and totaled 1.4 h per day (Tab. 6).
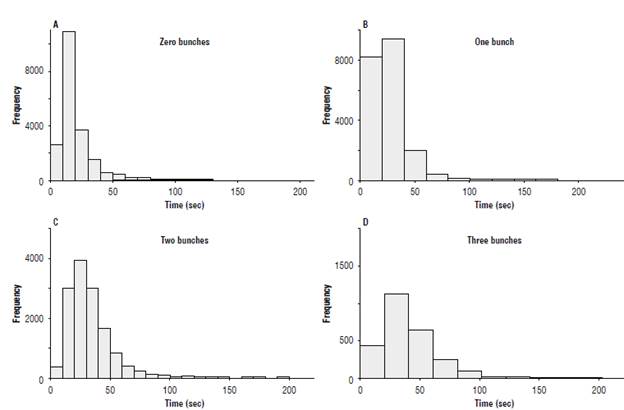
FIGURE 4 Distribution of time elapsed per work cycle according to number of bunches cut using the mechanized oil palm cutter.
Number and weight of bunches cut per workday (labor productivity)
Cutters using the MOPC averaged 546 palms harvested per workday (approximately 4.7 ha), while cutters using chisels averaged 320 palms harvested per workday (approximately 2.76 ha). The latter implies an increase of 71% in the number of oil palm trees harvested.
Regarding the number of bunches cut per workday, cutters using the MOPC cut an average of 551 FFB per workday (3.3 t FFB/workday), while workers using chisels cut an average 291 FFB per workday (2.5 t FFB/workday). Thus, the labor productivity increased 90% when workers used a MOPC palm cutter. During the workday, labor productivity tended to decrease due to physical fatigue experienced when performing the job (Fig. 5). The latter was observed for both harvest tools.
Cost efficiency analysis
The use of the palm cutter implies the need for an extra worker to pick up the bunches and to accommodate fronds, compared to the situation in which the cutter uses a chisel for cutting bunches (Tab. 7). Finally, we considered the number of tons cut to estimate the costs per ton of FFB harvested (Tab. 7).
Fixed costs
We used market prices for equipment, tools and animals required to complete the harvest. The price of a cutting tool was COL$45,000 for the chisel (6-month lifespan) and COL$1,600,000 for the MOPC (1-year lifespan). The price of a trained buffalo was COL$4,000,000 (10-year lifespan). Finally, the price of a wheeled container was COL$5,000,000 (3-year life span). Calculations were performed to estimate the cost per ton of FFB harvested (Tab. 8).
Variable costs
The estimated costs of the harvest when using the MOPC was COL$ 18,531 t-1 FFB harvested, while the costs of the harvest when using the chisel was COL$ 21,816 t-1 FFB. This means the harvest costs decrease 15%, and the total costs of producing a ton of FFB decreases 2.4% (Tab. 8).
Cutting FFB using the MOPC implies that the harvesting team must be rearranged. The increase in the number of cut bunches implies that one cutter will require two pickers, instead of requiring one picker for each cutter, as when using the chisel. This allows for a cost decrease in labor that suffices to offset the extra costs incurred with the use of the MOPC (depreciation, maintenance, fuel and fuel oil).
The results of this study are consistent with findings from previous reports showing that mechanized processes represent an alternative for lowering unit costs (Castiblanco and Mosquera, 2010; Fontanilla et al., 2010; Alfonso and Castiblanco, 2013). Additionally, given the fact that there is a scarcity of labor in rural areas, this is a significant contribution from using the MOPC.
Conclusion
The switch from using a chisel to using a MOPC implies that the strength needed to cut off bunches is no longer provided by the cutter but by the engine. Naturally, a learning curve must be considered. At Palmeiras, the company where this study was conducted, harvesters (cutters) required approximately one year to master the use of the MOPC. During the adjustment to the use of the MOPC, some minor damage to the equipment occurred since workers typically forgot that they no longer needed to strike the palms.
However, the benefits of using these mechanized tools justify the costs associated with the training process since labor productivity increased by 90%. The costs of harvest decreased because the MOPC facilitates the completion of the job by cutters and increases labor productivity, which offsets not only the greater price of the tool but the expenses related to the operation and repair of the MOPC.
Additionally, one of the main results of this study is the development of a method to use information collected by an information system, such as Click Palm, as if it was data collected for a time and motion study. This approach is very interesting since the use of software for controlling cropping processes is a trend that may improve labor productivity studies.
Finally, there is little to no literature associated to OxG crossings, specifically when it comes to the efficiency of harvesting methods. These crossings have been grown at an industrial scale for only 13 years in Colombia, so there are a few references to harvesting this type of palms that differ from E. guineensis in the sense that leaves are thicker and more difficult to cut off. In this regard, this work fills a gap in the existing knowledge.