I. Introduction
White cast irons are ferrous alloys whose main constituents are chromium and carbon. They have hypoeutectic and hypereutectic compositions consisting in a hard carbide phase (M23C6, M7C3 and M3C) in a hardening matrix. These alloys are commonly used, mostly in the mining sector, mineral grinding and processing, and slurry pumps in the cement industries. Particularly, HCWCI has become a highly demanded material, due to its high hardness, abrasion and oxidation/corrosion resistance. HCWCI may have either a martensitic or austenitic microstructure with a high content of eutectic carbides. M7C3 eutectic carbide has a hexagonal crystalline structure with hardness ranging from 1200 to 1800 HV. Usually, austenizing temperatures of white cast iron range from 800 to 1100 °C 1. Besides the selected temperature, holding time and quenching severity also influence the type of microstructure and second phase particles. Hardness depends on both the amount of precipitate of secondary fine carbides and the transformation from austenite to martensite 2. In most cases, the material undergoes quenching to obtain a martensite matrix with little amount of retained austenite and precipitate carbides. This heterogeneous structure provides a material with high wear resistance and significant toughness 3.
Since most high chromium cast applications require high abrasive wear resistance, test must be run to guarantee the selection of the best material.
Nonetheless, the values of wear resistance can fluctuate considerably, depending on combinations and properties of constituents, and also on test parameters such as load and abrasive agent size. Hence, it is necessary to standardize the tests, otherwise performance classifications must be established based on particular results 3. HCWCI abrasive resistance can be modified by adjusting proportions, shapes and types of carbides. Likewise, relative hardness and matrix toughness can be determinant factors. Required properties are obtained with cautious control over material composition, procedure path and final heat treatment 4.
II. Experimental procedure
A. Material characterization
In this study, we used HCWCI manufactured by a local company; the material was subsequently subjected to metallographic analysis and characterization by means of optical emission spectrometry using a ARL ASSURE spectrometer, SEM-EDS with a JEOL JSM 5910 electronic microscope, and XRD using a Phillips Xpert Pro Panalytical diffractometer equipped with a RX generator and an empyrean tube (CuKα,λ= 1.5406 Å). Table 1 summarizes the chemical composition of the material. Based on values reported for the major constituents (C and Cr), the material can be classified as Class III, type A, in accordance with the ASTM A532 standard 5.
Table 1 .HCWCI Chemical Composition
Element | C | Si | Mn | Mo | Fe | Cr | P | S |
wt. % | 3.02 | 0.47 | 0.74 | 1.02 | 69.69 | 24.93 | 0.126 | 0.003 |
B. Heat treatments
All samples were destabilized at 950 °C for 1 hour, then they were temporarily removed from the furnace until their temperatures nearly decreased to the pre-established values of austempering treatment (650, 450, 350, 250 and 150 °C), then, the samples were taken back to furnace, thereby achieving the completion of the isothermal treatment. Austempering holding times for each pre-established temperature were estimated with the assistance of the isothermal transformation diagram (Fig. 1), and were verified by equations (1),(2) and (3) that model transient heat transfer (6).
Where T and T∞ denote the austempering temperature and the room temperature respectively; Ti expresses the sample temperature when is removed from the furnace after austenizing. Additionally, the convective heat transfer coefficient, the thermal conductivity of the material, and the time the sample takes to reach Ti are given by h, k and t, respectively. Estimated t values are shown in Table 2. Fig. 1 shows that the transformation final time is about 12 hours for the working temperature interval. For each isothermal treatment, whose t (initial austempering time) is indicated in Table 2, specimens were austempered during the following holding times: 3, 6, 9 and 12 hours. Finally, all samples underwent water quenching.
Table 2 Initial times of isothermal treatments for each austempering temperature
Temperature (°C) | 950 | 650 | 450 | 350 | 250 | 150 |
Time (s) | 0.00 | 105.6 | 209.4 | 282 | 381.6 | 540 |
C. Tests of abrasive wear resistance
Three-body abrasive wear testing was carried out with a dry sand/rubber wheel apparatus (Fig. 2), following the procedure A from the ASTM G65 standard. The following test parameters were used: force of 130 N, wheel angular velocity of 6000 rpm, abrasion total length of 4309 m, and AFS 50-70 quartz particles.
Once the isothermal treatment was completed, 25.4 mm x 76.2 mm x 7.6 mm specimens were subjected to abrasion testing. Contacting faces were polished up to P600 sandpaper (particle size of 25.8 μm). Volume loss was the main indicator of abrasive wear, whose estimation took into account mass loss and material density (7700 kg/m3).
III. Results and analysis
A. Characterization
Fig. 3(a) depicts the microstructure of the material before isothermal treatment, which consist of eutectic austenite (γ) + chromium carbides. EDS spectrum of chemical composition (Fig. 3b) corroborates the presence of high contents of chromium and a low percentage of silicon. Additionally, as seen in Fig. 4, typical XRD spectrum of HCWCI before isothermal treatment identifies the microstructure (matrix and type of precipitates), where diffraction peaks attest to the presence of ferrite, primary austenite (proeutectic), secondary austenite (eutectic), and eutectic orthorhombic ((Fe,Cr)7C3) and cubic ((Fe,Cr)23C6) carbides.
XRD analysis focused on angles 2θ (Bragg angles) from 38 to -54°. For better clarity, Miller Indexes (hkl) of weaker intensities of diffraction were neglected (2 % in respect to the highest intensity) 10. Besides the typical diffraction peaks of austenite (111), (200) and ferrite (110), Fig. 4 also verifies the presence of the eutectic carbides, &7C3 in planes (150), (112), (151), (222), and Cr23C6 in planes (422), (511) and (531) 10.
Fig. 5 reports the equilibrium of the HCWCI phases with fixed percentages of chromium (25 %) and Carbon (3 %). In respect to 3.02 % C at temperatures lower than 650 °C, there is a presence of chromium carbides (K2+ K1) in a ferritic matrix corresponding to (Fe,Cr)7C3 and (Fe,Cr)23C6 respectively 11,12. This high percentage of chromium decreased the amount of carbon (from 4.3 to 3.02 %) and increased the temperature (from 1147 °C to 1280 °C of the eutectic point); thereby, promoting a major presence of stable chromium carbides 6.
Due to its carbon percentage, HCWCI reports liquidus, solidus and eutectic temperatures different from those presented in the unalloyed white cast irons (1290, 1260 and 1270 °C respectively) 13,14. However, as the carbon content dissolves in the austenite, and the tendency of eutectoid transformation increases, these temperatures of phase transformation tend to decrease due to the reduction of austenite stability in the transformation zone (Fig. 5a). In the cases of fixed carbon (Fig. 5b), a reduction of temperatures of crystallization and eutectic transition is observed. A rise of temperature range between solid and liquid phases takes place when reducing the chromium content; that is, this range decreases with the increase of the ratio chromium/carbon, while the value is minimum at eutectic temperature 16,17. Chromium increase (Fig. 5b) implies narrowing of the austenite phase (γ phase), expansion of the zone α + K1 + K2 and increase of the temperature of eutectic transition. The result of such eutectic transformation is given by γ + M7C318.
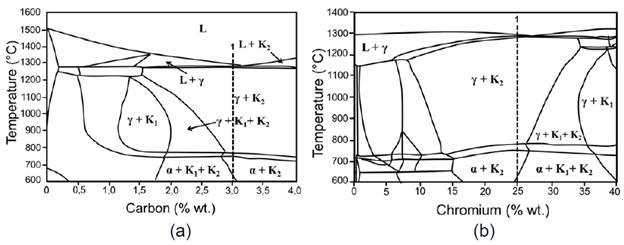
Fig. 5 Equilibrium phases of the metallic systems. (a) Fe-C 25%Cr (fixed) with C variation; (b) Fe-Cr 3%C (fixed) with Cr variation 15.
B. Wear resistance
The behavior against abrasive wear of ASTM A 532 can be seen in Fig. 6, where a significant improvement is verified for all austempering conditions in comparison to delivery-supply status. Such improvement can be explained by the formation of a variety of microstructures in terms of holding times at austempering temperatures. At the highest austempering temperature (650 °C), progressive precipitation of secondary laminar compounds, mainly Cr23C6 type, was observed; further, longer holding times promoted the formation of localized zones where Cr23C6 carbides started to transform into Cr7C3 type 7,8. Such transformation is determinant for abrasive wear resistance at 650 °C.
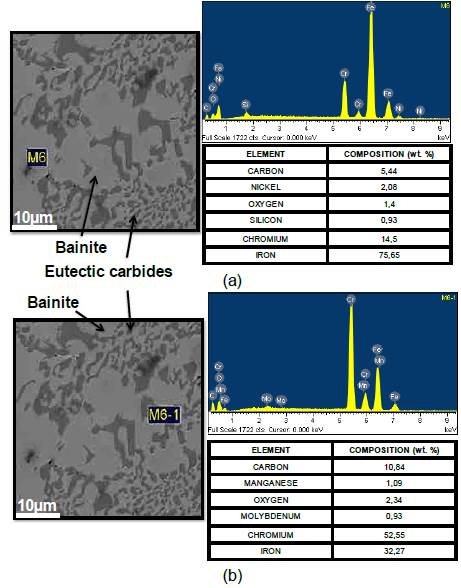
Fig. 7 Microstructure at austempering temperatures of 450 °C (holding time of 6 hours). (a) Bainite Matrix (Zone M6); (b) Eutectic Carbides (Zone M6-1).
According to Fig. 6, the best wear resistance was found at austempering temperatures of 450 and 150 °C (holding time of 6 hours). Microstructures corresponding to the former case, consists of a bainite matrix (zone M6 of Fig. 7a) with high contents of carbon and chromium (ausferrite), and alloyed carbides Type I with high content of chromium produced during the solidification phase (M7C3 and M23C6); whereas during austempering at 150 °C, the main precipitated compounds are eutectic carbides with high content of chromium type II (M7C3), as seen in zone M6-1 of Fig. 7b. This microstructure was confirmed with XRD (Fig. 9).
At the lowest austempering temperature (150 °C), the best wear resistance was expected. However, an incomplete transformation to martensite, due to the presence of retained austenite, did not prompt the expected result. Despite this, all the austempering conditions at 150 °C yielded a wear resistance as satisfactory as those achieved at 350 °C with holding times of 3 and 9 hours. Regarding the microstructure at 350 °C, Fig. 9 shows a bainite/martensite matrix with primary eutectic carbides of chromium (M7C3), and secondary Cr7C3, Cr3C2 and Cr23C6. Finally, less favorable results occurred after holding times of 6 hours at austempering temperatures of 650 °C, and after holding times of 9 hours at 650, 450 and 250 °C.
For all the austempering conditions, the following abrasive wear mechanisms were reported: ploughing, spalling, plastic deformation and formation of pits. Fig. 8 depicts traces of abrasive wear at 650 °C (holding time of 3 hours) and at 350 °C (holding time of 9 hours). Debris detachment, mostly due to cutting, can be explained by the differences of hardness between the abrasive agent (1900-2000 HV) and the obtained contacting face of the matrices: martensite (770800 HV), bainite (600-800 HV), retained austenite (300-400 HV) or any combination of them. Retained austenite has been reported (20) as the cause of plastic deformation, ploughing and spalling of superficial layers of material.
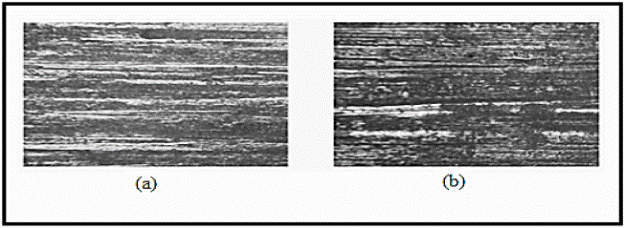
Fig. 8 Traces of abrasive wear presented in ASTM A 532. (a) 650 °C (holding time of 3 hours); (b) 350 °C (holding time of 9 hours).
The carbides obtained in this study exhibited a hardness range from 1000 to 2000 HV. Usually for all the carbides, shear stress by abrasive particles results in direct tearing of the material attested by the presence of pits 18,19.
C. Microstructure variation during austempering
XRD peaks in Fig. 9 corroborate the presence of matrices: martensite (ά), bainite (110), and austenite (111) and (200). XRD planes also confirm the presence of carbides: Cr7C3 (150), (112), (151), (222), Cr23C6 (511), and Cr3C2 (230) and (221). The presence of austenite was constant for all the cases; thus, it did not undergo complete transformation. The peaks corresponding to martensite (250 and 150 °C) and bainite (650 and 350 °C) can be seen within the range 43.8-45.2° (Fig. 9); a slight displacement of them was observed, which indicates internal stress due to transformation. The most representative displacement occured at 250 °C and can be explained by the presence of a mixed matrix of martensite-bainite with little amount of retained austenite.
IV. conclusions
Status-delivery status of HCWCI consisted of primary austenite dendrites in low proportion and a eutectic mixture of chromium carbides with eutectic austenite (M7C3/austenite). It is also reported a little amount of martensite in the boundaries of carbides, due to chromium impoverishment in the matrix.
Heat treatment involving austenizing and austempering drastically modified the microstructure, leading to the precipitation of carbide particles of type M23C6 in the matrix. Decreasing austempering temperatures and increasing holding times resulted in a larger amount of carbides, hence a greater martensite transformation. Eutectic carbides are not affected by heat treatment; thus, the dendrite microstructure remains the same.
The least volume loss was achieved for the case of austempering at 450 °C with holding time of 6 hours, thanks to a homogeneous mixture of bainite with high content of chromium and carbon (ausferrite), and eutectic carbides ((Fe,Cr)7C3, (Fe,Cr)23C6).