I. Introducción
Los materiales nanoestructurados son definidos como sólidos que cuentan con características microestructurales en el rango de 1-100 nm al menos en una dirección [1]. Los materiales nanoestructurados pueden ser sintetizados, ya sea, mediante la consolidación de pequeñas agrupaciones o por fragmentación microestructural del material másico policristalino en unidades cristalinas con dimensiones nanométricas. Estos procesos han sido clasificadas como “bottom up” y “top down”, respectivamente. En el proceso “bottom up” la nanoestructura se ordena átomo por átomo o capa por capa. Por ejemplo, en esta categoría se incluyen técnicas como condensación en gas inerte, electrodeposición y deposición química y física. En el proceso “top down” se inicia con un material másico y se fragmenta la microestructura en una nanoestructura [2].
Las técnicas más destacadas incluyen el uso de deformación plástica severa, en la cual, los materiales son sometidos a una deformación muy grande sin la introducción de cambios significativos en las dimensiones de la sección transversal de las piezas. Varios métodos de procesamiento por deformación plástica severa (SPD) están disponibles actualmente, incluyendo presión en canal angular de sección constante (ECAP) [3,4], torsión alta presión (HPT) [5,6], unión por laminado acumulativo (ARB) [7,8], corrugado y enderezamiento repetitivo (RCS). Algunos intentos se han hecho para combinar algunos de estos procedimientos, tales como ECAP y laminado en frio, ARB y FSP o ECAP y HPT [9].
De las técnicas SPD anteriormente mencionadas, el procesamiento por ECAP tiene por lo menos dos ventajas que favorecen su adopción a nivel industrial. Primero, puede ser escalada para producir muestras másicas relativamente grandes. Segundo, puede ser incorporada en trenes de laminación convencional para procesamiento continuo. El proceso ECAP consiste en presionar una pieza metálica a través de una matriz metálica en donde dos canales se interceptan en un ángulo interno (Φ), comprendido entre 60° y 160° y en un ángulo externo (Ψ) que puede estar comprendido entre 0º≤ ψ ≤(π-Ф)º resultando una gran deformación por pase sobre las muestras metálicas, la cual puede ser estimada mediante aproximaciones analíticas basadas en las configuraciones geométricas de la matriz, como se muestra en la Figura 1.
La Figura 1 plantea tres condiciones diferentes para el cálculo de la deformación de von Mises en función de la configuración de la matriz ECAP. Para la simulación de cada condición, se asumió que las probetas están completamente lubricadas, por lo tanto, los efectos de fricción fueron despreciados. Para el análisis se utilizó un elemento cuadrado situado en la entrada del canal, etiquetado como “abcd”, que pasa a través de un plano de corte teórico y se distorsiona en el paralelogramo etiquetado como “a´b´c´d´”.
Caso 1: El cual corresponde a una situación límite en donde Ψ = 0º (Figura 1a), la deformación cortante equivale a γ =a´q/qd´, en donde qd´=ad y ab´=dc´= a´p= pq = ad y a´q = 2ad
, por lo tanto, “ γ” fue calculada por la siguiente relación [3]:
Caso 2: El cual corresponde a la situación en donde Ψ = (π-Ф)º (Figura 1b), la deformación cortante equivale a γ =rc´/rb´, en donde rb´=da= (oa-od), ab´= dc´= oa Ψ = (rc´+odΨ) y rc´= (oa-od)Ψ. Por lo tanto, “ γ” cumple la siguiente relación [3]:
Caso 3: El cual corresponde a la situación intermedia en donde 0º < ψ < (π-Ф)º (Figura1c), la deformación cortante equivale a γ =a´u/d´u, en donde d´u = ad y a´u puede ser obtenida por las relaciones a´u=(a´t+tu)=(rc´+as), y como as=ad, ab´=dc´= (as+osΨ)= (rc´+odΨ), (os-od)= ad
y a´u= 2ad
. Por lo tanto, “ γ” cumple la siguiente relación [3]:
La deformación unitaria equivalente, εeq, está representada por:
Por lo tanto, la deformación ε, después de 1 pase es:
Y la deformación equivalente después de N pasadas por la matriz de ECAP, εN está representada por la relación desarrollada por Iwahashi et al. [10]:
El objetivo de este trabajo es analizar el efecto de los parámetros de diseño de la matriz ECAP, tales como, ángulo interno (Φ=90°, 120° y 140°) con un ángulo externo fijo (Ψ=20°) y las condiciones de fricción (µ=0, 0.02, 0.05, 0.1, 0.2, 0.3 y 0.32) sobre la distribución de esfuerzos en una probeta de la aleación de aluminio 6061-T6 procesada por ECAP.
II. Modelamiento y simulación
Haciendo uso del software ANSYS y su módulo de estática estructural, se llevó a cabo el modelamiento y la posterior simulación del proceso ECAP, basado en análisis 2D. Las variaciones de parámetros tales como fricción, ángulo externo (Ψ) y ángulo interno (Φ) se realizaron con el fin de estudiar las diferentes respuestas elastoplásticas del material. Para esto, se utilizó una probeta de aluminio con dimensiones 70 x 14 x14 mm. Sus propiedades se resumen en la Tabla 1.
La Figura 2 muestra el esquema general de la matriz simulada. Para la simulación se utilizó un mallado de 966 elementos cuadriláteros iniciales de 1 mm en la probeta. Debido a las altas condiciones de deformación que se presentan en la probeta durante el procesado por ECAP, la calidad de la malla disminuye y se hace necesaria la implementación de un remallado durante la simulación, de manera que permita la compilación de esta.
Tabla 1 Propiedades de la aleación de Aluminio 6061-T6 utilizado en la simulación [11].
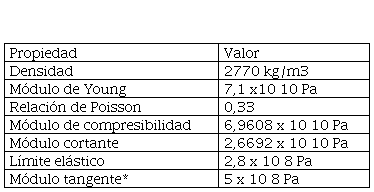
*Propiedades para un comportamiento bilineal.
De acuerdo con la Figura 2a, d representa el desplazamiento de los nodos superiores de la probeta de 70 mm en la dirección Y. Los cuerpos laterales son la estructura del canal, los cuales se fijaron de manera que no sufran desplazamiento ni rotación. Con este modelo se realizaron seis simulaciones, cada una de ellas variando los coeficientes de fricción (µ): 0, 0.02, 0.05, 0.1, 0.2, 0.3 y 0.32 para diferentes ángulos internos (Φ=90°, 120° y 140°) y con un ángulo externo fijo (Ψ=20°).
III. Resultados y análisis
En la Figura 3 se muestran los resultados de la simulación al variar el coeficiente de fricción (µ) para una matriz ECAP con un ángulo interno de Φ=90° y externo Ψ=20°.De acuerdo con los planteamientos de Segal et al. [9] e Iwahashi et al. [10] descritos en la ecuación (6), la deformación impuesta al utilizar una matriz ECAP con esta configuración será de 1,05 por pase.
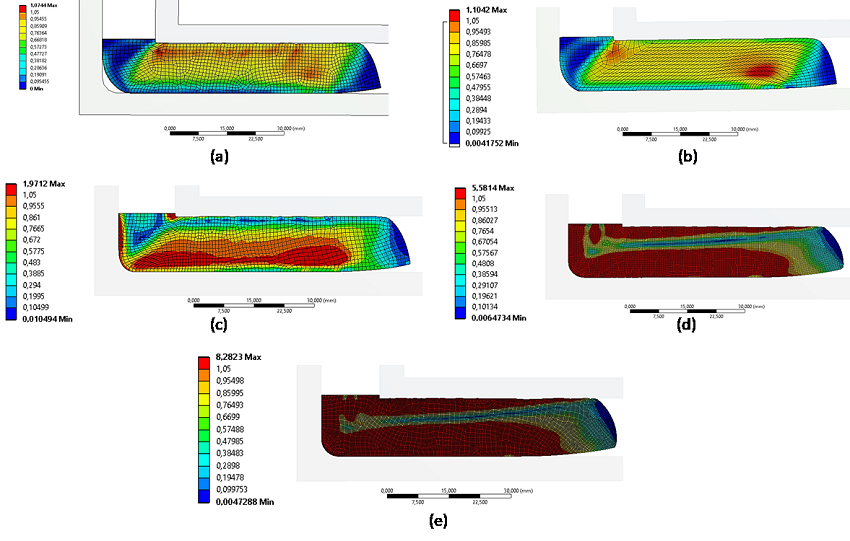
Fig. 3 Comportamiento plástico de la probeta de aluminio sometida a ECAP bajo diferentes condiciones de fricción. (a) µ=0, (b) µ=0.1, (c) µ=0.2, (d) µ=0.3 y (e) µ=0.32.
En la Figura 3a se presentan los resultados de la simulación en condiciones ideales de deslizamiento (µ=0). Al ser un deslizamiento sin fricción, la probeta tiende a separar su contacto con la zona de redondeo de la matriz o la zona muerta del canal, dicho comportamiento se define como “llenado incompleto”, lo cual impide que el cuerpo muestre la respuesta esperada por la teoría de Segal et al. [9], ya que éste no logra la deformación por cizalladura uniforme a lo largo de la probeta. Al incrementar el coeficiente de fricción a µ=0.1 (Figura 3b) se presenta un incremento en la deformación máxima y en el llenado de la zona muerta, en comparación con el observado en la Figura 3a. En cuanto al coeficiente de fricción µ=0.2 (Figura 3c), la deformación plástica equivalente máxima aumentó hasta 1,972 mm/mm en la parte baja de la probeta (zona de redondeo de la matriz), mientras que, en la parte superior de la probeta, la deformación disminuyó, lo que podría deberse al llenado total de la zona muerta que minimiza el contacto al momento del giro en la arista superior. Un comportamiento similar fue reportado por Bowen et al. [12] al deformar aluminio de alta pureza mediante ECAE utilizando un matriz de ϕ = 90° y ψ = 0°, para dos condiciones distintas de fricción, una en la cual se asume deslizamiento ideal y otra donde se asume una fricción de 0,25. En dicho estudio se analizó únicamente el comportamiento visual del material durante la extrusión y cómo el mallado de éste se veía influenciado por el mismo. Las respuestas obtenidas muestran un comportamiento similar a los obtenidos en este trabajo para coeficientes de fricción de cero (Figura 3a y 4a) y 0,2 (Figura 3cy 4c). En cuanto a valores superiores del coeficiente de fricción µ=0.3 (Figura 3d) y µ=0.32 (Figura 3e) se obtuvieron valores muy superiores a los planteados teóricamente del orden de 5.5814 mm/mm y 8.2823 mm/mm, respectivamente, localizados tanto en la parte superior e inferior de la probeta. Con el fin de verificar la homogeneidad de la deformación plástica se realizó una comparación entre la probeta completa (Figura 3) y una isocapa que muestra la región de la probeta que alcanzó por lo menos un 70% de la deformación plástica teórica (Figura 4).
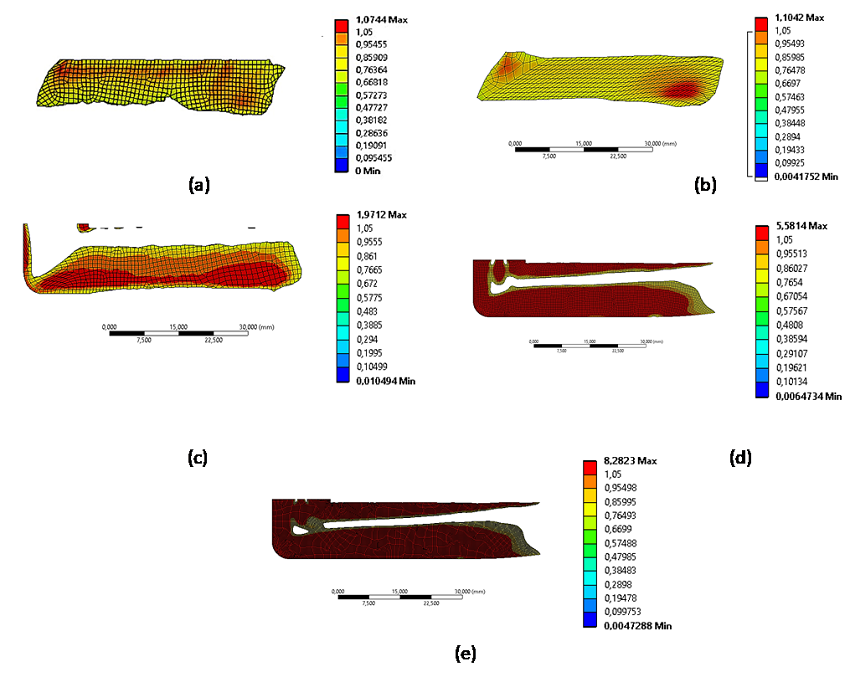
Fig. 4 Comparativa a isocapas de deformación 0,75 con un factor de fricción (a) µ=0, (b) µ=0.1, (c) µ=0.2, (d) µ=0.3 y (e) µ=0.32.
Las deformaciones plásticas logradas durante el proceso tuvieron una región parcialmente homogénea en el núcleo de la probeta, mientras en sus extremos fueron inferiores, lo cual supone que para un material procesado por ECAP, los extremos de la probeta deben ser descartados. Igualmente, la superficie de contacto de la muestra con el punto de giro de la matriz (borde superior) presentó deformaciones que, si bien fueron superiores a la de los extremos, siguen siendo muy bajas en comparación con las de su núcleo, reduciendo aún más la homogeneidad de las deformaciones logradas en el material. Las deformaciones obtenidas en la probeta comprendieron amplios rangos al aumentar la fricción. Para indicar una tendencia en el comportamiento se tomó el promedio de 10 muestras en el núcleo de la probeta en cada proceso para un coeficiente fricción dado. Dicho comportamiento se resume en la Figura 5. En donde se observa una tendencia de incremento lineal hasta un coeficiente de fricción de 0,2. A partir de allí, las deformaciones del núcleo dejan de incrementar para concentrarse en la zona de contacto de la probeta. Sin embargo, con un coeficiente de fricción de 0,32 aparenta haber un gran salto en la deformación del núcleo lo que hace que la homogeneidad en las deformaciones plásticas de la probeta disminuya.
Al aumentar el ángulo interno a valores de Φ=120°y 140° con un ángulo externo de Ψ=20° se obtiene menores valores en la deformación aplicada a las muestras en comparación a la presentada en la Figura 3. Esto es coherente con lo planteado por Iwahashi et al. [10] en la ecuación (6). En donde para la matriz con una configuración Φ=120°y Ψ=20° el resultado teórico es 0,635 por pase y para una matriz con una configuración Φ=140°y Ψ=20° el resultado teórico es 0,408 por pase. Los resultados obtenidos se muestran en la Figura 6. La Figura 6a muestra un menor llenado de la matriz durante la deformación en comparación con el obtenido en la Figura 6b. Esto se debe principalmente a que el paso en la zona de giro es menos restrictivo para la probeta en la matriz con un ángulo interno mayor (Φ=140°). En la matriz con ángulo interno de Φ=120° la máxima deformación obtenida fue de ε=0,72373, la cual no está muy por encima de la teórica (0,635). Aun así, mantiene la tendencia que tienen los bordes de la probeta a sufrir bajas deformaciones. Además, se puede observar una alta homogeneidad en la deformación en el núcleo, en donde más del 80% de la probeta obtuvo una deformación igual o superior al 70% de la deformación teórica.
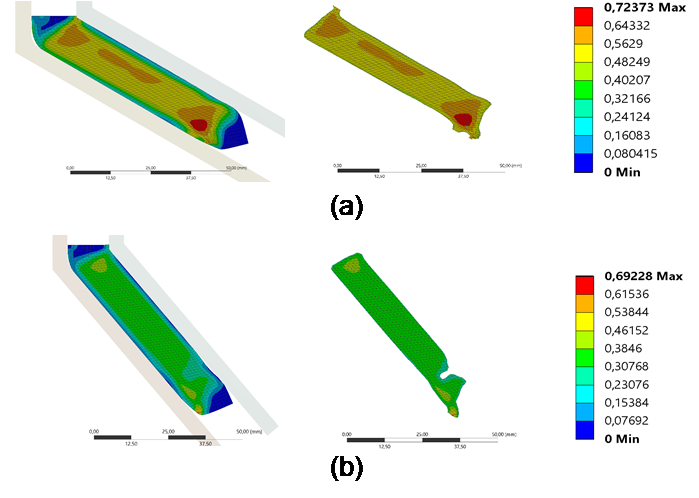
Fig. 6 Comportamiento plástico de la probeta de aluminio sometida a ECAP y Comparativa a isocapas de deformación 0,75 bajo condiciones ideales de fricción (µ=0). (a) Φ=120°y (b) 140° con un ángulo externo de Ψ=20°.
En cuanto a la matriz con ángulo interno de Φ=140° se observa como la uniformidad se mantiene en el núcleo de la probeta. La deformación máxima obtenida fue de ε=0,69228 concentrándose en el primer punto que hace contacto con el redondeo de la zona muerta, en este ángulo, ya no se generan deformaciones concentradas en el punto de contacto con la arista de 90°. Un comportamiento similar fue observado por Krishnaiah et al. [13] al procesar por ECAP cobre de alta pureza en una matriz con un ángulo interno de 120° y externo de 0°y con un coeficiente de fricción µ=0.15. Sin embargo, las deformaciones plásticas obtenidas en su estudio son superiores a las obtenidas en este trabajo. En conclusión, los resultados presentados en la Figura 6 confirman cómo al aumentar el ángulo y disminuir la restricción al flujo de la probeta, la deformación disminuye, pero su homogeneidad aumenta. Indicando un buen comportamiento y una buena similitud con las predicciones determinadas por Segal et al. [9] e Iwahashi et al. [10].
Las respuestas plásticas del material obtenidas con altas condiciones de fricción muestran comportamientos particulares donde se generan zonas de alta deformación plástica mientras en otras por el contrario disminuyen. Una justificación a dicho comportamiento se puede obtener a partir del comportamiento propuesto por Segal et al. [9], el cual se puede apreciar en la Figura 7a, la cual describe claramente el comportamiento ideal de un cuerpo sometido a un proceso ECAE, en el cual no se presentan efectos de fricción. Allí se muestra cómo el ángulo abc del elemento previo al proceso de extrusión es de 90° y se reduce una vez extruido. A partir de allí, se analiza la respuesta para un comportamiento donde se tienen en cuenta las condiciones de fricción mostrado en la Figura 7b, la cual ilustra el comportamiento de los elementos que presentan deformación por cizalladura generada por la fricción y el desplazamiento de la probeta.
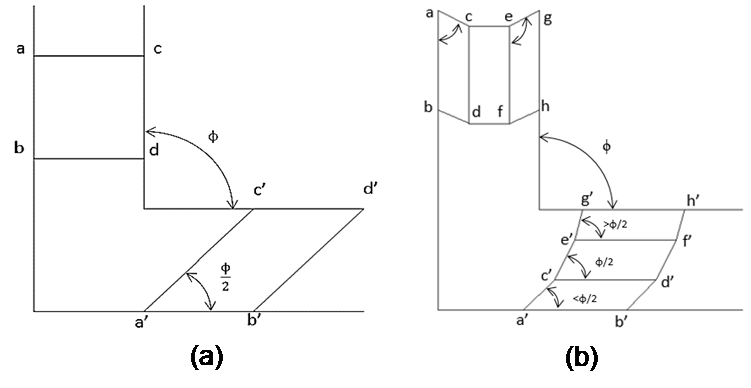
Fig. 7 Deformación por cizalladura generada por un proceso ECAE (a) sin fricción y (b) con fricción [9].
Los cuerpos ‘abcd’ y ‘efgh’ se encuentran bajo deformación por cizalladura previo al punto de giro generada por la fricción. En el esquema es posible ver como el ángulo efg antes del proceso es mayor a 90° y una vez realizado el giro éste disminuye, acercándose al ángulo de 90° donde la deformación por cizalladura disminuye. Por el contrario, el ángulo abc ya se encuentra comprendido en valores inferiores a 90°, por lo cual, el proceso de cizalladura del giro en la extrusión lo disminuye aún más, aumentando así su deformación plástica.
IV. Conclusiones
Los resultados obtenidos en las simulaciones identificaron a la fricción como un factor que afecta directamente el comportamiento de la probeta en términos de deformación durante el proceso ECAP.
El coeficiente de fricción que generó la mejor relación entre uniformidad y magnitud de deformación fue 0,2. Razón por la cual fue el coeficiente utilizado para las condiciones de giro de 120° y 140°.
La uniformidad de las deformaciones generadas en las probetas deformadas por ECAP en matrices con ángulos internos de 120° y 140° son superiores a las obtenidas para ángulos de 90°. Sin embargo, las magnitudes de sus deformaciones son inferiores, de acuerdo con lo determinado por Iwahashi [10] donde las deformaciones son acumulativas, y ellas aumentarán conforme se aumente el número de procesados, por lo cual al repetirse el procedimiento aumentará consecuentemente la deformación con una alta uniformidad.
Los extremos superior e inferior de las probetas son descartables después del procesado por ECAP, ya que son zonas que no logran deformaciones apreciables en el material, por lo tanto, el punto de análisis debe ser la parte central de las probetas ECAP.
Contribución de los autores
La contribución al trabajo por parte de los autores se realizó de la siguiente manera: Luis Carlos Flórez y Cristian Pedraza plantearon el modelo de la simulación en ANSYS y Oscar Fabián Higuera analizó el efecto de la fricción y geometría de la matriz ECAP en el comportamiento de la aleación de aluminio 6061-T6.