I. Introduction
During industrial application, it is common for materials to be subjected to processes that involve abrasive wear conditions, which could produce damage to machine elements that are in service. Depending on their application, materials will present a greater surface degradation due to constant friction between abrasive particles (high hardness) and the surface of the base material, producing its removal and causing a considerable deterioration in useful components over time [2, 3]. Some of the most commonly used materials for applications involving wear conditions are alloyed iron castings, D, M or T type tool steels, Hardox steel, ASTM A 128 steels [4], and flame spray coated metal alloys [5], among others. As for non-ferrous alloys, copper alloys such as brasses (Cu-Zn), bronze (Cu-Sn), Cu-Cr, Cu-Ag and Cu-Be alloys stand out. These harden by both solid solution and precipitation mechanisms during the heat treatment of aging [6]. A group of materials that has gained importance is the one of copper-beryllium alloys, since they present high mechanical resistance and high thermal or electrical conductivity according to their chemical composition or the heat treatment applied. This type of alloys is used in the manufacture of injection molds, valve guides, rods, springs, diaphragms, injection pistons, anti-spark tools, spring connectors, shafts, pumps and gears, all components that experience both abrasive and adhesive wear phenomena in corrosive environments. At present, two types of alloys have been developed, high strength alloys containing 1.8 to 2% beryllium, and high conductivity alloys, containing 0.4 to 0.8% Be, as well as the addition of 1.4 to 2.5% Ni + Co [7, 8]. The aim of this work was to analyze the abrasive wear behavior of the Cu-1.9Be-0.25(Co+Ni) alloy after being subjected to different solubilization temperatures and cooling media, and later being aged for 1h.
II. Methodology
The material used for this study was a Cu-1.9Be-0.25(Co+Ni) alloy, received in a heat-treated condition with an initial hardness of 40 HRC. The chemical composition of the material was obtained with Energy Dispersive X Ray Fluorescence (EDXRF) using a Thermo SCIENTIFIC Niton Serie XL3t X Ray Fluorescence spectrometer. The microstructure and wear trace analysis in the specimens was performed using Scanning Electron Microscopy (SEM) and Energy Dispersive X Ray Spectroscopy, utilizing a HITACHI SUM3500 scanning electron microscope at 20 kV accelerate voltage. The microhardness tests were performed using a STRUERS DURASCAN G5 micro-Vickers hardness tester under an indentation load of 500 g for 15s, according to the ASTM E384 Standard [9]. The heat treatments were carried out in a Model D8 TERRIGENO Furnace. Table 1 summarizes the heat cycles applied in this study.
Abrasive wear tests were performed using dry sand/rubber wheel equipment on rectangular specimens, which were machined with dimensions of 25 mm wide, 5 mm thick and 76 mm long according to ASTM G65-16 [10]. Procedure E was used in this study, the parameters applied were: force against specimen (130 N), wheel revolutions (1000 rpm), lineal abrasion (718 m) and testing time (5 min). The mass loss of the samples was measured on a Mettler Toledo ME204T analytical balance with a sensitivity of 0.0001 g. The values of volume loss were calculated according to equation (1) with the density of the material as a given value (8,350 g/cm3).
The wear rate of the material was calculated according to equation (2):
While the wear coefficient was determined according to equation (3):
Where: V: volume of material lost [mm3.]; H: hardness of material [Brinell]; P: load [kg]; L: sliding distance [mm].
Because equation (3) requires Brinell hardness, the hardness values in Figure 2c were obtained by converting the values of the Vickers scale to the Brinell scale following the guidelines of ASTM E140-07 [11].
III. Results and discussion
The most relevant results obtained in the different stages of this research are presented below.
A. Chemical and Microestructural Characterization of the as-Supply Material
To corroborate the chemical composition of the material, the Energy Dispersive X Ray Fluorescence technique was applied. Table 2 summarizes the results obtained.
The presence of elements such as cobalt, iron, vanadium, silicon and titanium alter the thermodynamics of the Cu-Be system (Figure 1a), modifying the stability zones of the phases and the temperatures of the invariant reactions. In this investigation, the selection of the temperature range was made by analyzing the binary system only. For an alloy with Cu-1.9%Be the working range used during the solubilization process was between 650-900°C. In the Cu-Be Binary system there are 6 invariant reactions: 3 peritectics, 1 eutectic and 2 eutectoids. Of which, and due to the percentage of beryllium in the alloy, only 2 reactions would be directly considered: peritectic reaction at 858 ºC: α2,2%Be+L4,4%Be ↔ β4,3%Be, and eutectoid reaction at 618 ºC :β6,09%Be ↔ α1,8%Be + γ10,5%Be [12].
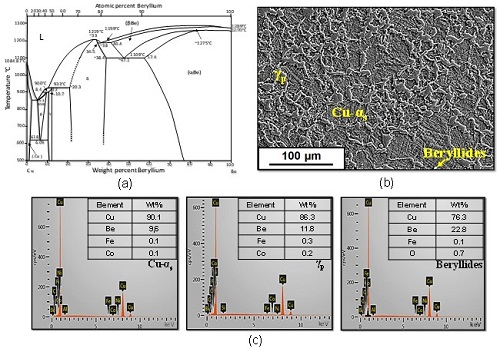
Fig. 1. (a) Phase diagram of Cu-Be system [13] and (b) Microstructural behavior of the Cu-1.9Be-0.25(Co+Ni) alloy in as-received conditio
Figure 1b shows the microstructural behavior of the Cu-1.9Be-0.25(Co+Ni) alloy in as-supply condition. In the initial microstructure, the presence of Cu-α grains was observed, supersaturated with 9.6% beryllium and Cu-Co-Be-Ni precipitates, known as beryllides, with copper (76.3%) and beryllium (22.8%). In addition, the presence of the precipitated γ phase (γp) was observed at the grain boundaries of the α phase with copper (86.3%), beryllium (11.8%), iron (0.3%) and cobalt (0.2%) (Figure 1c).
B. Wear Resistance Analysis
The results presented in Figure 2 show that all the thermal cycles applied in this research improved the wear resistance of the material in the as-supply state. It was also observed that a high hardness is not a parameter that allows to anticipate a good behavior in the abrasive wear of the Cu-1.9Be-0.25(Co+Ni) alloy.
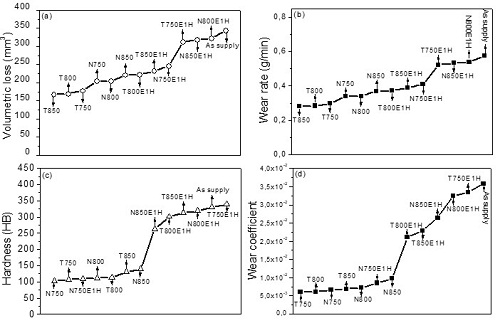
Fig. 2. (a) Volumetric loss, (b) wear rate, (c) Hardness and (d) wear coefficient of the Cu-1.9Be-0.25(Co+Ni) alloy.
The results of the volumetric loss for the heat treatments carried out showed that the softer specimens presented the best results to wear. The increase of the wear rate as a function of the complexity of the microstructure was observed. The presence of the precipitated gamma phase on a supersaturated alpha copper matrix increased the rate of wear, because during the wear process, the removal of the precipitated material occurred, which produced an increase in the volumetric loss and, therefore, in the rate of wear compared to samples that presented only a single-phase supersaturated copper structure. Figure 3 shows the behavior of the worn surfaces for the different thermal cycles under study. The presence of micro-plowing as the predominant wear micro-mechanism accompanied by the formation of superficial grooves, fracture ridges and micro-cracking was observed. The lowest wear rates were obtained in the specimens that showed mainly an oversaturated single-phase behavior (Cu-α). A microstructural analysis of the material under study will then be carried out.
C. Microestructural Characterization of Heat-Treated Material
Figure 4 shows the microstructural behavior of the material subjected to the different thermal cycles evaluated. The microstructure of the material solubilized at 750ºC and (T750) cooled in water, shows an atypical behavior (see Figure 4a), since at this temperature, the material should present twinning grains of copper alpha phase according to the phase diagram of Figure 1a. The phase Cu-α presents a crystalline structure FCC: Fm3 ̅m (CF4), the phase β presents a crystalline structure BCC: Im3 ̅m (CI2) and the phase γ presents a crystalline structure cubic type CsCl: Pm3 ̅m (CP2) [13]. However, this material was cooled in water, which would allow the presence of an alternate laminar structure of supersaturated Cu-αs and γ. In addition, the presence of twinning grains of Cu-αs in proeutectoid phase is observed, with precipitates (beryllides) rich in beryllium (93.2%), copper (5.8%) and cobalt (1%). A similar behavior was reported by Donthula et al. [14] when analyzing the morphological evolution of the eutectoid transformation products in a Cu-12%Ti alloy.
It is worth noting that the absence of a homogeneous alpha phase may be due to the lack of dissolution of the β phase, since it would indicate that the solvent line of the Cu-Be system was not exceeded during heating, which would be transformed into Cu-α+γ phase by eutectoid reaction (β6,09%Be↔α1,8%Be+γ10,5%Be), under stable cooling conditions (N750), as shown in Figure 4d. When the temperature increases to 800ºC and 850 °C, a supersaturated single-phase Cu-α phase behavior is observed, with a large presence of coherent and incoherent twinning typical of a recrystallization process (see Figures 4b, 4c, 5e and 4f), which is consistent with the Cu- Be system. However, at 800°C, the presence of some precipitated beryllides rich in Cu (82%), Be (17.5%) and Co is still detected. As for the solubilized samples at 850°C, they show a larger grain size compared to what was observed in the samples at 800°C. Besides, the presence of porosities is observed at the grain boundaries, which could indicate that the temperature used in the solubilization treatment was extreme and close to the solidus temperature of the material, indicating the beginning of melting. The presence of some precipitates rich in copper (87.2%), cobalt (7%) and beryllium (4.7%) is also noted.
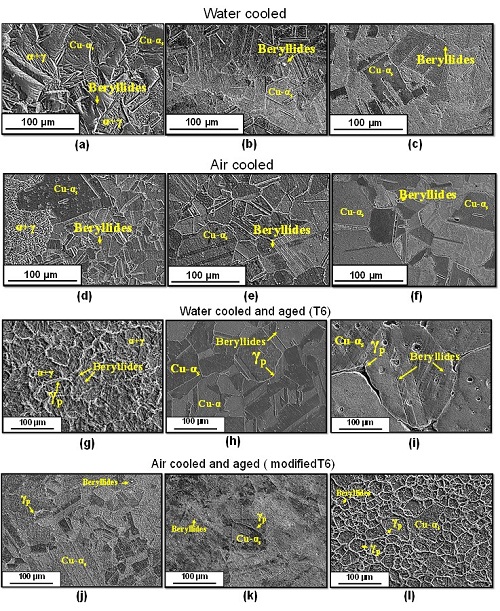
Fig. 4. Microstructural behavior of Cu-1.9Be-0.25(Co+Ni) alloy solubilized at (a, d, g, j) 750 °C, (b,e, h, k) 800 °C and (c,f, I, l) 850 ºC.
As for the samples cooled in water from the different temperatures of solubilization (750°C, 800°C and 850°C) and aged at 300°C for 1h, Figure 4g (T750E1H) shows the presence of the Cu-α+γ phase, spherical beryllides uniformly distributed (secondary) and, in the grain boundaries of the Cu-αs. phase, the precipitated gamma phase (γp). When increasing the temperature of the solubilized to 800 °C (Figure 4h) and 850 °C (Figure 4i), the specimens show the presence of supersaturated alpha copper and precipitates γ. at the grain boundaries with high beryllium content. Also, the presence of primary and secondary beryllides is observed at the grain boundaries. The results are consistent with those made by Guoliang [8] and Tang [15] who, with solubilization treatments at temperatures of approximately 800ºC and with aging times of about 4 hours, found transition precipitates γ in equilibrium. These were found in the form of thin strips, distributed in a state of equilibrium within the copper matrix α.
As for the samples cooled with air from the different temperatures of solubilization (750°C, 800°C and 850°C) and aged at 300°C for 1h, there is a similarity between the samples heated to 750°C and the ones heated to 800°C, since they present twinning supersaturated Cu-α phase grains of different sizes and with the presence of γp phase in the grain boundaries. When performing a general mapping to the specimen by means of the energy dispersive spectrometry (EDS) technique, values in the order of 12.4 - 47.3 %Be were detected, confirming the presence of γp and supersaturated Cu-α phase (αs), according to the Cu-Be system (Figure 1a). The presence of cobalt and nickel beryllides was also noted. The solubilized test specimen at 850°C (Figure 4l) shows a behavior very similar to that of the supply material (Figure 1b) with the presence of twinning Cu-α grains and precipitates γp at the grain boundaries that started to form. Within the grains, the presence of beryllides (white spots) distributed over the entire surface is observed.
IV. Conclusions
The results showed that all heat treatments applied to Cu-1.9Be-0.25(Co+Ni) alloy specimens improve the response to abrasive wear of the alloy in the as-supply state. In addition, it was found that high hardness is not a parameter that allows predicting the wear behavior of this alloy. The results showed that the lower wear rates were presented by the softer specimens.
The specimens that reported the best behavior to abrasive wear and, therefore, the lowest volumetric losses, were those that were only subjected to the solubilizing heat treatment and were cooled both in water and air. In these test pieces, only solid solution hardening and plastic deformation mechanisms were present, in comparison with the test pieces submitted to the aging treatment, where the precipitation hardening mechanism was activated. This essentially allows the detachment of the precipitates that did not manage to remain adhered to the copper matrix when in contact with the dry sand, producing the greatest volumetric losses.