INTRODUCCIÓN
La pirólisis se define como un proceso en el cual, a través de reacciones de craqueo térmico en ambientes libres de oxígeno, polímeros largos de alto peso molecular se transforman a moléculas de menor tamaño [1]. Según Arandes et al. [2], la pirólisis es eficiente al recuperar monómeros y obtener combustibles con una importante reducción en emisión de gases y compuestos volátiles comparada con la gasificación, significando una disminución en los contaminantes que podrían producirse durante el proceso. Calderón [3] explica que obtener combustibles a partir de los residuos plásticos mediante el proceso de pirólisis representa un avance hacia un mejor manejo de los residuos sólidos. Esto por cuanto proporciona una alternativa al tratamiento adecuado de gran cantidad de residuos plásticos que no pueden ser recuperados económicamente por operaciones convencionales. Anuar et al. [4] menciona que la pirólisis de plásticos produce componentes en estado líquido, sólido y gaseoso, dependiendo de la composición del plástico a tratar y las condiciones en las que se lleve a cabo el proceso. Los productos gaseosos son generalmente enviados a un proceso de destilación para la separación de sus componentes, mientras que los residuos líquidos o sólidos son utilizados en procesos alternativos, como lo es el craqueo catalítico, para tratar de aumentar el rendimiento de productos utilizables.
El craqueo catalítico es el proceso en el cual se toman los hidrocarburos de cadenas largas y se convierten en hidrocarburos de menor tamaño de cadena con ayuda de un catalizador [5]. Actualmente, los sistemas de craqueo catalítico fluidizado son de suma importancia en las refinerías, debido a que estos sistemas se utilizan para convertir residuos en gasolina de alto octanaje y diésel [6]. El proceso de craqueo presenta una serie de reacciones catalíticas que ocurren al mismo tiempo y a gran velocidad. El proceso se ve influenciado por diversos factores, tales como: el tipo de materia prima alimentada, la presión de trabajo, la temperatura de reacción, el tiempo de residencia, el tipo de catalizador, la relación másica catalizador/reactivos y, por último, la regeneración del catalizador para reactivar su actividad catalítica. Decroocq [7] expone que la conversión aumenta proporcionalmente con la presión. Sin embargo, destaca que la práctica común en la industria es la de llevar a cabo el proceso a presión cercana a la presión atmosférica. Esto se realiza porque las reacciones de craqueo son favorecidas termodinámicamente a bajas presiones y bajo condiciones de presión elevadas se favorece tanto termodinámica como cinéticamente la formación de coque. También resalta la importancia de la temperatura en el proceso debido a que esta variable está directamente relacionada con la constante de velocidad de reacción.
Gao [1] indica que los catalizadores se utilizan para optimizar las reacciones y modificar las distribuciones de productos obtenidos. Además, se ha encontrado que las energías de activación son mucho menores en la presencia de un catalizador. De acuerdo con Decroocq [7], los catalizadores típicos para el caso de reacciones de craqueo son aquellos basados en estructuras de alúmina-sílica. La actividad de esta clase de catalizadores se debe a sus sitios ácidos, los cuales dependen del contenido de aluminio. Se han estudiado otras formas de óxidos metálicos, como los óxidos de alúmina-boro o sílica-zirconio. Sin embargo, la estabilidad de estos es bastante mala comparada con la obtenida por el sistema de alúmina-sílica [7]. Sriningsih et al. [8] investigaron el craqueo de residuos plásticos a productos líquidos sobre zeolitas ZSM-5 impregnada con metales como Ni y Co, obteniendo rendimientos entre 23.89 %wt y 23.92 %wt a 350 °C.
Actualmente, las zeolitas son los materiales más ampliamente usados porque cumplen con las características deseadas para un catalizador de craqueo. Zhu et al. [9] informan que el tamaño del poro de la zeolita determina el rango de productos que se obtienen del craqueo. Inagaki et al. [10] mencionan que la ZSM-5 es una de las zeolitas de mayor uso a nivel industrial dada su alta actividad catalítica, así como su selectividad hacia moléculas de menor tamaño como el propileno. Mientras que según Vogt & Weckhuysen [11], la zeolita responsable de generar moléculas en el rango de gasolinas es la denomina Zeolita Y, ésta cuenta con un tamaño de poro aproximado de 7.3 A, mientras que en el caso de la zeolita ZSM-5 los poros son un poco elípticos con diámetros que varían entre 5.1 A y 5.6 A. Por otro lado, la relación en la que se alimentan el catalizador y los reactivos afecta también el rendimiento del proceso. Esto se debe a que, como investigó Decroocq [7] si la cantidad de reactivo es mayor que la cantidad de catalizador alimentado, ciertas moléculas de reactivos no encontraran sitios activos en el catalizador capaces de llevar a cabo la reacción.
Actualmente la empresa Balanced Energy, en Costa Rica, trata desechos de plásticos a través de un proceso de pirólisis, estos plásticos son en su totalidad residuos sólidos que representan una problemática actual por su carácter contaminante. Los plásticos que se reciclan a través de este proceso son el polietileno, polipropileno y el poliestireno. El proceso de conversión actual logra transformar 1 kg de plástico en 0.8 kg de líquido, 0.15 kg de gas (mayoritariamente propano y metano) y 0.05 kg de carbón. Sin embargo, también se obtienen parafinas, sólidas a temperatura ambiente, como desecho del proceso de pirólisis de los plásticos, las cuales pueden ser aprovechadas para obtener productos de alto valor por medio del proceso de craqueo catalítico. Por tanto, el objetivo de esta investigación fue evaluar el efecto del tipo de catalizador, la temperatura de reacción y la relación másica catalizador/parafinas en la conversión de parafinas provenientes de la pirólisis de plásticos a través de un proceso de craqueo catalítico.
SISTEMA EXPERIMENTAL
Para llevar a cabo las corridas experimentales se empleó un reactor de lecho fijo, fabricado por la empresa Cobybsa, en Costa Rica. El reactor tiene capacidad para 1.5 kg de parafina, un lecho para 600 g de catalizador, y una temperatura máxima de 600°C, con sistema de calentamiento por medio de resistencias eléctricas. El equipo posee un sistema de control automático que permite monitorear la temperatura, la velocidad de calentamiento, y la presión del sistema. El sistema fue diseñado con características similares a las requeridas para realizar la prueba de micro actividad [12], la cual se rige bajo la norma ASTM D3907.
CATALIZADORES
Se decidió emplear la Zeolita ZSM-5 y la Zeolita Y como los catalizadores para esta investigación dado que actualmente son los de mayor uso en los procesos de craqueo catalítico de la industria petrolera. Los estudios científicos que respaldan su uso, tales como: los liderados por Gao [1], Vogt & Weckhuysen [11], y Komatzu [13], entre otros; tanto en sistemas de craqueo de productos derivados directamente de la industria de refinación del petróleo como de los procesos de pirólisis de plásticos, justifican considerar a estos dos catalizadores como los mejores candidatos para investigar su uso en el craqueo de los residuos de la pirólisis de plásticos que se lleva a cabo en la empresa Balanced Energy. Ambos catalizadores fueron comprados a Pingxiang Naike Chemical Industry Equipment Packing Co. En la Tabla 1 se mencionan algunas características importantes de las zeolitas usadas en esta investigación (proporcionadas por el fabricante).
FACTORES DE ESTUDIO
Los factores de estudio en esta investigación fueron el tipo de catalizador, la temperatura de reacción y la relación másica catalizador/ parafina. Weekman [14] indica que en un reactor de lecho fijo se pueden utilizar relaciones másicas de catalizador/parafina desde los 0.1875:1 hasta los 1.5:1, y temperaturas entre 454°C y 482°C. Sin embargo, debido a la capacidad del sistema experimental y al elevado costo de los catalizadores, en esta investigación se decidió probar bajas relaciones másicas y temperaturas no mayores a 450°C. Además, la reacción se llevó a cabo a presión atmosférica. En la Tabla 2 se mencionan los niveles en los cuales se investigó cada factor.
METODOLOGÍA
Se decidió dividir el trabajo experimental en dos partes. En un primer experimento se evaluaron únicamente el efecto de los factores tipo de catalizador (Zeolita Y, Zeolita ZSM-5) y relación másica catalizador/parafina (0.40:1 y 0.20:1), sobre el rendimiento a productos líquidos. Para este caso el factor de temperatura de reacción se mantuvo fijo en 440°C. Se analizó por medio de un ANOVA de dos vías. Se realizaron dos réplicas para cada corrida. El diseño empleado se muestra en la Tabla 3. Las hipótesis planteadas para el primer experimento son:
Ho = No hay diferencia en las medias del factor de estudio.
Ha = Al menos una media del factor de estudio es diferente.
En otras pruebas realizadas en la primera etapa a temperaturas de 475 °C y 500 °C, la cantidad de gases generados durante la reacción fue excesiva, lo cual provocó una presurización elevada del reactor al no permitir de manera adecuada la liberación de los gases. Debido a dicha problemática presentada y a que, los productos de interés en esta investigación son los líquidos y no los gases, para el segundo experimento se decidió estudiar una temperatura de reacción menor a 440 °C a la cual no se presentaron los problemas mencionados. En el segundo experimento se evaluó solamente el efecto de la temperatura de reacción (400°C y 440°C) sobre el rendimiento a productos líquidos. Tomando en cuenta los resultados obtenidos del primer experimento, se escogieron para esta parte, el mejor catalizador y la mejor relación másica catalizador/parafina. Se ejecutaron 5 corridas experimentales para cada nivel, y se aplicó un análisis t de Student a los resultados obtenidos. La hipótesis nula y alternativa planteadas para el segundo experimento son:
Ho = No hay diferencia en las medias del factor de temperatura de reacción
Ha = Al menos una media del factor de temperatura de reacción es diferente.
Todas las corridas experimentales se llevaron a cabo empleando como materia prima aproximadamente 500 g de parafinas obtenidas como producto secundario del proceso de pirólisis de plásticos. El tiempo de reacción fue de 60 min, se empleó de 100 g a 200 g de catalizador según la relación másica estudiada y la presión del sistema se mantuvo constante al valor atmosférico el cual fue de 102 kPa. Cada 5 min se tomaron datos de volumen acumulado de productos líquidos. Luego, para una muestra total a cada 60 min de reacción se determinó la masa total obtenida y la densidad de cada muestra. El rendimiento a productos líquidos se determinó por medio de la Ec. (1) de acuerdo con Sriningsih et al. [8].
donde:
wf= masa inicial de alimentación de parafinas, g
w L = masa de producto líquido obtenido una vez finalizado el tiempo de reacción, g
Las mediciones de densidad fueron llevadas a cabo en el Laboratorio de la Escuela de Ingeniería Química de la Universidad de Costa Rica utilizando un picnómetro de 10.302 mL y cada una de las mediciones fue tomada a temperatura ambiente de 21°C. Para poder utilizar estos valores de densidad y compararlos contra otros valores de referencia o contra los combustibles comercializados a nivel nacional, los resultados de densidad obtenidos para las muestras craqueadas se corrigieron a una temperatura de referencia, la cual es generalmente en la industria de 15.56°C. Para corregir estos valores se utilizó el procedimiento empleado de manera regular por la Refinadora Costarricense de Petróleo (RECOPE) [15], el cual consta de un proceso iterativo de cálculos para obtener el valor de densidad corregido a 15.56 °C.
Además, se realizaron análisis por cromatografía de gases para determinar de manera aproximada la composición química de los productos obtenidos y la distribución de los rangos de cadena de los hidrocarburos obtenidos. Los análisis se llevaron a cabo con la colaboración del Centro de Electroquímica y Energía Química (CELEQ) de la Universidad de Costa Rica y utilizando un método basado en la norma ASTM D2887 "Método de prueba para la distribución de los rangos de ebullición de fracciones de petróleo por Cromatografía de Gases". Las condiciones del método cromatográfico se muestran en Tabla 4.
RESULTADOS Y ANÁLISIS
Como se explicó en la sección anterior, se ejecutaron dos experimentos separados para lograr evaluar los tres factores de estudio planteados en esta investigación. La información obtenida del primer experimento fue necesaria para la ejecución del segundo.
EFECTO DE LOS FACTORES ESTUDIADOS SOBRE EL RENDIMIENTO A PRODUCTOS LÍQUIDOS
En la Tabla 5 se presentan los resultados de volumen de productos líquidos obtenidos para el primer experimento, según la nomenclatura empleada, la letra (A, B, C, D) corresponde a la reacción según los niveles en estudio de cada variable (Tabla 3) y los números arábigos indican que se realizó cada reacción por triplicado (1, 2, 3). Se observa que de las reacciones B y D que fueron realizadas con la zeolita ZSM-5 se obtuvo mayor volumen de productos líquidos (160 ml-170 ml) con respecto a las reacciones A y C que fueron realizadas con la zeolita Y (77 ml-91 ml). Sin embargo, al comparar los valores de volumen obtenidos con cada zeolita, variando la relación másica catalizador/parafina, no se observa una diferencia significativa. Según los datos mostrados en la Tabla 5, para la zeolita ZSM-5 con una relación 0.40:1 se obtuvo un volumen promedio de 166 ml, mientras que para la misma zeolita con una relación 0.20:1 se obtuvo un volumen promedio de 164 ml. Por lo que, con base en estos resultados podría considerarse que el tipo de catalizador tiene un efecto mayor sobre el volumen de productos líquidos obtenido que la relación másica catalizador/parafina.
Además, en la Tabla 5 se muestran los resultados de rendimiento a productos líquidos, Es evidente que con la zeolita ZSM-5 se obtuvieron valores de rendimiento mayores (26.4-29.9 %) que con la zeolita Y (11.9-15.1 %). En cuanto a la relación másica catalizador/parafina, las relaciones estudiadas parecen no tener un efecto evidente sobre el rendimiento. Souza et al. [16] indican que, si bien las conversiones generalmente aumentan al incrementar la relación másica catalizador/parafina, la cantidad del catalizador también llega a un límite donde las conversiones y selectividades se mantienen constantes. Sin embargo, habría que probar otras relaciones más amplias para comprobar este hecho.
Tabla 5 Valores de volumen y rendimiento a productos líquidos para cada corrida del primer experimento.
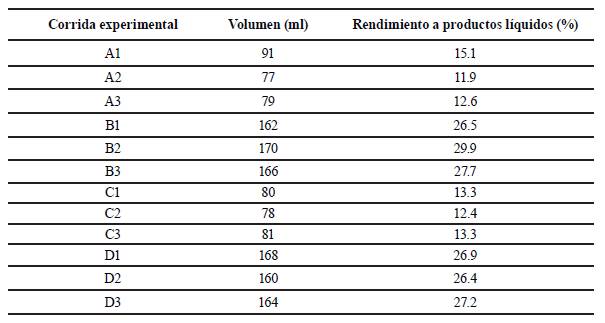
Según Chang et al. [17], la cantidad de sitios ácidos del catalizador está cercanamente relaciona-da a su actividad en el proceso de hidrocraqueo. Además, Decroocq [7] indica que la actividad de esta clase de catalizadores se debe a sus sitios ácidos, los cuales dependen del contenido de aluminio. En esta investigación no se midió la acidez de las zeolitas, sin embargo, según los datos mostrados en la Tabla 1, la zeolita Y tiene una relación Si/Al de 6 mientras que la zeolita ZSM-5 tiene una relación Si/Al de 25, con lo cual podría considerarse que la zeolita Y tiene mayor acidez [18]. Ohkita et al. [19] en su estudio de craqueo térmico de polietileno sobre silica-alúmina a 400 °C observó que un incremento en la acidez del catalizador aumentó la cantidad de productos gaseosos obtenidos y disminuyó la cantidad de aceites obtenidos. Por lo que la menor acidez de la zeolita ZSM-5 empleada en esta investigación, podría ser una razón por la cual se obtuvo rendimientos mayores a productos líquidos con la zeolita ZSM-5 con respecto a la zeolita Y. Por otra parte, Akpanudoh et al. [20] determinaron que un exceso de zeolita y por tanto de acidez, claramente promueve un sobre-craqueo de los líquidos produciendo más productos gaseosos.
Además, el menor rendimiento a productos líquidos obtenido con la zeolita Y podría deberse también al tamaño de poro [21], que en este caso es de 7 Å. Ratnasari et al. [18] mencionan que la acidez de un catalizador provee la actividad catalítica mientras que el tamaño de poro provee la selectividad de tamaño. Según Manos et al. [22], es razonable considerar que las macromoléculas de plástico se rompen primero en la superficie externa del catalizador, y solo ciertos fragmentos pueden entrar a la estructura de poros del catalizador para producir moléculas más pequeñas e incrementar el rendimiento a productos gaseosos (cadenas de C1 a C4). En la presente investigación, la zeolita Y con un tamaño de poro de 7 Å tendría mayor posibilidad de permitir el ingreso de fragmentos grandes en sus poros y generar más productos gaseosos que la zeolita ZSM-5 con un tamaño de poro de 5 Å. Además, la zeolita Y tiene mayor área superficial (650 m2/g) que la zeolita ZSM-5 (340 m2/g) y según Syamsiro et al. [23] áreas superficiales más altas permitirán mayor contacto entre las moléculas de reactivos y el catalizador lo cual significa un mayor craqueo hacia hidrocarburos de cadenas más cortas como productos gaseosos. La fase gas no fue analizada en esta investigación, sin embargo, de forma visual se evidenció la formación de gran cantidad de gases con la zeolita Y.
Por otra parte, a los resultados de rendimiento de la Tabla 5 se les aplicó un análisis ANOVA de dos vías, para determinar si los factores estudiados tienen un efecto significativo sobre los resultados de rendimiento obtenidos. En este análisis se consideró un 95% de confianza y se tomó en cuenta la posible interacción de los dos factores en estudio. Los resultados obtenidos de dicho análisis se muestran en la Tabla 6. Se observa que para el caso del factor relación másica catalizador/parafina el valor de 0.94 para F es menor que el valor de F crítico de 7.71 utilizando la prueba Fisher. Por tanto, no se tiene suficiente evidencia para rechazar la hipótesis nula indicando así que este factor no afecta significativamente el rendimiento a productos líquidos ya que no existe diferencia significativa entre las medias de este factor. Para corroborar dicha situación se evaluó el valor de p el cual es de 0.360, valor superior al nivel de significancia de 0.05, por lo cual se confirma que la hipótesis nula no puede rechazarse.
Al analizar los valores de F y de p para el caso del factor tipo de catalizador (Tabla 6), se determina que este factor sí afecta de manera significativa y se rechaza la hipótesis nula indicando de esta manera que sí existe diferencia significativa entre las medias de este factor. Para el caso del valor F se obtuvo un valor de 395.30 mientras que el valor crítico es de apenas 7.71, el valor de p por otra parte fue de 4.3x10-8 el cual es un valor menor con respecto al nivel de significancia de 0.05. Estas dos razones llevan a la conclusión que el factor tipo de catalizador sí afecta de manera significativa el rendimiento a productos líquidos obtenido.
Además, en la Tabla 6 se observa que para la interacción de los dos factores (relación másica catalizador/parafina y tipo de catalizador) se obtuvo un valor de F de 0.48, dicho valor es menor que el valor critico de F de 7.71, razón por la cual se determina que la interacción de los factores no afecta de manera significativa el rendimiento a productos líquidos. Para reafirmar dicha situación, se analizó de la misma manera el valor de p, este fue de 0.508 lo que determina que al ser superior al nivel de significancia (0.05) debe de aceptarse la hipótesis nula y por tanto concluir que la interacción no afecta de manera significativa la variable de respuesta.
Aunado a lo anterior, se analizaron los valores de las sumas ajustadas de cuadrados para cada una de las fuentes de variación con el objetivo de determinar cuál de estas fuentes de variación afecta de mayor manera la variación total de la variable de respuesta de este experimento. Según los datos de sumas de cuadrados mostrados en la Tabla 6, es notable que la fuente que produce más variación en los datos obtenidos es el factor tipo de catalizador el cual es responsable de un 97.67 % de la variación total, por esta razón se dejó fijo este factor durante la aplicación del experimento 2 en el nivel que presentó una media de rendimiento a productos líquidos mayor, el cual fue la zeolita ZSM-5. Por otra parte, dado que se obtuvo que el factor de la relación másica catalizador/ parafina no afecta de manera significativa la variable de respuesta, se decidió utilizar el nivel menor (0.20:1) de este factor para reducir costos operativos. Por tanto, se fijaron las variables anteriores y se estudió el efecto de la temperatura de reacción en dos niveles: 400°C y 440°C. En la Tabla 7 se presentan los resultados de rendimiento a productos líquidos obtenidos para el segundo experimento, según la nomenclatura empleada, la letra (E, D) corresponde a la reacción según la temperatura en estudio (E:400 °C, D:440°C) y los números arábigos (1, 2, 3, 4, 5) indican que se ejecutaron 5 corridas experimentales para cada nivel.
Sriningsih et al. [8] mencionan que la conversión de residuos plásticos a productos líquidos aumenta conforme aumenta la temperatura de 350°C a 450°C, esto debido a que, según la ecuación de Arrhenius, la constante de velocidad de reacción se incrementa con la temperatura. Sin embargo, obtuvieron porcentajes de rendimiento muy similares al emplear el catalizador Ni/ZSM-5 a 350 °C (23.89 %), a 400°C (24.69 %), y a 450°C (30.64 %). Además, Sriningsih et al. [8] concluyen que la temperatura de 350 °C es la más efectiva ya que, al pasar de 350 °C a 400 °C, la cantidad de carbón generado pasó de 0.94% a 1.10%, respectivamente. De forma similar, en la presente investigación se obtuvieron porcentajes de rendimiento muy cercanos entre sí (Tabla 7), se obtuvo un rendimiento promedio de 27.52 % a 400°C mientras que a 440°C se obtuvo un rendimiento promedio de 25.67% (Tabla 8). Estos resultados sugieren que a la más alta temperatura (440°C) el catalizador podría estar experimentando pérdida de sitios activos por sinterización o por deposición de carbón, sin embargo, para comprobarlo se tendría que medir el área superficial y la cantidad de carbón depositado después de reacción.
Para ver si existen diferencias significativas entre los resultados obtenidos a ambas temperaturas de estudio se aplicó una prueba t de Student a los resultados de rendimiento de la Tabla 7, se consideró dicho estudio para un 95 % de confianza y se supuso varianza igual para ambas muestras. Los resultados obtenidos de dicho análisis se muestran en la Tabla 8.
Para este caso en específico se obtuvo un valor t de Student de 3.36, mientras que el valor crítico para un 95 % de confianza es de 2.306 indicando así que se rechaza la hipótesis nula y que por lo menos una media del factor en estudio es diferente. Para este caso el valor p obtenido fue de 0.028, menor al valor de significancia de 0.05, por tanto, se rechaza la hipótesis nula indicando que sí existe diferencia significativa entre ambas muestras.
DENSIDAD DE LOS PRODUCTOS OBTENIDOS
Por otro lado, como parte de esta investigación se realizaron análisis que permitieran determinar de manera aproximada la composición química de los productos obtenidos y la distribución de los rangos de cadena de los hidrocarburos obtenidos. Este análisis brinda aún más información sobre los efectos de los factores evaluados, ya que se determina cuáles productos aproximados se están obteniendo y si estos dependen de los factores estudiados durante el proceso de craqueo catalítico.
Al tratarse de un producto líquido combustible, debe analizarse una propiedad física de medición sencilla como lo es la densidad. Esta propiedad es utilizada en diversos combustibles de uso común como una referencia de los componentes que pueden haber dentro de este compuesto y que aportan de distinta manera debido a su peso molecular. En otras palabras, la densidad puede indicar si los productos obtenidos son livianos o pesados y esto brindaria una aproximación a los rangos de cadena obtenidos. Los resultados de densidad corregida a 15.56°C, tal como se mencionó en la sección de metodologia, para las muestras analizadas se observan en la Tabla 9.
Como se aprecia en la Tabla 9, en los valores promedios de densidad obtenidos para cada condición de reacción, 819.6 kg/m3 para 400°C y 800.2 kg/m3 para 440°C, los productos obtenidos para la temperatura menor son más pesados que los obtenidos a la temperatura mayor. Esta diferencia en densidad promedio debe de estar directamente relacionada con los productos obtenidos durante el proceso de craqueo, sugiriendo que los productos obtenidos a una temperatura menor son más pesados y por ende se esperaría una mayor cantidad de productos con cadenas de hidrocarburos más extensas cuando se analicen estos productos. Según Sung et al. [24], un aumento de la temperatura incide en la conversión hacia materiales más volátiles y reduce la formación de polímeros pesados o coque, lo cual coincide con lo obtenido en esta investigación.
Se decidió comparar estos valores de densidad promedio con la densidad de los combustibles comercializados a nivel nacional por RECOPE, ya que se considera que dentro de los productos obtenidos se encuentran componentes que pueden utilizarse como combustibles y que podrían por ende ser separados por medio de un proceso de destilación. La Autoridad Reguladora de los Servicios Públicos (ARESEP) realiza fiscalizaciones a los productos comercializados por RECOPE y presenta de manera anual un reporte con los resultados de los parámetros analizados para cada combustible distribuido a nivel nacional. De acuerdo con el informe presentado por ARESEP para el año 2017 [25], se reportan las densidades promedio para los productos Gasolina Regular, Diésel, Jet A-1 y Av Gas en los planteles de distribución respectivos como se aprecia en la Tabla 10.
Tabla 10 Densidades promedio en kg/m3 a 15.56°C para los productos en los planteles de distribución de RECOPE [25]
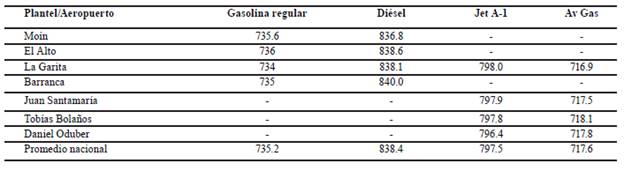
Al comparar los resultados promedio de la Tabla 10 con los obtenidos para los productos líquidos analizados en esta investigación (Tabla 9) se aprecia que los mismos, si bien son una mezcla compleja de diversos productos, pueden contener cortes de productos muy similares a los compuestos presentes en los combustibles de RECOPE ya que presentan densidades que se encuentran entre los promedios para el combustible más pesado (diésel con un promedio de 838.4 kg/ m3) y el más liviano (Av Gas con un promedio de 717.6 kg/rrr3). Con estos resultados preliminares se podría pensar entonces que al aumentar la temperatura de reacción se obtienen productos más livianos de hidrocarburos, ya que la densidad promedio de las muestras obtenidas a 400°C es mayor que la obtenida a 440°C, es decir, se logra un mayor craqueo de las cadenas largas de hidrocarburos presentes en las parafinas tratadas y por ende se obtienen productos más livianos en la muestra de líquido examinada. Este hecho se evalúa más a fondo con los resultados de los análisis cromatográficos de los productos.
DISTRIBUCIÓN DE CADENAS DE ÁTOMOS DE CARBONO EN LOS PRODUCTOS LÍQUIDOS
La temperatura de reacción afectó de manera significativa el rendimiento a productos líquidos, como se concluyó durante la aplicación del diseño experimental, sin embargo, debe de analizarse además si la temperatura afecta la gama de productos obtenidos y su concentración relativa. Por esta razón, se tomó la decisión de analizar los productos obtenidos utilizando ambas temperaturas de reacción, por lo que aunado al análisis de densidad, para determinar la composición química aproximada de los hidrocarburos presentes se utilizó cromatografía de gases. El método empleado se basó en la norma ASTM D2887 [26], como la mejor manera para determinar las longitudes de cadena y caracterizar los productos líquidos obtenidos.
Además de analizar las muestras, se realizaron 4 corridas con los combustibles Gasolina Regular, Diésel, Jet A-1 y Av Gas que son distribuidos a nivel nacional por RECOPE, esto con el objetivo de obtener una referencia cromatográfica para los productos obtenidos del craqueo, así como para corroborar el correcto funcionamiento del método desarrollado. Estos cromatogramas se muestran en las Figuras 1 y 2. En la Figura 1 se aprecia la similitud entre los combustibles Jet A-1 y Diésel en relación a que presentan absorbancias menores a las 3500 unidades y una gran concentración de sustancias alrededor de los 5 min de retención y hasta los 30 min, siguiendo un comportamiento de aumento creciente en la concentración de las sustancias y luego un decrecimiento notable. Para el caso específico del diésel (Figura 1a), se encuentran compuestos más pesados siendo que los mismos comienzan a presentar concentraciones importantes alrededor de los 10 min de retención y continúan hasta los casi 30 min, por otra parte, el combustible Jet A-1 (Figura 1b) presenta concentraciones importantes de compuestos desde los 5 min y comienzan a disminuir al acercarse a los 20 min, indicando así que este último es un combustible más liviano. Esto se corrobora al comparar las densidades de ambos combustibles (Tabla 10) siendo que la del diésel es casi 20 kg/m3 mayor que la del combustible de aviación.
Estos combustibles contrastan con los carburantes más livianos como lo son la gasolina regular y Av Gas mostrados en la Figura 2, los cuales presentan tiempos de retención inferiores a los 15 min y a los 10 min, respectivamente. Ambos combustibles presentan absorbancias cercanas a las 35 000 unidades en tiempos muy cortos de retención, indicando de esta manera la gran presencia de sustancias volátiles y por ende se podría esperar una densidad menor para ambos combustibles ya que se consideran compuestos más livianos, tal como se observa en la Tabla 10.
Se presentan entonces dos posibles escenarios a observar durante los análisis cromatográficos de las muestras obtenidas del craqueo de las parafinas en esta investigación. En primera instancia, se puede presentar una gama de productos más pesados y con concentraciones más distribuidas en un tiempo de retención extenso como lo son los combustibles más pesados como el Jet A-1 y el diésel, o se pueden presentar combustibles más livianos con bajos tiempos de retención como la gasolina y el Av Gas.
En la industria de refinación se relaciona generalmente un cierto rango de cadena de productos como los principales componentes de los combustibles diésel, gasolina y Jet A-1. Estos rangos de cadena son desde C5 hasta C10 para las gasolinas, de C9 hasta C15 para el combustible de aviación Jet A-1 y de C12 hasta C20 para el diésel. Para conocer aproximadamente dónde se ubican esta clase de compuestos en los cromatogramas se realizó una corrida utilizando 5 compuestos patrones de heptano, isoctano, xilenos, decano, duodecano, tetradecano y hexadecano. Este cromatograma con la señal de cada compuesto patrón se muestra en la Figura 3.
Es importante notar el tiempo de retención al cual se obtiene la señal para los patrones analizados, ya que este tiempo puede utilizarse de referencia para identificar los posibles compuestos presentes en las mezclas complejas de los combustibles, tanto los utilizados de referencia como los de las muestras obtenidas del proceso de craqueo catalítico. Por ejemplo, las señales de mayor absorbancia obtenidas para el combustible diésel (Figura 1a) comenzaron aproximadamente a los 10 min de retención y fueron decreciendo hasta casi los 25 min de retención, obteniéndose la señal de mayor absorbancia a los 17 min. Este ámbito de tiempo de retención permite relacionar con seguridad la presencia de compuestos que poseen cadenas de carbonos de longitudes desde los 10 carbonos hasta por encima de 16 carbonos.
Al contar con cromatogramas para cada uno de los combustibles distribuidos a nivel nacional (Figura 1 y Figura 2) y con un patrón de compuestos (Figura 3) que permitan determinar los posibles cortes de cadenas de carbono, se procedió con el análisis de las muestras obtenidas del proceso de craqueo en esta investigación. Se analizaron 8 muestras en total, siendo 4 muestras tomadas a una temperatura de reacción de 400°C y las 4 restantes a 440°C. Se analizaron las muestras 2, 3, 4 y 5 para las corridas ejecutadas a 400°C y las muestras 1, 2, 3 y 4 para las corridas realizadas a una temperatura de 440°C. Es importante comparar primero si dentro de las mismas condiciones de reacción existe alguna diferencia en cuanto al comportamiento de los productos obtenidos. Para verificar esto, en la Figura 4(a) se muestra la superposición de los cromatogramas de las muestras obtenidas a 400°C, y en la Figura 4(b) se muestra la superposición de los cromatogramas de las muestras obtenidas a 440°C.
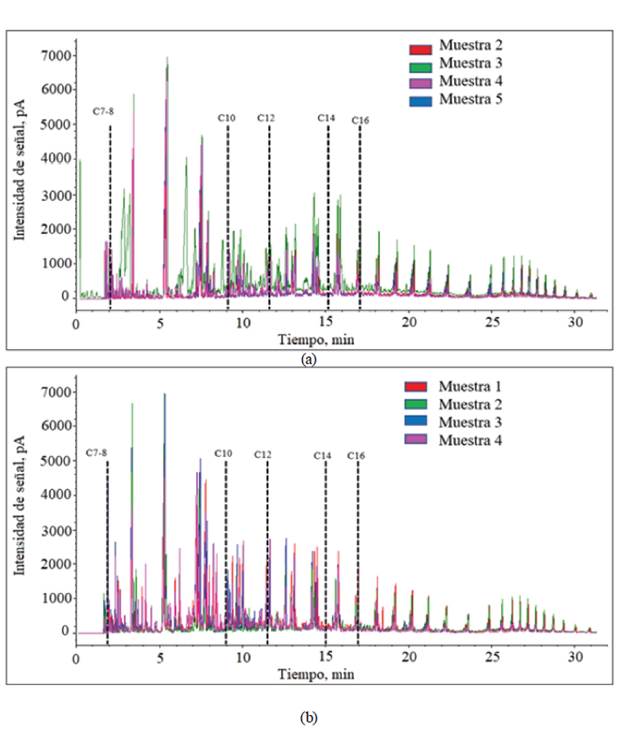
Figura 4 Superposición de los cromatogramas de las 4 muestras analizadas obtenidas a una temperatura de (a) 400 °C, (b) 440 °C.
De la Figura 4(a) se aprecia claramente que las 4 muestras obtenidas a 400°C tienen comportamien -tos similares en cuanto a los productos obtenidos, ya que presentan tendencias casi idénticas en cuanto a los tiempos de retención para los compuestos contenidos. Al sobreponer con líneas punteadas los tiempos de retención en los cuales se obtuvieron los patrones anteriormente (Figura 3), se aprecia que la mayor cantidad de productos obtenidos se encuentra por debajo de los 16 carbonos. De la misma forma en la Figura 4(b) se observa que para las 4 muestras tomadas a 440°C se obtuvieron resultados consistentes entre las corridas indicando que, si bien en algunas muestras se obtuvo mayor concentración de algunos cortes de compuestos, las muestras presentan un contenido similar respecto a los cortes de los productos craqueados. De ambos resultados se identifica entonces que el proceso permite obtener productos con cortes similares al utilizar las mismas condiciones de reacción.
Las diferentes longitudes de cadenas de carbonos encontradas en las muestras son similares a las encontradas en otros estudios. Sharratt et al. [27] reportan que a partir del craqueo de polietileno de alta densidad (HDPE) sobre ZSM-5 a 360°C obtuvieron alrededor de 70 wt.% de productos en el rango de C1 a C4, y de 25 a 30 wt.% de productos en el rango de fracciones de la gasolina (C5-C9). Por otra parte, Ratnasari et al. [18] reportan gran cantidad (90% en área) de hidrocarburos en el rango de las gasolinas (C8-C12) y un 10% en área de hidrocarburos de alto peso molecular (C13+) para la conversión de HDPE sobre ZSM-5. San Miguel et al. [28] concluyen que el uso de la zeolita HZSM-5 condujo a la formación de productos en el rango de las gasolinas (C8-C12). Sin embargo, es importante aclarar que los productos obtenidos dependerán de la materia prima alimentada al reactor [24]. Syamsiro et al. [23] concluyen en su investigación que los tipos de materia prima afectan fuertemente los rendimientos del producto y la calidad de los productos líquidos y sólidos obtenidos.
Se decidió comparar una muestra obtenida a cada una de las condiciones estudiadas con tres combustibles distribuidos a nivel nacional como lo son el diésel, la gasolina regular y el Jet A-1. Estas comparaciones se realizaron sobreponiendo los cromatogramas necesarios en cada caso, y se aprecian en las Figuras 5, 6, y 7. Al comparar tanto en la Figura 5(a) la muestra obtenida a 400°C como en la Figura 5(b) la muestra obtenida a 440°C con el diésel distribuido por RECOPE, claramente se observa que los componentes comunes del combustible diésel se encuentran presentes en las muestras obtenidas por el proceso de craqueo en esta investigación. Aunque para el diésel la concentración de estos es mayor, los tiempos de retención para los productos son muy similares llevando a considerar que dentro de la matriz completa de productos craqueados se podría obtener un producto como el diésel luego de un proceso de separación adecuado como lo sería la destilación. Además, se puede apreciar como los cortes de los patrones en el combustible diésel coinciden con los heurísticos mencionados anteriormente, en el sentido de que la mayor concentración de compuestos para el diésel ronda los C12 hasta C20 y en el cromatograma estos intervalos se cumplen para el combustible distribuido por RECOPE y se aprecia la presencia de estos mismos componentes en las muestras obtenidas del proceso en estudio.
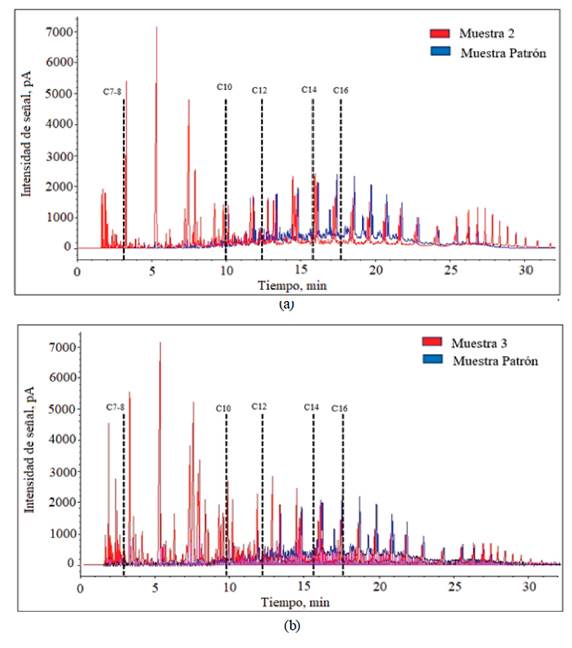
Figura 5 Superposición de los cromatogramas de (a) la muestra 2 a 400°C (señal roja) y (b) la muestra 3 a 440°C (señal roja), con la muestra patrón de combustible diésel (señal azul).
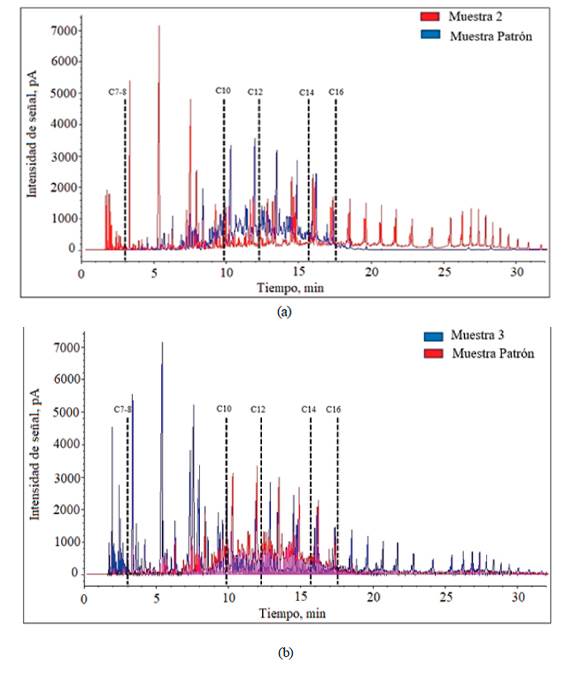
Figura 6 Superposición de los cromatogramas de (a) la muestra 2 a 400˚C (señal roja) con la muestra patrón de Jet A-1 (señal azul)y (b) la muestra 3 a 440˚C (señal azul), con la muestra patrón de Jet A-1 (señal roja)

Figura 7 Superposición de los cromatogramas de (a) la muestra 2 a 400°C (señal roja) y (b) la muestra 3 a 440°C (señal roja), con la muestra patrón de gasolina regular (señal azul).
Para el caso de la comparación con el combustible Jet A-1 con las muestras recolectadas a 400°C y a 440°C, se muestran en la Figura 6(a) y Figura 6(b), respectivamente. Al ser combustibles similares al diésel, en cuanto al rango de cadenas de carbono que los representan, podría esperarse que también dentro de la matriz de productos obtenidos de la reacción se obtengan productos similares al Jet A-1. Como bien se aprecia en la Figura 6, algunas señales de los compuestos del Jet A-1 están presentes en ambas muestras, siendo que para el caso de la muestra obtenida a mayor temperatura (Figura 6b) se presenta una mayor concentración de productos livianos como se discutió anteriormente. Se aprecia que para el combustible Jet A-1 las mayores concentraciones se obtienen entre el C10 y el C16 adecuándose a lo mencionado en el heurístico que ronda cadenas de 9 hasta 15 carbonos. De esta manera, podría esperarse entonces que sea posible obtener un combustible similar a este combustible de aviación, luego de realizar al producto de reacción un proceso de refinado adecuado.
De la misma manera se analizaron las muestras recolectadas a 400°C y 440°C contra una muestra de gasolina regular y se muestran en la Figura 7(a) y Figura 7(b), respectivamente. Se aprecia como también se presentan compuestos en los tiempos de retención presentes en la gasolina regular (Figura 2b), indicando la posibilidad de obtener un producto con características similares a la gasolina, luego de un proceso de separación adecuado. Se verifica el cumplimiento del heurístico respecto a la gasolina ya que presenta la mayor concentración entre compuestos de cadenas entre 5 y 10 carbonos y estas mismas sustancias se encuentran presentes en el producto craqueado.
Debe de aclararse que estas comparaciones se están realizando entre productos listos para su comercialización, como lo son diésel, combustible de aviación Jet A-1 y gasolina regular, y el "crudo" obtenido del proceso de craqueo. Esto aclara por qué la concentración no es la misma para los compuestos analizados, al presentar absorbancias menores, ya que se está comparando un producto refinado terminado contra una mezcla de posibles compuestos obtenidos de un proceso de reacción a los cuales se les está buscando una posible aplicación.
De estas comparaciones se puede observar entonces que la matriz de productos obtenidos del proceso de craqueo en esta investigación puede tratarse como un "crudo" de derivados de hidrocarburos, con cadenas de entre 5 y 16 carbonos, que podría ser procesado para obtener distintos productos importantes en la industria de los combustibles, dentro de los cuales destaca la posibilidad de obtener productos similares al diésel, combustible de aviación Jet A-1 y gasolina regular.
CONCLUSIONES
En esta investigación se evaluó el efecto del tipo de catalizador, la temperatura de reacción y la relación másica catalizador/parafinas en la conversión de parafinas, provenientes de residuos de la pirólisis de plásticos, a través de un proceso de craqueo catalítico. Se determinó por medio de un ANOVA de dos vías que el factor del tipo de catalizador afecta significativamente el rendimiento a productos líquidos, y que la relación másica catalizador/parafina no afecta de manera significativa el rendimiento a productos líquidos, ambos análisis realizados con un 95% de confianza. Se determinó que al utilizar el catalizador zeolita ZSM-5 se obtuvo rendimientos mayores a productos líquidos (26.4-29.9 %) que con la zeolita Y (11.9-15.1 %). Además, se determinó que el factor de temperatura de reacción sí afecta de manera significativa el rendimiento a productos líquidos con un 95 % de confianza de acuerdo con el análisis realizado por medio de una prueba de t de Student.
Se obtuvo una densidad promedio de 819.6 kg/m3 para los productos obtenidos a 440°C y de 800.2 kg/m3 para los productos obtenidos a 400°C, por lo que los productos obtenidos a 440°C fueron en promedio más pesados que los obtenidos a 400°C, indicando que el proceso de craqueo fue más efectivo conforme se aumentó la temperatura. Por medio de los valores de densidad obtenidos, puede considerarse que los productos obtenidos del proceso de craqueo presentan cortes de productos con una composición similar a los compuestos presentes en los combustibles de RECOPE ya que presentan densidades que se encuentran entre los promedios para el combustible más pesado (diésel con un promedio de 838.4 kg/m3) y el más liviano (Av Gas con un promedio de 717.6 kg/rrr3). Además, a través de los análisis cromatográficos realizados a las muestras de reacción y a las muestras patrón, se observó que el crudo obtenido del craqueo catalítico contiene productos con cadenas de carbono que van desde los 5 hasta los 16 carbonos, y que podría ser procesado para obtener distintos productos importantes en la industria de los combustibles, dentro de los cuales destaca la posibilidad de obtener productos similares al diésel (C12 a C20), combustible de aviación Jet A-1 (C9 a C15) y gasolina regular (C5 a C10).