1. INTRODUCCIÓN
La producción y consumo de plásticos a nivel mundial se fundamenta, entre otras causas, en la baja densidad, alta resistencia química y bajo costo de estos materiales, propiedades que les confieren gran cantidad de aplicaciones en diferentes tipos de industrias. Pese a ello, los plásticos tienen una vida útil relativamente corta y (al menos en su forma convencional) no son biodegradables ni compostables, por lo que su alta demanda ha conllevado a que procesos cotidianos como la recolección de residuos sólidos urbanos impliquen una gran acumulación de materiales plásticos, llegando a ocasionar problemas ambientales, sociales y de salud pública en los sitios donde se acopian tales desechos [1], [2].
Según datos del Ministerio de Ambiente y Desarrollo Sostenible de Colombia, solo durante 2016 la generación de residuos sólidos en el país rondó los 9.5 millones de toneladas, de los cuales el 14 % correspondía a plásticos [3]. El manejo de estos residuos plásticos a través de un adecuado tratamiento o proceso de reciclaje primario (re-extrusión), secundario (mecánico), ternario (químico) y/o cuaternario (recuperación de energía) ayuda a disminuir el impacto de estos residuos, a la vez que puede representar una valiosa fuente de materiales reciclados, energía e ingresos [4], [5]. Los métodos primario y secundario para el reciclaje de plásticos se clasifican como convencionales e incluyen procesos como clasificación y molienda, técnicas con las cuales es posible recuperar entre un 15 y 20 % del total de residuos plásticos [4]. Por su parte, los métodos ternario y cuaternario pueden incluir procesos de transformación termoquímica como pirólisis o gasificación, que además de permitir el aprovechamiento energético de los residuos plásticos puede disminuir su volumen hasta en un 90 % [6].
La pirólisis es una técnica de reciclaje en la que se da la descomposición térmica de los polímeros en ausencia de oxígeno o con una cantidad limitada del mismo, normalmente a temperaturas entre 300 y 900°C [4H7]. Dependiendo de la temperatura a la cual se dé la pirólisis y otras condiciones de operación del proceso (como presión, flujos o carga de materia prima, velocidad de calentamiento, tiempo de exposición, etc.), pueden obtenerse mezclas de productos sólidos, líquidos y/o gaseosos en diferente proporción y con diferente composición.
Normalmente los productos sólidos se clasifican como cenizas y corresponden mayoritariamente a materiales inertes que pueden entrar en el proceso de acuerdo con la materia prima utilizada y el carbono formado por las reacciones que se pueden dar durante el proceso. Los productos gaseosos pueden clasificarse como gas de síntesis (syngas) y contienen los gases no condensables, como H2, CH4, C2H6, C2H4, CO, CO2, entre otros. Por último, el producto líquido suele clasificarse como biocombustible (o combustible sintético) y consiste en una mezcla de olefinas, fenoles y compuestos aromáticos caracterizados por la ausencia de oxígenos como sustitutos, tales como benceno, naftaleno, antraceno, tolueno, indeno, entre otros [8]. La composición de cada una de estas corrientes también dependerá de la naturaleza o composición de los plásticos o residuos que se utilizan como materia prima en el proceso.
En el caso de los residuos sólidos municipales, los tipos de plásticos más comúnmente encontrados son el polietileno tereftalato (PET), polipropileno (PP), poliestireno (PS), polietileno de alta densidad (HDPE) y polietileno de baja densidad (LDPE), entre otros [9]. En la tabla 1 se presenta una clasificación de estos materiales de acuerdo con su composición según análisis próximo, es decir, su contenido de humedad, carbono fijo, material volátil y cenizas, así como su análisis último o elemental (contenido de carbono, hidrógeno, oxígeno y nitrógeno).
Tabla 1 Análisis próximo y último de algunos plásticos comunes en los residuos sólidos municipales
Caracterización | PET | PP | PS | HDPE | LDPE |
---|---|---|---|---|---|
Análisis próximo (% peso) | |||||
Humedad | 0,46 a 0,61 b | 0,18 b 0,10 c | 0,25 a 0,30 b | 0,00 b | 0,30 a 0,10 c |
Carbono fijo | 7,77 a 13,17 b | 0,16 b 2,30 c | 0,12 a 0,20 b | 0.03 b | 0,00 a 0,20 c |
Material volátil | 91,75 a 86,83 b | 97,85 b 97,70 c | 99,63 a 99,50 b | 98,57 b | 99,70 a 99,80 c |
Cenizas | 0,02 a 0,00 b | 1,99 b 0,00 c | 0,00 a 0,00 b | 1,40 b | 0,00 a 0,00 c |
Análisis último (% peso) | |||||
C | 62,95 c | 83,25 c 86,10 d | 89,81 c 90,20 d | 83,90 d | 83,67 c |
H | 4,12 c | 14,76 c 13,70 d | 7.48 c 8,50 d | 14,70 d | 16,33 c |
O | 32,93 c | 0,00 c 0,20 d | 0,00 c 1,30 d | 0,00 d | 0,00 c |
N | 0,00 c | 0,00 c 0,00 d | 2,71 c 0,00 d | 0,00 d | 0,00 c |
a referencia [2], b referencia [10], c referencia [11], d referencia [12].
Fuente: autores usando datos de las referencias [2], [10], [11] y [12].
Las diferentes posibilidades de operación de un reactor de pirólisis, así como la gran variedad de plásticos (y sus diferentes composiciones), dan lugar a una elevada combinación de subproductos que pueden tener diversas aplicaciones. De este modo, explorar las condiciones que favorezcan la producción y calidad de algún o algunos productos en particular (por ejemplo, los combustibles sintéticos) puede llegar a ser una tarea dispendiosa en tiempo y recursos, incluso a partir de una materia prima dada. En ese aspecto, el uso razonable de herramientas computacionales que ayude a simular y predecir la cantidad y composición de los productos de pirólisis de plásticos se hace fundamental para estudiar y determinar las mejores condiciones de operación para la obtención de algún o algunos productos en particular a partir de la valorización de residuos plásticos.
Para tal fin, uno de los software o paquetes computacionales más frecuentemente utilizado es el software Aspen Plus. Peters y colaboradores [13] utilizaron un modelo en Aspen Plus para simular la pirólisis de materiales lignocelulósicos, basados en la cinética de las principales reacciones involucradas. El modelo les permitió analizar el efecto de diferentes parámetros de operación sobre la cantidad y calidad de los productos, además de predecir la composición de los productos líquidos obtenidos. La validación de sus modelos la realizaron a partir de reportes de la literatura. Suárez y colaboradores [14] simularon la obtención de un gas de síntesis útil para la obtención de biocombustibles, también a partir de material lignocelulósico y en Aspen Plus, pero en este caso los autores emplearon una aproximación a través de equilibrios termodinámicos para simular el proceso de gasificación. Otros autores han reportado modelos similares en Aspen plus para estudiar la pirólisis de llantas usadas, llegando a predecir mediante estos la formación de más de 110 productos de interés dependiendo de las condiciones de operación [15]. También se ha reportado el uso del software Aspen plus en la simulación de la pirólisis de desechos municipales para obtener biocombustibles, biochar y gas de síntesis [16], validando los modelos mediante la comparación de resultados simulados y datos experimentales. Estos autores posteriormente utilizaron sus modelos para determinar condiciones de operación que permiten optimizar la producción de biocombustibles a partir de dichos residuos.
Específicamente para la simulación de la transformación termoquímica de plásticos, Nasir y Lagtah [17] reportaron modelos de diferente nivel de complejidad en Aspen Hysys para diseñar, simular y optimizar la obtención de hidrocarburos líquidos (combustibles sintéticos) a partir de la pirólisis de LDPE, validando sus modelos a partir de datos experimentales. Otros autores [18] también utilizan Aspen Hysys para simular la conversión de residuos plásticos y estudiar las condiciones que favorezcan la producción de hidrocarburos específicos como gas, nafta, diésel, parafinas, ole-finas, naftenos y aromáticos, incluyendo además análisis técnico económicos apoyados en los resultados de las simulaciones. Por su parte, Bartonhill [19] utilizó un modelo termodinámico en Aspen Plus para simular y optimizar la pirólisis de PP, incluyendo en el modelo tanto procesos físicos como químicos que permiten predecir la composición de los gases formados en el proceso, mientras que otros autores han reportado el uso de modelos similares (en equilibrio) para estudiar la gasificación de materiales como el polietileno [20].
Del análisis de la literatura consultada se concluye que efectivamente el software Aspen Plus resulta útil para modelar y simular la transformación termoquímica de diferentes tipos de plásticos u otras materias primas y que, bien a partir de modelos cinéticos o de modelos en equilibrio termodinámico, cada uno de ellos mediante aproximaciones simplificadas o detalladas puede utilizarse para predecir razonablemente la formación y propiedades de productos específicos, como por ejemplo, los combustibles sintéticos. No obstante, dadas las múltiples combinaciones de operación y propiedades o composición de la materia prima, así como las suposiciones o simplificaciones que se incorporen en el modelo, es necesaria una validación adecuada para garantizar la confiabilidad de los resultados que arroje el software.
En esta contribución se proponen y comparan dos modelos en Aspen Plus versión 8.7 (uno cinético y otro en equilibrio termodinámico) que permiten simular y estudiar la pirólisis de algunos plásticos comunes encontrados en residuos sólidos municipales en Colombia. El objeto de la contribución es proveer una herramienta computacional razonable que permita analizar y tomar decisiones en cuanto a la posibilidad de reciclar residuos plásticos mediante su transformación termoquímica para la obtención de combustibles sintéticos, así como proveer una idea preliminar sobre la calidad de los combustibles que se obtienen mediante tales procesos.
2. METODOLOGÍA
Simulación de la pirólisis de plásticos en el software Aspen Plus
La implementación de los modelos en Aspen Plus (versión 8.7) se realizó de acuerdo con recomendaciones de la literatura para simular transformaciones termoquímicas; por ello se utilizaron dos aproximaciones diferentes: modelos basados en la termodinámica (utilizando reactores donde se minimiza la energía libre de Gibbs "RGIBBS") [14], [21] y modelos basados en la cinética (utilizando reactores por lotes "RBATCH") [2], [11], [15]. Para ambas aproximaciones, los plásticos cuya pirólisis se simuló en el proceso (PET, PP, PS, HDPE y LDPE) se ingresaron mediante la corriente ALIMENTO (figura 1) como sólidos no convencionales, caracterizándolos de acuerdo con datos de análisis próximo y último de cada material en base seca y con cenizas [21]. El bloque DESCOMP (figura 1) corresponde a un reactor de rendimiento (R-YIELD) en el cual, con ayuda de subrutinas en FORTRAN [14]-[21], se estimó la composición de cada plástico en elementos convencionales que permitieran posteriormente simular las reacciones (a partir de la termodinámica o la cinética, de acuerdo al modelo utilizado) en el bloque REACTOR (figura 1). En el modelo, los productos de pirólisis provenientes del reactor se dividen en dos corrientes (equipo SEP-1, Figura 1): una corriente de sólidos no convencionales remanentes que de acuerdo con los modelos utilizados se asume que solo contiene cenizas, y otra corriente que luego de enfriarse hasta temperaturas cercanas a la ambiente (30°c) en el equipo INTERCAM (figura 1), se divide en el equipo SEP-2 (figura 1) para obtener los productos gaseosos a través de la corriente PROD-GAS (no condensables) y los combustibles sintéticos a través de la corriente BIO-COMB (figura 1). Los modelos de Aspen plus y las condiciones de operación de cada bloque de la figura 1 se detallan en la tabla 2.
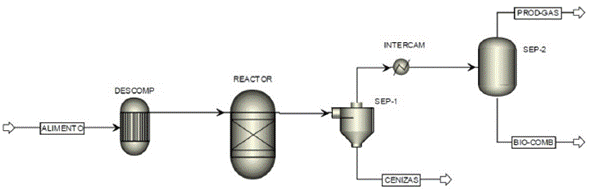
Fuente: autores.
Figura 1 Diagrama de flujo para simular el proceso de pirólisis de plásticos en Aspen Plus
Modelo termodinámico
Para la aproximación termodinámica se usó el modelo de reactor R-GIBBS de Aspen Plus. Este modelo resulta útil para estimar el rendimiento hacia las distintas fases de los productos (sólidos, líquidos y gaseosos), así como la composición de cada una de ellas, a partir de cada una de las materias primas (plásticos) simuladas en el proceso. No requiere especificar la estequiometria ni la cinética de las reacciones que ocurren durante la pirólisis, ya que incluye cálculos y subrutinas que permiten estimar equilibrios químicos y equilibrios de fases a partir de los átomos constituyentes de las sustancias involucradas mediante la minimización de la energía libre de Gibbs; por lo tanto, predice la formación de aquellas especies o compuestos que resulten termo-dinámicamente más estables según las condiciones de operación, de entre una lista de posibles productos suministrada por el usuario.
En este estudio se incluyeron alrededor de 90 posibles productos de acuerdo con reportes de la literatura para la pirólisis de plásticos como PET, PP, PS, LDPE. HDPE y PVC [2], [4], [22], y que incluyen (entre otros): agua, antraceno, acenafteno, acenaftileno, ácido benzoico, fenilbenzoico y acetilbenzoico, benceno, benzofenona, bifenilo, butanona, ciclohexano, cumeno, deceno, difenilmetano, difenilpropanos, dimetilbenceno, dimetilnaftalenos, estireno, etilnaftaleno, etilbenceno, etiltolueno, fluoreno, fenilnaftaleno, hepteno, hexeno, indeno, metil ciclopentano, metilfluoreno, metilnaftaleno, metilindeno, metilpentano, metil ciclopentano, metilestireno, noneno, naftaleno, octano, propanona, propilnaftaleno, propilbenceno, tolueno, trifenilbenceno y xileno (para los combustibles líquidos), e hidrógeno, metano, etano, etileno, propano, butano, buteno, dióxido de carbono, monóxido de carbono, nitrógeno, óxidos de azufre, óxidos de nitrógeno, oxígeno, amoniaco y cloruro de hidrógeno (para los gases).
Modelo cinético
El modelo cinético requiere la especificación de las reacciones (estequiometría y cinética) que se pueden presentar durante el proceso de pirólisis, por lo que puede llegar a proporcionar estimaciones más acertadas en cuanto a la distribución y la composición de las corrientes de productos, dependiendo de las condiciones del reactor y la composición del alimento. En esta investigación se utilizaron dos reactores por lotes RBATCH, en los cuales se ingresó información para alrededor de 90 reacciones diferentes que dan lugar a los mismos productos descritos en el modelo termodinámico, tomando toda la información cinética (factor de frecuencia y energía de activación) de la literatura [15]. En el primer reactor se ingresaron las reacciones primarias y en el segundo las reacciones secundarias que se dan en la fase vapor una vez los productos abandonan el primer reactor, aumentando los rendimientos hacia los combustibles líquidos [8]. Para las simulaciones se fijó un tiempo máximo de operación de los reactores de 1 hora. Si bien algunos productos de las reacciones incluyen elementos como flúor y nitrógeno que no se encuentran en todas las materias primas simuladas, se mantienen en el set de reacciones definido para dar mayor robustez al modelo y permitir su uso incluso en la simulación de la transformación termoquímica de otras materias primas.
Validación de los modelos
Para la validación de los modelos se siguieron dos estrategias diferentes. La primera consistió en simular la pirólisis de PP, PS. HDPE y LDPE bajo condiciones reportadas en la literatura y comparar los resultados de las simulaciones en cuanto a la distribución (% peso) de productos líquidos, sólidos y gaseosos. Igualmente se compararon algunas propiedades reportadas en la literatura para combustibles líquidos obtenidos por pirólisis de estos plásticos con las propiedades de los combustibles líquidos predichas por el software. Tales propiedades incluyen el poder calórico superior (PCS), octanaje mínimo de motor (MOR), octanaje mínimo investigativo (RON), índice antidetonante y densidad. Adicionalmente, los valores de estas propiedades se compararon con valores de referencia para gasolina y diésel, de modo que se pudiera obtener un indicio sobre la calidad de los combustibles líquidos obtenidos de acuerdo con las simulaciones.
La segunda estrategia consistió en realizar experimentalmente la pirólisis de PET y HDPE en un reactor de pirólisis artesanal y posteriormente simular las mismas condiciones experimentales en los modelos implementados en Aspen Plus para comparar la distribución (% peso) de productos líquidos, sólidos y gaseosos (estos últimos por diferencia en el balance de materia). Igualmente, se determinaron experimentalmente algunas propiedades para los combustibles líquidos producidos y estas se compararon con las propiedades de los combustibles predichas por el software. Las propiedades medidas experimentalmente fueron gravedad API (ASTM D 1298-12b), densidad, punto de anilina (ASTM D611) e índice de refracción.
Recolección y caracterización de muestras
Para la pirólisis experimental se utilizaron como materias primas botellas recicladas de bebidas gaseosas (PET) y residuos plásticos de aseo (HDPE), los cuales se encuentran entre los residuos más comunes en vertederos y zonas de reciclaje. Cada uno de estos residuos por separado (aproximadamente 250 g de cada uno) se lavó con abundante agua, se secó al ambiente, se trozó en piezas más o menos rectangulares de aproximadamente 2 cm x 2 cm y se caracterizó mediante análisis próximo y último. El análisis próximo (por triplicado) se realizó en un analizador termogravimétrico modelo Q500 V20.13 Build 39, de la marca TA Instruments, utilizando entre 10 y 20 mg por muestra. La humedad se determinó por pérdida de peso en atmósfera de nitrógeno, calentando la muestra a 120°C, luego la materia volátil se determinó incrementando la temperatura a razón constante de 40°C/min hasta llegar a 800°C. El carbono fijo se determinó a 800 °C y por último, el contenido de cenizas se determinó a esta misma temperatura, pero en atmósfera de oxígeno. Por su parte, el análisis último se realizó en un analizador elemental modelo TruSpec micro, de la marca LECO, siguiendo las pautas del método ASTM D-5373-08. El análisis se llevó a cabo en un ambiente de oxígeno a 1050 °C para determinar el contenido elemental de carbono, hidrógeno y nitrógeno. Luego se hizo la cuantificación del contenido de oxígeno a 1250 °C y finalmente el contenido de azufre se determinó a 1350 °C. En todos los casos se usó helio como gas de arrastre. En este caso, la cantidad de muestra fue entre 1 y 2 mg.
El poder calorífico superior (PCS) de los plásticos se calculó a partir de la correlación derivada por Channiwala y Parikh [23]. Para ello se usaron los resultados de los análisis próximo y último de acuerdo con (1), donde el PCS se encuentra en Mj/kg y C, H, O, N, S y Ceniza hacen referencia al porcentaje másico del carbono, hidrógeno, oxígeno, nitrógeno y cenizas (respectivamente) en base seca.
Reactor de pirólisis
La experimentación se realizó en un equipo artesanal (de fabricación "casera") cuyo esquema se representa en la figura 2. Todos los materiales utilizados en su construcción (excepto la termocupla) fueron materiales reciclados.
El reactor de pirólisis (tipo batch) se construyó con una lata de acero recubierta de hojalata (lata de pintura) de 1 mm de espesor, 8,5 cm de diámetro externo y 10 cm de altura, a la cual se acopló una manguera de acero inoxidable de 2 cm de diámetro para retirar los vapores producidos en el proceso. Además, se recubrió el reactor con fibra de vidrio para aislarlo térmicamente. Como fuente de calor para el reactor se utilizó un fogón de gas natural doméstico. El sistema de pre enfriamiento consistió en un tanque de agua (aproximadamente 20 cm de longitud) que se mantuvo a temperatura ambiente (aproximadamente 23 °C) para comenzar a condensar los vapores producidos en el reactor. A la salida de este tanque la manguera de acero inoxidable se empalmó a una manguera plástica (más flexible) que se llevó al condensador. El condensador, por su parte, consistió en un balde de agua (temperatura ambiente) en el interior del cual se pasó la manguera (productos del reactor) en forma de serpentín. La salida del condensador se pasó a un recipiente de vidrio conectado por su parte superior con otros dos recipientes a través de mangueras plásticas. En el montaje de los equipos se mantuvo suficiente pendiente de caída en la línea de salida de producto desde el reactor hasta el primer recipiente de vidrio colector, de modo que se evitara acumulación de líquidos condensados a través del sistema, de este modo, en los dos primeros recipientes de vidrio se recogió el combustible líquido y a través del tercero se liberaron los gases no condensables.
Para cada tipo de plástico (PET y HDPE) se realizaron dos experimentos, fijando el tiempo de reacción (30 minutos para PET y 40 minutos para HDPE) y la cantidad de plástico (40 g en cada caso). Para la experimentación no se utilizó atmósfera inerte, pero una vez cargadas las muestras en el reactor, este se mantuvo sellado para evitar el ingreso de aire u otros oxidantes durante el proceso, garantizando así la presencia limitada de oxígeno. La temperatura se registró con ayuda de una termocupla tipo K acoplada a un multímetro. Para mantener la temperatura en un rango cercano a la temperatura de diseño, se ajustó manualmente la potencia de la fuente de acuerdo con las variaciones de temperatura registradas con ayuda de la termocupla. Para el PET las temperaturas medidas variaron entre 500 y 525 °C, y para el HDPE entre 550 y 575 °C.
Caracterización del producto líquido
La densidad del combustible líquido (p f) se determinó con (2). El volumen (V) y peso (m) de cada combustible líquido se midió con balanza analítica y probeta a temperatura ambiente (25 °C). Posteriormente se verificaron los datos con ayuda de un picnómetro de vidrio borosilicato (Blaudbrand de 50 ml).
La gravedad API se determinó acorde a la norma ASTM D 1298-12b, tomando como densidad del agua (p ag) 0,996016 g/cm3. Debido a que la temperatura de análisis es 25 °C (77°F) y normalmente se expresa el grado api a condiciones estándar (15 °C o 60 °F) se emplea un factor de corrección para obtener el grado API estándar (3).
El punto de anilina es la temperatura mínima de solubilidad entre una muestra de crudo y anilina; esta propiedad se puede determinar de acuerdo con la norma ASTM D611. Para determinar el punto de anilina se empleó igual cantidad en volumen de muestra y anilina, se calentó la mezcla en baño María y se registró la temperatura en la cual se pudo observar miscibilidad entre los compuestos o desaparición de fases, luego se enfrió hasta observar de nuevo la separación de las fases.
El índice de refracción (η) para una fracción de petróleo o derivados varía según la estructura química y el peso molecular de compuesto analizado; esta propiedad incrementa de la siguiente manera: n parafinas < η naftenos < η aromáticos. Para determinar el índice de refracción se empleó un refractómetro modelo CARL ZEISS JENA.
3. RESULTADOS Y DISCUSIÓN
Recolección y caracterización de muestras
La tabla 3 muestra los resultados de la caracterización de PET y HDPE utilizados en esta investigación. Los datos se encuentran normalizados en base seca y con cenizas para facilitar las simulaciones en Aspen plus. Al comparar con datos de la literatura (ver tabla 1) se observan similitudes en el valor de todos los parámetros evaluados, en especial con el material PET. En cuanto al HDPE, la literatura reporta muy bajos contenidos de carbono fijo (según el análisis próximo) y ausencia de oxígeno (según el análisis último), mientras que en este estudio se encontraron bajos contenidos de oxígeno y ausencia de carbono fijo, además de un mayor contenido de cenizas. Probablemente tales diferencias se originen debido a la presencia de pigmentos que pueden ser utilizados para dar color a este tipo de plásticos o eventual suciedad (biodegradable e inerte) que puede acompañar las muestras tomadas directamente de RSU. En cualquier caso, los valores reportados en la tabla 3 coinciden en orden de magnitud con valores reportados en la literatura (tabla 1).
Tabla 3 Análisis próximo (% peso) y último (% peso) de algunos plásticos comunes en los residuos sólidos municipales
Caracterización | PET | HDPE |
---|---|---|
Humedad | 0,41 | 0,01 |
Carbono fijo | 11,02 | 0,00 |
Material volátil | 88,57 | 96,87 |
Cenizas | 0,00 | 3,12 |
C | 64,00 | 82,65 |
H | 4,25 | 13,31 |
O | 31,20 | 0,36 |
N | 0,00 | 0,00 |
S | 0,55 | 0,56 |
PCS (MJ/kg) | 24,18 | 44,49 |
Fuente: autores.
Validación de los modelos
Comparación entre datos simulados y valores reportados en la literatura
En la figura 3 se muestran comparativamente los resultados de las simulaciones en cuanto al rendimiento hacia productos líquidos y gaseosos (% peso) utilizando el modelo termodinámico, el modelo cinético y datos reportados en la literatura (obtenidos bajo las mismas condiciones simuladas) para las diferentes materias primas (PP, PS, HDPE y LDPE). En todos los casos la fracción de productos sólidos resultó ≤ 2 %, por lo tanto no se incluyen en el gráfico para no afectar la escala comparativa en la capacidad predictiva de los modelos con relación a la obtención de las fases líquida y gaseosa. En la figura 3 se observa que el modelo cinético resulta más acertado que el modelo termodinámico para predecir la formación de combustibles líquidos y productos gaseosos (por comparación con datos de la literatura) independiente de la materia prima utilizada. El porcentaje de error entre los datos predichos por el modelo cinético y los datos de la literatura son ≤ 2 %, excepto para la formación de productos líquidos utilizando PS como materia prima (figura 3b), donde el error es cercano al 8 %.
En general, el modelo cinético predice acertadamente la cantidad de combustibles líquidos y gases que se generan en el proceso. Por el contrario, para el modelo termodinámico los errores entre los datos simulados y reportados en la literatura son notables en todos los casos. Vale la pena recordar que con el modelo termodinámico se asume que todas las reacciones involucradas alcanzan el equilibrio y no se considera la cinética de las mismas. Allí podría radicar la principal causa de las diferencias observadas en los resultados obtenidos con los dos modelos. El modelo termodinámico para la simulación de la pirólisis de PE y PS sobreestima la producción de líquidos y subestima la producción de gases, mientras que con HDPE y LPDE subestima la producción de gases y sobreestima la producción de líquidos. Con este modelo, para algunas simulaciones las diferencias entre los datos simulados por el software y los valores esperados según la literatura llegan a exceder el 20 %. Por tal razón, la posterior comparación entre propiedades estimadas por el software para los combustibles líquidos obtenidos y datos de la literatura se hace con relación a los datos obtenidos a partir del modelo cinético. De acuerdo con la figura 3, tanto con los datos simulados como con los consultados en la literatura se espera que la producción de combustibles líquidos (bajo las condiciones dadas) sea superior en el siguiente orden para las materias primas evaluadas: PS > HDPE ≈ LPDE > PET.
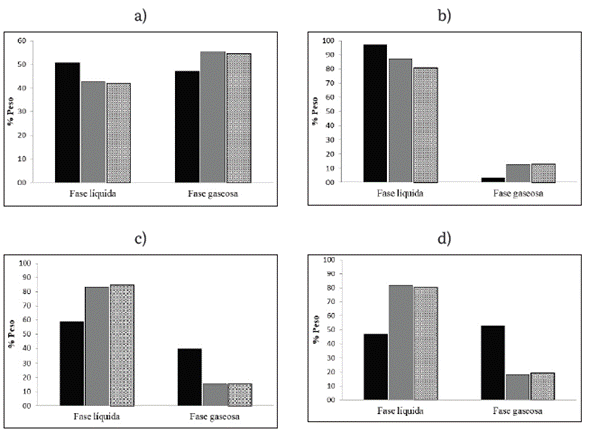
Fuente: autores.
Figura 3 Rendimiento hacia productos líquidos y gaseosos para distintos tipos de plástico
a) PP, b) PS, c) HDPE, d) LDPE; (■) modelo termodinámico, (□) modelo cinético, (◙) literatura.
Tabla 4 Propiedades del combustible líquido producido por pirólisis de residuos plásticos
Materia prima | Valores referencia | |||||||||
---|---|---|---|---|---|---|---|---|---|---|
PP | PS | HDPE | LDPE | Gasolina | Diésel | |||||
L | S | L | S | L | S | L | S | |||
PCS (Mj/Kg) | 40,8 | 44,0 | 43,0 | 44,0 | 40,5 | 38,5 | 39,5 | 44,6 | 42,5 | 43,0 |
Octanaje mínimo (MON) | 87,6 | 82,0 | - | 101,5 | 85,3 | 82,2 | - | 107,9 | 81-90 | -- |
Octanaje mínimo (ron) | 97,8 | 102,0 | 98,0 | 114,9 | 95,3 | 102,6 | - | 118,0 | 90-100 | -- |
Índice antidetonante | 92,7 | 92,0 | - | 108,2 | 90,3 | 92,4 | - | 113,0 | 81,0 | -- |
Densidad @15°C (g/cm.3) | 0,86 | 0,98 | 0,85 | 0,87 | 0,89 | 0,82 | 0,78 | 0,93 | 0,76 | 0,83 |
L: dato de la literatura [2], S: valor obtenido por simulación, -: dato no disponible.
Fuente: autores.
En la tabla 4 se presentan algunas propiedades estimadas con el software Aspen plus para los combustibles líquidos obtenidos mediante la simulación de la pirólisis de diferentes plásticos utilizando el modelo cinético y datos de la literatura [2]. Los valores obtenidos mediante simulación (y los tomados de la literatura) se comparan con valores de referencia (Resolución 898/95) para la gasolina y el diésel convencional en Colombia. Se observa, por comparación de las propiedades estimadas con el software y reportadas en la literatura, que las diferencias son < 20 %, independiente de la propiedad o la materia prima. Se resalta que los datos simulados para la densidad de los combustibles sintéticos son más cercanos a la densidad del diésel que a la densidad de la gasolina. En cuanto al PCS, la diferencia entre valores estimados con el modelo y reportados es < 10 % para el PP, PS y HDPE, y < 17% para el LDPE, en todos los casos con valores similares a los valores de referencia para gasolina y diésel; es decir, se puede esperar que los combustibles líquidos obtenidos a partir de la pirólisis de estos plásticos permitan generar cantidades de energía comparables con combustibles convencionales. Para los índices de octanaje de motor (MOR), octanaje investigado (RON) e índice antidetonante, las diferencias entre valores simulados y reportados son < 10 %, aunque difieren (~ 20 %) al compararse con el valor de referencia para la gasolina. De acuerdo con las simulaciones, la distribución de productos en fase líquida y en fase gaseosa puede ser diferente dependiendo de la materia prima utilizada. En la tabla 5 se muestra la distribución de los productos mayoritarios (% peso) en cada fase estimada en el software.
Tabla 5 Distribución de principales productos de acuerdo a las simulaciones
PP | PS | HDPE | LDPE | ||||
---|---|---|---|---|---|---|---|
Compuesto | peso | Compuesto | % peso | Compuesto | % | Compuesto | peso |
Difenil | 11,0 | Tolueno | 20,1 | Tolueno | 21,3 | Tolueno | 18,2 |
Metilnaftaleno | 8,9 | Etilbenceno | 15,7 | Xileno | 15,0 | Xileno | 12,8 |
Fenantreno | 8,3 | Estireno | 13,8 | Tetradecano | 11,7 | Metilnaftaleno | 10,6 |
Etilbenceno | 4,6 | Metilnaftaleno | 10,4 | Pentadecano | 6,1 | Etilnaftaleno | 9,0 |
Xileno | 4,3 | Metilestireno | 7,7 | Hexadecano | 5,4 | Dimetilnaftaleno | 7,9 |
Metiletilbenceno | 1,7 | Propilbenceno | 6,5 | Benceno | 4,1 | Fluoreno | 4,7 |
Propilbenceno | 1,2 | Benceno | 6,4 | Noneno | 3,5 | Indeno | 4,0 |
Benceno | 1,2 | Cumeno | 6,4 | Undecano | 2,8 | Benceno | 3,5 |
Otros * | 58,8 | Otros* | 13,0 | Otros* | 30,1 | Otros* | 29,2 |
Metano | 20,5 | Eteno | 7,2 | Metano | 4,9 | H2 | 7,7 |
Eteno | 17,5 | Propeno | 2,0 | Eteno | 4,2 | Metano | 4,0 |
Propeno | 4,9 | Etano | 1,7 | H2 | 2,2 | Eteno | 3,4 |
Etano | 4,1 | Propano | 1,3 | Propeno | 1,2 | Propeno | 0,9 |
Otros** | 52,9 | Otros** | 87,7 | Otros** | 87,4 | Otros** | 84,0 |
*En fase líquida, incluyen ácido benzoico, benzofenona, ácido fenilbenzoico, difenilmetano, butanona, propanona y ácido acetilbenzoico, acenafteno, acenaftileno y dimetilbenceno, entre otros; ** en fase gaseosa incluyen, etileno, propano, monóxido de carbono y dióxido de carbono, entre otros
Fuente: autores.
Comparación entre datos simulados y experimentales
Si bien en el equipo de pirólisis utilizado, su diseño y las condiciones de operación distan de un equipo de pirólisis óptimo para llevar a cabo el proceso, para el propósito de esta investigación proporcionan información suficiente que permite comparar los datos experimentales extraídos del equipo con los datos simulados en el modelo propuesto al utilizar condiciones de operación similares a las experimentales.
En la tabla 6 se presenta la distribución de productos sólidos, líquidos y gaseosos que se obtuvo experimentalmente (valores promedio) en la pirólisis de PET y HDPE utilizando el equipo artesanal (figura 2) y se comparan con los valores predichos por el modelo cinético utilizando las mismas condiciones experimentales (500 °C, 1 atm, 30 min para PET y 550 °C, 1 atm, 40 min para HDPE). Al igual que en los datos reportados en la figura 3, se observa que el modelo cinético reproduce con gran precisión los datos experimentales, con errores ≤ 5 %. Igualmente, se observa que el rendimiento hacia productos líquidos (a las condiciones dadas) se favorece con el HDPE, mientras que con el PET se favorece la obtención de productos gaseosos. La ausencia de productos sólidos con el PET indica la descomposición completa del material (eliminación total del desecho plástico utilizado como materia prima), mientras que el HDPE genera una cantidad de sólidos cercana al 3 %, debido a que este material contiene compuestos inorgánicos (pigmentos empleados para dar color al material) que bajo las condiciones de operación se mantienen como cenizas.
La caracterización del combustible líquido obtenido a partir del PET y HDPE mediante la evaluación de propiedades como densidad, gravedad API, punto de anilina e índice de refracción, así como la comparación con los valores para las mismas propiedades estimadas con ayuda del software, también se incluyen en la tabla 5. En general los valores experimentales y los datos simulados presentan desviaciones ≤ 5 %, lo cual reafirma que el modelo cinético representa de manera adecuada el proceso de pirólisis de los materiales estudiados.
Los valores experimentales promedio de gravedad API muestran que para el combustible líquido obtenido a partir del PET dicho valor coincide con el de crudos medianos (22 < API < 29,9) y para el combustible líquido del HDPE con el valor de crudos ligeros (30 < API < 50). Los valores experimentales para el punto de anilina indican que el producto líquido derivado del pet debe contener mayor cantidad de compuestos aromáticos, mientras que el combustible líquido obtenido a partir del HDPE probablemente contendrá mayor proporción de hidrocarburos paranínficos. Los resultados de las simulaciones en cuanto a la composición de las corrientes (no incluidos en este reporte) muestran que los productos líquidos para el PET presentan efectivamente mayor porcentaje de carbonos aromáticos (25,9 % peso) y nafténicos (50,8 % peso), mientras que el producto líquido del HDPE presenta un alto contenido de parafínicos (60,6 % peso).
De acuerdo con las simulaciones, los principales componentes de los productos líquidos al utilizar PET como materia prima incluyen antraceno, ácido benzoico, benzofenona, bifenilo, ácido fenilbenzoico, difenilmetano, butanona, propanona y ácido acetilbenzoico; mientras que al simular la pirolisis de HDPE los principales productos obtenidos en la fase líquida incluyen acenafteno, acenaftileno, benceno, dimetilbenceno, dimetilnaftaleno, etilnaftaleno y metilnaftaleno. Por su parte, la fase gaseosa (simulada) contiene principalmente metano, etano, etileno, propano, hidrógeno, monóxido de carbono y dióxido de carbono, independiente de la materia prima utilizada en la simulación.
Tabla 6 Propiedades del combustible líquido producido
Distribución de productos | Material | |||
---|---|---|---|---|
PET | HDPE | |||
S | E | S | ||
Líquidos | 37,9 ± 2,3 | 36,0 | 83,9 ±2,7 | 84,5 |
Gases | 62,1 ± 2,3 | 64,0 | 13,0 ± 2,5 | 12,4 |
Sólidos | 0,0 ± 0,0 | 0,0 | 3,1 ± 0,1 | 3,1 |
Caracterización | ||||
Densidad (g/cm3) | 0,91 ± 0,02 | 0,87 | 0,82 ± 0,01 | 0,79 |
Gravedad API (60 °F) | 28,26 ± 2,76 | 31,14 | 48,54 ± 1,56 | 47,62 |
Punto de anilina (°C) | 34,5 ± 0,7 | 27,0 | 61,0 ± 0,1 | 63,02 |
Índice de refracción (%) | 1,50 ± 0,00 | 1,45 | 1,45 ± 0,07 | 1,44 |
Nota: E: valor experimental, S: valor simulado.
Fuente: autores.
CONCLUSIONES
La disminución del volumen de residuos plásticos y su valorización a través de su transformación a combustibles líquidos mediante procesos de pirólisis es técnicamente factible y las propiedades (como el PCS) de los combustibles obtenidos son comparables con las de combustibles convencionales como gasolina o diésel. Para el estudio y eventual optimización del proceso, es posible implementar modelos en software comercial como Aspen plus, que pueden llegar a predecir acertadamente la cantidad y calidad de los combustibles líquidos producidos. En este aspecto, de esta investigación se concluye que los modelos de base cinética resultan más acertados que los modelos que se fundamentan en el equilibrio termodinámico para simular la pirólisis de los materiales seleccionados. De acuerdo con los resultados de las simulaciones, materiales como HDPE favorecen la formación de combustibles líquidos, mientras que materiales como PET favorecen la formación de productos gaseosos. Con los modelos propuestos resulta relativamente sencillo evaluar y estudiar las condiciones operacionales y/o la naturaleza de las materias primas que permitan optimizar la obtención de alguno de ellos; por lo tanto, los modelos propuestos representan una herramienta computacional adecuada y útil para estudiar la valoración de residuos plásticos mediante su transformación termoquímica hacia determinado producto de interés.