INTRODUCTION
Spent Ni-Cd batteries have been recycled using pyrometallurgy for decades, for example, by processes such as Snam-Savam [1], Sab-Nife [2], Accurec [3] and Inmetco [4]. In pyrometallurgy, cadmium is volatilized and recovered by condensation, and used for new batteries, whereas nickel is applied in steel production [5], [6]. Nevertheless, steel producers cannot incorporate Ni-Cd batteries into the molten steel in large amounts [7]. All the above-mentioned processes are associated with fume emissions that require compliance with strict standards related to flue gas filtration systems [6]. There are also hydrometallurgical plants for recycling Ni-Cd batteries such as Batenus and Batmix [11,14]. These processes avoid emissions of contaminating gases into the atmosphere and save energy, compared to pyrometallurgy [6]. However, the use of concentrated sulfuric acid as a leaching agent and the recovery of metals from the pregnant liquor (Ni, Cd, Cu, Hg, Zn, Fe) by selective ion exchange [8] generates contaminated aqueous effluents implies high processing costs [9]. On the other hand, some promising biohydrometallurgical processes for treating spent Ni-Cd batteries have been devised, but their implementation has been discouraged because of its long reaction time [10], [11]. Unlike mineral acids, used in traditional leaching procedures, organic acids are safe and biodegradable chemical agents. Organic acids also have the attractive feature of showing metal complexing properties, which makes them valuable for selective leaching operations [12]. So, it is important to focus research efforts on the technological development of more sustainable reclamation procedures for the cadmium and the nickel contained in spent Ni-Cd batteries by applying organic acids as leaching agents.
Considering these ideas, this work aimed to propose a novel hydrometallurgical processing route, based on the application of diluted organic acids (citric and acetic) as Cd-selective leaching agents, for the treatment of spent Ni-Cd batteries. The treatment of the leaching liquors (crystallization, precipitation) produced organic salts containing Ni and Cd that were physiochemically characterized. Also, we proposed a conceptual process flow diagram for the battery recycling operation. Finally, from a circular economy standpoint, we discussed the possible application of the solid products obtained as raw materials for several industrial applications.
METHODOLOGY
Extraction of electrode active powders from spent Ni-Cd batteries
We obtained from a local waste management company 110 Ni-Cd battery cells (different brands and sizes), equivalent to 3,27 kg. The cells were discharged using a resistance circuit. Later, the cells were dismantled using hand tools to separate the anode and cathode ribbons from other materials (labels, cases, connectors, and separators). The electrode ribbons were milled separately and sieved, so a cathodic powder and an anodic powder were obtained, dried at 70 °C, and stored in closed vessels at room temperature for further use. The disassembled Ni-Cd cells averaged a cathode-to-anode powder mass ratio of 1:1. As obtained by atomic absorption spectroscopy [13], the composition of the cathode was 7±2 wt.% Cd and 52±io wt.% Ni, and the composition of the anode was 65±4 wt.% Cd and ii±2 wt.% Ni.
Leaching of the active powder materials and recovery of products
The electrode powder materials from spent Ni-Cd batteries were leached in shake flasks at room temperature (~25°C). The leaching tests were performed with 2 g of active material dried powder and 40 mL of acid leaching agent. The reaction constituents were put into 250 mL Erlenmeyer flasks and placed on an orbital shaker at a constant speed (200 rpm) for one hour. The pulp was filtered, and the solution was submitted to atomic absorption spectroscopy (AS) for Ni and Cd analysis, using a SavantAA GBC Scientific Equipment spectrometer.
The rationale of the leaching tests carried out was divided into two stages, as follows:
- Initially, the active powders (cathode and anode) were separately leached to test the performance of the leaching agents used.
- Then, a 1:1 mass ratio cathode-to-anode mixture was leached to determine selectivity, leaching time, and acid mixtures for more efficient recovery of valuable metals. Finally, a conceptual process flow diagram was developed for the recycling operation.
In the first stage, cathode and anode powders were leached, separately, in solutions containing 5 °% m/m of the following leaching agents: acetic, citric, oxalic, hydrochloric, and sulfuric acids. After this, the organic acids showing greater leaching efficiency were tested again, at the following concentrations: 10, 15 and 20 % m/m. Three replicates were performed for each experimental condition. The reported values are the average, and the error bars represent one standard deviation.
The acids and concentrations showing a better performance were tested again, on a cathode-to-anode 1:1 powder blend, to simulate the real composition of the electrode mass that could be obtained after an industrial milling operation or spent Ni-Cd batteries. The most selective leaching agents from this test were studied at different leaching times, from 5 to 360 min, to determine the reaction time. The solutions obtained from this first stage (360 min test) were submitted to a process of evaporation/crystallization at 70 °C for 24 h and the solids recovered were physical chemically characterized as described in the next section. After the selective leaching of Cd from spent Ni-Cd batteries, the second stage of leaching was carried out for 1 h, on the remaining solids, using acetic acid and sulfuric acid, both separately and blended at different proportions (see "Results and discussion" section). All experiments were triplicated, the reported values correspond to the average, and the error bars indicate one standard deviation.
Once the leaching agent for the second leaching stage was determined, NaOH was added to the second leaching solution obtained, in a ratio of 3,5 g for each 50 mL of solution (pH>12). This procedure was intended to precipitate the metal leached. The NaOH was added gradually under constant stirring at 50°C for 10 min, and then, to separate the precipitates, the solution was centrifuged at 2300 rpm for 10 min. Finally, after leaving the liquor to stand for 24 h and subsequently evaporating/crystallizing the solid in an oven at 70 °C for another 24 h, the product was submitted to several physicochemical analyses. The remaining solid from the second stage of leaching was also submitted to further analyses, as explained in the following section.
Physicochemical characterization of the solid products
As indicated above, the liquid solutions obtained from the first and second leaching stages were treated by evaporation/crystallization and NaOH precipitation, respectively. The solid products obtained in each of the stages were characterized by utilizing the following analysis techniques: scanning electron microscopy (SEM) with energy dispersive spectroscopy (EDS), atomic spectroscopy (AS), X-ray diffraction (XRD), and Fourier transform infrared spectroscopy (FTIR).
For SEM-EDS analysis, a representative sample of each product was placed on a brass holder using carbon conductive adhesive tape. The sample was sputter-coated with conductive carbon and analyzed on a JEOL scanning electron microscope model JSM-6390 (20 kV) for morphological and microchemical analysis. For elemental quantitative chemical analysis, both absorption and emission techniques were implemented using AS using a SavantAA GBC Scientific Equipment spectrophotometer. Solid product samples and remaining solids from the second leaching stage were digested in distilled water acidified with a few drops of concentrated HNO3 and a hydrochloric-nitric acid mixture heated at 80°C, respectively. After digestion, several metals were quantified under standard conditions of wavelength, slit, and flame, according to each element analyzed. For mineralogical analysis and functional group determination, the samples were oven-dried (70 °C, 24 h) and finely ground in an agate mortar. The crystalline minerals present in the samples were determined by XRD, using a PW-1840 Philips diffractometer with an incident wavelength corresponding to the copper Ka1 radiation (1,5406 Å) was used. The diffraction angle (2θ) was scanned from 10 ° to 80°. The phase identification was carried out using the ICDD (International Centre for Diffraction Data) database. Finally, for FTIR analysis the samples were mixed with KBr at a 99:1 mass ratio and their spectra were recorded using a Bruker Tensor 27 spectrometer.
RESULTS AND DISCUSSION
Leaching of active materials from spent Ni-Cd batteries
The Cd-rich anode and the Ni-rich cathode of the Ni-Cd spent batteries were separately leached in different media, using the shake flask technique, to assess the efficiency of each leaching agent used. The results are shown in Figure 1 (a). As expected, the inorganic acids (HCl, H2SO4) are the most effective when it comes to dissolving metals and this fact is coincident with previous reports [14], [15]. From Figure 1 (a), we can also observe that oxalic acid did not leach the anode and the cathode of the spent batteries, and the Cd-rich anode is more amenable to leaching than the Ni-rich cathode. Additionally, H2SO4 is the most effective leaching agent for both, the Cd-rich anode, and the Ni-rich cathode of the spent Ni-Cd batteries. This very same observation has been reported in previous works [16], [17]. Regarding the organic acids, acetic acid was more effective than citric acid for both electrode materials. The application of acetic acid as a successful leaching agent for Ni-MH spent batteries, a similar battery system, was reported in a previous paper [12].
Nonetheless, the aim of this study is to gain insights into the possible application of organic acids as leaching agents for spent Ni-Cd batteries. Despite their lower efficacy when compared to inorganic acids, experiments carried out with acetic and citric acids were kept on at higher concentrations. It can be seen in Figure 1 (b) that at concentrations higher than 5 % m/m, both acids increase their leaching capacity, particularly for cadmium. On average, acetic acid dissolves 60 % more Ni from the Ni-rich cathode than citric acid for all the concentrations tested, but the yield for leached Ni is still low (circa 20 %). In the case of the cadmium leached out from the Cd-rich anode, both acids behave similarly, showing yields of over 80 %. Since both the acids (acetic and citric) at a concentration of 15 % m/m rendered slightly better results, a selectivity test was devised. In this test, cathode and anode powder were mixed at the same mass ratio found in the batteries (1:1).
The solid mixture was subjected to leaching in shake flasks at room temperature with 15 % m/m of each acid separately, and the results are shown in Figure 1 (c). Whereas both organic acids, acetic and citric, exhibited good leaching yields for cadmium, the selectivity test showed that acetic acid leached five times more nickel than citric acid from the mixed electrode powder. These results confirm that cadmium contained in the battery powder is more amenable to leaching than nickel. A practical consequence of the results shown in Figure 1 (c) is that citric acid works as a selective leaching agent for cadmium. When nickel and cadmium are both present in the leaching system, citric acid preferentially attacks cadmium compounds, and nickel compounds are not dissolved to a great extent.
So, we performed a time-course leaching test on active materials from Ni-Cd batteries mixed in a 1:1 ratio, using citric acid in a 15 % m/m concentration, as shown in Figure 1 (d). The most advantageous leaching time found was 60 min, as highlighted in Figure 1 (d). After this time, it is possible to recover a large percentage of Cd (85 ± 5 %) and only a small amount of Ni (4 ± 1 %), confirming conditions for the selective leaching of cadmium using citric acid. Longer leaching times are not practical, since the cadmium leaching does not increase and, by contrast, the presence of nickel in the solution increases, lowering the selectivity of this first leaching step.
As shown, citric acid mainly dissolves the anode's cadmium of the spent Ni-Cd batteries. Thus, the solids remaining from the citric acid leaching (first leaching step) were filtered out and submitted to the second leaching stage, using acetic and sulfuric acid either separately or blended, using different concentrations of each acid.
These tests were performed to determine the best leaching agent to recover the nickel remaining from the first leaching stage with citric acid. As shown in Figure 2, by using a combination of 5 % m/m acetic acid and 3 % m/m sulfuric acid, the highest recovery percentage of Ni is achieved (50±3 wt.%). Besides, this combination recovered 6±2 wt.% of the remaining Cd from the first leaching stage. This combination was more efficient than acetic acid alone (5 % m/m) and sulfuric acid alone (5 and 10 % m/m), indicating a synergistic effect by combining acetic and sulfuric acid. Such behavior can be explained because, during the leaching reaction of the battery materials, the inorganic acid (sulfuric acid) provides a greater concentration of H+ ions which promotes protonic attack of the solid, whereas the organic acid (acetic acid) can continue extraction by complexing metal ions in the solution, forming soluble metal acetates [18]. Both phenomena create proper conditions for enhanced metal extraction from the solid substrate.

Source: Own elaboration.
FIGURE 1 (A) ACID LEACHING OF ACTIVE MATERIALS FROM N i-c d BATTERIES, SEPARATELY, USING BOTH ORGANIC AND INORGANIC ACIDS IN A 5 % M/M CONCENTRATION. (B) ACID LEACHING OF ACTIVE MATERIALS FROM N i-c d BATTERIES, SEPARATELY, USING ACETIC AND CITRIC ACIDS AT THE FOLLOWING CONCENTRATIONS: 10 %, 15 %, AND 20 % (M/M). (c) ACID LEACHING OF ACTIVE MATERIALS FROM N i -c d BATTERIES MIXED IN A 1:1 RATIO, USING ACETIC AND CITRIC ACIDS IN A 15 % M/M CONCENTRATION. (D) TIME-COURSE FOR THE ACID LEACHING OF ACTIVE MATERIALS FROM N i-c d BATTERIES MIXED IN A 1:1 RATIO, USING CITRIC ACID 15 % M/M.
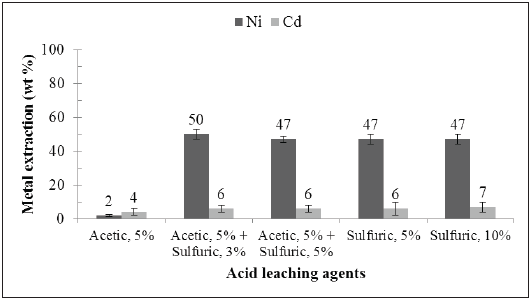
Source: Own elaboration.
FIGURE 2 CADMIUM AND NICKEL EXTRACTION IN THE SECOND STAGE OF ACID LEACHING IS PERFORMED USING THE REMAINING SOLID FROM THE FIRST LEACHING STEP (CITRIC ACID, 60 MIN). ACETIC AND SULFURIC ACIDS, BOTH SEPARATELY AND BLENDED, WERE TESTED IN SEVERAL CONCENTRATIONS (% M/M), AS INDICATED.
Physicochemical characterization of the products
As indicated previously, we treated the solutions obtained from the first and the second leaching stages of the internal materials of the Ni-Cd spent batteries to get solid products. The leachate from the first stage (citric acid 15 %, leaching for 60 min) was processed by evaporation/crystallization. The leachate from the second leaching stage (acetic acid 5 % + sulfuric acid 3 %, leaching for 60 min) was precipitated by NaOH addition. As a first approximation, the characterization of these solid products (crystals) was carried out by SEM-EDS analysis. The secondary electrons SEM images of products obtained at the end of the two leaching stages of the active material from spent Ni-Cd batteries, as well as that one of the remaining solids, filtered out from the second leaching stage, are shown in Figure 3. The percentage by weight of each element detected over the area of these images, obtained by a semi-quantitative chemical microanalysis using EDS, is also shown in Table 1.
Both the leaching products and the remaining solid from the second leaching stage have a heterogeneous morphology established by particles with an average diameter ranging from a few microns to 500 μm, and even a little more in the case of the product and the remaining solid from the second leaching stage. In the case of the solid product from the solution of the first leaching stage, the particles tend to form agglomerates. Besides, the particles constituting the product crystallized from the solution of the second leaching stage show massive grains. Finally, the remaining solids from the second leaching stage, i. e. the material not solubilized, show a porous morphology and the presence of metal structures resembling the typical nickel foam cathode mesh of the original battery [19].
Because having used organic acids as leaching agents, C and O are found in the solids recovered from the leaching solutions in both stages. The solids from the first leaching stage contained Cd and no Ni, which confirms the selectivity of the leaching process. Besides, the solids from the second leaching stage are more complex but exhibit the presence of Ni and some residual Cd. In this solid, the detection of S is due to the use of sulfuric acid in the second leaching stage, whereas Co is usually present at the cathode of Ni-Cd batteries, as some other authors have reported [12], [20]; and Al is probably an impurity in the electrodes of these batteries. It must be highlighted that the solids from the second leaching stage contained Na, due to the NaOH excess used for the precipitation of this product. In addition, both the solids obtained from the first and second leaching stage contained K. The presence of K in the solid products obtained from the leachates can be explained by the fact that potassium hydroxide (KOH) is the electrolyte in the Ni-Cd battery system [1], [4].
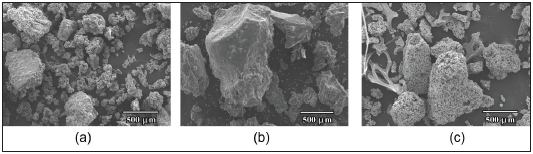
Source: Own elaboration.
FIGURE 3 SECONDARY ELECTRONS SEM IMAGES OF THE SOLID PRODUCTS CRYSTALLIZED FROM THE SOLUTIONS OBTAINED IN THE FIRST (A) AND SECOND (B) LEACHING STAGES AND THE REMAINING SOLID FROM THE SECOND LEACHING STAGE (C).
TABLE 1 SEMI-QUANTITATIVE CHEMICAL MICROANALYSIS (EDS) OF THE ENTIRE AREA OF SEM IMAGES IN FIGURES 3A, 3B AND 3c
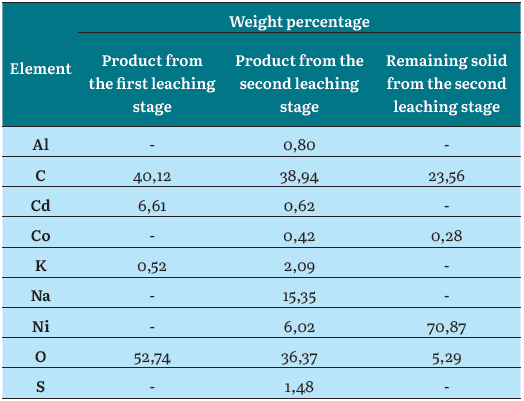
Source: Own elaboration.
Unlike the solid products derived from the leachates, the solid remaining from the second leaching stage had Ni as a major element, followed by a considerable weight percentage of C. It contained O and traces of Co. The C and O can be attributed either to the presence of the remaining leaching agent or by some carbon that is added to the electrodes of the battery to increase the electrical conductivity [21]. In any case, some of the carbon detected by the EDS analysis in these samples can be an artifact caused by the coating used for the sample preparation [22]. These findings are concomitant with the fact that the remaining solids are composed of some of the Ni-metal mesh and carbon particles that compose the electrodes of the spent batteries, as can be seen in Figure 3 (c). Anyways, the EDS microchemical analysis must be taken cautiously, because of its semi-quantitative nature. Table 2 shows the quantitative chemical analysis by AS made to the solids from both leaching stages and the remaining solid. The solid product of the first leaching stage successfully concentrated the cadmium present in the battery since its Cd content was 15 wt.%. Besides, Ni was found as an impurity in the product with a concentration of 3,2 wt.%, which is well correlated to the results shown in Figure 1 (d) for the 60 min first-stage leaching experiment. Other minor metals, such as Co, Fe, Mn, and Na were detected in the product of the first leaching stage.
TABLE 2 CHEMICAL ANALYSIS OF METALS IN THE PRODUCTS AND REMAINING SOLID FROM BOTH LEACHING STAGES
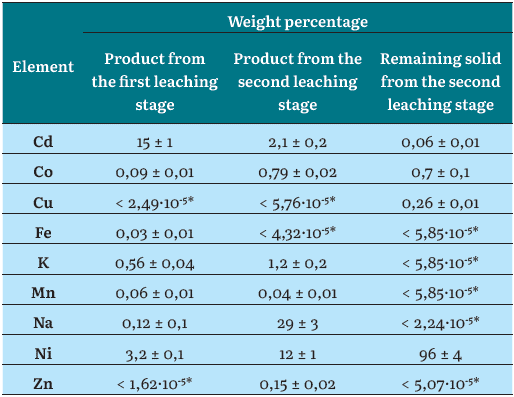
* Detection limit,
Source: Own elaboration.
From the second leaching stage, Na was the dominant metal in the product, followed by Ni, representing 36 and 12 wt.% of the product, respectively. Likewise, some impurities containing Cd, Co, K, Mn, and Zn were found, but only Cd and potassium are present in a considerable weight percentage, 2,1 and 1,2 wt.%, respectively.
Finally, the remaining solid from the second leaching stage showed a nickel content of 96 wt.%, a value that turns this insoluble fraction into an exploitable high-value metal product, for example, as an alloying element in metallurgical processes. This material also showed small amounts of Cd, Co and Cu.
In Figure 4, we showed the crystalline phases identified in the products from the first and second leaching stages. In the product from the first leaching stage (Figure 4a), we identified citric acid hydrate (C6H8O7-H2O), ICDD 00-015-0985; cadmium oxalate hydrate (CdC2O4'3H2O), ICDD 00-053-0085; and metallic cadmium, ICDD 00-005-0674. Besides, in the second stage of a solid product (Figure 4b), the nature of the nickel phases is due to the leaching agents used as well as the precipitating agent used. The following species were identified: sodium hydroxide (NaOH), ICDD 00-027-0711; nickel oxide hydroxide (NiOOH), ICDD 00-027-0956; nickel hydroxide hydrate, (Ni(OH)2-0,75H2O), ICDD 00038-0715; nickel acetate hydrate (C4H6NiO4-4H2O), ICDD 00-049-1173; and nickel sulfate (NiSO4), ICDD 01-072-1195. It must be pointed out that the diffraction pattern recorded in Figure 4b shows some background displacement, due to fluorescence [24], as it has been reported previously for nickel hydroxide samples [25].
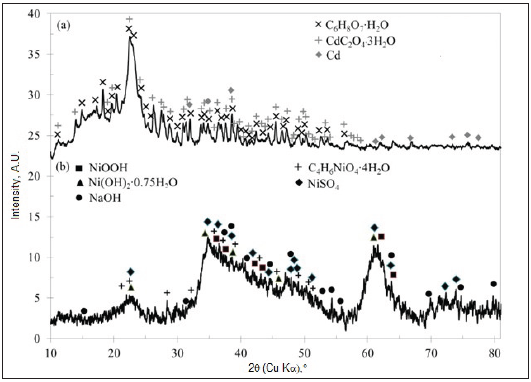
Source: Own elaboration.
FIGURE 4 XRD DIFFRACTOGRAMS FOR CRYSTALLINE PHASE IDENTIFICATION IN THE PRODUCTS OBTAINED BY LEACHING THE ACTIVE MATERIALS FROM SPENT N i c d BATTERIES. (A) PRODUCT FROM THE FIRST LEACHING STAGE. (B) PRODUCT FROM THE SECOND LEACHING STAGE.
Nonetheless, the presence of a cadmium citrate hydrate (Cd3(C6H5O7)2.2H2O) in the solid product obtained in the first stage of leaching, cannot be ruled out, due to their similarities with citrate salts synthesized by other researchers [23], [26]. To obtain a deeper understanding of this feature, the FTIR spectrum of the solid product obtained from the first leaching stage is shown in Figure 5a. The broad band at 3444 cm-1 corresponds to HOH stretching of the water present in the crystal lattice [27], [28]; the bands at 2993, 2742, and 2619 cm-1 are related to organic salts which possess -COOH where there are electrostatic interactions due to the complexity of its structure [29], as well as the band at 1905 cm-1, correspond to CO molecular vibrations of complex salts [27]; the bands at 1620, 1396, and 1338 cm-1 are the main COO molecular stretches of salts from carboxylic acids [26], [27], [30], [31]. Those at 1223 and 1134 cm-1 are CO stretches [27], while the bands at 1076, 791, and 594 cm-1 are molecular vibrations of rocking, wagging, and scissoring, respectively, typical of carboxylic acid salts [26], [29], [29]. The bands at 895, 513, and 467 cm-1 are MO molecular vibrations, being M a metallic element. Apart from cadmium citrate and oxalate, which are complex salts formed in the presence of citric acid [32], in the product some unreacted citric acid could be present, as evidenced by the bands located at 1736 and 930 cm-1 [27], [28]. These results confirm the phases found by XRD. Finally, metallic cadmium identified by XRD could be a consequence that citric acid and its salts may act as reducing agents [32].
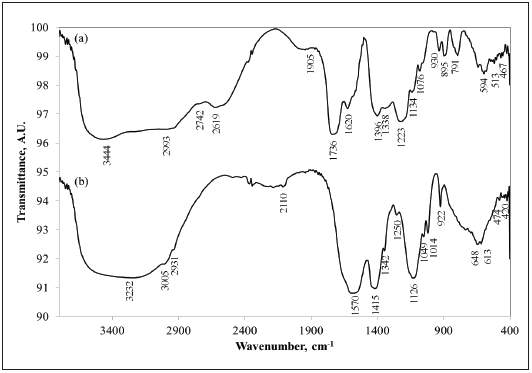
Source: Own elaboration.
FIGURE 5 FTIR SPECTRA OF PRODUCTS OBTAINED BY LEACHING OF ACTIVE MATERIALS FROM SPENT N i c d BATTERIES. (A) SOLID PRODUCT FROM THE FIRST LEACHING STAGE. (B) SOLID PRODUCT FROM THE SECOND LEACHING STAGE.
On the other hand, the FTIR spectrum of the product from the second leaching stage verifies the presence of the NiSO4 and nickel acetate hydrate phases identified using XRD. In the case of nickel acetate, the broadband at 3232 cm-1 corresponds to HOH stretching of the water present in the crystal lattice [27], [28]; the bands at 1570, 1415, and 1250 cm-1 are the main molecular COO stretches of acetates, whereas those at 648 and 613 cm-1 are CO deformations; the bands at 3005, 2931, 1342, 1049 and 1014 cm-1 are related to CH3 stretching and deformation and those at 922 and 474 cm-1 are CC stretching and CCO deformation, respectively; and the band at 420 cm-1 is an MCO bending [27], [29]. Concerning nickel sulfate, the bands around 2110 cm-1 correspond to SO4 - [29], and that one at 1126 cm-1 represents the SO4 - main stretch [27]; the bands at 648 and 613 cm-1 may also represent SO4 - out of plane deformations [27], [29]. However, no specific bands related to nickel and sodium hydroxides, nor the nickel hydroxide oxide were assigned because the characteristic bands of this kind of compounds may have been either overlapped by the band corresponding to crystal lattice water or located at wavenumbers smaller than 400 cm-1, which are typical of these compounds [33].
Conceptual process flow diagram for the hydrometallurgical processing of spent Ni-Cd batteries using organic acids
Based on the results shown above, a conceptual route for the hydrometallurgical processing for spent Ni-Cd batteries using organic acids can be devised, focused on two stages of selective leaching. The first stage of selective leaching for Cd would use 15 % m/m citric acid as a leaching agent, and a second stage for the selective leaching of Ni would use a mixture of 5 % m/m acetic acid and 3 % m/m sulfuric acid as leaching agent. All products obtained through this processing route, shown in bold in Figure 6, can be used as starting materials either to prepare chemical commodities or to produce metallic Cd and Ni coatings by electrolytic processes [34], [35]. Additionally, due to their composition, these products could be used directly as dye mordants in textiles [36] and as ceramic pigments [37].
CONCLUSION
Under the experimental conditions evaluated in this work, we can conclude:
- Compared to citric and acetic acids, the leaching yield of sulfuric acid was higher for nickel and cadmium; however, the selectivity exhibited by sulfuric acid was low.
- Acetic and citric acids showed promising leaching yields for cadmium.
- The selectivity test showed that acetic acid leached 5 times more nickel than citric acid from the mixed electrode powder.
- The time-course for the acid leaching of active materials from Ni-Cd batteries mixed in a 1:1 ratio, using citric acid 15 % m/m showed that proper leaching yields can be attained after 60 min of leaching.
- Up to 50±3 wt.% of Ni was recovered in the first leaching stage employing a combination of 5 % m/m acetic acid and 3 % m/m sulfuric acid. This combination was more efficient than acetic acid alone (5 % m/m) and sulfuric acid alone (5 and 10 % m/m), indicating a synergistic effect by combining acetic and sulfuric acid.
- By compiling all the results, a conceptual process flow diagram was devised to recycle Ni and Cd from spent batteries in the form of valuable materials for industrial applications.