Serviços Personalizados
Journal
Artigo
Indicadores
-
Citado por SciELO
-
Acessos
Links relacionados
-
Citado por Google
-
Similares em SciELO
-
Similares em Google
Compartilhar
CT&F - Ciencia, Tecnología y Futuro
versão impressa ISSN 0122-5383versão On-line ISSN 2382-4581
C.T.F Cienc. Tecnol. Futuro v.2 n.2 Bucaramanga jan./dez. 2001
ABSTRACT
The effect of the ICP contactor and the mixture valve on the desalting process was evaluated as a contact system in the crude oil washing process. The evaluation was carried out in the two desalters at the Cartagena Refinery (GRC) and a desalter at the Barrancabermeja Refinery (GCB) of ECOPETROL. The pressure drop was measured and the efficiency of the desalting processes, dehydration and hydrocarbon crude intake in the water was calculated based on the BS&W measurement, salt content and hydrocarbon concentration in the water. Results showed that the contactor improved desalting, water in the crude oil was reduced and crude carry-over in the wastewater was reduced between 50 and 92% at the Barrancabermeja Refinery, and between 40 and 95% at the Cartagena Refinery, which mean savings of approximately US$ 373.000 dollars per year at both refineries, due to the fact that less water is loaded into the process. Furthermore, hydrocarbon loss in wastewater was reduced by about 3650 barrels per year. The pressure drop was reduced between 88 and 94 % in relation to the mixing valve.
Keywords: crude desalting, in line contactor, oily wastewaters.
RESUMEN
Se evalúo el efecto que tiene en el desalado el uso del contactor ICP y la válvula de mezcla como sistema de contacto en el proceso de lavado del crudo. Para la evaluación se trabajó en dos desaladores de la refinería de Cartagena y en uno de la refinería de Barrancabermeja de ECOPETROL. Se midió la caída de presión y se calculó la eficiencia de los procesos de desalado, deshidratación y arrastre de hidrocarburo tomando como base la medida del BS&W, el contenido de sal y la concentración de hidrocarburo en el agua. Los resultados mostraron que con el contactor hubo una mejora en el desalado, se redujo el contenido de agua en el crudo y se redujo el arrastre de hidrocarburo en el agua residual, entre un 50 y 92 % en la refinería de Barrancabermeja y entre un 40 y 95 % en la refinería de Cartagena, lo que significó un ahorro aproximado de US$ 373.000 dólares anuales en las dos refinerías debido a que se carga menos agua al proceso. Además se redujo la pérdida de hidrocarburo en el agua de lavado en cerca de 3650 barriles por año. La caída de presión se redujo entre un 88 y 94 % con respecto a la válvula de mezcla.
Palabras clave: desalación del crudo, en contactor de línea, aguas residuales.
INTRODUCTION
For most continuous processes where inmiscible liquid streams are put in contact, it is necessary to apply in-line mixing strategies, under conditions of laminar or turbulent flow. Within the technological development of contact systems for in-line mixing, there are different techniques that use conventional devices such as mix valve, orifice plates, and scattering flutes, which are subject to numerous operational limitations. These mixing systems are not very efficient from the viewpoint of mass transfer and subsequent separation. On the contrary, they are good to promote the generation of strong emulsions and carry-over of one product in another (Lang and Dritina, 1995).
It is often that applications using dynamic mixers are found to stir the products stored in tanks in order to eliminate variations in fluid quality due to inventories with different characteristics. In these cases, energy consumption and operations costs are high and control over the distribution of residence time is not adequate (Yang and Odedra, 1997).
Mixing by natural turbulence in pipelines without internal devices is not efficient. Stretches of piping from 100 to 200 times their diameter are required to obtain a good dispersion, when there is not much difference in viscosities between the fluids in contact. This is not very practical in most processes, which is why in-line static contactors or mixers are used to obtain efficient mixing in short distances (low residence time) and minimum energy losses (Lang and Dritina, 1995).
The application of static contact systems to guarantee close contact between immiscible streams is to produce a large interfacial area to optimize mass transfer. It should be kept in mind that mass transfer in inmiscible liquids is a clear example of the processes where the selection of application strategy is carried out in a practically empirical manner (considering the criteria of experience of the designer and the specific knowledge of the field where the system is applied). This situation is due to a great variety of processes and a great amount of theoretically applicable mixing tools (Koiranen et al., 1994).
As part of the technologies developed by the Instituto Colombiano del Petróleo (ICP) to optimize industrial processes "at the source", the application of new contact or mixing systems is included. These systems have been setup to generate stable flow patterns producing scattering with even-sized particles, preventing the formation of emulsions and promoting rapid separation, thus improving the quality of feed and products in treatments where complementary streams are involved, such as water, steam, additives, solvents and catalysts, among others. The use of in-line Mixers for continuous mixing operations simplifies system operation with low costs for infrastructure and maintenance (Forero et al, 2000).
Design and operation of static contactors
For applications in liquid-liquid contact processes in refining and petrochemical systems, where it is important to ensure close contact between different fluids and to facilitate the rapid separation of phases without carry-over of one product in another, new in-line contact systems have been designed, evaluated and developed at an industrial scale with high efficiency in mass transfer. Due to their configuration, they generate stable flow patterns, preventing the formation of emulsions and promoting rapid separation (Forero et al, 2000).
A static contactor can be defined as a series of rigid modules, organized as divergent flow elements that are installed in a current inside pipelines or ducts. The operation of static mixers in continuous processes allows mass transfer and homogenization to take place without using moving parts.
By continuously dividing and recombining fluids, the mixer produces changes in rate profiles and gradually reduces the differences in the properties presented by the fluids that are put in contact (Pressdee, 1992).
Some analyses indicate that in order to obtain good results in mixing behavior (Figure 1), an in-line contactor must be composed of several modules. It is generally recommended to use between three and nine (Faroui et al, 1998). If the evaluation of the contactor is focused on mass transfer behavior, location and shape of injection point of the scattered phase have a great influence on the distribution of particle size generated at the outlet (Figure 2) (Berkman and Calabrese, 1988).
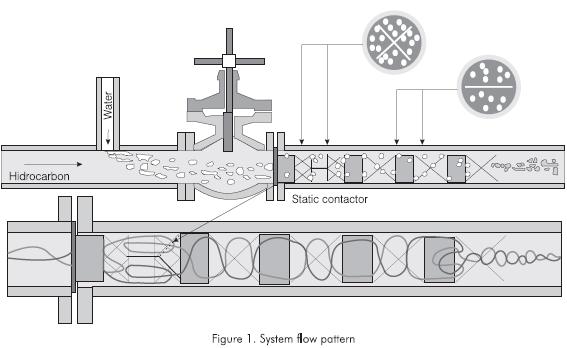
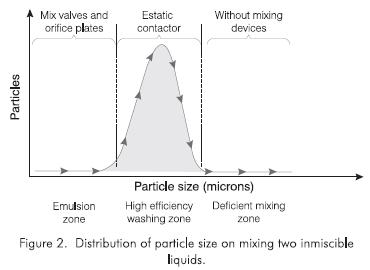
Detailed analyses show that a considerable part of the mixing takes place downstream from the static contactor. The series of modules that make up the equipment generate even flow patterns, which are responsible for the mixing process and maximizing mass transfer (Bourne et al, 1992).
In the application of a contact system on a specific process, there are important aspects of design, such as characteristics of the fluids to be mixed, available contact time, flow regime, and the pattern of mixing and scattering that is generated. Other aspects to be considered, that are less important in design but significant in application, are ensuring non-blockage, ease of maintenance, installation costs, useful life and the pressure available in the process to satisfy low energy consumption required by the contact system (Scheider, 1983)
Fundamentals of mass transfer in the desalting process
In desalting systems, before sending a stream of crude oil to the distillation process, it is put in contact with water by means of a mixing system that promotes close contact between the phases in order to remove salts, metals and solids in the crude.
In accordance with normal operating conditions in these processes of liquid-liquid contact, it is estimated that 10 to 20 minutes are enough time for separating phases. Less time would indicate that the superficial contact area was too low and therefore, the efficiency of the mass transfer would limit the process. In the case of separation times that are higher than the range indicated, the cost of the separating drums would begin to increase, limiting the process economically (Forero et al., 2000).
Effect of water carried-over in the crude oil on distillation units
Water carry-over in hydrocarbon increases operating costs. During the process, the carried-over water is heated from a temperature of 25 OK (121°C) at the outlet of the desalterupto atemperature of 680K (360°C) at the inlet of the atmospheric tower. This heating represents energy consumption of 1100 BTU (2558.6 kJ/kg) per pound of water, which generates additional costs for heating. In addition, the water will occupy six to nine times the volume occupied by the same amount of crude oil.
Ensuring proper removal of salts, metals and solids from the crude oil will depend mainly on a good contact system in washing the crude oil, which ensures close contact between the phases, facilitates the separation of the aqueous phase, and increases charge capacity.
The objective of this study is to compare the effect of a mixing valve and a static contactor as contact systems in hydrocarbon desalting process.
AREA OF STUDY
Work was carried out at the crude oil plant of the Cartagena Refinery and at the 250 crude oil unit of at the Barrancabermeja Refinery of the Empresa Colombiana de Petróleos (ECOPETROL).
EXPERIMENTAL DEVELOPMENT
This project was carried out in two stages. The experimental stage was performed at the laboratory and pilot plant scale at the ICP The second stage of application and evaluation at the industrial scale took place at the ECOPETROL Refineries. The method listed below was followed:
-
Revision of real operating conditions of the desalting process at each plant, in fluids as well as desalting equipment, as follows: crude oil and water flows, temperature, pressure and interface level in the desalter, presure drop in the contact system.
-
Testing at laboratory and pilot plant scale, in which the contact systems were designed and chosen focusing on their application in the industrial process of desalting crude oil.
-
Tracking the process in order to define a base line of operation, measuring the following physical-chemical parameters of the fluids under study (crude oil and water) taking samples at the inlet and outlet of the desalters, operating with a mixture valve system as the contact device.
-
Installation of new contact systems at the industrial scale.
-
Subsequent tracking of the process in order to quantify the benefits reached in the global desalting system, operating under the new contact system designed by the ICP. The same physical-chemical parameters were measured as in numeral 3.
- BS&W and salt were measured in the crude oil in accordance with Standard ASTM D4007 and a modification of Standard ASTM D512-A.
- Salt and hydrocarbon content were measured in the water in accordance with Standards AWWA 5520-A,C/98 and ASTM D512-A.
- Pressure drop in the contact system.
Throughout the study, the desalter's operating parameters were kept constant.
Calculation of efficiencies: Desalting efficiency was evaluated in terms of minimum amount of salt carried-over by the crude oil, this variable being in function of salt concentration in the crude oil, the percentage of wash water, the amount of water in the crude oil and salt content in the wash water in accordance with the following equation:
Where:
A = minimum amount of salt in the desalted crude oil, PTB.
C = water carried-over in the desalted crude oil, % volume.
R = salt content in the crude oil that has not been desalted, PTB.
W = wash water, % volume
S = salt content in wastewater, ppm.
X = water in the crude oil that has not been desalted, % volume.
Thus, knowing the minimum amount of salt in the crude oil that has not been desalted, obtained from the above equation, the desalter performance can be calculated using the following equation:
Where:
- D = salt in the desalted crude oil, PTB.
The equation of desalter performance is based on the assumption that mixture efficiency is 100%. That is, that the wash water dilutes the salt in the water, so the salt content in the crude oil depends on the water content of the crude oil at the outlet of the desalter.
Dehydration efficiency is evaluated by the desalter's capacity to remove water from the crude oil. This is calculated as follows (Yang and Odedra, 1997):
Description of the modification in the mixing system
Cartagena refinery
Incoming crude oil is divided into two currents that go to desaltere D-301 and D-306 (Figure 3), which work in a parallel manner. Before entering each desalter, the crude oil is put in contact with a stream of water by means of a mixing system, which later goes to the drum-desalter where the phases are separated. Figures 4a and 4b illustrate the desalting process and the modification in the mixing system evaluated in this study.
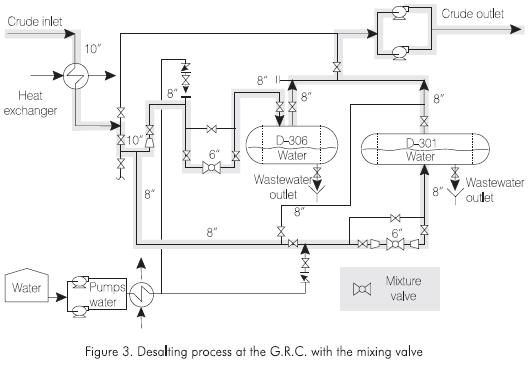
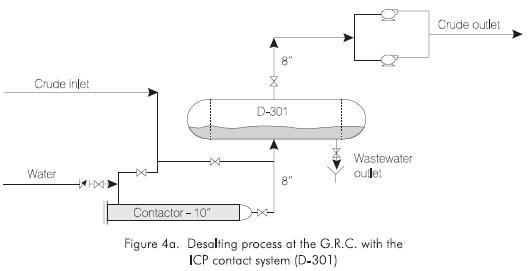
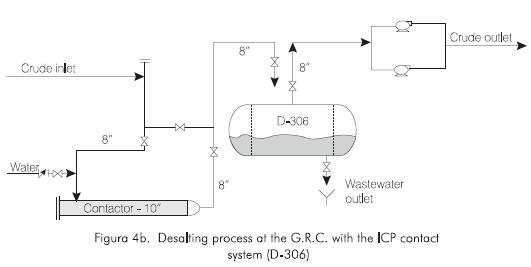
Barrancabermeja refinery
The crude oil is put in contact with a stream of water by means of a mixing system that later separates in the drum-desalter. Figures 5 and 6 illustrate the desalting process and the modification in the mixing system evaluated in this study.
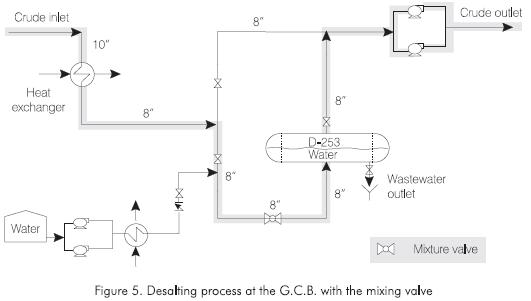
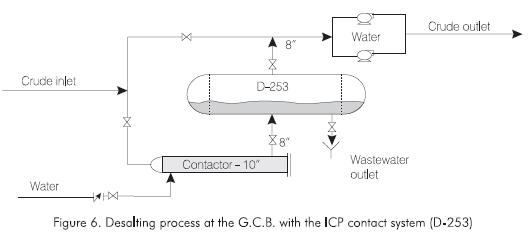
RESULTS AND DISCUSSION
Operating parameters
Table 1 indicates the values of the desalters' operating parameters at the Cartagena and Barrancabermeja Refineries.
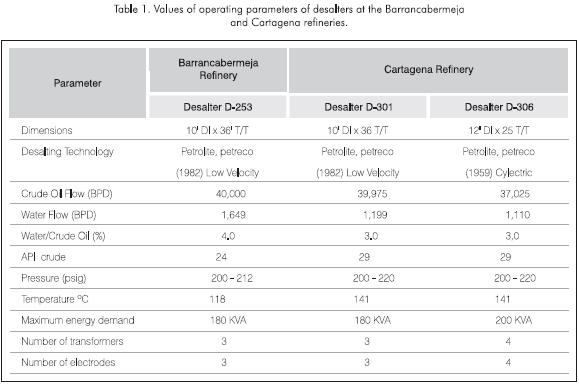
Evaluation of contact systems at the pilot plant
In crude oil desalting processes, mass transfer occurs mainly during the stage of crude oil contact with fresh water. Therefore, to have an efficient desalting process, this stage should have a balance between particle diameter and the contact area of the water dispersed within the crude oil so that the size of the water droplets is small enough for there to be a large area of contact, but also an easy separation of the phases.
The most appropriate contact system was selected during the laboratory stage in which the crude oil is washed with fresh water. The results that were obtained are illus-trated in Figure 7.
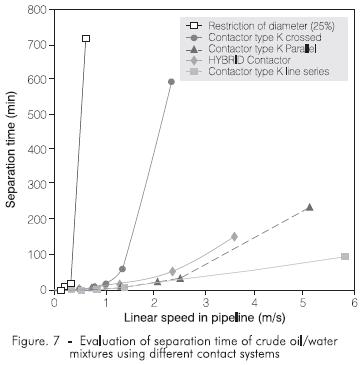
According to the results, the systems based on diameter restriction (mixing valves and orifice plates) produce very small water particles. This implies that mixing is very efficient and thus forms a very large interfacial area for mass transfer. But since the water particles are so small, strong emulsions are formed. These emulsions are stabilized by natural surfactants in the crude oil, which make the separation of phases very difficult. As a consequence, high BS&W values are produced in the crude oil at the outlet of the desalter and hydrocarbon is lost in the wastewater that is disposed of.
The desalting systems were operated with linear flow rates from 1.3 m/s to 1.5 m/s. According to Figure 7, at these operating rates at the industrial level, the systems based on diameter restriction requires very high retention times in order to separate the phases (over 1,000 minutes).
The contact systems that were evaluated show an efficient mixing, low retention times and low pressure drops. In order to maintain the rate conditions, HYBRID contactors were installed in 10 inch piping, thus ensuring phase separation times below 25 minutes, in agreement with residence times in the desalters.
The values obtained experimentally (Tables 2, 3, 4) led to the following analyses:
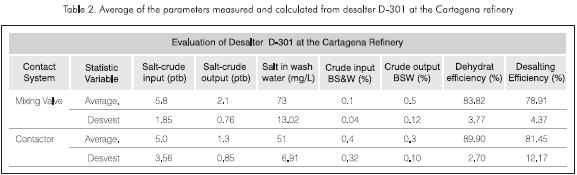
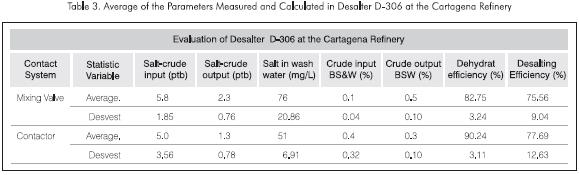
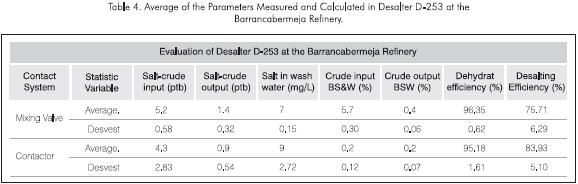
Desalting efficiency
The use of the static mixer slightly increased desalting efficiency. This explains why the average water content in the crude oil at the desalter outlet was higher when the mixing valve was used as a contact system.
Dehydration efficiency
Dehydration efficiency in both cases was higher with the use of the static mixer, except in the case of Desalter D-253 at the Barrancabermeja Refinery. This can be explained due to the fact that the water content in the crude oil input was too high. Nevertheless, if we compare the average BS&W of the crude oil output of the desalters, it was found that it decreased by 50% at the Barrancabermeja Refinery and by 40% in the two desalters of the Cartagena Refinery. The use of the contactor as the contact system reduced energy costs by decreasing water content in the crude output of the desalter by 154 and 80 BPD at the Cartagena and Barrancabermeja Refineries, respectively. This means savings at both refineries of US$ 373,000 per year represented in the margin of refining by increasing feed.
Hydrocarbon crude carried-over in the wastewater
Table 5 shows the results obtained regarding the hydrocarbon content in the water output of the desalting system at the Cartagena and Barrancabermeja Refineries.
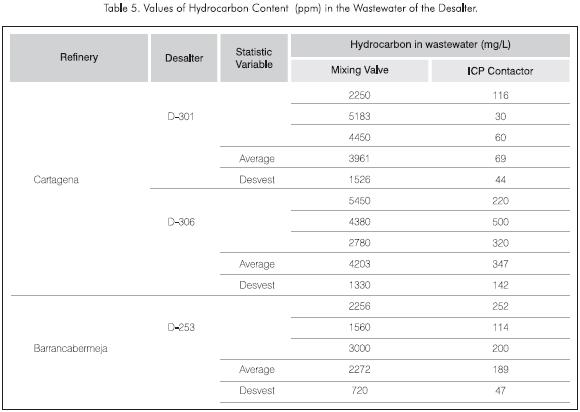
The use of the static mixer decreases hydrocarbon carry-over in the wastewater by 92% in Desalter of the GCB, and 98% and 92% in Desalters at the GRC.
Table 6 indicates the approximate values of hydrocarbon loss in the wastewater of desalters with contact systems.
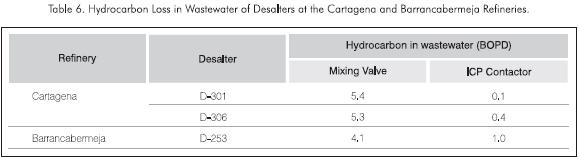
Pressure drop
It was found that the mixing valve produced a pressure drop between 10 and 15 psi and was reduced to 1 - 2 psi with the contactor. According to these data, the pressure drop was decreased between 85% and 90%, which means a remarkable increase in feed capacity.
General comparison
Tables 7 and 8 compare the values obtained from the water and the crude oil at the outlet of the desalters that were studied.
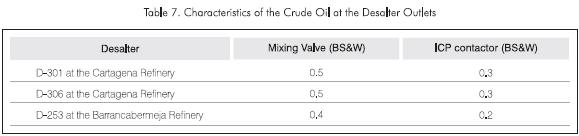
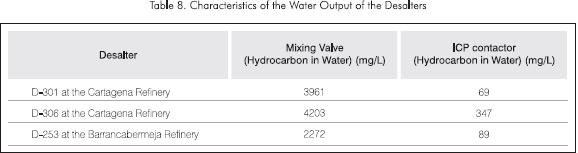
Results show that less water is obtained in the crude oil output and less crude oil in the wastewater output with the static mixer, which means economic and environmental benefits for the refinery.
CONCLUSIONS
The study allows us to conclude that:
In the desalting systems, the static mixer has greater advantages than the mixing valve for the following reasons:
-
It improved crude oil desalting efficiency.
-
Fewer tendencies to form emulsions, which mean a decrease in hydrocarbon loss in the water.
-
It increased the capacity of the lines by reducing pressure drop.
-
Environmental and economic benefits are obtained because there is less crude oil in the wastewater, and water carried-over in the crude oil at the desalter output is decreased.
ACKNOWLEDGEMENTS
The authors would like to express their thanks to the Engineers, Saul Santamaría, Domingo Escalante, Ezequiel Acosta, Luis Elias Yañez and John Pollock from the ECOPETROL.
They would also like to thank the personnel from the Rheology laboratories and Environmental Affairs at the ICP for their valuable cooperation and support in carrying out the tests and assays.
REFERENCES
Berkman, P. D. and Calabrese, R.V., 1988. "Dispersion of Viscous Liquids by Turbulent Flow in a Static Mixer", Aiche Journal, 34 (4): 602 - 609. [ Links ]
Bourne, J.R., Lenzner, J. and Petrozzi, S., 1992. "Micromixing in Static Mixers: An Experimental Study", Ind. Eng Chem., 31(4): 1216-1222. [ Links ]
Faroui, A., Hakenholz, F., Le Sauze, N., Costes, J. and Bertrand, J., 1998. "Determination of the Mixing Performance of Sulzer SMV Static Mixers by Laser Induced Fluorescence", The Canadian Journal of Chemical Engineering, 76: 522 - 526. [ Links ]
Forero, J., Diaz, J., Duque, J., 2000. "Diseño y evaluación de sistemas de contacto para aplicaciones de transferencia de masa en procesos de contacto líquido-líquido" Informe técnico Ecopetrol - ICP. [ Links ]
Koiranen, T., Kraslawski, A. and Nyström, L., 1994. "Knowledge -Based System for Mixing Type Selection", Ind. Chem. Res, 33:1756-1764. [ Links ]
Lang, E. and Dritina, P., 1995. "Numerical Simulation of the Fluid Flow and the Mixing Process in a Static Mixer", Int. J. Heat Mass Transfer., 38 (12): 2239 - 2250. [ Links ]
Nauman, E.B., 1982. "Reactions and Residence Time Distributions in Motionless Mixers", The Canadian Journal of Chemical Engineering, 60: 136 -140. [ Links ]
Pressdee, B., 1992. "A Dynamic Approach to Static Mixing", CIM Supplement- Process Engineering, Sep, 73: 79. [ Links ]
Scheider, G, 1983. "Contactores estáticos en la industria petrolífera". Revista Técnica Sulzer. [ Links ]
Xiaodong, Y, 2000. "Gas Oil Desalting Reduces Chlorides in Crude". Oil and Gas Journal, 98 (42): 76-78. [ Links ]
Yang, J. and Odedra, D., 1997. "Effect of Using Static Mixers on Gas-Liquid Mass Transfer", Aiche - Annual Meeting Session 148. [ Links ]