Services on Demand
Journal
Article
Indicators
-
Cited by SciELO
-
Access statistics
Related links
-
Cited by Google
-
Similars in SciELO
-
Similars in Google
Share
CT&F - Ciencia, Tecnología y Futuro
Print version ISSN 0122-5383On-line version ISSN 2382-4581
C.T.F Cienc. Tecnol. Futuro vol.4 no.1 Bucaramanga Jan./July 2010
2Ecopetrol S.A. - Gerencia Refinería de Barrancabermeja, Barrancabermeja, Santander, Colombia
3Ambiocoop, Piedecuesta, Santander, Colombia
e-mail: Mariael.Gomez@ecopetrol.com.co
(Received, Mar. 17, 2010; Accepted June 16, 2010)
* To whom correspondence may be addressed
ABSTRACT
Polycyclic Aromatics (PCA) are aromatic hydrocarbons and related sulphur and nitrogen compounds, containing three or more fused aromatic rings, which are considered as toxic compounds. PCA control is a complex task because the Base Oil production involves different processes with many variables such as pressure, temperature, feedstock quality, catalyst, etc.
This study focuses on controlling the hydrotreating temperature as main variable in the reduction of PCA in Naphthenic Bases. Two Naphthenic distillate fractions taken from an industrial plant were hydrotreated in pilot plant at different temperatures. The results show that PCA are reduced as hydrotreating temperature increases; however there is an optimum temperature above it, the thermodynamic equilibrium of aromatic hydrogenation reverses, increasing as a result, the PCA content. These results were implemented in the industrial Unit by installing a hydrogen quench between the two industrial reactors to guarantee that the profile of temperature, due to exothermic character of some reactions, be always in the optimun operating range.
Palabras clave: polynuclear aromatic hydrocarbon, hydrotreating, base oil.
RESUMEN
Los PCA están relacionados con el contenido de Policiclo Aromáticos de más de tres anillos y moléculas asociadas de nitrógeno y azufre, los cuales son considerados como compuestos tóxicos. Hacer control de PCA es tarea compleja, pues la producción de Bases involucra diferentes procesos industriales y muchas variables de control como presión, temperatura, calidad de carga, catalizador, etc.
Este estudio se enfoca en el control de la temperatura de hidrotratamiento como variable principal en la reducción de PCA en las bases Nafténicas. Se tomaron dos fracciones de destilado Nafténico de la planta industrial y se hidrotrataron en planta piloto a diferentes temperaturas. Los resultados muestran que los PCA son reducidos a medida que se incrementa la temperatura de hidrotratamiento; sin embargo se encontró una temperatura óptima de máxima reducción por encima de la cual se invierte el equilibrio termodinámico de las reacciones de hidrogenación de aromáticos, lo cual incrementa por consiguiente el contenido de PCA. Basado en lo anterior se estableció un quench de hidrógeno entre los dos reactores industriales para garantizar que el perfil de temperatura, debido a la exotermicidad de las reacciones, se mantenga en el rango óptimo de operación.
Key words: hidrocarburos aromáticos polinucleares, hidrotratamiento, bases lubricantes.
INTRODUCTION
The industrial process for production of the Naphthenic Base Oils studied in this paper involves Vacuum Distillation and hydrotreatment. Naphthenic Crude Oil is first distillated in an atmospheric distillation Unit to remove gases, Naphthas, kerosene and atmospheric Gas Oil. The long residue is then fractionated in a Vacuum Distillation Unit to obtain two Oil fractions, Medium and Heavy Naphthenic Bases, in the range of 700-850°F and 850-1000°F. These fractions are not extracted, both of them are hydrotreated in two reactors equally sized with no gas quench facilities that operate at high pressure and temperature to improve color and reduce some undesiderable constituents such as Polycyclic Aromatics to fit PCA.
According with some European Environment Agencies (Ellison & Simpson, 1994) the content of PCA in Naphthenic Base Oils must be below 3% in order to avoid the presence of some toxic compounds related with Polycyclic Aromatics of more than three rings. These compounds can come in direct contact with the skin by the users of the final products such as lubricant oils and greases obtained from Naphthenic Base Oils. Currently, many refineries have adopted the IP346 methodology which represents a relatively cheap and quick option in determining PCA.
The scope of this study is to find the best industrial conditions to achieve lower PCA as possible, keeping product quality under specifications. Considering the whole process involves only two units, distillation and hydrotreating, this study will focus on hydrotreatment, assuming that the two fractions from distillation are always in the specific boiling range.
In general, in an existing Commercial Unit, the operational conditions are fixed during the unit design and are difficult and expensive to modify. Temperature and up to some extension Space Velocity (LHSV) and Catalyst are the most commonly variables to fit in an industrial reactor. Concerning the catalyst, some Ni-Mo solids were tested without outstanding results to show in this paper.
A series of pilot plant tests is therefore proposed to see the relationship between operating conditions and product quality to minimize PCA keeping the other properties under specifications.
Understood the response of hydrotreating reactions to changes in operating conditions is a key to guarantee suitable results in each particular industrial process. In general, the reactions in any Hidrotreater are always the same, aromatic saturation, sulphur and metal removal, etc. However depending on feedstock type and the purpose of the hydrotreated stream, each process needs to make only emphasis in some reactions. So, in the case of Gasoil pre-treatment, the process needs mainly aromatic saturation to improve naphtha and distillates in Fluid Catalytic Cracking (FCC) and reduce catalyst poisons such as metals and Nitrogen. But in the case of Base Oils the process requires Hydrogen addition to saturate aromatics, reduce PCA and improve VI; sulphur removal is not of interest since sulphur is considered by some literature as a natural antioxidant; metals and Carbon removal is not of interest here since distillates from Fractionator are almost free of these catalyst poisons.
THEORETICAL FRAMEWORK
Experiments with Phenanthrene over several catalysts (Qian, Yoda, Hirai, Ishihara & Kabe 1999) show that hydrogenation of aromatics (Figure 1) is a reversible reaction, limited by the chemical equilibrium. At this condition the forward reactions of aromatic saturation equal the reverse rate of dehydrogenation of Naphthenes. Curves in Figure 1 show a maximum saturation at about 644°F.
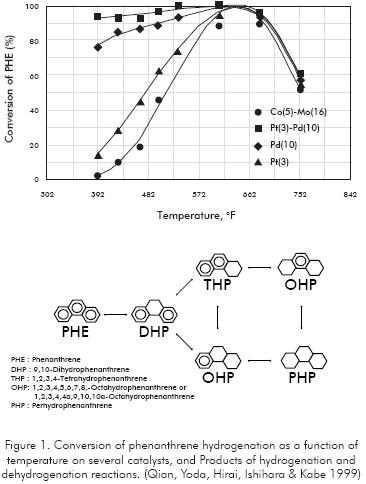
Other experiments with industrial Gasoils in the boiling range of 300-630°F also have shown that aromatics conversion passes through a maximum with respect to the temperature at nearly 720°F (Figure 2). This optimum temperature depends on the other operating variables of the unit, like pressure, catalyst type and the chemistry of the feedstock. Operate at higher pressures let to increase the optimum temperature since the chemical equilibrium is move forward to the right, allowing greater saturation of aromatics (Figure 3a). The catalyst type does not affect significantly the optimum temperature but it has impact in the extension of saturation (Figure 3b).
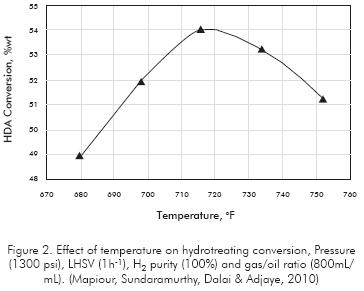
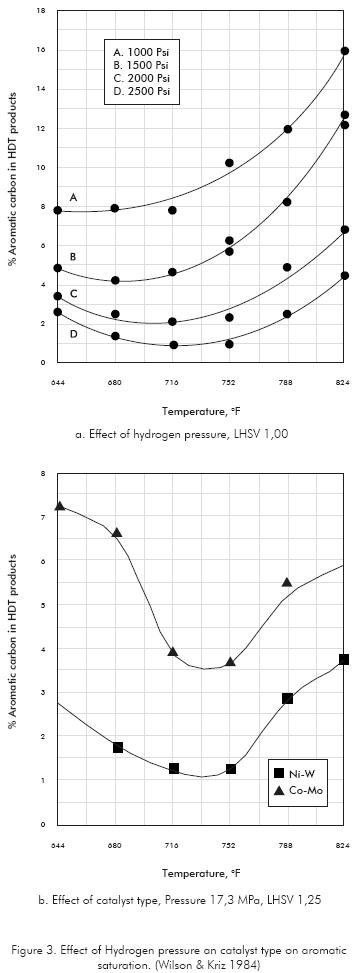
According to literature cited above, hydrotreatment temperature is a critical variable in aromatic saturation. This fact joint to most of the hydrotreating reactions are exothermic, make the reactor designs must fit to the requirements of temperature control by developing facilities of heat removal. Modern designed units try to achieve an isothermal reaction by distributing the catalyst over various beds and using intermediate quenching with cold gas to limit the temperature range of the reaction.
EXPERIMENTAL DEVELOPMENT
HDT studies were conducted in a once through hydrogen Pilot Plant of 120 ml in capacity. Reactor temperature was maintained isothermal by four independent controlling heating coils. The internal bed temperature is monitored by using an axial thermocouple located in a thermowell. The catalyst was diluted 1:1 with Otawa Sand mesh 100 to improve flow pattern by minimizing channeling, wall effects and back mixing phenomena. Previous experiment has demonstrated this sand is completely inert to the hydrotreating reactions. The catalyst and the inert were calcined and then charged into the reactor to operate in upflow mode, this also improve flow pattern.
Activation of the catalyst was carried out by using a medium distillate spiked with 2,5wt% Dimethyldisulfide (DMDS) during 8 hours to ensure complete catalyst presulfiding. The catalyst were deactivated with the feed oil at Liquid hourly space velocity (LHSV) of 3h-1 until the HDS conversion reached at steady value (8 days to ensure good stability during the whole test that lasted 8 days).
The catalyst used to performance the test was the industrial one recommended for this type of processes: A trilobulate extrudate NiMo catalyst supported on Alumina.
The experiments were carried out at six different temperatures (581, 608, 653, 680, 707 and 734°F) and two hourly space velocities, 0,5 and 1,0 h-1. The other variables were kept constants at conditions of the industrial plant, 1500 psi, hydrogen to Oil ratio of 1500 ft3/bbl.
Boiling point distribution of the feed and liquid products was obtained from gas chromatographic simulated distillations according to ASTM D-2887 for middle fractions and D-5307 for heavy fractions. Sulfur content was carried out using a Horiba analyzer and following the ASTM D-4294. The Viscosity Index "VI" was determined according to the ASTM D2270 procedure.
PCA, considered as aromatics containing three or more fused aromatic rings with short alkyl or cycloalkyl groups as substituents, were determined following the method described in IP346. This standard consists on several extractions with dimethylsulphoxide of the Base Oil diluted with cyclohexane.
The hydrocarbon group types were determined by mass spectrometry using a GC/MS analyzer.
RESULTS
Medium and Heavy Naphthenic Distillates coming from industrial Vacuum Unit were used as feedstocks to perform the HDT Pilot Plant experiments. Table 1 shows the properties of these streams and the expected specifications of the final hydrotreated Naphthenic Base Oil, which become the target of improvements to reach by HDT in color, Viscosity, VI and PCA.
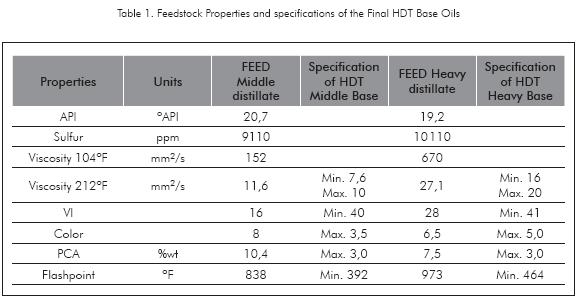
Product viscosity at 212°F is a property to keep under a narrow specification, between 7,6-10 and 16-20 mm2/s for Middle and Heavy Base Oils respectively (Table 1). These requirements in viscosity are better controlled from Vacuum Unit by setting the appropriate range of distillation, taking into account that viscosity drops with HDT severity (Figure 4). The scope of HDT is not to fit viscosity under specifications, it is to improve VI, reduce PCA and to give good appearance to the Base especially in color.
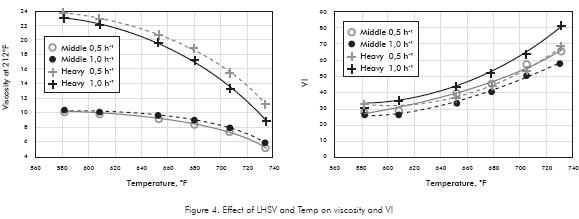
Contrary to Heavy Base behavior, the Middle Base viscosity is less sensitive to temperature; its profile is quite flat as severity progress. Heavy Base viscosity drops quickly and falls below specifications at about 690°F (Figure 4). These results could indicate that the distillation range of the Middle and Heavy Oils should be fitted a little from the Vacuum Unit to ensure the specifications from this process. So, all the attention in HDT can hold on improving the other specifications. Few changes in viscosity are observed as space velocity drop, the same profile is observed at 0,5h-1.
As HDT severity rise, the presence of new compounds, coming from reactions of hydrogen addition take place, making products of lower molecular weight, lower boiling point and higher VI. Thus, Polycyclic Aromatics of low VI (even negative values) are saturated into compounds of higher VI such as Polycyclic Paraffines (Figure 5a), which can be turn to Monocyclic Paraffines of VI higher than 100 through hydrodecyclization reactions (Figure 5b).
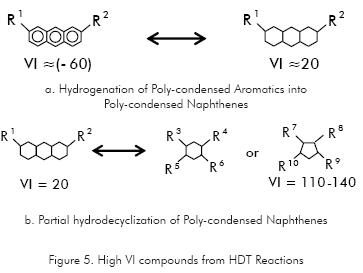
Big Iso-Paraffines of even higher VI (165), like C26H54, can be produced but under more severe conductions like those of Hydrocracking.
Severity in temperature should handle carefully, avoiding undesirable products from cracking reactions that makes the molecular weight and the liquid yield becomes uncontrollably lower. These two facts represent a serious detriment in product specifications and in consequence on process economy.
VI increases as temperature increases (Figure 4). This fact is more significantly true as cracking reactions take place, due to components of low molecular weight and low viscosity such as linear Paraffines of high VI but nil value as base oils. Higher VI's are desirable when they come from hydrogen addition reactions like was described in Figure 5.
Products from Hydrotreatment are lighter than those in Distillates. However, high amounts of Lights should be controlled avoiding cracking reactions produced by excess of process severity. Chromatographic distillation was used for this control since it is more efficient than lab distillations in the analysis of the initial boiling points of the hydrocarbons. Figure 6 show how lighter fractions lower than 700°F, for Middle Bases, and 800°F for Heavy Bases, increase as temperature become higher. Thus, at HDT temperature of 734°F it is evident the presence of products from cracking reactions since, in both cases, the light fraction reach up to 35% of the total stream.
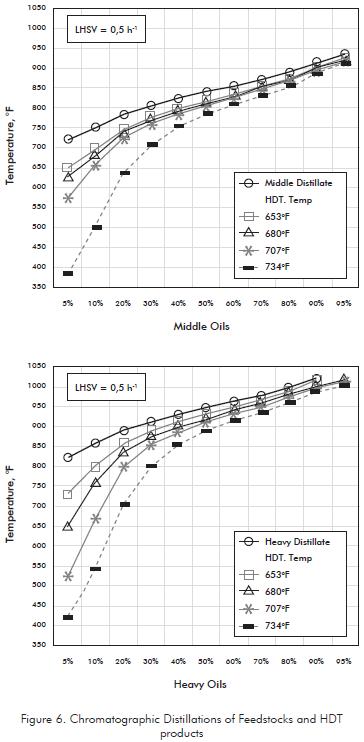
Products from hydrotreatment like Naphthenes have lower density than molecules in Distillate, so it is expected that API increase linearly as temperature get higher. However at 680°F, this profile becomes more sloping (Figure 7) being affected by lighter fractions produced by cracking at high temperatures. The profile is similar at both space velocities.
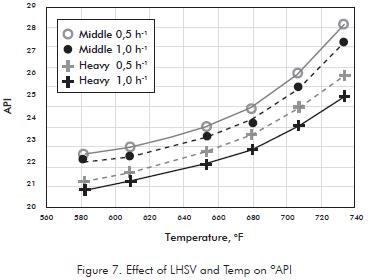
Saturation of aromatics with more than three rings is the special interest for this study not only because these molecules are responsible of low VI, but also because they are related with PCA. In Figure 8, results of PCA show how they are reduced as the treated temperature increase, but nearly above 680°F there is an inflexion point where the PCA begin to increase. This point corresponds to the optimum temperature where the chemical equilibrium takes place. Above this temperature PCA begin to increase.
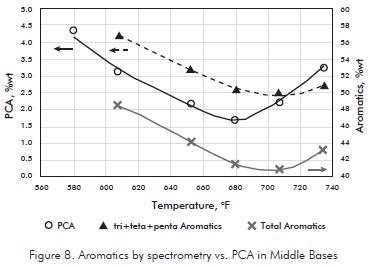
Saturation of aromatics with more than three rings is the special interest for this study not only because these molecules are responsible of low VI, but also because they are related with PCA. In Figure 8, results of PCA show how they are reduced as the treated temperature increase, but nearly above 680°F there is an inflexion point where the PCA begin to increase. This point corresponds to the optimum temperature where the chemical equilibrium takes place. Above this temperature PCA begin to increase. Middle Distillates and their hydrotreated products were analyzed by mass spectrometry to study the changes in the structural basic groups. According with the results (Table 2), aromatics of five rings are almost completely saturated; tetra, tri and di-Aromatics are progressively saturated toward one ring aromatics which in fact are the only aromatic group that increases with HDT temperature.
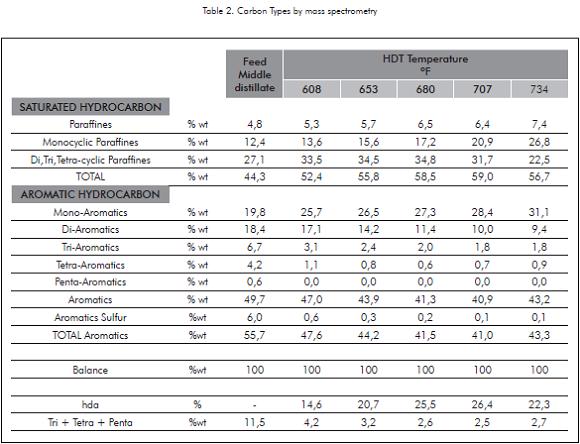
Tri, Tetra and Penta-Aromatics together are reduced from 11,5% in the feed up to 2,5% in the Base Oil (Figure 8), these data match PCA results, and in both cases they are under 3%. However must be taken into account that there is no comparison between mass spectrometry and PCA results; as it was described at the beginning of this paper, they follow completely different analytical procedures.
For Total Aromatics, they decrease to some extension showing a minimum in the range of 680- 700°F (Figure 8). In this range, 26% is the maximum saturation of Total Aromatics. This minimum is not observed in the individual aromatics groups, only Tetra-Aromatics increase a little, from 0,7 at 707°F to 0,9 at 734°F, which it is not too significant. The rise in Total Aromatics at 700°F is coincident with a fall in Polycyclic Paraffines from 31 to 22% that increase mono-Aromatics and Monocyclic Paraffines from reactions of deshidrogenation and hydrodecyclization but also from cracking reactions.
The shape of Total Aromatics saturation profile matches well PCA temperature profile. That means that Total Aromatics by mass spectrometry could be used as a quick tool to set optimum reactor conditions but keeping in mind that further PCA analysis should be done to finally tune reactor temperature and then ensure product specifications.
Paraffines increase along the range of studied temperature. but the net result of saturated hydrocarbons increase with temperature until nearly 700°F and then they drop from 59% to 56%. This behavior is consistent with Total Aromatics profile, as Total Aromatics rise with temperature from nearly 700°F, saturated hydrocarbons drop.
Even so aromatic saturation is better performed at low LHSV, the effect of LHSV was also studied in order to evaluate a possible increase in HDT capacity by reducing the residence time. The results show that increase LHSV from 0,5 to 1,0h-1 is some risky for PCA performance, since at 1,0h-1 the PCA specifications are on the edge of the limits, 3%, (Figure 9), so operate at these conditions required continuous PCA monitoring.
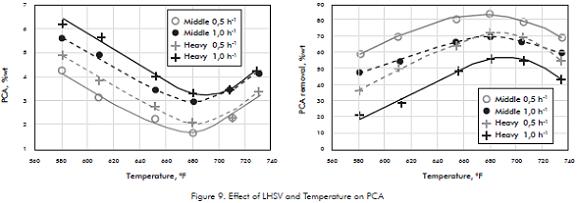
Hydrotreating severity results also in a high degree of hydrodesulphurization (HDS) even so, it is not desired to low sulfur content, since sulfur is considered as a natural antioxidant, that help to maintain the quality product during storage (Figure 10).
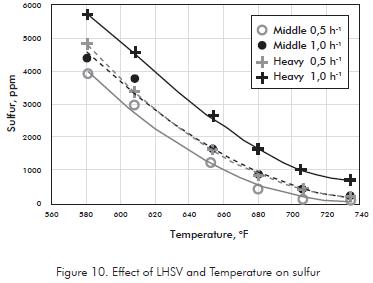
The results indicate that the control of temperature is very important to guarantee the PCA in specifications, this task is some difficult in the industrial reactor
Contrary to the Pilot plant which operates on isothermal mode, the temperature of the industrial reactor rises gradually along the reactor due to exothermic reactions; these reactors with big amounts of catalyst are difficult to control. For this reason a series of Pilot plant test are required before embarking on designing a quench system.
In this case, based on these results, it was design and installed between the two industrial reactors a quench line at the inlet of the second reactor. The temperature along the two reactors, before and after the quench is shown in Figure 11.

Industrial tests "before" and "after" the quench have some differences in Feed flowrates, 70 vs. 75 bbl/h, that affects the deltas in temperature due to the heat generate by the reactions along each reactor, the more feed to reactor the higher the deltas, so that deltas after the quench are 10 and 5°F higher than before the quench; more flowrate, after the quench, also make inlet temperature be 10°F lower.
Before the quench only the first reactor operates in the recommended range of temperature, the second one reaches temperatures between 690 and 715°F. If the Unit operates at higher flowrates, with no quench, the outlet temperatures would be higher. This situation threatens PCA specifications.
After the quench the temperature at the inlet of the second Reactor drops 30°, from 690°F to 660°F and leaves it at 690°F, 10° above the optimum, but still under PCA specifications. Thus, the desired temperature profile was achieved successfully in the industrial plant.
CONCLUSIONS
- This study highlights the importance to optimize the HDT conditions of Naphthenic distillates to minimize PCA content in Base Oils. It was found a temperature of maximum aromatic saturation in the range of 680- 700°F that guarantee PCA values lower than 3,0 and good performance of the other properties, color, VI and viscosity, under specifications.
- Some literature (Mapiour, Sundaramurthy, Dalai, & Adjaye, 2010) in the case of Gasoil, has found this max saturation at about 720°F, which is higher than the found here for Base Oils. Some refiners apply this maximum reported in literature for Gasoils, since there is no available information for Base Oils. But despite Gasoil and Base Oils have a similar distillation cut, their chemistry is different
- Not only feed chemistry but also unit design conditions represent variables in process optimization, for instance catalyst type or operating pressure also affects the degree of aromatic saturation and the optimum operational temperature as was mentioned in the theoretical framework, thus the importance to customize operational conditions for each particular process.
ACKNOWLEDGEMENTS
The authors express their gratitude to the HDT Pilot Plant personnel and Laboratories of Refining located at the Instituto Colombiano del Petróleo (ICP) for their cooperation in trial development, and to the people of the Refinery for their compromise in the Industrial tests runs. The authors also thank CT&F editors and evaluators for their careful observations.
REFERENCES
ASTM Standard D-4294. (2008). Standard Test Method for Sulfur in Petroleum and Petroleum Products by Energy Dispersive X-ray Fluorescence Spectrometry. ASTM International, http://www.astm.org. [ Links ]
ASTM Standard D-2887. (2008). Standard Test Method for Boiling Range Distribution of Petroleum Fractions by Gas Chromatography. ASTM International, http://www.astm.org. [ Links ]
ASTM Standard D-2270. (2004). Standard practice for calculating viscosity index from kinematic viscosity at 40 and 100°C. ASTM International, http://www.astm.org. [ Links ]
ASTM Standard D-5307. (2007). Standard test method for determination of boiling range distribution of crude by gas chromatography. ASTM International, http://www.astm.org. [ Links ]
Ellison, R. J. & Simpson, B. J. (1994). The use of the dimethyl sulphoxide (DMSO) extract by the IP 346 method as an indicator of the carcinogenicity of lubricant base oils and distillate aromatic extracts. CONCAWE, Brussels: 1-41. [ Links ]
IP 346. (1993). Determination of polycyclic aromatics in unused lubricating base oils and asphaltene free petroleum fractions - dimethyl sulphoxide extraction refractive index method. Standard methods for analysis and testing of petroleum and related products. 2. Chichester: John Wiley and Sons. [ Links ]
Mapiour, M., Sundaramurthy, V., Dalai, A. K., & Adjaye, J. (2010). Effects of the operating variables on hydrotreating of heavy gas oil: experimental, modeling, and kinetic studies. Fuel. 89: 2536-2543. [ Links ]
Qian, W., Yoda, Y., Hirai, Y., Ishihara, A., & Kabe, T. (1999). Hydrodesulfurization of dibenzothiophene and hydrogenation of phenanthrene on alumina-supported Pt and Pd catalysts. Appl. Catal. A: Gen. 184: 81-88. [ Links ]
Wilson, M., & Kriz, J. (1984). Upgrading of middle distillate fractions of a syncrude from Athabasca oil sands. Fuel, 63: 190-196. [ Links ]