Services on Demand
Journal
Article
Indicators
-
Cited by SciELO
-
Access statistics
Related links
-
Cited by Google
-
Similars in SciELO
-
Similars in Google
Share
CT&F - Ciencia, Tecnología y Futuro
Print version ISSN 0122-5383On-line version ISSN 2382-4581
C.T.F Cienc. Tecnol. Futuro vol.4 no.5 Bucaramanga Jan./June 2012
2Programa de Ingeniería Mecánica, Facultad de Ingeniería, Universidad Tecnológica de Bolívar, Cartagena, Colombia
ABSTRACT
The main objective of this paper is the experimental investigation of the energy indexes of a cogeneration plant with Gas Turbines (GT) and Heat Recuperator Steam Generators (HRSGs) while changing its operational load. The energy indicators were determined using the following International Standards and Codes: ASME PTC1, ASME PTC 22 and ASME PTC 4.4. The results of energy calculations indexes are in the form of curves. The mathematical equations of the curves corresponding to the real energy indexes are obtained applying multivariate regression.
The main research results correspond to a process plant with nominal capacity of 4800 kW. The range of lower energy consumption values obtained for the HR of the turbine are around 13000 kJ/kW·h, while for the Heat Rate of the plant is 7000 kJ/kW·h. For these values of the Heat Rate (HR), the electrical output remains in the environment of 3500 kW. It was found that the thermal efficiency of HRSGs varies from 50 to 60% with very high values of sensible heat losses in flue gases due to the operation with high excess air and high temperatures of the gases at the outlet of HRSGs. The contributions of this research are used in operational management in order to reduce fuel consumption and environmental impact on the generation of electricity and heat cogeneration plant evaluated. The results of this research in the plant have been implemented to monitor the transaction on the basis of the variation in real-time energy indexes evaluated, besides the traditional control of the parameters only, which is more effective.
Keywords: Energy indexes, Cogeneration, Specific consumptions, Mathematic equations, Thermal efficiency.
RESUMEN
El objetivo principal del artículo es la investigación experimental de los índices energéticos de una planta cogeneradora con Turbinas a Gas (TG) y generadores de vapor recuperadores de calor (HRSGs) al variar su carga operacional. Los indicadores energéticos se determinaron aplicando las Normas y Códigos Internacionales siguientes: ASME PTC1, ASME PTC 22 y ASME PTC 4.4. Los resultados de los índices energéticos calculados se presentan en forma de curvas. Las ecuaciones matemáticas de las curvas correspondientes a los índices energéticos reales se obtienen aplicando la regresión lineal múltiple.
Los principales resultados de la investigación, corresponden a una planta con capacidad nominal de 4800 kW. El rango de menor consumo energético se obtiene para valores del Heat Rate de la turbina que están alrededor de los 13000 kJ/kW·h, mientras que para el Heat Rate de la planta es de 7000 kJ/kW·h. Para estos valores del Heat Rate, la potencia eléctrica generada se mantiene en el entorno de los 3500 kW. Se obtuvo que la eficiencia térmica del HRSGs varía del 50 al 60%, con valores muy altos de las perdidas por calor sensible en gases de chimenea debido a la operación con elevados excesos de aire y altas temperaturas de los gases a la salida del HRSGs. Los aportes de esta investigación se utilizan en la gestión operacional con el propósito de disminuir el consumo de combustible y el impacto ambiental en los procesos de generación de energía eléctrica y térmica de la planta de cogeneración evaluada. A parir de los resultados de esta investigación en la planta se ha implementado el monitoreo de la operación sobre la base de la variación en tiempo real de los índices energéticos evaluados, además del control tradicional sólo de los parámetros, lo cual resulta más efectivo.
Palabras clave: Indices energéticos, Cogeneración, Consumos específicos, Ecuaciones matemáticas, Eficiencia térmica.
RESUMO
Objetivo principal do artigo é a pesquisa experimental dos índices energéticos de uma planta co-geradora com Turbinas a Gás (TG) e geradores de vapor recuperadores de calor (HRSGs) ao variar a sua carga operacional. Os indicadores energéticos se determinaram aplicando as Normas e Códigos Internacionais seguintes: ASME PTC 1, ASME PTC 22 e ASME PTC 4.4. Os resultados dos índices energéticos calculados apresentam-se em forma de curvas. As equações matemáticas das curvas correspondentes aos índices energéticos reais se obtêm aplicando a regressão lineal múltipla.
Os principais resultados da pesquisa correspondem a uma planta com capacidade nominal de 4800 kW. A categoria de menor consumo energético se obtém para valores do Heat Rate da turbina que estão ao redor dos 13000 kJ/kW·h, enquanto que para o taxa de calor da planta é de 7000 kJ/kW·h. Para estes valores do taxa de calor, a potência elétrica gerada se mantém no entorno dos 3500 kW. Obteve-se que a eficiência térmica do HRSGs varia de 50 a 60%, com valores muito altos das perdas por calor sensíve em gases de chaminé devido à operação com elevados excessos de ar e altas temperaturas dos gases na saída do HRSGs. Os aportes desta pesquisa se utilizam na gestão operacional com o propósito de diminuir o consumo de combustível e o impacto ambiental nos processos de geração de energia elétrica e térmica da planta de co-geração avaliada. A partir dos resultados desta pesquisa na planta se tem implementado o monitoramento da operação sobre a base da variação em tempo real dos índices energéticos avaliados, além do controle tradicional só dos parâmetros, o qual resulta mais efetivo.
Palavras chave: índices energéticos, Co-geracáo, Consumos específicos, Equacóes matemáticas, Eficiência térmica.
1. INTRODUCTION
The main objective of this paper is the experimental research of the energy indexes of a cogeneration plant with GT and HRSGs while changing its operational load. The research was conducted in one of the two cogeneration plants installed in the Biofilm S.A. company in Cartagena (Colombia), specifically in the cogeneration plant with a capacity of 4,8 MW electric power generation and steam generation capacity of 14 ton/h. The energy indicators were determined by applying the following international standards and codes: ASME PTC1, ASME PTC 22 and ASME PTC 4.4.
The scope of this research was the study, in real operating conditions in which the cogeneration plant is operating, of the variation of the following energy indexes:
-
HR of the plant in relation to power generated.
-
HR of the GT in relation to power generated.
-
Generated steam in the HRSGs in relation to overall efficiency.
-
Generated steam in relation to the HR of the plant.
-
Generated steam in relation to the GT.
-
Thermal efficiency of the HRSGs.
This research has as a particular fact that Biofilm S.A., has an Energy Management System that establishes the need for monitoring of electricity consumption in each shift to identify the causes of its variation. This periodic monitoring allows for a continuous follow up when implementing actions to improve processes and equipment, it also shows the decrease of energy efficiency when carrying out events that involve a higher energy expenditure such as keeping some electric motors without charge working withought production, frequent starts in a given period, replacement of equipment by others of higher power that are not needed for the process. The control variables, which are those that can change the indicator of energy consumption rate can be: operational parameters, process events, maintenance problems or technical state of equipment, knowledge problems, information and coordination, implementation problems, regulation and control; structural or administrative control of the process problems (e2 Energía Eficiente, 2003).
Other specific background elements to take into account in terms of this this article are the results of experimental research titled in its English translation "Method for operational control online in GT power generation: Case Biofilm S.A. Cartagena plant" (Bermúdez, 2010).
In order to implement the work a data acquisition system designed and put to work to take readings of the operating parameters, processing and determination of energy indexes in real time.
The main impacts of the research results are as follows:
-
Implementing a system for real-time monitoring of the behavior of the energy indexes of the cogeneration plant with GT and HRSGs.
-
The variation of the main energy indexes of all the cogeneration plant and of the GT, when operating with different values in the generation of electrical power and steam flow to the outlet of the HRSGs.
-
The mathematical models obtained by processing the experimental data using multivariate regression. Models correspond to the efficiencies (global and the HRSGs), and the HR (turbine and plant) in relation to the operational parameters such as the power generated, the steam flow, flow and temperature of combustion products.
-
The thermal efficiency of the HRSG, by conducting heat balances, quantification of losses and combustion analysis, which makes it possible to determine the current indexes of efficiency and ways to increase its potential with the implementation of measures to use energy efficiently.
-
The economic benefits that could be obtained by applying actions to reduce energy losses in the HRSGs and operating the cogeneration plant in the optimal range of specific consumption.
2. THEORETICAL FRAMEWORK
Cogeneration is defined as the simultaneous generation of useful thermal energy (useful heat) and electricity and/or mechanical, it is a very efficient means for energy conversion. Its use has positive impacts on the economy, environment, and safety of energy supply. Cogeneration shows energy efficiency than conventional plants (independent production of heat and electricity). Cogeneration is defined as the simultaneous generation of useful thermal energy (useful heat) and electricity and /or mechanical, is a very efficient energy conversion.
Cogeneration shows greater energy efficiency than that of conventional plants (independent heat and electricity production). This leads to saving primary energy and reducing emissions of carbon dioxide, which is the first greenhouse effect gas. The specialized literature addresses the cogeneration technology using similar concepts, with some particular emphases. Sala (1994), defines cogeneration as joint production, in sequential process, electrical (or mechanical energy) and useful thermal energy. It is also defined as the combined heat and electrical power production (Combined Heat and Power, CHP).
Cogeneration means simultaneous production of two or more types of energy. Energies that are typically generated are electricity and heat, although there may also be generation of mechanical energy and heat (and /or cold) (Garcia & Fraile, 2008). It has been shown (Troyanovsky, Filippov & Bulkin, 1987) that you can get a great economic advantage when producing in a combined manner electricity and heat.
According to the analyzes performed, the Carnot efficiency behaves as follows: a steam plant without reheating is in the range of 37 to 50% and with reheating it is 45 to 54%, where as for a plant with simple GT the range is 42 to 47%, and for a power plant of combined cycle the efficiency of the Carnot cycle is in the range of 63 to 68% (Kehlhofer, 1997).
Cogeneration with GT with combined cycle can achieve 80% overall efficiency in energy use (Stultz & Kitto, 1992). Also, the cogeneration with GT in combined cycle reaches electrical efficiency values between 35 and 50%, greater tan the range between 7 and 20% reported with back pressure steam turbines for the same range of electric power (IDAE, 2008).
Table 1, presented by Garcia and Fraile (2008), shows the evolution in the performance of GT and the relationship between the combustion temperature and performance. It is demonstrated that by raising the temperature of the gases in the GT inlet from 943 to 1380°C, performance nearly doubles ISO conditions.
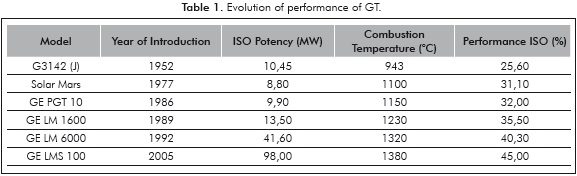
In the works of Garcia and Fraile (2008); Teopa, Picón and Rodríguez (2005), Pintanga, Hacon, Tessarollo and Reis (2010); Balli, Aras and Hepbasli (2010) and Schicktanz, Waple and Henning (2011), it is established that cogeneration plants are classified as:
-
Cogeneration with alternative motor for gas or fuel.
-
Cogeneration with steam turbines.
-
Cogeneration in combined cycle, with GT.
-
Cogeneration in combined cycle, with alternative turbine.
-
Combined cycle cogeneration with reciprocating engine.
-
Cogeneration with GT and HRSGs.
-
Trigeneration.
Methods to improve the thermal efficiency (advanced systems) of cogeneration plants with GT and HRSGs, are the following according to Booyce (2002); ASME PTC 22 norm (Galip & Durriye, 2004; Bruno, Ortega & Coronas, 2009): regeneration, intercooling, reheating, combination of the mentioned methods.
The electrical energy generated in this plant supplies 94% of demand in the processes of: line 3, regranulation 3, metallizer 3, primary cutter 3, line 3 ventilation, secondary cutters 1; 2 and 3,83% of consumption in line 3 corresponds to the following consumption by product sub-areas: extrusion, transportation, services, regranulation and metallizer 3 (e2 Energía Eficiente, 2003). It has proven that it very useful and advantageous to go beyond the traditional method of operation of power plants, which monitor only the parameters to ensure safety, to an operation based on the monitoring of performance indicators to ensure efficiency, maintaining security (Santos, 1999).
It is equally useful and advantageous to maintain a continuous monitoring of energy indicators related to the operation of the cogeneration plant to identify and prevent the causes of greater impact on energy efficiency in the production of electricity and thermal energy.
This articles objective is to present the results of research conducted for the purpose of evaluating the behavior of energy indicators in a cogeneration plant with GT and HRSGs. To meet this objective a data acquisition system was designed and implemented to take readings of the operating parameters, their processing and determination of energy indexes in real time.
3. EXPERIMENTAL DEVELOPMENT
Standards and international codes (ASME) used in this study were the following: ASME PTC 1 General Instructions for Power Test Code; ASME PTC 22 GT power plants - Power test code and ASME PTC 4.4 GT heat recovery steam generators performance test code. The energy indicators investigated in this paper are:
Turbine HR:
Thermal efficiency of the GT:
Thermal efficiency of the vapor generator (HRSGs):
HR of thecogeneration station:
To quantify the efficiency of the HRSGs the methodology for calculating overall ASME PTC 4.4 was adapted. This methodology recommends two methods of calculation: the input - output method also known as the direct method, and the loss method, also known as the indirect method.
Obtaining the flow of combustion products is a result of the knowledge of the chemical composition and rate of fuel consumed and the chemical composition of the products of combustion. The proposed methodology for the calculation of combustion gas flow is based on work carried out by several researchers (Ganapathy, 2003; Kenneth & Heselton, 2005; Baukal, 2000), from the theoretical combustion reactions and the concentration of each constituent present in the fuel, as well as the application of mass balance.
Combustion Gas Enthalpy
The enthalpy of combustion gases depends on specific heat and temperatures. Several researchers have shown that the chemical composition and excess air in the combustion influence the magnitude of the specific heat of the combustion gases (Chandok, Kar & Tuli, 2008; Eicher, 2000; Kyle, 1984; Yrjölä, Paavilainen & Sillanpää, 2006).
The specific heat influences the heat transfer coefficient that in turn varies with pressure and temperature of the combustion gases. At the exit of the combustor gases have a temperature that fluctuates around 1100°C and the temperature at the outlet of the GT is approximately at 500°C.
The combustor operates with a significant amount of excess air as one of measures to reduce mechanical failures associated with high temperatures. As a result some methodologies suggests considering the combustion products as one hundred percent air rather than combustion products (Horlock, 2003; Booyce, 2002).
The specific heat of air at the entrance of the GT, estimated at 1000°C, as compared to the 500°C at the output of the GT, show a difference of 4,5%, at atmospheric pressure. In the case of the specific heat of carbon dioxide, which is always present in combustion gas, the estimated difference for that same temperature range is of 9,7% (Kizniezova, 1987).
Research carried out reports different methodologies to calculate the specific heat of combustion gases (Ganaphaty, 1993; Cengel, 2008; Coskun, Oktay & Ilten, 2009).
The authors of this paper used the methodology reported by Coskun et al. (2009), to calculate the specific heat of the combustion gases at the inlet and outlet of the GT and HRSGs. With the calculated values of specific heat it is then necessary to determine the enthalpy of the gases.
Data Acquisition and Processing System
After selecting the expressions to be used for determining the energy indexes of the cogeneration plant, the programming of these expressions was performed in Microsoft Excel spreadsheets in and a program designed for their interaction with the data from each of the instruments of the cogeneration plant.
The system is designed to work online and make the calculation of rates the minute. The program for data acquisition of the monitoring system in real time (Bermúdez, 2010), export to Excel, performing calculations and minute storage, were implemented by using the software tool WinCC flexible provided by SIEMENS.
The methodological procedure (Bermúdez, 2010) was as follows:
Evaluation of cogeneration to different values of electrical output, for each value of electric power are recorded several readings of the variables involved in the calculation of energy indexes. The database is subjected to statistical analysis, calculation of energy indexes selected for this research, graphic representation of the variation in indexes obtained from actual plant performance. Attainment of mathematical models corresponding to the graphs mentioned above and lastly, economic valuation.
4. RESULTS AND ANALYSIS
The research was conducted in a cogeneration plant of a company engaged in the manufacture of biaxial oriented polypropylene. Cogeneration plant shown in Figure 1. It consists of a compressor, a combustor, a GT and a pirotubular-shell type HRSGs. This HRSGs is unique in having two heat exchange sections, internally separated: one section is used to exchange heat from the gases from the GT and the other section is used to capture the heat produced by the support or conventional burner, the latter used to raise steam generating capacity of the HRSGs.
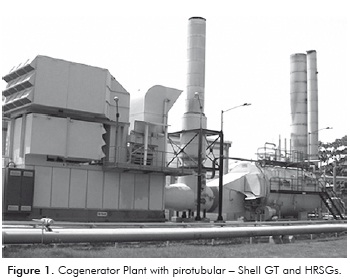
A database was developed and data was processed statistically for each of the three operation shifts. The measurement data of the variables or parameters measured in real time were: power generated kW, air temperature at the compressor inlet (°C), Generated steam pressure (bar), output gas temperature GT (°C), temperature of gas outlet of the HRSGs by the recuperator section (°C), temperature of gases outlet of the HRSGs by the burner section (°C), feed water flow temperature (°C), feedwater flow (kg/h), Generated steam flow (kg/h), consumption of natural gas (KPC corrected), gas flow at the outlet of the GT (lb/h), natural gas flow supplied to the burner (lb/h) (Bermúdez, 2010). An example of the data table in real time is shown in Table 3.
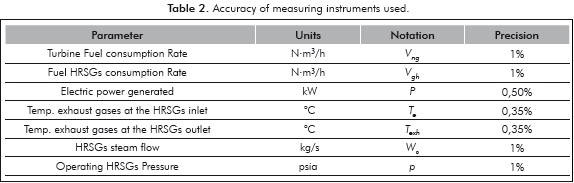
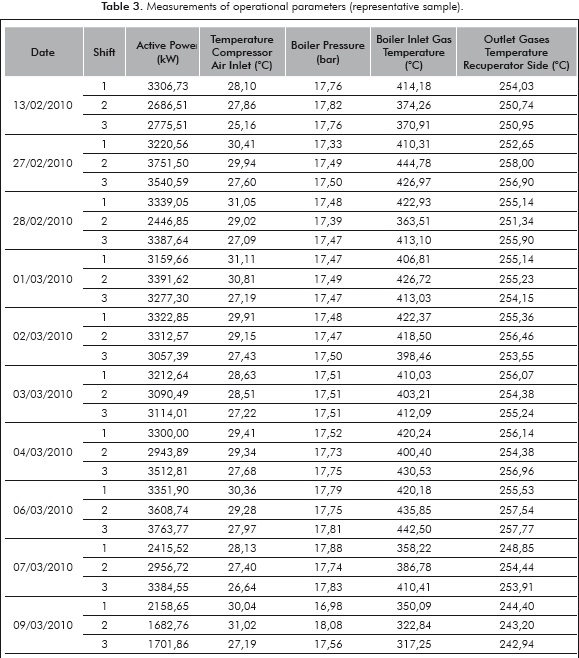
The International Organization for Standardization (ISO) established a guide for the analysis of uncertainty in measurement instruments, known as "Guide to the expression of uncertainty in measurements", which establishes the general rules for evaluating and expressing uncertainty level of an outcome in which multiple measuring elements with different accuracy levels are involved. This methodology was used in the execution of this research (Bermúdez, 2010), where an Excel spreadsheet was developed, based on the precision of measuring instruments of the cogeneration plant. This data is detailed in Table 2.
Control Charts
The data obtained and processed for real-time monitoring offers the possibility of having accurate knowledge about the variability of the process, to establish control limits for each energy index knowing the inherent variability of the process and equipment. Control charts show the behavior of the calculated parameters in a typical day.
The values that are outside the control limits show the variability of the process in real conditions and are a useful information source for technical and operations personnel to establish measures to improve efficiency, quality and competitiveness of the plant.
The results for a day of plant operation are shown below. Their statistical analysis was performed with the Minitab program.
Global Effciency and HR of Cogeneration Plant Control Charts
The control graphics of overall efficiency and HR from the cogeneration plant are presented in Figure 2a and 2b. The overall efficiency has an average of 47,98% while the HR is in the order of 7512,6 kJ/kW·h. Both indexes show a significant variability and several values that are outside the maximum and minimum limits. All this makes the case for analyzing and evaluating measures to improve the behavior of both efficiency indicators.
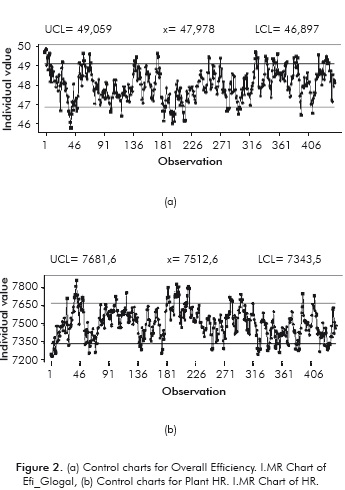
Energy Indexes: Curves and Regression Models
The main energy indexes of the evaluated cogeneration plant will now be analyzed . Figures 3; 4; 5; 6 and 7 show, in addition to the curve and the mathematical model index analyzed, prediction bands as well as confidence bands. The prediction band is a measure of the accuracy of individual values around the linear regression. The confidence band is a measure of the certainty values. It is a confidence interval on the observed data and includes the population mean. The interval is guaranteed with 95% accuracy in the average population. The term "S" is the "standard error of prediction" or the standard error around the regression line and R2 is the variability of sample data that are clarified by the prediction equation.
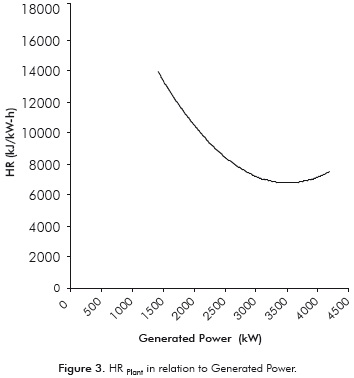
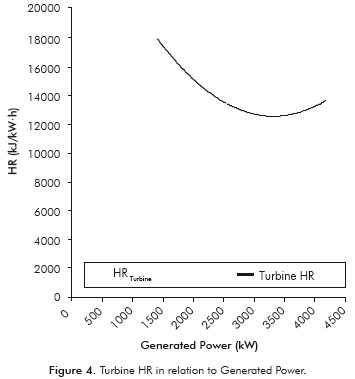
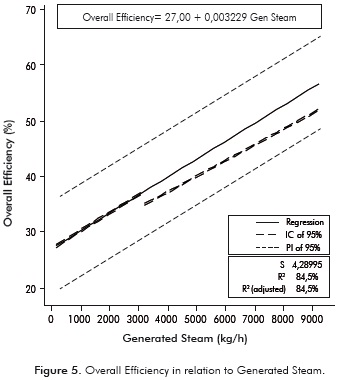
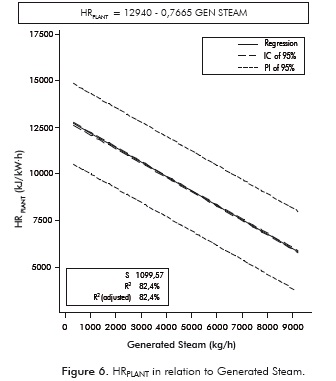
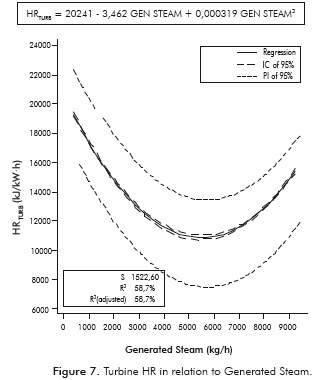
HR of the Plant in Terms of Power Generated
HR variation of the plant with the electric power generated is shown in Figure 3. As shown, the energy consumption (kJ/h) to produce 1 kW is decreasing to the extent that this power increases. The minimum HRplant values are lower than 7500 kJ/kW·h for an electrical power of about 3500 kW. In those cases where it is required to operate at values close to the plate data of the generator 4800 kW, there is an implied increase in the HR of the plant and therefore in the cost per kW generated. Similarly, operation at lower values than 3000 kW also leads to increased consumption and generation costs per kW.
The equation describing the change in the HR plant with power generated, for the current operating conditions and mechanical technical condition of the cogeneration plant with GT and HRSGs, is as follows:
HR of the GT in Relation to Power Generated
The improved performance of the GT, expressed as HR of the turbine, is obtained when the electrical output is 3400 kW, whose value corresponds to a HR of the turbine of 12500 kJ/kW·h. This is shown in Figure 4. The operating range of the GT with lower energy consumption in relation to power generated behaves similarly to the HR of the plant. Operating above or below 3500 kW, leads to an unnecessary increase in the consumption of heat in the GT and the plant, which is reflected in higher cost per kW generated and greater environmental impact.
The equation describing the change in HR of the turbine power generated for the current operating conditions and mechanical technical condition of the cogeneration plant with GT and HRSGs is as follows:
This equation having R2 = 51,1%, does not provide reliable values in predictive studies.
Overall Effciency of the Cogeneration Against Generated Steam
The overall efficiency of the cogeneration plant with GT and HRSGs varies with the amount of steam produced in the HRSGs, which is in turn related to the heat required by the production process. Figure 5 shows that increasing the generation of steam also increases the thermal efficiency of the cogeneration plant.
The regression equation that describes the overall thermal efficiency of the cogeneration plant in relation to the amount of steam produced is as follows:
Plant and Turbine HR in Relation to Amount of Generated Steam
Figure 6 shows that the HR of the plant decreases as the amount of Generated steam increases. This is a logical dependency dynamic for a cogeneration plant with GT and HRSGs. Figure 7 shows the variation of the HR of the GT when varying the amount of Generated steam. When the amount of Generated steam is in the range of 500 to 600 kg/h, RH minimum of the turbine is reached, about 11000 kJ/kW·h, and for this same range the HR of the plant is close to 900 kJ/kW·h. This means that, in the operating conditions in which the HRSGs is producing about 550 kg/h of steam every kW generated in the GT requires a minimal amount of energy (11000 kJ/kW·h)
The equation is:
The equation is :
This equation is not completely reliable due to its R2 value = 58,7%
The coefficient of determination R2 is useful to measure the overall quality of the multiple regression models. This ratio quantifies the percentage of variability in the data that is explained by the model. For forecasting purposes we recommend a coefficient of determination of at least 70%.
When R2 is less than than 70% this indicates that the effect or variability attributable to factors studied is minor compared with the rest of the variation observed in the experiment. A low R2 may be due to one or more of the following reasons: the factors studied on their own do not have enough influence to explain the observed variations in the response variable, levels of the factors studied are too narrow, so the effect on the response variable when changing from one level to another is too small, e xperimental errors and errors of measurement may also come into play as well as other factors not studied in the experiment that were not kept sufficiently fixed, so that having variations during the experiment caused a lot of experimental variation.
Caution should be taken when analyzing which of these reasons influenced in having lower coefficients of determination. The results should not be discarded and interpretations about the models inability to work should not be made. In general terms, experiments generate information that should be used to raise new conjectures and experimental studies.
HRSGs Effciency Using the Direct Method (Input -Output) and Indirect or Losses Method
The thermal efficiency of HRSGs is a useful energy index in cogeneration plants with GT and HRSGs, as they allow us to assess how the energy contained in combustion gases from the GT is being used to generate steam in the HRSGs. In this research, this index was evaluated using the two methods specified in ASTM standards. Its values are shown in Figures 8 and 9. When using the method of inputs and outputs the maximum value of the efficiency of the HRSGs will not exceed 50%, whereas, with the method of losses the maximum average a value is around 60%. There will always be a difference present in terms of efficiency of a steam generator calculated by direct balance and calculated by the method of thermal losses. The causes of the differences could be related to the errors of measuring instruments and inaccuracies in the calculation methods used.
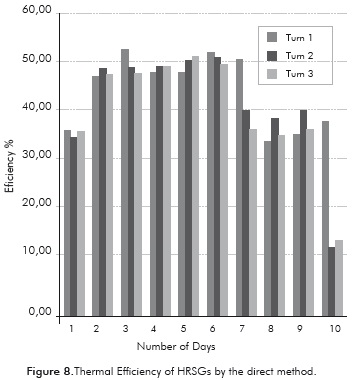
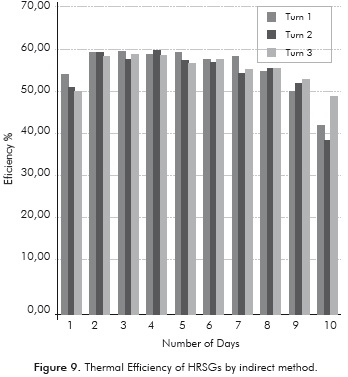
In addition to evaluating the heat losses in HRSGs this investigation also examined looked into the following question: Of the total amount of energy used in the HRSGs, which proportion corresponds to the heat content in the combustion gases from the GT and which proportion is provided by the support burners installed in the HRSGs? The results of this study provides answered that tell us that approximately 80% of the energy used in the HRSGs is from the heat contained in exhaust gases from the GT.
Economic Assessment
Tables 4 and 5 show the potential economic savings from estimates related to improving the performance of the GT and the HRSGs.
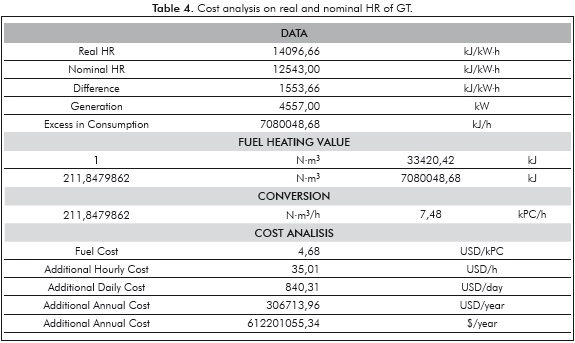
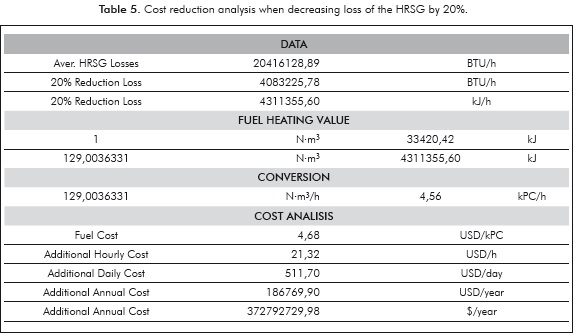
Table 4 shows that if we decrease the actual HR of the turbine to face value, it could achieve cost savings of about USD 612 million per year of operation, a value that currently appears as an additional cost of the cogeneration plant and company.
Similarly, if we apply measures to reduce 20% of current heat loss in the HRSGs, this would save USD 373 million annually. (See Table 5).
5. CONCLUSIONS
The most significant results of research conducted in the cogeneration plant with GT and HRSGs are the following :
-
Energy indexes of cogeneration plants with GT and HRSGs are: plant and turbine HR in relation to electrical power generated; plant and turbine HR in relation to depending on the amount of steam produced in the HRSGs; plant overall thermal efficiency in relation to the Generated steam in the HRSGs; thermal efficiency of the HRSGs. The values of these indicators are presented throughout the body of work.
-
The specific minimum consumption of heat for both the GT as well as the Cogeneration Plant are obtained when the generated power is maintained at about 3500 kW.
-
When the HRSGs is generating between 5000 and 6000 kg/h of steam, this corresponds to lower specific consumption in the GT.
-
Most of the mathematical models derived from this research can be used as a starting point for optimization and simulation of cogeneration plants with GT and HRSGs, making the necessary adjustments according to capacity and technical parameters of equipment that make up the cogeneration plant.
-
According to economic estimates, using adjustment measures and operational control, the implementation of the system could generate an estimated economic savings of about USD 985 million annually.
ACKNOWLEDGMENTS
Thank you to the Management Area of Biofilm S.A. located in Cartagena, for all the support and positive evaluation of the results of the research. Special appreciation to the engineers Ricardo Ricardo, Jonathan Miranda and others in the sub- maintenance area.
REFERENCES
ANSI/ASME PTC 1-2004 (R2009). General Instructions for Power Test Code. American Society of Mechanical Engi-neers / 31-Dec-2004. ISBN: 0791829227. [ Links ]
ANSI/ASME PTC 22-1997 (R2006). Performance Test Code on Gas Turbines. American Society of Mechanical Engineers / 30-May-2006. ISBN: 0791829545. [ Links ]
ANSI/ASME PTC 4.4-1981 (R1992). Gas Turbine Heat Re-covery Steam Generators. American Society of Mechanical Engineers / 01-jan-1981. ISBN: 9780791831397. [ Links ]
Balli, O., Aras, H. & Hepbasli, A. (2010). Thermodynamic and thermoeconomic analysis of a trigeneration (TRI-GEN) system with a gas-diesel machine: Part II - An application. Energy Conversion and Management, 51 (11), 2260-2271. [ Links ]
Baukal, C. E. (2000). Heat transfer in industrial combustion. New York: CRC Press LLC. [ Links ]
Bermúdez, L. F. (2010). Método para el control operacional en línea de la generación de electricidad en turbogas: Caso Biofilm S.A. planta Cartagena. Tesis de Maestría Fac. Ing. Universidad Tecnológica de Bolívar. Cartagena, Colombia, 191pp. [ Links ]
Boyce, M. (2002). Gas turbine engineering handbook. 2nd ed. Houston: Bristish library. [ Links ]
Bruno, J. Ortega, V. & Coronas, A. (2009). Integration of cooling systems into gas turbine trigeneration systems using biogás: Case study of a sewage treatment plant. Applied Energy, 86 (6), 837-847. [ Links ]
Cengel, Y. A. (2008). Termodinámica. Sexta Edición. New York: McGraww-Hill Companies. [ Links ]
Chandok, J., Kar, I. & Tuli, S. (2008). Estimation of Furnace exit Gas Temperature (FEGT) using optimized radial basis and back-propagation neural networks. Energy Conversion and Management, 49 (8), 1989-1998. [ Links ]
Coskun, C., Oktay, Z. & Ilten, N. (2009). A new approach for simplifying the calculation of flue gas specific heat and specific exergy value depending on fuel composition. Energy, 34 (11), 1898-1902. [ Links ]
Eicher, A. (2000). Calculation of combustion gas flow rate and residence time based on stack gas data. Waste Man-agement, 20 (5-6), 403-407. [ Links ]
e2 Energía Eficiente (2003). Manual de Gestión Energética Integral. Biofilm S.A., Planta Cartagena. [ Links ]
Galip, T. & Durriye, B. (2004). Thermoeconomic analysis of a trigeneration system. Applied Thermal Engineering, 24 (17-18), 2689- 2699. [ Links ]
Ganapathy, V. (1993). Applied Heat Transfer. Tulsa: Penn Well Books Company. [ Links ]
Ganapathy, V. (2003). Industrial boiler and heat recovery steam generators. New York: Marcel Dekker. [ Links ]
Garcia, G. S. & Fraile, C. D. (2008). Cogeneración-diseño operación y mantenimiento de plantas. 2nd. Ed. Madrid: Diaz Santos. [ Links ]
Horlock, J. H. (2003). Advanced Gas Turbine cycles. UK: Elsevier Science. [ Links ]
IDAE, (2008). Análisis del potencial de cogeneración de alta eficiencia en España. 2010 - 2015 - 2020. Instituto para la Diversificación y el Ahorro de Energía. [ Links ]
Kehlhofer, R. (1997). Combined - cycle gas and steam turbine power plant. Oklahoma: Penn Well. [ Links ]
Kenneth, E. & Heselton, P. E. (2005). Boiler operatos handbook. New York: The Fairmont Press. [ Links ]
Kizniezova, N. V. (1987). Cálculo térmico de agregados de calderas. Método Normativo de la Unión Sovíetica. Moscú: Energía. [ Links ]
Kyle, B. G. (1984). Chemical and process thermodynamics. Englewood Cliffs: NJ Prentice - Hall. [ Links ]
Pitanga, R., Hacon, D., Tessarollo, A. & Reis, J. (2010). Thermodynamic analysis of trigeneration systems taking into account refrigeration, heating and electricity load demands. Energy and Buildings, 42 (12), 2323-2330. [ Links ]
Sala, J. (1994). Cogeneration. Thermodynamic, technological and economic. Bilbao: Servicio Editorial Universidad del Vasco. [ Links ]
Santos, L. (1999). Tecnología de monitoreo, control, optimización y diagnostico operacional para el incremento de la eficiencia energética en centrales termoeléctricas. Tesis Doctoral, Universidad de Cienfuegos, Cienfuegos, Cuba, 186 pp. [ Links ]
Schicktanz, M., Waple, J. & Henning, H. (2011). Primary energy and economic analysis of combined heating, cooling and power systems. Energy, 36 (1), 575-585. [ Links ]
Stultz, S. C. & Kitto, J. B. (1992). Steam: Its generation and use. 40th edition. Ohio: The Babcock and Wilcox Company, Barberton. [ Links ]
Teopa, E., Picón, M. & Rodríguez, M. (2005). Thermal integration of trigeneration systems. Applied Thermal Engineering, 25 (7), 973-984. [ Links ]
Troyanovski, B. M, Filippov, G. A. & Bulkin, A. E. (1987). Turbinas de vapor y de gas de las centrales nucleoeléctricas. Moscú: Editorial Mir. [ Links ]
Yrjölä, J., Paavilainen, J. & Sillanpää, M. (2006). Modelling and experimental studies on heat transfer in the convection section of a biomass boiler. Inter., J. of Enery Reser., 30 (12), 939-953. [ Links ]
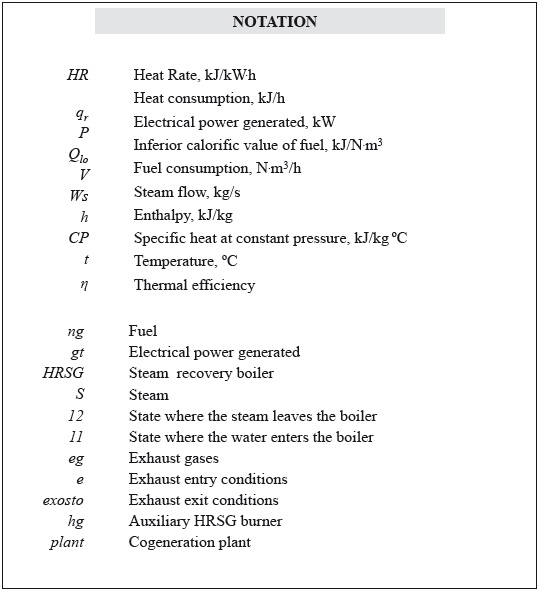