1. Introduction
Market competition is widely linked to the productive function that demands the manufacturing of trustworthy, defect-free products. This condition favors the creation of a competitive advantage [1]. Nevertheless, this cannot be disassociated from human resources. Recent studies highlight the necessity for companies to develop their employees’ creativity, recognizing them as basic units of knowledge; likewise, they indicate that it is common to employ the storm methodology and idea competition for this purpose, extending beyond Kaizen [2]. The Kaizen philosophy has its origins in Japan; it was developed after World War II and comes from the words kai (change) and zen (for the better) [3].
Lean thinking is a relevant strategy for world-class development. Although it is known as a manufacturing system, its success requires a broader vision [4]. The lean philosophy demands that the organization learn continuously, and change is common at all levels [5]. In addition, lean thinking is a technique that reduces waste, and its practice maximizes the value of production [6]. The lean system continuously challenges workers to creatively employ their talents, abilities and experience to identify waste and remove impediments so they can execute their jobs correctly, improving the process and quality control [7].
The literature recognizes that there are gaps in the research of lean environments, particularly in the exploration of their impact on social development and how motivation is linked [8]. In this vein, [9] remark that an effective transformation in a lean implementation process requires an understanding of the socio-technical system. The research scarcity is due to a primary focus on the sustainability of the technical system’s results achieved through the implementation of a Kaizen event, with few studies considering the social system’s results [10]. Many companies fail when implementing a sustainable lean production system if they view the manufacturing area as a solely technical system [11], and do not realize that the improvements achieved through Kaizen events occur in both the technical (improved cycle times) and social systems (positive changes in ability, knowledge, and employee attitudes) [12].
Lean manufacturing is applied not only in the automotive industry but also in the electronics, aeronautical, ceramics, and furniture fabrication areas, to name a few [8]. In this research, we focused on a Mexican manufacturer of exported goods located in Ciudad Juárez, Chihuahua. This company has a lean manufacturing environment, manufacturing items for the telecommunications industry. We investigated four variables relevant to the company’s socio-technical system: the impact of abilities developed during Kaizen, the employee’s attitude toward work, motivation, and the impact on the work area. We organized this article in four sections. The first section presents the theoretical concepts that sustain the developed work together with the hypotheses. The second shows the method, instrument operationalization, and the reliability and validity of the measurement model. The third section presents the descriptive results of the structural equation model. Finally, we present the results and conclusions of this work.
Lean and Kaizen are useful techniques in organizational contexts. Lean is a manufacturing philosophy that reduces the wait time between the client’s order and the delivery of all required services and parts through an overall minimization of waste [13]. One of its principal concepts is a bottom-up strategy, which asks workers to be continuously involved in the identification of waste sources. In addition to this, workers formulate suggestions to eliminate said sources employing their creativity in diverse ways, such as through their participation in Kaizen events [7]. A Kaizen event is a project focused on structured improvement (an interdisciplinary team is dedicated to improve specific work areas, with defined goals, in an accelerated timeframe (<1 week-)), characterized by several traits, including a low capital investment, an orientation to action and autonomy, and an application of tools for the establishment of quality and process analyses [10,14,15]. This type of event can generate improvement in both social and technical systems [16]. With respect to the former, the theory of human capital affirms that people have abilities, experience and knowledge; these traits possess an economic value for companies [17,18]. In particular, the Kaizen approach requires that employees focus on process quality and efficiency [19]. Thus, the success of continuous improvement processes depends on the potential of the members in the organization [20]. Consequently, it is expected that Kaizen teams will develop both continuous improvement as well as internal process abilities [21], benefiting from the interaction and the integration of accumulated abilities from the organizational knowledge [22].
The development of employees’ abilities is crucial for lean systems [15] because teams must function optimally regarding performance, effectiveness, knowledge and members’ attitudes [15,23]. Cheser [24] affirms that Kaizen culture generates a positive change in employees’ attitudes. In accordance to this, we consider the following hypothesis:
H1: The abilities obtained from Kaizen positively influence worker’s attitudes toward their job.
Lean, Kaizen and human resource (HR) management are related. First, in HR management models, abilities, motivation and opportunities are relevant investments; it is a requirement that employees respond positively to these variables for the success of lean production systems [25], in addition to maintaining an adequate balance when sustaining motivation [26]. Second, a previous work affirms that motivation will increase because the Kaizen training affects employee knowledge and abilities [24]. Third, the Kaizen methodology is a useful method to increase workers’ motivation in the company, favoring teamwork and teaching its members to work in a systematic and ordered manner [27], a key factor to improve the firm’s performance [28]. It is important to say that long-term investments are required to obtain a larger contribution from the labor force and to reinforce interest when securing the firm’s success [26].
Motivation studies can be categorized as pertaining to need, cognitive or reinforcement theories [29]. This research follows the cognitive perspective, based in expectations and tendencies to act in a certain manner, resulting from both intrinsic necessities as well as experiences and interactions with the environment [30]. Furthermore, applied research studies regarding the application of Kaizen in Mexican manufacturers [31,32] have shown a significant impact of diverse variables upon employee motivation. Likewise, [31,33,34] point to motivation as one of the key success factors in Kaizen implementation. Additionally, enthusiasm and persistence in performing the organization’s tasks [35] are factors related to motivation. Based on the above statements, we can propose the following:
H2: The abilities developed during Kaizen events positively influence workers’ motivation
The basis of Kaizen philosophy stems from the participation of individuals from all areas and processes of an organization. Its purpose is to work on achieving gradual improvements for individual [36] and overall work areas [20]. The abilities obtained from the efforts to permeate a Kaizen culture produce an impact on activities, processes and work areas, improving performance, the work environment and teamwork [14]. Additionally, the success of a Kaizen strategy depends upon human effort to optimize work area results through process improvement [36]. The impact on the work area is a construct utilized in previous research works developed in Kaizen environments [14] and refers to the perceptions of the impact of Kaizen activities on the work environment. Based on the above, we can state the following:
H3: The abilities developed in Kaizen environments have a positive influence on the work area impact.
On the other hand, Kaizen events can result in a change of attitude toward work life, transforming employees’ mentality [37]. For this reason, Kaizen must be seen as a philosophy or an attitude rather than a specific technique [18]. A relevant factor that influences its successful implementation is that of the organization’s attitude towards mistakes, starting with recognizing the necessity of improvement [38,39]. Employees’ attitudes can increase motivation, enthusiasm and commitment, contributing to the program’s success and stimulating the participation in future activities [15,40]. Recently, [41] shows that some organizations fail when motivating employees’ participation in Kaizen activities due to the absence of compensation and rewards, inadequate resources, and delays when applying suggestions. Owing to this, the following is proposed: H4: Employee attitude towards work influences motivation.
Additionally, motivation systems affect the success of philosophies such as Kaizen and thus play an important role in the improvement of manufacturing system performance [42]. This has implications in both technical and social environments, as the employees (when trained continuously) are capable of making better decisions in their personal environment, finding meaning in their work tasks, and influencing the performance of the work area [43]. The assessment of the influence of Kaizen upon a work area requires an evaluation of the perception of the activity’s impact upon the work environment [14]. Due to this, we can expect that organizations will encourage improvements in the work area through strong, long-term motivation strategies for employees [26]. Thus, it is possible to expect the following:
H5: Motivation affects the work area in a positive manner.
2. Materials and methods
We designed a quantitative investigation. The investigation has an explanatory, empirical and cross-sectional design, based on a literature review focused on the following variables: employees’ attitude towards their job, motivation, abilities developed during a Kaizen event, and the impact on the work area. We employ a deliberate, non-probabilistic sampling because we performed the research in a company with a lean-kaizen manufacturing environment. This company performs Kaizen events in accordance with requirements related to the solution of specific issues. The company was chosen because they had performed Kaizen activities for more than a year (prior to the start of this research), had utilized Kaizen in a systematic manner, and had practiced Kaizen events in a frequent manner (at least once a month). The firm is a large-scale export manufacturing company focused on the fabrication of items used in the telecommunications industry, producing fiber-optic components used for the connection and protection of data flow in many commercial brands. We do not reveal the name of the company due to confidentiality issues.
We performed a self-conducted poll to collect information in a work context. The sample consisted of workers that had participated in Kaizen events. The sample was non-probabilistic and a sampling for convenience was performed (this type of sampling depends on the researchers’ choices as a function of the research characteristics and is not calculated with probabilistic formulas [44]) in accordance with the allowed access. The poll included items with a Likert-type format (the participants were asked to express their degree of agreement with the statements), in five answer categories, where 1 means “disagree completely” and 5 means “agree completely”. We had 100 participants.
Both the employees’ attitude towards work and motivation variables were measured with scales proposed by [45], composed of 8 and 3 items. Both scales were constructed by considering content validity through experts in several disciplines, exploratory factorial analysis and internal consistency.
On the other hand, the variables abilities developed during Kaizen events and impact on the work area have been evaluated with 5 items in a scale proposed by [14]. In the case of these variables, the authors indicate that the items measure participants’ perception of their new abilities obtained due to their involvement in Kaizen activities and of the impact that these activities have in the work area. In addition, the scales report a good indication of internal reliability and were developed with the objective of being applied in environments where Kaizen events are performed. We present the items of each of these variables in Table 1.
Table 1 Operationalization of the latent variables used in the measurement model
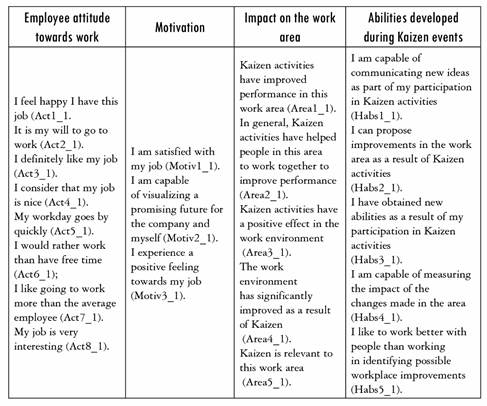
Source: Authors' own elaboration
We used structural equation modeling employing Partial Least Squares (PLS) as a technique of statistical analysis, considered useful for path models employing indirectly measured latent variables [46]. The technique is a multivariate statistical analysis method that allows for the establishment of an effect between exogenous and endogenous variables whose causal relationships are established with a theoretical basis [47]. The employed statistical software is Smart PLS3.0. We performed the structural modeling process in two stages. As the measurement of latent variables is a prerequisite to the analysis of causal relationships between theoretical constructs [48], we revised the external measurement model to ensure reliability and validity in the first stage. In the second stage, we validated the internal structural model.
Reliability and validity of the measurement model
Initially, the measurement model had 21 items. Based on the PLS algorithm’s results, two items were removed (Motiv 1_1 and Act1_1). These variables resulted in issues of discriminant validity. Thus, the final measurement model had 19 observable variables. In the model, the employee attitude towards work variable is measured with 7 items (Act2_1, Act3_1, Act4_1, Act5_1, Act6_1, Act7_1, Act8_1); Motivation is measured by 2 items (Motiv2_1, Motiv3_1); the abilities developed in Kaizen events is measured by 5 items (Habs1_1, Habs 2_1, Habs3_1, Habs4_1, Habs5_1). Finally, impact in the work area is measured by 5 items (Area1_1, Area2_1, Area3_1, Area4_1, Area5_1).
The items’ factorial loads range between 0.554 and 0.922, with a t-value of more than 1.96 for all cases (resulting in statistical relevance with a confidence interval of 95%). Likewise, the magnitude of both the loads and the Average Variance Extracted (AVE) is more than the critical point (0.50). We can affirm that 50% or more of the indicator’s variance is included in the corresponding construct [49-51]. Finally, the internal consistency indexes of all latent variables presented acceptable indicators. In all cases, these indexes exceed the recommended values (0.70 for Cronbach’s alpha, and 0.60 for the composite reliability (CR) index) [49] (see Table 2).
Diverse criteria exist to evaluate discriminant validity. We calculated the AVE and the Heterotrait-Monotrait Ratio (HTMT) indicators in this research work. According to the AVE criteria, discriminant validity exists when the square root of the AVE is larger than the correlation of any of the other latent variables included in the model [50,51]. In Table 3, we present these values: the diagonal shows the square root of each construct’s AVE. The corresponding correlations are shown under the diagonal. As seen in the table, in all cases the value of the diagonal exceeds the value of the correlations between constructs, evidence that discriminant validity exists according to this criterion.
Table 3 Discriminant validity according to the Average Variance Extracted criterion
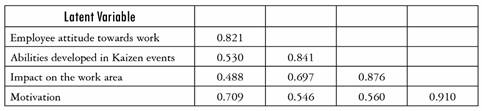
Source: Authors' own elaboration
On the other hand, the HTMT indicator of the correlations calculates the average of the correlations’ heterotrait-heteromethod (correlations between indicators that measure different constructs) [52]. Discriminant validity can be established as a criterion or as a statistical proof. This work analyzes the discriminant validity with a basis in the first choice (as a criterion). To determine the discriminant validity, we choose a comparison point (usually 0.85 or 0.9) and we compared it to the Heterotrait-Monotrait ratios: discriminant validity exists when the HTMT are lower than the established comparison point (in this case, this point was chosen as 0.85). Table 4 shows the comparison point exceeds all the cases, evidence that discriminant validity exists according to this indicator.
3. Results
This section presents some of the statistical data describing the participants. We must note that not all participants completed this section of the questionnaire: for gender, only 96 answered; for the remaining demographic variables, we report the information for only 98 participants. The results show that 75% of the participants are men, and 51% of the participants had completed a university degree. Additionally, 60% of the participants are in the age range of 31-50. With respect to job position, 32% work in management roles, and 25% of them are engineers. Finally, 49% indicate they have worked at the company for more than 8 years (See Table 5).
Validation of the structural method
To evaluate the prediction quality of a structural PLS model, it is recommended to employ the coefficient of determination (R2) and path values. With respect to the former, literature indicates this parameter establishes the degree to which the model explains the data [50]. With respect to its magnitude, a R2 value of 0.67 is substantial, a R2 value of 0.35 is moderate and a R2 value of 0.19 is weak [53,54]. Thus, the obtained results indicate that in a weak-moderate capacity, the ‘employee attitude towards work’ variable (R2 = 0.280) is explained by the ‘abilities developed in Kaizen events’ variable. On the other hand, empirical evidence indicates that the ‘employee motivation’ variable (R2 = 0.543) is predicted in a moderate-substantial manner by both the ‘employee attitude towards work’ and ‘abilities developed during Kaizen events’ variables. Finally, the results show that the ‘impact on the work area’ (R2 = 0.532) variable is explained in a moderate-substantial manner by the ‘motivation’ and ‘abilities developed during Kaizen events’ variables.
It is necessary to assess the algebraic sign, magnitude and significance term of the path values; when the path indicators coincide with the established postulates, there is a partial empirical validation of the proposed theoretical relationships in the model [54]. In this work, the structural path values coincide with the established postulates. They are statistically significant (t-values of more than 1.96 with a confidence interval of 95%) and exceed the minimum established point of 0.20 [53]. Thus, we do not reject any of the proposed hypotheses (see Table 6).
Table 6 Proposed structural relationships in the model
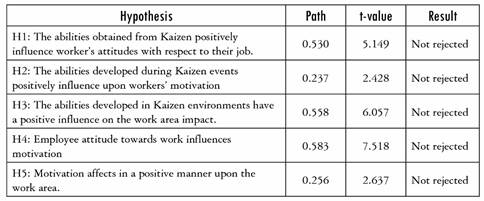
Source: Authors' own elaboration, based on Smart PLS results
Figure 1 shows the compared model. The figure presents the factorial load values of each of the observable variables, the path values of the structural relationships, and the corresponding R2 values.
4. Conclusions
Lean manufacturing is a relevant technique with both social and technical effects. This research work investigates both of these aspects in the context of a Mexican manufacturer of exported electronic goods, where Kaizen events are common. The results show that there is a synergy between the studied variables.
First, the evidence indicates that the abilities developed during Kaizen events variable favorably influences the employees’ attitude towards work variable. This coincides with the results of previous research [12,15,24]. In this company, employees perceive their job as interesting, affirm it is their own will to go to work and have a greater appreciation for their job compared to the average worker. It must be mentioned that attitude is considered as a relevant aspect for the success of Kaizen because it facilitates the collaboration between the team and the members of the organization [55]. In this sense, a recent work [56] considers that this philosophy of Japanese thinking promotes attitudes and behaviors that improve workplaces and processes while reinforcing deep learning and a cultural code unusual in the West. For the organization studied, it was observed that employees developed new abilities as a result of Kaizen events and are thus capable of proposing improvements, measuring the impact of their changes, and identifying opportunity areas with their coworkers. It is possible to affirm that the empirical evidence of this work coincides with theoretical affirmations.
Second, the results indicate that the abilities developed during Kaizen events variable influences the motivation variable, positively affecting the impact on the work area. These results are promising because literature [15,21] affirms that these relationships are critical due to their contribution in aspects such as continuous improvement, efficiency and effectiveness of internal processes. They also increase organizational knowledge. At the structural level, it must be highlighted that there is a strong relationship between the abilities developed during Kaizen events and the impact on the work area variables. This is because employees that have collaborated in Kaizen events believe there are significant improvements in aspects such as processes, work environment and teamwork. That is, there is an agreement with past results [14,36] that suggest employees perceive positive results that impact the optimization of the work area. From the employees’ perception, the work area has better performance, achieved through cooperation, in an enhanced work environment.
Third, evidence indicates that the abilities developed during Kaizen events variable impacts the motivation variable. This matches previous studies that have evaluated the effect of this variable on social constructs in Kaizen. Thus, it is possible to affirm that the development of new abilities in Kaizen events both contributes to the efficiency and the success of the continuous improvement processes, as well as increases the employees’ intrinsic motivation [15,26]. In this Mexican manufacturer, workers stated they visualize a promising future for themselves and for the company, and they have favorable feelings toward their job. The empirical findings also coincide with the approaches taken by several authors [15,40], who state that employees’ attitudes towards work have strong positive effects on their motivation, favoring the success of the program and inciting future participation. In a specific manner, recent work in the Latin American context has found that motivation is a relevant factor in process improvement through the implementation of Kaizen in Brazilian [1] and Mexican [31,32] manufacturers. The results of this work add to this evidence.
Finally, in this analysis of synergistic relationships, our findings indicate that a worker’s motivation favorably influences the work area. That is, for this Mexican manufacturer, the greater the workers’ motivation, the better results are obtained in the work area. With respect to this, [57] affirms that in Kaizen environments, motivation is the variable with the largest impact on work per formance, especially related to work area tasks, and it is suggested that it can compensate for lack of experience and abilities.
As in similar research, this effort has limitations. Among these is the fact that we performed the study at a single company with a non-probabilistic employee sample. From the temporality perspective, we used a cross-sectional design, reducing the possibility of result generalization. We must also highlight that we measured motivation with a small item scale, limiting its assessment. For future studies, due to its logical relationship, we recommend assessing the impact of the employee attitude towards work variable on the impact on the work area variable. In addition, it would be useful to analyze the effect of the studied variables on the productivity and profitability of organizations with a Kaizen environment. Finally, we recommend replicating this research work in a different context and sector, ensuring that the chosen analysis subject had performed Kaizen events for a certain time range.