1. Introducción
La eficiencia energética juega un papel fundamental en cualquier proceso industrial. La agroindustria asociada a la producción de azúcar y sus derivados no es la excepción, y hoy por hoy, además de los productos típicamente comercializados, la generación de energía eléctrica para consumo interno y comercialización de excedentes ha entrado a jugar un papel importante como producto derivado de esta agroindustria. Es así como cualquier iniciativa conducente a un mejor uso del vapor en los procesos de fábrica, trae consigo un aumento en la eficiencia productiva de esta, y con ello excedentes de vapor que pueden ser empleados en la generación de electricidad.
En relación con lo anterior, Sanz & Burbano (1) en el año 2014 realizaron un análisis y optimización exergética de una planta de cogeneración utilizada en la industria azucarera con el fin de maximizar la potencia eléctrica. Los resultados permitieron determinar que, para los esquemas de cogeneración de los casos estudiados, la destrucción de exergía se presenta en su mayor parte durante la combustión del bagazo empleado para la generación de vapor, y que la configuración de los equipos utilizados en el sistema convencional (turbinas de baja eficiencia, válvulas reductoras de vapor y termocompresores) reducen la capacidad de generar energía eléctrica, ya que, esta configuración está dirigida primordialmente a suplir la demanda de vapor al proceso. Por otra parte, determinó que para maximizar la potencia eléctrica útil generada y la eficiencia exergética del ciclo, se debe incrementar la presión y temperatura de vapor durante la generación de este, implementando un esquema de cogeneración de contrapresión-condensación.
Por otra parte, Rein (2) , presenta aspectos prácticos del diseño y operación de los molinos y el proceso de extracción del jugo y la posterior cristalización del azúcar. Asimismo, expone los procesos asociados a la utilización del vapor para generación eléctrica, el tratamiento de los subproductos del proceso de obtención de azúcar (cachaza, bagazo, hojas y puntas de la caña) para la producción de etanol, entre otras aplicaciones. Por otra parte, el estudio permite identificar el número de evaporadores que deben utilizarse dependiendo de la capacidad de la planta, describe ventajas y desventajas de las tecnologías presentes en el mercado, así como, el diseño y condiciones de operación de estos.
También, Lora et al. (3) , realizaron una discusión de los cambios tecnológicos relacionados con la implementación de la cogeneración a gran escala y la producción de biocombustibles en la industria del azúcar y el alcohol. La discusión abarca temas como la reducción del consumo de vapor de proceso, la implementación de nuevas alternativas en los molinos impulsores, la práctica generalizada del uso de altos parámetros de vapor en las instalaciones de cogeneración, la inserción de nuevas tecnologías para la producción de biocombustibles (hidrólisis y gasificación), la conversión energética de residuos de la caña de azúcar y de la vinaza, entre otros. El estudio concluye que el desarrollo tecnológico de la industria azucarera permitirá la integración de nuevos productos y subproductos como bioetanol celulósico, metanol y biobutanol, entre otros. Asimismo, se reducirá el desperdicio de la materia prima y permitirá el incremento en la producción de energía eléctrica.
De Souza-Santos et al. (4) , realizaron un estudio para determinar la mejor configuración para el proceso de generación de energía eléctrica a partir del vapor generado por el bagazo de caña, con el fin de mejorar la eficiencia de la planta. Los resultados les permitieron concluir que, el uso de calderas supercríticas proporciona una gran flexibilidad para la generación de energía y vapor para los procesos que requieren las unidades de azúcar y alcohol. Además, la modernización de los sistemas tradicionales permitiría el uso de bagazo húmedo extraído directamente del molino y generaría una disminución asociada a los costos en sistemas de alimentación en cascada.
Amezcua-Allieri et al. (5) , realizaron un análisis comparativo desde los enfoques tecnoeconómico y de ciclo de vida de un proceso de producción de azúcar empleando el fuel oil o el bagazo de caña de azúcar para la cogeneración energética de un ingenio azucarero ubicado en el sur de México. A partir de los resultados concluyeron que, existe una gran ventaja en el uso del bagazo como combustible sólido, ya que el costo de producción de energía en forma de vapor y electricidad es menor en comparación con el fuel oil. Asimismo, determinaron que, es importante encontrar técnicas agrícolas alternativas que utilicen menos pesticidas y fertilizantes, además de implementar un mejor sistema de tratamiento de agua y considerar el uso de bagazo con un menor porcentaje de humedad, con el fin de mejorar el desempeño ambiental y económico.
Mkwananzi et al. (6) , determinaron indicadores y parámetros energético para el consumo de energía de un ingenio azucarero convencional en función de las actividades de las unidades del proceso. Para la evaluación del estudio realizaron una simulación en MATLAB del balance de masa y energía de un ingenio azucarero genérico con un rendimiento de caña de 250 toneladas por hora y un consumo de 400 kg de vapor por tonelada de caña molida (kgvapor/TCM). A partir de los resultados los autores concluyeron que, un aumento del 28% en el reciclaje de masa cocida, tiene un incremento significativo del 5.5% en el indicador de energía de la unidad de evaporación en comparación con el 2% para el indicador de energía de la unidad de cristalización. Asimismo, el incremento del flujo de vapor del efecto final al condensador representa una oportunidad adicional de ahorro de energía que se puede lograr mejorando la configuración de los evaporadores, y reconfigurando las purgas de vapor.
Khoodaruth (7) , investigó la reducción del consumo de vapor de un evaporador de efecto múltiple agregando un efecto del tipo de evaporador de película delgada descendente. Los resultados mostraron que la integración del evaporador genera un ahorro de 41.5 kgvapor/TCM por cada hora de operación. Esta cantidad de vapor ahorrado será utilizada por plantas de cogeneración para producir una cantidad adicional de 18 GWh de electricidad al año.
Igualmente, Voigt et al. (8) , analizaron y discutieron las tecnologías de evaporadores modulares utilizados comúnmente en la industria azucarera, describiendo las ventajas y desventajas de las mismas y señalando las principales diferencias respecto a los evaporadores utilizados convencionalmente. A partir de la discusión, los autores determinaron que las innovaciones en los equipos de proceso no son comunes en la industria azucarera. Sin embargo, el entorno cambiante en el que opera la industria ocasionalmente promueve nuevos diseños, y el evaporador modular es un ejemplo de tal innovación. Este concepto permite que el área de la superficie de calentamiento de los evaporadores existentes aumente de manera relativamente económica y proporciona un funcionamiento continuo del evaporador que evita un tiempo de limpieza improductivo.
Moller et al. (9) , realizaron una modificación en el sistema de evaporación de un ingenio azucarero con el fin de incrementar la temperatura de vapor a través de la unidad para suministrar mayor cantidad de vapor. Los resultados les permitieron concluir que, la operación del evaporador presenta pequeñas diferencias de temperatura en el vapor a través de la unidad, y la capacidad de suministrar vapor a 190 kPa-abs permite potenciales mejoras en diferentes problemas operativos y de control de la fábrica.
Considerando lo anterior, el Ingenio Risaralda, desde el año 2017, identificó condiciones de mejora energética en el proceso de elaboración de azúcar, pues el vapor no era utilizado de una manera adecuada. Por un lado, se tenía una limitante tecnológica en los equipos instalados para el proceso productivo, los cuales no cumplían con las condiciones adecuadas de rendimiento que requería la planta. Adicional a esto, el área de transferencia de calor en el proceso de evaporación no permitía configurar las extracciones de vapor con un esquema apropiado desde el punto de vista energético, perdiendo la oportunidad de usar vapores vegetales producidos durante la evaporación del jugo de caña y de baja presión en las etapas de calentamiento de jugo, cristalización y secado. Estas condiciones anteriormente mencionadas generaban el gasto de 1,450 lbmvapor/TCM [657.6 kgvapor/TCM].
El presente artículo presenta los resultados de las mejoras implementadas por el ingenio Risaralda para dar solución a la problemática aquí indicada. Se propuso mejorar la eficiencia energética en el proceso de elaboración de azúcar a través del rediseño en sus etapas, la instalación, validación y puesta en marcha de equipos de mayor eficiencia energética, además de la utilización de sistemas de control, con el fin de obtener un ahorro en el consumo de vapor, disminuir los costos de producción y mejorar la producción de excedentes de energía eléctrica. Para cumplir con este propósito, a partir del año 2017 se desarrolló el proyecto de innovación titulado: Economía de vapor en el proceso de elaboración de azúcar del Ingenio Risaralda. Mediante la ejecución de este proyecto se logró llegar a un consumo de vapor de 1,172 lbmvapor/TCM [531.5 kgvapor/TCM], pudiendo de esa forma emplear el vapor ahorrado para la producción de energía eléctrica para venta como excedentes hasta 121.5 GWh en el año 2020.
1.1. Descripción del proceso industrial
El Ingenio Risaralda S.A. es una empresa agroindustrial y de alimentos con más de 40 años de experiencia en el mercado, se encuentra ubicada en Colombia en el municipio de Balboa, Risaralda. El Ingenio se caracteriza por ser una empresa altamente innovadora y con productos amoldados a las necesidades de sus clientes. Actualmente ofrece entre sus productos:
Elaboración de azúcar moscabado, blanco corriente, blanco especial, refinado y micro pulverizado.
Alcohol carburante, el cual se elabora a partir de las etapas de fermentación, destilación y deshidratación por tamices moleculares.
Compostaje, el cual es un proceso de descomposición de la materia orgánica, mediante el cual se obtiene un producto benéfico para los suelos.
Energía eléctrica proveniente de su propia central de generación, esta última producida con turbogeneradores, que son movidos por turbinas de vapor a alta presión.
Durante el año 2020 el Ingenio Risaralda procesó 1.58 millones de toneladas de caña, lo cual le permitió producir 161.6 mil toneladas de azúcar, 25.4 millones de litros de alcohol carburante, 19 mil toneladas de abono orgánico y una producción de excedentes de energía eléctrica a la red de 121.6 GWh. El bagazo de caña, generado en el proceso, se emplea como combustible para generar vapor de alta presión y temperatura en un generador de vapor con una capacidad de producción de 159 toneladas por hora. El vapor generado es distribuido para algunos de los procesos productivos del ingenio y para generar energía eléctrica en tres turbogeneradores. La energía eléctrica producida se usa para el consumo interno del ingenio, y los excedentes de esta son vendidos a la red eléctrica nacional.
El 54.5% de la energía térmica que contiene el vapor es usada en la planta de elaboración de azúcar que se subdivide en las siguientes etapas: calentamiento del jugo, purificación del jugo, evaporación, cristalización, centrifugación y secado. La Figura 1 muestra el diagrama de distribución y uso del vapor en la fábrica de azúcar antes del año 2017.
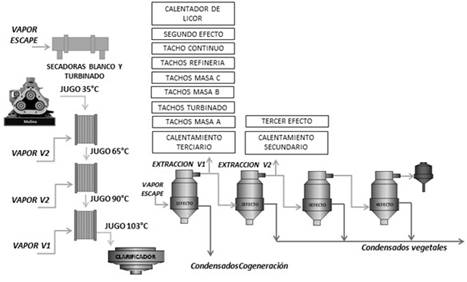
Fuente: elaboración propia
Figura 1 Diagrama de distribución y uso del vapor en la fábrica de azúcar antes del proceso de mejoramiento realizado.
La caña se recibe en el patio y se conduce por medio de transportadores a la etapa de preparación, la cual se encarga de abrir la caña en pequeñas fibras para facilitar el proceso de extracción de jugo en los molinos. En esta etapa, utilizando la presión ejercida por rodillos dentados, se logra la extracción del jugo de la caña. El jugo de caña que es extraído se conduce por medio de bombas tipo centrífugo hacia el proceso de purificación, que consta de las etapas de calentamiento, alcalización, clarificación y filtración. Por medio de estas operaciones los insumos tales como la lechada de cal y floculante forman puentes con las impurezas contenidas en el jugo, creando moléculas pesadas que se sedimentan en los clarificadores. Estos sedimentos se envían a los filtros rotatorios donde se recupera la sacarosa remanente y luego la torta resultante es enviada a la planta de compostaje para la elaboración de mejoradores de suelo. Posteriormente el jugo se somete a un proceso de evaporación en serie, en un arreglo tal que puede variar de cuádruple a quíntuple efecto. En estas etapas sucesivas de evaporación, se elimina gran parte del agua contenida en el jugo (alrededor del 80%), resultando un líquido más denso llamado meladura.
La meladura se alimenta hacia equipos de cristalización operados a presión de vacío (tachos), donde se realiza la cristalización de la sacarosa. Al tacho se introducen núcleos de sacarosa previamente formados, de tamaño homogéneo, para lograr un crecimiento de cristales de azúcar de manera uniforme. Una vez obtenidos los cristales del tamaño y pureza deseados el producto obtenido es llamado masa cocida, el cual es enviado hacia las centrifugas. Las centrífugas giran a velocidades mayores a 1000 revoluciones por minuto, obteniendo una separación de la capa de miel que rodea al cristal de azúcar. El cristal libre de miel es transportado a las secadoras de azúcar, equipos que permiten el contacto del azúcar con aire caliente desde un extremo del tambor para eliminar la humedad ligada al cristal y a su vez permitir el contacto con aire frio desde el otro tambor para el acondicionamiento térmico de los cristales. El azúcar seco se envía hacia silos de enfriamiento a través de un transportador de banda y elevadores para su empacado final.
A partir del 2015 el Ingenio Risaralda S.A aumentó su venta de excedentes de energía eléctrica, pasando de 2.5 a 16.4 MWh con la instalación de un generador de vapor de alta presión el cual, en condición nominal genera 159 toneladas por hora [t/h] de vapor @ 950 psig [6.55 MPa] y 505°C [778 K] y un conjunto de turbogeneradores de alta eficiencia, combinando sistemas de contrapresión y extracción-condensación. Esta mejora en el proceso trajo consigo grandes retos en materia de gestión energética, haciendo imperativo optimizar el uso de vapor en la fábrica de azúcar para aprovechar la energía ahorrada y entregarla como excedentes a la red nacional.
2. Metodología
Para alcanzar el objetivo propuesto en el proyecto se ejecutaron 5 etapas, las cuales abarcaron cambios en los procesos de: calentamiento del jugo, evaporación del jugo, cristalización y secado. El proceso productivo de azúcar se reconfiguró en todas sus fases, pasando de una distribución del uso del vapor como se indica en la Figura 1 a la distribución mostrada en la Figura 2. Para llegar a la nueva configuración del proceso y lograr la reducción esperada en el uso del vapor de agua el proyecto se desarrolló en 4 etapas, así:
2.1. Rediseño del proceso de calentamiento primario de jugo crudo
Se realizó la instalación y puesta en marcha de un intercambiador de calor el cual usa los condensados vegetales del proceso productivo para precalentar el jugo crudo. Esto permitió dividir la etapa de calentamiento primario del jugo crudo en dos fases. La primera utiliza la energía disponible en los condensados vegetales los cuales antes de la ejecución del proyecto eran vertidos a la piscina de enfriamiento. La segunda aprovecha la energía del vapor vegetal proveniente del tercer efecto de evaporación. De esta forma en el proceso de calentamiento primario se incrementó el área de transferencia en casi tres veces y se garantizó el perfil de temperatura requerido en esta etapa, calentando el jugo crudo desde 35°C hasta 75°C.
2.2. Incremento del perfil de temperatura en el jugo claro alimentado al primer efecto de evaporación
Se instalaron y pusieron en marcha un conjunto de intercambiadores de calor para aumentar la temperatura del jugo claro desde 93°C hasta 115°C. En esta fase se logró una reducción del 50% en el tiempo de residencia del jugo en el primer efecto de evaporación y un aprovechamiento del 100% del área de transferencia de calor disponible en el proceso de evaporación de jugo. En el esquema de operación indicado en la Figura 1, que muestra el proceso antes de la intervención realizada con el proyecto, el tiempo de residencia y el área utilizada en la evaporación del primer efecto correspondían a 10 minutos y 75% del área, respectivamente. En la Figura 2 se indica el esquema de operación mejorado con la instalación de los calentadores de jugo claro.
2.3. Rediseño del área de transferencia de calor del tándem de evaporación
Mediante la instalación y puesta en marcha de un evaporador modular tipo Kestner se incrementó en 29.9% el área total de transferencia lo que permitió la redistribución de los usos del vapor vegetal en los procesos de cristalización y secado.
2.4. Reconfiguración de los usos de vapor vegetal para los procesos de cristalización de masa cocida y secado de azúcar húmedo, en las unidades de producción de casa de crudo y refinería
En esta fase se modificó la alimentación de vapor hacia los tachos de masa A, B y C, las secadoras de azúcar blanco, crudo y refinado; pasando de usar vapor de mayor energía como el vapor de escape y vapor vegetal proveniente del primer efecto de evaporación al uso de vapores vegetales del segundo y tercer efecto de evaporación, como se indica en la Figura 2.
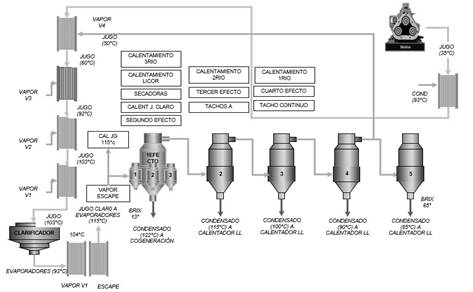
Fuente: elaboración propia
Figura 2 Diagrama de distribución y uso del vapor en la fábrica de azúcar después del proceso de mejoramiento de uso del vapor.
La valoración de esta reconfiguración se realizó siguiendo el principio de Norbert Rillieux establece que las extracciones que se realizan en el tándem de evaporación generan un ahorro directo en el consumo de vapor de escape igual a la cantidad de vapor usado divido entre el número de efectos y multiplicado por la posición de la extracción. En la Ec.1, se indica el cálculo de ahorro de vapor según el principio de Rillieux
donde 𝑖 representa la posición de la extracción de vapor, y 𝑛: número de efectos del tándem de evaporación.
3. Resultados
3.1. Rediseño del proceso de calentamiento primario de jugo crudo
Con la instalación y puesta en marcha del calentador de jugo líquido-líquido se incrementó en 15°C la temperatura del jugo crudo proveniente de la molienda y una reducción aproximada en el consumo específico de vapor de 80.3 lbmvapor/TCM [36.4 kgvapor/TCM]. Con lo anterior se logró recuperar la energía contenida en 1,434 t/día de condensado vegetal y una reducción de la temperatura en el condensado vertido de 96 °C a 40 °C. En la Tabla 1 se indican los datos de operación del proceso antes y después de la instalación de la puesta en marcha del calentador de placas.
Tabla 1 Características del proceso de calentamiento de jugo primario antes y después de las intervenciones realizadas
Parámetro | Unidad | Condición inicial | Condición final |
---|---|---|---|
Área de calentamiento primario | [m2] | 926 | 1,300 |
Flujo másico de jugo crudo procesado | [t/h] | 240 | 240 |
Flujo másico promedio condensado aprovechado | [t/día] | 0 | 1,434 |
Consumo específico de vapor fábrica azúcar | [lbmvapor/TCM] | 1,450 | 1,370 |
[kgvapor/TCM] | 657.6 | 621.3 |
Fuente: elaboración propia
Entre el 2018 y el 2020, periodo de operación del calentador de placas con condesados vegetales, se recuperó la energía contenida en 925,560 toneladas de condensado vegetal a 96°C, como se indica en la Figura 3.
3.2. Incremento del perfil de temperatura en el jugo claro alimentado al primer efecto de evaporación
Antes de implementar el mejoramiento del sistema, el jugo claro se alimentaba al primer efecto de evaporación a una temperatura de 93°C subutilizando el tándem de evaporación. Lo anterior debido a que parte de la energía del vapor de escape se usaba para el calentamiento del jugo hasta su punto de ebullición de 116°C. Para mejorar esta condición se instaló una etapa de calentamiento antes del tándem de evaporación, la cual está compuesta por dos calentadores de placas que operan en serie por el lado jugo.
La primera etapa recibe el jugo a una temperatura de 93°C y usando vapor vegetal 1, aumenta su temperatura hasta 105°C. El jugo resultante pasa a la segunda etapa encargada de elevar su temperatura hasta los 115°C mediante el uso de vapor de escape. Con la implementación de esta etapa de calentamiento se logró un aprovechamiento adicional del 23% del área de evaporación en el primer efecto y una reducción en el consumo de vapor de escape de 82.9 lbmvapor/TCM [37.6 kgvapor/TCM]. Cabe resaltar que el aumento de la temperatura en el jugo claro que alimenta al primer efecto de evaporación redujo en 44.5 % el tiempo de residencia del jugo en este equipo. Esto impactó positivamente la recuperación de sacarosa al evitar la degradación térmica, la cual es característica de esta parte del proceso cuando se manejan altos tiempos de residencia (> 5 minutos). En la Figura 4 se indica el esquema de operación detallado para los calentadores del jugo claro que alimenta al primer efecto de evaporación. Así mismo, los datos que relacionan el antes y después de la ejecución de esta etapa del proyecto se presentan en la Tabla 2.
Tabla 2 Características del proceso de calentamiento de jugo claro antes y después de las intervenciones realizadas.
Parámetro | Unidad | Condición inicial | Condición final |
---|---|---|---|
Área de calentamiento jugo claro | [m2] | 0 | 483 |
Flujo másico de jugo claro procesado | [t/h] | 260 | 260 |
Flujo másico vapor vegetal 1 a 112 °C Etapa 1 | [t/h] | 0 | 6.0 |
Flujo másico vapor escape a 125 °C Etapa 2 | [t/h] | 0 | 5.6 |
Tiempo de residencia primer efecto evaporación | [min] | 9.5 | 5 |
Consumo específico de vapor fábrica azúcar | [lbmvapor/TCM] | 1,370 | 1,287 |
[kgvapor/TCM] | 621.3 | 583.7 |
Fuente: elaboración propia
3.3. Rediseño del área de transferencia de calor del tándem de evaporación
Luego de realizar un análisis de cada una de las tecnologías existentes para la evaporación de jugo de caña, se instaló un evaporador modular compuesto por tres calandrias, cada uno de 1,900 m2 y un tanque de expansión encargado de separar la fase líquida de la gaseosa en el jugo evaporado (balón de expansión). Las principales ventajas de este tipo de tecnología se resumen con un mayor coeficiente de transferencia de calor respecto a evaporadores tipo Roberts y Falling Film, y una reducción del tiempo de residencia del jugo en el evaporador del primer efecto. Con la instalación de este equipo el Ingenio Risaralda redistribuyó las áreas de cada uno de los efectos de evaporación como se muestra en la Tabla 3 expresando en dichas áreas en metros cuadrados.
Tabla 3 Características del tándem de evaporación antes y después de las intervenciones realizadas.
Área transferencia de calor | Condición inicial [m2] | Condición final [m2] |
---|---|---|
Primer efecto | 4,180 | 3,716 |
Segundo efecto | 1,672 | 4,180 |
Tercer efecto | 1,300 | 2,972 |
Cuarto efecto | 1,300 | 1,300 |
Quinto efecto | 583 | 743 |
Stand by para aseos | 750 | 1,350 |
Área Total Evaporación de Jugo | 10,502 | 14,261 |
Fuente: elaboración propia
3.4. Reconfiguración de los usos de vapor vegetal para los procesos de cristalización de masa cocida y secado de azúcar húmedo
Tal como se indicó en la Figura 2, la instalación del evaporador modular en el primer efecto de evaporación permitió reconfigurar todo el sistema de alimentación de jugo y extracciones de vapor en cada uno de los efectos de evaporación. En la Tabla 4 se muestra la configuración inicial y final del uso de vapor en los procesos de cristalización y secado luego de la reconfiguración (ver Figuras 1 y 2) en el tándem de evaporador desde el primer hasta el quinto efecto.
Tabla 4 Configuración de proceso antes y después de las intervenciones realizadas -vapor en cristalización y secado
Proceso | Condición inicial | Condición final |
---|---|---|
Tacho continuo masa A | Vapor vegetal I | Vapor vegetal III |
Cristalización masa A | Vapor vegetal I | Vapor vegetal II |
Cristalización masa B | Vapor vegetal I | Vapor vegetal II |
Cristalización masa C | Vapor vegetal I | Vapor vegetal II |
Secadora azúcar blanco | Vapor escape | Vapor vegetal I |
Secadora azúcar turbinado | Vapor escape | Vapor vegetal I |
Secadora azúcar refinado | Vapor vegetal I | Vapor vegetal II |
Fuente: elaboración propia
En la Figura 5 muestra el esquema de operación del proceso de secado con el cambio de vapor escape hacia vapor vegetal I, y la reconfiguración de las líneas de vapor hacia la unidad de cristalización. La Figura 6 muestra algunos de los equipos montados durante la ejecución del proyecto para alcanzar el objetivo propuesto en términos de consumo de vapor.
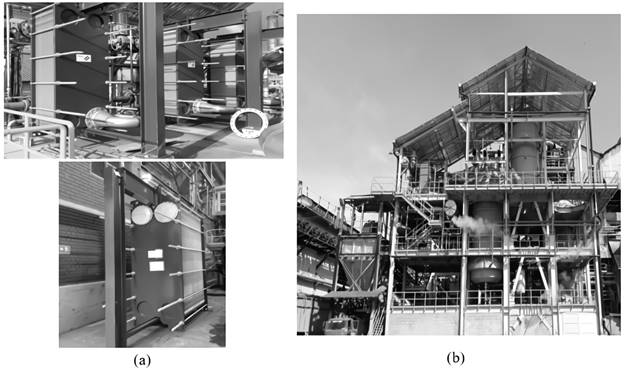
Fuente: elaboración propia
Figura 6 Equipos instalados: (a) Intercambiadores de calor de jugo crudo y claro. (b) Evaporador Multicalandria de primer efecto.
El año 2020 fue el más relevante en cuanto a la reducción del consumo específico de vapor, esto se dio con la entrada en operación del evaporador modular y la reconfiguración de las extracciones de vapor vegetal para los procesos de secado de azúcar, calentamiento de jugo y cristalización. En la Tabla 5 se presenta un resumen del ahorro de vapor de escape por tonelada de caña molida obtenido siguiendo la reconfiguración indicada en el numeral 3.4, donde se integró completamente el proceso de economía de vapor en todas las fases de elaboración de azúcar.
Tabla 5 Mejoramiento del uso del vapor de escape en proceso de cristalización masas A, B, C y secado de azúcar húmedo
Proceso | Reducción consumo de vapor | |
---|---|---|
[lbmvapor/TCM] | [kgvapor/TCM] | |
Cambio vapor secadoras de azúcar | 10.1 | 4.6 |
Cambio vapor tacho masa A | 80.3 | 36.4 |
Cambio vapor tacho masa B | 22.9 | 10.4 |
Cambio vapor tacho masa C | 1.9 | 0.86 |
Fuente: elaboración propia
El año 2020 fue el más relevante en cuanto a la reducción del consumo específico de vapor, esto se dio con la entrada en operación del evaporador modular y la reconfiguración de las extracciones de vapor vegetal para los procesos de secado de azúcar, calentamiento de jugo y cristalización. En la Tabla 5 se presenta un resumen del ahorro de vapor de escape por tonelada de caña molida obtenido siguiendo la reconfiguración indicada en el numeral 3.4, donde se integró completamente el proceso de economía de vapor en todas las fases de elaboración de azúcar.
En la Figura 7a se presenta la tendencia de consumo de vapor específico desde el inicio del proyecto en el año 2017 hasta el año 2020. Se evidencia un descenso total de 278 lbmvapor [126 kgvapor/TCM]. Como efecto de este mejoramiento en el uso del vapor de fábrica, la venta de energía muestra un incremento 3.3 GWh entre los años de ejecución del proyecto, según se indica en la Figura 7b.
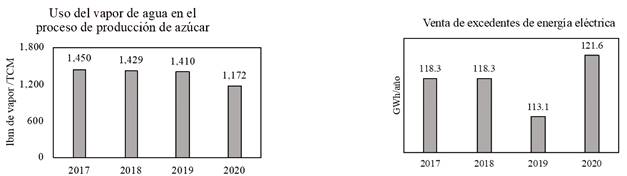
Fuente: elaboración propia
Figura 7 (a) Consumo específico de vapor proceso elaboración de azúcar (b) Venta anual de excedentes de energía.
En la Tabla 6 se resumen las principales características de los equipos instalados durante la ejecución del proyecto.
Tabla 6 Principales características de los equipos instalados en el Ingenio Risaralda S.A para la ejecución del proyecto de integración energética
Nombre | Clase | Área de transferencia | Material de construcción |
---|---|---|---|
Calentador de jugo L-L | Placas | 374 m2 | SS-316 |
Calentador jugo claro 7 | Placas | 175 m2 | SS-316 |
Calentador jugo claro 8 | Placas | 175 m2 | SS-316 |
Calentador jugo claro 9 | Placas | 154 m2 | SS-316 |
Calandria 1 | Calandria tubular | 1,900 m2 | SS-304 |
Calandria 2 | Calandria tubular | 1,900 m2 | SS-304 |
Calandria 3 | Calandria tubular | 1,900 m2 | SS-304 |
Balón de expansión | Tanque separador | N/A | 3CR-12 |
Fuente: elaboración propia
4. Conclusiones
Con el mejoramiento del uso del vapor en los procesos de calentamiento y evaporación de jugo, cristalización de masa cocida y secado de azúcar húmeda, se logró un ahorro de 278 lbmvapor [126 kgvapor/TCM] equivalente al 19.2% del vapor utilizado en fábrica antes de la ejecución del proyecto. Este ahorro en los consumos de vapor permitió incrementar la venta de excedentes en 3.3 GWh en el año 2020, al finalizar el proyecto.
Por otro lado, el aprovechamiento de la energía residual contenida en los condensados de la evaporación del jugo de caña (condensados vegetales) impactó significativamente la eficiencia energética del proceso de calentamiento de jugo crudo con el uso de 1,434 toneladas día de consensados vegetales. Esta corriente de energía anteriormente no era aprovechada, debido a que se vertía en el circuito de agua de enfriamiento de la fábrica. Esta aplicación contribuyó con un 28.7% del vapor total ahorrado en el proceso de elaboración de azúcar.
El cambio de las áreas de transferencia de calor en evaporadores permitió la reconfiguración de todo del sistema de extracciones de vapor vegetal (V1, V2, V3 y V4) utilizado en los procesos de calentamiento de jugo, cristalización y secado. Con esta modificación se obtuvo una reducción equivalente al 41.4% del vapor total ahorrado en la unidad de elaboración de azúcar. De esta forma, se logró demostrar que los proyectos de optimización energética deben enfocarse en trabajar sobre las etapas de evaporación y cristalización para generar impactos significativos en la reducción del indicador de consumo energético.
Seguidamente, la implementación de los calentadores de jugo claro para el aumento de la temperatura de entrada al primer efecto de evaporación permitió reducir el consumo específico aportando un 29.8% del total de vapor ahorrado. Además, se redujo en 44.5% el tiempo de residencia en el primer efecto de evaporación, generando efectos colaterales positivos en la recuperación y reducción de pérdidas sacarosa; y el 100% del aprovechamiento en las áreas de transferencia de calor para la evaporación del jugo.
Finalmente, se identificó oportunidades de optimización energética para la reducción de consumo de vapor y aumento de la venta de excedentes a la red, usando vapores flash de los condensados de vapor de escape, tanque de expansión del clarificador de jugo y vapor vegetal 5 para las etapas de calentamiento de jugo. Adicional a esto, es importante analizar los consumos de energía eléctrica en el proceso con el objetivo de maximizar el potencial de ahorro eléctrico que beneficiaria la entrega de excedentes.