1. Introducción
La biomasa es potencial fuente energética proveniente de materia orgánica renovable de origen animal, vegetal o producto de un proceso de transformación 1,2. La utilización de la biomasa como fuente energética se debe fundamentalmente a su bajo costo, alta disponibilidad y relativa sostenibilidad 3. Una de las potenciales fuentes de biomasa en Colombia son los residuos provenientes del cultivo de Palma de Aceite Africana. El proceso de extracción de aceite o palmiste produce biomasa residual denominada tusa. En Colombia se producen aproximadamente seis millones de ton/año de tusa, lo cual equivale a 9380 MW/h-mes de energía eléctrica, considerando la eficiencia global de conversión a energía eléctrica 1,3. Se extraen de acuerdo con el último censo realizado por Fedepalma 8682 ton/h de corozo o fruta, siendo el 20,22% del corozo biomasa residual tipo tusa, es decir, que se producen 1.264.311 ton/año de tusa 4. Específicamente en Norte de Santander y Cesar hay 23.156 y 72.778 hectáreas respectivamente sembradas de cultivos de Palma Africana de acuerdo con Fedepalma. En Norte de Santander se producen 9 ton/h; mientras que en el Cesar se cuenta con tres plantas extractoras con una capacidad total instalada de 24 ton/h 5. En la actualidad la tusa es utilizada como abono para las plantaciones, siendo depositada entre las líneas de los cultivos de Palma de Aceite Africana. El transporte de la tusa a los cultivos provoca la compactación de los suelos donde se encuentran los cultivos, trayendo como consecuencia disminución en la producción de fruta de palma de aceite o corozo. Un segundo factor negativo de la deposición de la tusa entre líneas de cultivo es la obstaculización que produce para las labores de cosecha 3. Además, la baja densidad de esta biomasa dificulta su transporte y almacenamiento, generando sobrecostos en un esquema de aprovechamiento como residuo agroindustrial.
Una posible solución a todos esto problemas es la posible utilización en la propia planta extractora de la tusa de palma de aceite africana como combustible renovable, con un costo más competitivo que los combustibles actuales, con bajas emisiones de CO2 y SO2 y con la garantía que se cuente con un poder calorífico similar a otros combustibles de fuentes renovables existentes en el mercado. Para que la tusa pueda ser utilizada en la producción de combustible a un costo competitivo, se requiere de procesos previos de secado y densificación 3,5,6. En años recientes se ha incrementado las investigaciones sobre procesos de densificación de biomasas (PDB) 7-11. Lo anterior debido a la necesidad de la industria agropecuaria de aprovechar los desechos generados de la producción de azúcar, panela, arroz y aceite de palma africana. En el proceso de densificación mediante acción mecánica se han implementado diferentes sistemas, como los de palancas, biela-manivela, rodillos y de tornillo sinfín. Cada uno de los mecanismos mencionados anteriormente utiliza un principio de densificación, los cuales son compresión o contrición, impacto y extrusión 3,6. El principio de prensado por impacto o extrusión utiliza un mecanismo biela-manivela. Este tipo de mecanismo permite convertir un movimiento circular de la manivela en uno lineal del pistón, por lo tanto, puede ser implementado para grandes producciones al tener incorporado un motor, sin embargo, puede ser operado manualmente. En los equipos que utilizan este principio, la briqueta se forma en la cámara de compactación. En el principio de prensado por compresión se utiliza fuerza axial hidráulica. Debido a los bajos costos de implementación el método es seleccionado para la fabricación de prensas a escalas de laboratorio, donde prima el control y determinación de rangos de valores de las variables involucradas en el proceso sobre la producción. En el método de comprensión por fuerza axial, la densificación ocurre en la cámara de compactación 1,3,6. Mientras el principio de prensado por compresión o contrición utiliza prensas de rodillos para la fabricación de briquetas. Este tipo de prensa emplea un arreglo de rodillos solidarios a un eje, cuya alimentación se realiza por gravedad de manera manual o utilizando una tolva. La geometría de la briqueta depende de las muescas en la superficie de los rodillos. Las prensas de rodillos están clasificadas en función de la construcción de los rodillos como prensas de rodillos integrales o segmentados y paralelos o perpendiculares; siendo utilizadas en la fabricación de briquetas a altas temperatura y cuyo material es abrasivo, por lo tanto, su material debe presentar buen comportamiento a la abrasión y altas temperaturas 3,6,12.
Por otra parte, en el proceso de densificación de biomasas varios investigadores han utilizado aglutinantes, como son los carbohidratos solubles en agua, cuyo porcentaje en briquetas de las biomasas tales como cascara de arroz y bagazo de caña se encuentra entre 2,2% y 7,9% y almidón de 0,4% -3% del volumen, lo anterior con el fin de obtener briquetas con mayor durabilidad. Otros investigadores han utilizado lignina presente en la biomasa, la cual usualmente se encuentra presente en un porcentaje en masa que varía entre 8,8% a 9,2%, para lograr la cohesión y durabilidad mecánica de las briquetas 13-15. Sin embargo, para la utilización de la lignina en el proceso se requiere primero de su activación por temperatura, posibilitando que actúe como adherente o soldadura entre fibras de la biomasa. Para que la lignina se active se requiere llevarla a su estado líquido y luego enfriar para permitir la unión entre fibras 3. Específicamente, en la activación de la lignina presente en la tusa se requiere de una temperatura de 100°C, para tiempos comprendidos entre 10 a 50s, cuya variación depende del contenido de humedad presente en la biomasa. Para un contenido de humedad entre el 8 y el 12% b.h. el tiempo oscila entre 20 s a 40 s.
Para fabricar briquetas de tusa de palma de aceite africana es posible utilizar una cámara de compactación con calentamiento eléctrico y un pistón accionado mediante un actuador hidráulico. Sin embargo, se hace necesario realizar una caracterización experimental de la biomasa y simular el comportamiento térmico de la cámara de compactación. Se deberá tomar también en consideración la influencia que poseen la longitud de la fibra y el contenido de humedad de la biomasa en el fenómeno de densificación 3,6. Partiendo de ello se plantea la hipótesis de si es posible diseñar una prensa briqueteadora para ser empleada en laboratorio basada en una cámara con calentamiento y un pistón accionado mediante un sistema hidráulico, que permita emplear la lignina presente en la fibra de tusa como único aglutinante en el proceso de densificación; además, que el calentamiento de la biomasa se realice lo más rápido posible, manteniéndose los esfuerzos y deformaciones en la cámara de compactación en niveles seguros definidos por diseño, de acuerdo con las propiedades del material utilizado. Para conocer el comportamiento del flujo de calor, el campo de temperatura, los esfuerzos y las deformaciones en las diferentes zonas de la cámara de compactación se propone utilizar simulaciones soportadas por el método de los elementos finitos. Este método tiene la ventaja de su bajo costo y alta calidad. El método emplea mallado adaptativo de la geometría, siendo fundamental para la calidad el número de elementos 16. Los softwares de elementos finitos permiten generar una malla empleando elementos tetraédricos, hexaédricos, con capa de inflación prismática o hexaédrica 16,17. La selección del número de elementos influye en el costo computacional, tiempo de solución y nivel de resolución. En dicha selección se debe encontrar un balance correcto entre el nivel de resolución y calidad de los resultados, y los recursos computacionales que son necesarios 16.
De lo expuesto anteriormente, se requiere realizar un estudio basado en simulaciones que utilizan el método de los elementos finitos, para explicar el efecto que posee la geometría de la cámara de compactación en el calentamiento de la biomasa residual tipo tusa proveniente de cultivos de palma de aceite africana de los Departamentos del Norte de Santander y Cesar. Este artículo presenta los resultados de simulación sobre el comportamiento de la transferencia de calor en la cámara de compactación utilizando una fuente de calor en la pared externa, y de los esfuerzos y deformaciones que ocurren del cilindro producto a la fuerza axial hidráulica aplicada. Lo anterior, con el propósito de establecer la geometría adecuada de la cámara de compactación para lograr un rápido calentamiento de la biomasa con un uso mínimo del material necesario en la fabricación de esta cámara.
2. Metodología
El proceso de simulación inicia con el cálculo de las dimensiones preliminares del espacio de compactación. De acuerdo con la investigación realizada para procesos de compactación 3,18, la densidad de la tusa previa al proceso de densificación es de 149 kg/m3, para una longitud de fibras en el rango de 70 a 150 mm, típica para cultivos de entre 5 a 20 años, además se define una masa objetivo de 42 g para una briqueta. Además, la norma sueca SS187120 establece un diámetro mínimo para las briquetas de 25 mm, mientras la Norma Técnica Colombiana NTC 2160 que corresponde a briquetas combustibles para uso doméstico, define que el diámetro mínimo debe ser 30 mm. Partiendo del valor de densidad, longitud promedio de fibras, dimensiones mínimas por norma para briquetas el volumen de la cámara de compactación deberá ser de 282 cm3, y predefiniendo un diámetro interno tentativo de 30 mm para la cámara de compactación, de acuerdo con NTC 2060 19, la longitud total de la cámara deberá ser L= 400 mm, con lo cual se garantiza un recorrido de la cabeza del émbolo o pistón suficiente para alcanzar relaciones de compresión (Rc) que conduzcan a un nivel de densificación apreciable de la biomasa. La relación de compresión se define como la posición inicial de la cabeza el émbolo respecto al extremo superior cerrado de la cámara de compresión dividido entre esta misma posición al finalizar el proceso de densificación. La relación de compresión que se logre es importante entonces para alcanzar valores de densidad aparente de la biomasa, con los cuales se cumpla lo establecido en las normas para briquetas de biomasa.
Para definir preliminarmente el espesor de la pared del cilindro se tiene en cuenta la longitud de la rosca de la termocupla. Se selecciona para el diseño una termocupla tipo K con longitud de rosca de 8 mm y un diámetro 5 mm; además, se sugieren al menos 2 mm de espesor adicional de la pared para evitar el contacto directo de la termocupla con la biomasa. Basado en lo anterior, el espesor preliminar para el diseño inicial de la cámara de compactación es de 10 mm.
La modelación de la geometría se realiza mediante el módulo Design Modeler de Ansys. Se parametriza el diámetro externo e interno de la camisa de compactación para una posterior optimización considerando como variable de respuesta esencial la temperatura de la superficie de la biomasa, la temperatura máxima alcanzada y la temperatura para la ubicación de la termocupla. En el estudio mecánico se consideró un comportamiento lineal elástico tanto para las piezas mecánicas como para la biomasa. La condición de apoyo definida es deslizante para la superficie inferior de la brida y los agujeros cilíndricos de sujeción. Las cargas sobre el ensamblen fueron la de trabajo del cilindro hidráulico y la gravedad. Se establecieron condiciones de contacto sin penetración para todas las superficies en contacto. Para la simulación se realiza un mallado utilizando elementos tetragonales de tamaño 5 mm para un total de 15 547 elementos en los cuatro componentes (cámara, tapón superior, pistón y la biomasa). Las condiciones de contacto incluyen la imposibilidad de penetración de una parte con relación a la otra, con un con un mallado tipo compatible. Además, se define un coeficiente de fricción de 0,15 entre las partes en acero y de 0,25 entre la biomasa y las partes en acero, los cuales son valores típicos de coeficiente de fricción para estos materiales 20.
Las condiciones de contacto incluyen la imposibilidad de penetración de una parte con relación a la otra, mallado compatible, un coeficiente de fricción de 0,15 entre las partes en acero y de 0,25 entre la biomasa y las partes en acero.
Los resultados de temperatura luego pueden ser validados con mediciones experimentales. Previamente para la simulación se definieron los materiales del cilindro, tapón, pistón de la cámara de compactación, asimismo de la biomasa residual. Para el cilindro tapón y pistón se utilizó acero H13 debido a su excelente comportamiento al choque térmico. El módulo de elasticidad del acero H13 es 207 GPa, posee una densidad de 7750 kg/m3, conductividad térmica de 26 W/K m y calor específico de 550 J/kg K [21, 22]21. Mientras para la biomasa residual de tusa se utilizan los valores de acuerdo con la revisión bibliográfica 3.
En la Figura 1 a) se muestra un esquema inicial de la sección longitudinal de la de la cámara de compactación. Esta última se acopla a la estructura soporte mediante una brida con pernos. Como parte del proceso de diseño se busca establecer las dimensiones adecuadas para esta brida. La temperatura en el borde de la brida de sujeción debe ser próxima a la temperatura ambiente de 13°C, con el fin de utilizar pernos normalizados típicos. En la Figura 1 b) se muestra una foto de la instalación experimental preliminar utilizada para realizar los experimentos de densificación de biomasa y registrar el comportamiento de la temperatura (termocupla tipo K) y la presión de compactación (celda de carga de 20 ton fuerza) durante las corridas experimentales.
Una vez parametrizada la geometría de la cámara de compactación se requiere establecer los flujos de calor y los tiempos de calentamiento. El flujo de calor se genera mediante una camisa de resistencias eléctricas ubicadas en el exterior de la cámara. Este flujo se determina en función de la potencia del equipo y el área envolvente de la camisa de resistencias fabricadas para tal fin. El diámetro de la camisa de resistencia eléctrica en el prototipo físico inicial concuerda con el exterior del cilindro de compactación de diámetro 50,8 mm y su longitud es de 300 mm. Para el cálculo de la potencia de la resistencia eléctrica se utiliza el voltaje nominal de la red, 220V, mientras el valor de la corriente medida experimentalmente es de 6,56 A. Con los datos anteriores se conoce que la potencia nominal suministrada por la resistencia eléctrica es 1,44 kW; por lo tanto, el flujo de calor para la geometría inicial \phi_q es 0,03014 W/mm2. Por otro lado, el tiempo de calentamiento dependerá fundamentalmente del flujo de calor, geometría de las partes, conductividad térmica de los materiales involucrados, los fenómenos de transferencia de calor y las condiciones ambientales. De acuerdo con un estudio experimental previo, se requiere alcanzar una temperatura en la superficie de la biomasa de al menos 100°C, para unos periodos de calentamiento de 10, 20 y 40 s respectivamente, para obtener una óptima durabilidad mecánica y resistencia a la compresión de las briquetas de tusa 3.
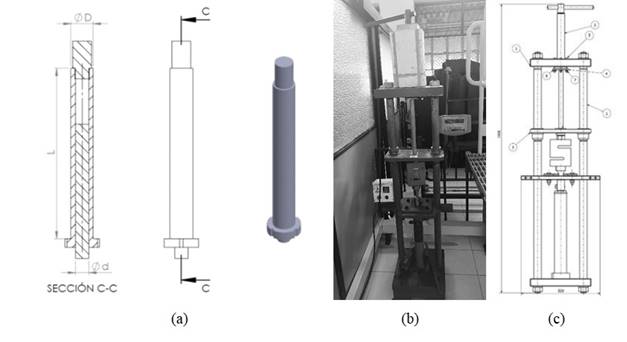
Fuente: elaboración propia
Figura 1 a) Representación de la cámara de compactación y sus dimensiones básicas; b) fotografía del primer prototipo de briqueteadora experimental .c) Prensa briquetadora para densificación de Tusa. Partes: 1. Columnas. 2. Cámara de compactación. 3. Base guía. 4. Arandela de sujeción. 5, 6 y 7. Pernos. 3.
Se plantea un diseño de experimentos basado en simulaciones utilizando como factores independientes el diámetro interno y el externo de la camisa de compactación. El diámetro interno se varía entre 27 mm y 33 mm mientras que el diámetro externo se varía entre 45 mm y 55 mm, respectivamente. La fuerza axial hidráulica se mantuvo para todas las simulaciones igual a 78 445 N, que es la fuerza máxima que entrega el sistema hidráulico del prototipo experimental, mientras que la potencia eléctrica se mantuvo constante con valor de 1,44 kW.
En las simulaciones térmicas se considera un coeficiente de convección de calor de 5 W/m2 K, considerando que el equipo opera en un espacio cerrado y que el exterior del cilindro esta recubierto por una manta térmica. Además, se tiene en cuenta la conducción de calor a través de la brida de sujeción a la placa de la bancada del equipo y no se consideran las pérdidas por radiación. Para el diseño de la cámara de compactación se realiza un análisis térmico transitorio utilizando el software Ansys Workbench versión R2021ª. En este estudio se utilizan mediciones obtenidas por vía experimental de la temperatura en un primer prototipo de camisa de compactación, como forma de validación de los resultados computacionales.
Finalmente se plantea una optimización para obtener una camisa de compactación con mínimo uso de material teniendo como restricción que el esfuerzo equivalente en la pared no supere el valor de esfuerzo admisible de diseño y que la potencia eléctrica se mantenga constante, lo cual conlleva a que el flujo de calor es función de las dimensiones exteriores de la camisa. La función objetivo a evaluar se define como:
Siendo:
Sujeto a:
Donde:
𝜉: función de cantidad de material (mm2).
D: diámetro externo de la camisa de compactación (mm).
d: diámetro interno de la camisa de compactación (mm).
L: longitud efectiva de la camisa de compactación (mm).
(max eq: Esfuerzo equivalente Von Mises máximo en la camisa (MPa).
[(]: esfuerzo permisible de diseño (MPa) ( [(]=400 MPa ).
(q: Flujo de calor (W/mm2).
Pot: Potencia eléctrica de la resistencia utilizada para el calentamiento (W).
3. Resultados
En un primer estudio se realizaron simulaciones sin biomasa y comenzando el calentamiento de la cámara de compactación a partir de la temperatura ambiente. El propósito de este estudio preliminar fue poder comparar los resultados de simulación con datos experimentalmente medidos sobre el comportamiento de la cámara fabricada para uso experimental. En la Figura 2 se muestran las curvas de temperatura medidas experimentalmente con termocupla instalada en el equipo y la obtenida como resultado de simulación. Se puede apreciar que el error relativo cometido en la simulación es pequeño, no superando el 7%. En la Figura 3 se puede apreciar la influencia marcada que posee la magnitud del flujo de calor en la velocidad de calentamiento de la camisa de compactación y la biomasa en su interior. Por ejemplo, se puede alcanzar la temperatura de 100°C en un tiempo 50 s más rápido en la superficie interior de la cámara de compactación, cuando el flujo de calor se incrementa de 0,0208 a 0,0410 W/mm2.
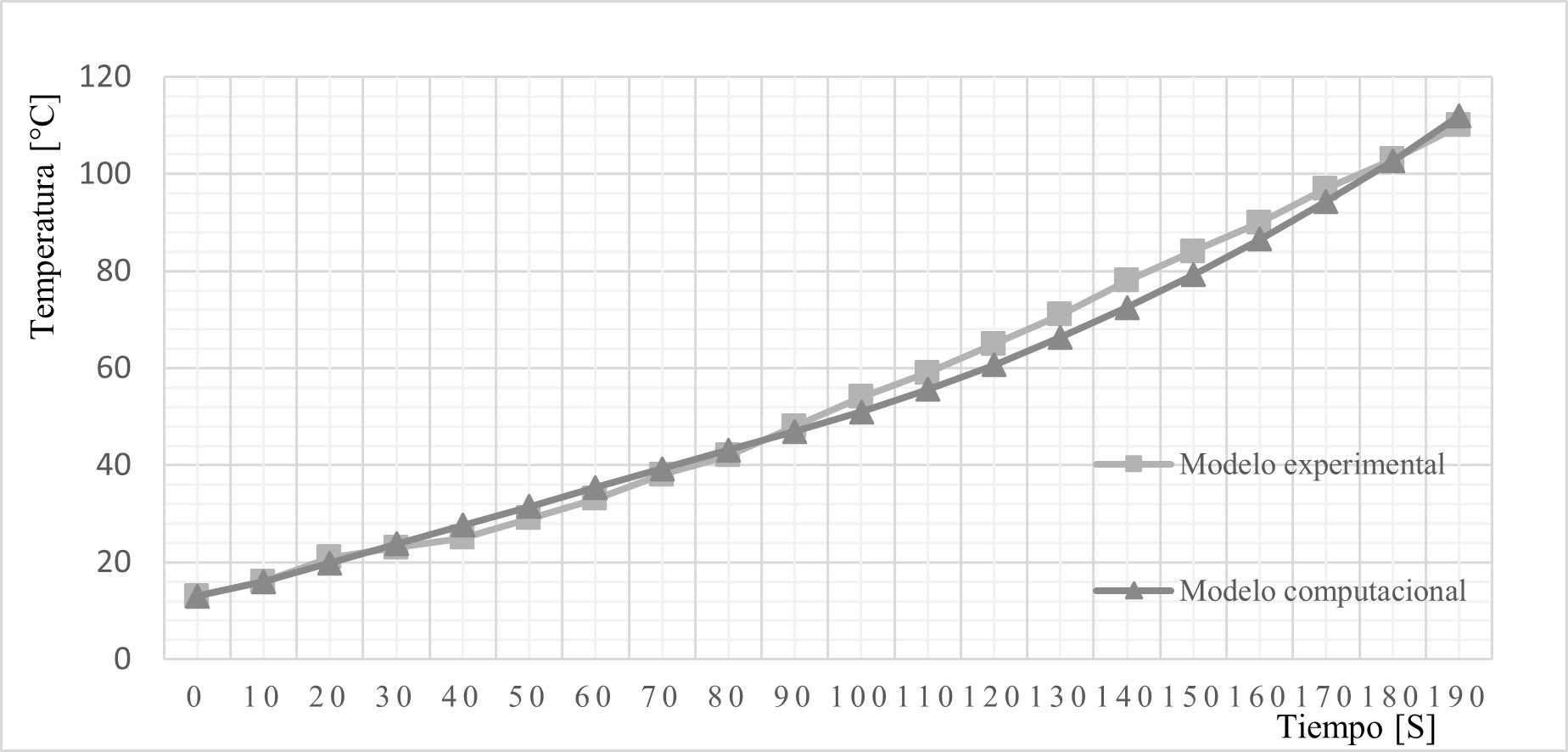
Fuente: autores.
Figura 2 Curvas de incremento de temperatura obtenidas en el modelo físico experimental y mediante simulación.
En la Figura 4 se muestran los trazados del campo de temperatura para los resultados de simulaciones térmicas transitorias cuando se utiliza un flujo de calor de 0,003 W/mm2, para tiempos de calentamiento de a) 110 s, b) 120 s, c) 130 s y d) 150 s respectivamente. Para estas simulaciones se consideró que la camisa se encuentra en t=0 s a una temperatura homogénea de 45°C (precalentamiento) y que ya el pistón realizó completamente su recorrido de compactación. Los diámetros interno y externo considerados para este estudio fueron 30 mm y 50 mm respectivamente. Se puede apreciar como a partir de un tiempo de calentamiento de 120 s se comienza a exceder la temperatura de 100°C en la superficie de la briqueta que se está conformando en la cámara de compactación, condición necesaria para la activación de la lignina presente en la biomasa
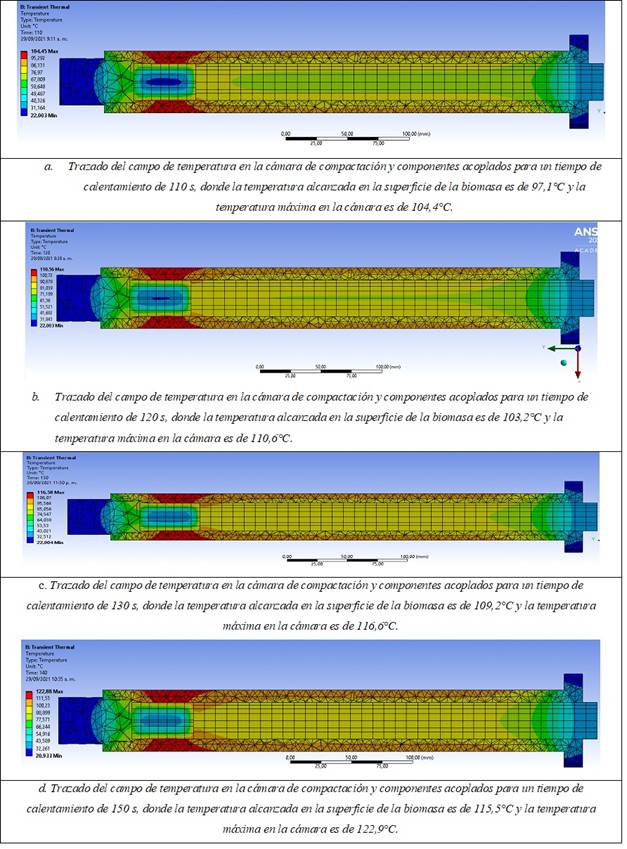
Fuente: autores.
Figura 4 Comportamiento de la temperatura en el cilindro de compactación para distintos tiempos de calentamiento.
Otro resultado particularmente útil es la influencia de la geometría de la camisa de compactación (diámetros exterior e interior) en la temperatura máxima alcanzada y la temperatura en la superficie interna de la camisa en contacto con la biomasa para distintos tiempos de calentamiento. Para estas simulaciones también se consideró un precalentamiento de 45°C de la cámara de compactación y que ya el pistón realizó completamente su recorrido de compactación. En la Figura 5 aparecen las superficies de respuesta para la temperatura máxima y la temperatura interna que alcanza la camisa de compactación en función de los diámetros exterior e interior y distintos tiempos de calentamiento final: a y b) para 120 s; c y d) para 130 s; y e y f) para 150 s, respectivamente.

Fuente: autores.
Figura 5 Superficies de respuesta para la temperatura máxima y la temperatura interna que alcanza la camisa de compactación en función de los diámetros exterior e interior, y para distintos tiempos de calentamiento.
En la Figura 6 aparece el trazado del campo de deformaciones, donde se puede apreciar como la biomasa al encontrarse en un estado de compresión confinada posee un campo de deformación homogéneo en su centro. Sin embargo, se aprecia un efecto de borde bastante pronunciado sobre todo en el contacto con el tapón de cierre. Luego, en la Figura 7 se muestra el trazado del esfuerzo equivalente Von Mises. En este último trazado se aprecia como los mayores esfuerzos ocurren en la brida de sujeción y en el agujero de acople de la termocupla; la superficie interna de la camisa en contacto con la biomasa también presenta valores significativos de esfuerzos equivalentes.
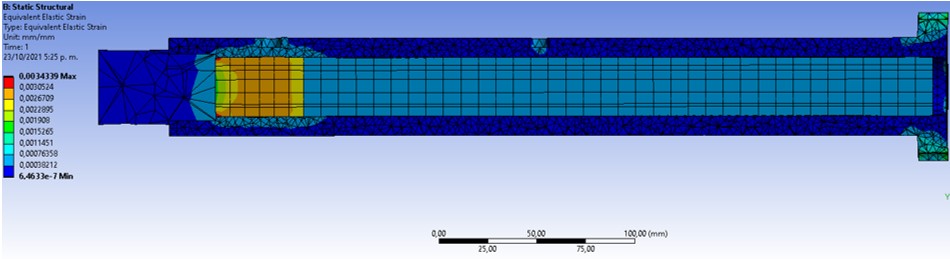
Fuente: Autores.
Figura 6 Deformación equivalente de los distintos componentes bajo estudio de la briqueteadora durante el proceso de densificación de la biomasa.
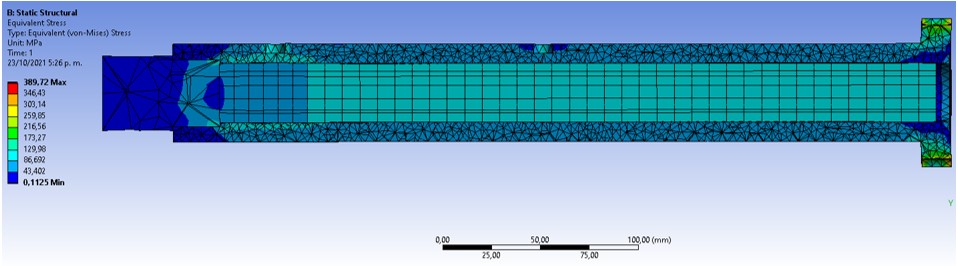
Fuente: Autores.
Figura 7 Esfuerzo equivalente Von Mises de los distintos componentes bajo estudio de la briqueteadora durante el proceso de densificación de la biomasa.
En la Figura 8 se muestra la superficie de respuesta para el esfuerzo máximo equivalente en función de los diámetros externos e internos del cilindro. El espesor de pared se reduce hasta un 40% en la simulación variando entre 12 mm y 6 mm, con el fin de establecer un valor apropiado en función de los esfuerzos equivalentes actuantes, los cuales son obtenidos considerando todos los detalles geométricos funcionales necesarios, como por ejemplo el agujero roscado para la termocupla. Para espesores mayores o iguales a 10 mm de pared el esfuerzo equivalente se encuentra por debajo de 360 MPa, mientras para espesores menores a 7 mm el esfuerzo crece de forma rápida por encima del esfuerzo permisible.
En la Figura 9 se muestra la superficie de respuesta para la temperatura en la superficie de la biomasa en función de los diámetros, interno y externo, de la cámara de compactación, donde se observa que a mayor espesor de pared es menor la temperatura alcanzada de acuerdo con el planteamiento de Fourier para la transferencia de calor por conducción. A medida que decrece el espesor se incrementa la temperatura, y se alcanza un valor de temperatura en la superficie de la biomasa de 160°C para un espesor de pared de la cámara de 6 mm; siendo el crecimiento lineal cuando se varía el espesor y manteniendo constante el diámetro interno. Sin embargo, si se mantiene constante el diámetro externo y se varía el diámetro interno, el comportamiento es aproximadamente cuadrático, siendo el punto de menor temperatura el punto medio del rango de variación del diámetro interno. Lo anterior obedece a la geometría de la cámara de compactación.
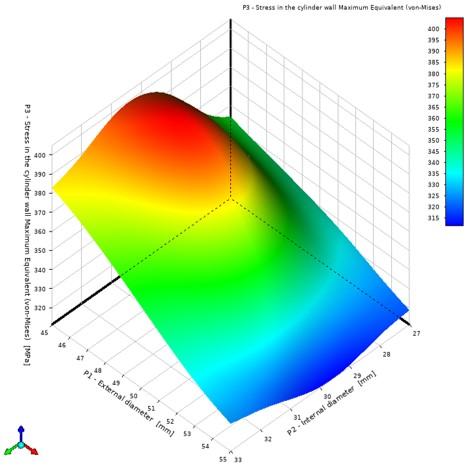
Fuente: Autores.
Figura 8 Comportamiento del esfuerzo máximo equivalente Von Mises en función de los diámetros externo e interno de la cámara de compactación.
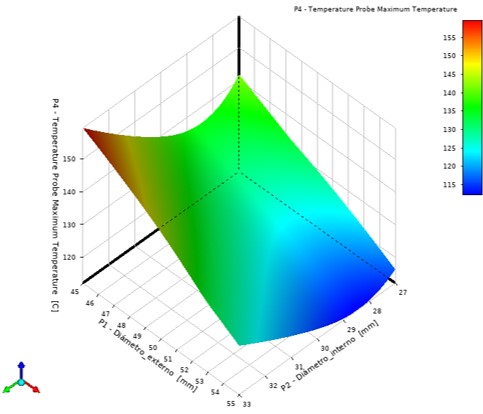
Fuente: Autores.
Figura 9 Comportamiento de la temperatura en la biomasa vs los diámetros de la camisa de compactación.
En la Figura 10 se muestra la superficie de respuesta para la temperatura máxima en función del diámetro externo y el flujo de calor. La superficie de respuesta muestra su máximo valor para la temperatura de 145°C en valores bajos de espesor pared (6 mm) donde el diámetro externo es de 45 mm y el flujo de calor es mayor, siendo su valor 0,035 W/mm2. A medida que se incrementa el diámetro externo y decrece el flujo de calor, para una resistencia eléctrica instalada de potencia constante, se produce disminución en el valor de la temperatura máxima alcanzada en el cilindro.
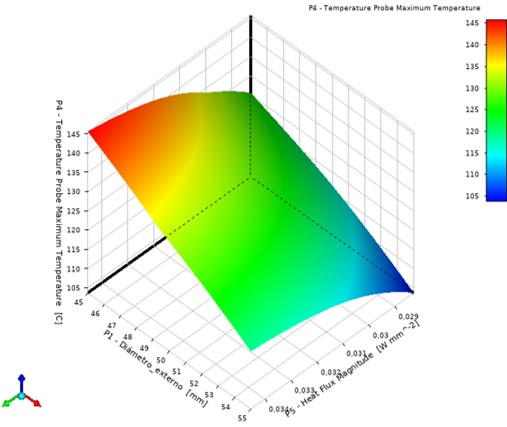
Fuente: Autores.
Figura 10 Comportamiento de la temperatura en la superficie de la biomasa en función del diámetro externo y el flujo de calor.
En la Tabla 1 se muestran las combinaciones de los valores de diámetros externos e internos establecidos mediante optimización, para obtener un valor de 100 °C en la superficie de la biomasa en un tiempo de 120 s. De acuerdo con la revisión bibliográfica cuando la superficie externa de la biomasa en proceso de compactación alcanza dicho valor se obtienen las mejores propiedades de durabilidad y resistencia a la compresión 3,6.
Tabla 1 Valores apropiados de diámetro externo e interno para obtener una temperatura en la superficie de la biomasa de 100°C.
Diámetro externo [mm] | Diámetro interno [mm] | Temperatura máxima [°C] | Temperatura externa de la biomasa [°C] | Porcentaje de variación |
---|---|---|---|---|
54,753 | 29,87 | 104,02 | 100 | 0.00% |
49,869 | 27,276 | 113,97 | 100 | 0.00% |
51,405 | 28,488 | 109,36 | 100 | 0.00% |
4.Conclusiones
Se obtuvo un diseño paramétrico de la cámara de compactación que incluye todos los detalles geométricos esenciales para dar cumplimiento a las funciones necesarias.
Las condiciones de carga, contacto y apoyo que se apliquen sobre el modelo de la cámara de compactación emulan lo mejor posible las características de operación reales de la briqueteadora. Estas últimas, a su vez, han sido obtenidas de experimentación previa, donde se establecieron valores para los parámetros esenciales como son, la longitud de la cámara de compactación suficiente para alcanzar relaciones de compresión adecuadas, la presión de compactación, temperatura de calentamiento de la biomasa y dimensiones de las briquetas para que cumplieran con la normatividad específica existente.
Se obtienen superficies de respuesta que dan cuenta de la gran influencia que poseen el diámetro externo, el diámetro interno y el flujo de calor para evaluar el tiempo necesario para alcanzar la temperatura de activación de la lignina en la biomasa. La temperatura en la superficie de la briqueta depende de una manera aproximadamente cuadrática con el diámetro interno, mientras que la dependencia de esta temperatura es aproximadamente lineal e inversamente proporcional con el diámetro externo de la cámara de compactación.
Se selecciona una camisa de compactación con dimensiones principales D= 46 mm, d= 32 mm y L=400 mm, con la cual se cumplen las restricciones de diseño establecidas, como son la meta de relación de compresión necesaria, las dimensiones de la probeta según los estándares existentes y la resistencia mecánica suficiente para el diseño (332 MPa < [(]=400 MPa). Para esta geometría y la potencia de calentamiento fija instalada, se logra una temperatura en la superficie de la briqueta de 118°C para un tiempo total de calentamiento de la biomasa de 130 s.
La metodología seguida en el actual trabajo sirve como una guía de diseño para cámaras de compactación de biomasa, mostrando las simulaciones basadas en el método de los elementos finitos donde son necesarias, las variables independiente influyentes que participan y las respuestas que funcionan como especificaciones técnicas, que caracterizan el desempeño de este subsistema perteneciente a los equipos para densificación de biomasa de esta categoría.