1. INTRODUCCIÓN
El titanio y sus aleaciones vienen ganando importancia en diferentes aplicaciones, especialmente en aplicaciones biomédicas teniendo en cuenta su resistencia a la corrosión, su alta resistencia específica, su baja densidad, su bajo módulo de elasticidad y buenas características superficiales y de biocompatibilidad [1]-[3]. El buen desempeño en cuanto a su estabilidad química se debe básicamente a la formación de una capa de óxido densa y pasiva sobre su superficie, sin embargo, cuando se utiliza como implante debido a las superficies biotribológicas que se forman, se rompe esta película de óxido y por tanto su pasividad, permitiendo la liberación de iones metálicos agravando la corrosión del implante creando una sinergia con el fenómeno biotribológico [4]-[7].
Por otro lado, la aleación Ti6Al4V se utiliza para la fabricación de prótesis de cadera y de ahí el interés por estudiar su comportamiento biotribológico. Los residuos generados en los implantes de cadera pueden provocar reacciones adversas que conducen a la pérdida de hueso alrededor del implante y, por tanto, al aflojamiento de la prótesis, obligando a una nueva cirugía de revisión [8]-[10]. Lo anterior, ha llevado al desarrollo de técnicas de modificación superficial que permitan mejorar las características superficiales. Entre estas técnicas se tienen; oxidación anódica (proceso de anodizado realizado a bajos voltajes), proyección térmica, CVD, sol-gel, PEO (proceso de anodizado realizado a altos voltajes), etc. [11]-[14].
El proceso de anodizado presenta ventajas respecto a otras técnicas de modificación superficial, debido a que la capa modificada superficialmente por esta técnica y principalmente por oxidación electrolítica por plasma (PEO), permiten la formación de capas de óxido con buena adherencia al sustrato, mejor desempeño frente a la corrosión y al desgaste, mayor dureza y una buena biocompatibilidad. Las propiedades de estas capas de óxido obtenidas por el proceso PEO dependen en gran medida de los parámetros del proceso empleados como: densidad, voltaje, tiempo, temperatura y del electrolito, donde el control de estas variables permite obtener las características de la capa de óxido de acuerdo con su aplicación final [15], [16].
Se han estudiado varios electrolitos, con el fin de lograr la incorporación de elementos necesarios en la capa anódica de óxido para mejorar la bioactividad y biocompatibilidad de las prótesis de titanio y sus aleaciones, debido a que estos materiales son bioinertes y por lo tanto no ocurre una integración química con el tejido óseo [13], [16]-[18]. Este comportamiento depende principalmente de las propiedades superficiales del material y de la capa de óxido formada (composición, cristalinidad y morfología) [19]. Empleando electrolitos alcalinos de fosfatos y de calcio se ha logrado la formación de capas anódicas biocompatibles, hasta la formación de especies biocompatibles y bioactivas en la capa de óxido de titanio, como es el caso de la hidroxiapatita que es un biomaterial con buena capacidad osteoconductiva, lo que facilita una buena osteointegración. También, se ha encontrado que al utilizar electrolitos de silicatos mejora la biocompatibilidad de las capas anódicas debido a que especies de Si inducen la formación de hueso [13], [17], [7], [20], [21].
Por otro lado, los procesos de manufactura aditiva (MA) vienen ganando cada vez mayor interés debido a su capacidad para producir piezas con geometrías complejas a un ritmo más rápido que los métodos convencionales [22], [23]. A diferencia de los procesos tradicionales, que requieren costosas herramientas y mecanizado para materiales duros, los procesos de MA por fusión de lecho de polvo sólo requieren la fusión de la materia prima en polvo con una fuente de calor como el láser o el haz de electrones [24]. El Ti6Al4V es uno de los materiales más comunes que se fabrican con esta tecnología, en particular para aplicaciones aeroespaciales y biomédicas [25]. La fusión por haz de electrones (Electron Beam Melting EBM) es un proceso de manufactura aditiva que a pesar de las ventajas que presenta en la fabricación de piezas con diseños complejos, adaptación de las propiedades y el menor desperdicio de material, el acabado superficial final obtenido con este proceso EBM tiene una rugosidad media de 10-30 µm [26], [24]. Para generar la superficie funcional con tolerancias estrechas de ˂ 0.5 µm, es necesario el mecanizado CNC. Las piezas construidas con manufactura aditiva se fabrican con un margen para el mecanizado final para darle las condiciones del acabado requerido. La combinación de los procesos de MA y las técnicas convencionales ofrece ventajas de ambas tecnologías y es económicamente viable. La ASTM define la MA como "el proceso de unir materiales para fabricar piezas a partir de datos de modelos 3D, normalmente capa sobre capa, a diferencia de las metodologías de fabricación sustractivas" [27]. Esta tecnología es aplicable a diversos materiales de ingeniería, como metales, cerámicas, polímeros, materiales compuestos y sistemas biológicos. LA MA hace posible la fabricación de productos más funcionales y únicos que no pueden fabricarse con los métodos tradicionales. Mediante MA se pueden fabricar exclusivas herramientas de corte que pueden aumentar la productividad con geometrías de diseño innovador en herramientas para proporcionar condiciones de corte óptimas. Sin limitaciones de diseño, se pueden fabricar productos más duraderos, ligeros y funcionales, así como piezas muy complejas, como un intercambiador de calor sin necesidad de procesos más complicados y lentos. Fabricación de implantes y prótesis complejas, de forma cercana, hechas a medida, con una reducción significativa del mecanizado para aplicaciones biomédicas. Además, los productos fabricados por MA pueden presentar propiedades más funcionales, rendimientos de trabajo más eficientes y una vida útil más larga [28].
En un estudio se analizó la superficie y subsuperficie en el torneado de la aleación Ti6Al4V, fabricada mediante EBM utilizando diferentes ajustes de contorno. También se estudió el efecto del tratamiento térmico posterior, es decir, el prensado isostático en caliente (HIP). Los resultados indican que evitar los contornos requiere una sobremedida de mecanizado de 1 mm para obtener una rugosidad superficial de aproximadamente 0.5 µm. En el caso de tres y cinco contornos la tolerancia de mecanizado puede reducirse a 0.25 mm. Las diferencias microestructurales derivadas del tratamiento posterior por HIP no afectaron la maquinabilidad de la aleación [29].
Teniendo en cuenta que la fusión por haz de electrones (EBM) se utiliza cada vez más para producir piezas biomédicas de Ti6Al4V y las superficies funcionales deben mecanizarse posteriormente, una investigación analizó la integridad superficial de las piezas EBM cuando son sometidas a operaciones de mecanizado en condiciones de refrigeración seca, húmeda y criogénica y se comparó con los mismos ensayos realizados en la aleación forjada convencional. Este estudio pone de manifiesto las diferencias en la maquinabilidad de las dos aleaciones investigadas, resaltando la necesidad de nuevos conocimientos sobre la optimización de parámetros para el mecanizado de aleaciones fabricadas por manufactura aditiva [30].
El presente artículo se deriva de un trabajo previo presentado en el Congreso Internacional ExpoIngeniería 2022 y publicado como capítulo de libro en las memorias del congreso [31], en el cual se presentaron los resultados de las pruebas biotribológicas que se realizaron a muestras de la aleación Ti6Al4V fabricada por forja, EBM y posteriormente anodizada utilizando como parámetros de las pruebas biotribológicas una carga de 5N y una velocidad de 30 rpm. En el presente trabajo el estudio se extendió a la evaluación de las propiedades biotribológicas con la carga de 5 N y velocidades de 30, 50 y 70 rpm, en un fluido corporal simulado (Simulated Body Fluid) SBF a una temperatura de 37 °C, simulando la temperatura corporal. Además, se hizo un análisis más profundo de la fricción, el desgaste y sus mecanismos, así como el efecto de la velocidad en el desempeño biotribológico de esta aleación obtenida mediante diferentes métodos de procesamiento: forja, fusión por haz de electrones (EBM) sin y con anodizado por PEO.
2. METODOLOGÍA
Muestras de la aleación Ti6Al4V se fabricaron mediante fusión por haz de electrones (EBM) y para efectos de comparación también se prepararon muestras de la misma aleación obtenidas por forjado convencional. El proceso EBM o Fusión por haz de electrones consiste en términos generales en la fabricación de componentes metálicos mediante la fusión de polvo en un proceso que ocurre capa por capa. El sistema EBM, está compuesto por una unidad superior (generación de electrones) y una inferior (zona de impresión o manufactura). En la zona superior se alcanza un vacío de 106 mbar mientras en la cámara de impresión de 104mbar. Esto permite evitar oxidación o contaminación del material fabricado.
Los electrones que se utilizan para la fusión del polvo metálico se generan en el cañón ubicado en la unidad superior del equipo, por calentamiento de un filamento de tungsteno. Al aplicarse una diferencia de potencial, los electrones excitados del filamento son acelerados formando un haz que es corregido, focalizado y deflectado por intermedio de una serie de lentes electromagnéticos ubicados en la columna superior del equipo. Dicho haz es utilizado para fundir el polvo metálico, que se dispone sobre la plataforma de impresión en la unidad inferior, o zona de impresión del equipo. En dicha zona, un brazo mecánico (“rake”) se ocupa de dispersar una capa uniforme de polvo que se alimenta de dos contenedores ubicados a ambos lados de la plataforma de impresión.
Cada capa de material impreso es obtenida en 4 etapas durante el proceso de impresión. En la primera el brazo dispersa una capa uniforme de polvo, moviéndose de forma lateral. Posteriormente, el haz de electrones se ocupa de pre-calentar y sinterizar polvo en un área rectangular que contiene las piezas a fundir; para ello se utiliza un haz de electrones desfocalizado. Esta segunda etapa se conoce como precalentamiento, y es necesaria en la técnica EBM para evitar la generación de explosiones producto del contacto directo del haz focalizado con partículas de polvo dispersas. Posteriormente, un haz de electrones focalizado es barrido sobre la capa de polvo previamente sinterizado, para fundir los componentes en cuestión, durante la etapa de fusión. La fusión a su vez se divide en fusión de los contornos y del “hatch” o interior de los componentes. Los contornos se funden utilizando un haz con condiciones especiales, especialmente un menor tamaño de sección transversal (“spot size”), para obtener un mejor acabado superficial. Finalmente, una vez fundidas las áreas correspondientes a cada capa, la plataforma de impresión es desplazada hacia abajo en el eje vertical (-z) una distancia correspondiente al espesor de capa (etapa 4), y el proceso vuelve a repetirse hasta completar la fusión completa de las piezas incluidas en el trabajo de impresión, capa por capa.
Una vez completado el proceso de fabricación, la mesa de impresión se desplaza en el eje vertical (+z), de manera que el volumen de polvo sinterizado, que contiene las piezas fundidas (embebidas en su interior) se puede remover. Dicho volumen de polvo con las piezas embebidas se conoce como torta de polvo (“powder cake”). Para la fabricación de las piezas por EBM en el presente estudio, se utilizó una impresora Arcam A2X (ARCAM, Mölndal, Västra Götaland, Suecia). Los parámetros del proceso EBM fueron: vacío entre 10-4 y 105(mbar), tensión de aceleración 60 kV, grosor de capa 50 µm, velocidad de barrido 0.50 m/s, y una temperatura en la cámara de 973 K (el lecho de polvo se precalentó a 973 K antes de fundir cada capa). Las muestras se cortaron en discos de 18.02 mm de diámetro y 3.77 mm de espesor. Algunas de las muestras que fueron obtenidas mediante fusión por haz de electrones, posteriormente se anodizaron con el fin de analizar el efecto de este tratamiento superficial en el desempeño biotribológico de estos materiales. Los parámetros utilizados durante el anodizado se presentan en la Tabla 1.
Tabla 1 Composición química del electrolito y parámetros empleados para obtener los recubrimientos anódicos.
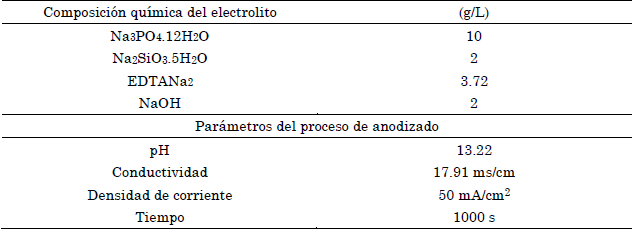
Fuente: elaboración propia.
Una vez obtenidas todas las muestras en los tamaños indicados, se pulieron con papel de esmeril de SiC de diferentes tamaños de grano. Seguidamente, se realizaron 5 medidas de rugosidad (Ra) en diferentes zonas de cada muestra con un perfilómetro Bruker Dektak XT utilizando recorridos longitudinales de 1500 µm a una velocidad de 100 µm/s.
Adicionalmente, se hicieron medidas de microdureza Vickers en un equipo Instron Tukon 2100 B aplicando una carga de 0.5 Kg durante 15 s. El ángulo de contacto generado entre las superficies de las muestras fabricadas por forja, EBM y EBM anodizada se analizó empleando agua y se utilizó un Goniómetro estándar Ramé-Hart modelo 250-F4.
Las pruebas biotribológicas se llevaron a cabo por duplicado en un tribómetro de tipo esfera sobre disco utilizando los parámetros que se muestran en la Tabla 2, el tribómetro empleado es de fabricación propia y cumple con la norma ASTM G99. Se obtuvieron registros del comportamiento de los coeficientes de fricción a lo largo de las pruebas directamente desde el tribómetro. Las muestras se limpiaron con etanol en un baño de ultrasonido durante 5 minutos y luego se pesaron para determinar la pérdida de masa durante las pruebas biotribológicas, este procedimiento se realizó antes y después de cada prueba para encontrar la tasa de desgaste. Para calcular la pérdida de masa se utilizó una microbalanza Mettler Toledo UMX5 con una precisión de ± 0.1 μg. La tasa de desgaste se calculó de acuerdo con (1).
Donde K es la tasa de desgaste (Kg/Nm), m es la pérdida de masa a lo largo de la prueba, w es la carga normal aplicada y l es la distancia total deslizada.
Además, se analizaron las superficies biotribológicas tanto de las muestras de interés como de los contracuerpos mediante microscopía óptica (Nikon Eclipse MA 100) para identificar posibles mecanismos de desgaste en los diferentes pares biotribológicos. Mediante SEM (JEOL-JSM 6490LV) se analizaron algunas huellas de desgaste sobre las superficies anodizadas.
3. RESULTADOS Y DISCUSIONES
La Tabla 3 muestra los valores de ángulo de contacto, rugosidad y dureza de las muestras obtenidas por los diferentes métodos. Respecto al ángulo de contacto se encontraron valores mayores a 90 ° sobre las superficies de la muestra forjada y fabricada por EBM indicando que son hidrofóbicas, mientras que la superficie anodizada mostró hidrofilicidad. También, se puede observar que las muestras anodizadas tienen la mayor rugosidad, seguidas de las muestras forjadas, mientras que las muestras preparadas por EBM muestran la menor rugosidad de todas. La elevada rugosidad de las muestras anodizadas podría favorecer el crecimiento celular en los implantes. Las muestras procesadas por EBM muestran una mayor dureza que las forjadas. No fue posible medir la microdureza en las muestras anodizadas debido a la alta rugosidad superficial. Bertolini et al. reportan para la aleación Ti6Al4V procesada por forja una dureza alrededor de 316 HV superior a la dureza de la aleación forjada del presente estudio y para esta misma aleación fabricada por EBM una dureza cercana a 296 HV, en la cual obtuvieron una dureza inferior a la aleación fabricada por EBM en el presente trabajo [32]. Estas diferencias pueden estar asociadas a los equipos y parámetros empleados para el proceso de fabricación de las aleaciones.
Tabla 3 Ángulo de contacto, rugosidad y microdureza de las muestras evaluadas

Fuente: elaboración propia.
3.1 Fricción
La Figura 1 muestra la evolución de los registros de los coeficientes de fricción en función del tiempo de ensayo para todas las muestras. Se identificaron dos etapas en el comportamiento de los coeficientes de fricción hasta 2400 s, un comportamiento transitorio inicial durante el acople entre las dos superficies biotribológicas exhibió una alta fluctuación en los valores de los coeficientes de fricción con un corto período de incremento continuo seguido por un régimen estable hasta el final de la prueba. En general, durante el período de acoplamiento inicial se produce una deformación plástica en la región de la subsuperficie, por lo que el trabajo de fricción se debe principalmente a la deformación plástica.
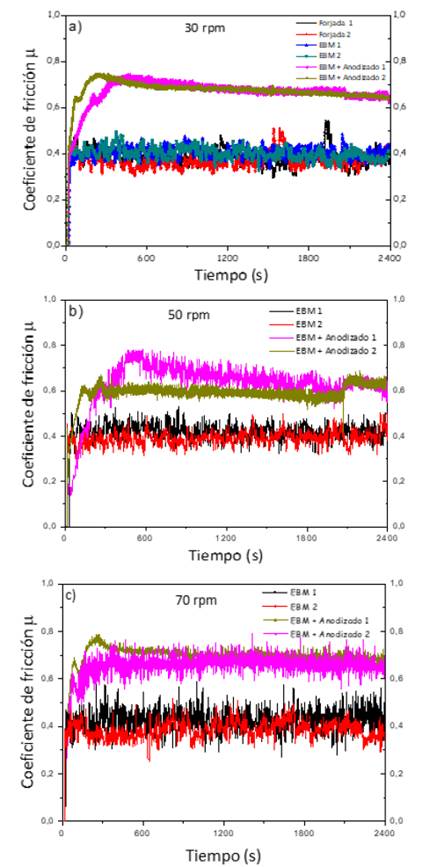
Fuente: elaboración propia.
Figura 1 Registros de los coeficientes de fricción en función del tiempo de prueba para: a) 30 rpm, b) 50 rpm y c) 70 rpm
De acuerdo con la Figura 1, el período de acoplamiento para las muestras forjadas y EBM se produjo para t < 100 s, mientras que este periodo para las muestras fabricadas por EBM y posteriormente anodizadas es alrededor de los 500 s a las velocidades de 30 y 70 rpm y de 600 s a la velocidad de 50 rpm.
Después del acoplamiento inicial se puede apreciar en todos los registros de la Figura 1 que en general se alcanza un régimen estable del coeficiente de fricción hasta finalizar las pruebas. Las repeticiones de cada ensayo muestran resultados reproducibles, además, en la etapa de régimen estable las muestras fabricadas por EBM y posteriormente anodizadas muestran registros más suaves (con menos fluctuaciones) que las muestras forjadas y las fabricadas por EBM sin tratamiento de anodizado. En general este comportamiento se observa con todas las velocidades evaluadas. Estas fluctuaciones alrededor de un valor medio que muestran los registros de fricción en régimen estable son típicas de este tipo de ensayos, las cuales se relacionan con las heterogeneidades de los materiales a lo largo de la pista de desgaste y que conllevan a diferentes mecanismos de fricción y desgaste [33].
En la Figura 2 se observan los valores medios de los coeficientes de fricción en régimen estable a las diferentes velocidades estudiadas. Se puede apreciar que los registros de fricción con valores más altos corresponden a las muestras anodizadas (µ = 0.68), mientras que las muestras fabricadas por forja y EBM exhiben valores similares (µ = 0.4). Las muestras fabricadas por EBM muestran coeficientes de fricción muy similares a las 3 velocidades, teniendo en cuenta sus desviaciones estándar no hay un efecto claro de la velocidad de la prueba en el valor de los coeficientes de fricción obtenidos. En las muestras que fueron anodizadas, el valor medio obtenido a 50 rpm muestra un coeficiente de fricción un poco menor que los obtenidos a las otras velocidades, pero teniendo en cuenta las desviaciones estándar, para estas muestras la velocidad no muestra un efecto importante en los valores de fricción.
Los valores más altos en los coeficientes de fricción en las muestras anodizadas se deben a que estas muestras debido al tratamiento, su superficie de contacto tribológico es óxido de titanio, el cual queda en contacto con óxido de alúmina proveniente de la esfera, ambos materiales con durezas cerámicas conducen a valores más elevados de coeficientes de fricción. Mientras que en el caso de las muestras forjadas y fabricadas por EBM la superficie es metálica, siendo el par tribológico metal-cerámico y al ser el metal más dúctil en contacto con un cerámico más duro los coeficientes de fricción disminuyen, dándose de forma más fácil la remoción de material desde el cuerpo metálico.
3.2 Desgaste
La Figura 3 muestra las tasas de desgaste de las muestras y los respectivos contracuerpos, como se puede apreciar las muestras forjadas presentan el mayor valor de tasa de desgaste (3.65 x 10-9 kg/Nm), lo cual es congruente con la menor dureza de esta muestra (Figura 3a). Las muestras preparadas por EBM presentan una disminución de la tasa de desgaste respecto a las muestras forjadas, lo cual también se corresponde con un incremento en la dureza de estas muestras, mientras que el tratamiento de anodizado permitió disminuir aún más la tasa de desgaste obteniendo el valor más bajo de todos con la muestra evaluada a 30 rpm (0.29 x 10-9 kg/Nm).
El tratamiento de anodizado muestra un efecto significativo en la mejora de la resistencia al desgaste del material fabricado por EBM con respecto al procesamiento convencional por forja. El anodizado, a pesar de aumentar el coeficiente de fricción, muestra una disminución muy importante de la tasa de desgaste. Estos resultados, aparentemente contradictorios, se deben probablemente a la naturaleza cerámica de la superficie anodizada que, al ser más dura y estar en contacto tribológico con el contracuerpo que es también cerámico aumenta el valor de fricción, pero al mismo tiempo es más protectora contra el desgaste.
Respecto a las velocidades evaluadas en las tasas de desgaste, se observa que a la menor velocidad (30 rpm) se observan las menores tasas de desgaste para los diferentes procesos de fabricación de las muestras, a 50 rpm se obtuvieron tasas de desgaste similares para las muestras fabricadas por EBM con y sin anodizar. De las muestras preparadas por EBM, el valor más alto de desgate se obtuvo a 70 rpm, mientras que de las muestras anodizadas el mayor valor de desgaste se obtuvo con la muestra evaluada a la velocidad de 50 rpm.
En la Figura 3b se observan las tasas de desgaste de los contracuerpos evaluados con las respectivas muestras, se aprecia que las tasas de desgaste de estos son 3 órdenes de magnitud inferiores a los valores mostrados por las muestras de Ti6Al4V, lo cual es coherente con la mayor dureza que presentan estos cuerpos cerámicos respecto a las muestras de naturaleza metálica. Las tasas de desgaste de los contracuerpos muestran la misma tendencia de las tasas de desgaste de las muestras, los contracuerpos de las muestras forjadas mostraron la mayor tasa de desgaste, seguidos de los contracuerpos evaluados con las muestras preparadas por EBM, mientras que los contracuerpos evaluados con las muestras anodizadas mostraron las menores tasas de desgaste.
Las tasas de desgaste de los contracuerpos evaluados con las muestras fabricadas por EBM con y sin anodizado mostraron un comportamiento paralelo.
La mayor tasa de desgaste se obtuvo a la velocidad de 30 rpm, seguida de la velocidad de 50 rpm, obteniendo el menor valor de desgaste el contracuerpo evaluado a 70 rpm, mostrando un efecto la velocidad utilizada en la prueba sobre la resistencia al desgaste del contracuerpo, a menor velocidad mayor desgaste. Cabe anotar que los contracuerpos evaluados contra las muestras preparadas por EBM con y sin anodizado arrojaron valores negativos de pérdida de masa, indicando que al finalizar las pruebas biotribológicas quedó material adherido a estas superficies estableciendo una ganancia en la masa
La Figura 4, muestra imágenes comparativas de las superficies desgastadas de Ti6Al4V obtenidas después de los ensayos biotribológicos a la velocidad de 30 rpm. Como se puede apreciar el tratamiento de anodizado da un aspecto superficial diferente al de las muestras metálicas, mostrando una mayor rugosidad como fue evidenciado en las medidas por perfilometría. El mecanismo de desgaste predominante en las muestras de Ti6Al4V forjado, Ti6Al4V EBM y Ti6Al4V anodizado es abrasión, mostrando surcos característicos en la dirección de deslizamiento. De hecho, las huellas de desgaste muestran un desgaste más severo en la aleación forjada, que corresponde al par tribológico con mayor diferencia de dureza entre las superficies tribológicas Ti6Al4V y el contracuerpo de alúmina, seguida de la aleación procesada con EBM, en la cual la diferencia de durezas entre las superficies tribológicas disminuye, mientras que la aleación anodizada después del procesamiento con EBM revela el mismo mecanismo de desgaste abrasivo, pero menos severo. También se puede apreciar en esta muestra anodizada material adherido al lado de la huella como lo indica la flecha.
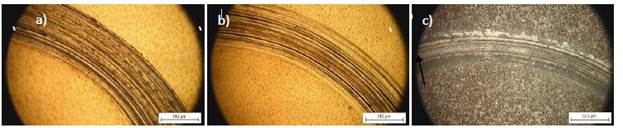
Fuente: elaboración propia.
Figura 4 Imágenes de microscopía óptica de las superficies desgastadas después de las pruebas biotribológicas a 30 rpm. a) Forjada, b) EBM y c) EBM+Anodizada
En la Figura 5 se muestra una imagen de esta huella en la muestra anodizada a mayores aumentos, aquí se puede observar con mayor detalle el material adherido alrededor de la huella de desgaste. Este material seguramente corresponde a las partículas de desgaste que se generaron a lo largo de la prueba proveniente tanto de la muestra de la capa de óxido como del contracuerpo, estos terceros cuerpos generados durante la prueba son los responsables de los altos coeficientes de fricción obtenidos en estos pares tribológicos. Además, la mayor rugosidad resultante de este tratamiento probablemente la hace más adecuada para los implantes al facilitar la adhesión celular.
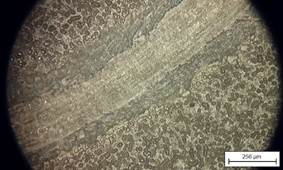
Fuente: elaboración propia.
Figura 5 Aspecto de la huella EBM anodizado, prueba biotribológica a 30 rpm a mayores aumentos
La Figura 6 muestra las superficies de las huellas obtenidas con las velocidades de 50 y 70 rpm, tanto de la aleación de Ti6Al4V como de sus respectivos contracuerpos. Como se observa, a estas velocidades también se identifica como principal mecanismo de desgaste abrasión en todas las muestras de la aleación de Ti6Al4V, mostrando la aleación anodizada huellas de desgaste con un ancho menor al ancho exhibido en las huellas de las muestras fabricadas por EBM, lo cual es coherente con las tasas de desgaste halladas donde las muestras anodizadas mostraron las menores tasas de desgaste, así como sus respectivos contracuerpos. Alrededor de las huellas obtenidas en las muestras anodizadas también se observa el material adherido que permaneció después del lavado de las muestras. En los contracuerpos se puede observar de forma similar material adherido alrededor de la superficie tribológica en todas las condiciones de velocidad y proceso de fabricación de las aleaciones. Tal como lo revelaron las tasas de desgaste calculadas, se aprecia un mayor desgaste en los contracuerpos utilizados con las muestras fabricadas por EBM respecto a los contracuerpos empleados con las muestras anodizadas. En la imagen de la Figura 6b, se observan manchas al interior de la huella de desgaste de la muestra fabricada por EBM evaluada a 70 rpm, las cuales probablemente pueden estar asociadas a la formación de productos de tribocorrosión generados durante la interacción entre las superficies tribológicas y el fluido simulado SBF utilizado durante la prueba.
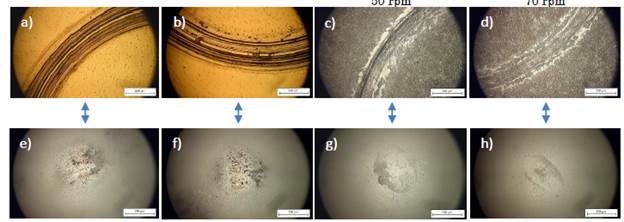
Fuente: elaboración propia.
Figura 6 Aspecto de las superficies de los contactos biotribológicos después de finalizadas las pruebas: a) huella EBM 50 rpm, b) huella EBM 70 rpm, c) huella EBM+Anodizado 50 rpm, d) EBM+Anodizado 70 rpm, e) contracuerpo EBM 50 rpm, f) contracuerpo EBM 70 rpm, g) contracuerpo EBM+Anodizado 50 rpm y h) contracuerpo EBM+Anodizado 70 rpm
En la Figura 7 se observa una imagen SEM de una huella de desgaste obtenida sobre la superficie anodizada y un zoom al lado derecho. En estas imágenes se pueden observar los poros característicos del anodizado a los lados de la huella de desgaste, además de la abrasión, en el interior de la huella y en el borde de la misma, se logra apreciar “spalling” que es una forma de desgaste por fatiga. Debido a la fragilidad de estos recubrimientos que son de naturaleza cerámica normalmente óxidos de titanio y la elevada porosidad que hay debajo de la superficie por donde hace presión el contracuerpo durante la prueba biotribológica se inician grietas y luego en la medida en que el ensayo avanza éstas van creciendo y se cruzan permitiendo el desprendimiento del recubrimiento por partes.
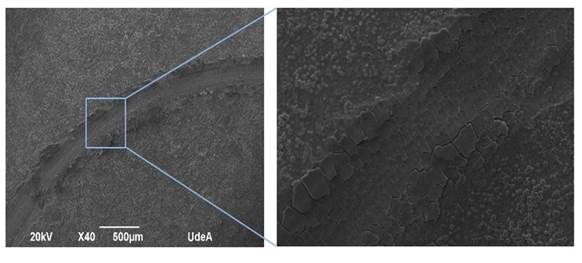
Fuente: elaboración propia.
Figura 7 Imagen SEM de la huella de desgaste obtenida a 30 rpm anodizada
En un estudio se evaluó el desempeño mediante pruebas de tribocorrosión de cilindros de Ti6Al4V obtenidos por forja y EBM después de maquinado en seco, en húmedo y criogénico. Para las pruebas de tribocorrosión se utilizó como contracuerpo una placa plana de ZrO2, en saliva artificial a 37 °C, los experimentos se realizaron a una frecuencia de 1 Hz durante 3600 s aplicando una fuerza normal de 45 N. Los resultados mostraron mayor desgaste en la aleación maquinada en seco, siendo superior el desgaste cuando la aleación fue fabricada por EBM que cuando se fabricó por forja. En las condiciones de maquinado en húmedo y criogénico el desgaste fue menor, mostrando un valor muy similar en ambos medios, mientras que en el presente estudio el mayor desgaste se obtuvo en la muestra forjada comparando con la prueba realizada a la misma velocidad respecto a las muestras fabricadas por EBM con y sin anodizar. En general, se pudieron detectar diferentes mecanismos de desgaste, desgaste abrasivo y adhesivo, independientemente de la ruta de procesamiento y estrategias de refrigeración durante el maquinado. Todas las imágenes mostraron ranuras uniformes alineadas con de deslizamiento las cuales son representativas del desgaste abrasivo. El desgaste adhesivo se evidenció por la presencia de parches de material de naturaleza del sustrato [32]. Estos mecanismos de desgaste también se evidenciaron en el presente estudio.
En otro trabajo se estudió el comportamiento de la aleación Ti6Al4V fabricada por EBM mecanizada a 80 y 110 m/min antes y después de tratamiento térmico durante 2 h en una atmósfera de argón a una temperatura de 980 °C. La aleación presentó una dureza Vickers (HV0.05) de 335 antes del tratamiento térmico, inferior a la dureza que se encontró en el presente estudio. Se realizaron pruebas tribológicas en trayectoria recíproca lineal utilizando una configuración de cilindro (Ti6Al4V) sobre placa (CoCrMo) en una solución salina a 37 °C con una frecuencia de 10 Hz y una carga de 7 N durante 10000 ciclos. Las muestras tratadas térmicamente mostraron coeficientes de fricción más bajos que las muestras no tratadas térmicamente, los valores de los coeficientes de fricción están en el rango entre 0.4 y 0.6. La resistencia al desgaste de las muestras no tratadas térmicamente es mucho menor respecto a las muestras tratadas térmicamente.
La pérdida por desgaste de la aleación Ti6Al4V recién mecanizada es más del doble que la de la aleación tratada térmicamente, independientemente de los parámetros de corte. Como mecanismos de desgaste se encontraron evidencias de abrasión y adhesión [34].
4. CONCLUSIONES
El proceso de fabricación EBM confirió a la aleación Ti6Al4V un incremento del 27 % en la dureza respecto al proceso de forja convencional, representando un proceso con gran potencial para la fabricación de prótesis.
Los registros de los coeficientes de fricción de las muestras fabricadas por EBM y posteriormente anodizadas fueron más elevados que los valores de las muestras fabricadas por forja y EBM sin anodizar independiente de la velocidad utilizada en la prueba biotribológica, lo cual se debe a la naturaleza cerámica del recubrimiento.
El proceso de fabricación por forja mostró la menor resistencia al desgaste, mientras que el procesamiento por EBM muestra un incremento en la resistencia al desgaste y el tratamiento superficial de anodizado sobre muestras fabricadas por EBM exhibió el menor desgaste de todas las muestras estudiadas.
Con la velocidad de 30 rpm se obtuvieron las menores tasas de desgaste para la aleación de Ti6Al4V con los diferentes procesos de fabricación, con esta misma velocidad se obtuvieron las mayores tasas de desgaste de los contracuerpos de todos los pares biotribológicos evaluados.
Respecto a los mecanismos de desgaste, la abrasión fue el mecanismo predominante en todas las condiciones evaluadas, siendo menos severa en las muestras anodizadas. Solo en la muestra fabricada por EBM evaluada a 70 rpm, además de la abrasión, se encontraron manchas características de fenómenos de tribocorrosión.