Introduction
Avant-garde energy-efficient materials reveal new construction solutions and high-cost technologies that dismiss every day the possibilities of implementing sustainable systems in the construction industry. Facades play a fundamental role in the environmental transformation of cities and their buildings; for this reason, its function is to strategically control the transfer of energy from the outside to the inside of the building and prevent high energy demand by artificial ventilation, refrigeration, and heating systems [1], [2].
The ceramic industry shows that 90% of the clays are destined to produce construction elements [3]. In Norte de Santander, Colombia, the ceramic industry has become established due to the manufacture of high-quality products and the mineralogical and chemical properties of the material from clay deposits [4], [5]. However, product design innovation for masonry is not consistent in such a major industry.
Exceptionally, some companies and designers stand out in the supply of products regionally by innovating the shape of products and the design of raw material mixtures. As it is the case of the Termo dissipator block, which provides thermal isolation through a horizontal ventilated air chamber, thermal bridge insulation, the modification of the perforation geometry, and shading [6]. Likewise, the termoarcilla block was developed using different mixtures with clay and polystyrene, which implied a 60% thermal conductivity reduction [2]. Although these products are innovative proposals, the consumer still refuses/hesitates to acquire this kind of product.
This research seeks to demonstrate energy efficiency from the design of ceramic products. Thus, two proposed bricks were designed under thermal insulation criteria and called ECO Design (ECO-D). Later, they were simulated by ANSYS R16 to validate the energy behavior through transfer and heat fluxes. Taking these results into account, the design with the highest thermal benefit, compared with the multiperforated brick (MB), was selected to be manufactured on a laboratory scale using a mixture of 100% clay (M-C) and a mixture of 95% clay and 5% coffee dust (M-CCD). Finally, a series of laboratory tests were carried out to validate linear shrinkage, water absorption, porosity, bulk density, compressive strength, dimensions, and efflorescence of the ceramic product.
Materials and methods
Dividing the product development process is fundamental because it allows delving into different types and levels of techniques and, at the same time, creating interdisciplinary synergies to advance product innovation. The method of developing a ceramic product on a laboratory scale is divided into three fundamental stages, namely, (i) product design, (ii) thermal validation, and (iii) technical validation. It was essential to compare the physical, mechanical, and energetic behaviors of the proposed ECO-D and MB to identify advantages and differences between them.
Product design
In the product design stage, a vertically perforated ceramic brick (ECO-D) for façade walls is proposed. Its main objective is to mitigate the heat transfer from the exterior to the interior surface of the brick by implementing guidelines such as treatment of mortar joints [7], ventilated air chamber [6], modification of cell distribution [6], [7], and exterior surface shape [6], [8].
Thermal validation
The thermal validation stage estimates the energy behavior of the bricks. In this stage, it was necessary to achieve heat transfer and heat flux simulations in ANSYS R16 software through the finite element method (FEM).
For conducting this process, the thermal conductivity data was supplied for standard clay bricks and cement mortar. Furthermore, alternative mixtures with organic waste in different percentages were used, modifying the thermal conductivity of the materials. The conductivity of materials used in this paper are described in Table 1.
Table 1 Conductivity of mixtures
Name | Mixtures | Conductivity |
---|---|---|
M-C | 100% clay | 0.691 Wm.°C [9] |
M-CCD | 95% clay and 5% coffee dust | 0.677 Wm.°C |
M-CCD-15 | 85% clay and 15% coffee dust | 0.639 Wm.°C |
M-CCD-30 | 70% clay and 30% coffee dust | 0.588 Wm.°C |
mortar | . | 0.88 Wm.°C [10] |
Source: Own elaboration.
The following data of San José de Cúcuta's environmental conditions are taken from the Ideam [11]. September was selected for being the month with the most extreme climatic conditions, described in Table 2.
Table 2 Climatic conditions of San José de Cúcuta
Condition | Value |
---|---|
Average maximum temperature | 91.4 °F |
Average maximum solar radiation | 796,8 Whm2 |
Time | 12:00 to 13:00 hours |
Q'Solar | 796.8 Wm2 |
Average wind speed | 4 m/s |
Source: Own elaboration.
The bricks undergo interactions in alternate physical conditions such as fluids and heat loads. The external wind condition (convection: 5 Wm2.°C) and solar radiation (heat flux: 796.8 Wm2.°C) are applied to the front face, and the internal natural convection condition (convection: 25.903 Wm2.°C). is applied to the rear face and the faces of the ventilation chambers.
Technical validation
Technical validation is the most complex stage. It involves manufacturing the ECO-D on a laboratory scale and analyzing the manufactured samples' physical and mechanical properties. This stage was performed following the MB development process on a laboratory scale established in [8] to compare the product's behavior and draw conclusions.
Manufacturing
Considering the thermal validation obtained from the heat transfer and heat flux simulations, the ECO-D1 product in M-C and M-CCD was selected for manufacturing because of their thermal benefits recorded in simulations. Its physical and mechanical behavior was analyzed in the laboratory. The product manufacturing process is divided into four parts: mixture preparation, extrusion, drying, and firing.
Mixture preparation: The raw materials used for this product were Murano clay (C) and coffee dust (CD). Both C and CD went through drying, grinding, mashing, crushing, grinding, sieving, and kneading. Two pastes were used: M-C, which is composed of 100% clay, and M-CCD, a mixture of 95% clay and 5% coffee dust.
Extrusion: Before the final extrusion process, a series of M-C nozzle tests were performed to correct the production and manufacturing details in the laboratory. The extrusion was carried out at the Ceramic Materials Research Center (CIMAC) on a 1:75 laboratory scale.
Drying: After extrusion, the samples were stored at room temperature for 24 hours. Then, they were subjected to a drying process at 212- 230 °F for another 24 hours.
Firing: Once the drying process was completed, the samples were fired at 1,832 °F.
Moreover, during the manufacturing process, the size of the samples (length, width, and thickness) was measured in wet, dry, and fired conditions.
Analysis
The manufactured samples were prepared on a laboratory scale to validate the of the ceramic masonry product development technically. This validation included the determination of linear shrinkage, mass losses, mechanical resistance to compression, efflorescence, porosity, bulk density, water absorption, and dimensions.
ECO-D1 was analyzed in 100% clay (M-C) and 95% clay with 5% coffee dust (M-CCD) and compared with the results of the thermal and technical characterization of MB [9]. The results shown in Table 7 and Table 8 are the average values of the data obtained from each test. The standards used to perform these procedures were UNE-EN 772-11 [12], UNE-EN 772-21 [13], and ASTM C-373 [14], NTC 4017 [15], and NTC 4205 [16].
Table 7 Dimensions
Sample | L (mm) | W (mm) | H (mm) | WP Partition (mm) | Perforated area (mm2) |
---|---|---|---|---|---|
ECO-D1 M-C | 42.24 | 26.88 | 13.02 | 3.20 | 31.15 |
ECO-D2 M-CCD | 41.92 | 26.37 | 12.55 | 3.29 | 33.50 |
MB M-C | 45.99 | 21.26 | 12.56 | 3.88 | 32.79 |
MB M-CCD | 45.58 | 21.12 | 12.83 | 4.29 | 30.07 |
Source: Own elaboration.
Table 8 Physical and mechanical properties of manufactured samples
Test | Material | |||
M-C | M-CCD | |||
MB | ECO-D | MB | ECO-D | |
Linear shrinkage ls (%) | 0.93 | 2.55 | 0.75 | 2.48 |
Lost mass (%) | 7.13 | 7.42 | 9.46 | 9.99 |
Initial water absorption rate by capillarity | 0.47 | 0.16 | 0.47 | 0.22 |
Water absorption by immersion in cold water (%) | 13.49 | 8.80 | 17.40 | 11.71 |
Apparent porosity (%) | 27.04 | 20.35 | 32.25 | 27.51 |
Water absorption by boiling (%) | 14.29 | 9.87 | 18.13 | 14.47 |
Apparent specific gravity | 2.61 | 2.59 | 2.63 | 2.62 |
Bulk density (g/cm³) | 1.90 | 2.06 | 1.78 | 1.90 |
Compressive strength (Kgf/cm²) | 5.56 | 2.71 | 5.00 | 1.84 |
Efflorescence | Effloresced. Yellow spots concentrated mainly on the edges of the surface. | Not effloresced | Effloresced. Yellow and thick veils on the edges of the surface | Not effloresced |
Source: Own elaboration.
Results
Product design
The product design stage is vital because of the necessity to search for new materials and shape elements for architectural envelopments to mitigate heat transfer, decrease energy consumption in buildings, and guarantee users' indoor comfort.
ECO-D consists of two formal options: eco Design-1 (ECO-D1) and ECO Design-2 (ECO-D2), as shown in Fig. 1. ECO-D1 has orthogonal characteristics. Its perforation geometry is parallel rectangles that lock together to slow heat transfer by conduction. Also, the air chamber is divided into four vertical channels with varied dimensions (width) to alter the shape of the façade.
ECO-D2 proposes organic façades through its curved appearance. Its perforation geometry is irregular since the outer arch that delimits the air chamber is offset in distorted rectangular cells on its longest side to the interior surface of the piece. Both designs propose lateral flanges to isolate the thermal bridges generated by the mortar joints. Additionally, ECO-D is designed for combination with MB to create different façade patterns.
Thermal validation
Thermal validation by heat transfer
The thermal validation by heat transfer records the parts' behavior in °C, i.e., both the outer and inner surface temperature. This paper contains the thermal profiles of MB [8], ECO-D1, and ECO-D2 in M-C and M-CCD, as shown in Fig. 2.
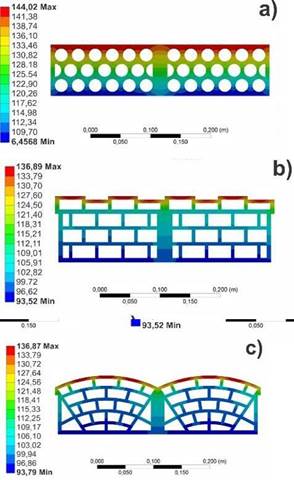
Source: Own elaboration.
Fig. 2. Thermal validation by heat transfer (°F): a) MB, b) ECO-D1, c) ECO-D2
Table 3 registers heat transfer values for MB. In M-C, it records an outer surface temperature of 144.01 °F, while the inner one was 107.06 °F; in M-CCD, the outer surface temperature was 144.06 °F while the inner one was 106.84 °F. Being a product positioned in the industry, MB was taken as a standard to compare the ECO-D1 and ECO-D2 external and internal behavior. The data shows that both proposals are heated outside at approximately 138.2 °F; that is, the thermal benefit outside is nearly 39.2 °F.
Table 3 Thermal validation of the ceramic product design by heat transfer (°F)
Source: Own elaboration.
Due to the ventilated air chamber and the thermal bridge's insulation, ECO-D1 and ECO-D2 mitigate the outer surface heating. Therefore, the inner surface temperature decreases to 93.2 °F, which means an internal thermal benefit of 45.5 °F in ECO-D1 (M-C and M-CCD) and 45.14 °F in ECO-D2 (M-C and M-CCD) due to the distribution of the interior cells.
Thermal validation by heat fluxes
On the other hand, thermal validation by heat fluxes identifies the points where energy is stored according to how the maximum and minimum standards are concentrated. The data is registered in W/m2. The areas that accumulate energy in the ECO-D proposals are the air chambers; however, MB shows that the absence of an air chamber and the exposure of the mortar joint (thermal bridge) increases energy concentrations in the whole product (Fig. 3).
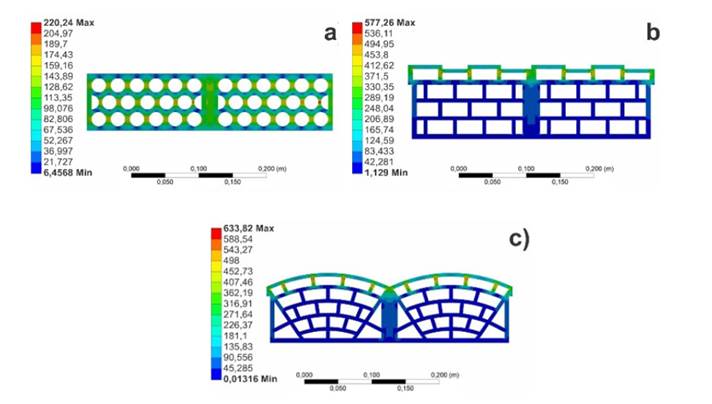
Source: Own elaboration.
Fig. 3 Thermal validation by heat fluxes (W/m2): a) MB, B) ECO-D1, and c) ECO-D2.
MB is taken as a pattern, as shown in Table 4, where the maximum heat flux reaches 220.24 W/ m2 and the minimum 6.45 W/m2. In this case, an inverse behavior is observed; the maximum heat fluxes are concentrated in the external surface and increase between 340 and 415 W/m2 compared to mb but the heat flux in the inner surface of ECO-D in M-C and M-CCD decrease between 5 and 6.5 W/m2.
Table 4 Thermal validation of the ceramic product design by heat fluxes (Hf) (W/m2)
Mixtures | Multi-perforated MB | ECO-D1 | ECO-D2 | ||
---|---|---|---|---|---|
M-C : 100% clay | Max. Hf | 220.24 | 577.26 | 633.82 | |
Min. Hf | 6.4568 | 1.129 | 0.01316 | ||
Energy benefit | Outer | ↑ 357.02 | ↑ 413.58 | ||
Inner | Pattern | ↓ 5.3278 | ↓ 6.4436 | ||
M-CCD: 95% clay and 5% coffee dust | Max. Hf | 217.35 | 557.52 | 623.62 | |
Min. Hf | 6.4197 | 1.0929 | 0.0066 | ||
Energy benefit | Outer | ↑ 340.17 | ↑ 406.27 | ||
Inner | Pattern | ↓ 5.3268 | ↓ 6.4131 |
Source: Own elaboration.
Product selection
According to the simulation results, ECO-D1 was selected for the efficiency of its thermal behavior in the specified environmental conditions. For this reason, the behavior of this design in different mixtures was further explored. ECO-D1 was simulated in two other mixtures, and the clay sample was taken as a standard to compare the thermal benefit. The mixtures vary according to the percentage of coffee dust in the paste: M-CCD 15% (85% clay and 15% coffee dust) and M-CCD 30% (70% clay and 30% coffee dust), as shown in Table 5.
Table 5 Thermal validation of the ceramic product design by heat transfer (°F)
ECO-D1 | Ext. T | Int. T | Thermal benefit | |
External | Internal | |||
Clay | 136.89 | 93.52 | Pattern | |
M-CCD | 136.94 | 93.46 | ↑ 32.04 | ↓ 32.06 |
M-CCD 15 | 137.06 | 93.28 | ↑ 32.16 | ↓ 32.24 |
M-CCD 30 | 137.23 | 93.04 | ↑ 32.33 | ↓ 32.48 |
Source: Own elaboration.
The percentage variation of organic material in the mixture does not represent a considerable thermal benefit compared to the thermal benefit obtained from the innovative shape. Oddly, as seen in Table 6, in the design's outer surface temperature (minimum) increases, but the inner surface temperature decreases between 32.06 and 32.48 °F. M-CCD 30% is the best result, which only increases the thermal benefit by 32.48°F on the design's interior surface.
Table 6 Thermal validation of the ceramic product design by heat fluxes (Hf) (W/m2)
ECO-D1 | Max. Hf | Min. Hf | Thermal benefit | |
Maximum | Minimum | |||
Clay | 577.26 | 1.129 | Pattern | |
M-CCD | 577.52 | 1.0929 | ↑ 0.26 | ↓ 0.0361 |
M-CCD 15 | 541.31 | 0.9802 | ↓ 35.95 | ↓ 0.1488 |
M-CCD 30 | 517.51 | 0.5354 | ↓ 59.85 | ↓ 0.5936 |
Source: Own elaboration.
Technical validation
Technical validation comprises ECO-D1 manufacturing and the analysis of its physical and mechanical properties. Fig. 4 shows the photographic record of some tests performed on the samples, such as the determination of dimensions, efflorescence, initial water absorption rate by capillarity, and water absorption by immersion in cold water.

Source: Own elaboration.
Fig. 4 a) dimensions, b) efflorescence, c) initial water absorption rate by capillarity and d) water absorption by immersion in cold water.
The determination of masonry units' dimensions includes the length, width, and depth of a masonry component (Fig. 5).
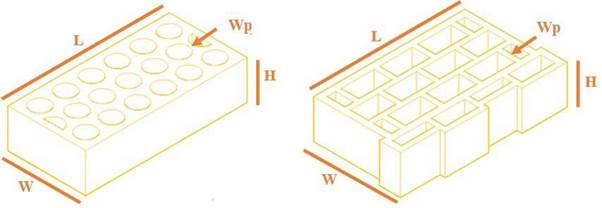
Source: Own elaboration.
Fig. 5 Length (L), Width (W), Height (h) and Width of partition (WP): MB (LEFT), ECO-D1 (RIGHT).
Tables 7 and 8 summarize the values of ECO-D1 dimensions of length (l), width (w), weight (h) and width of partition (wp) and properties, such as linear shrinkage (ls), mass losses, mechanical Table 7. Dimensions resistance to compression, efflorescence, porosity, bulk density and water absorption [12]-[16]. Likewise, Tables 7 and 8 contrast MB values.
Water absorption is the test carried out to determine a ceramic product's capacity to store water. Three water absorption tests were carried out: capillarity, immersion in cold water, and boiling. The test to determine the compressive strength consists of subjecting the masonry unit to a specific load, considering its construction application.
The qualitative determination of efflorescence allows registering the salt concentration of the material used for the sample manufacture by conducting the water evaporation process on the brick, which accumulates the salts on the outer surfaces in the form of white (sulfate salts) or yellow (vanadium salts) spots.
The general, dimensional, thermal, technical, construction, and regulatory characteristics of the ceramic product are described and illustrated in a technical sheet. According to Table 6, the linear shrinkage in MB, in both mixtures, have lower values than ECO-D1, which means that the samples of ECO-D1 in M-C and M-CCD are more prone to fissures and firing pathologies due to the higher values of LS. This finding is related to the compressive strength values since; ECO-D1 is less strong than mb, and water absorption capacity.
Conclusions
ECO-D is a proposal that integrates different disciplines (design, chemistry engineering, construction, and architecture) to conceive a comprehensive idea of all the phases that require the development of products in fired clay for building envelopes. The transition between stages widens communication between collaborators and creates synergies to solve the problems that arise throughout the research. There were different drawbacks during manufacturing due to the complexity of the design, the paste's composition, and the nozzle. These factors influenced the discontinuities in the extruded material because the paste granulometry is very thick, and the partitions' width is very narrow.
On the other hand, the simulation results verify and confirm the energy efficiency obtained from the design of a product, taking into account real extreme conditions of a specific site projected in virtual realities. ECO-D1 offers a thermal benefit of 44.6 °F in the interior temperature, which guarantees an improved comfort of the spaces delimited by this product.
Weaknesses usually limit the benefits of a product. In ECO-D1, its design makes it a light product because of the width of its partitions and the amplitude of its perforations, reducing its percentage of water absorption and apparent porosity compared to MB, which could mean a mechanical advantage to increase compressive strength. However, these variables do not influence this behavior. On the contrary, its capacity decreases resistance by half compared to MB.
Finally, the development of ECO-D demonstrates the importance of the relationship between the product's shape and the manufacturing material's physical, thermal, and mechanical properties. Thermal benefits in reducing internal temperatures of ECO-D are the result of a conscious design, according to the behavior of heat transfer in a material such as clay, in order to obtain spatial and thermal comfort in buildings and, hence, mitigate energy consumption.